Directional Flow in Pipe Unions 7 Critical Installation Guidelines for Maintenance Technicians
Directional Flow in Pipe Unions 7 Critical Installation Guidelines for Maintenance Technicians - Ground Joint Union Directional Setup Proper Ring Side Placement
When working with ground joint unions, particularly in systems where directional flow is critical, like steam lines, the placement of the union's components becomes significant. These unions, unlike some others, don't rely on insulating gaskets or sleeves for their seal, making them well-suited for higher pressure and velocity applications. This unique design highlights the importance of proper orientation during installation.
It's often recommended, though not universally required, to position the "nut side" of the ground joint union facing the direction of fluid flow. This arrangement can contribute to better operational efficiency and, in the long run, may simplify maintenance activities. Correct installation is fundamental here, ensuring the union nut's threads are aligned properly and that all components are securely positioned.
By paying attention to these seemingly minor details – the orientation of the nut and the overall placement of parts – technicians can create a much more robust and reliable pipeline setup, ultimately extending the life and performance of the piping system. Neglecting these details could lead to complications down the line.
Ground joint unions achieve their sealing prowess through the compression generated during tightening, essentially creating a metal-to-metal seal. This is fundamentally different from unions that use gaskets, and it's a key factor in ensuring leak-free performance in applications where directional flow is critical.
The position of the union ring is crucial. If not placed correctly, the force distribution across the joint becomes uneven, potentially leading to premature failure under pressure. It's a bit like trying to balance a stack of bricks – if one brick is slightly off, the whole stack becomes unstable.
While a pipe union's orientation isn't always strictly dictated, it can influence how downstream equipment functions. For example, poorly placed union rings can lead to fluid turbulence, which could affect the overall efficiency of the system. This highlights the importance of understanding the broader flow dynamics within a pipeline.
Choosing the right material for the union rings can have a significant effect on thermal properties. For example, in high-temperature applications, the material's thermal conductivity needs to be considered to ensure the union doesn't create hotspots or lead to excessive heat dissipation. This is particularly important if temperature changes rapidly or if you're dealing with fluids that are highly sensitive to temperature fluctuations.
When tightening a union, the correct torque is crucial. Applying too much or too little can cause misalignment or damage the metal itself. Unfortunately, torque requirements differ depending on pipe diameter, making it vital to refer to the manufacturer’s specifications.
Beyond preventing leaks, proper installation also reduces the risk of galling – where the metal surfaces fuse together. Galling can hinder regular maintenance and lead to costly repairs. It's important to consider the specific materials involved in the union and how they might react under various operating conditions.
The quality of the surface finish on the components can also influence how effectively the union seals. A smoother surface usually leads to a tighter fit, which helps ensure a better seal. This reinforces the importance of ensuring the union's components are well-manufactured and free of defects.
Environmental factors like temperature swings and vibrations need to be taken into account. These external influences can impact the lifespan and performance of a ground joint union over time. Engineers need to consider the expected conditions and design the system accordingly to ensure long-term reliability.
There's a tendency for maintenance technicians to sometimes overlook regular inspections of these unions. However, routine checks can help detect wear and tear early, preventing potential failures. A simple visual inspection can go a long way in ensuring the system remains operational.
Ground joint unions' design contributes to ideal flow alignment. The right-angle configuration makes them well-suited for applications with space restrictions and complex piping geometries. This design aspect underscores their versatility in a variety of scenarios.
Directional Flow in Pipe Unions 7 Critical Installation Guidelines for Maintenance Technicians - Flow Rate Impact Steam Systems Upstream Installation Standards
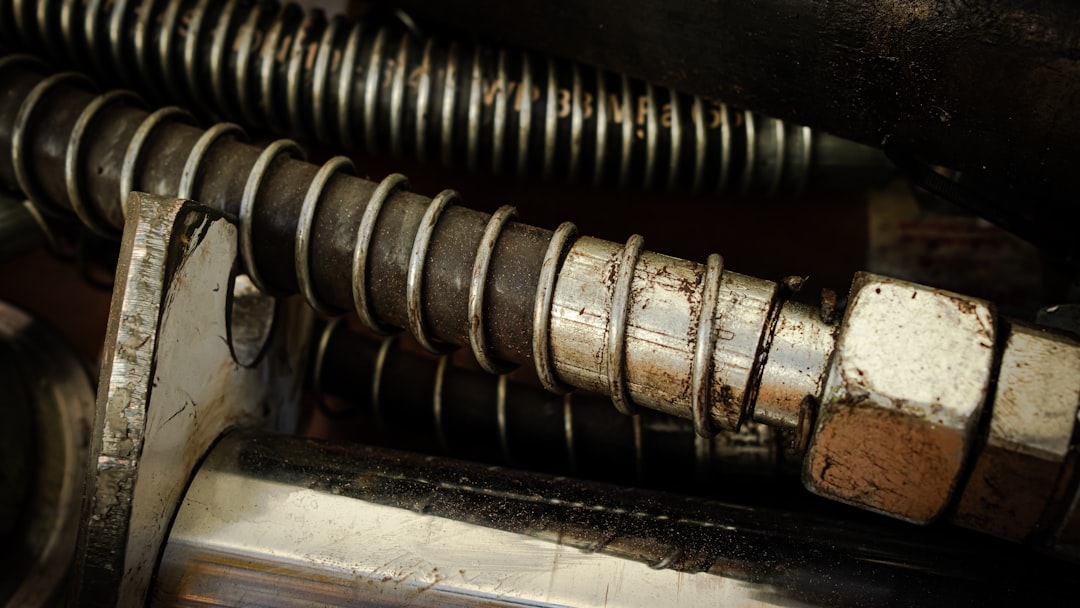
When dealing with steam systems, paying close attention to how flow rate impacts upstream installations is essential for the system to work well. Although the direction of flow through pipe unions isn't always strictly defined, steam systems, especially those with high-velocity flow, require a different approach. This involves making sure the steam velocity stays within the recommended range, choosing the right pipe sizes, and making sure there's a clear, straight path of pipe before flow measurement points. These installations should adhere to standards that stop things like water hammer and poor steam distribution from occurring. Ultimately, this careful design and installation leads to a more reliable and long-lasting steam infrastructure. If maintenance technicians understand and follow these principles, they'll be more likely to create a well-functioning steam system with fewer problems. Ignoring these issues can cause issues down the line.
Flow rate significantly influences pressure loss within steam systems, primarily due to friction within the pipes. It's crucial to understand this relationship when designing and optimizing steam systems to ensure efficient operation.
The transition between laminar and turbulent flow, which typically happens around a Reynolds number of 2000, is significant for steam systems. This transition affects how effectively ground joint unions seal and operate.
Over time, high-pressure steam can cause deformation in the materials used in ground joint unions, potentially impacting their ability to seal properly. This highlights the importance of understanding the long-term structural integrity of the union materials to prevent catastrophic failure.
Some steam systems might exhibit non-Newtonian flow behavior where the viscosity of the steam changes depending on pressure and flow rate. This complexity needs careful consideration when designing piping systems and applying standard installation techniques.
Sometimes, poorly placed unions can lead to "vapor lock," where steam gets trapped with air, disrupting the flow and causing inefficiencies. This phenomenon is another example of why understanding the direction of flow and placement of ground joint unions is so important.
The varying thermal expansion rates of different materials in unions can cause misalignment in high-temperature steam systems if installation standards don't address thermal expansion properly. It's a design consideration for systems where temperatures fluctuate.
The diameter of the pipes connected by unions substantially affects the velocity and flow patterns within the system. Larger pipe diameters typically decrease flow velocity, potentially impacting the overall performance of steam distribution lines.
High-velocity steam can lead to erosion or cavitation issues, especially if unions are not installed correctly. These concerns can damage both the union and downstream components. It's another factor to be careful of in the design stage.
The metal-to-metal seal in a ground joint union can be affected by extreme thermal cycling, potentially altering the compression of the seal over time. Close monitoring is essential for maintaining a leak-free system in these challenging environments.
Applications with frequent starts and stops create dynamic loads on the pipe unions, increasing the importance of adhering to installation standards. These dynamic loads can cause vibration-induced wear and fatigue, which can shorten the lifespan of the components.
It's important to note that this is still a developing area of study and understanding. The research will undoubtedly continue and could refine some of our understandings of installation practices.
Directional Flow in Pipe Unions 7 Critical Installation Guidelines for Maintenance Technicians - Temperature Changes Effects Thermal Expansion Adaptations
Temperature fluctuations cause materials to expand and contract, a phenomenon known as thermal expansion. This effect is especially relevant in piping systems, where varying temperatures can lead to significant changes in pipe length. Different materials exhibit varying degrees of thermal expansion, with plastics often expanding and contracting much more than metals under the same temperature change. Understanding these differences is crucial for maintenance technicians, particularly when working with pipe unions. Failing to account for thermal expansion during installation can result in issues like misalignment and leaks, potentially leading to system failure.
To mitigate the effects of thermal expansion, careful planning and installation practices are essential. This includes incorporating expansion joints or loops into the system design to absorb the changes in length. Moreover, accurate calculations of potential thermal movement are critical to prevent excessive stretching or compression of the pipe, which can damage the system. Maintenance technicians need a strong grasp of thermal expansion principles and how they influence the performance and longevity of pipe unions. By incorporating these principles into their work, they can ensure efficient and reliable operation of piping systems across various applications.
Temperature changes invariably lead to thermal expansion or contraction in piping materials. Generally, materials expand when heated and contract when cooled. This behavior is predictable using formulas that incorporate the material's thermal expansion coefficient, initial length, and the temperature change. For instance, polyethylene pipes exhibit a notable expansion rate, while CPVC pipes might expand an inch over a 50-foot length for a 50°F temperature increase.
The magnitude of expansion varies considerably among materials. Plastics tend to be much more susceptible to thermal expansion than metals, experiencing a four to five times greater change in length under the same temperature shift. This discrepancy in expansion behavior between dissimilar materials becomes especially critical when designing and installing pipe unions.
If only one end of a pipe is fixed, the other end is free to expand or contract. For long runs of pipe materials like PEX, a relatively small temperature swing can result in a substantial change in length. These expansion characteristics need careful consideration by maintenance technicians when handling pipe unions and their installations.
Understanding directional flow in pipe unions is pivotal when dealing with thermal expansion issues. Ignoring the impact of temperature changes on the system can compromise installations and even lead to system failures if not properly managed. For example, expansion joints or loops can be incorporated into piping systems to accommodate these changes and prevent excessive stress on the unions and pipes.
Accurate calculations of thermal expansion are essential for preventing system failure due to temperature fluctuations. Overlooking thermal movement during installation can subject unions and pipelines to excessive stretching or compression, leading to compromised sealing and leaks. If the expansion isn't properly accommodated during design and construction, stress can lead to material fatigue and eventually failure. This highlights the need for engineers to carefully consider the material properties and anticipated temperature changes within the system during the design phase.
It's interesting that the non-linearity of thermal expansion in some materials can cause difficulties in design. This means that simple linear formulas don't always accurately predict expansion behavior in extreme situations.
Moreover, different materials have varying thermal properties. Aluminum and steel have different coefficients of thermal expansion, for example. This can cause problems when dissimilar materials are joined together in unions because each material will expand or contract at a different rate. This differential expansion can result in misalignment and stress on the union, leading to leaks or failures.
When temperatures fluctuate repeatedly, a phenomenon known as thermal cycling occurs. Thermal cycling can induce fatigue stresses on materials, potentially shortening the lifespan of unions and pipes. Furthermore, the specific heat capacity of materials can lead to uneven temperature distributions within unions, causing localized expansion and stress. This is a hidden challenge that engineers need to consider to avoid long-term system problems.
The viscosity of fluids within a pipeline can also change with temperature. When fluids change viscosity, their flow characteristics are altered. This can also influence how the unions perform and how well they seal under different thermal conditions.
Thermal shock, which arises from rapid changes in temperature, can be particularly problematic in piping systems, sometimes leading to crack propagation in sensitive materials. This is important to consider when working with fluids that have significant temperature differences, or if the process involves frequent and abrupt changes in temperature.
Engineers frequently incorporate thermal expansion gaps to accommodate these material movements. Careful sizing of these gaps is essential to avoid either over-constraining the pipe or wasting valuable space in the system.
These factors illustrate the need for maintenance technicians and engineers to have a thorough understanding of thermal expansion and its impact on pipe unions during the installation and maintenance of piping systems. The consequences of overlooking these seemingly minor details can be severe, highlighting the crucial role that knowledge and attention to detail play in ensuring a safe and reliable system.
Directional Flow in Pipe Unions 7 Critical Installation Guidelines for Maintenance Technicians - Pressure Loss Prevention Through Union Joint Assembly
Preventing pressure loss within piping systems using union joints requires a mindful approach to installation. The path of fluid flow through the union can have a significant effect on overall pressure, meaning careful consideration of the union's orientation is important. Friction created by fittings and bends can increase pressure drop, and overlooking factors like union ring material selection or the design of the joint itself can exacerbate this issue, especially when dealing with high-speed fluid flow. Recognizing how poorly placed or assembled unions can lead to greater pressure loss is critical. Technicians must adhere to best practices when assembling these components. Doing so not only preserves the desired system pressure but can improve efficiency and reliability of the entire pipe network.
In pipe unions, especially at higher flow rates, the orientation can influence the flow pattern. Misalignment can create turbulence, leading to more pressure loss due to friction and a less efficient system.
Ground joint unions excel at resisting pressure loss because of their metal-to-metal sealing. This design, unlike those using gaskets, is especially beneficial for higher pressures and temperatures as it minimizes issues associated with thermal expansion.
However, even correctly installed unions may face stress during pressure spikes caused by rapid valve closures. It's important to understand these peak pressure conditions when selecting or designing unions to ensure they maintain integrity under extreme operating conditions.
The susceptibility to galling can change depending on the specific metal used. Some metals are more resistant to this issue than others. So, picking the right materials for high-pressure environments becomes crucial.
How a union is assembled can also affect its ability to handle pressure. Proper alignment and tightening techniques distribute stress more evenly, lessening the chance of leaks and weak points during operation.
Repeated thermal changes can affect not only the seal but also the microstructure of the union's materials over time, potentially making them brittle. This indicates a need to carefully choose the right materials and consider the design in applications with high temperatures.
Unions, just like other fittings and bends, contribute to overall pressure loss in a system. This can be factored into the design phase, and the union's specific shape and installation method can improve flow and reduce energy use.
The amount of torque needed to properly install a union depends on the union's size and materials. Using the correct torque is important to prevent issues from over- or under-tightening, which can both lead to leaks and damage the union.
In systems with variable loads, such as pumps that constantly start and stop, unions are more prone to premature failure. When designing these systems, engineers should take into account the impact of these dynamic forces to reduce the chance of resonance and fatigue failures.
For some fluids, viscosity changes with how quickly they are flowing. This non-Newtonian behavior makes it difficult to accurately predict pressure loss. To understand how well the system will perform, engineers need to use more complex simulation models during the design process.
Directional Flow in Pipe Unions 7 Critical Installation Guidelines for Maintenance Technicians - Thread Sealing Methods Metal Male Female Connection Points
Connecting metal male and female pipe components relies heavily on effective thread sealing methods. These methods are critical for preventing leaks and ensuring a robust connection, especially in high-pressure applications. Achieving a proper seal often involves ensuring the female thread has a slightly larger diameter than the male thread, thereby preventing binding and promoting a snug fit. Selecting an appropriate thread sealant, designed for the expected operating temperatures and pressures, is another essential aspect. These sealants are often formulated to tolerate high temperatures (up to 300°F) and significant pressures (up to 10,000 psi) while allowing for some adjustment within the piping system.
During installation, technicians must be meticulous about the alignment of the threaded components. Incorrect alignment can lead to stress concentrations and, ultimately, failure points. Applying the right amount of torque is also essential. Over-tightening can cause damage to the metal threads, while insufficient tightening can compromise the seal. In either case, galling—a phenomenon where metal surfaces fuse together—can occur, leading to difficulties with future maintenance and potential system failures. A solid grasp of thread sealing techniques and best practices in pipe union installation is crucial for maintenance technicians to build durable and efficient piping systems that can withstand the rigors of industrial operations.
When it comes to the connection points of metal pipes, particularly those with male and female threads, a multitude of factors can affect the quality of the seal. The materials used in these connections can have a significant impact, especially if they're not compatible. For example, pairing aluminum with copper can lead to galvanic corrosion, where one metal corrodes faster due to an electrochemical reaction, eventually compromising the seal. This interaction highlights the importance of careful material selection for long-term reliability.
Furthermore, threaded connections, under pressure, can stretch. Understanding the yield strength of the metals used is crucial. Exceeding that limit can lead to failure and potential leaks. It's like stretching a rubber band too far, eventually it breaks. So, it's vital to consider how the threads might react to the loads they are meant to withstand.
The proper application of torque is also vital. Too much, and you risk fracturing the material, creating points of weakness that can lead to premature failure. Too little, and you don't create a good seal, increasing the risk of leakage. Each material has an optimal torque range determined by its tensile strength and ability to deform without breaking.
The thread's shape also has implications for the durability of the connection. The roots and crests of the threads are points where stress tends to concentrate. This makes them susceptible to fatigue failure under repeated loads, which is something engineers have to factor into their design.
In addition, the seal design has a profound effect on how fluids flow through the joint. A misaligned male-female connection can create turbulence and eddies, which wastes energy and can increase wear and tear on other components downstream. It's akin to a rough spot in a river, the water doesn't flow smoothly.
The thermal characteristics of the metals involved can also cause issues. If the metals have different heat conductivities, uneven heating or cooling can lead to warping or distortion. This can be particularly troublesome in high-temperature applications, like steam systems, where consistent fittings are critical for safety and efficiency.
Interestingly, in some cases, a metal-to-metal connection can actually improve its sealing over time, as the materials get compressed and worked into a tighter seal with use. This is in contrast to gaskets that are often subject to deterioration from the operating environment.
Protective coatings like electroplated zinc can play a crucial role in protecting the threaded connection from corrosion. However, it's essential to make sure the coatings are compatible with the fluids they'll be exposed to because the wrong coatings can negatively impact the sealing ability.
Pipeline vibrations, both rotational and translational, can also loosen threaded connections over time. Engineers frequently use various locking mechanisms or thread sealants to address this problem, ensuring long-term reliability.
Many industries that operate in high-pressure or high-temperature environments require adherence to stringent testing standards for threaded connections. These tests provide assurance that the components can handle specified pressures and temperatures without failing. It's this rigorous testing in the design phase that instills confidence in the long-term safety and reliability of the systems.
By understanding these factors, engineers can design more durable, reliable, and efficient piping systems and technicians can maintain them effectively. It's a complex interplay of factors that contribute to a safe and operational pipeline system.
Directional Flow in Pipe Unions 7 Critical Installation Guidelines for Maintenance Technicians - Chemical Reactivity Protection Gasket Material Selection
When it comes to protecting pipelines from chemical reactions, selecting the right gasket material is crucial, especially in systems handling a variety of fluids. A gasket's ability to perform well depends on factors like the system's temperature, the pressure it experiences, and, most importantly, whether the gasket material is compatible with the fluids it will come into contact with. The development of new synthetic rubber materials has opened up more options for gaskets, making it easier to find the right one for specific fluid types. However, choosing a material that isn't compatible with the fluid being moved is a recipe for disaster, especially if the fluid is corrosive or the system operates at high temperatures. The result can be leaks or even catastrophic failures. This highlights how critical a good understanding of the chemical compatibility of gasket materials is to the overall reliability and lifespan of piping systems. It's not just about selecting a material; correct installation methods are also necessary to ensure a long-lasting and effective seal.
Choosing the right gasket material is crucial, as it involves considering factors like the system's temperature, pressure, and the compatibility of the gasket with both the fluids and the flanges it's sealing. The field of synthetic elastomers has exploded, leading to a wide array of gasket options for many different pipe applications. It's interesting to note how quickly new material technologies emerge, each with pros and cons.
Proper installation is also key to avoiding leaks and blowouts. Bringing flanges together gradually and ensuring they're perfectly aligned can significantly reduce the chances of a problem. I've noticed that using a minimum of three bolt tightening passes when installing a new gasket is often a good idea to get a really effective seal.
The European Sealing Association's influence is noteworthy, representing a significant portion of the European fluid sealing market, and highlighting the overall importance of selecting the right sealing materials to prevent leaks and ensure the safe handling of fluids. It's clear that the selection of gaskets has become a very important area for designers and technicians.
Gasket selection can be simplified by categorizing fluids to guide the material selection process. However, I've found that relying solely on fluid categories isn't always sufficient because you also need to account for the chemical nature of the fluid in question. Some materials, like certain polymers, simply can't handle certain chemicals without degrading, which is an issue especially common in the presence of petroleum oils or solvents. It's often better to be conservative and avoid gasket choices that might be prone to issues.
The European Standard EN 13555 helps create a consistent way to evaluate gasket performance and helps make the selection process easier. Having a standard like this lets designers compare different gasket options, which is a valuable thing to have.
There's a wide range of applications that different gasket materials are capable of handling. For instance, some are designed for temperatures up to 230°F and can be used with many different water and chemical combinations. It's impressive how some materials are formulated to operate in such a wide range of environments.
Producing gaskets that meet and exceed industry standards for safety and performance in these applications requires using high-quality materials. You can't cut corners in gasket manufacture, or you risk creating components that might fail in harsh environments. There's certainly a safety aspect here, especially in high-pressure systems where gasket failure could lead to severe accidents. The demand for higher quality and greater consistency in manufacturing has also increased, which is a trend that I think is very positive for long-term safety.
Directional Flow in Pipe Unions 7 Critical Installation Guidelines for Maintenance Technicians - Maintenance Access Position Union Placement Guidelines
When planning and installing pipe unions, particularly in industrial settings, "Maintenance Access Position Union Placement Guidelines" are essential. These guidelines emphasize the importance of strategically positioning unions to make them easily accessible for future maintenance. This focus on ease of access becomes particularly critical in situations where regular inspection or repair is required, helping minimize downtime.
By considering maintenance needs during the initial design and installation phases, engineers and technicians can ensure that unions are placed in locations that facilitate easy access to critical components of the piping system. This approach, focused on future maintenance requirements, contributes to streamlined operations. Proper union placement, especially concerning directional flow, optimizes both operational performance and simplifies troubleshooting if problems arise.
The guidelines promote the implementation of strategies that avoid the need to cut pipes during maintenance. This translates to a more adaptable and dynamic piping network, allowing for greater flexibility in responding to future operational changes and repair needs. In short, following these guidelines forms a solid foundation for a reliable piping system that can handle the demands of regular maintenance and operational efficiency.
1. **Union Placement and Operational Efficiency:** How maintenance access points are positioned on a pipe union can greatly affect how well the system runs. If unions aren't aligned properly, they can create turbulence in the fluid flow, which can make the system less efficient and also cause parts further down the line to wear out faster.
2. **Thermal Expansion Impact:** Maintenance access points can change how a union handles repeated temperature changes. In applications where things get very hot, access points need to be placed in a way that takes into account how materials expand and contract. Otherwise, the union might become misaligned or strained, increasing the risk of leaks.
3. **Stress Distribution and Union Integrity:** The placement of maintenance access points plays a role in how the stresses from pressure and flow are distributed across the union and pipes. If the unions are placed poorly, the stress distribution becomes uneven, which can lead to failures during periods of high system activity.
4. **Inspection Accessibility:** Good placement of maintenance access points can make it easier to regularly check on unions. Making sure that technicians can get to unions easily makes it possible to spot issues like wear, material fatigue, or galling before they cause major problems.
5. **Torque Application and Access Challenges:** How much torque a maintenance technician uses when working on a union can depend on how easily they can get to it. If a union is in a hard-to-reach spot, the technician might not be able to apply the correct torque. This can either lead to over-tightening, which causes the metal to deform, or under-tightening, which can lead to leaks.
6. **Material Compatibility at Access Points:** Some maintenance access configurations can unintentionally lead to combinations of different metals at union joints. Designers and maintenance technicians need to be careful when choosing materials, particularly to avoid issues where one metal corrodes faster than another due to a chemical reaction. This interaction can eventually ruin the integrity of the whole system.
7. **Maintenance Procedure Complexity:** The way a maintenance access point is designed can dictate how hard or easy the maintenance procedures are. If access points aren't thought out carefully, even basic tasks can become much more complex, which can lead to longer downtime and higher operational costs as technicians need to maneuver in tight spaces.
8. **Future System Adaptability:** Engineers sometimes don't account for how a system might change over time, like if it needs to be expanded or updated. Designing for convenient maintenance access right from the start can significantly help simplify any changes down the road.
9. **Vibration Propagation and Maintenance Access:** The distance and placement of union access points in piping systems can influence how vibrations travel through the system. For systems that operate in environments where there are lots of vibrations, the placement of maintenance access points needs to be carefully considered. Poorly placed access points can exacerbate vibration issues, which lead to material fatigue.
10. **Emergency Access Considerations:** In emergencies, maintenance technicians need to be able to access unions quickly and easily, without any obstructions. Poor accessibility can lead to delays in addressing critical failures, making the problem potentially worse and extending repair times.
More Posts from aistructuralreview.com: