Optimizing Symmetry Features in Ansys DesignModeler A Practical Guide for FEA Efficiency
Optimizing Symmetry Features in Ansys DesignModeler A Practical Guide for FEA Efficiency - Understanding Symmetry Types in DesignModeler
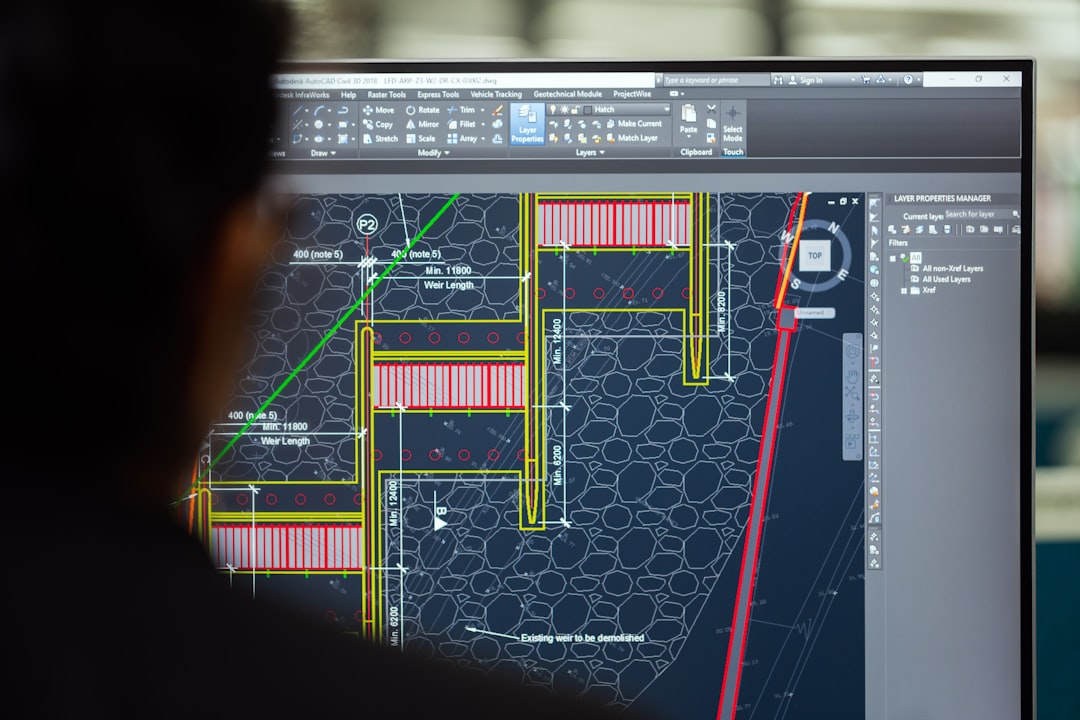
When setting up a model in Ansys DesignModeler, you can use symmetry to simplify it and make simulations run faster. Symmetry is achieved by defining a plane that cuts the model in half. This plane acts like a mirror, so only the portion of the model on one side of the plane needs to be built. The details of this symmetry are set in the "Details" view of the Symmetry Region object. Here you can choose different types of symmetry, and depending on your choice, the model can be classified as either a "Full Model" or a "Partial Model." The type of symmetry you choose directly influences how the model behaves during analysis.
One of the biggest advantages of using symmetry in FEA is that it reduces the number of elements in the model, which significantly speeds up analysis time. Imagine cutting a square in half with a diagonal line, you are working with only half the number of elements. Since each element requires computational power, you are cutting your simulation time down substantially. While this can be a huge benefit, it's also crucial to apply the right boundary conditions based on the symmetry you've chosen to make sure the results are accurate.
Symmetry is a powerful tool in DesignModeler, offering several types, including planar, axial, and rotational, to represent various geometric forms. Each symmetry type has a specific role in modeling, impacting the setup and execution of simulations. Leveraging symmetry can dramatically simplify complex geometries, cutting down modeling time and required computational resources. This is crucial for large assemblies, where the reduction in complexity can be substantial. The correct application of symmetry also leads to more precise boundary conditions. This ensures forces and constraints are applied accurately, enhancing the reliability of FEA results. It also helps maintain mesh quality and consistency, leading to better convergence during analysis and reduced computational overhead. For large models, symmetry drastically shrinks the problem size, enabling more efficient simulations without compromising accuracy. Beyond geometry simplification, identifying symmetry allows for better understanding of complex system interactions, making it easier to analyze results and troubleshoot potential issues. DesignModeler conveniently offers transformation tools that automatically generate symmetrical counterparts from the original geometry, streamlining the modeling process. However, a crucial aspect of using symmetry effectively is understanding its limitations. Misapplying symmetry, especially in asymmetric designs, can lead to inaccurate results. Therefore, careful consideration of geometric and loading conditions is vital for correct application. When conducting parametric studies, symmetry enables exploring a wider range of design variations while managing computational load. This facilitates efficient optimization of designs. Importantly, these symmetry types in DesignModeler integrate seamlessly with other Ansys simulation tools, creating a smooth workflow for comprehensive analysis across various engineering disciplines. While symmetry presents numerous benefits, its effective implementation relies on a thorough understanding of its different types, application limitations, and impact on simulation outcomes. This allows engineers to maximize its potential for efficient and accurate modeling within the context of their specific design goals.
Optimizing Symmetry Features in Ansys DesignModeler A Practical Guide for FEA Efficiency - Applying Boundary Conditions for Symmetry Planes
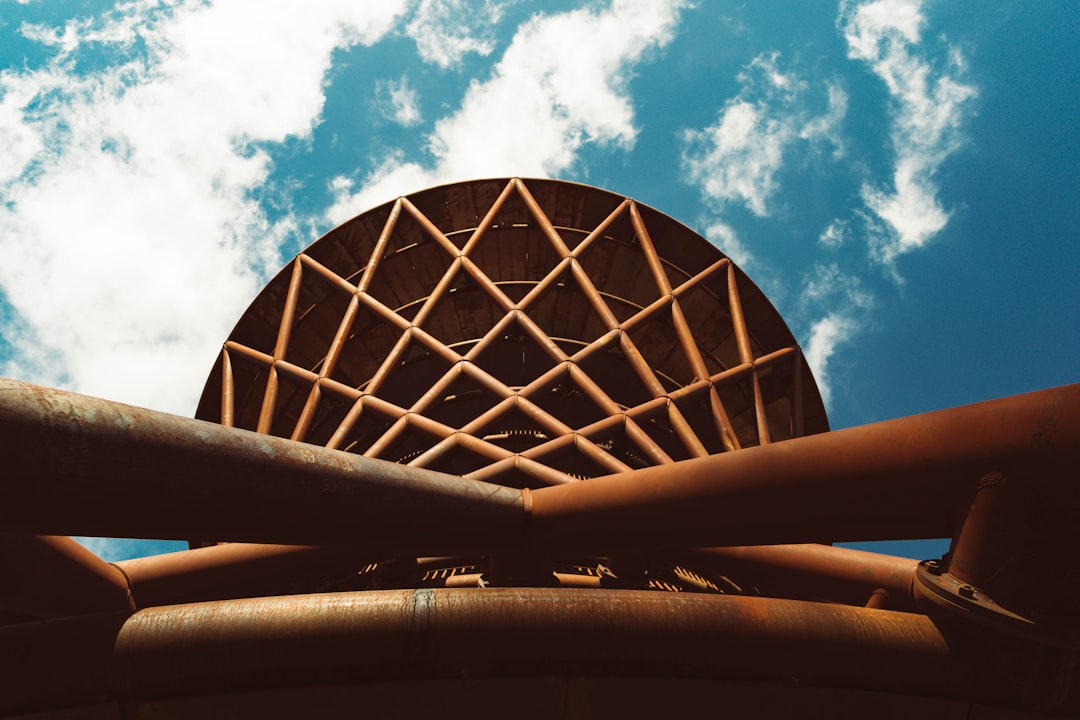
Applying boundary conditions on symmetry planes in Ansys DesignModeler is critical to achieving efficiency in finite element analysis (FEA). These conditions, based on the specific type of symmetry you've chosen, allow you to accurately simulate physical behaviors using only a portion of the full model. This leads to huge reductions in computing power and time. To ensure that your results are accurate, make sure to use appropriate restraints on the plane. For example, in some situations you might set vertical displacements to zero to maintain the correct behavior.
However, you need to be careful to apply symmetry only when the actual geometry reflects mirror symmetry. Otherwise, your analysis results may be misleading. Knowing the ins and outs of symmetry boundary conditions helps you to streamline the modeling process, resulting in more accurate FEA simulations.
Using symmetry in Ansys DesignModeler is a powerful technique to speed up simulations by reducing the model size. However, while it's great for simplifying geometry, the real challenge lies in applying the right boundary conditions. These conditions dictate how the model behaves along the symmetry plane, and getting them wrong can lead to significant errors in the final results.
One common issue is how the magnitude of boundary conditions affects the model's behavior. Even subtle changes in these conditions can drastically alter stress distribution and overall performance, making careful setup crucial. Another consideration is how symmetry affects dynamic analyses. In these cases, incorrect symmetry definitions might lead to unexpected resonances, making the validation process more complex.
Defining displacement constraints along the symmetry plane is another area that requires attention. Failing to properly define these can result in unintended reactions within the model, causing unrealistic deformations that skew the analysis. Complex loading scenarios, like thermal or pressure differentials, also demand careful application of boundary conditions along the symmetry plane to accurately capture the model's response.
Further complicating things are non-linear materials and large deformation effects, which often don't behave symmetrically. This makes evaluating how boundary conditions interact with material properties critically important.
To ensure accurate results, it's essential to validate symmetry assumptions against real-world test cases or experimental data, as real-world deviations from idealized behavior can sometimes make symmetric modeling inadequate. It's also wise to be prepared for iterative refinement even when using symmetry assumptions. Acknowledging its limitations helps engineers refine models iteratively, improving accuracy in subsequent simulations.
The challenges only grow when integrating thermal, fluid, or electromagnetic conditions into symmetric frameworks alongside structural loading. These multi-physics scenarios require a more sophisticated approach to accurately apply boundary conditions. And even with a well-defined symmetry, a poorly chosen mesh in the vicinity of symmetry planes can significantly impact computational efficiency and accuracy.
Ultimately, the decision to use symmetry in FEA involves balancing the potential for computational savings against the need for potentially complex boundary condition setups. The best approach depends on the specific project requirements and its associated complexity.
Optimizing Symmetry Features in Ansys DesignModeler A Practical Guide for FEA Efficiency - Managing Symmetry Regions in Mechanical Application
In the world of mechanical applications, effectively managing symmetry regions within finite element analysis (FEA) is key to achieving both efficient calculations and precise results. This is done by strategically defining planes of symmetry within the model, allowing for a significant reduction in the model's overall size. This reduction translates to faster simulations and a lighter computational load.
However, getting the boundary conditions along these symmetry planes right is crucial. Any errors here can lead to inaccurate results. It's worth noting that the early days of FEA relied heavily on symmetry as a way to overcome the limitations of computing power. While technology has advanced, symmetry still remains a valuable technique in modern FEA.
The success of managing symmetry regions depends on a very precise and thoughtful approach to setting up and verifying the model. This ensures the simulations faithfully capture the true physical behavior of the system being analyzed.
The symmetry features in Ansys DesignModeler are a powerful tool for optimizing the efficiency of finite element analysis (FEA). By leveraging symmetry, engineers can create simplified models that accurately represent the behavior of complex structures. While this approach offers significant advantages in terms of computational resources, careful consideration and implementation are crucial to ensure accurate results.
One of the key benefits of symmetry is its ability to represent complex geometries with a reduced number of elements. This not only decreases computational time but also reduces memory usage. However, symmetry can also have unintended consequences. For example, the application of symmetry can significantly affect dynamic analysis. If symmetry is not accurately applied, unexpected resonant frequencies might emerge, requiring further validation. This highlights the need to carefully analyze the impact of symmetry on the dynamic performance of the model.
Another area where symmetry requires special attention is in the realm of non-linear materials. The assumption of symmetry might not be valid for materials that exhibit non-linear behavior, particularly when subjected to large deformations or changing load conditions. It is critical to consider how symmetry can mask these complex material responses, leading to overly simplistic results.
The precision of boundary conditions is also critical when using symmetry. Minor mistakes in the application of boundary conditions along symmetry planes can lead to substantial differences in the stress distribution within the model. This sensitivity underscores the importance of meticulous setup and careful consideration of real-world loading scenarios.
Finally, while symmetry can be applied to asymmetric designs, it is essential to recognize potential limitations and ensure that assumptions align with the actual geometry. By carefully exploring hidden symmetry within these designs, engineers can benefit from its efficiency without compromising accuracy.
Overall, using symmetry effectively requires a balance between the advantages of computational efficiency and the potential challenges associated with its implementation. By meticulously applying and validating symmetry assumptions, engineers can leverage this powerful tool to enhance FEA analysis while ensuring accurate and reliable results.
Optimizing Symmetry Features in Ansys DesignModeler A Practical Guide for FEA Efficiency - Implementing Symmetry During Analysis Process
Implementing symmetry during the analysis process within Ansys DesignModeler is essential for achieving efficient finite element analysis (FEA). This involves carefully defining planes of symmetry within the model, leading to a significant reduction in model complexity, ultimately resulting in faster simulations and optimized resource utilization. Introducing symmetry regions simplifies the modeling process, but it also demands accurate application of boundary conditions to ensure accurate simulation results. It's crucial to carefully manage these symmetry settings while being mindful of their limitations to ensure accurate representation of the true behavior of complex systems in structural analysis. In essence, a deliberate approach to symmetry implementation offers significant advantages in both computational efficiency and accuracy.
Symmetry is a powerful tool that can streamline finite element analysis (FEA) by reducing the model size and computational demands. It achieves this by dividing the model along a plane, mirroring one half to represent the whole. This results in significant reductions in simulation time and resource usage, particularly for large, complex models. However, the simplicity of this technique shouldn't mask the challenges of proper application.
Ensuring that symmetry assumptions accurately reflect the physical system under analysis is crucial. A simple validation using experimental data or established models can help prevent inaccurate or misleading results.
It is also important to acknowledge the complex interactions that arise when applying symmetry to dynamic analyses. While symmetry can be helpful for reducing computational burden, incorrect implementation can introduce unintended vibrational modes, making validation more challenging.
The boundary conditions along symmetry planes are very sensitive, and even slight variations in their definition can lead to large differences in stress distribution within the model. This underscores the importance of meticulous setup and careful consideration of the real-world loading scenario.
It is also worth noting that symmetry may not be as reliable when dealing with non-linear materials, especially under large deformations or changing load conditions. These materials may exhibit behavior that doesn't conform to the symmetry assumption, leading to inaccurate stress analysis and potentially misleading results.
Hidden or imperfect symmetry can exist even in asymmetrical designs, presenting opportunities for simplification. However, a keen eye and cautious application are critical to avoid inaccurate results.
Mesh quality in regions near symmetry planes can also significantly affect the accuracy of simulations. Poorly constructed meshes in these areas can lead to convergence issues that nullify some of the computational advantages of applying symmetry.
Implementing symmetry in multi-physics applications, which combine various physical phenomena, requires a thorough understanding of their interactions to accurately capture the model's behavior.
Furthermore, even with a well-defined symmetrical model, iterative refinement may be necessary to improve accuracy based on insights gained during analysis. This approach acknowledges that real-world systems are often more complex than idealized representations.
It is important to remember that the use of symmetry in FEA was initially motivated by limitations in computing power. Although technology has progressed, the technique remains valuable today, providing a way to streamline analyses and enhance computational efficiency.
Optimizing Symmetry Features in Ansys DesignModeler A Practical Guide for FEA Efficiency - Optimizing Mesh Generation for FEA Efficiency
Optimizing mesh generation is a critical step in improving finite element analysis (FEA) efficiency, especially when using software like Ansys. A well-constructed mesh is crucial for obtaining accurate simulation results. It is a balancing act between representing the model's detail and keeping the analysis computationally feasible. Various techniques exist to achieve this balance, such as Mesh-Based Defeaturing and Virtual Topology, which aim to simplify complex geometries without sacrificing essential features. The decision of whether to use shell or solid elements is also important. Choosing the right type of mesh element, along with the choice of shapes like triangular or quadrilateral, can greatly impact both the accuracy of the analysis and the computational resources required. Ansys provides tools to help with this, such as curvature-based refinement settings, which allow you to fine-tune the mesh density according to the complexity of your model, leading to improved solver performance. Ultimately, understanding mesh generation's finer points can make a huge difference in optimizing your FEA results and how effectively you use resources.
Mesh generation is often overlooked, but it is crucial for obtaining accurate and efficient results in finite element analysis (FEA). An optimized mesh can greatly improve the efficiency and accuracy of your simulations. A well-designed mesh ensures a uniform distribution of elements throughout the model, leading to more reliable stress calculations and reducing the occurrence of numerical artifacts. Furthermore, strategically refining the mesh in areas of high stress gradients allows for more accurate results with fewer elements, making the most of your computational resources.
Modern mesh generation tools are becoming increasingly sophisticated, capable of automatically recognizing geometric features like fillets and holes. These tools adapt to the model's complexity, saving time and ensuring that crucial regions are appropriately meshed. Some tools even employ adaptive meshing techniques, refining the mesh as the solution progresses. This allows for greater accuracy in regions of high stress, such as at stress concentration points, while maintaining a coarser mesh in less critical areas.
The power of parallel processing allows for even large assemblies to be meshed quickly without sacrificing performance. And, by carefully balancing mesh quality and size with the expected convergence tolerance of the FEA simulation, engineers can optimize for speed while maintaining the accuracy of their results. This balance is especially crucial for large simulations where computational resources are often stretched thin.
In cases involving fluid-structure interactions (FSI), incorporating boundary layer meshes is essential for capturing the flow characteristics necessary for accurate simulation results. This is critical in fields like aerospace and automotive engineering where accurate structural integrity assessments are paramount.
Validation of mesh strategies through benchmarking helps to ensure that the chosen approach is not only well-suited to the model but also trustworthy for critical decision-making. Advanced mesh generation tools often include built-in error assessment features that predict potential inaccuracies, helping engineers proactively make adjustments and reduce post-processing corrections and wasted computational resources.
By leveraging these capabilities, engineers can define custom mesh quality criteria based on specific project requirements. This tailored approach allows for optimization aligned with the unique demands of the simulation, ultimately leading to improved results with efficient resource use.
Optimizing Symmetry Features in Ansys DesignModeler A Practical Guide for FEA Efficiency - Addressing Challenges in Topology Optimization with Symmetry
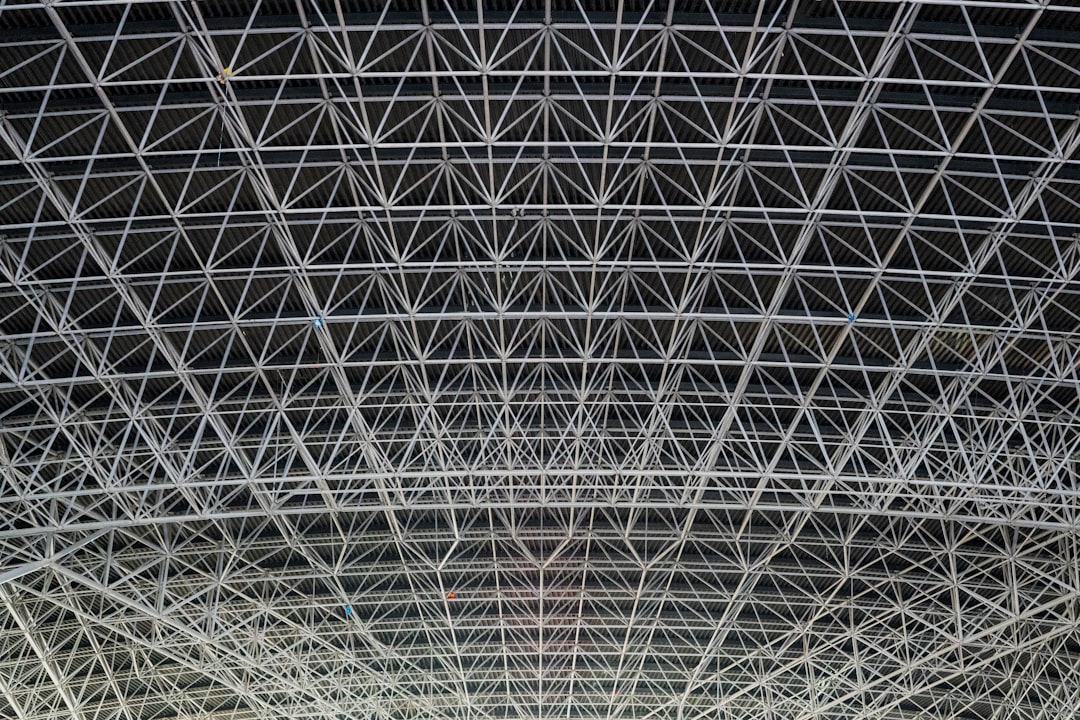
Topology optimization with symmetry offers a powerful way to streamline designs and improve computational efficiency. But symmetry also brings its own set of challenges, particularly when dealing with complex structures and demanding engineering goals. One issue is that symmetry can sometimes lead to multiple, equally valid solutions, making it difficult to pinpoint the optimal design. Additionally, accurately applying boundary conditions along the symmetry planes is critical for obtaining reliable results. This becomes even more important when working with multiple engineering disciplines, like structural and thermal analysis, where the interactions between different factors become increasingly complex.
Even with a well-defined symmetry, there are situations where the symmetry assumption can break down. For example, materials that don't behave predictably under high loads or changing conditions can't always be treated as symmetrical. Similarly, the dynamic behavior of structures can be affected by symmetry in unexpected ways, requiring additional analysis and verification. Engineers need to carefully consider these limitations and balance the computational benefits of symmetry against the need to accurately reflect the real-world behavior of their designs.
Topology optimization, a powerful tool for design optimization, presents challenges when it comes to symmetry. While symmetry is often a boon for efficiency in simulations, misapplying it to non-symmetric designs can lead to incorrect results. This underscores the critical need to assess the actual geometry before introducing symmetry.
Symmetry also has an intriguing effect on dynamic analyses. The simplified model, while computationally efficient, may not accurately capture the nuances of the original system's behavior, particularly in transient simulations. This can lead to the introduction of unexpected dynamic modes or resonance frequencies.
Furthermore, achieving accurate results using symmetry hinges upon the careful application of boundary conditions. Even small discrepancies in the definition of these conditions can significantly alter the stress distribution within the model. This necessitates meticulous setup and thorough understanding of real-world loading scenarios.
The use of symmetry in simulations also has limitations when applied to non-linear materials. These materials might exhibit non-symmetric behavior under varying loads or large deformations, making symmetry assumptions less reliable in these situations.
Mesh quality is another important aspect to consider when employing symmetry. The areas around symmetry planes need careful mesh design. Poor mesh quality in these regions can lead to reduced accuracy, convergence problems, and even negate some of the computational advantages of using symmetry.
Interestingly, hidden symmetries might exist within seemingly asymmetric designs. If identified and properly utilized, these hidden symmetries can simplify models and streamline computational efforts. However, careful validation is critical to ensure that the assumptions made based on this hidden symmetry align with real-world conditions.
When dealing with multi-physics simulations that combine various physical phenomena, the integration of symmetry becomes complex. The accurate application of boundary conditions in these cases requires understanding the interplay between different physical aspects.
It's important to remember that symmetry techniques in finite element analysis (FEA) initially stemmed from the limitations of early computing technologies. While computing power has advanced, symmetry remains a valuable tool for achieving computational efficiency. However, engineers need to carefully consider its limitations and potential consequences.
Even with a well-defined symmetrical model, an iterative approach to model refinement can be beneficial. This allows engineers to compare initial symmetry assumptions against real-world data to continuously improve the accuracy of simulations.
Finally, symmetry proves to be an invaluable tool when conducting parametric studies. It allows engineers to explore a wider range of design variations while maintaining computational efficiency. This balance between efficiency and rigorous exploration is crucial for evaluating the parametric influence on overall performance.
More Posts from aistructuralreview.com: