Understanding ANSI Class 150 Pressure Ratings A Comprehensive Guide for Engineers
Understanding ANSI Class 150 Pressure Ratings A Comprehensive Guide for Engineers - ANSI Class 150 Pressure Rating Basics and Applications
ANSI Class 150, the lowest commonly used pressure rating in the ASME B16.5 standard, provides a foundational understanding of safe operating conditions for pipe flanges, particularly in situations involving lower pressure. For carbon steel flanges, the standard specifies a maximum pressure of roughly 285 psi at a comfortable 100°F. However, it's vital to acknowledge that temperature fluctuations considerably impact this rating. As temperatures rise, the permissible pressure decreases; at 400°F, the maximum pressure drops to about 180 psi, illustrating the need for careful consideration of temperature derating. The practicality of Class 150 is seen in its frequent use in applications such as water conveyance and air systems, demonstrating its utility in a range of industrial contexts. When selecting components, engineers must carefully assess the interplay of material choices and operating temperatures, as these elements fundamentally affect the overall safety and performance of the piping system. A thorough understanding of the basics within the ANSI Class 150 standard is thus paramount for ensuring reliability and integrity in the design of piping systems, especially in less demanding pressure scenarios.
ANSI Class 150, a foundational pressure rating within the ANSI framework, typically handles pressures up to 285 psi at a standard 100°F for carbon steel. However, this pressure capability isn't static. As temperatures rise, the maximum allowable pressure significantly diminishes. For instance, at 400°F, the pressure limit drops to roughly 180 psi. These pressure-temperature relationships are integral for system safety and form the basis of ASME B16.5, a key standard that governs flange design and specifications. ASME B16.5 categorizes flanges into seven pressure classes, with Class 150 being the lowest commonly utilized rating. It's important to note that this pressure rating doesn't solely depend on the pipe material but is also influenced by flange design, gasket characteristics, and the specific fluid being handled.
The application of Class 150 spans a wide range of industries, including water supply networks, air distribution systems, and processes involving low-pressure chemicals. Its widespread adoption stems from a good balance of reliability and affordability compared to higher pressure classes. Materials play a crucial role, and the allowable pressure can fluctuate based on the chosen material and operating conditions. It's worth noting that the ANSI B16.5 standard itself covers a broad spectrum of pipe sizes, ranging from 0.5 inches to 24 inches in nominal diameter.
To ensure safety, engineers must consider temperature derating factors. This is particularly important when working with steel pipelines and flanges where temperatures deviate from the standard 100°F. While hydrostatic testing, which is typically conducted at 1.5 times the rated pressure, plays a key role in validating the ratings, potential stresses due to mechanical loads can impact long-term performance. These stresses can lead to phenomena like creep and fatigue, making regular inspection and maintenance crucial.
Despite being a relatively lower pressure rating, ANSI Class 150 is employed in critical settings like oil and gas production, chemical manufacturing, and water treatment. Yet, one common pitfall is the assumption that all ANSI-rated components are fully interchangeable. Manufacturing variations and tolerance differences across vendors can influence component compatibility and performance. Therefore, engineers working with ANSI Class 150 systems must deeply understand the specifics of the operating environment to ensure system reliability, especially given the potential for failures in these vital systems.
Lastly, a critical element that is often overlooked is the interaction between flanges, gaskets, and bolts in Class 150 assemblies. Maintaining correct alignment and adhering to appropriate torque specifications is essential for achieving leak-free and safe operations. These seemingly minor factors can profoundly impact the overall system's integrity and reliability, underscoring the importance of detailed design considerations for even the seemingly simplest systems.
Understanding ANSI Class 150 Pressure Ratings A Comprehensive Guide for Engineers - Temperature Effects on Class 150 Flange Pressure Limits
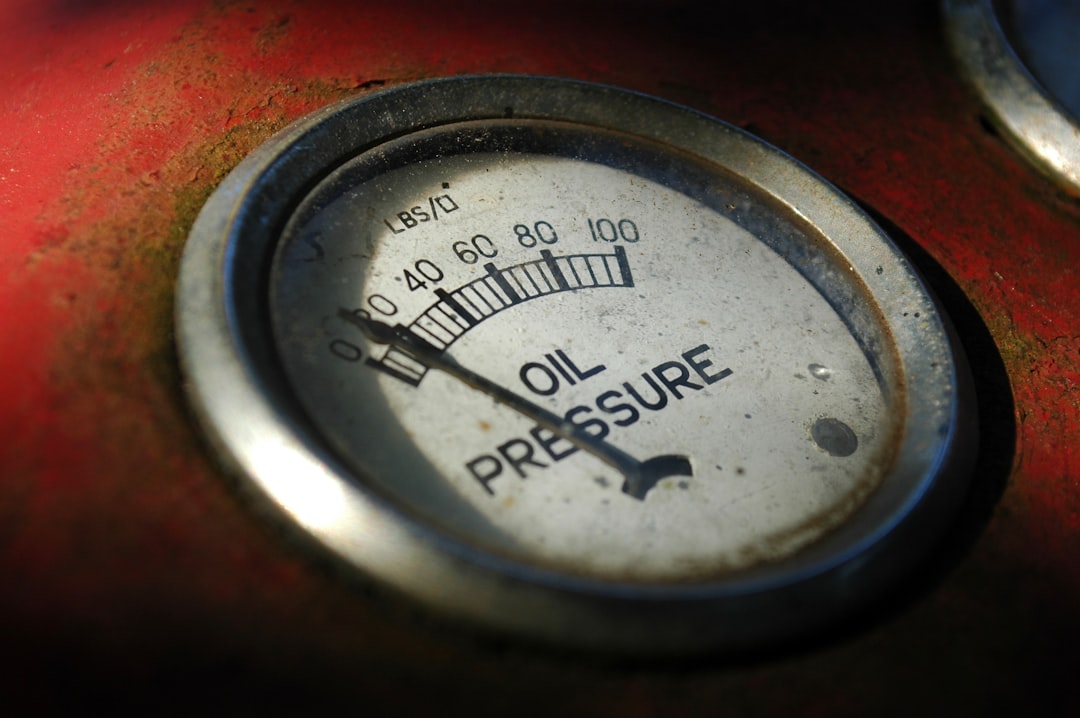
The pressure limits of ANSI Class 150 flanges are significantly influenced by temperature. Higher temperatures generally result in lower allowable pressures. For example, carbon steel flanges, which can handle up to 285 psi at 100°F, see a substantial decrease in this limit as temperatures climb. At 400°F, the maximum pressure drops to about 180 psi. This relationship between temperature and pressure is crucial for engineers to understand, particularly when dealing with various materials. Different materials have different strengths at different temperatures, and recognizing these variations is key for safe and reliable piping system designs, especially when dealing with fluctuating temperatures. By taking these factors into account, engineers can effectively manage system integrity and ensure safety across a wide array of applications. It's important to avoid operating outside these limits as it can lead to unexpected failures in critical systems.
While Class 150 flanges, as per ANSI B16.5, offer a foundational pressure rating of up to 285 psi at 100°F for carbon steel, the impact of temperature on these limits is not as straightforward as it might seem. The relationship between pressure and temperature isn't linear; it's intricately tied to the specific material used. For instance, carbon steel's yield strength takes a noticeable hit at higher temperatures, requiring more careful pressure calculations in such situations.
Material choice becomes even more crucial as different materials react differently to temperature changes. A Class 150 flange fashioned from carbon steel will behave quite differently than one made from alloy steel or a composite under thermal stress. This emphasizes the importance of selecting materials that align with expected operating temperatures.
It's not just about a sudden decrease in pressure capability with rising temperature; there's also the factor of creep to consider. At elevated temperatures, materials can gradually deform over time, a phenomenon that might not be a concern at lower temperatures. This long-term material behavior becomes increasingly important when designing systems with extended lifespans.
The gasket's role in sealing the flange joint isn't static either. Some gasket materials may lose their sealing effectiveness at higher temperatures. Thus, selecting the appropriate gasket material and ensuring it's properly installed becomes a crucial consideration for high-temperature applications.
Then there's the influence of thermal expansion on bolt loads. As temperatures fluctuate, the flange and bolt materials expand and contract differently. This leads to changing bolt loads, potentially compromising the clamping force needed for a leak-free seal. Failing to revisit torque settings after significant temperature cycling can become a point of failure.
Even the fluid being transported can introduce complications. High-viscosity fluids can create additional thermal and stress loads on the flange assembly. Therefore, understanding the fluid's behavior at different temperatures is vital for ensuring system integrity.
Furthermore, repeated heating and cooling cycles can accelerate material fatigue, potentially leading to flange cracks or weakening even if the pressure remains within Class 150 limits. This fatigue issue emphasizes the importance of accounting for thermal cycling in design and system lifespan estimates.
Hydrostatic testing, while critical, may not entirely capture the complexities of how materials behave under real-world thermal stresses. This reveals a potential gap between standardized testing and the actual operational conditions experienced by the flange assembly.
Installation methods play a significant role in maintaining the safety margins. Errors in procedures, like neglecting proper thermal expansion allowances or incorrectly tightening bolts, can dramatically reduce the system's ability to withstand temperature fluctuations. These issues often serve as underlying causes of flange system failures.
Finally, the regulatory environment also plays a role. Not all applications using Class 150 components are under the same level of scrutiny. In less regulated industries, engineers may unintentionally overlook temperature-related factors during system design, inadvertently increasing the likelihood of unforeseen issues. This highlights the need for thorough engineering practices even in less regulated contexts.
In conclusion, while Class 150 represents a fundamental pressure class, its application in varied thermal environments necessitates a more nuanced understanding than initially perceived. Careful material selection, consideration for creep and fatigue, understanding gasket behavior, appropriate installation, and awareness of the operating environment, including fluid characteristics and regulatory context, are critical for ensuring safe and reliable performance of Class 150 flanges.
Understanding ANSI Class 150 Pressure Ratings A Comprehensive Guide for Engineers - Material Considerations for ANSI Class 150 Flanges
The choice of material for ANSI Class 150 flanges is critical because it directly affects the flange's ability to withstand pressure and temperature. Common choices include carbon steel and stainless steel, each having specific pressure and temperature limits detailed within the ASME B16.5 standard. Carbon steel, for instance, can handle up to 285 psi at 100°F, but this capability significantly drops with higher temperatures. This highlights the importance of understanding how carbon steel behaves under thermal stress. Furthermore, the type of gasket material used is equally important, as certain gasket types may not perform well at higher temperatures. As a result, engineers must carefully consider the properties of the chosen materials, the operating conditions, and needed maintenance procedures to assure the dependable and safe performance of piping systems using ANSI Class 150 flanges. Failing to carefully evaluate all these factors could result in problems with system integrity and safety.
When considering materials for ANSI Class 150 flanges, we find that the strength of commonly used materials, like ASTM A105 carbon steel, is significantly impacted by temperature. At room temperature, the yield strength might be around 36,000 psi, but at temperatures above 600°F, it can drop considerably to roughly 20,000 psi. This highlights the importance of material selection, especially in applications with fluctuating thermal conditions.
It's interesting to note that the hydrostatic test, a standard practice for Class 150 flanges, involves applying 1.5 times the rated pressure, potentially subjecting the flange to about 427 psi. However, this testing doesn't fully replicate the dynamic stresses experienced in real-world applications, and thus may not accurately represent long-term material performance.
Beyond pressure limitations, temperature affects the expansion of materials. For instance, stainless steel and carbon steel expand at different rates, potentially causing misalignments if not considered during design and installation. This underscores the importance of meticulously accounting for thermal expansion during the design phase.
The type of fluid transported through the piping system is another key consideration. Aggressive substances, for example, can accelerate degradation, leading to issues like localized corrosion or stress corrosion cracking, particularly in less corrosion-resistant materials like carbon steel. Therefore, the compatibility of the flange material with the transported fluid needs careful consideration.
While many engineers may assume all Class 150 flanges are interchangeable, variations in manufacturing processes can lead to subtle differences in dimensional tolerances. These deviations can impact sealing surfaces and compromise the integrity of the joint even when flanges share the same nominal size. It's essential to be aware of these potential discrepancies when selecting flange components.
Creep, a slow deformation under constant stress, becomes a more significant factor at higher temperatures. Carbon steel flanges, for instance, can experience noticeable dimensional changes at temperatures over 300°F due to this phenomenon, affecting the long-term reliability of the system.
Furthermore, the gasket material plays a pivotal role in maintaining the seal. Some gasket materials, like PTFE, can lose their effectiveness at elevated temperatures, underscoring the importance of choosing materials that can withstand the operational conditions.
Transient thermal cycling, which involves repeated heating and cooling, can lead to micro-cracking and fatigue in the flange material. This implies that frequent inspections may be required, even if the operating pressure remains within the Class 150 rating, to prevent unforeseen failures.
Bolt tightening and subsequent pre-tensioning are also influenced by temperature fluctuations. If these forces aren't properly accounted for, joint failures can occur. Consequently, the need for regular assessments of bolt torque, especially after significant temperature cycling, is crucial for maintaining system integrity.
Finally, the regulatory environment plays a vital role in the application of Class 150 flanges. Across different industries, the level of oversight and regulatory compliance varies. In industries with less strict regulations, crucial errors related to thermal stress might be overlooked, leading to potential safety and reliability issues if proper oversight is not enforced.
This illustrates the importance of a comprehensive approach to designing and maintaining ANSI Class 150 flange systems. Careful material selection, thorough understanding of thermal effects, and awareness of operational conditions are paramount for ensuring long-term safety and reliability, especially in demanding and variable environments.
Understanding ANSI Class 150 Pressure Ratings A Comprehensive Guide for Engineers - Sizing and Dimensional Standards for Class 150 Flanges
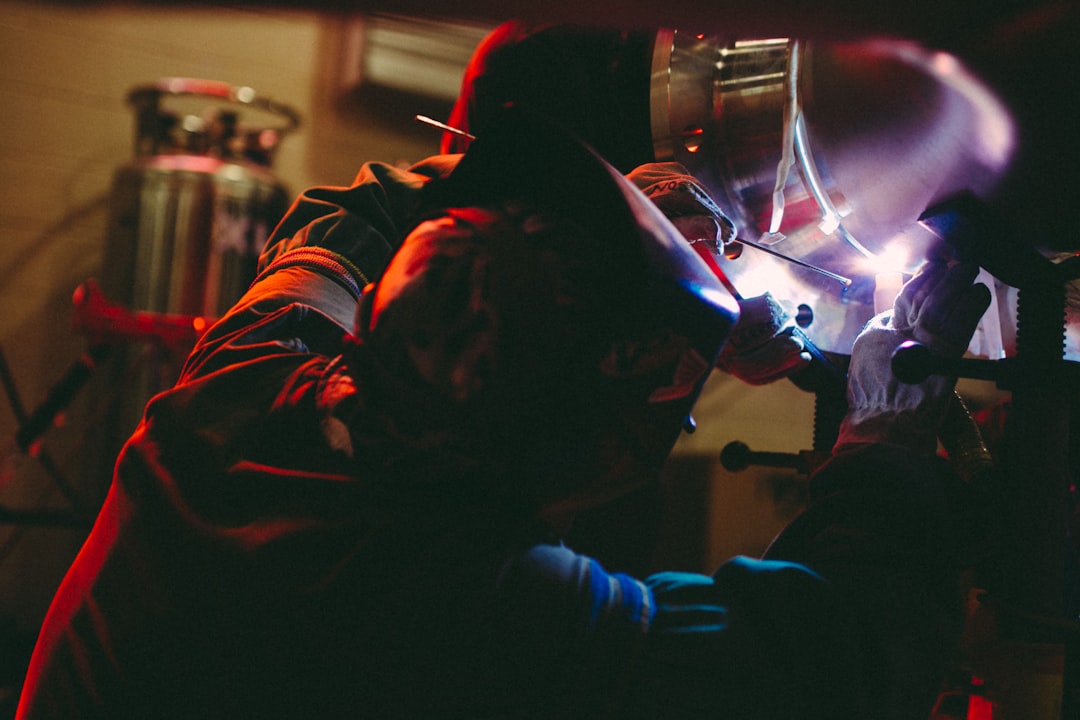
When dealing with ANSI Class 150 flanges, understanding their size and dimensions is crucial for ensuring the integrity and reliability of piping systems. These flanges come in a range of sizes, from 1 inch to 24 inches in nominal diameter, as outlined in the ASME B16.5 standard. This standard provides a blueprint for the dimensions, including the arrangement of bolt holes, making it easier to create consistent designs that meet different pressure requirements. Importantly, the choice of material significantly influences the flange's performance, particularly its ability to withstand pressure and operate at various temperatures. For instance, carbon steel and stainless steel have distinct pressure and temperature limits that engineers must consider. Failure to adhere to these standards and material considerations can lead to problems, especially when dealing with changing temperatures or incompatible materials, potentially resulting in failures within the system. Understanding these standards is fundamental for engineers to ensure system reliability and safety in applications using Class 150 flanges.
ANSI Class 150 flanges, while adhering to standardized dimensions, often exhibit variations in actual manufacturing, impacting assembly. Even seemingly small deviations like a 0.01-inch difference in flange face flatness can create misalignment during installation, potentially compromising system integrity. This highlights the need for meticulous attention to detail during manufacturing and installation.
The strength of materials like carbon steel, commonly used for Class 150 flanges, is strongly affected by temperature. For example, a yield strength of roughly 36,000 psi at room temperature can fall to around 20,000 psi at temperatures exceeding 600°F. This variability emphasizes the importance of carefully considering temperature when selecting materials, especially for applications with fluctuating temperatures.
At higher temperatures, creep becomes a noticeable phenomenon. Carbon steel flanges, in particular, can undergo dimensional changes that may lead to flange joint failures, even at pressures below the maximum rating. This slow deformation under constant stress, which intensifies at higher temperatures, necessitates regular inspections for early detection of potential problems, particularly in systems with long-term operational requirements.
The standard practice of hydrostatic testing, where flanges are tested at 1.5 times the rated pressure (approximately 427 psi for Class 150), doesn't fully reflect the dynamic conditions seen in real-world applications. This gap between standardized testing and actual operational scenarios can potentially lead to an overestimation of flange reliability, as the test may not accurately capture how the flange will respond to a variety of fluctuating thermal and pressure conditions over time.
Gasket material selection is critical since many materials lose sealing efficiency at higher temperatures. Certain widely used materials like PTFE, for example, exhibit rapid degradation at elevated temperatures. This makes material compatibility assessments for gaskets a crucial part of design, especially in high-temperature applications.
Thermal expansion differences between commonly paired materials like carbon steel and stainless steel present challenges for maintaining joint integrity. These differences can cause misalignment and create gaps that lead to leaks or joint failures, particularly in applications involving mixed-material systems. This aspect of flange design necessitates meticulous consideration of thermal expansion during design.
The choice of flange material can be greatly impacted by the nature of the fluid it handles. Aggressive fluids can cause accelerated corrosion or stress corrosion cracking in less resistant materials like carbon steel. Understanding the compatibility of flange materials with the transported fluid is crucial for material selection and ensures long-term system integrity.
The viscosity of the fluid in the system plays a role in thermal loading on flange assemblies. Highly viscous fluids create increased stress on the flange during flow, which could lead to flange failure if not properly considered in the design. Engineers need to account for such loading conditions during the design phase to minimize risks.
Bolt tightening and initial pre-tension are not one-time adjustments. Temperature fluctuations can affect clamping forces, potentially leading to joint failures. Consequently, regularly reassessing bolt torque, particularly after significant temperature shifts, is essential for maintaining effective sealing forces and preventing leakage or failure.
The level of regulatory scrutiny in different industries varies when it comes to Class 150 components. In industries with less stringent regulations, there is a greater chance that critical thermal stress design considerations may be overlooked, increasing the potential for safety hazards and system failures. Engineers in these environments must remain vigilant and ensure best practices are followed to avoid such issues.
These insights demonstrate that understanding ANSI Class 150 flanges involves more than simply knowing the pressure rating. Careful consideration of material selection, temperature effects, operational conditions, and regulatory context is essential to ensure reliable and safe long-term performance, especially in challenging environments.
Understanding ANSI Class 150 Pressure Ratings A Comprehensive Guide for Engineers - Comparing ANSI Class 150 to Higher Pressure Ratings
When comparing ANSI Class 150 to higher pressure classes, the differences in their suitability for various applications become evident. ANSI Class 150, with a maximum pressure rating of around 285 psi at 100°F, is well-suited for lower-pressure applications, like water and air lines. It's important to remember that temperature significantly influences the pressure capability of Class 150 flanges. As temperatures rise, the maximum allowable pressure drops considerably—for example, to roughly 180 psi at 400°F. This contrasts with higher pressure classes, like Class 300 and beyond, which are designed to withstand substantially higher pressures, making them necessary for more demanding applications within sectors such as oil and gas, or high-pressure chemical handling. Ultimately, engineers need to meticulously analyze their operational needs, considering both material selection and the potential impact of temperature changes in relation to anticipated pressure levels. This careful analysis is essential to guarantee the long-term dependability and safety of their engineered systems.
When comparing ANSI Class 150 to flanges with higher pressure ratings, we uncover some notable distinctions. Higher-class flanges, like those in Class 300 or 600, are designed to manage significantly greater pressures at comparable temperatures. This is critical when safety margins are paramount, highlighting the necessity of aligning flange selection with the specific application demands.
Material choices also differ. While Class 150 commonly employs carbon steel, higher pressure ratings often necessitate stronger materials like alloys or specialized composites. These materials are chosen for their enhanced strength and corrosion resistance, attributes essential in more demanding scenarios.
Furthermore, the temperature derating phenomenon—where pressure capabilities decrease with temperature increases—becomes even more pronounced in higher pressure ratings. For instance, a Class 600 flange may experience a steeper decline in pressure limits at higher temperatures than a Class 150 flange. Maintaining optimal temperature control in these settings is thus vital.
One interesting aspect is the observed boost in long-term durability of higher-pressure flanges, especially in challenging, fluctuating environments. While the initial investment in these components might be greater, the potential for reduced lifecycle costs due to enhanced resilience could make them a more cost-effective solution in the long run.
Interestingly, the hydrostatic testing procedures also become more rigorous as pressure ratings increase. While Class 150 undergoes testing at 1.5 times the rated pressure, higher classes might require more intense protocols to ensure they can safely withstand extreme conditions beyond their nominal limits.
Installation techniques can become more complex with higher pressure classes, requiring specialized bolting practices and advanced gasket materials. These complexities are paramount to prevent joint failures, which can be more catastrophic at higher pressures.
Moreover, the materials used in higher pressure flanges frequently incorporate creep resistance, reducing the gradual dimensional changes seen in carbon steel at elevated temperatures. This is highly advantageous in high-temperature environments where Class 150 materials might degrade prematurely.
Additionally, flanges in higher classes are engineered to handle dynamic loading conditions—rapid fluctuations in pressure and temperature—which are prevalent in applications like oil and gas production. Class 150 flanges, in contrast, primarily handle more steady-state situations.
Aggressive or corrosive fluids, which can shorten the lifespan of Class 150 flanges, necessitate special coatings or linings in higher-pressure systems. This enhances corrosion resistance and sustains system integrity over longer periods.
Finally, the bolting requirements for higher-pressure flanges are more stringent, demanding careful assessment of torque specifications and material interactions. Improper handling of these elements can significantly elevate the risk of leakage or failure, particularly in demanding high-pressure scenarios.
In conclusion, selecting flanges involves more than simply choosing the lowest pressure class that seems adequate. Recognizing the unique characteristics of higher pressure ratings and aligning those with application-specific demands ensures both safety and performance, especially in situations where operational conditions become more challenging.
Understanding ANSI Class 150 Pressure Ratings A Comprehensive Guide for Engineers - Safety and Regulatory Aspects of ANSI Class 150 Flange Selection
Selecting ANSI Class 150 flanges involves crucial safety and regulatory considerations to guarantee the integrity and proper functioning of piping systems. Engineers must carefully manage the pressure ratings, understanding that temperature significantly impacts these limits. Failing to consider the interplay of pressure and temperature can result in severe system failures, highlighting the need for precise design and material selection.
Furthermore, the regulatory landscape varies across industries, potentially influencing the level of scrutiny given to material choices and design decisions, especially in applications where lower pressures are prevalent. Proper bolting practices and ensuring the chosen gasket material is compatible with operating temperatures are critical components of safe system operation. Incorrect alignment or an unsuitable gasket can severely compromise system reliability.
Therefore, a comprehensive understanding of materials, the specific operating conditions, and adherence to relevant safety regulations is paramount for achieving both safety and performance when using ANSI Class 150 flanges in any system. Ignoring these factors risks compromising the integrity of the entire piping system.
ANSI Class 150, while offering a seemingly simple pressure rating framework, presents complexities that engineers must understand for safe and reliable system design. One potential pitfall is the assumption of interchangeability. Even though components might fall under the Class 150 designation, variations in manufacturing tolerances between different suppliers can lead to incompatibility and unexpected leak paths. It's a subtle but crucial point that necessitates close scrutiny during the selection phase.
Furthermore, temperature has a non-trivial influence on the maximum allowable pressure for Class 150 flanges. The relationship isn't linear; as temperatures increase, the pressure limit can decrease dramatically. For example, carbon steel flanges, capable of withstanding 285 psi at a comfortable 100°F, see that limit drop to about 180 psi at a moderately elevated 400°F. Understanding this temperature-pressure interplay is key to designing for safety across a range of conditions.
The choice of gasket material is also intertwined with thermal considerations. Different gasket materials degrade at varying rates under high temperatures, which can compromise the integrity of the seal. Selecting a material that can maintain its effectiveness within the intended temperature range is crucial for maintaining a leak-free and safe system over time.
Creep, the slow, time-dependent deformation under sustained stress, becomes a more noticeable concern at higher temperatures. For instance, carbon steel flanges used in Class 150 systems can experience creep at temperatures above 300°F, leading to gradual dimensional changes and, eventually, joint failure. Engineers need to anticipate this effect in designs, particularly in applications involving long-term use under these conditions.
While hydrostatic testing is a standard practice, involving pressure testing at 1.5 times the rated pressure, it may not always accurately simulate the dynamic stresses experienced in real-world applications. This means a hydrostatic test, while informative, doesn't provide a full picture of how the flange will perform over time under dynamic conditions.
Differences in thermal expansion rates between materials, such as the commonly used stainless steel and carbon steel, can also introduce issues. During installation, misalignments caused by these differences can arise if not properly accounted for, leading to compromised sealing surfaces and potential joint failure.
The aggressiveness of the fluid being transported can also play a significant role. Highly corrosive or aggressive fluids can contribute to issues such as stress corrosion cracking, particularly in less resistant materials like carbon steel. Matching the flange material to the characteristics of the fluid is crucial for long-term system reliability.
Bolting also plays a key role. While properly tightened bolts are essential for creating a secure seal, fluctuations in temperature can alter clamping forces. Therefore, engineers need to implement strategies for regular bolt torque reassessments, especially after significant temperature swings, to maintain adequate sealing and avoid leaks.
Regulatory landscapes across industries are not uniform. In industries with fewer regulations, there's a heightened chance that the critical thermal considerations required for Class 150 flange applications might be overlooked. Engineers should be particularly cautious and adhere to best practices in these settings.
Finally, it's vital to acknowledge the potential for fatigue from thermal cycling. Even when operating pressures are within acceptable limits, frequent thermal cycling can accelerate material fatigue, leading to micro-cracking. This emphasizes the need for periodic inspections and proactive maintenance to prolong the life of these critical components.
In summary, while the ANSI Class 150 framework seems straightforward, a comprehensive understanding of the nuances of material behavior, thermal effects, fluid compatibility, and regulatory contexts is vital for engineers when designing with these components. A holistic approach considering these factors is needed to ensure safe and reliable performance in diverse operational environments.
More Posts from aistructuralreview.com: