Sealtight Connectors Enhancing Structural Integrity in Wet Environments
Sealtight Connectors Enhancing Structural Integrity in Wet Environments - Moisture-resistant design prevents electrical system failures
The ability of a design to withstand moisture is paramount to preventing electrical system failures. This is particularly true in locations that experience consistent dampness or direct water exposure. The utilization of Sealtight connectors plays a key role, not just in strengthening the physical structure, but also in ensuring the longevity of these systems by providing an efficient barrier against moisture and the damaging effects of the environment. In industries like food processing and construction, where wet conditions are the norm, the use of liquid-tight conduits has proven beneficial. These solutions impede the entry of moisture, leading to a longer lifespan for the electrical components within. Employing robust moisture-resistant connectors and durable construction materials directly impacts the overall reliability of critical safety systems, allowing them to function effectively under challenging circumstances without failing due to electrical issues. This emphasis on moisture resistance is critical to reducing the risks involved with sensitive electrical systems when exposed to demanding environments.
The concept of moisture-resistant design is crucial for maintaining the reliability of electrical systems, particularly in environments where water intrusion is a constant threat. While it's been widely recognized that moisture can lead to various forms of degradation and failure within these systems, preventing its entry through clever design is becoming increasingly vital.
We often see the effects of moisture on electrical components as corrosion, which, concerningly, can accelerate significantly with temperature increases. This suggests that a combination of humidity and even moderately warm environments can create conditions that quickly compromise the functionality of sensitive electrical parts. This, in turn, can result in a cascade of problems, from degraded insulation to eventual failures in the entire system.
A challenge in preventing failure is the fact that the presence of moisture in cabling can drastically diminish insulation resistance, which is a key parameter for safety and performance. This issue is compounded by the fact that in many electrical applications, it isn't practical to completely eliminate the possibility of water coming into contact with wiring. Thus, the focus shifts towards proactive design choices that can resist and mitigate the effects of water ingress.
One approach that seems promising in the quest to mitigate moisture damage is the incorporation of materials with inherent water-repelling properties. Materials like thermoplastic elastomers seem to be suitable, as they can handle both the penetration of water and the stresses they may experience in practical applications. This offers a longer-term solution compared to many traditional materials which have proven susceptible to degradation.
While some standards such as ingress protection (IP) rating help to categorize the moisture-resistant qualities of components, it's crucial to understand the limits of these ratings in the context of the specific application. A well-defined understanding of the environmental stresses a system will encounter, for example, can help ensure that suitable products and designs are specified. In turn, this aids in ensuring that moisture damage is minimized over the system's lifetime.
One area that deserves attention is the potential for moisture in the air to influence the dielectric properties of certain materials. These dielectric properties are vital for a well-functioning electrical system, so understanding the implications of changing these properties due to humidity is crucial for designing reliable systems. It seems that certain materials, under a range of humidity conditions, may exhibit undesirable changes. Therefore, the focus on selecting materials and system configurations that resist moisture damage under a range of anticipated conditions must be prioritized.
It's likely we will see the application of materials such as hydrophobic coatings expand in the future. These coatings are applied to surfaces with the aim of repelling water and reducing any unwanted effects of surface moisture. If properly implemented, these coatings may help to mitigate the accumulation of water droplets that can potentially lead to short circuits or failures.
While preventative measures can mitigate a lot of water damage, regular inspections and maintenance of electrical systems is still important. There are many sources of water intrusion, and a lot of it depends on application and environment. The goal is to implement designs that minimize maintenance activities, not eliminate them completely. Perhaps as a way to minimize ongoing issues, the design of electrical systems and applications that experience a degree of water intrusion might benefit from preventative and proactive designs as well as maintenance schedules.
Sealtight Connectors Enhancing Structural Integrity in Wet Environments - Flexible metallic vs PVC sealtight conduits comparison
When evaluating flexible metallic and PVC sealtight conduits for use in wet environments, several factors come into play. Flexible metallic conduits typically excel in environments requiring high durability and corrosion resistance, making them suitable for demanding applications like car washes or industrial processing facilities. Their inherent strength can also be beneficial in heavy-duty applications. Conversely, PVC conduits offer a more economical and lightweight solution, which can be advantageous in installations where ease of handling and cost are critical considerations. Notably, PVC's non-conductive properties can be valuable in situations where electrical conductivity is a concern. Furthermore, PVC demonstrates adequate performance in wet or damp environments, and even in underground installations, highlighting its versatility. The decision between these two conduit types ultimately hinges on the specific environmental challenges and application demands. Understanding the trade-offs between durability, cost, and weight is crucial for selecting the most appropriate conduit for ensuring the reliability and long-term functionality of electrical systems exposed to wet conditions.
Flexible metallic and PVC sealtight conduits each present distinct advantages and disadvantages when considering their suitability for various applications, particularly in wet environments. Metallic conduits, often constructed from materials like galvanized steel or aluminum, offer robust structural integrity and the ability to withstand significant physical stress and temperature fluctuations, making them ideal for demanding industrial environments where these factors are prominent. They also inherently provide electrical grounding, crucial for safety. However, their susceptibility to corrosion in harsh environments, even with galvanization, is a potential drawback. While some metallic conduits may have fire resistance properties, PVC, due to its inherent nature, can be a more cost-effective option and generally weighs less, potentially simplifying installation.
PVC conduits, on the other hand, often excel in scenarios where chemical resistance is paramount. They are naturally resistant to many corrosive substances, making them a common choice in industries like chemical processing. Their flexibility and lower weight can make installation simpler, particularly in tight spaces or when dealing with large projects where minimizing weight is desirable. Their inherent non-conductivity, however, necessitates separate grounding methods, which can increase design complexity. While PVC may be an initial lower-cost option, it may be less durable and potentially less fire-resistant depending on formulation and additives. Furthermore, their temperature resilience tends to be limited to a narrower range compared to metallic alternatives, influencing their utility in extremely hot or cold conditions.
Both material types are marketed as having water ingress protection, a critical factor in wet environments. While some PVC versions do have an emphasis on this, it may require extra sealing efforts at connection points. Metallic options often have tighter seals at connections, making them more suitable in settings where water intrusion is a major concern. From an aesthetic perspective, metallic conduits might be preferred in some visible applications because of their industrial look. While PVC is also available in various colors, it may not always match design preferences for certain architectural settings.
The selection of a conduit type must consider the specific application's environment and requirements. Factors such as cost, weight, corrosion resistance, fire safety, grounding considerations, and temperature extremes all must be analyzed to ensure that the chosen solution optimally supports the long-term function and safety of the electrical system. It's crucial to recognize that the total cost of ownership is not only the initial purchase but also maintenance and replacement costs over a longer lifespan, often favoring higher initial costs of metallic for harsh environments. In conclusion, each conduit type possesses a unique set of characteristics that render it more suitable for certain applications than others. A thorough evaluation of the environment, operating conditions, and desired performance parameters is needed to make an informed decision.
Sealtight Connectors Enhancing Structural Integrity in Wet Environments - Waterproof sealing mechanism using silicone gaskets
Silicone gaskets are a crucial component in achieving waterproof sealing within connector systems, especially important for maintaining the structural integrity of electrical systems in wet environments. Silicone, a material prized for its ability to withstand both water and high temperatures, acts as a barrier that prevents moisture from penetrating connectors, safeguarding sensitive electronics within. The design of these waterproof connectors, when combined with the inherent properties of silicone gaskets, significantly extends the lifespan and reliability of electrical systems exposed to damp or wet conditions. From everyday electronics to more specialized applications like outdoor gear, silicone gaskets offer a protective layer against the potential harm of moisture intrusion. It's important to acknowledge, however, that proper installation and careful consideration of the intended use are key to ensuring that these seals fulfill their purpose and contribute to the long-term integrity of the system. The effectiveness of a silicone gasket's waterproof seal depends heavily on its correct application, highlighting the importance of installation methods.
Silicone, a synthetic rubber, has garnered attention for its waterproofing capabilities in electrical applications due to its inherent resistance to both heat and water. It's this combination of properties that makes it a compelling choice for sealing mechanisms in connectors, particularly in wet environments. This approach effectively insulates and waterproofs electronic components by sealing any cracks or openings that might allow moisture ingress. While it’s often used to seal wire entries, silicone's versatility also allows it to be shaped into different forms such as gaskets, O-rings, and specialized seals, each providing a specific sealing function within connectors.
One noteworthy attribute of silicone is its flexibility across a broad temperature range. This characteristic is particularly valuable in applications subject to significant thermal fluctuations due to environmental changes or operational factors. The ability to maintain its elasticity under these conditions helps ensure a consistent and reliable seal. It's worth noting that silicone's hydrophobic nature – its resistance to water absorption – contrasts with some other rubber materials that can readily absorb moisture over time. This intrinsic characteristic safeguards the silicone's mechanical properties, guaranteeing it retains its ability to effectively seal in environments with persistent water exposure.
While silicone's resistance to a wide array of chemicals, including oils and solvents, is often touted as a benefit, the potential long-term degradation of other gasket materials due to such exposure is a pertinent issue to consider. However, this resistance isn’t universal. Silicone's low compression set is another desirable attribute. This property implies that it can bounce back to its original form after being compressed, making it well-suited for applications with dynamic loading conditions, thus maintaining effective seals over time. Furthermore, silicone's vibration dampening capabilities are particularly relevant in mechanical and electrical applications where vibrations can potentially degrade seals and connected components. This property can help extend the lifespan of associated elements.
It's also important to recognize silicone's resistance to UV light and ozone exposure. This resistance is crucial for ensuring long-term sealing integrity in applications located outdoors or in high-altitude settings where environmental conditions can accelerate the degradation of many materials. While certain formulations are deemed food-safe, allowing for their use in applications where contact with food products is unavoidable, the question of biocompatibility with different food types is still an area of ongoing study. Silicone’s ability to be custom-molded into diverse shapes and sizes is a significant advantage for manufacturers who want to tailor seals to specific design constraints and optimize the functionality of their products.
However, it's not all sunshine and roses. While silicone is touted as an excellent electrical insulator, the reality of performance in demanding conditions is complex. The level of performance can depend on the specific formulation used and how it is integrated within the connector. There are also a few drawbacks; certain formulations can become more brittle or vulnerable to degradation at very high temperatures or under persistent stress. Certain grades of silicone can dissipate static charge, providing an extra measure of safety in environments where the risk of electrical discharges is a concern. While there is a growing body of knowledge regarding its effectiveness, further research is still necessary to ensure the reliability of silicone-based sealing mechanisms in demanding, real-world scenarios.
While silicone gaskets represent a significant advancement in sealing technologies, the design of robust and reliable waterproof connectors requires a holistic approach that accounts for a multitude of environmental conditions and stresses. Understanding the strengths and limitations of different sealing materials, like silicone, remains critical for successfully tackling the challenge of designing connectors that function reliably in demanding wet environments.
Sealtight Connectors Enhancing Structural Integrity in Wet Environments - Marine applications benefit from saltwater protection
Marine environments pose a unique challenge due to the constant exposure to saltwater, which is highly corrosive. This corrosive nature can quickly degrade many materials commonly used in marine applications, such as steel and aluminum. To combat this, designers and engineers need to incorporate specific features and materials to protect structures and components. For instance, using materials inherently more resistant to saltwater, like certain types of plastics or composites, can improve longevity. Additionally, protective coatings or treatments, like electroplating, can significantly extend the lifespan of metal components. The choice of materials and construction techniques must carefully consider the harsh environment, as even minor compromises can lead to premature degradation and potentially safety issues. Ensuring that the structural integrity of a marine application is maintained in the face of such a challenging environment is a key design consideration. The use of materials like geopolymer concrete, which naturally resists corrosion, highlights how careful material selection can contribute to longer lasting and safer marine structures. In essence, addressing the corrosive effects of saltwater is vital for ensuring the continued reliability and safety of marine infrastructure.
Marine environments pose unique challenges for materials and designs due to the constant presence of saltwater. Saltwater's corrosive nature, stemming from galvanic corrosion, can rapidly degrade materials, particularly when different metals are in contact. While stainless steel generally offers better corrosion resistance than standard steel, certain grades, such as 316 stainless, are specifically chosen for marine applications due to their improved resistance to the chlorides present in saltwater. This careful material selection is critical for maintaining structural integrity.
The dielectric properties of insulating materials can be significantly impacted by saltwater. This means that components used in marine environments need to maintain their electrical insulation characteristics even under constant saline exposure to prevent electrical failures. Researchers are exploring the use of hydrophobic coatings to address this challenge by creating water-repelling surfaces on connectors and other components, thus reducing the accumulation of water and the risk of corrosion. This effort highlights the need for solutions tailored to marine applications.
The interplay of temperature fluctuations and different materials can pose challenges as well. Thermal expansion rates differ considerably between metals and non-metals, resulting in mechanical stresses that can disrupt seals if not addressed within the design. This is especially relevant for marine environments with wide temperature variations. Furthermore, advancements in sealing technology, such as seals that adjust to changing pressures, are being implemented in connectors for marine applications subjected to high mechanical loads.
In a move towards customization, manufacturers are increasingly employing custom-molded connectors made from sophisticated elastomers. These are specifically engineered to withstand the harsh marine environment and provide superior moisture resistance, contributing to the overall durability and performance. However, marine conditions expose structures to a complex combination of temperature fluctuations, pressure changes, and moisture, potentially degrading conventional sealing mechanisms. Finding solutions that accommodate these combinations is crucial.
Furthermore, components exposed to saltwater are frequently subject to UV degradation from sunlight. This factor necessitates the utilization of UV-stabilized materials for systems both submerged and exposed to sunlight. It’s clear that the lifespan and reliability of connectors in these conditions are strongly dependent on proper assembly and effective sealing, emphasizing the significance of rigorous quality control during the manufacturing process. These conditions drive the need for careful evaluation of material choice, design, and manufacturing to ensure long-term performance in the marine setting.
Sealtight Connectors Enhancing Structural Integrity in Wet Environments - UL-listed sealtite conduits for direct burial installations
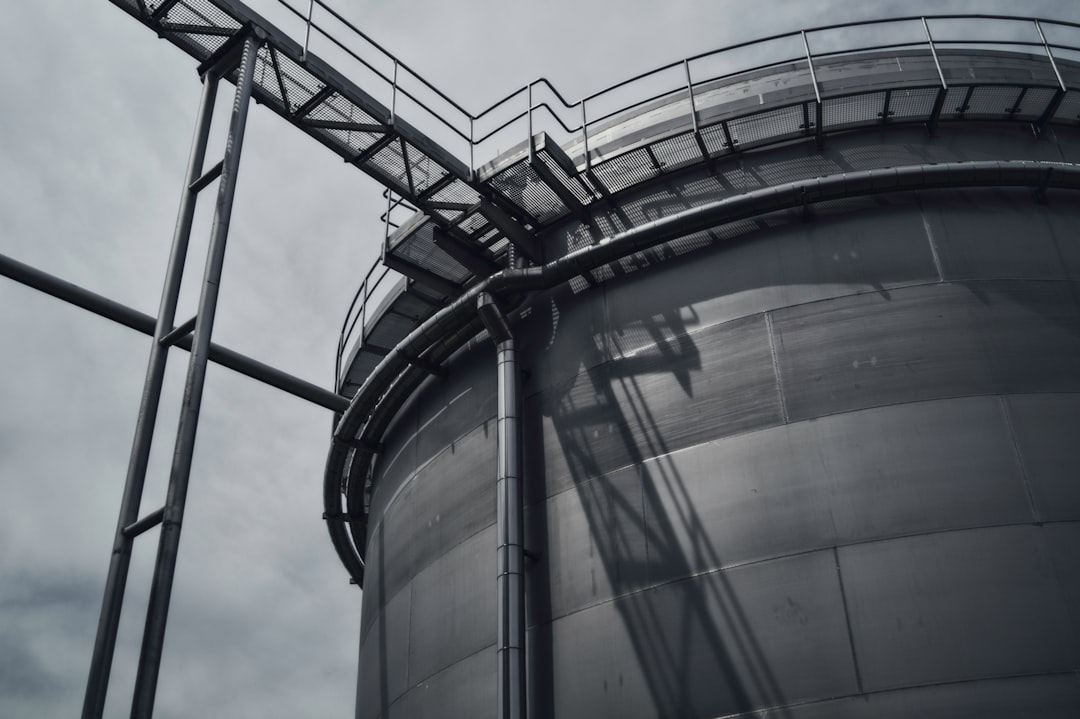
UL-listed Sealtite conduits are specifically engineered for underground installations, safeguarding electrical wiring from the harsh conditions encountered beneath the surface. These conduits are made from hot-dipped galvanized steel, providing a high level of protection against both crushing and corrosion. They are also designed to operate across a broad range of temperatures, from -46°C to 105°C, making them suitable for various climates and environments. Beyond temperature tolerance, these conduits are liquid-tight, effectively preventing moisture from damaging the wires they enclose. This characteristic, coupled with their suitability for use in Class I, Division 2 hazardous locations, makes them particularly well-suited for applications where water and potentially flammable substances are present. However, it's crucial that the conduits are clearly labeled as "DIR BURIAL" or "DIRECT BURIAL" to ensure they are correctly used in underground settings. Users should also ensure their installation complies with local electrical codes and standards, which might include specific burial depth requirements. While these conduits offer a robust solution for direct burial applications, they aren't suitable for every scenario, and adhering to proper usage guidelines is crucial for ensuring system reliability and safety.
UL-listed Sealtite conduits, having passed rigorous testing, are deemed suitable for direct burial installations. This means they're designed to protect electrical wiring from the harsh conditions found underground. Their approval encompasses a wide range of temperatures, from -46°C to 105°C, making them suitable for diverse climates. This temperature tolerance, while a positive feature, might still require consideration of material properties at the extremes.
These conduits excel in their liquid-tight and corrosion-resistant nature. It's worth noting that they're also suitable for hazardous environments classified as Class I, Division 2. However, for underground use, the conduits need to be explicitly labeled as "DIR BURIAL" or "DIRECT BURIAL" for proper identification. It would be useful if a more universal standard existed for marking, as this seemingly minor detail could lead to confusion or misapplication.
The material used, continuously interlocked hot-dipped zinc galvanized steel, provides good crush and corrosion resistance. While this is a positive, we should keep an eye on how the zinc coating will hold up under long-term exposure to soil and moisture. They have a certain degree of flexibility in design, particularly when flexibility and protection against liquids or vapors are needed. Their use is not limited to underground applications; they can be employed in exposed and concealed locations as well.
There seems to be an emphasis on using only straight fittings for direct burial—no 45 or 90-degree fittings are permitted. This constraint might present challenges in certain installations that would benefit from flexible layouts. The question arises whether future design iterations will integrate a larger variety of fittings while maintaining a high degree of water tightness.
UV resistance is another characteristic of these conduits, which is useful if they are exposed to sunlight during or after installation. However, this UV protection is generally not tested as stringently as in photovoltaics or other outdoor applications, so further investigation into specific levels of resistance would be beneficial. As with all installations, the local building codes and standards related to burial depths must be consulted and adhered to for compliance and safety. This is particularly relevant for projects across different jurisdictions.
Interestingly, it appears that Anamet Electrical Inc. has the exclusive manufacturing rights for these conduits. It would be interesting to see if this monopoly will continue, or if other manufacturers will eventually introduce competitive products in the future. We need to monitor how this limited supply impacts the long-term cost of these conduits and availability.
Sealtight Connectors Enhancing Structural Integrity in Wet Environments - Corrosion-resistant galvanized steel core enhances durability
The core of Sealtight connectors, constructed from galvanized steel, is designed to withstand the corrosive effects of moisture, thereby significantly enhancing the overall durability of the connector. This galvanized steel core, formed through a process of hot-dipping, provides a strong and resilient foundation for the connector while also offering exceptional resistance to rust and deterioration. The protective zinc coating that results from this process ensures the connector can reliably perform in environments with high humidity or direct water exposure, ultimately extending the lifespan of the electrical systems they support. While the use of galvanized steel provides substantial protection against corrosion, it is important to acknowledge that the effectiveness of this protective layer can be influenced by factors like environmental conditions and duration of exposure. Therefore, ongoing assessment of the long-term performance and potential degradation of the galvanized steel core is crucial to maintain the reliability and structural integrity of these connectors in demanding applications.
The core of these Sealtight connectors is constructed from hot-dipped galvanized steel, which offers a compelling combination of durability and corrosion resistance. This approach utilizes a layer of zinc to protect the underlying steel. When exposed to moisture, the zinc corrodes preferentially, sacrificing itself to prevent the steel from rusting. This sacrificial protection extends the service life of the steel core in challenging environments, including those with high humidity or exposure to various pollutants, as outlined in national standards.
The choice of galvanized steel also provides a degree of thermal stability, enabling it to function reliably across a considerable temperature range, from well below freezing to moderately high temperatures. However, this temperature range has limits. In very high temperatures (over 200°C), the zinc layer itself can degrade, potentially reducing its protective qualities.
Galvanization doesn't just provide corrosion protection; it also has an influence on the electrochemical properties of the connector. By altering the surface characteristics, it can help prevent certain types of corrosion, particularly galvanic corrosion that arises from dissimilar metals being connected within the same electrical system.
Furthermore, the zinc layer provides a measure of enhanced mechanical strength, making the connectors better able to withstand stresses due to physical impacts or vibration. It's this inherent strength that benefits applications where the system might be subjected to harsh handling or demanding environments.
Research suggests that galvanized steel connections can offer a significantly extended lifespan compared to standard, uncoated steel. This longevity can reach up to several decades in some settings. While this is a desirable trait, the long-term performance in a particular application still depends on things like the severity of the environment and how the connectors are installed. While it reduces maintenance needs, galvanized steel does require occasional inspection, especially at connections where the zinc layer may be compromised.
The corrosion-resistant nature of galvanized steel makes it a suitable choice for systems with other materials, offering improved overall durability. But it's crucial to consider that the zinc coating can slightly impact the electrical conductivity. This change in impedance may need to be accounted for in specific electronic designs to prevent issues. The suitability of galvanized steel for long-term use and its interaction with other materials highlight its utility, but potential concerns about maintenance, high-temperature limitations, and electrical conductivity should be weighed against its corrosion resistance and mechanical benefits.
More Posts from aistructuralreview.com: