Zinc Plating vs Galvanizing A Comparative Analysis of Corrosion Protection Methods in 2024
Zinc Plating vs Galvanizing A Comparative Analysis of Corrosion Protection Methods in 2024 - Zinc Plating Process and Applications in 2024
Zinc plating remains a prominent surface treatment in 2024, particularly when moderate corrosion protection is sufficient. The core method is electroplating, often referred to as electro-galvanizing, making it a widely used and economical choice. This process applies a relatively thin layer of zinc, making it suitable for interior and less aggressive environments. Its ability to provide a visually appealing finish adds to its attractiveness, especially in applications where aesthetics are important. While useful, zinc plating generally delivers less corrosion resistance than galvanizing due to the thinner coating, making it less ideal for harsh external environments. However, ongoing developments in zinc plating technology, including specialized types like Type I and Type II, are leading to its increased use in applications like aerospace and marine, where tailored properties are crucial. Despite these advancements, users should carefully consider the trade-offs between the cost and aesthetic benefits of zinc plating and its inherent limitations in resisting corrosion compared to galvanizing, especially for projects requiring long-term durability.
1. Zinc plating, achieved through an electrolytic process, creates a relatively thin zinc layer on a substrate, often steel. This coating acts as a barrier against corrosion and, in standardized testing, demonstrates strong performance against corrosive environments like salt spray, often exceeding 1,000 hours. This makes it a viable option for many applications needing at least moderate corrosion protection.
2. The protective properties of zinc plating can be enhanced by incorporating alloying elements like nickel during the plating process. This approach can yield a harder and more durable coating, making zinc plating suitable for situations demanding greater resistance to wear and tear.
3. Unlike the high-temperature process of galvanizing, zinc plating is usually conducted at ambient temperatures. This attribute allows it to be used on components or substrates that are sensitive to heat, expanding its applicability in areas where galvanizing is unsuitable.
4. The methods for applying zinc plating vary, including electroplating, hot-dip plating, and mechanical plating. These techniques offer different levels of control over coating thickness and surface finish, offering flexibility for tailoring the process to specific application requirements.
5. Proper surface preparation is paramount for ensuring a strong bond between the substrate and the zinc layer. Without careful cleaning and surface conditioning, adhesion is compromised, and the effectiveness of the coating is diminished. Achieving optimal corrosion protection relies heavily on maximizing adhesion through appropriate preparation.
6. Zinc plating can often be combined with additional treatments, such as passivation. Passivation involves creating a protective film on the zinc surface, which can provide even further resistance against corrosion. By employing passivation, the life cycle of the zinc coating can be significantly extended.
7. The appearance of zinc-plated surfaces varies, ranging from bright to dull finishes. The coloration is influenced by the specific chemical makeup and processes employed during plating. For applications where aesthetics matter, this range in appearance allows for some flexibility.
8. While zinc plating isn't as thick or robust as galvanizing, particularly in harsh conditions, it represents a more cost-effective solution for indoor environments or milder outdoor exposures. It's a useful consideration when the highest level of corrosion protection isn't the primary driver.
9. Specialized formulations of zinc plating baths are designed to minimize issues like hydrogen embrittlement, which can occur when plating high-strength steels. These specialized formulations help to mitigate potential safety and performance issues, making zinc plating compatible with a broader range of engineering applications.
10. Ongoing research and development in the zinc plating industry are exploring new techniques and materials. Duplex coatings that combine zinc with organic polymers are a prime example. These innovations offer the potential for significant advancements in corrosion protection without necessarily needing to increase the thickness of the zinc layer itself, providing a path for improving the performance and longevity of zinc plating in a variety of settings.
Zinc Plating vs Galvanizing A Comparative Analysis of Corrosion Protection Methods in 2024 - Hot-Dip Galvanizing Technique and Its Advantages
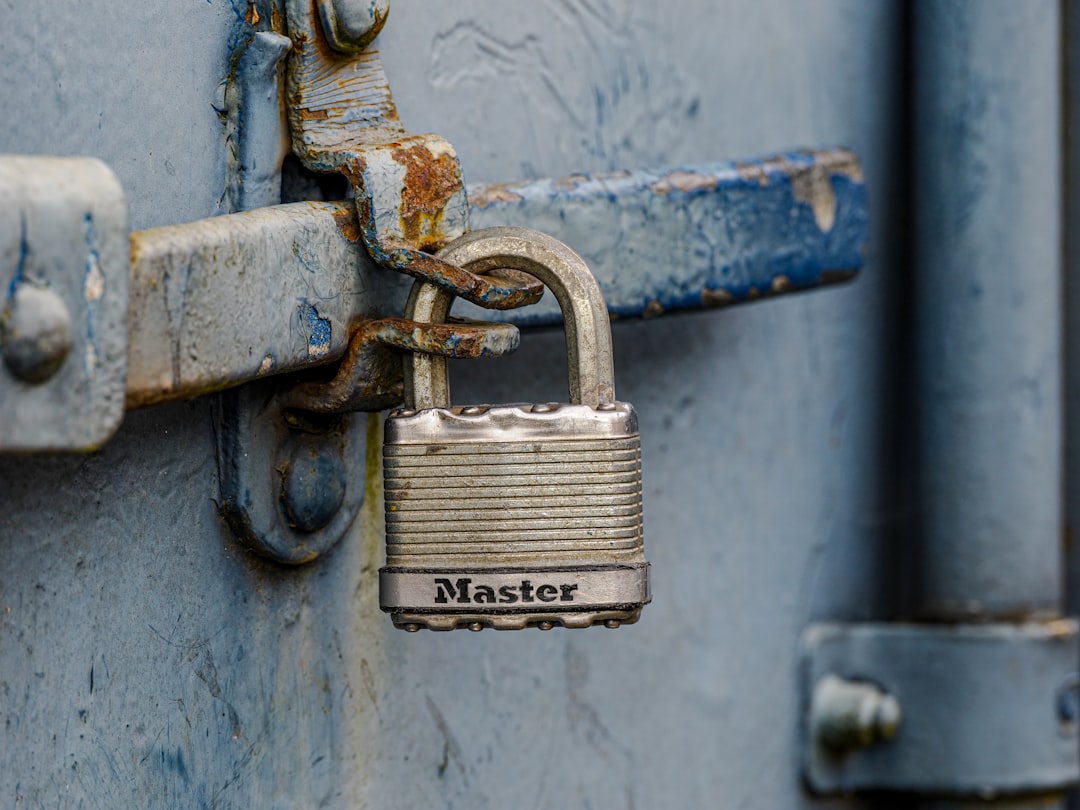
Hot-dip galvanizing is a technique where steel is submerged in molten zinc, resulting in a thick, protective coating. This coating, which can range from 2 to 8 mils in thickness, is significantly thicker than zinc plating, providing superior corrosion resistance. The process creates a metallurgical bond between the zinc and the steel, leading to a strong and durable finish that's well-suited for large outdoor structures like fences and pipes.
The thick zinc layer and the metallurgical bond combine to offer exceptionally high corrosion protection, with some structures lasting decades without significant rusting. While the formation of zinc oxide provides added protection, this method typically comes with a higher price tag than zinc plating. However, the long-term durability and performance make it a financially attractive choice for applications where corrosion protection is critical, particularly for projects requiring extended life spans and resistance to severe weather.
Essentially, when dealing with structures or components exposed to the elements, hot-dip galvanizing offers a compelling solution for long-term protection from corrosion, which is a major factor in maintaining structural integrity. The durability and corrosion resistance offered can result in significant savings in the long run, making it a valuable technique in diverse fields.
Hot-dip galvanizing stands out as a corrosion protection technique due to its unique approach and the substantial advantages it offers. The process involves immersing steel parts in a bath of molten zinc, typically maintained at around 450 degrees Celsius. This high-temperature immersion leads to the formation of a relatively thick zinc coating, often ranging from 2 to 8 mils, significantly thicker than the coatings achieved through zinc plating. This thicker coating is a key contributor to galvanizing's superior corrosion resistance.
A fascinating aspect of hot-dip galvanizing is the metallurgical bond that develops between the zinc and the steel substrate. This bond isn't just a surface layer but creates a series of intermetallic layers, effectively merging the two materials. This intermetallic structure plays a crucial role in enhancing the coating's adhesion to the steel and contributes significantly to its long-term performance in the face of corrosion. Interestingly, the galvanizing process imparts a self-healing characteristic to the coating. If the coating is scratched or damaged, the surrounding zinc can continue to provide cathodic protection to the exposed steel. This self-healing nature prevents the rapid spread of rust, ensuring that the integrity of the underlying steel is maintained for extended periods.
The high-temperature nature of the process and the relatively fast cooling times (often under 10 minutes) mean hot-dip galvanizing can handle large batches of components efficiently. This efficiency is particularly valuable in manufacturing settings where production speed is paramount, such as in the construction and automotive industries. It's worth noting that the ability to control the thickness of the zinc coating during galvanization makes it versatile. It can produce thin alloy layers for specific applications or much thicker coatings (occasionally exceeding 100 microns) for environments that require maximum protection, such as harsh marine or industrial settings.
Hot-dip galvanizing provides an impressive level of protection against mechanical damage. Compared to other surface treatments, it offers exceptional abrasion and impact resistance, a key consideration in manufacturing environments where parts may experience significant wear and tear. Moreover, its ability to coat intricate and irregularly shaped components uniformly ensures that even hidden areas are adequately protected, a crucial aspect often overlooked in other protection methods.
While the distinct "slightly mottled" appearance of a hot-dip galvanized surface may not appeal to everyone, it's a characteristic that adds a unique visual touch to some architectural designs. Beyond aesthetics, the visual cues help quickly identify galvanized steel, and this long-lasting corrosion protection means galvanized materials require less maintenance compared to other methods, particularly painted surfaces. Reduced maintenance translates to lower costs and reduced resource consumption, contributing to its sustainability and overall economic appeal in a variety of construction projects. In essence, the lifespan of a hot-dip galvanized part can extend for many years or even decades, representing a cost-effective and durable approach to protecting steel from corrosion. This makes it a valuable option across a wide range of engineering applications where durability and long-term performance are essential.
Zinc Plating vs Galvanizing A Comparative Analysis of Corrosion Protection Methods in 2024 - Coating Thickness Comparison Between Zinc Plating and Galvanizing
When evaluating corrosion protection methods, the thickness of the zinc coating applied is a key differentiator between zinc plating and hot-dip galvanizing. Hot-dip galvanizing consistently produces a much thicker zinc coating, typically ranging from 2 to 8 mils. This substantial thickness provides a higher level of corrosion protection, making it ideal for structures and components subjected to harsh environmental conditions, such as outdoor installations and marine applications. Conversely, zinc plating results in a thinner layer of zinc, usually around 0.2 to 0.5 mils. This thinner coating is sufficient for applications with less demanding environments and where aesthetics or cost are major concerns. The notable difference in thickness is also reflected in the surface texture. Hot-dip galvanized surfaces have a more pronounced, sometimes rougher texture, while zinc plating leads to a smoother surface finish. While zinc plating can be economically attractive and provide a visually pleasing result, users should consider the potential limitations of the thinner coating when long-term corrosion protection is crucial. Choosing between these two approaches depends on carefully assessing the specific environmental factors and desired performance outcomes for a given application.
When comparing zinc plating and galvanizing, one of the most notable distinctions lies in the thickness of the zinc coating they produce. Galvanizing, with its immersion in molten zinc, generates a coating typically ranging from 2 to 8 mils, significantly thicker than the 0.2 to 0.5 mil layer achieved by zinc plating. This difference has a direct impact on corrosion resistance, with galvanized coatings offering superior protection in harsh environments.
The thicker coating in galvanizing is more than just a physical barrier. During the high-temperature process, a metallurgical bond forms between the zinc and the steel substrate. This bond enhances adhesion and, intriguingly, contributes to the coating's longevity. Zinc plating, on the other hand, often requires additional treatments to achieve similar corrosion protection.
Interestingly, this thickness difference can also influence how each coating performs under stress. While the thinner zinc plating can be beneficial for applications with precise dimensional tolerances, it's susceptible to quicker wear, particularly in high-friction environments. Galvanizing, with its thicker layer, can endure mechanical stress more readily thanks to the greater mass of zinc providing a more robust defense against abrasion.
Moreover, the application temperatures play a key role in the resulting coating properties. Zinc plating is carried out at room temperature, eliminating any concerns about heat treatment. Conversely, the high temperature employed in galvanizing fosters diffusion processes that generate intermetallic compounds between the zinc and the steel. These compounds further enhance corrosion resistance beyond what a typical zinc plating process can achieve.
However, the thicker nature of the galvanized coating can also be a disadvantage in specific circumstances. If precise engineering tolerances are required, the thinner profile of zinc plating can be preferable. This, though, comes at the expense of reduced durability compared to the robustness of the galvanizing coating which is frequently a necessity in outdoor or high-stress applications.
It's important to remember that despite its potentially superior corrosion resistance, galvanizing often has a rougher texture compared to the typically smoother finish of zinc-plated materials. This can be a decisive factor in applications emphasizing aesthetics. Sometimes, the visually appealing surface provided by zinc plating might overshadow the consideration of the critical performance differences that arise from the thinner coating in some environments.
Beyond aesthetics, the difference in thickness influences mechanical resistance as well. Galvanized components tend to have greater resistance to impact and abrasion due to the robust coating. This is a notable advantage in environments with considerable wear and tear. Consequently, choosing the appropriate method hinges on the specific operational demands the components are expected to face.
Applications like marine environments, where seawater can accelerate corrosion, are a stark example of how coating thickness becomes paramount. The aggressive nature of saltwater can rapidly degrade the thinner coatings of zinc plating, making galvanizing the preferred choice for durability and longevity. This reinforces the importance of carefully considering the environmental factors when selecting the optimal coating technique.
While hot-dip galvanizing can create uniform coatings even on complex shapes, it's important to be aware that the dipping process might occasionally lead to inconsistencies in the coating thickness. This can potentially create weak spots that are less common in the more controlled zinc plating application methods.
Finally, considering the curing times and the reliability of each coating is crucial. Galvanized components often cure through an exothermic reaction, meaning they can be put into use quickly after treatment. In contrast, zinc-plated items may require more cautious handling until they achieve their optimal performance levels, which underscores the need for users to be cognizant of these procedural differences and how they might impact post-treatment handling.
In conclusion, the coating thickness comparison between zinc plating and galvanizing reveals distinct advantages and disadvantages for each technique. Carefully evaluating the specific needs of a given application – whether it's aesthetics, corrosion resistance, mechanical strength, or environmental factors – is essential for selecting the optimal method for long-term protection and performance.
Zinc Plating vs Galvanizing A Comparative Analysis of Corrosion Protection Methods in 2024 - Environmental Performance of Zinc Plating vs Galvanizing
When evaluating corrosion protection methods, the environmental performance of zinc plating and galvanizing becomes a central aspect. Zinc plating, often favored for its affordability and attractive finish, provides adequate protection in less demanding environments. However, its thinner zinc layer limits its effectiveness in more aggressive situations. Conversely, galvanizing, through the hot-dip process, delivers a significantly thicker zinc coating that provides superior corrosion resistance. Furthermore, the unique metallurgical bond created in galvanizing gives the coating a degree of self-healing, improving its adaptability in environments with fluctuating conditions. However, both methods have environmental implications to consider, including their specific processes, coating durability, and long-term maintenance demands. When making a decision between these two methods, it's important to carefully evaluate the specific environmental factors and the desired application. A balanced approach is needed to understand the performance advantages and potential ecological implications associated with each technique, allowing for a more informed choice. This careful analysis is crucial for achieving both durable corrosion protection and minimizing any potential environmental impact.
Zinc plating, while offering a cost-effective and visually appealing finish, can sometimes be susceptible to "white rust," a zinc hydroxide formation that occurs in humid environments. This can compromise the appearance and protective qualities of the coating, highlighting the importance of proper handling and maintenance. Particularly in high-salinity environments like coastal areas, the relatively thin zinc layer of plating may not provide the long-term protection offered by galvanizing. It can degrade more quickly, leading to underlying steel corrosion, whereas galvanizing's thicker coating offers better durability in such conditions.
The application versatility of zinc plating is generally higher due to the electroplating process, making it suitable for a wider range of shapes and sizes. Galvanizing, with its immersion technique, can sometimes struggle with intricate geometries. Therefore, part design can heavily influence the selection of a suitable method. It's worth noting that while both methods offer a protective barrier, zinc plating doesn't provide the same inherent cathodic protection to steel as galvanizing. The latter, with its metallurgical bond and thicker coating, enables a 'self-healing' effect where damaged areas are still protected by the surrounding zinc, extending the life of the structure.
Zinc plating's lower labor intensity contributes to its cost-effectiveness, especially for smaller parts and simpler components. However, this often translates to a shorter service life compared to galvanizing, particularly in harsh environments. The temperature sensitivity of parts is also a consideration: zinc plating, occurring at ambient temperature, is less likely to warp or damage heat-sensitive components, unlike galvanizing which can pose issues due to its high-temperature process.
While galvanizing can achieve coating thicknesses exceeding 100 microns, zinc plating's maximum thickness is usually around 25 microns, showcasing a significant difference in protective capacity. Furthermore, zinc plating often achieves superior surface finishes on complex designs, as it adheres better to intricate features. This makes it a prime candidate for applications where aesthetics are important, such as in jewelry or decorative automotive trims.
When considering the practical aspects of each process, the curing time can be a factor. Galvanized components, due to exothermic reactions during cooling, are often ready for use quickly. In contrast, zinc plating might necessitate a longer waiting period before handling to avoid damage.
Interestingly, the initially rough texture of hot-dip galvanized surfaces can evolve over time. A protective patina can develop, adding an appealing visual element that's desirable in certain architectural applications. It demonstrates that while the initial appearance of a surface may differ, long-term performance and aesthetic qualities can shift over time.
Overall, the choice between zinc plating and galvanizing involves a careful balancing act between cost, aesthetics, and durability. A thorough understanding of the specific application requirements, including anticipated environmental factors and performance needs, is crucial for choosing the coating method that offers the best combination of corrosion resistance, longevity, and cost-effectiveness.
Zinc Plating vs Galvanizing A Comparative Analysis of Corrosion Protection Methods in 2024 - Cost Analysis and Long-Term Value of Both Methods
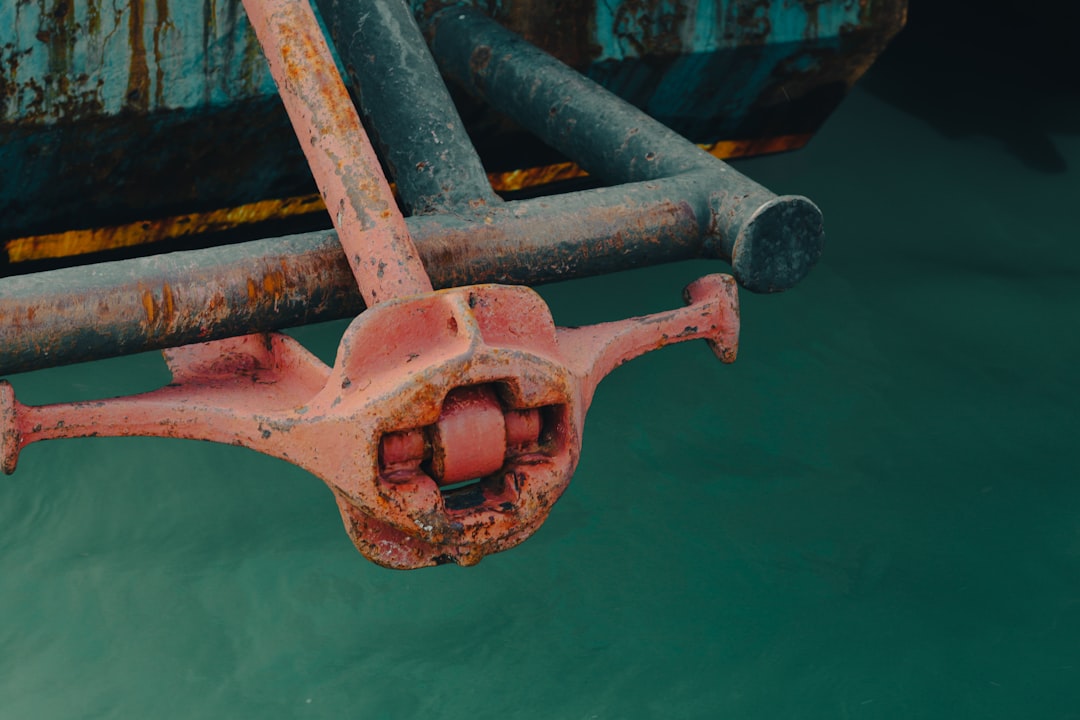
When comparing zinc plating and galvanizing in terms of cost and long-term value, we find significant differences that affect their suitability for different applications and environments. Zinc plating, with its thinner zinc coating, is generally more affordable upfront, especially when appearance and lower initial investment are key considerations. However, its moderate corrosion protection limits its effectiveness in challenging outdoor environments. This can lead to higher maintenance costs over time as the thinner layer degrades. In contrast, while hot-dip galvanizing is initially more expensive, it offers notably better long-term durability and corrosion protection. Due to its thicker, self-healing coating, the projected lifespan of galvanized steel can extend to 75 years, particularly in tough conditions. This means that a comprehensive life-cycle cost assessment usually shows that galvanizing becomes the more economical option for projects needing extremely reliable corrosion resistance, especially in outdoor applications or where harsh environments are encountered. Looking forward, ongoing advancements in both zinc plating and galvanizing technologies are continuously improving performance, promising a future with even better corrosion protection options.
Examining the long-term financial picture, hot-dip galvanizing can be surprisingly advantageous. Its thicker zinc layer not only extends the lifespan of parts in harsh environments but can potentially reduce overall costs by as much as 40% when you factor in maintenance and eventual replacements.
While initial costs for galvanizing are usually higher than zinc plating, its extended lifespan can make up for this in outdoor or industrial applications. If a coated component fails prematurely, you can easily end up spending far more than you'd initially save with a cheaper coating.
The protective layer formed by hot-dip galvanizing acts not only as a barrier but also undergoes a sort of mixing process during application, resulting in intermetallic compounds that enhance adhesion and corrosion resistance. This metallurgical bond is a unique benefit that zinc plating lacks.
In extreme environments, like coastal areas, galvanized steel offers a significant edge in performance over zinc-plated steel. Zinc plating often shows signs of corrosion within just a few years, while galvanized parts can often withstand decades of harsh conditions with minimal deterioration.
Zinc plating often requires more frequent re-coating in demanding environments because the thinner coating can get worn away more quickly. Galvanizing's substantial thickness provides a good reserve of protective zinc that can handle wear over longer periods.
It's interesting that while many people see zinc plating's smoother surface as always desirable, it can actually reduce the adhesion of paints in some applications. Galvanized surfaces, despite being rougher, can promote better adhesion for secondary protective coatings.
Analyzing wear resistance shows that the heavier, more robust galvanizing performs better than zinc plating in high-stress situations. This is due to the large amount of zinc, which acts as a solid defense against impacts and abrasion.
The durability of galvanized coatings is enhanced by their self-healing nature; the surrounding zinc can continue to protect even scratched areas. Zinc plating, however, lacks this feature, leading to a greater need for repairs and maintenance.
Research suggests that galvanized steel's corrosion behavior can improve over time due to protective layers that form naturally. However, zinc plating can suffer from issues like "white rust", particularly in humid environments, degrading its protective and aesthetic qualities.
When evaluating costs, it's easy to miss the impact of galvanizing on reducing maintenance and repair downtime. Structures that need minimal maintenance, as is typical with galvanized components, can see increased operational efficiency and savings that aren't always obvious in initial cost assessments.
Zinc Plating vs Galvanizing A Comparative Analysis of Corrosion Protection Methods in 2024 - Surface Finish and Aesthetic Considerations for Zinc Plating and Galvanizing
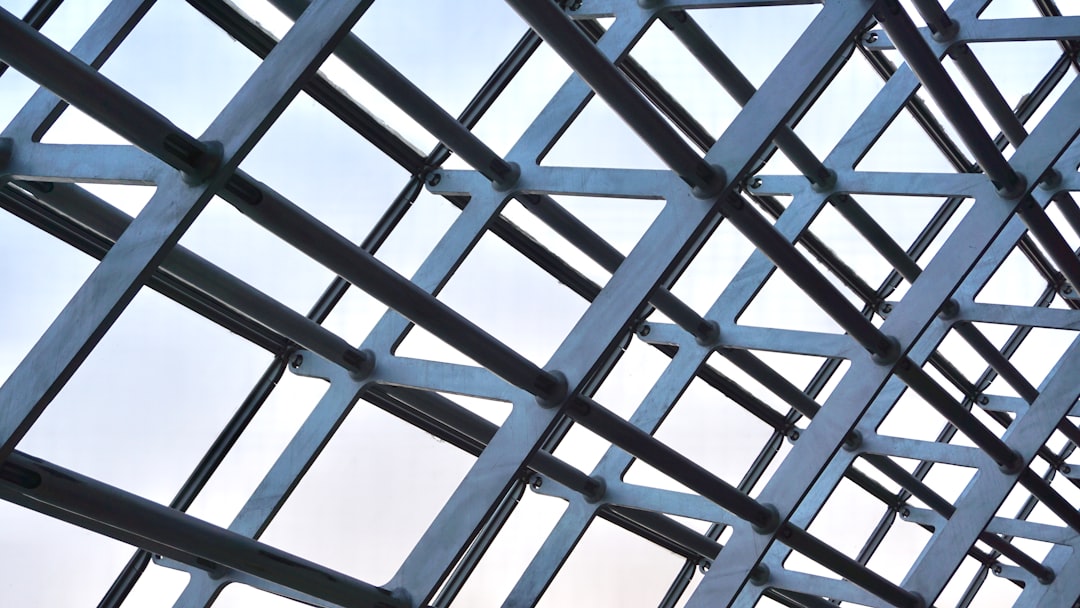
When it comes to surface appearance and aesthetic appeal in zinc plating and galvanizing, distinct differences come into play. Zinc plating generally produces a brighter and smoother surface, making it the preferred option for applications where visual appeal is a priority. This is particularly true for smaller, high-precision parts where a uniform finish is important. On the other hand, galvanizing, while offering superior long-term corrosion protection, results in a somewhat duller and often rougher finish. This is a direct consequence of the thicker coating created during the high-temperature immersion process. The contrasting aesthetic qualities can significantly influence the selection of a coating method based on the intended application.
However, it's crucial for users to carefully consider the trade-offs. The attractive finish of zinc plating might need to be weighed against its potential drawbacks, particularly its lesser durability and vulnerability to corrosion in certain environments. In harsh or outdoor conditions, the robust, thicker coating of galvanizing might be the more practical choice, even though its finish might be less refined. Ultimately, in 2024, the decision-making process for selecting a zinc coating requires careful consideration of both the desired aesthetic features and the necessary functional performance, acknowledging the compromises that may be involved in each method.
The surface finish produced by zinc plating can vary considerably, depending on factors like the chemicals in the plating bath and the environment during the process. This variability results in finishes ranging from shiny to dull, matte appearances, allowing for a degree of control based on the specific application needs.
Interestingly, the thinner zinc coating associated with zinc plating allows for more efficient inspection and quality testing during manufacturing. The quick assessment of surface quality provides a faster way to confirm that things are on track and can potentially lead to streamlined production without compromising quality control.
While hot-dip galvanizing often excels in providing maximal corrosion protection, the greater ability to influence the look of the zinc-plated surface can be crucial in applications where visual appeal is paramount. Industries like consumer goods and automotive, where a consistent and polished appearance is often required, can often benefit from zinc plating in this regard.
A technique called passivation, sometimes used on zinc-plated surfaces, not only enhances corrosion resistance but can also subtly shift the surface's appearance. It can lead to interesting iridescent colors, offering a unique aesthetic touch to the final product.
Despite its advantages, zinc plating can sometimes be impacted by a phenomenon known as "hydrogen embrittlement," particularly in high-strength steels. This susceptibility, which isn't usually seen with galvanized coatings, requires careful consideration when selecting surface treatments for components under significant mechanical stress.
Current research in zinc plating technology is driving the development of innovative nanostructured coatings. These specialized coatings have shown promising results in boosting corrosion protection while retaining a good visual appearance. It's this capability that's driving adoption in certain niche applications.
The issue of "white rust," a formation of zinc hydroxide, tends to be more associated with zinc plating due to the thinner zinc coating's propensity to react with humidity. Comparatively, galvanizing, with its thicker coating, is less prone to this issue, emphasizing a key performance difference between the two methods.
The mechanical performance of zinc plating is intertwined with the material it's applied to. For example, zinc-plated components could see a drop in fatigue strength over time when exposed to harsh mechanical environments. This potential reduction in performance is a factor not typically a concern with hot-dip galvanized parts.
The distinctive, rougher texture that results from hot-dip galvanizing, with its uneven surface finish, can surprisingly enhance the adhesion of subsequent coatings like paints. This naturally formed surface "tooth" offers a more robust bond than the typically smoother surfaces found after zinc plating.
Ongoing research in advanced coating technologies is exploring hybrid techniques, such as layering zinc plating prior to galvanizing. The potential is that these methods could offer the best of both worlds—blending the aesthetic attributes of plating with the superior corrosion resistance of galvanizing, opening up new possibilities for optimizing material properties in demanding applications.
More Posts from aistructuralreview.com: