Understanding Fracture Toughness Units MPa·√m Explained for Structural Engineers
Understanding Fracture Toughness Units MPa·√m Explained for Structural Engineers - The Definition and Significance of Fracture Toughness
Fracture toughness, represented by K1C, is a fundamental measure of a material's ability to resist the spread of cracks. It's a crucial factor in evaluating materials, particularly within the realm of structural engineering where safety is paramount. Expressed in MPa·√m, this metric quantifies how effectively a material can withstand the progression of existing cracks under stress. Essentially, it reveals how well a material can handle cracks, thereby impacting the overall reliability of structures. The significance of fracture toughness extends beyond simply being a numerical value. It's a key factor in streamlining manufacturing processes, ensuring components adhere to safety regulations, and ultimately preventing catastrophic failures. Engineers must understand fracture toughness to effectively analyze material responses to various loading situations and to design structures that mitigate failure risks. It allows engineers to delve deeper into material behavior, leading to improvements in design strategies.
1. Fracture toughness, represented by K1C, isn't an inherent property like density or melting point. It's a complex measure shaped by a material's microstructure, things like grain size, temperature it's exposed to, and the stress state it's under. This interconnectedness makes accurately defining and measuring it challenging.
2. The MPa·√m units tell us a lot about fracture toughness. They capture the interplay between a material's resistance to cracks growing and the size of a critical crack. Essentially, it's a combined measure that reveals how geometry and material behavior are tied together when it comes to fracture.
3. Fracture toughness can show substantial variation even within seemingly similar materials. Materials that deform a lot before breaking (ductile) tend to have higher fracture toughness than those that shatter easily (brittle) due to their ability to absorb more energy. This variation highlights the material's influence on its ability to resist fracture.
4. Several testing methods exist for measuring fracture toughness, like KIC, JIC, and GIC. However, each method can provide slightly different results. Choosing the appropriate test is vital for ensuring we're evaluating fracture toughness in a way that's relevant to the intended use and the behavior we want the material to have.
5. Intuitively, we think higher fracture toughness means longer-lasting materials. While this is often true, it's important to consider that very high fracture toughness can compromise other essential material properties. This means that material selection often involves striking a balance between desirable characteristics, making it a difficult engineering task.
6. The importance of fracture toughness becomes extremely clear in engineering applications where the consequences of failure are significant, such as aerospace and nuclear technologies. Understanding the risks and designing for safe performance in these contexts requires careful consideration of material's fracture resistance.
7. The study of "fatigue crack growth" is intriguing. It reveals that fracture toughness isn't just relevant to initial crack formation, but it also influences how quickly a crack grows when the material experiences repeated loading. This brings to light the long-term impact of fracture toughness.
8. Recent technological developments like Digital Image Correlation (DIC) are transforming how we study crack propagation. They allow for real-time observations of cracks as they grow during tests, offering a deeper, more nuanced understanding of fracture behavior.
9. The idea of fracture toughness can be somewhat counterintuitive. We might find that a material with high impact resistance may not always have high fracture toughness. This illustrates why selecting appropriate measures to assess material behavior is critical. It's not always as simple as it seems.
10. In structural engineering, understanding fracture toughness is vital for design and maintenance. By developing methods to predict when a structure might reach its fracture point, we can develop maintenance strategies that extend the structure's life and improve safety. This understanding can lead to more efficient resource allocation and improved risk management.
Understanding Fracture Toughness Units MPa·√m Explained for Structural Engineers - How MPa·√m Units Are Derived in Fracture Mechanics
The MPa·√m units used in fracture mechanics emerge from the need to understand how a material's resistance to crack growth interacts with the size of a potential crack. The megapascals (MPa) component represents the stress concentration at the tip of a crack, while the square root of meters (√m) accounts for the influence of crack length on that stress. This combined metric allows us to better grasp the relationship between a material's inherent toughness and the geometry of a developing crack.
The development of these units is rooted in the principles of linear elastic fracture mechanics, a field of study that allows us to predict how cracks might behave under different loading scenarios. In essence, it enables engineers to quantify the point at which a crack will begin to spread through a material, aiding in the design and analysis of structures. Being able to effectively characterize fracture toughness through these units is vital for engineers working on projects where structural reliability is crucial, allowing them to make informed decisions about material selection and design parameters to ensure structures meet safety requirements.
The MPa·√m unit, while initially appearing complex, actually arises from a fundamental relationship in fracture mechanics. The MPa part represents the stress, while the √m (square root of meters) reflects the critical role of crack length in influencing a material's resistance to fracture. This interconnectedness of stress and defect size is a core concept.
The presence of √m in the units is directly linked to the mathematical definition of stress intensity factors, which are crucial for understanding crack propagation. This emphasizes how the size of a crack significantly shapes a material's behavior when it comes to fracture.
Initially developed within the context of metals, MPa·√m has since become a valuable tool in assessing a wide range of materials, including ceramics and composites. Its broader applicability underlines the universal relevance of fracture mechanics across diverse engineering fields, highlighting that the principles aren't limited to traditional metallurgy.
The significance of √m extends to describing the geometry of the crack itself. Larger cracks, intuitively, require higher stress levels to start growing, and this relationship directly mirrors the square root function embedded in the unit's definition.
During the development of fracture toughness metrics, researchers have incorporated statistical mechanics to account for the inherent variability of defects within materials. Understanding this probabilistic aspect is critical for engineers making predictions about failure in real-world scenarios, where imperfections are unavoidable.
Interestingly, interpreting MPa·√m as a measure of energy release rate per unit crack area reveals a deeper meaning. It emphasizes that the unit isn't simply about failure, but rather provides insight into the conditions under which materials can safely withstand loads.
The field of fracture mechanics is seeing an increased use of numerical techniques, particularly finite element analysis (FEA), to model how different loading scenarios influence MPa·√m values. This computational approach is fundamentally changing the way engineers evaluate material safety and reliability.
Somewhat surprisingly, temperature and the rate at which a load is applied can significantly alter fracture toughness values. Higher temperatures often result in increased toughness, which adds a layer of complexity to the predictions solely based on static test results.
Current research is actively exploring how the understanding of fracture toughness might change at very small length scales. There's debate around whether conventional understanding holds for tiny components or structures, because size effects can seemingly reduce effective toughness in microscopic regions. This is particularly relevant for modern micro- and nanotechnologies.
Since fracture toughness plays such a crucial role in material science, researchers are exploring innovative ways to enhance it, like surface treatments or developing new material processing routes. These advancements could potentially lead to the creation of advanced materials with significantly better performance in demanding applications, which is exciting and a promising area of ongoing study.
Understanding Fracture Toughness Units MPa·√m Explained for Structural Engineers - Standardized Testing Methods for Determining Fracture Toughness
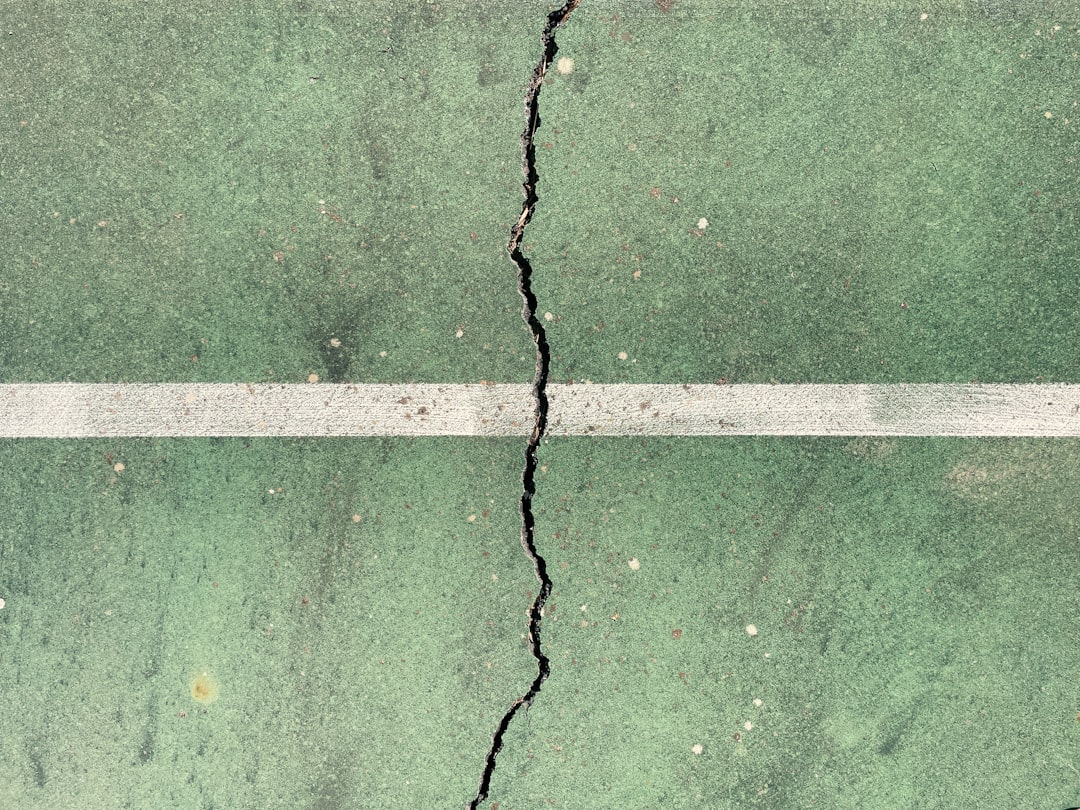
Determining a material's fracture toughness relies on standardized testing methods to ensure consistent and reliable results. These methods, including those based on the stress intensity factor (K), the J-integral (J), and crack tip opening displacement (CTOD), are designed to provide comprehensive assessments of a material's ability to resist cracks from growing. A key aspect of these tests is the accurate measurement of crack size, which significantly influences the results. This highlights the importance of meticulous specimen preparation, including careful consideration of both the specimen's size and its overall shape. Furthermore, recent advancements have broadened the scope of these methodologies by incorporating both linear elastic and elastic-plastic fracture mechanics. This has enhanced the understanding of material behavior under various stress conditions, making the results more applicable in real-world situations. A grasp of these standardized testing methods is essential for structural engineers seeking to design structures that effectively manage the risk of crack propagation and achieve optimal performance and safety.
1. A curious aspect of standardized fracture toughness tests is the reliance on various specimen geometries, like compact tension and three-point bending setups. The geometry itself can influence the measured toughness, highlighting the importance of carefully choosing the right configuration to accurately reflect the material's intended behavior.
2. It's quite fascinating that environmental factors like humidity and temperature can have a significant impact on fracture toughness results. Standardized tests often specify strict environmental conditions, but even small deviations can lead to substantially different toughness values. This reveals how material behavior can shift between brittle and ductile responses depending on the environment.
3. The K1C method, a commonly used approach, primarily applies to materials that behave in a linear elastic manner. However, when dealing with more complex materials like composites, we need alternative testing methods, which deviate from the traditional standards. This highlights a potential gap in the universality of current testing approaches.
4. It's a common assumption that tougher materials are automatically more damage-tolerant, but that's not always the case. Certain standardized tests might overlook potential flaws under critical loading conditions, leading to an inaccurate assessment of a material's suitability for high-stress applications. This suggests a potential for overconfidence in some scenarios.
5. An interesting point is that fracture toughness testing doesn't always meticulously consider pre-existing flaws within a material. Standardized methods often assess homogenous samples, potentially not accurately representing the real-world where variations and defects are commonplace. The disconnect between test specimens and actual structural elements can raise questions about the accuracy of our assessments.
6. The parameters used in fracture toughness standards are continuously evolving as new materials emerge. What works well for metals may not provide meaningful insights for advanced ceramics or polymers. This constant need for updates in testing protocols underscores the evolving nature of material science and its impact on our engineering practices.
7. We're seeing increased awareness that the stress intensity factors derived from fracture toughness tests can be influenced by the material's internal stress distribution, leading to potential under- or overestimations of its actual performance in structural contexts. This implies that our simplified models may not always fully capture the complexities of real-world materials.
8. It's perhaps surprising that not all fracture toughness standards directly incorporate crack propagation rate into their assessments, even though it's a critical element of understanding material fatigue behavior. This omission can lead to an oversimplified understanding of material integrity under repetitive loading scenarios, suggesting a possible limitation of current standardized tests.
9. In the realm of test execution, standardized fracture toughness specimen designs often prioritize simplicity and consistency over fully capturing the complexities found in real-world situations. This raises the question of how well these idealized test conditions can predict the actual behavior of a material within a structure. We might be trading complexity for simplicity, at the potential cost of predictive accuracy.
10. Many engineers might be surprised by the significant role statistical models play in interpreting fracture toughness data. The inherent variability within materials necessitates the use of complex statistical techniques to draw reliable conclusions from test results. This highlights the importance of understanding the implications of these statistical methods for building safe and reliable engineering structures.
Understanding Fracture Toughness Units MPa·√m Explained for Structural Engineers - Factors Influencing Fracture Toughness Values in Materials
Fracture toughness, a critical material property, is influenced by a variety of factors that significantly impact a material's ability to resist crack growth. These factors are interconnected and can lead to a wide range of toughness values, even within seemingly similar materials.
Material composition and microstructure are foundational influences. The chemical makeup and the arrangement of its internal structure, like grain size and phase distribution, directly affect how a material responds to stress and cracks. Processing techniques, such as heat treatments or manufacturing methods like additive manufacturing, can also heavily impact fracture toughness. For example, the strength of the bonds between layers in 3D-printed materials plays a significant role in their overall toughness.
Furthermore, the geometry and thickness of a structural component can influence constraint conditions at the crack tip, resulting in different failure modes. Thinner sections may experience a plane stress state when fractured, whereas thicker sections might experience plane strain. This distinction can lead to variations in fracture toughness values measured for a given material.
Understanding how these various factors interplay is essential for engineers. The ability to predict and manage fracture toughness is vital for material selection and design of structures where failure is not an option. This knowledge becomes even more critical in applications involving complex loading conditions or where tiny cracks could lead to catastrophic failures. While it's intuitive that higher fracture toughness is desirable, it's important to acknowledge that very high fracture toughness can sometimes lead to compromises in other critical material properties. Thus, material selection is often about finding a balance that meets the demands of a specific application.
Fracture toughness can change based on how quickly a load is applied during testing. Faster loading tends to lower fracture toughness, which reminds us that how a load is applied is important when engineers assess safety.
The presence of tiny particles within a material's structure can actually make it tougher. They act as barriers to cracks, illustrating how the internal structure of a material relates to its mechanical properties in a complicated way.
In certain polymers, changes in shape can cause a rearrangement of the material's structure. This can improve fracture toughness due to a more ordered structure developing under stress. It's like the material is rearranging itself to better resist breakage.
It's interesting that temperature doesn't always have a straightforward effect on fracture toughness. Some alloys might get tougher at certain temperatures but become brittle at others, making material selection a bit more complex.
The way a crack is shaped relative to the load it experiences can have a dramatic impact on how likely it is to spread. For instance, if a crack is oriented in a specific way, it could either make the crack more or less likely to grow. This suggests we need a good understanding of crack details when analyzing it.
Some modern composite materials exhibit what's called anisotropic fracture toughness. This means the resistance to cracks growing depends on the direction of the load. This complicates designs because the direction the load is applied matters a lot.
Smaller samples sometimes have higher fracture toughness than larger ones. It seems counterintuitive but this size effect reminds us that the size of a test sample can impact the results and needs to be accounted for when engineers apply the results to real-world situations.
Recent research shows that moisture can significantly alter fracture toughness in some materials, causing something called hydrogen embrittlement. This is a significant problem that can lead to failures in structures, something to be aware of when designing materials exposed to moisture.
The relationship between stress intensity and fracture toughness is not always a simple one. This is especially true for materials that deform plastically. This non-linear behavior needs to be modeled accurately so that we can understand how these materials behave under real-world conditions.
Fracture toughness can be significantly affected by how a metal is heat-treated. Different heat treatments can enhance or degrade toughness. This shows how material processing can really change how a material performs, something we need to keep in mind when thinking about a material's application.
Understanding Fracture Toughness Units MPa·√m Explained for Structural Engineers - Applying Fracture Toughness in Structural Design Calculations
Applying fracture toughness in structural design calculations is crucial for ensuring the safety and reliability of engineered structures. It acts as a critical input that allows engineers to predict and manage how materials respond to stress, especially when cracks are present. By understanding how things like loading speed, the surrounding environment, and the material's internal structure affect fracture toughness, engineers can make more informed decisions about which materials to use and how to design structures. However, it's also important to recognize that achieving high fracture toughness sometimes comes at the expense of other desirable material properties. This interconnectedness highlights the need for careful consideration during material selection to avoid unintended weaknesses. Ultimately, a sound understanding and application of fracture toughness principles leads to the development of more secure and robust structures for a wide range of demanding engineering applications.
1. The presence of secondary particles—like carbides or intermetallic compounds—within a metal matrix can substantially enhance its resistance to crack growth. These particles essentially act as obstacles to crack propagation, highlighting that a material's internal structure plays a significant role beyond simply determining its strength.
2. Fracture toughness isn't fixed; it can be manipulated through manufacturing processes. Techniques such as surface hardening or strategies for refining the grain structure can lead to a considerable improvement in toughness, demonstrating that carefully chosen manufacturing methods can optimize material performance.
3. Surprisingly, the shape and configuration of a structural component can dictate the measured fracture toughness. For example, parts under plane strain conditions often demonstrate higher resistance to cracks compared to those in plane stress situations, indicating the importance of considering the context in which toughness measurements are taken.
4. A material's mechanical response to loads can be complex and affected by temperature. Some materials may be very tough at room temperature, but then become brittle when exposed to lower temperatures, making them less suitable for applications in varying climates.
5. In specific high-performance polymers, the relationship between the molecular weight and fracture toughness is not always clear. Higher molecular weights might lead to greater ductility and toughness, but this can sometimes come at the cost of making the material easier to work with, creating a challenge in choosing and implementing the right material for a given task.
6. Studies suggest that the way a crack propagates in a brittle material can determine its path; whether it continues in a straight line or deflects. This behavior is sometimes influenced by the material's microstructure, highlighting that material design might be critical for preventing unexpected failure modes.
7. How quickly a load is applied can impact fracture toughness, with materials generally exhibiting reduced toughness under rapid loading. This presents a problem for engineers evaluating structures that may experience sudden shocks or dynamic forces.
8. The difference in toughness results between small-scale laboratory samples and larger-scale structures is important to consider. Small samples can sometimes provide misleadingly high fracture toughness values, suggesting that we should be careful when applying results from small samples to large structures, where stress patterns can be more complex.
9. Current standardized tests might not adequately address the impact of environmental influences—like humidity and temperature swings—on fracture toughness. This gap in the existing standards could lead to inaccurate calculations in crucial engineering applications where precise predictions of material behavior in variable environments are needed.
10. An emerging area of fracture toughness research is the study of how size influences material behavior, particularly in extremely small structures. As the size of structures shrinks, their apparent fracture toughness can change in unexpected ways, leading to a need to reconsider traditional toughness evaluation techniques in the design of micro- and nanostructures.
Understanding Fracture Toughness Units MPa·√m Explained for Structural Engineers - Future Trends in Fracture Toughness Research and Application
The future of fracture toughness research is marked by a growing interest in understanding material behavior across different length scales and under a wider range of conditions. New methods like the micropillar splitting technique allow for more precise measurements, especially at the microscopic level, enhancing our knowledge of how materials respond to fracture at small scales. Additionally, the field of high-entropy alloys is driving the development of a more complete understanding of the mechanical characteristics of novel materials, including their fracture toughness. The expanding field of biomaterials, particularly the study of bones and skeletal fractures in aging populations, highlights the importance of fracture toughness concepts in biomedical engineering.
The quest to improve the fracture toughness of brittle materials like 2D materials is driving the development of innovative design approaches. These materials, which are often found to be quite brittle, necessitate a fresh look at material design principles to create more durable and reliable applications. Overall, these trends suggest a more holistic view of fracture toughness, pushing the field towards more sophisticated techniques for assessing and enhancing the ability of materials to resist fracture in diverse engineering contexts. There's a growing need to consider how factors like material microstructure, environmental conditions, and loading rates interact with the inherent properties of the materials. This complex interaction will require further research and the development of more integrated design methodologies.
1. Fracture toughness research is increasingly delving into the intricate relationship between a material's microscopic structure and its toughness, particularly at the nanoscale. This is especially crucial for understanding how newer materials, like composites, might behave differently compared to traditional materials, raising questions about the validity of long-held toughness measurements.
2. Advanced imaging technologies, like X-ray tomography, are transforming how scientists investigate crack behavior within materials. These techniques offer real-time, high-resolution views, allowing us to study not only individual cracks but also how multiple cracks interact and contribute to material failure. This could fundamentally change how we assess and define fracture toughness.
3. The idea of "dynamic fracture toughness" is gaining prominence, especially in areas where rapid loading is common, like impact events. This involves re-examining how fracture toughness values, typically measured under more static conditions, hold up under high-speed impacts. It's particularly important for industries like aerospace and defense where high-velocity events are a concern.
4. Researchers are actively investigating "multiscale fracture mechanics" to connect material behavior across different length scales, from microscopic to macroscopic. This approach could lead to more refined fracture toughness predictions by incorporating how a material's properties vary at different scales, providing a more accurate framework for design decisions in engineering.
5. Studies have shown that introducing specific nanoparticles into polymers can dramatically boost fracture toughness, often by triggering toughening mechanisms we don't fully understand yet. This fascinating intersection of nanotechnology and materials science presents an exciting opportunity for developing materials with enhanced strength and resilience.
6. It's becoming evident that traditional standards for measuring fracture toughness may fall short when it comes to characterizing next-generation materials, particularly those engineered at the molecular level. This realization necessitates a reevaluation of current testing methods to keep pace with the rapid advancements in material science.
7. The impact of load paths on fracture toughness is a captivating area of research. It turns out that the direction from which a load is applied can significantly alter the toughness of a material. This deeper understanding could guide engineers toward designs that are optimized for specific loading conditions.
8. Research is extending into the intriguing realm of blended materials, like bio-composites, where the interaction between different material components can lead to unique fracture toughness characteristics. This holds promise for developing innovative sustainable and high-performance materials.
9. Emerging studies suggest that incorporating machine learning algorithms could improve our fracture toughness prediction models, potentially enabling real-time evaluations of material integrity in engineered structures. This advancement could transform how engineers approach design and maintenance practices.
10. The ongoing exploration of fracture toughness in demanding environments, like nuclear reactors or space applications, is crucial. These investigations are driving a deeper understanding of material behavior under extreme conditions. This is pushing researchers to develop tailored fracture toughness metrics that ensure safety in these high-stakes applications.
More Posts from aistructuralreview.com: