Structural Performance Analysis Key Differences Between Slip-On and Weld Neck Flanges in High-Stress Applications
Structural Performance Analysis Key Differences Between Slip-On and Weld Neck Flanges in High-Stress Applications - Load Distribution Analysis Between Slip On and Weld Neck Hub Geometry
When examining how loads are distributed within the hub geometries of slip-on and weld neck flanges, we find that weld neck flanges offer a more robust structural foundation in demanding applications. This superiority stems from their inherent ability to handle loads more effectively. The distinctive design of weld neck flanges promotes a more even dispersal of stress across the entire structure, thus minimizing the concentration of stress at specific points, a known cause of fatigue-related failures.
In contrast, slip-on flanges, despite their simpler installation and lower cost, possess a comparatively weaker structural capacity. This can lead to a compromise in joint integrity, especially when subjected to severe conditions. This difference highlights the importance of selecting the correct flange type based on specific operational demands, especially when facing high pressures or temperatures. Carefully considering these nuances is crucial for ensuring the dependable operation of systems within high-stress environments.
When examining how forces are distributed across slip-on and weld neck flanges, the hub's shape plays a crucial role. Slip-on flanges, due to their design, often concentrate stress at the weld zone more than weld neck flanges, potentially leading to earlier failures in demanding situations. In contrast, weld neck flanges are tapered, enabling a smoother transition of load from the pipe to the flange itself, which reduces stress concentrations. This is markedly different from the abrupt change in geometry present in slip-on designs.
The effectiveness of load distribution in slip-on flanges is sensitive to how well the pipe and flange fit together. This variability leads to inconsistent performance across different installations, which can be a source of uncertainty. Finite element analyses have demonstrated that weld neck flanges spread load more uniformly across their surface, minimizing localized yielding, a concern that arises more readily with slip-on designs.
High temperatures can distort slip-on flanges more easily, reducing their ability to carry loads over time. Weld neck flanges, benefiting from continuous support, tend to maintain their structural integrity better during thermal expansion. Slip-on flanges can experience increased rotational forces at the weld due to their stress distribution characteristics, leading to potential weld fatigue, a factor that must be considered in demanding applications.
Often, slip-on flanges are constructed from less expensive materials, potentially reducing initial costs. However, this can negatively impact load distribution, particularly in high-stress scenarios. Adding weld reinforcement to slip-on flanges doesn't inherently guarantee better load distribution. In fact, improperly designed reinforcements can exacerbate stress concentrations.
Experimental investigations have revealed that weld neck flanges show superior fatigue resistance when exposed to repetitive loading, making them a more suitable choice for dynamic environments. The choice between the two flange types significantly impacts the design process for high-stress applications. Since the methods of load distribution differ, engineers might need to incorporate extra support structures or make modifications to the system design to account for the limitations of slip-on designs.
Structural Performance Analysis Key Differences Between Slip-On and Weld Neck Flanges in High-Stress Applications - Weld Joint Integrity Testing Under Maximum Operating Pressure 1500 PSI
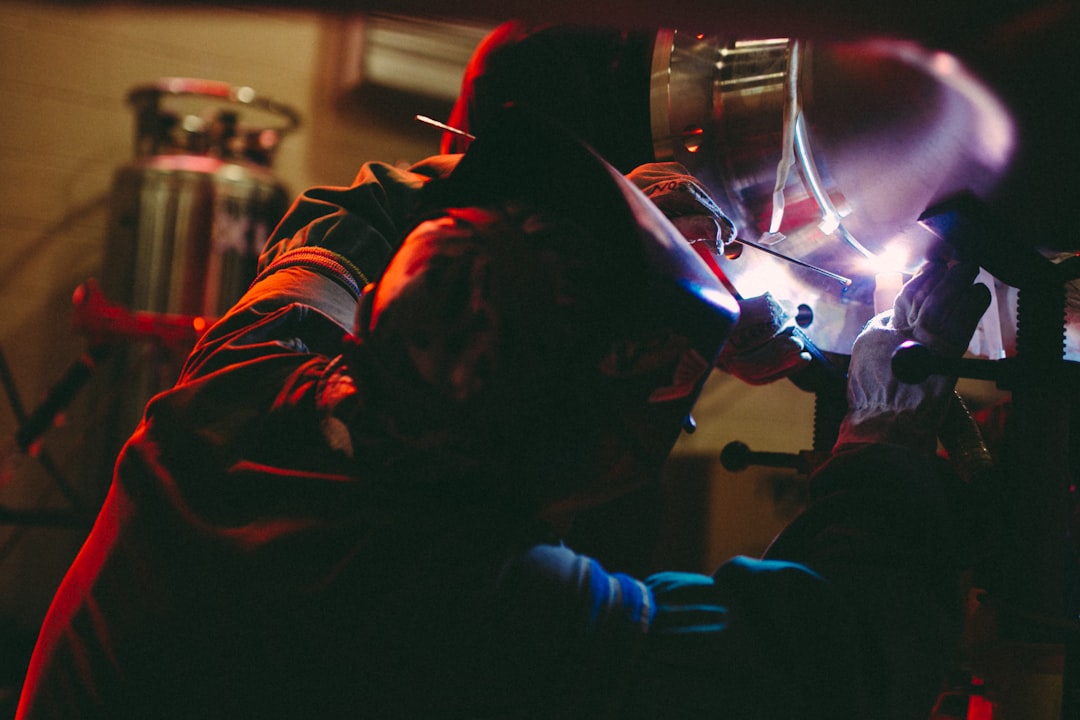
When systems operate under extreme pressures, like 1500 PSI, the integrity of welded joints becomes paramount. Testing these joints rigorously is vital to ensure they can safely handle such demanding conditions. These tests aren't just about the overall strength of the weld, but also delve into specifics like weld geometry and the properties of the areas around the weld that have been affected by the heat of the welding process.
Especially in scenarios with high stresses, the thickness of the weld's throat is a critical factor determining how well the joint will perform and last. This thickness significantly impacts the joint's capacity to handle the pressure and forces it experiences. Modern tools like computer-based weld analysis are helping engineers anticipate potential weaknesses and improve the reliability of welded joints in challenging situations.
However, skipping or skimping on these evaluations can have serious consequences. To avoid potential failures and ensure safe operation, a thorough and meticulous evaluation of weld integrity is essential in any application involving high-pressure environments.
Evaluating the integrity of weld joints under maximum operating pressures, such as 1500 PSI, is crucial for ensuring safety and reliability in high-stress applications. Traditional testing methods might not always accurately represent the stresses encountered during actual operation, making it imperative to push the weld's limits during testing to uncover potential flaws. For example, relying on standard pressure tests might not reveal subtle issues that become critical under these intense conditions.
The weld quality itself significantly influences the performance of a joint at high pressure. The heat input used during welding, the selection of filler materials, and the overall skill of the welder all play a role in the strength and integrity of the finished joint. Minor deviations from optimal welding practices can have a noticeable impact on the joint's overall strength, potentially creating areas more prone to failure.
During rigorous testing, it's common to see stress concentrate in certain areas of the weld. These points, often related to weld imperfections like porosity or inclusions, can magnify stress levels and increase the chances of failure. Even if a weld passes basic inspection, it may have weaknesses that only become obvious under high-pressure conditions. This is a reminder that we need to critically assess the results of various testing methods to form a comprehensive understanding of weld performance.
Developing innovative testing techniques that can monitor the weld's behavior in real-time under pressure could help us better understand how failures might occur. Acoustic emission monitoring is one example of a promising approach that can reveal early signs of crack formation or other damaging events, providing more insights than traditional inspection methods.
The type of welding process employed can influence a weld's fatigue resistance, which is particularly relevant for applications involving cyclical loading. Techniques like shielded metal arc welding (SMAW) and gas tungsten arc welding (GTAW) can lead to different weld microstructures and residual stress patterns, impacting how well the weld endures cyclic stress. Understanding the nuances of different welding methods is important for choosing the right approach for specific applications.
High-pressure hydraulic testing is intrinsically risky because of the large amount of stored energy. Safety protocols must be absolutely strict to minimize the chances of a catastrophic incident. These tests are essential for assessing weld integrity, but recognizing the hazards and implementing appropriate safety measures is critical.
The choice of base materials for the welded structure is another factor that can affect performance under maximum operating pressure. Certain alloy combinations might have inherent limitations at these high pressure levels, which can undermine the joint's integrity regardless of the quality of the welding process. This reinforces the importance of material selection in conjunction with weld procedures.
Non-destructive testing (NDT) methods, while helpful, have their limitations. Certain defects, particularly tiny micro-cracks, might go unnoticed until the weld is subjected to high pressures. It's critical to develop advanced inspection and testing methodologies that address this shortcoming and provide a more comprehensive view of a weld's internal condition.
The weld joint's geometry, including factors like the root gap and angle, is a significant factor in the way stresses are distributed across the joint. Subtle changes in these features can influence where stresses concentrate and can result in unusual failure mechanisms that are not readily apparent in conventional assessments.
Temperature, especially in fluctuating environments, can also alter the mechanical properties of the weld and affect its strength. A joint might withstand a specific pressure at room temperature, but when exposed to high operational temperatures or thermal cycles, the material properties can change, compromising its ability to handle those same pressure levels. Testing under a range of relevant temperatures can help engineers design systems that function properly under expected operating conditions.
In conclusion, evaluating weld joint integrity under maximum operating pressure requires careful consideration of a variety of factors, including weld quality, stress concentrations, material properties, and operational temperature variations. By understanding these potential challenges and exploring new approaches to testing, engineers can design and produce weldments that will perform reliably in challenging high-pressure applications.
Structural Performance Analysis Key Differences Between Slip-On and Weld Neck Flanges in High-Stress Applications - Material Fatigue Response During 10000 Hour Thermal Cycling Tests
When evaluating the long-term performance of materials in high-stress applications, it's essential to understand how they respond to prolonged thermal cycling. Specifically, subjecting materials to 10,000 hours of thermal cycling tests provides valuable insights into their fatigue characteristics. This type of extended testing highlights the interplay between temperature fluctuations and material stress, leading to fatigue behavior that might not be readily apparent in shorter tests.
Factors like peak stress during thermal cycles, the variation in stress levels experienced by the material, and the sheer number of these cycles are major contributors to a material's fatigue response. It's important to remember that material fatigue is a complex phenomenon. During thermal cycling, materials expand and contract repeatedly, potentially leading to various failure mechanisms like thermal fatigue. In some cases, thermal cycling can interact with surface conditions, accelerating the onset of corrosion-fatigue or other surface-related fatigue.
Ultimately, conducting and analyzing the results of these extensive thermal cycling tests allows engineers to develop a better understanding of how materials might fail under operational conditions that involve both stress and temperature changes. This knowledge is crucial for making informed decisions in the design and selection of materials for high-stress applications and can contribute to improving the reliability of components over their intended lifespan.
During 10,000-hour thermal cycling tests, we observe how materials respond to repeated heating and cooling cycles. These cycles cause changes within the material's microstructure due to the differences in how quickly different parts expand and contract with temperature. This can create internal stresses that can contribute to fatigue and possibly start crack growth sooner than expected.
Additionally, sustained high temperatures can lead to creep, a gradual deformation of the material. This effect becomes increasingly significant in applications where parts are continuously subjected to high-temperature cycling for long periods, and it can strongly influence the overall fatigue behavior.
Interestingly, increasing temperature can actually reduce a material's fatigue limit, the maximum stress it can withstand indefinitely. This weakening at higher temperatures reduces the overall resistance to cyclic loading, which is a major factor in determining the long-term performance of a part under these conditions.
Some materials undergo changes in their crystal structure, also known as phase transformations, when experiencing these thermal cycles. These transitions can significantly change a material's mechanical properties, leading to either a brittle or softer state, depending on the material's composition and the stresses it is under.
Furthermore, the microstructural changes that happen over time during thermal cycling, like grain growth or the evolution of tiny particles within the material, can cause uneven fatigue behavior across different parts of a component. This unevenness can lead to unexpected failure points that are difficult to foresee using standard analysis techniques.
The fatigue response of a material isn't always straightforward in thermal cycling. Instead of a linear relationship with the number of cycles, the fatigue behavior can be complex, influenced by factors such as the frequency of the load cycles and how much the temperature changes. This nonlinear behavior makes it challenging to predict long-term performance.
Some materials display what's called anisotropic fatigue behavior, meaning their resistance to fatigue is different depending on the direction of the applied load. This directional dependency is something to consider when choosing materials for applications involving thermal cycling and high stresses.
Designs that account for thermal fatigue generally need a larger margin of safety compared to those designed for static loads. This is because of the combined effect of temperature fluctuations and repetitive loading, requiring a more cautious approach in planning and material selection.
Every material has a certain temperature point beyond which its fatigue response significantly changes. Even a temporary exceedance of this critical threshold during thermal cycling can accelerate material degradation, highlighting the importance of precise temperature control in engineering design.
Recent progress in real-time monitoring technologies, like fiber optic sensors, allow engineers to track fatigue damage as it happens during thermal cycling tests. This ability provides a deeper understanding of how materials behave and helps us predict failures more accurately than we could with traditional methods.
Structural Performance Analysis Key Differences Between Slip-On and Weld Neck Flanges in High-Stress Applications - Stress Concentration Factors at Pipe to Flange Interface Points
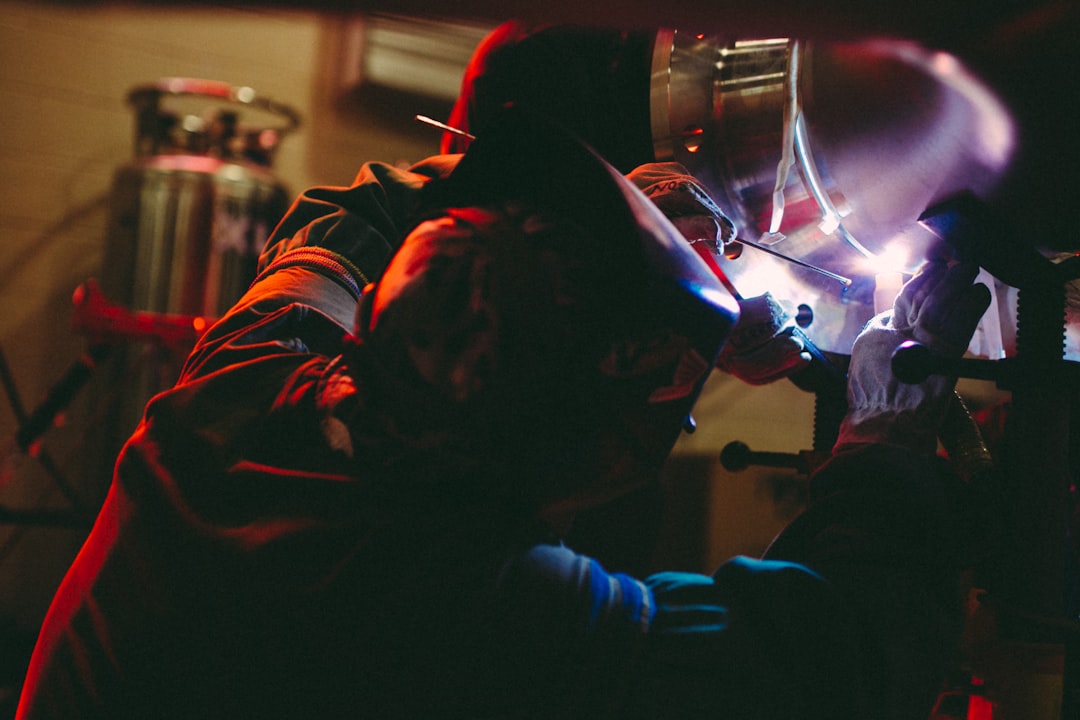
Understanding how stresses concentrate at the point where a pipe meets a flange is crucial for predicting potential failures, especially in high-pressure applications. These stress concentration factors (SCFs) play a significant role in how cracks begin and spread, particularly within the weld joints of these connections. This is because the transition from the pipe to the flange creates unique stress patterns.
In situations where stresses are consistently high, weld neck flanges often emerge as a better choice due to their design. They distribute stress more evenly across the interface, leading to lower peak stress values and increased overall joint strength. This is in contrast to slip-on flanges, where stress tends to concentrate, potentially accelerating fatigue failure.
Engineers can use advanced tools like the Finite Element Method (FEM) to analyze and model these interfaces. This allows for a more detailed understanding of the impact of factors like misalignment on the stress distribution, leading to more accurate assessments of structural performance.
It's vital to remember that SCFs can be a major factor in causing structural failures, especially in challenging operating environments. This highlights the necessity of carefully designed connections and the importance of choosing the right flange type for the specific application.
Stress concentration factors (SCFs) at the interface where a pipe meets a flange can significantly impact a structure's performance, particularly in high-stress applications. The flange type and its design play a substantial role in determining these SCFs. For example, weld neck flanges, with their tapered geometry, usually lead to a smoother transition of stress compared to the abrupt transition found in slip-on flanges, which inherently concentrate stress more. This smoother flow of stress in weld neck flanges can contribute to a lower SCF and improved structural integrity under demanding conditions.
A significant concern in slip-on flange designs is the high concentration of stress at the weld. This is a potential area for early fatigue failures, making them less ideal for applications involving repetitive or high-stress loads. In contrast, the design of weld neck flanges promotes a more even dispersal of stress, improving their overall structural resilience.
Finite element analysis (FEA) simulations often highlight that SCFs at the flange-pipe interface can surpass recommended values, especially in slip-on flange designs operating under high pressures. If not considered during the design process, these high SCFs can lead to unforeseen service failures.
It's crucial to acknowledge that temperature variations at the interface between the pipe and flange can intensify stress concentrations. This is especially important in environments with thermal cycling, where the mismatch in thermal expansion between different materials or sections can produce localized stress spikes that are frequently underestimated.
Even the materials chosen for the pipe and flange can influence the SCF. If the materials have different thermal expansion coefficients, it can create elevated stress concentrations at the interface, negatively impacting the overall structural integrity.
Interestingly, pre-loading the bolts connecting the flange can shift the stress distribution within the joint, potentially reducing the SCF. This method can be a helpful way to manage localized stress concentrations that could otherwise lead to failures.
It's important to realize that imperfections in the welds, even seemingly minor ones like porosity or gaps in the fusion, can substantially increase the SCF locally. This emphasizes the need for robust inspection methods to ensure the quality of the welds and to minimize the potential for premature failure.
Although certain standards advise specific inspection intervals for flanges in high-stress applications, many engineers often don't fully incorporate the influence of SCFs when determining the frequency of these inspections. More frequent inspection and analysis could significantly reduce the chance of catastrophic failures caused by unseen stress concentrations.
The initial cost savings associated with slip-on flanges are often seen as an advantage. However, their susceptibility to stress concentrations can lead to greater repair and replacement costs in the long run. This can call into question whether the initial cost savings are truly beneficial.
Exciting advances in materials science have brought about new options for flange and pipe construction. These new materials, such as advanced composites and high-strength alloys, can potentially reduce SCFs compared to traditional materials. These advancements offer promise for more durable designs that can withstand the rigors of high-stress environments.
Structural Performance Analysis Key Differences Between Slip-On and Weld Neck Flanges in High-Stress Applications - Deformation Limits and Structural Behavior Under External Loading
When analyzing structures subjected to external forces, especially in demanding applications like those involving flanges, understanding how materials deform and behave is crucial. The relationship between stress and strain, depicted by the stress-strain curve, shows how materials initially deform elastically, governed by their Young's modulus. However, once the yield stress is exceeded, the deformation becomes non-linear, with the specific behavior depending on the material. This non-linear response highlights the importance of considering material properties under various strain rates. The overall structural performance of components under cyclic or intense loads is also impacted, particularly in areas where stress tends to concentrate. These stress concentrations, for instance at the interface where the pipe and flange join, can potentially accelerate material fatigue and lead to failures. Therefore, in high-pressure systems, the choices of materials, design of joints, and consideration of expected loading conditions are crucial to ensure reliable and safe operation.
1. When a pipe connects to a flange, particularly in slip-on designs, stress tends to build up at the joint far more than predicted. This can lead to structural issues if engineers don't consider it in their calculations. It's a critical point of failure.
2. The materials used in the flange and pipe, including how they react to temperature changes, can heavily impact where stress gathers. Differences in how materials expand or contract can create hot spots of stress that can damage the joint if it's under load.
3. It's been shown that tightening the bolts that hold the flange together can alter the way stress is distributed in the joint. This pre-loading can reduce stress spikes, leading to a more robust connection.
4. When systems experience repeated heating and cooling, it makes stress concentration worse because materials expand and contract differently. This can cause fatigue issues that are harder to predict with standard analysis techniques.
5. The structure of materials at a microscopic level can change over time due to loads and temperature shifts. This change leads to unpredictable wear and tear patterns that aren't easily identified with typical assessments.
6. While methods for looking for flaws in materials without causing damage are very useful, they might miss small imperfections like microscopic cracks. These cracks could only show up under high stress, indicating that we need better inspection methods.
7. The shape of a weld joint is a big factor in how stress spreads. Small alterations in the angles and gaps can affect how it might fail, leading to unexpected failures.
8. Weld neck flanges, because of their shape, perform better when dealing with repeated stresses or vibrations than slip-on flanges. This is because they distribute the stress more evenly, improving the reliability under these conditions.
9. Higher operating temperatures can weaken a material's resistance to repeated stresses. This means that in environments where temperatures change often, material selection and designs need to consider this impact on fatigue.
10. Modern ways of observing systems while they're in operation, like using optical fiber sensors, are giving us a better picture of how stress builds up and damage occurs. This can be used for better maintenance and design changes.
Structural Performance Analysis Key Differences Between Slip-On and Weld Neck Flanges in High-Stress Applications - Field Performance Data From 36 Month High Temperature Applications
Data gathered from high-temperature applications lasting 36 months provides valuable insights into the durability and reliability of materials and designs in challenging environments. This data reveals the critical need for thorough assessments, particularly in high-stress situations. To improve design accuracy and material selection, advanced techniques like deep learning are increasingly used to forecast stress levels and temperature changes within components made of high-performance materials, especially those operating at extreme temperatures.
The behavior of structural materials in high-temperature environments is complex. Metallic alloys, commonly used in these demanding applications, undergo significant changes in their mechanical properties as temperatures fluctuate. The repeated expansion and contraction from thermal cycling can cause fatigue and stress concentrations, making it crucial to account for these effects in designs.
In this context, the choice of flange type becomes even more significant. The inherent structural advantages of weld neck flanges, such as better stress distribution, contribute to their superior performance compared to slip-on flanges when facing extreme stress. However, this field data suggests that the real-world performance of these components in demanding scenarios is best understood by ongoing monitoring of their operational status, with sensors capturing changes in performance, and even predicting failure before it becomes a critical risk to the system.
1. **Temperature Fluctuations and Stress**: Field data suggests that temperature changes can significantly increase stress concentration at the point where slip-on flanges meet pipes. This is often not fully accounted for in basic design calculations, hinting at a potential area of vulnerability.
2. **Material Response Beyond the Yield Point**: When flanges experience complex forces like both pulling and sideways stresses, materials can behave in ways that aren't always predictable. This non-linear response is something to watch out for, especially in slip-on designs where we might expect stress to build up unevenly.
3. **Material Choices Matter at High Temps**: The material used in a flange is incredibly important for how long it lasts, particularly when it's hot. Certain materials degrade much faster at higher temperatures, something design needs to address proactively.
4. **Hidden Changes Inside the Material**: Over time, repeated heating and cooling can cause tiny changes within the structure of a metal flange. This can lead to unexpected types of failure that are hard to spot with regular inspections. It suggests that we may be overlooking some failure mechanisms.
5. **Material Directionality**: Certain flange materials respond differently depending on the direction of the force applied. This adds a layer of complexity to design as we can't assume they behave the same in every situation.
6. **Slow Deformation at High Temperatures**: At high temperatures, some materials slowly deform over time, even under a constant load. This creep can weaken the flange-pipe connection in the long run, impacting the reliability of the joint.
7. **Limitations of Current Inspection Methods**: Current methods of examining flanges for defects without damaging them might miss tiny cracks that can only appear under real operating conditions. We need better ways to see these potential problem areas.
8. **Computer Simulations for Better Design**: Modern computer models can simulate loading conditions and stress distribution in greater detail than we could before. This gives us a better understanding of what can go wrong, helping designers create more robust designs.
9. **The Impact of Movement**: Slip-on flanges might not handle repeated or vibrating forces as well as expected. This can result in unexpected wear and tear over time, something weld neck flanges might be more resistant to.
10. **Seeing Stress in Real-Time**: New tools like fiber optic sensors let engineers observe stress and damage in a flange as it happens. This provides better insights into how it's actually behaving, leading to better maintenance and improved design in the future.
More Posts from aistructuralreview.com: