New Techniques in Detecting Hydrogen-Induced Cracking in High-Strength Steels for Structural Applications
New Techniques in Detecting Hydrogen-Induced Cracking in High-Strength Steels for Structural Applications - Electrochemical Hydrogen Charging Techniques for Crack Detection
Electrochemical hydrogen charging methods have emerged as valuable tools for evaluating the susceptibility of high-strength steels to hydrogen-induced cracking (HIC). These techniques enable researchers to scrutinize how hydrogen diffuses and gets trapped within the steel's microstructure, particularly in materials like X60 pipeline steels. Studies using these methods have shown that HIC often initiates at the core of the steel's cross-section after specific exposure durations to hydrogen. It's been observed that the base metal is susceptible to hydrogen blistering, while the weld metal, in comparison, shows greater resistance to both blistering and HIC. This disparity indicates that the steel's composition and microstructure play a significant role in how it responds to the presence of hydrogen and the subsequent propagation of cracks.
The sensitivity to hydrogen-induced cracking can vary dramatically depending on the steel's specific microstructure. This variability underscores the critical need for careful evaluation of high-strength steels, especially those destined for demanding applications such as offshore oil and gas infrastructure. The complex mechanisms by which hydrogen travels through the steel's microstructure are still being investigated. The understanding gained through electrochemical hydrogen charging will be essential for developing strategies to anticipate and control cracking in the future. Ultimately, it can help predict and ultimately prevent the catastrophic failure of components exposed to hydrogen in various environments.
1. Electrochemical hydrogen charging methods introduce hydrogen into materials by applying a controlled electrical current, mimicking the hydrogen exposure that can result in hydrogen-induced cracking (HIC) in real-world applications. This controlled approach allows for more accurate evaluations of a material's susceptibility to HIC.
2. Unlike traditional approaches that mostly rely on visual inspections or mechanical tests, electrochemical techniques offer the potential for real-time crack detection. This provides immediate feedback on the structural health of high-strength steels, which is valuable for timely assessment of integrity.
3. The selection of the electrolyte used during the electrochemical charging process is critically important because it significantly influences the amount and distribution of hydrogen within the steel. Understanding how the electrolyte impacts hydrogen behavior is crucial for correctly interpreting material responses under stress.
4. One of the noteworthy complexities associated with electrochemical hydrogen charging is the possibility of inadvertently altering the microstructure of the steel. If not carefully managed, these microstructural changes during the test process can influence the assessment results and potentially lead to inaccurate conclusions.
5. The sensitivity of electrochemical hydrogen charging techniques is influenced by environmental factors. Factors such as temperature and humidity can greatly impact the rate at which hydrogen diffuses through the material, which highlights the importance of controlled test environments to obtain meaningful and reproducible results.
6. Recent research has explored using nanomaterials or advanced surface coatings in tandem with electrochemical charging to improve the sensitivity of detecting precursors to HIC. This combination could potentially lead to earlier and more reliable identification of potential failure points.
7. Electrochemical techniques have shown the capability to detect cracks as small as a few micrometers. This level of precision surpasses that of conventional inspection methods, which frequently miss smaller defects, potentially leading to underestimation of the severity of defects in high-strength steel components.
8. Electrochemical hydrogen charging can be conducted in-situ, meaning that crack detection can be achieved without the need to remove components from their operating environment. This capability offers significant advantages, particularly for large-scale structural components where removal for inspection is challenging or impractical.
9. The proper calibration of the electrochemical sensing equipment is crucial for accurate results. Even minor discrepancies in calibration can result in false positives or negatives, underscoring the need for meticulous setup and validation procedures to ensure reliability.
10. By using electrochemical techniques to measure hydrogen diffusion, researchers can gain a deeper understanding of the mechanisms that drive hydrogen embrittlement. This knowledge can inform the development of improved high-strength steels with enhanced resistance to HIC, leading to improved durability and reliability in structural applications.
New Techniques in Detecting Hydrogen-Induced Cracking in High-Strength Steels for Structural Applications - Advanced Microscopy Methods in Identifying HIC Initiation Points
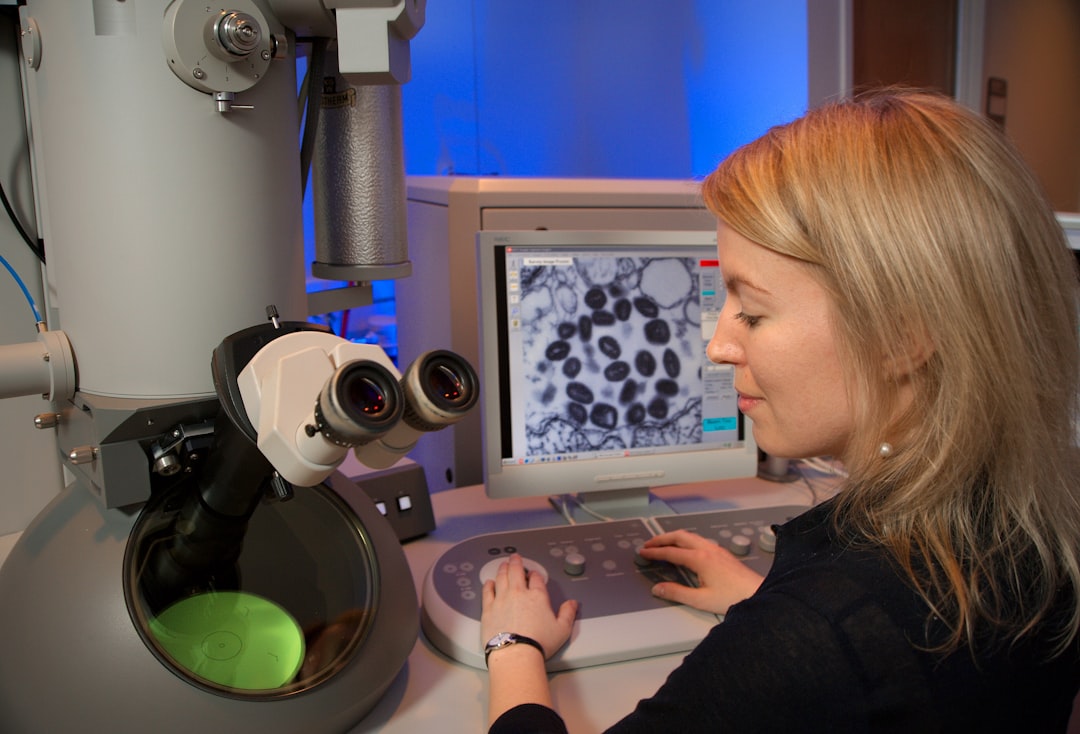
Advanced microscopy techniques are playing a growing role in pinpointing the initial stages of hydrogen-induced cracking (HIC) in high-strength steels. Methods like scanning electron microscopy (SEM) provide a powerful way to observe the microscopic details of crack formation, shedding light on how hydrogen interacts with the intricate structure of these steels. Studies utilizing these methods have revealed a common pattern: cracks tend to originate at the center of a high-strength steel's cross-section after being exposed to hydrogen for extended periods. This observation underscores the complex interplay of factors involved in HIC.
By combining these advanced microscopy techniques with more traditional inspection methods, scientists can gain a more complete understanding of how cracks propagate. This deeper knowledge is crucial for developing new approaches to design steels with better resistance to HIC. It's becoming increasingly clear that innovative techniques are vital for effectively tackling the challenges presented by hydrogen in high-strength steels used in demanding structural applications. While progress has been made, there are limitations to the current understanding, and further research is needed to fully unravel the complexities of HIC initiation and prevention.
Advanced microscopy methods are increasingly important in understanding hydrogen-induced cracking (HIC) initiation points in high-strength steels. While traditional methods like magnetic particle inspection have limitations in detecting these often-subtle defects, techniques like scanning electron microscopy (SEM) offer a much finer level of detail. SEM helps us visualize the shape and distribution of where cracks begin at a very small scale, offering insights often missed by macroscopic examination.
Transmission electron microscopy (TEM) goes even further, enabling us to see how hydrogen atoms distort the steel's crystal structure at an atomic level. This ability reveals how hydrogen can affect the mechanical properties of the steel, a critical factor in understanding crack formation. Atomic force microscopy (AFM) provides a precise way to measure how hydrogen changes the surface of the steel, which might provide more details on the relationship between the microstructure and HIC susceptibility.
Researchers are also using advanced tomography techniques like X-ray computed tomography (CT) to examine the internal structures of high-strength steels in three dimensions. This approach allows us to visualize hydrogen's journey through the steel's structure and potentially see the intricate pathways cracks follow. We're seeing more use of focused ion beam (FIB) milling, which allows for the precise removal of microscopic samples for higher-magnification analysis. This helps us understand the mechanisms of crack formation in more detail.
High-resolution energy dispersive X-ray spectroscopy (EDX) provides insights into the chemical makeup at the locations where HIC begins. By linking particular elements in the alloy with HIC resistance or susceptibility, this approach can potentially guide us towards better alloy development for these applications. Advanced optical microscopy methods, particularly phase imaging, allow us to see microstructural changes in real-time as hydrogen is introduced. This ability could be helpful in understanding the sequence of events leading to HIC.
The creation of 3D reconstructions of the initial stages of HIC using techniques like digital image correlation can clarify the interactions between microstructural features and hydrogen movement, which is critical for building more accurate models of HIC development. There's also a growing interest in using machine learning to analyze the vast amounts of data produced by advanced microscopy. This could potentially lead to better ways to identify patterns linked to HIC initiation, potentially paving the way for more effective predictive maintenance practices. Lastly, researchers are exploring cryogenic microscopy techniques to observe the fleeting microstructural changes during hydrogen exposure. This approach is designed to capture the dynamic changes that occur before permanent damage from HIC, hopefully shedding light on ways to prevent HIC altogether.
While these techniques are certainly showing promise, there are ongoing questions regarding their application in realistic industrial scenarios. Despite this, they are giving us a much more nuanced understanding of HIC formation in high-strength steels, hopefully aiding the development of stronger and more reliable structural components in the future.
New Techniques in Detecting Hydrogen-Induced Cracking in High-Strength Steels for Structural Applications - Machine Learning Algorithms for Predicting HIC Susceptibility
Machine learning algorithms offer a promising new avenue for predicting the susceptibility of high-strength steels to hydrogen-induced cracking (HIC). This approach leverages the power of computers to analyze extensive data gathered from experiments like electrochemical hydrogen charging and advanced microscopy. The goal is to identify specific features within the steel's microstructure that are closely tied to cracking behavior. Through machine learning techniques such as neural networks and decision trees, researchers hope to create predictive models that connect the material's characteristics and the surrounding environment to the risk of HIC. This data-driven approach promises to deepen our understanding of the complex processes that cause HIC and, consequently, lead to the development of steels less prone to hydrogen embrittlement. The ultimate aim is to build stronger, more dependable structures capable of withstanding challenging conditions. While the potential of these machine learning algorithms is significant, their effectiveness in practical settings still needs to be thoroughly validated. Further research and improvement are needed to ensure that these algorithms can reliably predict HIC susceptibility across a wide range of real-world scenarios.
Hydrogen-induced cracking (HIC) susceptibility in high-strength steels, especially those used in demanding environments, is a growing concern. Traditional methods for predicting HIC can be inaccurate and limited. Machine learning, however, offers a potential pathway to more reliable assessments. Algorithms can sift through extensive datasets from past hydrogen exposure tests, identifying patterns that link steel composition and microstructure to HIC risk. This ability to predict HIC susceptibility could reduce unexpected maintenance needs and disruptions in operation.
Supervised learning methods, like neural networks and support vector machines, have shown promise in categorizing steel samples based on their HIC behavior. These methods can leverage both compositional and microstructural features to make predictions. Expanding training datasets with diverse hydrogen exposure conditions and testing environments can help create models more readily applicable to a wider array of real-world scenarios, hopefully reducing the need for extensive new data collection in the future.
One of the major challenges with applying machine learning in this context is making sense of the predictions. If engineers can't understand what factors drive the models' conclusions, the insights may not be very helpful in guiding material choice or design. To improve accuracy and trustworthiness, methods like ensemble learning, which combine multiple machine learning algorithms, have been explored. They can identify subtle cues within steel microstructures that point to a higher HIC risk, potentially improving assessment reliability.
Researchers are also exploring transfer learning. In this approach, a model trained on one type of high-strength steel is adapted to predict HIC in other grades. This strategy could significantly reduce the amount of data required to train new models for various steel materials. Furthermore, the fusion of machine learning with advanced microscopy data provides a deeper understanding of hydrogen embrittlement and helps identify microstructural features that might be early warning signs of HIC.
Beyond understanding the mechanisms, this approach can help pinpoint specific alloying elements that appear to enhance HIC resistance. This information could inform the design of new high-strength steels with improved resistance to cracking. Despite the benefits, practical implementation of machine learning still has barriers to overcome. The need for substantial, clean datasets and real-time data acquisition for feeding predictive systems pose challenges.
Rigorous validation is critical for machine learning models in this context. The consequences of incorrect predictions could range from unnecessary costs to severe failures. False positives for HIC susceptibility can lead to unnecessary downtime and expense, while false negatives could lead to catastrophic incidents. Careful testing and validation are essential for developing reliable machine learning tools that contribute to enhanced safety and reliability in structural applications.
New Techniques in Detecting Hydrogen-Induced Cracking in High-Strength Steels for Structural Applications - Ultrasonic Testing Innovations for In-Situ HIC Monitoring
Ultrasonic testing is evolving to better monitor hydrogen-induced cracking (HIC) in high-strength steels, particularly in industries like petrochemicals and refineries. New approaches, including the Total Focusing Method (TFM) and Advanced Velocity Ratio (AVR) measurements, are being investigated to improve the detection of HIC. These methods, often combined with phased array ultrasonic testing (PAUT), allow for more comprehensive assessments of cracks, including their size, location, and orientation. However, traditional ultrasonic methods sometimes struggle with precisely identifying the size and exact location of HIC cracks, highlighting a need for continued research.
The development of these newer ultrasonic techniques is vital as HIC can severely compromise the integrity of steel structures, leading to potential failures. The ability to monitor for HIC in real-time is crucial for preventing potentially devastating accidents. Continued refinement of ultrasonic testing methods could significantly improve how we manage hydrogen embrittlement in the challenging environments where high-strength steels are frequently used, potentially leading to enhanced safety and reliability. There is a push to improve the accuracy of traditional methods which are often lacking in detail, the ability to do this in-situ (without removing the component from its operating environment) is vital. While promising, there are challenges still to overcome in reliably implementing these tools across diverse applications.
Ultrasonic testing, employing high-frequency sound waves, is being explored as a way to detect flaws and potentially predict hydrogen-induced cracking (HIC) in high-strength steels, particularly within operational environments. This non-destructive technique allows us to assess the structural health of materials without the need to disrupt their function, making it attractive for critical components. The ability to discern subtle defects, including those located beneath the surface, is valuable as early detection is key to preventing potential failures.
HIC is a critical concern, particularly in industries like oil and gas where equipment frequently encounters wet hydrogen sulfide (H₂S) at high pressure and temperature. Traditional ultrasonic tests have shown they can find HIC, but pinpointing the precise size and location of the cracks can be a challenge. We see that methods like phased array ultrasonic testing (PAUT) offer improvements because they can capture multiple angles and essentially create a "3D image" of the area under inspection. This improved imaging capability helps with more accurate defect characterization and speeds up the inspection process.
A potential advancement in ultrasonic techniques involves dual-frequency testing, which uses two different frequencies at the same time to get a better look at the subsurface. This could improve the ability to 'see' HIC before it fully develops. Further, researchers are coupling ultrasonic systems with machine learning, aiming to allow for automatic data interpretation, identifying patterns that might hint at when and where HIC is more likely to occur. This potentially moves from just detecting cracks to predicting where problems might arise in the future.
Interestingly, ultrasonic testing can be adapted for different environments and temperature ranges, making it suitable for use in realistic operational situations where conditions change frequently. These fluctuations can potentially increase the risk of HIC, so the ability to monitor within the operational space is attractive. Using signal processing in tandem with ultrasonic testing can refine the analysis and enhance visualization of the behavior of cracks within the steel. We might get a better handle on the mechanics of HIC development through these enhanced visuals.
The availability of portable ultrasonic equipment expands the possibilities for on-site inspection of components in remote or challenging locations. This could lead to significant cost and downtime savings in addition to contributing to the safety of the structure. The ability to continuously monitor structural elements using these ultrasonic techniques, particularly in hydrogen-rich environments like offshore platforms or hydrogen storage facilities, offers critical advantages.
While ultrasonic testing shows promise, challenges remain in the practical application of the technique. Factors like the experience of the operator, the precision of equipment calibration, and the ability to accurately interpret the results are critical for consistently reliable results. We must also acknowledge that ongoing training and development in these areas will be needed to build a proficient workforce that can get the most out of this technology. This will likely include developments in standards and certifications related to HIC detection using ultrasonics.
New Techniques in Detecting Hydrogen-Induced Cracking in High-Strength Steels for Structural Applications - Neutron Diffraction Analysis for Hydrogen Distribution Mapping
Neutron diffraction analysis presents a new way to map the locations of hydrogen atoms within high-strength steels. This is vital for understanding hydrogen embrittlement, a major concern affecting the structural integrity of these materials. Using this technique, scientists can visualize where hydrogen is concentrated within the steel, offering valuable clues on how it interacts with the complex inner structure of the material.
However, challenges remain. It can be difficult to get very precise images of hydrogen locations, and observing how hydrogen behaves in real-time under different conditions is still a work in progress. It appears that hydrogen's behavior is very sensitive to the surrounding environment. Combining neutron diffraction with other methods of analysis may help in understanding how hydrogen leads to cracks, offering better ways to develop stronger steel materials for use in challenging applications. The goal would be to design materials that better resist hydrogen embrittlement.
Neutron diffraction is a valuable tool for understanding hydrogen's distribution in high-strength steels because it can reveal the presence of light elements, like hydrogen, which are difficult to see using traditional X-ray methods. This capability is particularly useful for studying hydrogen embrittlement.
Unlike many other analysis techniques, neutron diffraction allows for deep penetration into materials without causing damage. This non-destructive feature is advantageous for studying large or sensitive components, keeping them intact for further evaluation.
The technique employs neutrons with a wavelength that matches the typical distance between atoms in solid materials, which is crucial for analyzing atomic arrangements and improving the resolution of hydrogen distribution maps.
We can use neutron diffraction to study hydrogen behavior at different temperatures, which helps us understand how temperature changes influence hydrogen diffusion and its role in embrittlement processes in these steels.
By examining the diffraction patterns produced, we can determine not just the quantity of hydrogen but also its local environment. This is particularly helpful for understanding how hydrogen interacts with different microstructural elements.
One limitation of neutron diffraction is that neutron sources are not very common, typically being housed in specialized facilities, limiting accessibility for widespread use in industrial settings. This practical aspect might hinder its broader implementation.
While the spatial resolution of neutron diffraction isn't yet as high as some techniques like electron microscopy, recent improvements have increased its accuracy in locating hydrogen on a microstructural scale.
Neutron diffraction can be used for in-situ experiments, where the absorption of hydrogen can be observed in real-time under changing external conditions. This is helpful for understanding how cracks develop due to the presence of hydrogen.
Interpreting neutron diffraction data can be intricate, requiring sophisticated computational techniques to separate meaningful data from background noise. This complexity can lead to some discrepancies in how researchers interpret hydrogen detection.
Combining neutron diffraction analysis with other techniques, such as electrochemical methods and microscopy, offers a better overall understanding of the negative effects of hydrogen on steel properties, guiding the development of better engineering solutions for mitigating hydrogen embrittlement issues.
New Techniques in Detecting Hydrogen-Induced Cracking in High-Strength Steels for Structural Applications - Thermal Desorption Spectroscopy Advancements in Hydrogen Trapping Assessment
Thermal Desorption Spectroscopy (TDS) has emerged as a valuable tool for understanding how hydrogen interacts with and becomes trapped within high-strength steels, particularly in structural applications. This technique allows scientists to not only measure the amount of hydrogen present but also determine the strength of the bonds between hydrogen and different trapping sites within the material. TDS can be used on a range of materials, from those with a regular crystal structure to those with a more disordered structure.
Recent developments in TDS have shed light on the intricate details of hydrogen trapping. For instance, studies exploring tungsten-based precipitates in iron-carbon-tungsten alloys have revealed how the steel's microstructure influences hydrogen behavior. This highlights the importance of understanding the specific arrangement of atoms within the steel when predicting how hydrogen will behave. Further, pairing TDS with advanced techniques like atom probe tomography allows researchers to pinpoint hydrogen distribution within very small areas of the material, offering a clearer picture of hydrogen's role in the cracking process.
However, there are still some uncertainties related to TDS. Results from TDS experiments on steels treated with different heat treatments (quenched and tempered) suggest that hydrogen trapping might not always behave as expected, leading to questions about how effectively we can predict the susceptibility of different types of steels to hydrogen embrittlement. Therefore, continuous investigation and refinement of TDS, particularly when applying it to real-world scenarios, will be vital for accurately predicting and mitigating hydrogen-induced cracking.
1. Thermal desorption spectroscopy (TDS) is a valuable tool for measuring how much hydrogen is trapped and released in materials, including both crystalline and non-crystalline structures, providing a quantitative understanding of this process in high-strength steels. It essentially involves heating the material and carefully monitoring the hydrogen that comes off, revealing how strongly hydrogen binds to different locations within the material.
2. Researchers have used TDS to investigate the effectiveness of hydrogen traps in tungsten-based precipitates found in iron-carbon-tungsten alloys with varying carbon content. This work underscores how the internal structure of the steel greatly impacts its susceptibility to hydrogen trapping.
3. Hydrogen embrittlement (HE), a serious issue, can lead to delayed fracture in high-strength steels. In a U-bend test, for instance, increasing the hydrogen content has been shown to reduce the time it takes for the material to fracture. This points to the critical role hydrogen plays in reducing material toughness.
4. Atom probe tomography (APT) has emerged as a powerful technique for imaging the distribution of hydrogen within extremely small features. By providing detailed chemical and structural information, it allows us to see how hydrogen gets trapped at locations like dislocations and grain boundaries, giving us a nanoscale perspective on this phenomenon.
5. TDS offers a unique way to analyze the amount of hydrogen and the strength of the bonds between hydrogen and trap sites in a material. By observing the release of hydrogen during heating, it can potentially provide insights into the different types of traps present in a given microstructure.
6. Hydrogen's presence in steels, especially in high-strength grades, can significantly impact their ability to deform, making them more brittle. This can lead to unexpected and catastrophic failures in structural components, underscoring the need for effective techniques to assess and mitigate hydrogen's effect on material strength.
7. Research using TDS suggests that small, hydrogen-trapping precipitates in the microstructure of steels can potentially help reduce hydrogen embrittlement. It's hypothesized that by creating more traps, we can possibly reduce the amount of free hydrogen that is available to weaken the material.
8. Interestingly, thermal desorption data has shown similar hydrogen trapping behaviors in quenched and tempered steels. This suggests that the perceived improvements in hydrogen embrittlement resistance linked to different heat treatment approaches might not be as straightforward as previously thought.
9. Mass spectrometry techniques, with their high spatial and mass resolution, can precisely identify the locations of hydrogen within the material. This high level of detail allows us to study the interactions of hydrogen with other elements in the steel's microstructure with greater accuracy.
10. There's a growing understanding of the role that dislocations and the stability of retained austenite play in hydrogen embrittlement. Dislocations, essentially defects in the crystal structure, can act as traps for hydrogen, while the presence of retained austenite (a phase of steel that is not fully transformed during processing) can impact the susceptibility of steel to HE. Understanding the interplay of these factors is key to developing strategies for improved hydrogen resistance in high-strength steels.
More Posts from aistructuralreview.com: