USB Serial Cables and Structural Engineering Efficiency An Analysis
USB Serial Cables and Structural Engineering Efficiency An Analysis - Tracing Tension Paths in Connected Structural Cables
Understanding how tension distributes along interconnected structural cables remains a critical focus, but ongoing developments are significantly impacting how this analysis is performed. Newer computational techniques, including more sophisticated finite element models and potentially machine learning applications, are allowing engineers to simulate tension paths in increasingly complex geometries and under more dynamic loading scenarios than previously practical. Furthermore, advancements in sensor technology and data acquisition systems are opening possibilities for real-time monitoring of cable tensions in actual structures, moving beyond theoretical models or sporadic measurements. While these methods promise greater insight into structural behavior and potential issues like fatigue or damage, challenges remain in processing vast amounts of data accurately and validating these advanced models against the unpredictable realities of long-term structural performance and environmental effects. This pushes the field towards integrating diverse analytical and monitoring approaches for a more comprehensive understanding.
1. It's quite remarkable how tracking something as subtle as a tiny vibration's journey time along a cable can reveal so much about the massive tensile forces it's carrying. The principle that stress wave speed scales with the square root of tension offers a genuinely dynamic window into load distribution – a perspective traditional static shape analysis simply can't provide in real-time. Still, getting clean measurements in a busy structural environment remains a persistent challenge.
2. When dealing with interconnected cable networks, load doesn't always flow in the direction you might first guess. Tension distributes itself based on the relative stiffness and specific configuration of each segment, often leading to paths that seem counter-intuitive at a glance. Understanding these complex, sometimes surprising, load flow patterns is absolutely critical because ignoring them means potentially misjudging where peak stresses truly land in the system.
3. A seemingly minor defect or variation in a cable, like a splice or even just surface roughness, isn't just cosmetic; it locally disrupts the smooth flow of tension. These subtle path deviations create localized stress concentrations that can disproportionately impact the cable's ability to withstand repeated loading cycles over time, long before global tension levels become a concern. Pinpointing these micro-scale hotspots accurately before they become failure points is a difficult but necessary task for reliable longevity assessment.
4. The structure itself isn't static; it's constantly responding to its environment. Differential heating or cooling across a large cable system due to sunlight, shade, or wind can cause parts to expand or contract unevenly. This thermal 'breathing' subtly, yet continuously, reshapes the tension paths throughout the day. Accounting for these dynamic, environmentally-driven shifts is crucial because the forces aren't fixed but are in a state of perpetual adjustment.
5. Structural cables seldom operate in isolation. Their interaction with other elements, particularly compression members they brace, is profound. The precise path the tension follows in a cable can directly influence the effective length and stability of the strut or column it's connected to, significantly impacting that member's resistance to buckling. Analyzing cable tension paths is therefore not just about the cable itself, but essential for understanding and ensuring the stability of the entire coupled structural system.
USB Serial Cables and Structural Engineering Efficiency An Analysis - The Digital Data Flow for Structural Performance Analysis
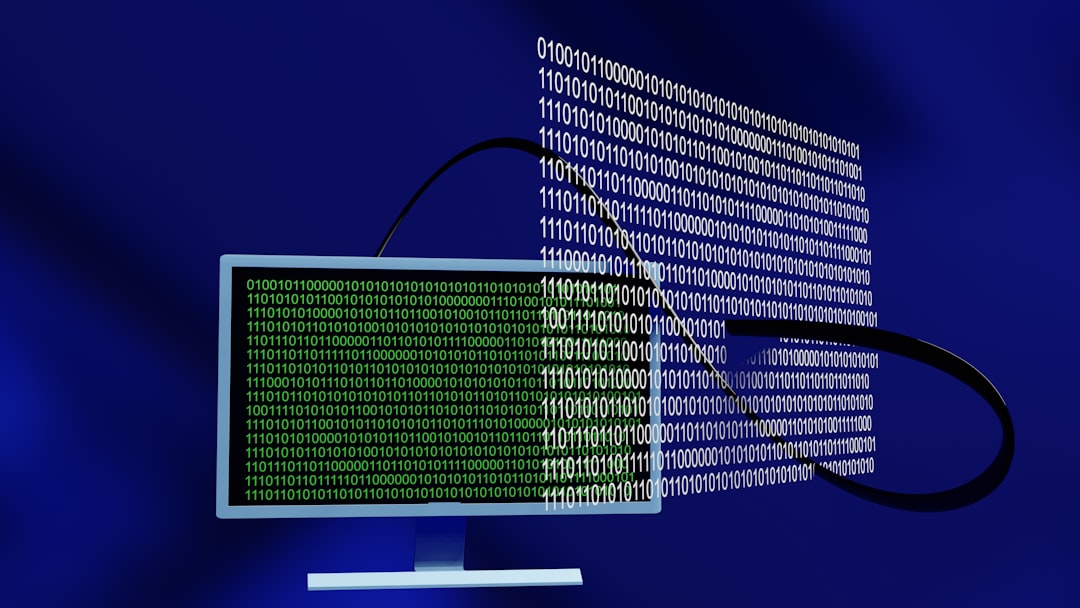
Evaluating how structures perform is undergoing a notable evolution, shifting towards a more unified approach. The focus is increasingly on creating a coherent digital picture of a structure, often termed a digital twin, that pulls together information from monitoring systems and inspections with analytical models. This aims to move beyond static assessments, providing engineers with a more dynamic, data-informed understanding of real-world behavior. While the potential for better insights and more responsive decision-making is clear, effectively merging disparate data streams and ensuring that these digital representations genuinely reflect the complex, ever-changing physical reality without being overwhelmed by sheer data volume remains a significant hurdle.
Exploring the flow of digital information in structural performance analysis reveals some fascinating and occasionally sobering aspects:
For starters, the sheer volume of sensor output from a structure under continuous observation can quickly become overwhelming. We're talking about data quantities that dwarf the original design files – potentially petabytes arriving annually. Just managing this deluge, let alone extracting meaningful insights from it amidst inherent noise and redundancy, presents a substantial logistical and computational hurdle that isn't trivial to overcome.
Beyond the simple numbers from sensors, a truly informative structural analysis often requires stitching together disparate datasets. This includes environmental readings, certainly, but also delves into potentially patchy manufacturing records detailing material nuances, or maintenance logs documenting past interventions. Integrating these varied, sometimes poorly formatted, information streams is less about seamless flow and more about painstaking fusion, yet it's crucial for understanding the structure's complex, real-world behaviour.
There's also a growing necessity to process significant portions of this monitoring data closer to the source, right there on the structure itself. Transmitting every raw data point back to a central hub for analysis is often impractical due to bandwidth constraints and the need for immediate responsiveness if something critical occurs. Pushing processing out to localized 'edge' devices minimizes communication latency and allows for faster identification of anomalies, though it introduces its own complexities in terms of distributed computation and reliability.
Furthermore, it's critical to acknowledge that these digital data pipelines aren't inherently secure or immune to manipulation. The integrity of the information flow is paramount; compromised data could potentially be used to deliberately obscure signs of distress or generate false alerts, presenting a genuine safety risk that moves beyond purely technical concerns into the realm of physical security and trust in the digital representation.
Finally, the ambition is for this incoming data stream to actively inform and refine our analytical models, allowing 'digital twins' to evolve alongside the physical structure. While the idea of continuously updating finite element parameters or training machine learning models with real-world feedback is compelling, the practical challenge lies in ensuring the quality and relevance of the data used for these updates. A flawed or biased data input risks sending the digital model down an unrepresentative path, potentially eroding confidence in its predictive capabilities.
USB Serial Cables and Structural Engineering Efficiency An Analysis - Specification Adherence A Shared Challenge for Connectors and Construction
Specification adherence isn't a straightforward matter for either the components connecting electronics or the components connecting buildings. Both domains grapple with the reality that designs, however detailed, must be translated into physical objects, and that translation process is fraught with potential inconsistencies. In the realm of connectors, say for digital interfaces, meeting prescribed electrical, mechanical, and environmental parameters precisely across mass production can be elusive. Minor variances, sometimes seemingly insignificant, can degrade signal integrity or physical durability, undermining the intended function. Similarly, in structural assembly, ensuring that materials, dimensions, and connections match engineering specifications without deviation is fundamental, yet persistent deviations occur. Even small departures in how elements are joined or the properties of materials used can accumulate or create local vulnerabilities that aren't immediately obvious but compromise long-term performance or structural integrity. As both fields push boundaries with more complex systems and tighter tolerances, the margin for error narrows. Relying solely on final inspection isn't enough; robust processes to *ensure* adherence throughout the lifecycle are critical. This highlights a fundamental, ongoing struggle: advancing capabilities while maintaining rigorous foundational quality control. It's a common ground of difficulty where technical requirements meet the unavoidable imperfections of real-world execution.
Grappling with ensuring things are built or made exactly to plan, or "to specification," is a surprisingly common battleground whether you're assembling minuscule electrical connectors or erecting sprawling structural steelwork. It seems a fundamental engineering hurdle, manifesting differently but sharing core difficulties.
It's quite striking how achieving precise dimensions for electrical connectors, where required tolerances are measured in just a few millionths of a meter to maintain signal integrity, presents a challenge fundamentally akin to hitting the critical millimetre-scale tolerances required for structural connections to ensure intended load transfer. Both domains confront the issue of unavoidable, small variations that accumulate through assembly, potentially leading to unexpected system behaviour or compromised performance if not meticulously controlled from raw material to final assembly.
Furthermore, achieving specification adherence isn't a 'one-time' checkbox. What meets spec initially can, over time, drift. Subtle, persistent environmental interactions—like thermal expansion cycles subtly altering the contact force in a connector pair or differential moisture absorption affecting composite behaviour in a structure—can shift properties outside their specified envelopes, necessitating ongoing consideration beyond initial compliance testing.
A perhaps overlooked aspect is that simply verifying a component's property falls *within* its acceptable range isn't a guarantee of predictable system function. The *nature* of the variability *within* that permissible range—how properties are distributed across a batch of resistors or throughout a concrete pour, for instance—can significantly alter how interconnected components interact, leading to performance distributions that are hard to predict if only min/max values were considered.
Ensuring adherence at the crucial junctures where components meet, the 'interfaces,' often proves the most difficult test of all. Whether it's guaranteeing the specified contact pressure and cleanliness on a tiny electrical pin mating surface to ensure reliable current flow, or verifying the effective load transfer mechanism across a complex structural joint involving welds, bolts, and mating plates, these interface specifications are notoriously hard to measure and verify accurately in the field, yet their performance is paramount for overall system reliability.
Finally, there remains a persistent gap between confirming individual components meet specifications in controlled lab settings and predicting their performance once integrated into a complex, interactive real-world system. An electrical connector might perform flawlessly in isolation but exhibit issues when subjected to system-level noise and signal reflections; similarly, a structural member verified for material properties might still face performance issues due to residual stresses from fabrication or unanticipated boundary conditions once part of the larger structure, highlighting the challenge of translating isolated compliance into integrated functionality.
USB Serial Cables and Structural Engineering Efficiency An Analysis - Assembly Sequences for Large Span Cable Systems
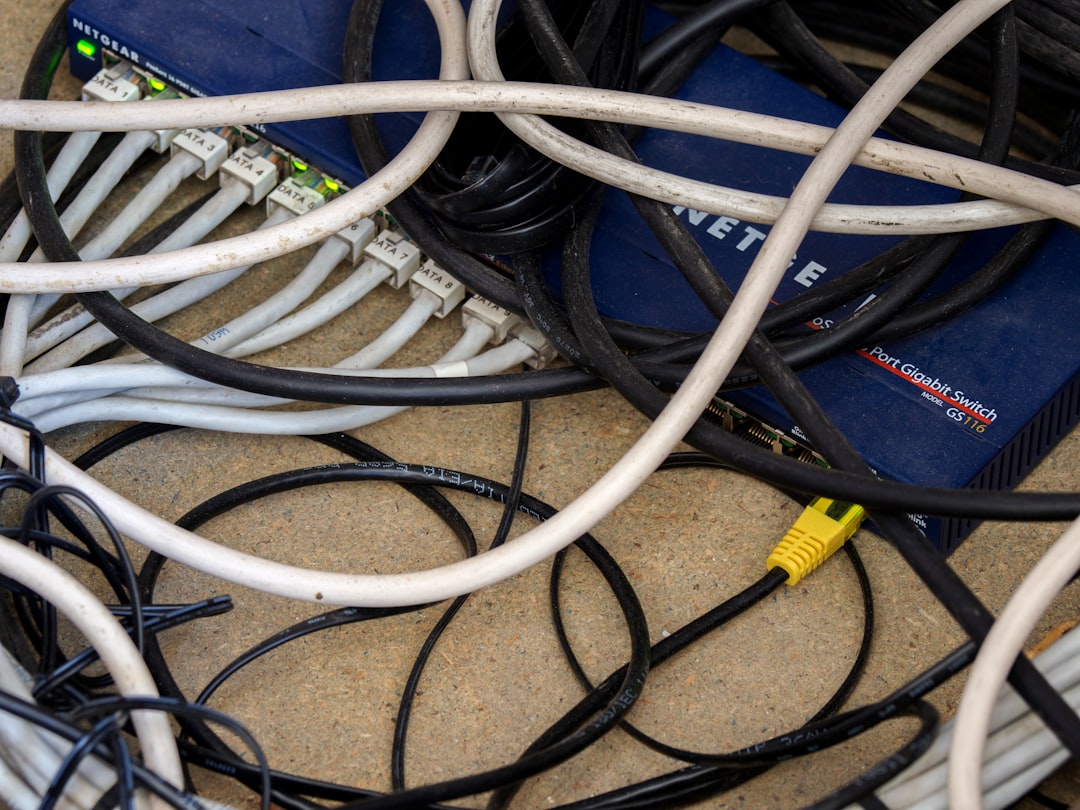
The process of constructing large span cable systems is increasingly driven by sophisticated planning and execution methods, moving beyond simpler step-by-step assembly. Modern approaches emphasize precise simulation of the entire erection and tensioning sequence computationally before any physical work begins. This allows engineers to predict the complex, non-linear behavior of the structure at every stage, anticipating how forces redistribute and geometries shift under temporary loads and staged tension applications – insights that were previously harder to gain prospectively. There's also a growing focus on developing and deploying specialized handling and lifting techniques tailored to the immense scale and flexibility of these components, acknowledging the inherent difficulties and risks involved in working with heavy, high-strength cables high above the ground. The goal is to ensure the final structure achieves its critical design state, particularly its intended tension profile and exact geometry, accurately and safely, rather than simply assembling components sequentially and hoping the final state aligns.
1. The exact sequence used to apply tension to individual cables is far more than a procedural detail; it fundamentally dictates the locked-in state of internal forces and deformations within the completed structure, establishing a 'memory' of its construction path that persists long after the last cable is stressed.
2. Temporary elements erected purely for the assembly phase – items like jacking towers or stability guys – don't merely provide passive support. They function as active, albeit transient, structural participants whose stiffness and geometry significantly shape the stress landscape and stability margins of the main system while it's still being built.
3. Pinpoint accuracy when establishing cable tensions during assembly requires continuous, often real-time, compensation for ambient temperature fluctuations along the enormous cable lengths, acknowledging that the force reading taken reflects not just the mechanical tension but also the immediate thermal state relative to the target design temperature.
4. Early stages of tensioning introduce subtle non-linearities; the initial seating of cable strands within sockets or the relative movement at connection points during these first load applications profoundly influence how the system responds to subsequent tension increments and ultimately impacts the effective stiffness characteristics of the assembled network.
5. In structurally complex systems, the tensioning might deliberately proceed in an unbalanced or asymmetric pattern, stressing different parts unevenly. This isn't an oversight but a calculated strategy employed to precisely control the motion and position of very large, heavy components during their integration into the structure.
More Posts from aistructuralreview.com: