Assessing Wind Energys Impact on Structural Engineering
Assessing Wind Energys Impact on Structural Engineering - Reviewing structural considerations for tall wind turbine towers
Wind turbine towers are fundamental to harnessing wind power, acting as the critical support structure required for efficient energy capture. Their design has undergone significant transformation, moving beyond simpler conventional forms towards sophisticated tubular, hybrid, and increasingly taller configurations. This continuous push for increased height and turbine size is primarily driven by the need to optimize energy production and improve economic viability, yet it introduces substantial structural complexities. Engineers face the demanding challenge of ensuring the tower's integrity under ever more complex load cases, which include dynamic wind forces, operational wear, and extreme environmental conditions, particularly for large-scale offshore installations. Advanced structural analysis techniques and design methodologies are essential to accurately predict performance and engineer robust components throughout the structure, from the main shell to critical connection points. The sheer scale of contemporary towers also presents considerable hurdles in manufacturing, transportation, and onsite installation. As wind energy technology evolves and turbines grow, the structural engineering of these vital towers remains a complex and ongoing endeavor, requiring constant adaptation to new demands and careful consideration of potential vulnerabilities under immense stress.
Looking at these colossal structures, several key structural challenges quickly come to the fore when considering their sheer scale.
Often, the primary concern isn't merely surviving a single, extreme wind event, but rather managing the long-term cumulative effects of dynamic loading. Over a typical operational life spanning several decades, these towers endure billions of cyclic load fluctuations from wind gusts and rotor rotation. Designing to prevent fatigue crack initiation and propagation throughout the structure becomes paramount, demanding a different design philosophy than static strength alone.
The dynamic behaviour is profoundly complex, necessitating intricate aeroelastic analyses. This isn't just about wind pushing a static object; it's about the coupled interaction between the flexible tower structure, the aerodynamic forces on the rotating blades and nacelle, and the turbine's active control system. Understanding and accurately predicting this combined, fluctuating response is critical for ensuring stability and structural integrity under operational conditions.
A potentially limiting factor, particularly towards the base of the tower, is local buckling of the steel shell. Where the bending moments and axial forces are highest, the thin-walled cylindrical sections can be prone to localized instability. This failure mode often dictates the required steel plate thickness and the necessity and layout of internal stiffeners, sometimes proving a tighter constraint on minimum wall dimensions than the overall global bending strength of the cantilevered tower.
Transmitting the immense overturning moments down to the ground requires equally substantial foundation systems. These are far from simple footings. Large-diameter piled foundations, vast concrete gravity bases, or other bespoke engineered solutions are often necessary, and their complexity and material demands can mean the cost of the foundation package rivals or even exceeds that of the fabricated tower sections themselves, a point often overlooked initially.
Finally, the physical scale presents significant logistical hurdles. Transporting the largest diameter segments of the tower base to often remote sites is increasingly challenging due to road width and height restrictions. This constraint inherently influences design choices, encouraging the exploration of segmented or modular tower concepts, the development of onsite fabrication or welding techniques, and pushing the adoption of alternative structural forms and materials like hybrid steel-concrete or full concrete towers to overcome transport limitations.
Assessing Wind Energys Impact on Structural Engineering - Managing dynamic forces and material fatigue in turbine components
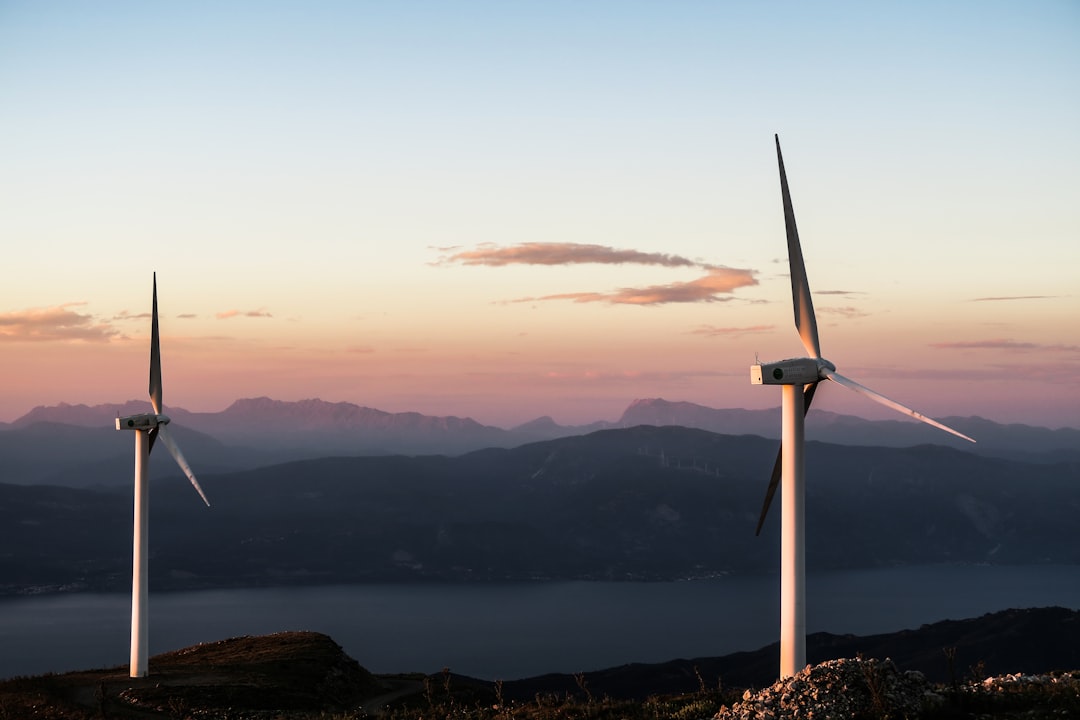
Maintaining the structural integrity and operational lifespan of wind turbine components hinges critically on effectively addressing the constant interplay of dynamic forces and the resulting material fatigue. These structures are relentlessly battered by the environment, with dynamic loads stemming primarily from fluctuating wind conditions and the continuous rotation of the rotor assembly. This imposes complex, varying stress patterns across the components over their intended service life, which can extend beyond two decades. Relying solely on design principles focused on surviving peak loads is insufficient; a deep understanding of cumulative damage accumulation over millions of load cycles is paramount. Consequently, assessing and managing fatigue demands sophisticated analytical techniques and, increasingly, the implementation of monitoring systems to track real-world load histories and estimate remaining component life. As turbine technology pushes boundaries in size and performance, navigating this intricate relationship between dynamic stresses and material endurance remains a fundamental, evolving challenge for structural engineering.
It's fascinating to consider how the challenges of dynamic forces and material fatigue extend beyond the main tower structure, impacting various critical components in surprisingly intricate ways.
For composite blades, for instance, the fatigue story is starkly different from steel. It isn't just about a crack starting and growing from one spot; instead, damage like micro-cracking in the matrix, broken fibres, or delamination occurs and accumulates throughout the material volume under cyclic loads. Assessing and predicting this widespread, insidious damage requires entirely different methodologies and presents a persistent challenge compared to the well-understood fatigue of metals.
Then there are the highly stressed parts of the drivetrain, particularly bearings and gears within the gearbox. Their fatigue life is critically tied not just to the torque and bending cycles they endure, but perhaps unexpectedly, to the characteristics of the lubrication – things like the thickness of the oil film and even minute particles contaminating the lubricant. This pushes the boundaries of structural analysis into the realm of tribology, where extremely high contact pressures and rapid load cycles drive specific fatigue modes like pitting and spalling that are distinct from bulk material fatigue.
It's also a curious paradox that active control systems, which are implemented to soften overall loads and dampen structural response, can introduce significant fatigue demands on their *own* components. The constant, small adjustments made by pitch control systems to manage aerodynamic loads, or yaw drives tracking wind direction, subject pitch bearings, actuators, and yaw gears to frequent, high-amplitude cycles. Designing these components to withstand the very cycles introduced by the control system's necessary operation is a critical, sometimes overlooked, aspect.
One quickly realizes that accurately predicting fatigue life isn't just about estimating a single equivalent load value. The actual sequence and frequency content of the dynamic loads, as the turbine experiences various wind conditions and operational states over its lifetime, can have a disproportionately large effect on cumulative damage. Capturing this complex load spectrum accurately and processing it correctly for assessment is a significant undertaking, highlighting limitations in simpler equivalent load approaches.
Finally, seemingly minor, localized events can have dramatic consequences. A relatively small impact on a composite blade surface, perhaps from a bird or hailstone, can create localized damage that acts as a severe stress riser. Under subsequent normal operational fatigue loading, a crack can initiate and propagate rapidly from this seemingly innocuous point, drastically reducing the component's life and underscoring the sensitivity of complex structures to unexpected environmental interactions.
Assessing Wind Energys Impact on Structural Engineering - Examining foundation approaches for varied wind farm locations
Moving beyond the tower itself, how we anchor these structures is perhaps the most location-dependent challenge. Selecting the right foundation for a wind turbine is critically tied to the specific site conditions, particularly when moving offshore where water depth and seabed properties vary dramatically. For shallower waters, simple monopiles have been common, but deeper sites push engineers toward more complex structures like tripods or jackets. The installation process itself varies significantly with type and location, often becoming time-consuming in difficult conditions and raising concerns about soil degradation effects around the piles or anchors. Traditional approaches using broader geological zones are increasingly proving insufficient, lacking the necessary adaptability for optimized site-specific designs. This necessitates more streamlined workflows for characterizing ground conditions uniquely at each position and incorporating approaches like probabilistic design to better assess risks and uncertainties under the constant dynamic loading from waves and wind. Furthermore, the long-term integrity of these subsea structures demands robust monitoring systems to track performance over their operational lives against complex environmental interactions.
It's perhaps easy to view the ground or seabed solely as a static support, but the reality is far more complex. The dynamic behaviour of the soil or rock under cyclic wind and wave loads isn't uniform; its response varies dramatically depending on the geology at each specific turbine location. This variable stiffness and damping from the foundation up critically influences the dynamic characteristics and overall fatigue life of the entire turbine-foundation system, making site-specific geotechnical understanding paramount and simple 'soil class' assumptions often insufficient.
Out at sea, a particularly insidious issue is seabed scour. This erosion around the foundation base, driven by currents and waves, isn't just a matter of losing a little support; it fundamentally alters the effective fixity of the foundation and can significantly increase stresses and fatigue loading over time. While we have mitigation strategies like rock dumping or sleeves, their long-term effectiveness needs constant monitoring, and predicting the exact progression of scour at varied locations with diverse current regimes remains a challenging, ongoing effort.
Back onshore, site variability doesn't disappear; it just takes different forms. Encountering uniform, ideal soil conditions is rare. Complex stratigraphy, varying water tables, and problematic soils (like expansive clays or soft peats) mean foundations can experience long-term differential settlement. This uneven sinking can tilt the entire tower assembly, potentially introducing unforeseen eccentric loads on the structure and altering the blade-tower clearance, raising questions about the true long-term performance predictions based on initial assumptions.
For foundation types beyond the simple monopile, such as jacket structures or those using transition pieces, the interfaces and connections become particularly critical. Relying on structural grout to transfer loads between large steel components underwater is common, but assessing the long-term fatigue performance and structural integrity of this non-metallic element under complex, cyclic subsurface loading can be considerably more uncertain than the fatigue behaviour of the main steelwork itself, potentially becoming a governing constraint.
Ultimately, the foundation isn't just a static base; it's an active participant in the system's dynamic response. The interaction between the foundation's stiffness and damping characteristics and those of the tower is crucial for avoiding resonance. Getting this tuning wrong – allowing a natural frequency to align with operational frequencies like blade pass or common wave periods – can lead to drastically amplified vibrations and accelerated fatigue damage. The challenge is that different foundation solutions offer very different stiffnesses, which must be precisely matched to the specific tower design and anticipated site conditions, a complex iterative process.
Assessing Wind Energys Impact on Structural Engineering - Utilizing computational tools in contemporary wind energy structural design
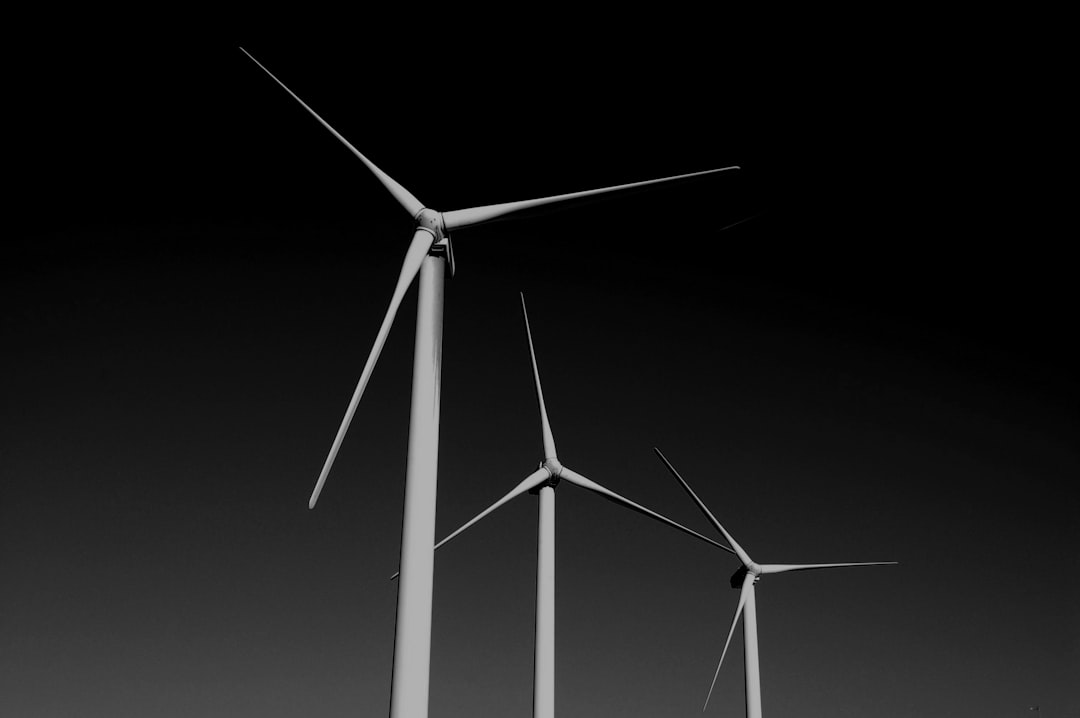
Computational approaches have become fundamental in tackling the complex structural design challenges in contemporary wind energy. This area, often broadly termed Computational Wind Engineering, involves sophisticated simulation and analysis techniques. Utilizing tools like advanced fluid dynamics simulations coupled with structural models allows engineers to predict the intricate dynamic interactions between fluctuating wind flows and turbine components, such as the tower, blades, and nacelle. This moves beyond simpler static or quasi-static assumptions to capture the full aeroelastic response critical for design validation. These computational methodologies are essential for accurately assessing structural performance under a wide spectrum of operating and extreme conditions, helping refine load predictions and evaluate long-term phenomena like cumulative fatigue damage, a key concern discussed previously. However, achieving reliable results requires rigorous verification and validation of the computational models and inputs against experimental data or real-world observations, which remains a significant area of focus and development within the field. The complexity of accurately modeling turbulent wind, highly flexible structures, and material behaviour under cyclic stress still presents notable challenges. Ultimately, the ongoing evolution and refinement of these computational tools and the practices surrounding their application are critical enablers for developing more robust, efficient, and resilient wind energy structures to meet future demands.
Stepping into the realm of structural design for wind energy today, one quickly finds that computational tools are no longer merely supplemental aids; they are absolutely central to the process. It’s remarkable how sophisticated frameworks integrating structural analysis solvers with optimization algorithms are now being leveraged. These aren't just checking a pre-conceived design; they're actively helping sculpt the structure, potentially identifying material mass savings, such as estimates of over 8% reduction in tower steel weight while still satisfying demanding safety criteria. This has tangible flow-on effects, significantly influencing manufacturing effort and complex transportation logistics, though precisely achieving these maximum predicted savings in practice often involves navigating various fabrication and site constraints.
To truly understand the long-term behaviour, especially regarding fatigue, the level of detail expected in computational analysis has become astonishingly fine-grained. Modern approaches frequently demand finite element models that zoom in to the scale of individual weld beads or meticulously account for the pre-tension states of bolts in critical flanged connections. The computational cost and effort involved in building and running models at this fidelity for a full turbine structure over a simulated operational lifetime is immense, pushing the boundaries of available computing resources.
Running these comprehensive full lifecycle simulations, particularly for large offshore turbines, illustrates another significant challenge: the sheer volume of data generated. The raw stress and load time series data can easily accumulate to multiple terabytes for just a single analysis run. Processing and extracting meaningful insights from this data mountain, crucial for probabilistic fatigue life predictions and assessing overall reliability, represents a formidable post-processing task in itself, requiring equally sophisticated data handling and analysis workflows.
The capabilities of these computational simulations have advanced to a point where they are increasingly relied upon to stand in for expensive physical prototypes and demanding full-scale structural tests, particularly when assessing behaviour under extreme conditions or complex failure modes. This accelerated virtual testing undoubtedly speeds up the design cycle and reduces some of the inherent costs and logistical hurdles associated with physical testing. However, it necessitates a significant degree of confidence in the fidelity and validation of the computational models against real-world behaviour, which is an ongoing area of research and validation rigor.
Looking ahead, the integration of Artificial Intelligence and Machine Learning algorithms directly into structural design pipelines is an emerging trend. These tools show promise in exploring vast potential design spaces far more rapidly than traditional iterative methods, or in predicting potential component degradation based on streams of structural health monitoring data with potentially increased accuracy. While exciting, integrating AI/ML into safety-critical engineering workflows requires careful consideration of explainability, validation, and the potential for unexpected outcomes, adding another layer of complexity to the computational toolkit.
More Posts from aistructuralreview.com: