Engineering Marvel Turns 65 ASM International's Geodesic Dome Showcases 1959 Aluminum Innovation in Materials Science
Engineering Marvel Turns 65 ASM International's Geodesic Dome Showcases 1959 Aluminum Innovation in Materials Science - R.
Buckminster Fuller Design Team Completes Ohio Aluminum Marvel in 1959
The year 1959 witnessed the culmination of R. Buckminster Fuller's design vision in the form of a remarkable aluminum geodesic dome in Ohio. Located near Chagrin Falls, this impressive structure, spanning 274 feet in diameter and rising 103 feet high, showcased innovative structural engineering. Fuller's team utilized roughly 65,000 individual pieces, primarily 13 miles of extruded aluminum tubing and tension rods, assembled into a network of hexagonal patterns. The dome's ingenious design eliminates internal supports, cleverly transferring the entire 80-ton weight onto five concrete pylons. This unique approach not only highlights the strength of aluminum but also underscores a new era in lightweight structural solutions. This architectural marvel, now considered the largest open-work dome globally, continues to serve as a testament to the power of innovative design and materials science, particularly the role of aluminum in creating resilient and lightweight structures. Its impact resonates to this day, serving as a powerful symbol for architects and engineers alike.
In 1959, the R. Buckminster Fuller Design Team finalized a remarkable structure in Ohio, a testament to their innovative approach to design. The team's application of mathematical principles optimized the dome's strength-to-weight ratio, a clever solution for its time. This was coupled with an unconventional choice of material, aluminum, reflecting a shift in how materials were perceived within the engineering world. Previously a niche material, aluminum became a significant player in large-scale construction through this project.
The dome's design was not just about materials; it was inspired by patterns found in nature, a concept now broadly understood as biomimicry. The idea of working *with* natural systems was central to Fuller's ethos, demonstrating a more holistic approach to design than was commonplace in traditional architectural schools. While we now acknowledge the importance of lightweight designs, the fact the dome was significantly lighter than a standard structure of similar size was a remarkable achievement in the late 1950s. This had implications for both material use and logistical challenges, reducing the overall impact of the construction.
Beyond its weight, the design incorporated engineering advancements related to wind loads. This was crucial since a large-span, open-work structure would be particularly susceptible to strong wind. Structural engineers were gaining an understanding of how to mitigate these forces, and the dome stood as a demonstration of such advancements in the field. Furthermore, the dome's design relied on prefabricated components, making assembly at the site faster and more streamlined. This pre-fabrication approach can be seen as an antecedent to modern construction strategies.
The dome, situated in Materials Park near Chagrin Falls, was not conceived as a single-purpose structure. Fuller imagined a versatile space that could accommodate many functions, foreshadowing the current trend toward mixed-use buildings. While this idea seems commonplace today, it was arguably a progressive notion in the 1950s. The project was a catalyst for reconsidering aluminum in building design. It moved past traditional perceptions and showed its ability to provide structural integrity in expansive, roof-like structures.
Fuller's work on the dome laid a path for future developments, including various other dome-like structures and tensile systems. This legacy has reverberated in engineering disciplines, architecture, and design fields, particularly for those focused on efficient structural designs. We must remember the Ohio dome was not the result of an individual, but a collaborative undertaking. This brought together architects, engineers, and craft workers. It established the precedent of multi-disciplinary collaborations that are essential for large architectural projects today. The collaborative spirit remains a vital element in modern engineering endeavors.
Engineering Marvel Turns 65 ASM International's Geodesic Dome Showcases 1959 Aluminum Innovation in Materials Science - 65,000 Parts Create Lightweight 80 Ton Open Air Structure
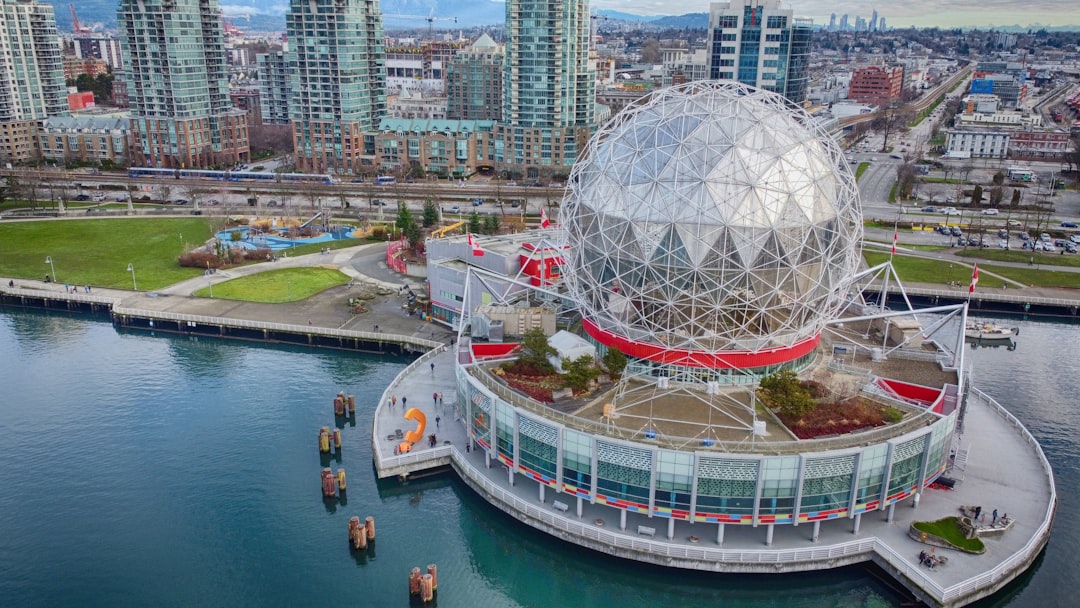
The ASM International geodesic dome, completed in 1959, stands as a testament to innovative engineering and material science. It's composed of an impressive 65,000 individual components, primarily 13 miles of extruded aluminum tubing, creating a remarkably lightweight structure for its size. Despite its 250-foot diameter and 103-foot height, the dome weighs only 80 tons, a feat achieved by distributing its load across just five concrete pylons. This ingenious approach eliminates the need for interior supports, resulting in a completely open space beneath the dome. The open-lattice design, while aesthetically pleasing, also highlights the capabilities of aluminum as a structural material. This choice of material was arguably unconventional at the time, showcasing a bold leap forward in construction practices and materials science. The ASM dome's lightweight design, achieved through clever engineering and the innovative use of aluminum, continues to inspire contemporary approaches to efficient and resilient structural engineering. It serves as a reminder of the potential for new materials to redefine the possibilities in large-scale construction.
The 1959 completion of the ASM International geodesic dome in Ohio represents a fascinating shift in how aluminum was perceived in the engineering world. Initially a relatively obscure material, its use in this large-scale structure dramatically altered its standing, illustrating its potential for both strength and adaptability in architecture. The dome's unique geometry, leveraging principles of spherical shapes, particularly hexagons and triangles, is a testament to Fuller's team's ability to optimize the structure's ability to withstand forces from all directions.
Interestingly, the dome's weight, a mere 80 tons, is supported by only five concrete pylons. This represents a significant departure from traditional structural engineering methods, highlighting how careful weight distribution can minimize the need for massive support structures. Such an innovation was remarkable for its time and foreshadows a more material-efficient approach to engineering projects.
A further look reveals the dome's construction also leveraged prefabrication, which is now a common practice, but was less prevalent in the late 1950s. Components were manufactured off-site, allowing for faster assembly and reduced errors during installation. This, in turn, potentially decreased material waste and construction times.
Because of its open, large-span nature, the dome's design also grappled with the effects of wind loads. The structural calculations required to address this were quite advanced for that era, showing a growing awareness among engineers of the environmental factors impacting such architectural creations. In essence, it represented a step forward in comprehending and mitigating wind forces in large-scale structures.
It's also important to acknowledge that the dome's creation wasn't a solitary pursuit. Instead, it arose from the collaborative efforts of architects, engineers, and skilled craftspeople. This collective approach became a model for future architectural projects, demonstrating that multifaceted expertise is often needed for complex structural feats. This is a lesson that still holds true for modern, sophisticated engineering projects.
Buckminster Fuller's design philosophy emphasized learning from nature, a concept gaining traction now. This approach resulted in a structure that was both aesthetically pleasing and practically effective. The design's influence is evident in its versatile functionality, a foresightful idea that anticipated contemporary preferences for mixed-use spaces and adaptability in building design.
The dome's spherical shape, with its maximized volume relative to surface area, represents an efficient use of materials. This concept, reducing heat loss and material requirements, is vital to a broader movement towards more efficient and sustainable building methods.
Even today, the dome serves as a significant reminder of the power of innovative material selection and smart design principles. Its use in structural engineering classrooms continues, inspiring engineers to reconsider traditional approaches and embrace creativity within their work. It serves as a reminder that engineering achievements are often collaborative and that looking to nature can offer elegant solutions for complex challenges.
Engineering Marvel Turns 65 ASM International's Geodesic Dome Showcases 1959 Aluminum Innovation in Materials Science - 274 Foot Wide Dome Houses Materials Science Research Center
The Materials Science Research Center in Ohio houses a 274-foot-wide dome, a striking example of 1959's innovative engineering and materials science. This impressive structure, built primarily from aluminum, demonstrates the potential for lightweight construction with significant strength. Its ingenious design, featuring only five supporting concrete pylons, showcases efficient weight distribution and the power of geodesic principles. The resulting open interior space reflects a shift toward modern structural engineering practices. The dome's construction also pioneered prefabrication techniques, demonstrating a forward-thinking approach to assembly. Recognized for its historical value, the dome remains a valuable educational tool, continuing to influence modern construction methods. Moreover, its collaborative development signifies the increasing importance of multidisciplinary teamwork in complex engineering and architectural endeavors, a trend prevalent in today's projects.
The ASM International Materials Science Research Center's geodesic dome, completed in 1959, showcases a fascinating blend of materials science and structural engineering. Its 274-foot diameter and 103-foot height are made possible through a unique design that maximizes efficiency. The dome's intricate geometry distributes forces across the structure's framework, resulting in an incredibly robust and lightweight roof. This clever design enables it to withstand environmental pressures with minimal material use, a remarkable feat for the time.
Interestingly, the dome's 65,000 components, most notably the 13 miles of extruded aluminum tubing, illustrate a pioneering approach to prefabrication. The aluminum itself was a bold material choice for 1959. This transition from a less common building material to a primary structural element is a clear demonstration of aluminum's potential in engineering. It showcased its capability to handle substantial loads while remaining remarkably lightweight. This shift, prompted by the dome, altered how architects and engineers thought about materials in large-scale construction.
Fuller's design team incorporated mathematical optimization principles to optimize the dome's strength-to-weight ratio. This refined approach went beyond conventional structural design methods of the time, demonstrating that pushing engineering boundaries could yield impressive results. The structure itself is a prime example, supported by just five concrete pylons, eliminating the need for internal columns. This resulted in a large open space beneath the dome that could be utilized for a variety of functions.
However, this lack of internal supports meant designers had to carefully consider the wind loads impacting a structure of this type and span. The advanced structural engineering involved in calculating wind forces on the open dome was a notable development for that era. It also underscores the increasing understanding of how to design for environmental factors during a time when these topics were just starting to become mainstream within engineering circles.
The dome's efficient design facilitated lighter construction, ultimately reducing material use and streamlining the assembly process on-site. This reduced material consumption and potential waste also simplified logistics, lowering the logistical challenges associated with handling and transporting such massive components. This approach likely influenced later construction methods where prefabricated elements are now widely implemented.
Fuller's design for the dome wasn't limited to structural concerns. The design integrates aerodynamic principles, an emerging field of engineering at the time. This attention to details like wind resistance contributed to the dome's resilience in harsh weather.
Furthermore, the dome's design foreshadowed today's trend toward mixed-use buildings. The foresight of crafting a space flexible enough for a variety of functions is particularly noteworthy. This versatility was arguably uncommon in the 1950s, highlighting the forward-thinking nature of the design team.
This extraordinary structure is a product of a collective effort. Architects, engineers, and skilled craftspeople collaborated seamlessly on the project. This teamwork became a foundational element in the architectural and engineering world, illustrating that challenging projects are more successful with diverse expertise. The collective effort on this project continues to serve as a reminder of the importance of such collaboration in modern engineering.
The ASM dome stands as a testament to a holistic approach to design. This approach blends engineering with a biomimicry sensibility. This project, while notable for its technological advancements, was also an exercise in design thinking. This approach draws inspiration from the natural world, contributing to a highly efficient structure. Even today, the dome inspires engineers, a testament to its influence on contemporary engineering thought and practices. It's a potent example of the power of collaborative work and the idea that looking to nature can provide inventive solutions for challenging engineering problems.
Engineering Marvel Turns 65 ASM International's Geodesic Dome Showcases 1959 Aluminum Innovation in Materials Science - 60 Mineral Ore Garden Documents Engineering History Since 1913
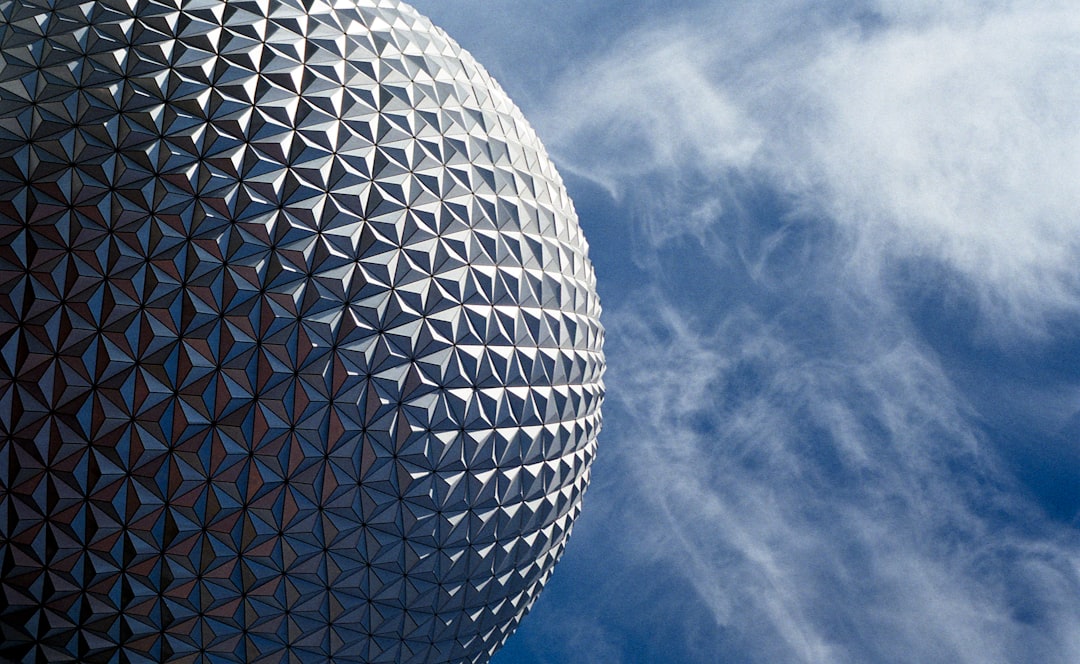
The Mineral Ore Garden at the ASM International headquarters offers a unique glimpse into the history of engineering, charting the evolution of materials science from its inception in 1913. Featuring over 60 different mineral ores, this garden effectively connects the raw materials used in engineering with their practical applications. Situated within the context of the renowned geodesic dome, it underscores the enduring significance of mineral resources in driving technological innovation. Understanding the inherent properties of materials is essential for pushing design boundaries, and the garden acts as a living testament to the critical role minerals have played in shaping modern engineering methods. While it celebrates historical advancements, it also reinforces the relevance of fundamental materials science in contemporary engineering feats. In essence, it serves as an educational resource that connects the past with the present, inviting visitors to recognize the profound impact of these materials on the structures and technologies we see around us today.
The ASM International geodesic dome, completed in 1959, serves as a compelling illustration of how materials science and structural engineering evolved. It marked a turning point in the perception of aluminum, transitioning from a relatively obscure material to a cornerstone for creating lightweight yet strong architectural structures. This change was partly due to the dome's unique geodesic form, which is based on a network of interconnected hexagons and triangles, a design that skillfully distributes forces throughout the framework, ensuring its stability and resistance to loads.
Furthermore, the dome's remarkable design, resting on only five concrete supports, demonstrates a sophisticated understanding of structural mechanics, especially considering the complexities of load calculations for such a large and open-span structure. It's a testament to the advanced engineering practices of the time. The construction process itself was innovative, as the dome was built primarily with prefabricated elements—65,000 individual pieces fabricated off-site, a practice less common in the late 1950s. This prefabrication approach highlighted the potential for streamlining assembly and minimizing construction errors, providing a foundation for the modular construction methods used today.
Beyond the structural innovations, the dome’s design also showcases early sustainability concepts. The spherical shape efficiently maximizes internal volume while minimizing the exterior surface area, illustrating a mindful approach to reducing material use without sacrificing strength. It's important to note that this achievement wouldn't have been possible without collaborative efforts involving architects, engineers, and skilled workers. This successful blend of expertise has established a standard for multidisciplinary teamwork in complex engineering and architectural endeavors, an approach that remains highly valued in modern projects.
Another significant aspect of the dome's design is its consideration of wind loads, a factor of vital importance in a large open-air structure. The designers meticulously addressed these challenges, highlighting a growing awareness of how environmental forces impact structural design. This demonstrated a shift toward understanding and integrating environmental factors into engineering practices, which has become central to current engineering design considerations. Further enhancing the design's ingenuity, aerodynamic principles were also incorporated, showing an early understanding of the interplay between different engineering disciplines. The dome's ability to adapt to different functionalities anticipated the contemporary trend of mixed-use buildings, representing a progressive approach to building design that moved away from fixed, single-purpose structures.
Even in 2024, the geodesic dome continues to serve as a valuable educational resource, informing civil and architectural engineering curricula. It inspires students to examine traditional design approaches critically and consider the potential of innovative materials and engineering philosophies. The dome’s story is a reminder of how collaborative efforts, combined with creative design choices and a deeper understanding of natural principles, can produce structures that are both functional and inspiring.
Engineering Marvel Turns 65 ASM International's Geodesic Dome Showcases 1959 Aluminum Innovation in Materials Science - Custom Copper Interior Details Match Aluminum Framework Innovation
The ASM International geodesic dome's design showcases a fascinating fusion of aesthetics and engineering through its use of custom copper interior elements alongside the aluminum framework. This pairing creates a visually appealing interplay, where traditional materials enhance the modern structure's engineering prowess. The decision to incorporate copper details within the aluminum structure demonstrates a thoughtful design approach that elevates the dome beyond just a functional space; it becomes an eye-catching architectural achievement. It's a good example of how the use of traditional materials and modern solutions can be carefully combined in a thoughtful design process, revealing the potential for aesthetically interesting and structurally sound buildings in the 21st century. While material science continues to advance, the concept of these synergistic relationships remains a powerful aspect of contemporary design and construction.
The ASM International geodesic dome, a marvel of 1959 engineering, cleverly integrates custom copper interior elements within its aluminum framework. This pairing of materials highlights the strengths of each metal: aluminum's celebrated lightweight durability and copper's renowned electrical conductivity and corrosion resistance. However, the decision to combine these metals necessitates careful consideration. The significant difference in their thermal conductivities, with copper far exceeding aluminum's, presents both opportunities and challenges for temperature regulation within the structure. While this could lead to novel passive heating/cooling solutions, it also raises concerns regarding uneven thermal expansion and contraction across the dome's structure.
Furthermore, the potential for galvanic corrosion, a phenomenon where dissimilar metals in contact accelerate corrosion, necessitates thoughtful surface treatment strategies for long-term structural integrity. Beyond the functional aspect, the use of copper clearly contributes to the dome's aesthetic appeal. The warm, rich tones of copper offer a visual contrast to the cool, industrial look of the aluminum frame, creating a more complex and visually pleasing design. This pairing signifies a shift away from solely prioritizing function in architectural design, incorporating artistic expression into the equation.
It's worth highlighting that the use of custom-fabricated copper details underscores a key aspect of this historical design: the advanced state of metallurgy in the late 1950s. This knowledge enabled engineers and architects to achieve complex, aesthetically interesting designs while ensuring reliability in large-scale construction. The use of aluminum and copper, both non-ferrous metals that resist rusting, signals a movement toward materials with extended lifespans, which was particularly crucial for projects of this magnitude in that era.
Beyond its visual appeal and structural stability, the use of copper also hints at broader possibilities. Copper's inherent antimicrobial properties, currently a subject of growing interest in architectural design, might have contributed to a healthier interior environment within the dome. The ability to shape and integrate the copper components with great precision exemplifies the critical role of specialized manufacturing processes in realizing such a complex project. One can speculate that the placement of copper elements could have influenced the acoustic behavior of the dome, perhaps providing for strategic sound dampening or amplification within the vast space.
Finally, the selection of copper details alongside aluminum embodies a legacy of cross-disciplinary collaboration. This project's success reflects an early understanding of how architects, engineers, and metallurgists need to work in tandem, a model that remains vital for complex engineering projects today. While this dome, in its initial conception, was not a research laboratory focused on exploring the interplay of copper and aluminum, it serves as a fascinating historical artifact showing how materials science and engineering knowledge can be applied to complex projects. The dome serves as a powerful testament to the ingenuity of the 1959 engineering community, a constant reminder of the interplay between materials selection, structural design, and aesthetic expression in large-scale construction.
Engineering Marvel Turns 65 ASM International's Geodesic Dome Showcases 1959 Aluminum Innovation in Materials Science - Detroit Metal Society Transforms Into Global Materials Hub at Materials Park
The former Detroit Metal Society has undergone a transformation, becoming a prominent global materials science center now situated at Materials Park, Ohio. This shift builds on ASM International's historical dedication to materials science and education, a commitment that dates back to the organization's origins in Detroit in 1913. Materials Park's centerpiece remains the iconic geodesic dome, but its purpose has expanded to include educational programs aimed at inspiring a new generation of materials scientists. These efforts range from hosting workshops for high school students to teacher training initiatives. The center's ongoing commitment to materials science is further evidenced by its embrace of data-driven approaches, with plans to use AI and machine learning to analyze vast datasets and make connections among materials scientists and engineers worldwide. Materials Park has thus evolved into a multifaceted hub. It serves as a testament to the rich legacy of ASM International in the materials science field while simultaneously showcasing its forward-looking vision for the future. The future of this park is tied to developing new materials in a collaborative environment which, hopefully, will promote innovation and a deeper understanding of materials science.
The evolution of the American Society for Metals, now known as ASM International, from its Detroit roots to a globally recognized materials hub, centered at Materials Park, is a testament to the organization's influence on materials science. This transformation, while geographically significant, also represents a broadening of focus from localized engineering expertise to a more interconnected approach. Aluminum, prominently featured in the dome's construction, serves as a poignant example of this shift. Originally, it was considered a somewhat niche material, but the dome showcased its potential. Now, aluminum is actively researched and refined, finding uses in areas like aerospace and automotive applications.
The dome itself, with its intelligent load-bearing structure—supported by just five pylons despite weighing 80 tons—is a compelling example of efficient structural engineering. This idea of maximizing strength while minimizing material continues to influence design thinking. This is further illustrated by the 13 miles of aluminum tubing used in the construction. Its successful use, a bold decision for its time, demonstrated its versatility, a characteristic that has helped propel aluminum into diverse engineering fields. Materials Park, where the dome stands, has evolved into more than a headquarters—it is a dynamic space where research on new materials is actively carried out. This includes working with new alloy compositions and composite materials, demonstrating that the organization's commitment to materials science has continued past the dome's construction.
The construction itself benefitted from the utilization of a prefabrication method that was not widely used in 1959. This approach significantly improved efficiency. This early application of prefabrication is an antecedent to modern-day modular construction. It's a practice that emphasizes less waste and faster assembly times, critical in today's fast-paced construction sector. The dome's composition, involving 65,000 customized pieces, underscores the manufacturing advancements of the late 1950s. It's clear that there was a meticulous attention to detail that resulted in a high level of complexity in the dome's design, and likely pushed the boundaries of what was considered possible for engineering projects at that time.
Moreover, the dome's design is a notable example of the synergy between engineering and aesthetics. This is a key element of the dome's lasting appeal; it's a visually striking building that performs a function, and it inspired and probably evokes an emotional response. The engineers and architects involved clearly recognized the importance of crafting a beautiful structure. This principle of merging function and aesthetics remains relevant to contemporary architecture. The dome's design also highlighted the growing understanding of environmental factors on structures. Wind loads, a primary concern for a structure with such an extensive open span, were carefully considered. This reflects how environmental factors started becoming an integral component of building design and how that evolved over time into the mainstream engineering practices we observe today.
The ASM's transformation, coupled with Materials Park's continued contribution to material research, points toward the interconnectedness of engineering disciplines. It reveals how engineering fields can work together and influence one another on a global stage. This collaborative approach to solving complex engineering problems using advanced materials is as vital now as it was when the dome was envisioned in 1959. It's a reminder that progress and innovation are not solely individual endeavors but require collaboration, a principle that is foundational to tackling global-scale engineering challenges in the future.
More Posts from aistructuralreview.com: