Analyzing K Values A Comprehensive Guide to Pressure Loss Coefficients in Pipe Fittings
Analyzing K Values A Comprehensive Guide to Pressure Loss Coefficients in Pipe Fittings - Understanding K Values in Pipe Fitting Pressure Loss
Comprehending K values is fundamental to accurately forecasting how fluids behave within pipe systems. These values represent the resistance encountered by fluids as they pass through fittings and valves, effectively quantifying the pressure drop that occurs. This K value method provides a more refined approach compared to the Equivalent Length method for calculating these pressure losses, as it considers the specific geometric features and flow characteristics of each individual fitting. Translating K values into head loss provides engineers with a clear understanding of the effect that fittings have on system efficiency. While using common K values is usually sufficient for preliminary calculations, in-depth analyses might require precise friction factors and advanced methodologies such as computational fluid dynamics (CFD). These advanced approaches can better represent the complexity of the pressure loss scenarios encountered in real-world systems.
Understanding the intricacies of K values reveals that they are not simply a fixed characteristic of a fitting's shape. The flow conditions themselves play a significant role. Turbulent flow, with its chaotic nature, can induce considerably higher K values compared to the smoother laminar flow. The Reynolds number, a measure of the interplay between inertial and viscous forces, further demonstrates the variability of K values. This implies that a fitting's pressure loss behavior can be quite different across varying flow rates.
Each type of fitting, be it an elbow, a tee, or a reducer, necessitates its own unique K value. It's notable that even fittings with the same nominal size can exhibit significant differences in K, emphasizing the need for careful selection. Using the K value, or “loss coefficient,” approach provides a streamlined way to tackle pressure loss in complex networks. Engineers can estimate the overall pressure loss by simply adding up the individual K values for each component, avoiding intricate flow equations for each section of the system.
Interestingly, the orientation of a fitting can influence its K value. A vertical bend might exhibit a lower pressure loss compared to a horizontal one due to the interplay of flow separation and turbulence. This highlights the nuanced impact of seemingly minor variations in the system's geometry. When consulting tables and standards for K values, it’s critical to remember that values can vary considerably based on the specific testing methods and standards used. This compels engineers to be diligent in selecting reliable sources for their applications.
In certain situations, neglecting to account for fittings, or using oversimplified average K values, can lead to pressure loss miscalculations exceeding 20%. This emphasizes the importance of careful consideration of fittings for accurate predictions and achieving optimal system efficiency. The surface roughness of the fitting also affects pressure loss. A smooth internal surface generally results in reduced friction, consequently lowering the pressure loss in turbulent flow regimes.
Furthermore, the cumulative pressure loss from multiple fittings isn't always linearly additive. As more fittings are added, the total pressure loss doesn't necessarily increase proportionally. This requires designers to carefully manage these additive effects. While manufacturers may offer fittings engineered with lower K values to minimize pressure loss, their effectiveness can vary significantly. Validating these reduced K value claims in real-world scenarios becomes crucial for optimizing system performance.
Analyzing K Values A Comprehensive Guide to Pressure Loss Coefficients in Pipe Fittings - Calculating Pressure Drop Using K Values
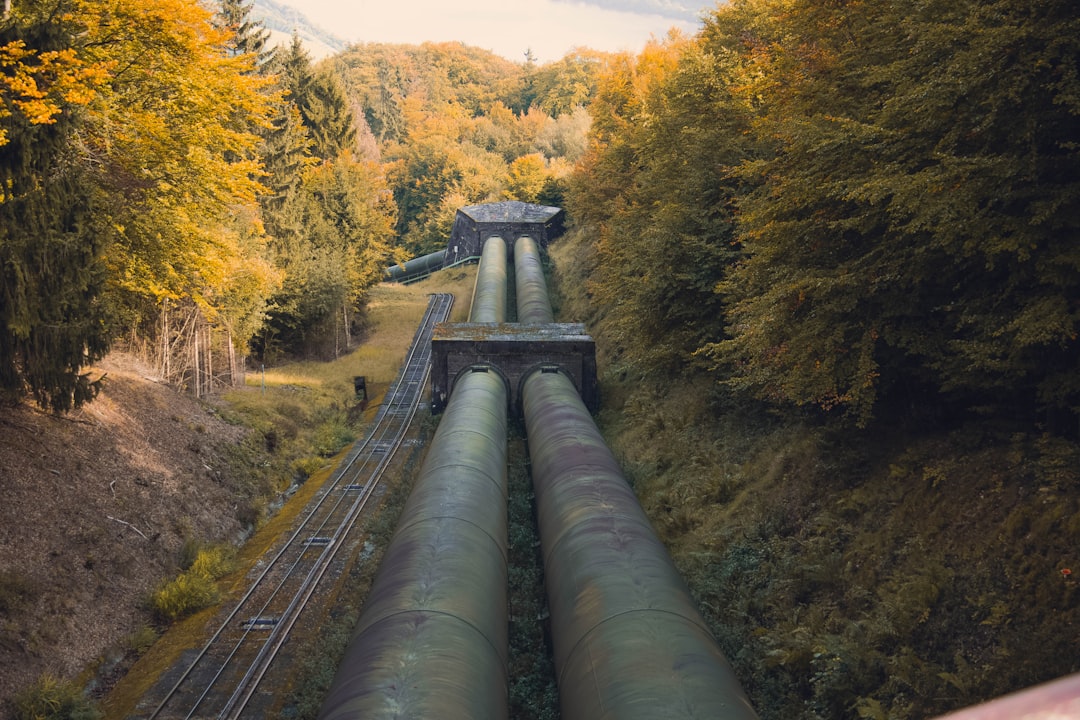
Calculating pressure drop using K values focuses on quantifying the pressure loss experienced by fluids as they traverse various pipe fittings. The K value itself represents the resistance encountered by the fluid, effectively acting as a multiplier of the velocity head lost. This value can be converted into head loss, a more tangible measure of energy loss, through a simple formula involving the K value, fluid velocity, and gravitational acceleration.
While the fundamental principle is straightforward, the accuracy of this approach depends on a nuanced understanding of K values and their variability. K values aren't static properties of fittings. They are influenced by a range of factors including the nature of the flow itself (laminar versus turbulent), the Reynolds number, and even the orientation of the fitting. This dynamic nature of K values necessitates careful consideration when performing calculations, especially in scenarios where pressure loss needs to be precisely controlled.
Methods like the 2K and 3K methods further illustrate the importance of understanding the variability of K values. These methods incorporate multiple K factors, allowing for a more refined prediction of pressure loss in scenarios where flow conditions and geometry are more complex. This underscores the importance of not simply treating K values as a fixed constant for each fitting but rather as variables that need to be assessed based on the specific conditions of a piping system. Ultimately, accurately calculating pressure drop involves incorporating a detailed understanding of how these K values are influenced by the complex interactions of fluid flow and fitting geometry. Without a firm grasp on these nuances, achieving accurate pressure loss calculations and optimizing piping system efficiency can be challenging.
1. It's easy to overlook that K values aren't just determined by the shape of a fitting. The type of fluid flow, whether it's smooth and predictable (laminar) or chaotic (turbulent), plays a massive role in determining the resistance the fluid encounters, significantly impacting the pressure drop.
2. Interestingly, the smoothness of a fitting's interior surface has a much bigger effect on pressure loss when the flow is turbulent. In laminar flow, this surface roughness doesn't seem to matter as much.
3. Engineers need to be mindful of the Reynolds number when figuring out pressure drops. It dictates if the flow is turbulent or laminar, directly influencing the K value for any fitting or valve.
4. The total pressure drop from a bunch of fittings isn't just the simple sum of each individual K value. The relationship can be more complex, where adding more fittings can lead to a disproportionately larger pressure drop.
5. The K value for a given fitting can change depending on how it's measured during testing. Differences in testing standards can lead to quite different reported K values, which makes it important to carefully evaluate the source of the information.
6. Surprisingly, how a fitting is positioned in the system – like horizontally or vertically – can affect the K value. A 90-degree elbow, for example, can have different pressure losses based on its orientation.
7. Relying on just average K values for fittings can introduce significant errors into the calculations. In some cases, the pressure loss can be miscalculated by over 20%, emphasizing the need for precise K values for accurate evaluation.
8. There are fittings being designed that claim to have reduced K values, aiming to minimize pressure loss. However, it's crucial for engineers to test these claims in real-world scenarios to make sure they deliver the advertised performance benefits.
9. Sharp changes in flow direction, like at a tee joint, can cause localized turbulence. This can make the K values higher than predicted from simple geometry considerations alone.
10. It's fascinating that K values can be affected by temperature. As the fluid's properties, like viscosity, change with temperature, the pressure drop can also vary in systems with changing conditions, highlighting the need for careful recalibration across different operating points.
Analyzing K Values A Comprehensive Guide to Pressure Loss Coefficients in Pipe Fittings - Common K Values for Different Pipe Fittings
When dealing with fluid flow in pipe systems, understanding the pressure drop caused by fittings is crucial. This understanding relies on the concept of K values, which represent the pressure loss associated with each specific fitting type. These K values, or loss coefficients, are unique to each fitting – elbows, tees, reducers, and more. The magnitude of the K value is influenced by the fitting's geometry and the fluid's flow characteristics. Factors such as the Reynolds number, indicating the flow regime, and the roughness of the fitting's interior surface can affect the K value. Moreover, even the orientation of the fitting can impact the pressure loss, underscoring the complexity of accurately determining K values for practical applications.
While readily available tables list common K values for various fittings, achieving accuracy in specific scenarios often requires going beyond these general values. Recognizing the influences of flow conditions and the individual characteristics of fittings is essential for precise pressure drop predictions. A thorough understanding of the relationship between K values and these diverse influencing factors is critical for effectively designing piping systems that optimize performance and efficiency. Without this nuanced understanding, accurate predictions of pressure loss become challenging.
1. While we often treat K values as fixed properties tied to specific fittings, they're actually sensitive to the Reynolds number, which reflects how smoothly or chaotically the fluid is moving. This implies that when picking fittings, we need to factor in the anticipated operating conditions of the entire pipe system.
2. Interestingly, the type of fluid flowing through a fitting can have a significant impact on its K value. For instance, thicker, more viscous fluids might lead to higher pressure losses due to interactions with the internal surface of the fitting.
3. The roughness of a fitting's internal surface seems to have a more prominent impact on pressure loss when the flow is turbulent. However, in smooth, laminar flows, this surface roughness doesn't appear to make as much of a difference.
4. It's somewhat surprising that the orientation of a fitting – for example, if a bend is horizontal or vertical – can alter its K value. A vertically-oriented bend might result in lower pressure losses compared to a horizontally-oriented one because of differences in how the flow separates and becomes turbulent.
5. The reliability of K values can be influenced by external factors, such as temperature and pressure. Since changes in temperature impact the viscosity of fluids, we need to expect that pressure losses calculated with K values will change as well. This reinforces the need for regular recalibration and adjustments to our K value estimates.
6. It's curious that the relationship between the K values of multiple fittings and the total pressure drop isn't always straightforward. As we add more fittings, the overall pressure drop might increase at a faster rate than the simple sum of their individual K values, complicating the design process.
7. Relying on generic average K values for fittings can lead to surprisingly large errors in our calculations, sometimes exceeding 20%. This underscores the importance of carefully selecting and applying specific K values during system design to ensure accuracy.
8. It's worth noting that fittings touted as having reduced K values don't always provide the advertised improvements in real-world scenarios. Their effectiveness seems to vary depending on the specifics of the system, suggesting the need for on-site validation to confirm the benefits of these specialized fittings.
9. While fitting geometry is a major consideration, we shouldn't neglect the impact that other elements like valves, gauges, or obstructions might have on the overall pressure loss. These features can interfere with the fluid flow and throw off our estimates of the K values.
10. The measurement method used to obtain K values can play a crucial role in determining the results. Differences in experimental conditions – such as the fluid's flow rate, type, and the condition of the fitting itself – can lead to varied K values being reported, highlighting the need to carefully examine the source of the information for accurate engineering decisions.
Analyzing K Values A Comprehensive Guide to Pressure Loss Coefficients in Pipe Fittings - Factors Affecting K Values in Piping Systems
K values, representing the pressure drop caused by fittings in piping systems, are essential for understanding fluid flow behavior. These values, also known as loss coefficients, are influenced by a range of factors. The type of fluid flow, whether it's smooth and predictable (laminar) or erratic (turbulent), significantly impacts K values. Additionally, the physical characteristics of fittings, including their shape and the smoothness of their internal surfaces, play a role. Further complicating matters, the way a fitting is oriented within the system and changes in operating conditions, such as temperature and pressure, can alter the pressure loss it creates.
It's crucial to recognize that K values are not simply fixed constants. Relying on general or average values can lead to large errors in pressure loss calculations, sometimes exceeding 20% of the actual value. For achieving optimal performance and efficiency in a piping system, it's imperative that engineers use precise K values that reflect the specific conditions of the system. Failure to consider these variables and use appropriately tailored K values can result in significant inaccuracies and suboptimal system performance.
1. While we often associate a specific K value with a particular fitting type, it's important to remember that the nominal size of the pipe it's connected to can also significantly impact the K value. This means that two fittings that look identical might cause different pressure losses simply because they are designed to be used with different pipe diameters.
2. The angle of a fitting can lead to substantial differences in pressure loss. For example, a 45-degree elbow might generate considerably less turbulence compared to a 90-degree elbow, resulting in a lower K value and reduced pressure loss. It's intriguing that such a seemingly minor geometrical difference can have a significant effect on fluid flow behavior.
3. It's not always obvious, but the properties of the fluid itself can influence the K value. Factors like temperature and density can impact the K value. For example, increasing the fluid temperature typically reduces viscosity, leading to a reduction in pressure loss during turbulent flow. This highlights the need to consider the operating conditions when selecting fittings for a system.
4. It's interesting to consider that the condition of the fitting itself plays a role in pressure loss. A new fitting might have a significantly different K value compared to one that has experienced wear or corrosion. The integrity of the fitting's material can significantly influence how much resistance it offers to fluid flow, causing variations in K values.
5. The flow rate through a fitting significantly impacts its K value. During low flow rates, the flow might transition from laminar to turbulent, dramatically increasing the K value. Engineers designing systems need to carefully calculate pressure drops across different flow regimes, especially if the system has varying demands.
6. The way fittings are arranged and spaced within a piping network can create intricate flow patterns. This can influence the K value in a way that isn't easily predicted simply by looking at the geometrical shape of each individual fitting. It's as though the collective arrangement of the system components can influence the overall flow behavior in unexpected ways.
7. Fittings that are designed with internal features like vanes or inserts to guide the flow can have significantly lower K values compared to standard fittings. These designs aim to improve system efficiency by minimizing turbulence and pressure loss. However, it's crucial to note that the performance of these specialized fittings should always be carefully tested and validated in practice.
8. Surprisingly, K values can exhibit hysteresis in systems with fluctuating flow conditions. This means the pressure drop can depend not just on the current flow rate but also on the previous history of flow through the system. This suggests that systems might 'remember' their recent flow history and this memory can influence the pressure drop.
9. K values obtained in controlled laboratory conditions might not perfectly match what's observed in real-world piping systems. Factors like temperature fluctuations and ambient pressures can cause discrepancies between predicted and measured K values. Engineers need to recognize that these conditions will impact the fitting's performance and should plan for adjustments to the calculated K values based on actual operating circumstances.
10. When evaluating fittings designed for reduced pressure loss (low-K fittings), it's important to recognize that their effectiveness isn't universal. They may only perform optimally within specific flow conditions. Overlooking these operating limitations can lead to unrealistic expectations of their performance in practice.
Analyzing K Values A Comprehensive Guide to Pressure Loss Coefficients in Pipe Fittings - K Values vs Equivalent Length Method
When determining pressure losses in piping systems, engineers must choose between using K values or the equivalent length method. The equivalent length method simplifies calculations by assuming fittings act like a specific length of straight pipe. While simple, it can lead to less accurate results, especially in complex systems. The K value method, on the other hand, offers a more nuanced approach. It uses K values, which represent the resistance a fitting presents to fluid flow. This method potentially yields more accurate results since it takes into account the unique characteristics of each fitting, as well as the flow conditions. This means designers can create systems that are more efficient by using precise calculations. However, it's crucial to be aware that simply using generic K values can lead to major inaccuracies in pressure loss calculations. Therefore, it's important to carefully evaluate individual fittings and their specific operating conditions for better results.
1. K values aren't fixed; they can shift considerably based on the speed of the fluid moving through them. As the fluid velocity increases, turbulence usually goes up, often resulting in larger K values. This highlights how a fitting's effect on pressure loss isn't static but changes with flow conditions.
2. Changes in temperature can influence the K value by affecting the fluid's viscosity. For example, if you raise the temperature of a fluid, its viscosity usually goes down, potentially resulting in a smaller pressure loss when the flow is turbulent. This shows that engineers need to rethink their K values when dealing with different temperatures.
3. The way a fitting is shaped isn't the whole story – even small changes in its angle can cause big differences in the pressure loss. For instance, a 45-degree elbow generally creates less resistance than a 90-degree one due to less turbulence. This emphasizes that even small design details are important.
4. How a K value is measured can greatly impact the results. Differences in the experimental setup, such as the kind of fluid used or how fast it's flowing, can produce different K values. This stresses that engineers need to carefully examine the source of their data.
5. Fittings with special internal shapes, like smooth surfaces or optimized designs, can greatly reduce K values. These specially designed fittings aim to reduce turbulence. However, whether they work as well in real situations compared to standard fittings needs to be checked.
6. The combined effect of multiple fittings on pressure loss isn't just a simple addition. As you add more fittings, the total pressure loss might become larger than just the sum of the individual K values due to how the flow interacts. This means that the system layout needs to be examined carefully.
7. Properties of the fluid like how dense it is and how easily it flows (viscosity) are key when it comes to K values. Using thicker fluids typically leads to greater resistance, meaning that the fitting's design has to be compatible with the expected fluid behavior to minimize pressure losses.
8. The age and condition of a fitting can change its K value quite a bit. Wear and tear can make the surfaces rougher, which increases friction and therefore pressure loss. This shows that piping systems need regular maintenance and inspection.
9. K values are affected by the specifics of the piping system and how it's arranged. The layout of the fittings can create unexpected flow patterns, resulting in pressure losses that aren't easily predicted just by looking at the fittings themselves.
10. Assuming that fittings designed for lower K values will perform well under all conditions isn't always accurate. Their effectiveness can vary greatly depending on how the flow behaves, and using them outside their intended range can result in the system working inefficiently.
Analyzing K Values A Comprehensive Guide to Pressure Loss Coefficients in Pipe Fittings - Practical Applications of K Values in Fluid Dynamics
The practical use of K values within fluid dynamics is vital for designing and evaluating piping systems, particularly in predicting pressure drops within fittings and valves. K values provide a deeper insight into how diverse fitting geometries and flow conditions impact fluid behavior, allowing engineers to optimize designs for better efficiency. Because these values are impacted by factors like fluid type, flow patterns, and the arrangement of fittings, accurately calculating pressure loss hinges on the careful selection and implementation of specific K values. This intricacy emphasizes the need for engineers to perform thorough analyses, moving beyond average or general K values, to ensure optimal performance in real-world applications. A strong understanding of K values not only enhances system design but is fundamentally important for minimizing energy waste in fluid transport.
K values aren't just about a fitting's shape; they're deeply intertwined with the nature of the fluid flow. Turbulent flows, with their chaotic swirls, can significantly increase K values compared to smoother laminar flows, even when other conditions are similar. This highlights that understanding the type of flow is vital when designing a system.
The speed of the fluid has a direct connection to the K value. As the fluid moves faster, K values can increase disproportionately due to increased turbulence. This means relying on static K values in systems where the flow rate fluctuates could lead to significant errors in our calculations.
Surprisingly, temperature can affect K values for fittings. For instance, higher temperatures often reduce a fluid's thickness (viscosity) and can noticeably decrease K values. This is a key factor to think about when designing systems that operate across a range of temperatures.
The angle of a fitting makes a big difference in its K value. For example, a 45-degree elbow can have a K value that's about half of a 90-degree elbow. This shows how seemingly small design changes can have a major effect on system efficiency, and we should consider that carefully.
The methods used to measure K values can produce different results. Variations in the experimental setup—whether it's the type of fluid, its temperature, or how fast it's flowing—can affect the K values that are reported. This means we must carefully examine the source of K values when designing a system.
K values can exhibit what's called hysteresis. This means the resistance a fitting offers to flow can depend on how it was flowing in the past. This implies that the history of a system can impact how it currently performs. So, designers should be mindful of this variability when designing a system.
The internal condition of a fitting, like wear or corrosion, can really change its K value. A well-maintained fitting performs much better than a worn-out one, which underlines the importance of regular checks and maintenance to keep a system efficient over time.
The direction a fitting is placed in a system—vertical or horizontal—can also have unexpected effects. For example, a vertical bend might cause less pressure loss compared to a horizontal one because of how the flow separates. This suggests that layout decisions should be made with the impact of orientation in mind.
The properties of the fluid, like how thick it is (viscosity) and how dense it is, are very important to K values. If we change a fluid's properties, we can get surprising pressure losses. This underscores the need to include these aspects during the initial design stages.
Fittings specifically designed with low-K values can be beneficial, but those benefits may only apply under certain flow conditions. Without thoroughly testing them in a real-world environment, relying on their theoretical advantages can lead to disappointing performance in actual use.
More Posts from aistructuralreview.com: