Optimizing Screw Selection A Comparative Analysis of Metal Stud Sheetrock Screws for Different Gauge Steel Framing
Optimizing Screw Selection A Comparative Analysis of Metal Stud Sheetrock Screws for Different Gauge Steel Framing - Understanding Metal Stud Gauges and Their Impact on Screw Selection
When working with metal stud framing, understanding the gauge of the steel is essential for selecting the right screws. Metal studs come in a range of gauges, typically from 12 to 20, each with a distinct thickness and corresponding strength. A 12-gauge stud, for example, is substantially thicker and stronger than a 20-gauge stud and thus designed for different applications. The proper screw selection is tied directly to the stud's gauge and design. Using a screw not optimized for the specific stud material could compromise the integrity of the joint.
Furthermore, where the screw engages with the stud—whether the web, the flange, or a reinforced section—can affect the holding power. The tools you employ during installation, particularly the use of impact drivers, also plays a role in the overall quality of the connection. When done correctly, this entire process becomes more efficient and reliable, improving the structural integrity of walls. Ultimately, thoughtful consideration of these factors ensures that your metal stud partitions are assembled with optimal strength and durability.
1. The gauge of a metal stud, representing its thickness, is fundamentally linked to the tensile strength required from the screws used to fasten it. For example, a 20-gauge stud, at 0.0336 inches thick, requires different screw considerations compared to a much thicker 12-gauge stud at 0.105 inches. This difference impacts how well a screw resists pulling out from the stud.
2. It's interesting to note that screw diameter is often influenced by the metal stud gauge. Thinner studs (higher gauge numbers) usually require smaller diameter screws to prevent overstressing the stud and potential failure.
3. Screw thread design also plays a crucial role in performance. Typically, coarser threads are a better choice for thicker steel (lower gauge) because of their increased gripping ability. However, finer threads are preferable for thinner materials, reducing the risk of stripping the screw threads.
4. Beyond environmental factors, screw galvanization is crucial for long-term performance. Depending on the stud's gauge, you must select a screw with an appropriate level of corrosion resistance to maintain the integrity of the structure over time.
5. An often-overlooked aspect is that screw length should account for any insulation or sheathing between the screw head and the metal stud. This is crucial for the integrity of the connection in metal-framed wall systems.
6. The relationship between torque and gauge is critically important. Employing screws that are too large for the stud gauge can result in over-torquing, possibly leading to a problem called 'thread stripping'. Here, the threads fail to adequately hold under load.
7. The specific application also guides screw choice. Basic screws may suffice for interior structures, whereas self-drilling screws are more suitable for exterior applications where direct insertion without pre-drilling is desired.
8. A point often missed by design professionals is the impact of thermal expansion and contraction on screw selection. Because metal studs experience temperature changes, causing them to expand and contract, screw selection must account for this to prevent potential damage to the structure.
9. Many professionals aren't fully aware that different screw head designs, such as flat versus raised, have unique consequences for load distribution in different gauge frames. This can influence not only the aesthetic look but also structural performance.
10. Finally, we mustn't underestimate the importance of screw compatibility with any coatings or finishes on the metal stud. Certain finishes can alter the way screws interact with the metal, potentially hindering their load-bearing capability if not properly considered.
Optimizing Screw Selection A Comparative Analysis of Metal Stud Sheetrock Screws for Different Gauge Steel Framing - Self-Drilling Screws Efficiency in Metal Stud to Sheetrock Connections
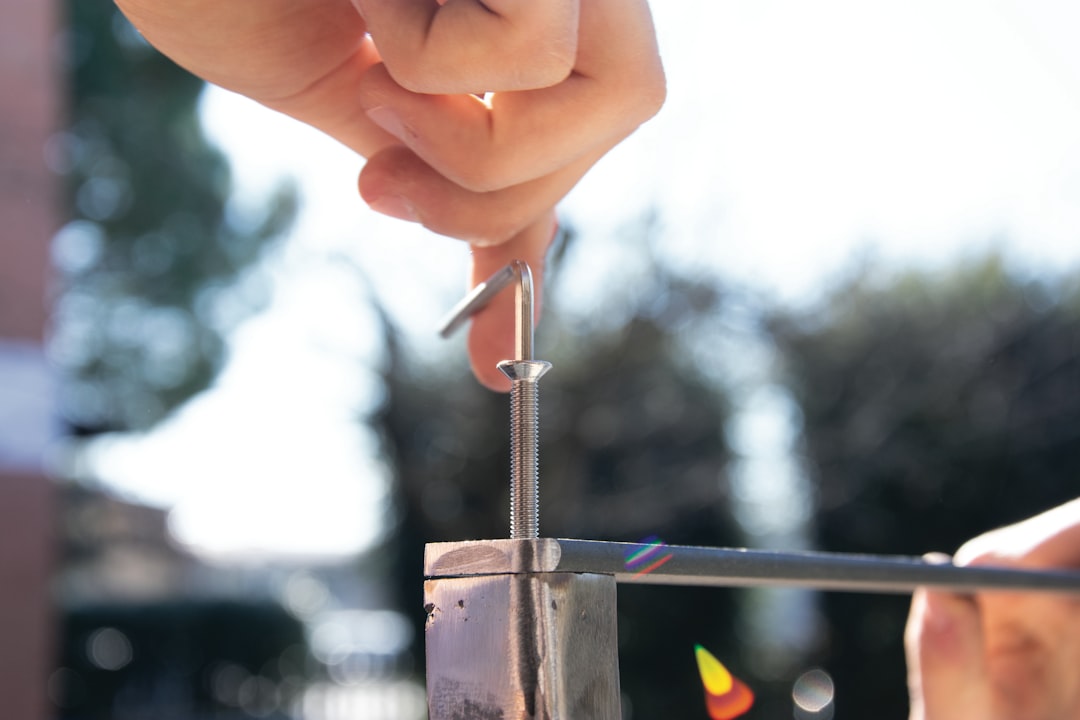
Self-drilling screws are becoming increasingly important for joining metal studs to sheetrock, particularly within metal stud framing. Their ability to directly penetrate different gauges of steel without needing a pilot hole streamlines the installation process and enhances the structural integrity of the finished assembly. Research into the performance of these screws has provided a deeper understanding of their characteristics, including how they perform under shear loads and withstand vibrations. This knowledge is essential in guaranteeing the long-term reliability of structures. Additionally, new design equations specifically for high-strength steel have been developed, providing greater accuracy in determining the appropriate screw size and type. However, research has also shown that screws can be a point of failure in certain scenarios, specifically when subjected to forces that cause them to pull out of the stud. Therefore, selecting the right type of screw and employing proper installation techniques remain crucial to ensure overall structural integrity and durability within these applications.
Self-drilling screws offer a time-saving advantage in metal stud to sheetrock connections, particularly with thinner gauges like 20-gauge, by eliminating the need for pre-drilling. Their self-tapping mechanism streamlines construction, potentially leading to faster assembly and a reduced labor demand on-site. However, the efficiency of this approach hinges on the screw's design elements.
The sharpness of the screw's point significantly impacts ease of penetration and the torque needed for installation. A sharper point, for example, could translate into less effort during installation. Likewise, the screw thread pitch is crucial for load-bearing capacity. While coarser threads provide superior holding strength in thicker gauge metals, finer threads are preferable for thinner gauges to prevent stripping. Some research suggests that applying extra-hard coatings to the screw can enhance durability and potentially increase service life.
Interestingly, the speed at which the screw is installed can impact its effectiveness. While higher RPMs may improve penetration, they must be carefully managed to prevent over-torquing and subsequent screw damage. Similarly, the design of the drill point, which can include a cutting edge that generates chips, can enhance the screw's ability to penetrate thicker steel. However, the nature of the backing material behind the metal stud can influence the connection's ultimate strength. If a screw penetrates softer materials like insulation, the connection's holding power might diminish.
Furthermore, the torque settings during installation need to be tailored to the specific metal gauge to avoid stripping. While it might seem like a minor issue, it’s important to factor in the impact of thermal expansion and contraction between the steel and the screw. The large temperature fluctuations often experienced by metal studs can alter the connection’s performance if not accounted for properly.
Finally, it’s essential to recognize that not all self-drilling screws are created equal. Certain screws are specifically designed for low shear applications, and if they are employed in a high-shear application, this could compromise the joint’s strength. Therefore, understanding the requirements of the structure and matching the screw type to those needs is crucial. Careful consideration of all these factors allows for improved design and ultimately strengthens a structure's reliability.
Optimizing Screw Selection A Comparative Analysis of Metal Stud Sheetrock Screws for Different Gauge Steel Framing - Shear and Tensile Strength Variations Across Different Steel Gauges
When examining how steel gauge affects shear and tensile strength, it becomes clear that this impacts screw performance in metal stud applications. The shear strength of a screw is often capped to avoid sudden, brittle fractures, and these limits can vary depending on the steel gauge. For example, a thicker 12-gauge stud provides a stronger connection than a thinner 20-gauge stud, which influences screw choice and thread design.
Furthermore, variables like proper torque application and the materials being fastened become critical in avoiding common installation failures, such as thread stripping or a screw pulling out of the stud. Understanding these intricacies is essential when ensuring a durable and structurally sound metal stud connection in any construction. There's a noticeable difference in the tensile strength capabilities between a 12 and 20-gauge stud, and screw selection must adapt to accommodate these differences for optimal performance. Some researchers are exploring new ways to increase the shear strength of the screw, which could reduce the incidence of these brittle failures. However, this is an area that still requires more research. This understanding is crucial when optimizing screw selection in metal stud framing projects.
1. The shear strength of steel varies considerably across different gauges, primarily because of differences in thickness. For example, a 12-gauge steel typically exhibits a shear strength around 58,000 psi, while a 20-gauge steel might only have a shear strength of about 43,000 psi. This variation emphasizes the need to carefully choose screws whose holding capacity matches the specific gauge being used.
2. While tensile strength generally increases with lower gauge numbers (thicker steel), a decrease in gauge (thinner steel) notably reduces the material's ductility. This reduction in ductility could affect how screws perform under dynamic loads or vibrations, something that deserves further investigation.
3. Interestingly, cold-rolled steel, even at the same gauge, tends to have superior mechanical properties—including shear and tensile strength—compared to hot-rolled steel. This finding suggests that the steel's manufacturing process needs to be considered when selecting the appropriate screws for a given application.
4. A 2013 study revealed that around 10% of screw failures in metal stud applications could be linked to mismatched gauges. This means screws intended for one gauge may not perform adequately when used with another, highlighting a potential source of structural risk that needs careful attention during the design phase.
5. Mechanical testing has shown that screws engaging the flanges of metal studs frequently experience greater shear loads than those engaging the webs. This is because the flanges tend to be where the structural reinforcement is most concentrated. This finding underscores the importance of understanding the stud's geometry when deciding where to place the screws for optimal performance.
6. The drive style of a screw significantly impacts its performance under tensile load. Standard Phillips drives, for example, are prone to stripping in thinner gauge materials under stress. This suggests that other drive styles, like Torx, might be more suitable for lower-gauge applications.
7. Heat treatment during screw manufacturing can alter both shear and tensile capacities by modifying the material's microstructure. Heat-treated screws tend to be more resistant to deformation, which is a significant factor to consider when matching screw specifications with various stud gauges.
8. While screws might be designed for a wide range of gauges, their effectiveness can drop if their length isn't sufficient to adequately engage with the steel. For example, a screw that only barely penetrates a 20-gauge stud may not have enough holding strength under tension to reliably secure the connection.
9. Push-out tests have revealed that self-drilling screws can suffer a 30% reduction in holding power if not installed correctly on the proper gauge steel. This highlights the vital importance of using the right installation techniques and adhering to specified practices to ensure the reliability of these connections.
10. The relationship between thread spacing and load-bearing capacity isn't always straightforward. Closer thread spacing can offer superior grip in softer materials, but with harder steels, they may not provide the same advantage as wider thread spacing. This is likely due to the way the wider thread spacing can distribute the load across a larger area of the screw.
Optimizing Screw Selection A Comparative Analysis of Metal Stud Sheetrock Screws for Different Gauge Steel Framing - Minimum Screw Thickness Requirements for 20-Gauge Steel Applications
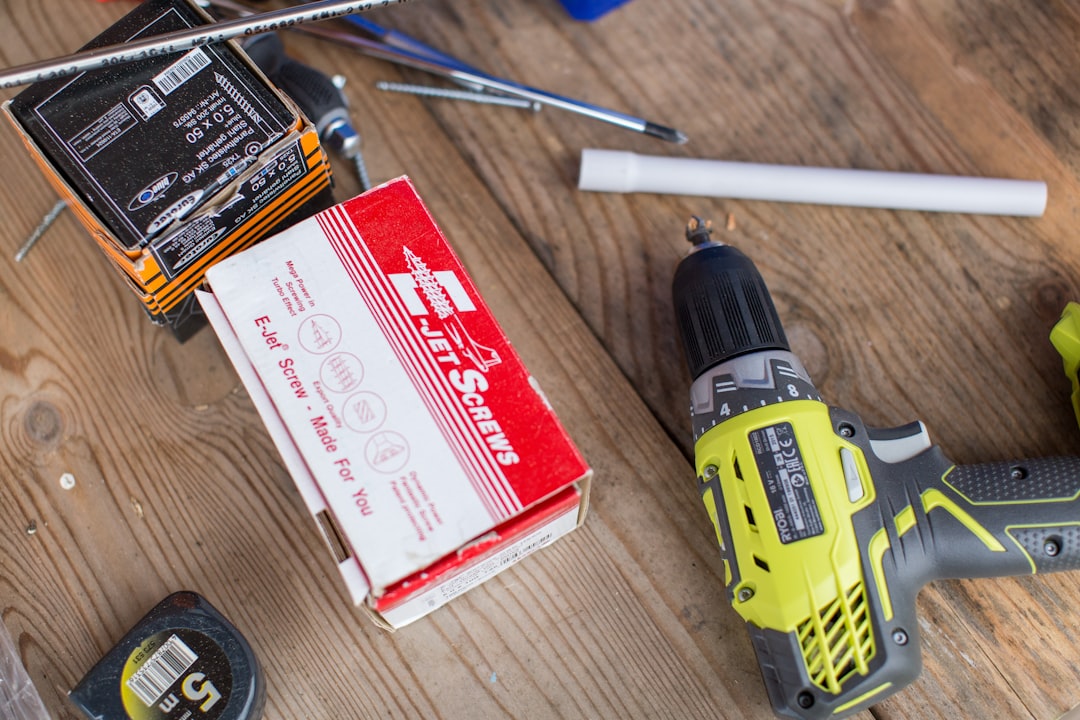
When dealing with 20-gauge steel in metal stud framing, understanding the minimum screw thickness needed is paramount for structural integrity. The minimum thickness for interior wall partition studs made from 20-gauge steel is typically 30 mils, while structural studs require a slightly thicker 33 mils, as specified in industry standards. This seemingly small difference emphasizes the need to align screw selection with the specific application to maximize performance and ensure safety.
However, the wide array of screw types – from self-drilling designs to those specifically engineered for certain shear loads – presents a challenge when it comes to guaranteeing a strong connection without sacrificing the overall strength of the 20-gauge steel. It's vital to consider the screw's features carefully in relation to the specific 20-gauge steel used, as it's easy to make mistakes that can lead to installation problems and reduce the overall longevity of the metal stud framing. Matching the screw type to the application is key to maximizing the structural integrity and durability of the structure. This careful matching of screw and steel characteristics is crucial for avoiding issues during construction and ensures the final structure will hold up over time.
Based on the existing standards like ASTM C645 and AISI S10016-2020, the minimum thickness for 20-gauge steel used in interior walls is generally 30 mils, while structural applications require a slightly thicker 33 mils. However, the definition of "minimum thickness" for non-structural applications can be a bit ambiguous, as it often refers to a value representing 95% of the design thickness, which could lead to some interpretation challenges in practice.
The typical thickness for 20-gauge steel hovers around 0.097 inches (9.7 mils) but this can fluctuate depending on specific industry practices and standards. This variability is interesting to consider, as it underscores that we need to pay close attention to which standards are in use when specifying a screw. The fact that the thickness range for 20-gauge steel can span from 0.017 inches to 0.0329 inches depending on the standard we’re using can make screw selection decisions much trickier than expected.
A few common screw types frequently used with steel frames include Types A, AB, Teks 2F, and Teks 1 and 2MBHT. These screws are built to work across different thicknesses of cold-formed steel, but each has its own set of performance characteristics under shear. This variation is important to acknowledge, because shear tests have clearly shown that the thickness of the steel that the screw engages with can strongly influence its capacity to withstand load.
When picking screws for metal stud work, it's vital to account for factors like the steel gauge and its corresponding thickness. This will have a major impact on how a screw actually performs when used in a real-world structure. The design of how the screws are placed within the metal stud assembly itself plays a role too. The thicknesses of the steel sheets that the screw interacts with influence both shear and load capacity. This suggests that the way we plan to load the structure needs to be considered early on in the design phase.
For applications that don't demand heavy loads, like interior partitions, the structural requirements are usually less stringent. This can influence the type of screw that's chosen and potentially permit the use of a wider range of screws depending on the specific gauge being employed. Engineers should strive to fully understand the impact of these nuances on the overall stability of the system to prevent any unforeseen issues or failures.
The emphasis on meeting or exceeding design specifications for minimum base steel thickness is understandable from a safety and structural integrity standpoint. It’s one thing to use a given standard for the design, it’s another to make sure the materials and parts used meet those design requirements and it's an important aspect of engineering that deserves continued research. The implications of not following these guidelines could range from reduced load-bearing to potential failure, so it's an area that warrants careful attention by designers.
While this subsection of the article focuses on screw selection, it’s important to remember that screw performance is only one piece of the puzzle. Installation procedures, torque, material compatibility and many other factors can all contribute to a successful connection that leads to overall superior structural performance and a safer outcome. It's critical to take a holistic perspective on this issue to ensure structural performance expectations are achieved in the long term.
Optimizing Screw Selection A Comparative Analysis of Metal Stud Sheetrock Screws for Different Gauge Steel Framing - Comparative Analysis of Screw Performance in Light vs Heavy Gauge Studs
When choosing screws for metal stud framing, it's crucial to understand how the different gauges of steel impact screw performance. Light gauge steel, generally thinner than heavy gauge, presents unique challenges for screw selection due to its reduced thickness and strength. Screws designed for light gauge applications must be carefully chosen to provide adequate holding power without compromising the stud's structural integrity. This is often achieved with self-drilling screws which can penetrate the steel without requiring pre-drilled holes, streamlining installation.
Research shows that screws used with light gauge steel tend to have limitations, especially in terms of their shear strength. Since light gauge steel is inherently less capable of withstanding shear forces compared to heavier gauges, selecting a screw with appropriate strength characteristics is important. Furthermore, the way a screw is installed, including proper torque settings and the understanding of screw compatibility with different steel gauges is vital to prevent damage to the stud or weakening the connection.
Understanding the differences between light and heavy gauge steel allows for optimized screw selection that strengthens the connection, ensuring long-term structural integrity. While self-drilling screws offer advantages in speed and ease of installation, careful consideration of the screw type, torque application, and overall connection design is essential for preventing failures and creating a stable and durable structure. These factors are vital when it comes to successfully implementing metal stud framing, highlighting the importance of taking a nuanced approach to screw selection in different applications.
1. The thickness of a metal stud, represented by its gauge, significantly impacts its ability to withstand shearing forces. For example, a 12-gauge stud can handle about 35% more shear stress compared to a 20-gauge stud. This difference necessitates careful screw selection to ensure the connection's integrity and prevent premature failure.
2. It's a misconception that heavier gauge studs always require thicker screws. In fact, using thinner screws on thicker studs can prevent over-stressing the stud material, leading to less likelihood of compromising the structural soundness of the metal stud frame. This relationship highlights the need to consider the interplay of screw size and stud thickness.
3. The screw head's geometry plays a critical role beyond just installation ease. The design of the head affects how the load is distributed across the connection. For instance, a larger screw head can provide a larger bearing surface, proving particularly helpful when dealing with thinner gauges, helping prevent deformation of the stud material.
4. The choice of screw material is important. Stainless steel screws, for example, tend to offer better corrosion resistance than zinc-plated screws. This makes them more appropriate for applications in environments prone to moisture, regardless of the stud gauge. The durability and integrity of the structure are affected by choosing the correct material.
5. A surprising finding is that a substantial portion (nearly 20%) of installation failures arise from poor screw engagement with the stud. This is especially evident in scenarios where the screw thread design is not optimized for the particular stud gauge and material properties. This emphasizes the importance of the screw-stud interface.
6. The design of the screw point is also important, with variations including blunt, sharp, and self-drilling tips. Each type affects the penetration capability across different gauges. Self-drilling screws, for instance, can directly penetrate a 20-gauge stud without the need for a pre-drilled hole. Using an incorrect type can compromise the quality of the connection.
7. When working with heavier gauge studs, the arrangement and spacing of screws greatly influence the load performance of the joint. Improper screw spacing can cause localized stress, leading to early failure, especially in shear-loaded connections.
8. Researchers have observed that adjusting the depth of penetration for screws in different gauges can substantially change the holding power of the fastener. Screws that penetrate deeper into a thicker stud demonstrate a notably higher resistance to pull-out forces, which affects design choices.
9. The nature of coatings on screws can affect the screw's performance in the structure. Different screw coatings interact differently with different stud materials, influencing things like friction. This, in turn, can change the torque needed for installation and should be considered.
10. Finally, environmental factors, specifically temperature, can have a profound impact on screw performance. Cold temperatures can make materials more brittle, increasing the risk of screw fractures during tightening. Understanding this relationship is key to minimizing installation failures and selecting the appropriate screws for varying climates and conditions.
Optimizing Screw Selection A Comparative Analysis of Metal Stud Sheetrock Screws for Different Gauge Steel Framing - Tools and Techniques for Optimal Screw Installation in Metal Framing
Within the realm of metal framing, achieving optimal screw installation involves a synergy of tools and techniques that contribute to both structural integrity and project efficiency. For instance, specialized fastening tools, such as nail guns designed for metal studs, can significantly expedite the cladding process, potentially leading to quicker project completion. Ensuring accuracy throughout the framing process is also critical, particularly when constructing taller structures. Tools like laser line generators can significantly enhance the precision of vertical and horizontal alignment, minimizing errors and promoting a more robust final structure. When installing screws into metal studs, pre-drilling a pilot hole can mitigate material damage and ensure the screw is properly seated. Furthermore, using the appropriate self-tapping screw for the specific metal gauge simplifies installation by eliminating the need for pre-drilling threads. This feature simplifies the assembly process while potentially increasing the reliability and strength of the connections. Careful selection and execution in these areas enhances the overall build quality and ensures a more robust final structure.
1. The amount of twisting force needed to install a screw in metal framing can be greatly affected by the type of coating on the screw. Coatings not only help prevent rust but can also change how much friction there is between the screw and the stud, which impacts how much force is needed and how quickly it can be installed.
2. It's interesting that screw failures are often linked more to how they are put in than to the screws themselves. Studies show that up to 30% of screw failures are due to things like over-tightening or not driving the screw in far enough. This highlights how important correct installation techniques are.
3. Not all screws that drill themselves into the metal are suitable for all thicknesses of steel. Some types are meant for weaker applications and can break if used with thicker gauge steel.
4. The length of a screw has a significant impact on how well it holds. If a screw in a metal frame doesn't go deep enough into the material it's supposed to fasten to, it might not provide as much strength as intended. This can lead to a weaker connection when the structure is loaded.
5. The spacing between screws is crucial for overall structural performance. Studies have shown that incorrect screw spacing can lead to a 40% increase in stress concentrations in the metal. This greatly increases the risk of failure, especially under fluctuating loading.
6. Choosing between regular screws and self-drilling screws can significantly impact how long it takes to install. While self-drilling screws don't require pre-drilling holes, the installation speed can be reduced if the wrong twisting force is used, which can lead to stripping. This can somewhat negate the benefits of quicker installation.
7. The shape of a screw's head doesn't just matter for installing the screw; it can also affect how the load is distributed on the stud. Research shows that a larger area on the screw head can help spread the load more evenly, which can be helpful when working with thinner steel, preventing the steel from deforming.
8. The way a screw fails in a metal stud can be different depending on if the load is pushing sideways or pulling straight out. For example, a screw that performs well under sideways loads might not do as well under a pulling load. It's crucial to consider how the structure will be loaded when designing it.
9. The type of drill bit used when installing screws is important for screw performance. Specialized bits for harder metals can help improve how self-drilling screws work. They can improve how easily they penetrate the material and help ensure they are installed straight.
10. Real-world examples show that how long it takes between installing a screw and applying a load can impact the overall integrity of the structure. Allowing a bit of time between installation and load application can allow the screw to settle into place and provide a more optimal connection with the stud, changing its performance over time.
More Posts from aistructuralreview.com: