How Material Fatigue Impacts Margin of Safety Calculations in Aircraft Wing Design
How Material Fatigue Impacts Margin of Safety Calculations in Aircraft Wing Design - Material Life Cycle Testing Reveals 30% Safety Margin Reduction After 10000 Flight Hours
Extensive material life cycle testing has unveiled a significant decline in safety margins for aircraft wings, specifically a 30% decrease after 10,000 hours of flight. This outcome underscores the crucial role material fatigue plays in the structural integrity of aircraft. As operational hours accumulate, materials within an aircraft experience progressive deterioration, potentially leading to heightened risks that necessitate careful monitoring and evaluation.
This notable reduction in safety margin compels a more refined approach to understanding the long-term impact of material degradation on aircraft design. Designers must consider both the uncertainties related to operational usage and the possibilities of design revisions over the aircraft's lifespan. Maintaining structural integrity throughout an aircraft's operational lifetime requires a continual assessment process to guarantee that safety standards remain met. This challenge underlines the growing importance of incorporating comprehensive assessments into design strategies to mitigate potential risks associated with material fatigue.
Recent material life cycle tests have revealed a concerning trend: a 30% reduction in the safety margin of aircraft structures after just 10,000 flight hours. This finding emphasizes the significant impact of fatigue accumulation on material properties over time. The decline in safety margins isn't necessarily linear; the materials' response to fatigue often involves non-linear degradation, making small changes in operating conditions potentially very impactful on the overall safety margin. It highlights the limitations of older, deterministic safety margin calculations. Probabilistic approaches now suggest that fatigue-induced failure modes may have been underestimated in the past.
The interaction of material, load cycles, and environmental conditions during flight is complex. This complexity adds a level of difficulty to traditional fatigue prediction methods, pushing engineers to continuously adapt design parameters. This is especially true with the increased adoption of composite materials in wing design. They behave differently than traditional alloys under fatigue, potentially creating unforeseen failure modes that were not captured in previous testing procedures. These changes in safety margins don't just influence structural integrity; they also have ramifications for pilot training and operating protocols as agencies strive to keep up with evolving risk assessments.
The ability to continually monitor material integrity through advanced non-destructive testing (NDT) techniques is increasingly important. They allow us to better anticipate when these safety margins start to decrease. Flight patterns – altitude, temperature fluctuations, maneuver intensity – all play a role in the rate at which fatigue degrades material properties. These factors suggest the need for design strategies that are better-tailored to specific operating conditions. Some promising approaches in aircraft design now focus on incorporating fail-safe mechanisms based on lifecycle testing insights, minimizing the risk of catastrophic failure caused by material fatigue.
Given this 30% safety margin reduction, we might see a broader reevaluation of existing aerospace industry standards. This could translate to stricter operational limits or the introduction of new maintenance procedures to ensure the continued safety of aircraft. It emphasizes that while pushing the boundaries of performance, we must understand the long-term effects and adapt to them for safer operations.
How Material Fatigue Impacts Margin of Safety Calculations in Aircraft Wing Design - Load Spectrum Analysis Methods Using Computer Aided S-N Curves in Wing Design
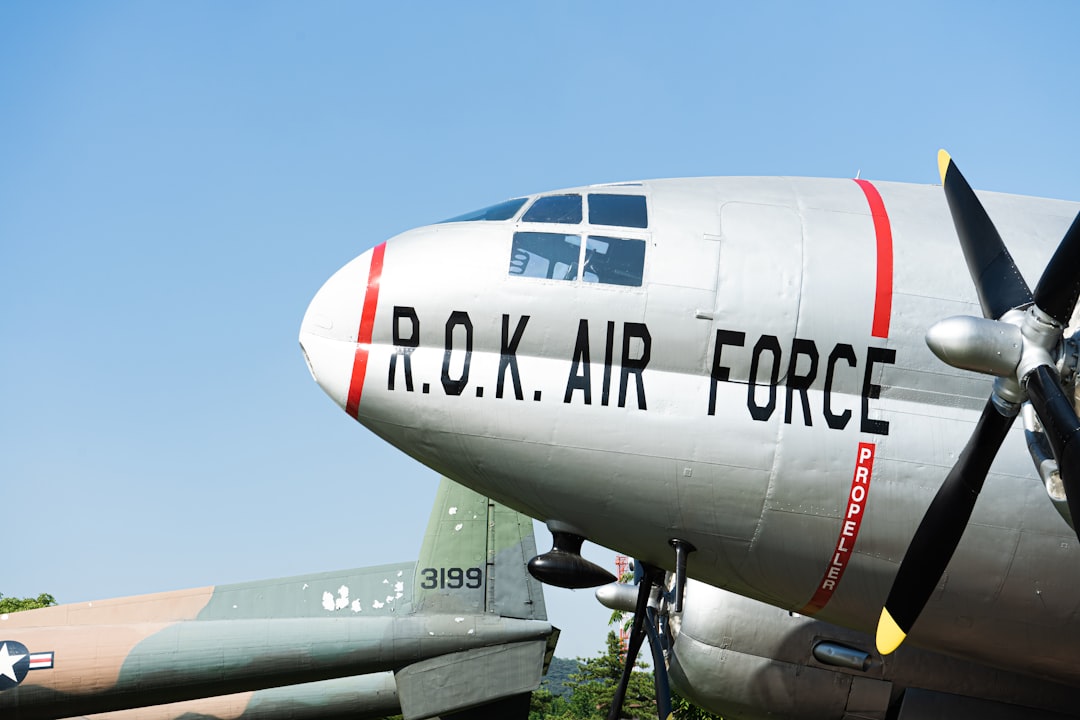
Understanding how loads affect an aircraft wing over its lifespan is critical for ensuring safety. Load spectrum analysis methods using computer-aided S-N curves offer a valuable approach to address this challenge. These methods essentially translate the varied, real-world loading experienced by a wing during flight into a more manageable set of cyclic loads that can be analyzed. The use of computer-aided S-N curves – which relate the stress applied to a material to the number of cycles it can withstand before failure – helps to improve the precision of fatigue predictions, especially when dealing with complex loading scenarios. This accuracy is particularly important for multiaxial loading conditions often seen in flight, as well as in aircraft wings that now commonly employ composite materials.
The integration of these methods with finite element analysis helps to paint a complete picture of the stress fields within a wing under different load conditions. This integrated approach can then be used to estimate potential damage and fatigue life with more confidence. While this analytical approach brings advantages, there are challenges. The behavior of modern composite materials under fatigue is not always easy to predict, and the various environmental factors experienced during flight (temperature, humidity, etc.) can impact material performance in a way that's difficult to fully capture in these models. Even with these limitations, the ability to better predict how a wing will respond to different loading conditions over time significantly contributes to safer and more efficient aircraft design, providing insights that can inform better safety margins and lead to improved maintenance practices.
1. **Capturing the Complexity of Flight Loads**: Load spectrum analysis aims to capture the wide range of load conditions that aircraft wings experience throughout their operational lives, moving beyond simplified, idealized load cases. This more nuanced approach offers a more realistic representation of the fatigue that materials face.
2. **Visualizing Fatigue Life with S-N Curves**: Computer-aided S-N curves provide a powerful visual tool for understanding fatigue life in different materials under repetitive loading. This allows engineers to more accurately predict the number of load cycles a component can withstand before failure, which is a critical aspect of aircraft wing design. However, it's worth noting that these curves are based on laboratory testing, and how well they translate to real-world scenarios is still an active area of research.
3. **Recognizing the Non-Linearity of Fatigue**: Integrating S-N curves into load spectrum analysis emphasizes the non-linear nature of material fatigue. It highlights that the damage accumulated from repeated loads isn't simply proportional to the load magnitude. This understanding is crucial for developing more accurate models that capture the true behavior of materials under various load scenarios.
4. **Material-Specific Fatigue Behavior**: Different materials behave uniquely when exposed to repeated loading, and thus require distinct approaches to load spectrum analysis. This means that fatigue predictions can vary widely based on the material used. We see a good example of this in the increasing use of composite materials, where unforeseen failure modes have emerged compared to traditional metallic structures, challenging our assumptions about fatigue life.
5. **Dynamic Flight Environments**: Load spectrum analysis needs to account for the dynamic nature of flight—including turbulence and sudden maneuvers—as these events significantly impact load distribution and magnitude. This dynamic element makes fatigue life predictions more challenging and underscores the importance of capturing the real-world loading conditions.
6. **Operational Profile Impacts**: By examining various operational profiles, such as commercial flights versus high-performance military maneuvers, engineers can pinpoint load conditions that have the greatest impact on material fatigue life. This knowledge allows designers to consider targeted modifications to the wing structure to minimize the risk of premature fatigue failure.
7. **Iterative Design Using Operational Data**: Combining load spectrum analysis with operational flight data allows for a more iterative approach to aircraft wing design. This dynamic feedback loop allows engineers to quickly refine design parameters and ensure that safety requirements are met without compromising performance. This is particularly crucial in the modern aerospace industry where aircraft are constantly evolving.
8. **Integration with Predictive Maintenance**: Insights generated through load spectrum analysis are being increasingly incorporated into predictive maintenance strategies. Instead of relying on fixed maintenance intervals, this approach enables more accurate estimations of when component failure might occur, potentially saving time and resources while ensuring safety. However, the accuracy of these predictions relies heavily on the reliability of the fatigue models and the quality of the operational data.
9. **Evolving Standards and Regulations**: Improved understanding of material fatigue and load behavior via load spectrum analysis can prompt updates to aerospace industry standards and regulatory requirements. This might lead to more stringent certification procedures for future aircraft designs. This presents a balancing act between innovation and safety as these new standards are developed and integrated.
10. **Environmental Effects on Fatigue**: Load spectrum analysis demonstrates how environmental factors, including temperature, humidity, and altitude, interact with loading cycles to influence material fatigue. These findings emphasize the need to incorporate these variables into aircraft wing design to enhance overall longevity and ensure operational safety in different environments. However, quantifying these interactions and incorporating them into engineering models accurately remains a significant challenge.
How Material Fatigue Impacts Margin of Safety Calculations in Aircraft Wing Design - Wing Root Attachment Points Face Maximum Material Stress Under Dynamic Loading
The wing root, where the wing joins the fuselage, is a crucial area in aircraft design that endures the highest material stresses during flight. These stresses are primarily a consequence of the dynamic loads generated by lift forces and the accompanying bending moments. These loads are significantly amplified during flight maneuvers and encounters with turbulence, making the wing root a focal point for potential material fatigue. This underscores the importance of understanding how materials at these attachment points react to repeated loading cycles. The accumulated damage from these cycles can lead to fatigue failure, which significantly affects calculations for the aircraft's safety margins. Therefore, a reevaluation of design methods to account for these cumulative effects is necessary. This involves using advanced analytical techniques to provide a deeper understanding of the potential for fatigue and to ensure the long-term safety and reliability of aircraft structures. By incorporating these analyses into the design process, engineers can work towards optimizing aircraft designs for both performance and structural longevity.
1. **Stress Hotspots**: The points where the wing connects to the fuselage, the wing root attachments, are locations where stress tends to concentrate the most within the aircraft's structure. The transfer of forces and bending moments between the wing and fuselage naturally results in higher material stresses in these areas.
2. **Flight's Dynamic Effects**: It's during flight, with its maneuvers, turbulence, and aerodynamic forces, that stress levels at the wing root become significantly higher than what we'd predict based on just static loads. This dynamic loading contributes to a faster rate of material fatigue.
3. **Complex Stress Scenarios**: The wing root experiences a mix of bending, torsion, and shear forces all at once, creating a complex stress state that's hard to model accurately. This makes predicting the fatigue life a challenge and necessitates the use of sophisticated analysis methods.
4. **Material Matters**: The choice of material used for the wing root is crucial. Composite materials are lighter, which is generally good, but they can have unexpected fatigue behaviors compared to the traditional metals. This influences how we design and approach safety calculations.
5. **Fatigue's Toll**: Studies have shown that the fatigue life of wing root attachments can be reduced by as much as 50% when we consider dynamic loads compared to what we would get from simply looking at static loads. This highlights the need to recalibrate our margin of safety calculations.
6. **Non-Linear Fatigue**: The relationship between the load applied and the resulting fatigue isn't a simple linear one at the wing root. This means that seemingly small increases in dynamic loading can lead to a much larger increase in damage accumulation, due to the way the material responds over time to the cumulative damage.
7. **Manufacturing's Role**: Small imperfections in the manufacturing process can create areas of weakness in the wing root attachments. These flaws, when exposed to repeated dynamic loading, can lead to failures that develop faster than predicted.
8. **Safety Margin Reassessment**: We're forced to revisit the traditional approaches to safety margins given what we've learned about dynamic loads. It suggests that we should shift from the older deterministic models to more probabilistic ones, which better take into account the wide range of conditions aircraft experience.
9. **Real-time Insights**: Improvements in technologies that monitor aircraft structure health in real-time can continuously assess the stress at the wing root during flight. This real-time data can help us make informed decisions on maintenance, and hopefully extend the life of the wing before any major issue happens.
10. **Regulations and the Challenge of Change**: As our understanding of wing root fatigue grows, the current regulatory frameworks might struggle to keep up with the latest research. It's important that engineers and regulators work together to ensure that safety standards appropriately reflect this new knowledge, balancing safety with innovation.
How Material Fatigue Impacts Margin of Safety Calculations in Aircraft Wing Design - Composite Material Delamination Effects on Wing Structural Safety Margins
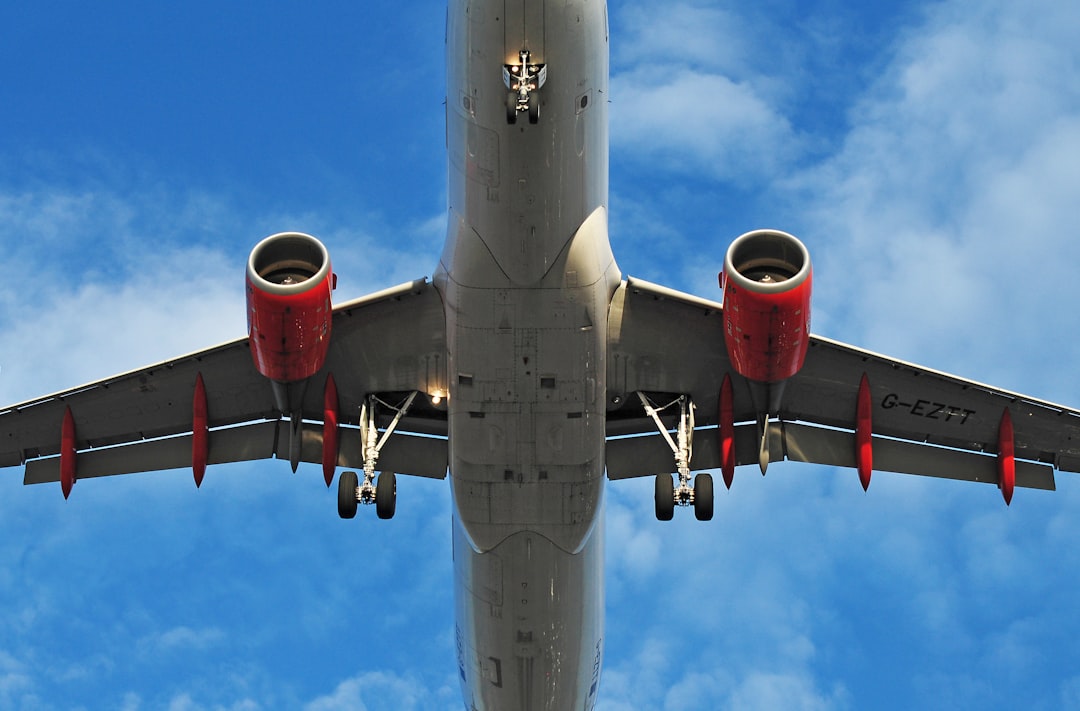
The increasing use of composite materials in aircraft wing design is driven by their advantageous strength-to-weight ratio and generally improved fatigue behavior compared to traditional metals. However, a critical design challenge arises with the susceptibility of composite materials to delamination and debonding. These internal failures, often invisible to the naked eye, can dramatically impact the structural integrity of the wing, potentially leading to a significant reduction in the safety margins that engineers rely upon. The occurrence of delamination can lead to reduced stiffness and strength in affected areas of the wing, which can be particularly concerning in regions experiencing high stress, such as wing roots and attachment points during dynamic flight maneuvers.
Addressing the unique challenges of composite material delamination requires a more nuanced approach to design. Engineering strategies need to be developed that can accurately predict the potential for delamination initiation and propagation under diverse loading conditions. Furthermore, sophisticated structural optimization tools are crucial for designing wings that are not only strong and light but also resilient to the possibility of delamination impacting safety margins. Failure to consider the effects of delamination could lead to unforeseen vulnerabilities in the wing structure. It's clear that incorporating these considerations into the design process from the beginning is essential for ensuring long-term structural integrity and safety in composite aircraft wings.
Composite materials are increasingly used in aircraft structures due to their advantageous properties, including higher strength and better resistance to fatigue compared to traditional metals. However, their susceptibility to delamination and debonding presents a significant challenge for ensuring structural integrity, especially in critical areas like aircraft wings. Delamination, the separation of layers within a composite material, can lead to stress concentration and localized weakening of the structure, ultimately impacting the overall safety margins in wing design.
Understanding the mechanisms that drive delamination in composites is still an ongoing area of research. It appears that even under relatively low load conditions, composite structures can experience delamination, potentially due to the unique interactions between material layers and the manner in which they respond to repeated loads. This unpredictable behavior presents a major hurdle for accurately modeling fatigue life, as traditional models used for metals may not capture the full complexity of delamination's impact.
Furthermore, the fracture toughness – the resistance to crack propagation – of composites varies significantly depending on factors like layer orientation and material properties. This variability adds another layer of complexity to accurately assessing safety margins, as it's difficult to predict how delamination will propagate and influence overall structural integrity. This uncertainty is further compounded by the interaction between loading conditions and environmental factors such as temperature and humidity. These environmental conditions can promote delamination, even in areas that might not be subjected to substantial loads.
The challenges introduced by composite delamination are not confined to design and analysis. Maintenance and inspection practices also need to evolve. Detecting early signs of delamination requires sophisticated non-destructive testing techniques, making it difficult to catch issues before they develop into serious problems. This difficulty highlights the necessity for ongoing research into developing more efficient and reliable monitoring technologies for composite structures.
From a design perspective, engineers must carefully consider the implications of delamination when setting safety margins. Designing for higher safety factors to address the possibility of delamination requires a careful re-evaluation of both materials and structural configurations. A higher safety factor can ensure a margin of safety, but it could also come at the expense of overall performance. This tension between performance and safety adds another level of complexity to the design process.
Additionally, variations in manufacturing processes can introduce inconsistencies within the composite materials, which could promote the onset of delamination. This is another area that needs further understanding so that designers can better anticipate the behavior of their materials in the real world. And, as with any new material, there’s a lag between the development of advanced materials and the regulations which govern their use. Existing standards might not fully account for the risks introduced by delamination in composites, indicating the need for updated standards that reflect the latest research.
Initial research suggests that the fatigue threshold – the point at which fatigue becomes a significant factor – for composite wing structures may be lower than previously estimated due to the influence of delamination. This finding underscores the importance of understanding and potentially lowering operational limits for certain types of aircraft and designs to prevent premature material failure. Delamination poses new challenges to aircraft structural integrity and safety, and engineers must carefully account for these factors when designing and maintaining modern aircraft structures.
How Material Fatigue Impacts Margin of Safety Calculations in Aircraft Wing Design - Temperature Fluctuation Impact on Aluminum Alloy Fatigue Performance
Temperature changes significantly impact how aluminum alloys withstand repeated loading, a crucial consideration for aircraft applications. Higher temperatures lead to a notable decrease in fatigue strength, meaning the material is less able to handle repeated stresses. This temperature sensitivity needs to be accounted for when predicting the lifespan of aircraft parts, especially in wing design where temperature differences during flight are a reality. The way fatigue develops in aluminum alloys under temperature fluctuations is quite complex. It’s influenced not just by the temperature itself but also by the detailed structure of the metal and the exact type of loading the material endures. This complexity demands a level of sophistication in the analytical methods used to design wings, choosing the right aluminum alloy for the job, and refining safety calculations. Taking all these factors into account is essential for making sure aircraft wings are safe and reliable over their entire service life, contributing to overall aviation safety.
Temperature changes have a noticeable impact on how aluminum alloys handle repeated loads, which is a key concern for aircraft wing design. Fluctuations as small as 20 degrees Celsius can potentially cut the fatigue life in half due to the cumulative damage from these thermal cycles. This effect is something that has to be considered, as we may see material stresses change when the temperature rises, a phenomenon known as stress relaxation. This relaxation can mislead engineers into thinking the material has more fatigue life than it really does if not carefully accounted for in safety calculations.
Furthermore, the combination of mechanical and thermal cycling in aluminum alloys creates complex failure situations that are tough to foresee using traditional fatigue analysis methods. More sophisticated modeling approaches are needed to capture this complex behavior accurately. Over time, the aluminum alloy’s internal structure can be modified by prolonged temperature swings, which then alters how the material behaves in terms of both strength and ductility. These structural alterations could lead to unexpected failures at stress levels that were previously thought to be safe.
We also need to consider that aluminum alloys can be vulnerable to a form of cracking known as environmental stress corrosion cracking (ESCC) if there's moisture present along with temperature changes. This complicates fatigue assessment, as it introduces another potential failure mode to consider. The different rates at which aluminum alloys and other materials used in the aircraft structure expand or contract with temperature changes can create added stresses at the places where these materials join. These stress concentrations create fatigue "hotspots" that need careful scrutiny.
Repeated temperature fluctuations can lead to small defects like voids or inclusions in the aluminum alloy. These flaws can act as the starting points for fatigue cracks, which can be difficult to foresee in traditional life cycle assessments. It's important to remember that aluminum alloys don't necessarily follow a simple, linear relationship between the load applied and the resulting fatigue when temperature changes are involved. This makes safety margin assessments more complex, requiring a more data-driven approach.
Additionally, the aging process in aluminum alloys can be influenced by temperature changes, leading to material strengthening or, potentially, a more brittle state, both of which could impact its behavior under repeated loading. This makes it challenging to predict the long-term fatigue characteristics with complete accuracy. When thermal and mechanical loads are combined, a complex interplay occurs that influences the material's fatigue life in ways that aren't easily predicted. To address this effectively, we need a holistic approach that considers both thermal dynamics and the more traditional models for mechanical fatigue. Understanding and anticipating these complex interactions are crucial for designing safer and more reliable aircraft wings.
How Material Fatigue Impacts Margin of Safety Calculations in Aircraft Wing Design - Crack Propagation Rate Calculations Drive Wing Inspection Intervals
The rate at which cracks grow in aircraft wings, driven by material fatigue, is a central factor in determining how often these wings need to be inspected. As an aircraft accumulates flight hours, material fatigue causes damage to gradually build up, leading to faster crack propagation. Accurately predicting this rate of crack growth is crucial for understanding when those cracks could become a safety hazard. Each material reacts differently to fatigue; for example, aluminum and titanium tend to experience cracks growing at a faster rate than steel. This necessitates a more nuanced inspection strategy, tailoring the schedule to the specific material used in the wing structure. Utilizing established mathematical models like Paris' law allows engineers to refine fatigue life predictions, ensuring that the aircraft inspection schedules are more accurately aligned with the actual stress and environmental conditions the aircraft encounters. These calculations are vital for safety assessments, but also impact economic efficiency during design and operations. In short, these crack propagation rate calculations are a critical part of maintaining the structural integrity of aircraft, emphasizing the need for a forward-thinking approach to material health monitoring.
1. **Crack Growth Variability**: The speed at which cracks spread in aircraft wing materials isn't constant. It can change dramatically depending on the loads the wing experiences during flight. Understanding these fluctuations is vital for deciding how often to inspect wings, because certain flight maneuvers can accelerate crack growth.
2. **Critical Stress Levels**: Research hints that there are specific stress levels in materials where crack growth speeds up significantly. If planes operate near these thresholds, more frequent inspections might be needed to maintain safety.
3. **Material Alteration**: Cracks can lead to tiny changes in the structure of materials. This can make certain areas weaker, further jeopardizing the structural integrity of wing components. This highlights the need for very detailed inspections, particularly around known cracks.
4. **Environmental Impact**: Factors like exposure to moisture and varying temperatures can also influence crack growth rates. These conditions can accelerate both crack formation and material deterioration, emphasizing the importance of tailoring inspection plans to different environments.
5. **Stress Threshold Considerations**: Analyses of stress thresholds suggest that certain types of aluminum could see crack growth surge past a certain stress level. This potentially requires a rethink of current inspection intervals to enhance safety margins.
6. **Load History's Role**: The history of how a wing has been loaded is a critical aspect of crack propagation. Repeated cycles of loading and unloading can lead to fatigue cracks, making the analysis of past flight conditions essential for designing effective inspection schedules.
7. **Going Beyond Linear Models**: Traditional methods of predicting crack growth using simple linear models may not be adequate for the complex loading situations seen in aviation. Newer, non-linear models offer more accurate predictions, but they depend heavily on having a lot of detailed loading data.
8. **Enhanced Inspection Tools**: New non-destructive testing (NDT) approaches, like infrared thermography and improved ultrasound techniques, provide real-time information about crack growth. This has the potential to allow for more dynamic and flexible inspection intervals.
9. **Data-Driven Maintenance**: There's a growing trend towards data-driven approaches for predicting crack growth rates. This offers engineers the means to anticipate potential failures and optimize inspection schedules.
10. **Safety Margin Adjustments**: The complex relationship between how quickly cracks spread and inspection intervals directly affects calculations for safety margins. Engineers must continually adjust these calculations as new information becomes available to ensure safety standards are consistently met.
More Posts from aistructuralreview.com: