Comparing Corrosion Resistance 304 vs 316 Stainless Steel in 1/2 x 2 Bolts for Structural Applications
Comparing Corrosion Resistance 304 vs 316 Stainless Steel in 1/2 x 2 Bolts for Structural Applications - Chemical Composition Differences Between 304 and 316 Stainless Steel
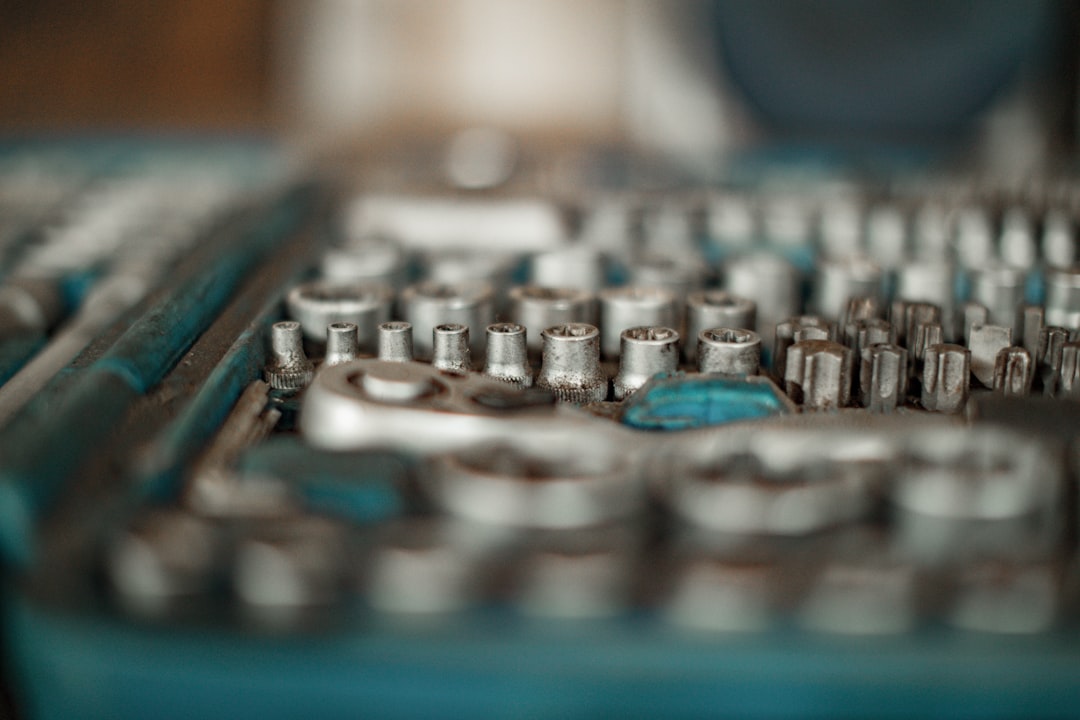
The most noticeable difference between 304 and 316 stainless steel is the presence of molybdenum in 316. This addition significantly boosts its resistance to corrosion, especially in environments with high chloride levels. This makes 316 much more suitable for applications like marine or chemical processing, where 304 might struggle. While the absence of molybdenum in 304 does make it easier to machine, its susceptibility to corrosion in harsher environments limits its usefulness in those situations. Ultimately, the specific chemical makeup of each alloy dictates where it can be used in structural applications.
The key chemical difference between 304 and 316 stainless steel is the addition of molybdenum in 316. This molybdenum content, typically around 2-3%, gives 316 significantly improved resistance to pitting corrosion, particularly in environments where chloride ions are present. This is important because chloride ions can lead to the formation of tiny pits on the surface of the metal, which can weaken the material and cause it to fail.
While both grades contain chromium (about 18%), the addition of molybdenum in 316 makes it a preferred choice in environments like marine settings or chemical processing plants, where exposure to chloride is common. The higher iron content in 304 compared to 316 might contribute to its slightly lesser performance in corrosion resistance, particularly in chloride-rich atmospheres.
The nickel content in 316 is usually higher than in 304. This not only contributes to improved corrosion resistance but also influences its ductility and formability.
When it comes to stress corrosion cracking (SCC), 316 demonstrably outperforms 304. This is largely attributed to the presence of molybdenum, making 316 the more reliable choice for critical applications in chemical processing, where SCC could lead to disastrous consequences.
Both 304 and 316 are non-magnetic in their annealed condition. However, 304 can become magnetic when cold worked, a factor to consider in applications where magnetic properties are crucial.
While 316 stainless steel is often chosen due to its superior corrosion resistance, it's also more expensive than 304. In many applications, 304 might suffice. However, for structures exposed to brine or high humidity, the additional cost of 316 may be worth it in the long run due to its extended service life.
The higher carbon content in some variants of 304 can lead to carbide precipitation when exposed to high temperatures, which can negatively affect its corrosion resistance. This issue is less common in 316 variants, making it a more reliable choice in certain applications.
In the food and pharmaceutical industries, where high cleanliness standards and sterilization compatibility are critical, 316 stainless steel is often preferred because of its superior overall corrosion resistance.
Finally, the presence of sulfur in low-sulfur variants of both stainless steels can influence their susceptibility to intergranular corrosion. This factor must be carefully considered when selecting these alloys for specific structural applications, especially those subjected to stress or high temperatures.
Comparing Corrosion Resistance 304 vs 316 Stainless Steel in 1/2 x 2 Bolts for Structural Applications - Corrosion Resistance Properties of 304 vs 316 in Chloride Environments
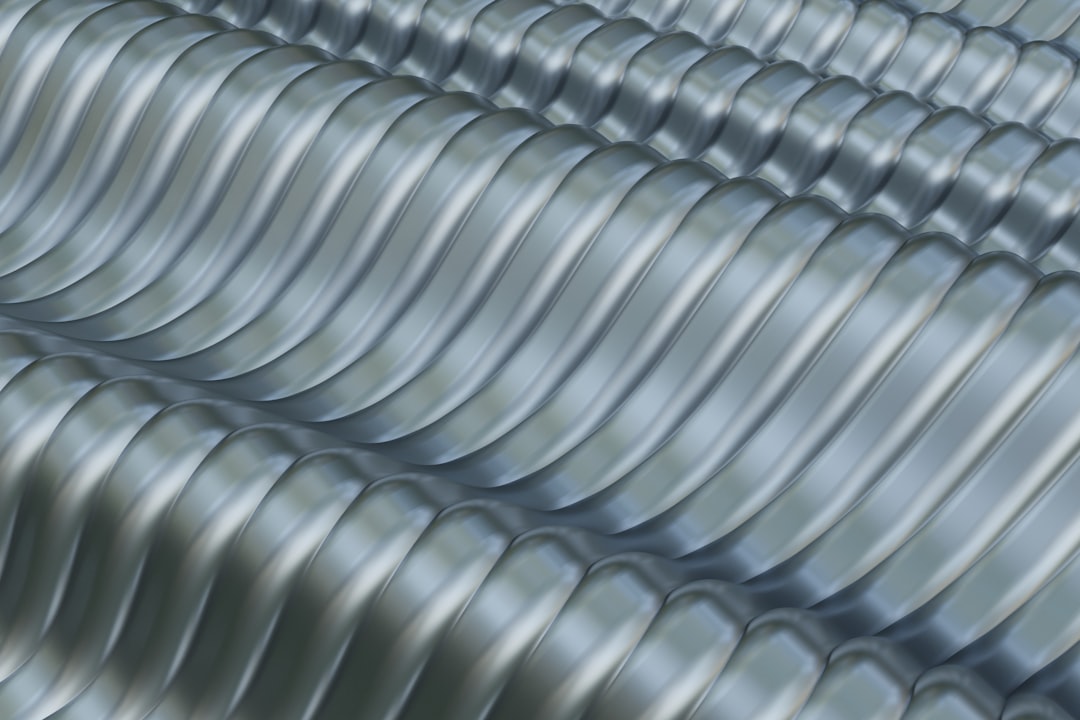
When it comes to battling corrosion in environments laden with chlorides, 304 and 316 stainless steel don't perform equally. While 304 is a solid choice in many standard situations, its lack of molybdenum puts it at a disadvantage in resisting the pitting and crevice corrosion caused by chloride ions. This makes 316 the champion when dealing with harsh environments like marine settings where constant exposure to saltwater is a reality. Despite the price difference, the extended durability and lifespan of 316 often make it the smarter choice for structural applications where reliability is paramount. It's crucial for engineers to thoroughly assess the conditions of their project to choose the best stainless steel grade for the job.
The presence of molybdenum in 316 stainless steel makes it significantly more resistant to corrosion, particularly in environments with high chloride levels. This is a critical difference when comparing it to 304 stainless steel, which lacks molybdenum and can struggle to withstand harsh conditions like those found in marine environments or chemical processing plants.
The molybdenum in 316 plays a vital role in resisting pitting corrosion, a type of localized corrosion that can weaken the material. This is crucial because chloride ions can react with the metal surface, creating tiny pits that can grow and compromise the structure's integrity.
316 stainless steel is typically chosen in applications where exposure to chloride is common, like in marine settings or chemical processing plants. Its resistance to pitting corrosion makes it a more reliable choice in such environments compared to 304, which may experience more rapid degradation due to the higher iron content.
The addition of molybdenum also enhances the resistance of 316 stainless steel to stress corrosion cracking (SCC), which is a form of cracking that can occur under stress in corrosive environments. This makes 316 a more reliable choice for load-bearing applications in demanding environments like offshore platforms, where SCC could lead to catastrophic failure.
While both grades contain chromium, the higher nickel content in 316 also contributes to improved corrosion resistance and influences its ductility and formability. This makes it more adaptable for various structural applications and might play a role in its overall resilience.
Despite its superior corrosion resistance, 316 stainless steel is more expensive than 304. While 304 might suffice for some structural applications, for structures exposed to harsh environments like saltwater or high humidity, the additional cost of 316 is often justified due to its extended service life. Choosing the right grade of stainless steel involves a careful balance of cost and performance. While 304 might seem more cost-effective initially, the potential for corrosion-induced failures and costly repairs could negate its initial price advantage in the long run.
Comparing Corrosion Resistance 304 vs 316 Stainless Steel in 1/2 x 2 Bolts for Structural Applications - Cost-Benefit Analysis for 1/2 x 2 Bolts in Structural Applications
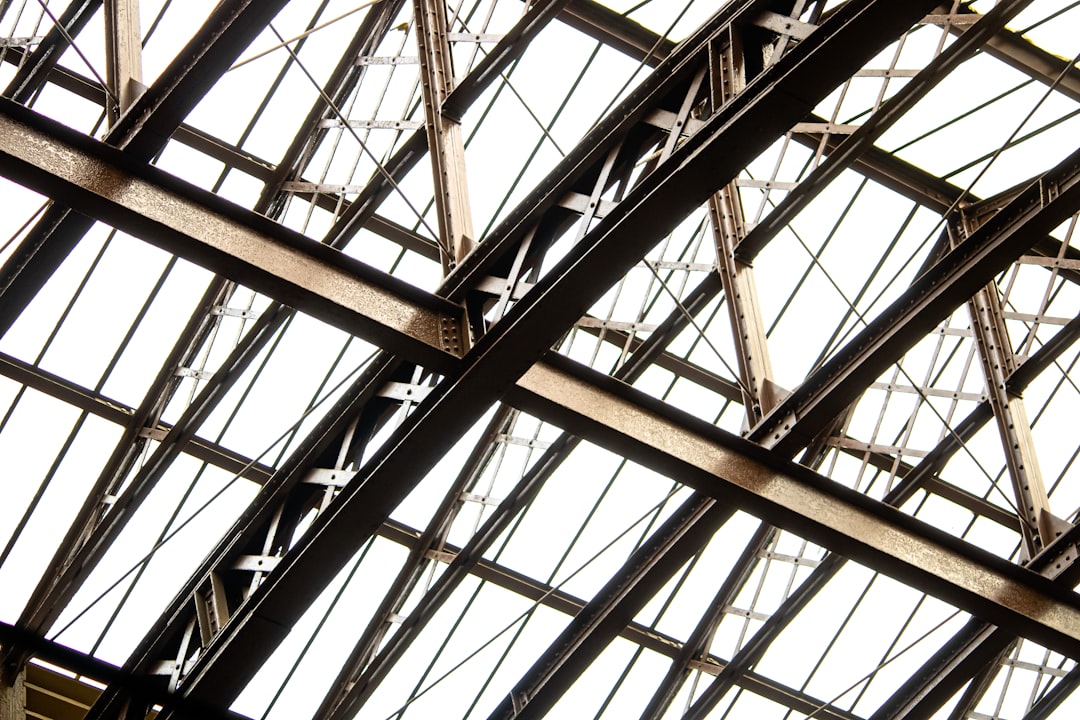
When it comes to choosing between 304 and 316 stainless steel for 1/2 x 2 bolts in structural applications, there's a trade-off between cost and performance. 304 is cheaper and generally sufficient, but it's not as resistant to corrosion as 316, especially in environments with high levels of chloride. 316, while more expensive, excels in those harsh situations, making it a better long-term investment for projects exposed to seawater or chemicals. Essentially, the decision boils down to a cost-benefit analysis – the lower initial cost of 304 might seem appealing, but the potential for corrosion-related failures and repairs could make 316 the smarter choice in the long run. The best option ultimately depends on the specific requirements and conditions of each individual project.
The choice between 304 and 316 stainless steel for 1/2 x 2 bolts in structural applications is often guided by the trade-off between cost and corrosion resistance. While 304 stainless steel is more affordable, its lack of molybdenum makes it less resistant to corrosion in chloride-rich environments, particularly in marine settings. 316 stainless steel, on the other hand, boasts superior corrosion resistance due to the presence of molybdenum.
This improved resistance comes at a higher price, but the long-term benefits, such as reduced maintenance and replacement costs, make 316 a compelling choice for critical applications. While the extra expense might seem like a drawback initially, the potential for corrosion-related failures and costly repairs could negate the initial price advantage of 304 in the long run.
Beyond corrosion resistance, it's crucial to consider other factors. The presence of molybdenum in 316 stainless steel can impact its weldability and strength, making it more challenging to weld and potentially leading to issues like hot cracking during the welding process.
In applications involving tensile stress, such as offshore structures, 316 stainless steel's higher resistance to stress corrosion cracking (SCC) is a significant advantage. However, engineers should carefully assess the specific mechanical properties of both 304 and 316 stainless steel to avoid potential over-specifications that might result in unnecessary weight and cost.
The passivation layer, a protective film formed on the surface of stainless steel bolts, also plays a crucial role in corrosion resistance. 316 stainless steel typically develops a more robust passivation layer in chloride-rich environments, further extending the service life of structural components.
Furthermore, temperature can impact the performance of both materials. While 316 stainless steel generally maintains better mechanical properties at higher temperatures, it's essential to consider the effects of thermal stress on both alloys.
The variability in nickel content between batches of stainless steel can also influence ductility and corrosion resistance. To ensure consistency, engineers should carefully consider the source of the materials and rely on reputable suppliers.
While coatings can enhance corrosion resistance, it's essential to select compatible coatings that don't negatively affect the surface of the alloy.
The manufacturing process can also impact the performance of stainless steel bolts. Cold working 316 stainless steel can enhance its strength, but it may also lead to reduced corrosion resistance if not properly annealed.
Choosing the right grade of stainless steel for structural applications requires a thorough understanding of the project's specific needs, environmental conditions, and the limitations of each alloy. By carefully considering these factors, engineers can select the best material to ensure structural integrity, long-term performance, and cost-effectiveness.
Comparing Corrosion Resistance 304 vs 316 Stainless Steel in 1/2 x 2 Bolts for Structural Applications - Temperature Performance Comparison for High-Heat Structural Uses
When comparing 304 and 316 stainless steel for high-heat applications, both alloys exhibit strong heat resistance. They can handle intermittent temperatures up to 870°C (1500°F) and continuous exposure at 925°C (1697°F). However, 304 has a melting range that's higher than 316, around 50 to 100°F higher, giving it a slight edge in extreme heat. While 316 stands out with its corrosion resistance thanks to molybdenum, its high-temperature performance is also good, especially for situations with chlorides or acids. Ultimately, choosing the right alloy depends on the specific demands of the project. You need to consider both the required temperature tolerance and the environmental conditions. Carefully examining the properties of each type helps engineers find the best option for structural integrity, durability, and long-term reliability.
When considering 304 and 316 stainless steel for high-heat structural applications, temperature performance becomes a crucial factor. While both grades boast good heat resistance, there are distinct differences in their behavior under extreme conditions.
316 stainless steel generally outperforms 304 in high-temperature environments. It can withstand intermittent use at temperatures up to 870°C (1600°F), while 304 starts to lose its mechanical integrity at temperatures above 700°C (1290°F). This makes 316 a more reliable choice for structural applications where high temperatures are involved.
The addition of molybdenum in 316 not only enhances corrosion resistance but also affects thermal expansion. Both grades have similar coefficients of thermal expansion, but even minor variations can become significant in tightly designed structures subjected to thermal cycling. While 304 might appear advantageous due to its slightly higher thermal conductivity, leading to quicker heat dissipation, 316’s higher thermal stability at extreme conditions might outweigh this benefit.
Furthermore, 304 is prone to carbide precipitation at temperatures exceeding 500°C (932°F), which can compromise its corrosion resistance. 316, on the other hand, is less susceptible to this phenomenon, making it more durable at elevated temperatures. This same principle applies to phase stability. At extreme temperatures, 316 exhibits greater resistance to changes in phase structure compared to 304, a critical factor for maintaining mechanical properties in high-stress applications.
Both 304 and 316 can be used in cryogenic applications and retain toughness at low temperatures. However, 316 shows better ductility and resistance to stress corrosion cracking under such conditions.
The differences extend beyond temperature limits. 316 displays superior oxidation resistance compared to 304 in high-temperature environments, an advantage in heat exchangers and chemical processing where scaling can occur. When it comes to heat treatments, both can be hardened, but 304 is more prone to warping or distortion due to its higher carbon content. High-temperature environments can also accelerate stress fatigue, but 316's higher nickel content makes it more resilient, suitable for load-bearing structures subjected to cyclical thermal and mechanical stresses.
Weldability also becomes a factor. While 304 is often preferred for its ease of welding, 316 demands more careful consideration in high-temperature applications to avoid hot cracking. It’s a significant factor in construction where precision is crucial.
Ultimately, the decision between 304 and 316 for high-heat structural applications requires a meticulous assessment of specific project needs, environmental conditions, and temperature performance expectations. It’s not merely about selecting the cheaper option but understanding the trade-offs inherent in each grade and choosing the one that provides the best combination of performance, longevity, and cost-effectiveness.
Comparing Corrosion Resistance 304 vs 316 Stainless Steel in 1/2 x 2 Bolts for Structural Applications - Machining Characteristics and Fabrication Considerations
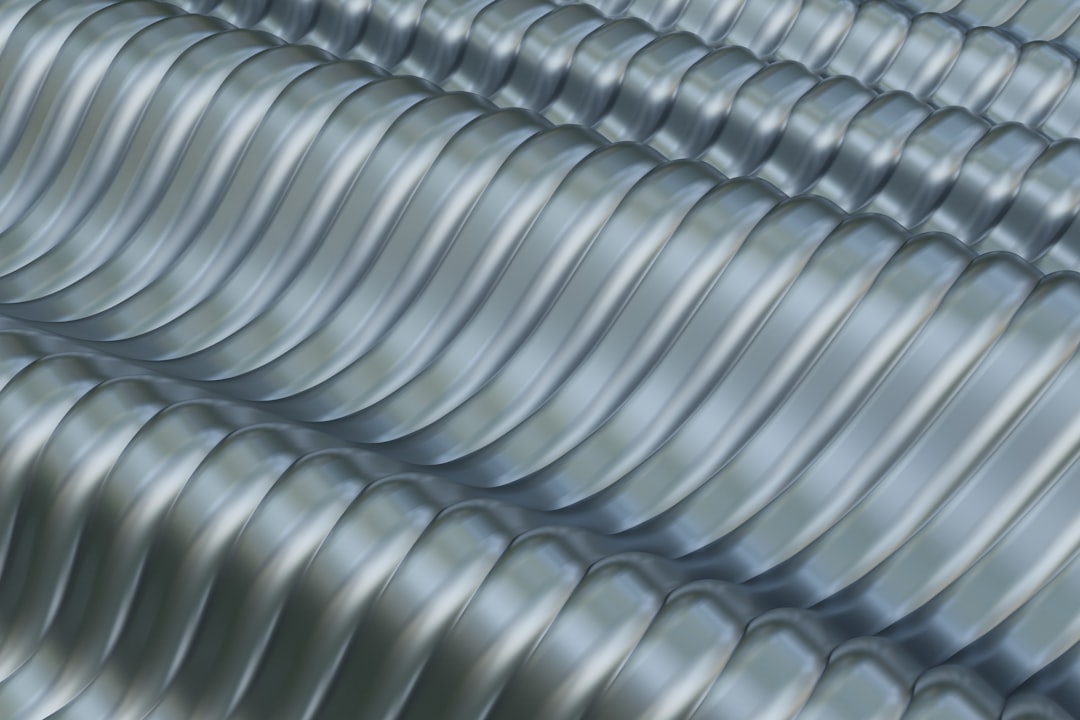
The choice between 304 and 316 stainless steel for structural applications often hinges on the ease of fabrication. While 304 is generally easier to machine due to its softer nature, 316 presents more of a challenge due to its higher hardness and the presence of molybdenum. However, this added difficulty in machining is compensated by 316's superior resistance to wear and corrosion, making it a more suitable option for demanding environments. This trade-off between ease of fabrication and performance is crucial for engineers to consider when choosing the appropriate stainless steel grade for their projects. Ultimately, the decision relies on a balance between cost and the required performance in the specific application. While 304 may be appealing for its lower cost, the added durability and resistance of 316 could be invaluable for long-term performance and maintenance, especially in harsh or high-stress applications.
The choice between 304 and 316 stainless steel goes beyond just corrosion resistance, and delves into their machinability and fabrication aspects. 304, without molybdenum, is generally easier to machine, making it more cost-effective in some manufacturing processes. However, the enhanced wear resistance of 316 can prove beneficial for components with longer service life requirements.
Heat treatment reveals another facet of their differences. While 304 is more susceptible to issues like carbide precipitation at higher temperatures, 316 remains more stable. This makes 316 a better option for applications involving significant heat exposure.
The surface finish of a stainless steel component significantly impacts its resistance to corrosion. 316, due to its composition, tends to develop a more robust oxide layer compared to 304. This makes the finishing process even more critical in specifying materials for demanding applications.
Furthermore, 304 is more vulnerable to intergranular corrosion, particularly after welding, if not properly heat treated. 316, however, mitigates this risk, providing greater reliability in welded structures.
Interestingly, cold working 304 can boost its strength but might also alter its magnetic properties due to the change in its microstructure. Cold working 316 has a lesser effect on its magnetism, a critical consideration in applications demanding non-magnetic properties.
The molybdenum in 316 not only enhances resistance to chlorides but also extends its protection against other corrosive substances such as sulfuric acid. This makes it a superior choice for chemical processing environments facing highly aggressive conditions.
In applications where cyclical loads are present, 316 showcases superior fatigue resistance compared to 304. This is critical for structural applications where components are subjected to repeated stresses over time, potentially causing failure.
While both grades exhibit good tensile strength, 316 tends to retain higher strength levels at elevated temperatures. This is crucial for components in environments where thermal stresses are expected.
The variability in nickel content in 316 can impact its ductility and workability. This inconsistency needs to be addressed during specification to ensure consistent performance in the final product.
Although 304 is often easier to weld, 316 demands more careful procedures to avoid hot cracking. The presence of molybdenum can complicate the welding process and necessitate qualified welding techniques for structural integrity.
Ultimately, choosing between 304 and 316 goes beyond just their cost. A thorough understanding of the project's specific needs, the environmental conditions, and the limitations of each material is necessary for informed decision-making. This ensures the optimal combination of performance, longevity, and cost-effectiveness in the final structure.
Comparing Corrosion Resistance 304 vs 316 Stainless Steel in 1/2 x 2 Bolts for Structural Applications - Long-Term Durability Expectations in Various Environmental Conditions
The long-term durability of 304 and 316 stainless steel hinges heavily on the specific environmental conditions they face. 316, thanks to its molybdenum content, demonstrably outperforms 304 in harsh environments with high chloride levels, particularly in marine or coastal settings. While 304 is perfectly suitable for a wide range of industrial applications, its susceptibility to corrosion can become a major issue in aggressive environments. Choosing between the two depends on a careful assessment of the long-term exposure conditions. The cost of maintenance and potential replacement due to corrosion-related failures should also be weighed in. Choosing the right alloy is critical for ensuring a structure's long-term performance and reliability.
While both 304 and 316 stainless steel have their place in structural applications, the long-term durability expectations can differ significantly based on the specific environment and intended use. 316, with its molybdenum addition, offers clear advantages in many situations, especially when considering long-term performance.
For example, 316 exhibits exceptional resistance to pitting corrosion in chloride-rich environments like marine settings, with studies indicating it can withstand saltwater exposure for a much longer duration than 304. This is crucial for structures requiring long-term integrity in harsh conditions.
While both alloys can withstand high temperatures, 316 demonstrates better corrosion resistance at elevated temperatures, making it a superior choice for applications prone to stress corrosion cracking (SCC) under high heat. This is especially pertinent in industries like aerospace, where components are subjected to extreme thermal cycling.
The microstructures of these alloys also play a role in long-term durability. 304, despite its general machinability, can experience intergranular corrosion after welding due to the formation of chromium carbides. This issue is less common in 316, making it more dependable in welded applications where long-term structural integrity is crucial.
Further, while both alloys share similar thermal expansion properties, 316 retains its strength better at high temperatures. This translates to better performance in structures subjected to thermal cycling, highlighting its potential in areas like aerospace engineering.
Another area where 316 stands out is oxidation resistance. When exposed to extreme temperatures, it exhibits better oxidation resistance than 304, which is essential in applications like chemical reactors and heat exchangers where scale build-up can affect performance.
Furthermore, while cold working can enhance 304’s strength, it also makes it more prone to becoming magnetic, which might pose problems in sensitive environments. 316 retains its non-magnetic properties better, making it more suitable in situations where magnetic fields are a concern.
When considering fatigue resistance, 316 surpasses 304, largely due to its higher nickel content. This is particularly relevant in infrastructure and transportation systems where components face fluctuating loads.
Looking at long-term heating effects, 316 retains a more stable microstructure under prolonged thermal stress. This characteristic makes it more resilient than 304 in high-performance applications, where the structural integrity needs to withstand prolonged heat exposure.
Both alloys can be vulnerable to intergranular corrosion, but 316 demonstrates better resistance, particularly in post-weld scenarios. This is vital for critical structural applications where failure could be catastrophic.
Finally, 316's lower ductility can present challenges in additive manufacturing techniques compared to 304. However, its superior corrosion resistance often makes it the preferred choice despite the fabrication complexity.
In conclusion, 316 stainless steel offers a robust long-term performance profile in various applications. While its higher cost may be a consideration, its superior corrosion resistance, temperature performance, and resistance to microstructural changes make it a more dependable option in demanding environments. However, it's essential for engineers to carefully consider the specific project demands and choose the alloy best suited for the intended application.
More Posts from aistructuralreview.com: