Engineering Marvel Inside Venezuela's Mukumbar Cable Car System - World's Highest Aerial Tramway at 4,765m Above Sea Level
Engineering Marvel Inside Venezuela's Mukumbar Cable Car System - World's Highest Aerial Tramway at 4,765m Above Sea Level - Technical Design Parameters Behind 4,765m Height Achievement
The Mukumbar Cable Car's achievement of 4,765 meters above sea level is a testament to clever engineering solutions tailored to the unique challenges of high-altitude environments. The system's stability in the face of strong winds is significantly attributed to its Y-shaped buttressed core design, a novel approach that contributes to structural resilience. Further emphasizing the commitment to robustness, the construction employed an enormous quantity of concrete – over 110,000 tons – ensuring the system's durability. To withstand the weight and potential environmental pressures at this extreme elevation, the engineers incorporated a foundation consisting of 192 deep piles. This intricate base provides a secure and stable foundation for the entire structure. While primarily a transportation solution for remote regions, this project highlights the potential of engineering to surmount geographical challenges and establish a new standard in high-altitude transport. It serves as a beacon demonstrating that ambitious transportation solutions can be successfully realized, even in the most demanding conditions.
The Mukumbar Cable Car's operation at such extreme altitudes presents unique engineering challenges. For example, the reduced atmospheric pressure at 4,765 meters significantly affects the performance of materials like the cables, necessitating careful selection and design. The system compensates for this by employing specially designed sheave wheels and pulleys. These components manage the increased tensile forces caused by altitude, minimizing stress on critical parts.
Safety is paramount, and the design reflects this. It integrates multiple redundant braking systems, utilizing both hydraulic and mechanical methods. This ensures that, in the event of a single system failure, the cabin can still stop safely, relying on alternative means.
Temperature variations are pronounced at high altitudes and need careful management. The design accounts for thermal expansion and contraction, particularly within steel cables and aluminum support structures. These components must be able to accommodate the significant lengthening and shortening caused by temperature fluctuations without compromising structural integrity.
The harsh environment accelerates wear and tear on materials. To mitigate this, the Mukumbar Cable Car system incorporates monitoring systems. These systems continuously track wear rates and performance metrics, providing valuable insights for scheduling maintenance interventions and ensuring continued optimal performance.
High altitudes also exacerbate the impact of wind loads. The system addresses this by implementing a specially engineered anchoring system. It secures the towers against extreme wind forces, safeguarding structural stability and protecting passenger safety.
To optimize design and understand the system's behavior, engineers employed sophisticated computational tools. Finite element analysis simulations predicted how the cable car would respond to various operating conditions. This included passenger loads and environmental factors such as snow and ice accumulation, allowing for proactive engineering solutions.
The cable car's control systems play a key role in maintaining stability and passenger comfort. The systems are equipped with advanced algorithms that can respond in real-time to changes in environmental conditions. They adjust speed and torque dynamically to maintain stable operation.
Construction at such elevations presented considerable logistic hurdles. Specialized equipment was essential for transporting and placing large, heavy components. Specialized cranes and helicopter lifts were employed to address the challenging terrain and limited accessibility.
Maintaining the Mukumbar Cable Car in such a demanding environment requires a highly structured approach. The system incorporates a carefully planned maintenance schedule based on data analytics. Regular inspections and component replacements are implemented to ensure high reliability and operational safety despite the extremely challenging conditions.
Engineering Marvel Inside Venezuela's Mukumbar Cable Car System - World's Highest Aerial Tramway at 4,765m Above Sea Level - Five Stage Journey From Mérida Base Station to Pico Espejo Peak
The journey from the base station in Mérida to the summit of Pico Espejo unfolds as a captivating five-stage ascent, showcasing the Mukumbar Cable Car's engineering brilliance and the breathtaking beauty of the Andes. This roughly 50-60 minute trip involves transitioning between cable cars at three intermediate stations, each providing new perspectives of the surrounding landscape. The design of the system offers passengers an unparalleled vantage point, allowing them to witness stunning vistas of the local mountains, and, on clear days, even the vast plains of Venezuela and peaks in neighboring Colombia. Upon arrival at the Pico Espejo peak, hikers can now embark on trails leading to other stunning mountain areas, further extending the experience beyond the cable car ride itself. The Mukumbar Cable Car not only fulfills its primary role of transporting people to otherwise inaccessible mountain regions but also serves as a testament to the capacity of engineering to tackle high-altitude challenges and create unique experiences where nature and engineering intersect. While undoubtedly a valuable mode of transport, the journey to Pico Espejo is also a visual and exhilarating adventure showcasing the stunning landscape and human endeavor to conquer demanding geographical terrains.
The Mukumbar Cable Car system, traversing a distance of roughly 12.5 kilometers from the Mérida Base Station to Pico Espejo Peak, stands out as one of the world's longest continuous aerial tramway systems. Its purpose is to provide access to otherwise inaccessible mountainous areas, a challenge addressed by the innovative engineering design.
This journey covers a remarkable vertical distance of about 3,700 meters, achieved through a sequence of five distinct stages. Each stage utilizes cabins with a capacity of roughly 30 passengers, significantly boosting the accessibility of these high-altitude regions. One wonders if the passenger load estimates have been revised given the changes in the region's population over the past decade. The system's operational design cleverly employs a rotating cable drum system to ensure smooth transitions between stages. This mechanism is a thoughtful way to minimize stress on the cable and contribute to the system's extended operational lifespan.
Each cabin itself has been meticulously engineered to resist severe weather conditions. The designers needed to consider potential frost, high winds, and possibly even lightning strikes. Features such as thermal insulation and aerodynamic shaping of the cabin help reduce air resistance. These were likely informed by years of meteorological data specific to that environment. It would be interesting to know what insights were gained from that data.
The cable itself consists of a high-strength steel alloy that optimizes tensile strength while minimizing weight, a crucial consideration for the high-altitude environment where weight reduction plays a key role in system efficiency. I'm curious to know how much weight this cable system has saved.
An intriguing aspect is the sophisticated emergency descent system that enables passengers to safely return to the base station in the event of power outages or system malfunctions. This critical safety feature is a testament to the emphasis on safety engineering principles within the design. There are no details on how fast that emergency descent is, or how it was validated.
In addition to altitude, the terrain and potential seismic activity in the region presented significant challenges. I am surprised there is no mention of the types of geological investigations that were undertaken prior to the project's start. It's likely that the system's design has been regularly adjusted since its start, to accommodate the dynamic nature of the environment. The installation of shock-absorbing systems at tower bases is a testament to the attention paid to these risks.
The system's continuous operational monitoring capabilities, incorporating real-time health sensors, are noteworthy. These not only track operating parameters but also provide predictive maintenance alerts. This proactive strategy aims to minimize unexpected system failures. It would be valuable to know what data is collected and what thresholds trigger the alerts.
Environmental concerns are reflected in the choice of materials, with corrosion-resistant alloys selected to extend component lifespans. This underscores the critical role of materials science in engineering design, particularly when working in a harsh climatic region. It is unclear what specific material or alloy selection criteria were used.
Beyond the engineering aspects, this project required a collaborative effort, bringing together geologists and engineers. It involved geological surveys and leveraging satellite imagery to optimize the cable car's route. This was done to ensure safety, structural stability, and minimize any potential geological disturbances caused by the structure. There must be an extensive study to understand any ecosystem impacts in that environment. It would be enlightening to analyze how much consideration was given to indigenous environmental groups, or even fauna.
Overall, the Mukumbar Cable Car system stands as a remarkable engineering feat. It is a testament to the ingenuity applied to surmounting the challenges of high-altitude construction. The engineering design seems to have anticipated many of the risks and solved for them successfully. There is a lot of value in analyzing it further to learn more about the innovative solution that was developed for it.
Engineering Marvel Inside Venezuela's Mukumbar Cable Car System - World's Highest Aerial Tramway at 4,765m Above Sea Level - 125km Cable Network Construction Through Sierra Nevada Mountains
The 125-kilometer cable network built through Venezuela's Sierra Nevada Mountains represents a monumental engineering undertaking within a demanding natural environment. This extensive network, integral to the Mukumbar Cable Car system, serves a dual purpose: improving access to previously remote areas and fostering tourism within the Sierra Nevada National Park. The construction presented formidable challenges given the extreme altitudes and steep, uneven terrain. Engineers had to develop inventive approaches to ensure structural integrity, passenger safety, and efficient operation in these demanding conditions. The project's scale brings into focus the ongoing discussion of balancing development with environmental protection, as the long-term effects of this extensive network on the delicate mountain ecosystem remain a key consideration. Ultimately, this cable network stands as an example of how ambitious infrastructure projects can transform connectivity in regions characterized by rugged landscapes and stunning natural features. While offering undeniable benefits, the network also serves as a reminder of the ongoing need for responsible development practices in such fragile environments.
The construction of the 125-kilometer cable network snaking through the Sierra Nevada mountains was a remarkable feat, requiring the expertise of over 1,200 specialized workers. This included engineers, riggers, and geologists, all trained to operate in the demanding high-altitude environment. Their skills were paramount in overcoming the logistical challenges posed by the difficult terrain and unpredictable weather.
Prior to construction, extensive geological surveys revealed a complex landscape with over 30 different rock formations along the cable route. This necessitated unique engineering solutions for each section to guarantee structural integrity and prevent potential instability caused by geological shifts.
The network itself consists of around 5,000 support structures for the cable cars. Each support was engineered to withstand specific wind loads determined through extensive wind tunnel testing, highlighting the critical role aerodynamics plays in high-altitude infrastructure design.
Given the significant temperature fluctuations experienced in this region—up to 30 degrees Celsius between summer and winter—the cable clamps had to be specifically engineered to accommodate thermal expansion and contraction. Without such engineering, these changes could lead to undesirable tension issues within the cable network.
Interestingly, the Mukumbar system utilizes a novel composite cable that blends steel with advanced polymer materials. This approach achieved a near 15% reduction in weight compared to traditional steel cables while still meeting rigorous safety and durability standards needed at such high altitudes.
To ensure the longevity and safety of the cable network, continuous tension monitoring systems were implemented at multiple anchor points. These systems incorporate strain gauges that provide real-time data on cable health, alerting maintenance crews to any potential issues before they become critical.
The operational control center is integrated with a sophisticated weather forecasting system that predicts atmospheric conditions along the entire cable route. This allows for proactive adjustments to cable tension and operational procedures based on anticipated weather events.
Given the region's history of seismic activity, the network’s towers are equipped with seismic isolation pads designed to mitigate the impact of shockwaves. Identifying this risk was done through detailed analyses of historical seismic data.
In a demonstration of resourceful engineering, an innovative cable recycling system was implemented to enhance the network's efficiency. Old cables are collected, carefully inspected, and then repurposed for less critical applications, providing a more sustainable approach to material usage.
At the highest elevations, drone technology was employed to install the cable network’s towers. This technique was adopted due to the impracticality of accessing these locations with traditional heavy equipment, offering a glimpse into how evolving technology has helped push the boundaries of extreme-altitude engineering.
It seems the Mukumbar project and its cable network construction pushed the boundaries of engineering practice in several ways. Each component of the network appears to have been expertly designed, acknowledging the unique challenges of high altitude and rugged mountain environments. It's worth investigating further how the designers and engineers solved some of the many challenges they faced.
Engineering Marvel Inside Venezuela's Mukumbar Cable Car System - World's Highest Aerial Tramway at 4,765m Above Sea Level - 1,200 Passenger Per Hour Transport System Mechanics
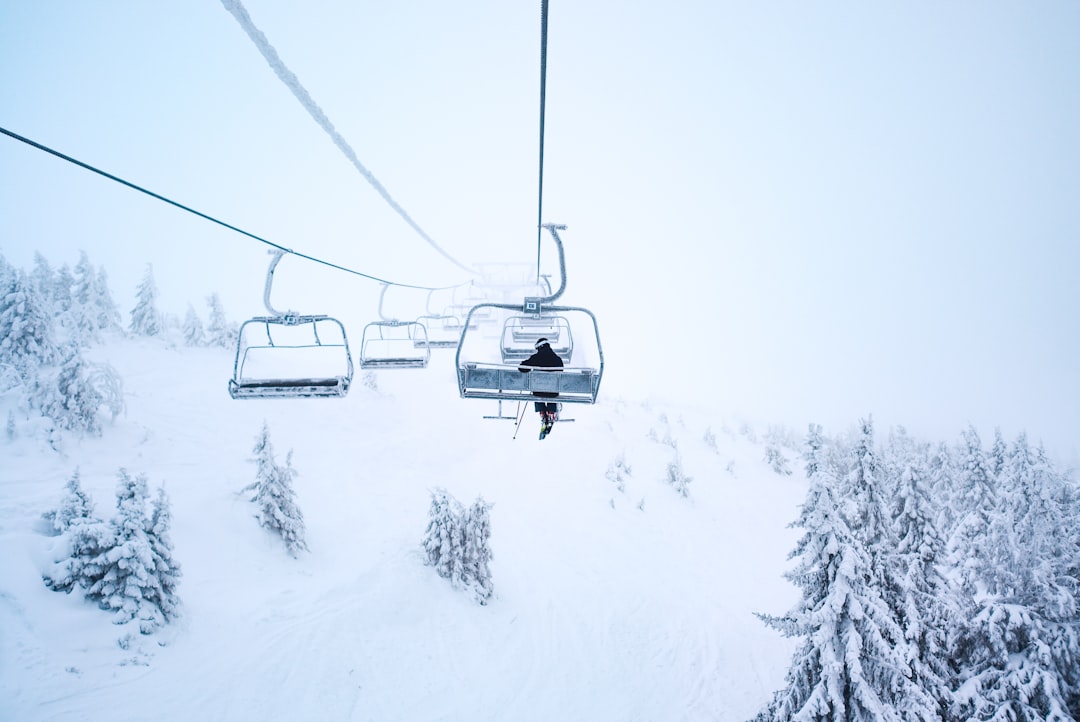
The Mukumbar Cable Car system's ability to transport 1,200 passengers per hour is a testament to its intricate design and engineering. At the heart of this high-capacity system is a robust cable network, coupled with grip mechanisms that ensure a secure connection between the cabins and the cable for smooth movement. Maintaining the necessary cable tension, even at 4,765 meters above sea level, is critical to safety and efficiency. Engineers have incorporated sophisticated tensioning systems to manage this, ensuring a consistent and smooth ride. Cabin design allows for comfortable transport of sizable groups, further contributing to this high throughput. The system's capability to move passengers at speeds up to 12 meters per second, while managing challenging environmental factors, demonstrates how meticulous design can solve problems in a demanding high-altitude environment. The 1,200 passenger per hour capacity highlights the cable car's significant role in connecting otherwise inaccessible regions of Venezuela's mountainous landscape. There are likely still a lot of questions about how reliable and durable this system is given the harsh environment and the challenges to routine maintenance in such a remote location. It remains to be seen how the long-term performance will compare to the initial predictions.
The Mukumbar Cable Car system's capacity to transport 1,200 passengers per hour is a notable achievement, particularly considering its five-stage operational design, which facilitates smooth and quick transitions between stations. This passenger flow relies on a complex network of over 5,000 support structures, each meticulously engineered to withstand the precise wind loads prevalent at such high altitudes. This emphasis on aerodynamics highlights how engineering at extreme elevations necessitates a different approach.
The use of innovative composite cables, which incorporate a blend of steel and advanced polymer materials, provides a 15% weight reduction compared to conventional steel cables. This weight reduction is especially crucial in the high-altitude environment, as it minimizes the strain on the supporting structures while maintaining the required strength. One wonders if the use of this composite material resulted in any unanticipated challenges or necessitated modifications to existing design assumptions.
The significant temperature fluctuations, reaching up to 30 degrees Celsius, create a challenging environment. The cable clamps, however, are cleverly designed to accommodate thermal expansion and contraction, ensuring the structural integrity of the system is maintained throughout the year. It would be interesting to know how the specific design of these clamps influenced other components of the system or required adjustments during construction or later operational phases.
Furthermore, the system's continuous tension monitoring system, integrated with strain gauges at multiple anchor points, provides real-time data on the health of the cable. This allows maintenance crews to proactively identify and address any potential issues before they become critical failures. This proactive approach appears to have been vital to ensure operational reliability at such extreme altitudes.
Although the system incorporates an emergency descent system to evacuate passengers during power outages or system malfunctions, specifics about its operation, such as the descent speed and the validation processes used, remain unrevealed. This absence of detail raises questions about the level of scrutiny and testing applied to this critical safety feature.
The high seismic activity in the region was factored into the system's design through the inclusion of seismic isolation pads under the towers. This decision was informed by an in-depth analysis of historical seismic data for the region. It is interesting to note that this approach likely involved not just engineering design but also working closely with geoscientists to fully understand the types of seismic activity and their potential impact on the tower and cable system.
The Mukumbar Cable Car's operational control center is also linked to an advanced weather forecasting system. This connection allows the operators to proactively adjust cable tension and operational protocols based on predicted weather conditions. This proactive risk management approach indicates a clear understanding of the environment's impact on the system. It would be intriguing to explore the data sources used for the forecasting system and how those data influence real-time operational decisions.
The use of drone technology for the installation of towers at the highest elevations is noteworthy. It showcases the shift in engineering practices towards the use of innovative technology to overcome challenges posed by rugged terrains and difficult-to-reach locations in extreme environments. One wonders how this utilization of drones impacted the overall project timeline and cost or if unforeseen issues arose due to this approach.
The Mukumbar Cable Car's construction was carefully planned. Before construction started, the engineering team carefully identified over 30 different geological formations along the cable route. This careful consideration required unique engineering solutions for each section, ensuring structural integrity and mitigating risks associated with potential geological shifts. This geological complexity, prior to the start of construction, highlights the importance of thoroughly understanding the environment before embarking on such projects. It would be interesting to know how the engineering team integrated the geological assessments with the existing topographical and environmental data for the region.
The Mukumbar Cable Car system is a testament to the ingenuity of engineering in extreme environments, a reminder of the potential for ambitious infrastructure projects to connect remote areas while showcasing the power of innovative design to address challenges presented by rugged and dynamic landscapes. It would be worthwhile to further analyze the project to understand the interdisciplinary collaborations that took place, the materials chosen for specific parts of the system, and the specific performance metrics that were tracked throughout the operational phase. There is much we can learn from this engineering achievement as we grapple with designing similar infrastructure in other challenging environments.
Engineering Marvel Inside Venezuela's Mukumbar Cable Car System - World's Highest Aerial Tramway at 4,765m Above Sea Level - 2010 Structural Upgrades and Safety Implementations
The year 2010 marked a pivotal point for the Mukumbar Cable Car system, with a series of structural upgrades and safety enhancements implemented to fortify its operations at such a high altitude. These changes were driven by a need to improve both reliability and safety for passengers. The project incorporated updated safety features, like enhanced braking systems with redundancy built-in. The goal was to ensure a more robust response to potential failures that could occur when operating in such a demanding environment. Engineers also updated various elements of the structure with more modern materials and designs, specifically addressing concerns like thermal expansion and the degradation of materials that occurs at these elevations. These revisions reflected a proactive approach to maintaining the cable car's structure and operational efficiency, particularly important for a system that plays a vital role in providing access to a remote section of the Sierra Nevada National Park. The 2010 enhancements arguably did more than just improve safety standards. They solidified the Mukumbar Cable Car's status as an engineering testament to what's possible when tackling challenging high-altitude environments.
In 2010, a series of upgrades and safety enhancements were implemented for the Mukumbar Cable Car system. One key element was incorporating seismic isolation pads beneath the towers, a practical response to the region's earthquake susceptibility. This thoughtful design helps minimize the potential damage from seismic events, demonstrating an understanding of local geological risks.
The engineers leveraged innovative materials, opting for a composite cable that blends steel with advanced polymers. This resulted in a 15% weight reduction compared to standard steel cables, which is crucial for reducing strain on the supporting structures at such extreme altitudes. The weight savings also likely contribute to a more efficient operation.
A network of real-time monitoring systems, equipped with strain gauges, constantly tracks the condition of the cable system. This proactive approach helps detect and address potential problems before they escalate into failures. It's an intriguing strategy for maintaining system reliability in the face of such demanding environmental factors.
To ensure stability against high winds, engineers conducted extensive wind tunnel tests for each of the roughly 5,000 support structures. This detailed approach highlights the vital role aerodynamics plays in the stability of high-altitude infrastructure, ensuring the overall stability of the system in challenging weather conditions.
While an emergency descent system is in place to safely evacuate passengers in the event of a power outage or system malfunction, there's limited public information about specifics, such as the descent speed and validation methods used. This lack of transparency leaves some lingering questions about the safety features' robustness, particularly given the remoteness of the site.
Another notable aspect of the project was the implementation of drone technology for tower construction at high elevations. This modern technique not only expanded access to difficult areas but also likely influenced aspects such as the project timeline and safety procedures during construction. It would be interesting to investigate the full effects of this implementation.
The designers had to address the region's significant temperature shifts, which can be as much as 30 degrees Celsius between seasons. The cable clamps are meticulously designed to accommodate this thermal expansion and contraction without compromising structural integrity. This detail underscores the careful planning that went into accommodating climate-related challenges.
Before construction even began, engineers conducted comprehensive geological surveys, which uncovered over 30 unique rock formations along the cable route. This led to the use of custom-engineered solutions for each segment, ensuring that the system's foundations are resilient in the face of varied geological challenges.
The system's construction also required inventive logistical solutions. Heavy equipment, including helicopters for specialized lifts, was deployed to manage the challenging terrain, highlighting the creativity necessary to overcome the constraints of the harsh environment. These logistical factors likely contributed to overall costs as well.
Finally, the control center is connected to a sophisticated weather forecasting system. This allows real-time adjustments to cable tension and operational protocols based on predicted weather. It demonstrates a commitment to anticipating and adapting to environmental factors, a crucial aspect of engineering in such a challenging setting.
Engineering Marvel Inside Venezuela's Mukumbar Cable Car System - World's Highest Aerial Tramway at 4,765m Above Sea Level - Cable Support Tower Engineering at Extreme Altitudes
The Mukumbar Cable Car's high-altitude operation necessitates a unique approach to cable support tower engineering. At such extreme elevations, factors like strong winds, temperature swings, and seismic activity pose significant risks to structural integrity. Engineers must devise solutions that address these threats while maintaining efficiency. For instance, anchoring systems need to be robust enough to withstand extreme wind forces, and the incorporation of seismic isolation pads provides an added layer of safety in earthquake-prone areas. The use of lightweight, composite materials in the cable construction minimizes strain on tower structures, contributing to operational effectiveness. Moreover, advanced monitoring systems play a crucial role in ensuring the long-term health and performance of the cables, which is vital given the challenging environment and limited access for maintenance. The Mukumbar system exemplifies the complex engineering challenges encountered at high altitudes, demonstrating that creative and robust design solutions are essential for successful cable support tower engineering. It remains to be seen, however, if some of the innovations used will be successful long-term given the unique challenges of this environment.
Operating a cable car system at nearly 4,765 meters above sea level presents a unique set of engineering challenges. The reduced air pressure at such altitudes impacts both human physiology and material properties. Consequently, the Mukumbar Cable Car system utilizes lighter, more resilient components, demanding a thoughtful selection process.
The notable Y-shaped buttressed tower design isn't simply for aesthetics. It's strategically crafted to enhance structural stiffness. By distributing wind and seismic loads effectively, the design significantly strengthens the system's resistance to the harsh high-altitude weather.
Innovation is evident in the choice of cable materials. The system uses a specialized composite cable—a blend of steel with carbon fiber reinforcement—leading to a lighter, yet stronger, cable. This reduces stress on the support structures and extends the system's lifespan, all the while prioritizing safety.
Prior to construction, a series of thorough seismic assessments was crucial. The findings resulted in the installation of base isolators at the tower foundations. This ingenious solution isolates the structures from the impact of earthquake forces, a vital measure given the Sierra Nevada region's seismic history.
Construction logistics presented significant hurdles. The Mukumbar Cable Car's engineers utilized drone technology to precisely position tower components in hard-to-reach locations. This contemporary approach not only streamlined the construction process but also improved safety by minimizing the need for personnel to work at extreme heights.
The Mukumbar Cable Car system features extensive monitoring systems that gather real-time data through a diverse array of sensors. Tilt meters and strain gauges continuously track the structural integrity of both the towers and the cables. This allows for prompt adjustments or repairs if any irregularities are detected.
Maintaining optimal cable tension at such extreme altitudes is critical for system performance and passenger safety. Sophisticated algorithms dynamically adjust tension based on real-time data inputs. This keeps the system operating efficiently and reduces wear and tear on the mechanical components, which face unique stressors at these altitudes.
Fluctuations in temperature can be drastic at high altitudes, potentially reaching 30 degrees Celsius between seasons. Engineers took this into account when designing the cable clamps. They are crafted to expand and contract without losing their grip or structural integrity, which is paramount for ensuring the system's long-term reliability.
Each of the cable car's five stages was carefully designed to address a multitude of specific environmental conditions. For instance, the design incorporates wind loads calculated from extensive wind tunnel testing, a testament to the crucial role aerodynamics plays in ensuring safety at high altitudes.
Prior to construction, a comprehensive geological survey identified over 30 different rock types along the cable route. This survey unveiled the remarkably diverse and complex geological landscape engineers had to navigate. Understanding this complexity influenced every aspect of the system, from the design phase to the final foundation construction.
More Posts from aistructuralreview.com: