New Standards for Corrosion Monitoring in Crude Oil Storage Tanks A 2024 Update
New Standards for Corrosion Monitoring in Crude Oil Storage Tanks A 2024 Update - Integration of Advanced In-Situ Monitoring Systems
The incorporation of sophisticated in-situ monitoring systems represents a substantial advancement in corrosion management for crude oil storage tanks. These systems, powered by technologies such as AI, robotics, and the IoT, offer a significant upgrade over traditional, often unreliable, visual inspections. By providing real-time data, these advanced systems allow for prompt intervention in corrosion events, lessening the probability of structural damage and related risks. Furthermore, the ongoing development of innovative sensors is enabling increasingly precise measurement of both generalized and localized corrosion, further refining the ability to manage risks proactively. The growing demand for more robust monitoring protocols underscores the vital role of these technologies in mitigating operational losses and enhancing safety across the industry. While traditional methods have their place, the push toward continuous, data-driven monitoring is crucial as we strive for better risk management within these critical storage facilities.
The integration of advanced in-situ monitoring systems represents a paradigm shift in how we approach corrosion management in crude oil storage tanks. These systems provide a continuous stream of real-time data, capturing the dynamic nature of corrosion, which can be heavily influenced by factors like fluctuating temperatures and shifts in the chemical composition of the stored crude.
This advancement over older methods allows for the detection of corrosion patterns that were previously missed or difficult to quantify. Tools like ultrasonic sensors and electromagnetic techniques, which are inherently non-destructive, are increasingly integrated within these systems. This means we can evaluate both surface and internal corrosion without needing to take tanks offline, minimizing costly and disruptive shutdowns.
One of the most exciting aspects of these advanced systems is their potential for predictive analytics. By leveraging historical data and environmental information, we can generate insights into future corrosion behaviour. This allows engineers to move towards a proactive, predictive maintenance strategy, rather than reacting to corrosion events after they've caused damage. Some systems even utilize machine learning, adding another layer of sophistication to the analysis and leading to potentially more accurate predictions compared to older statistical models.
Furthermore, modern sensor technology has been developed to withstand the harsh environments typical of crude storage. Sensors can now function reliably in aggressive chemical atmospheres and across a wider range of temperatures. This robustness is key to ensuring the system's long-term viability and data accuracy.
The incorporation of wireless communication technologies into the monitoring systems is critical for efficient data flow. Continuous data transfer to central control units allows for rapid responses to emerging corrosion problems. This quick feedback loop, combined with reduced manual inspections (which can be dangerous and time-consuming), allows maintenance personnel to focus on more complex issues that require a human touch.
Additionally, some advanced systems are designed to be compatible with existing asset management software, creating a more holistic approach to managing corrosion risks. Seamless integration enhances the decision-making process through clearer data visualization and comprehensive reporting.
These advanced monitoring systems also have a significant impact on regulatory compliance. The availability of detailed, comprehensive corrosion data can be incredibly beneficial during inspections and audits by regulatory bodies.
While the initial costs associated with implementing these advanced systems can be high, the long-term economic benefits can be considerable. By reducing the frequency of costly failures and unplanned maintenance events, we can expect to see significant reductions in overall operational costs over the life of a crude oil storage tank. The promise of these integrated systems is that we can potentially manage corrosion more effectively and efficiently, ultimately contributing to safer and more reliable operations.
New Standards for Corrosion Monitoring in Crude Oil Storage Tanks A 2024 Update - Updated Computed Corrosion Rate Prediction Models
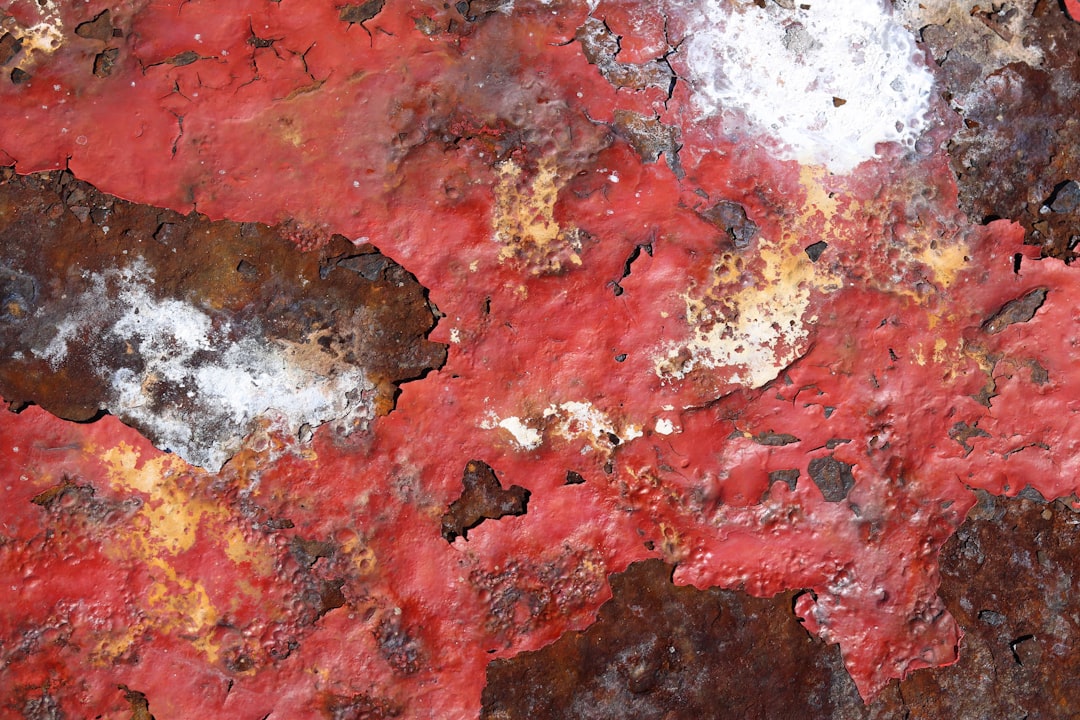
The way we predict corrosion rates in crude oil storage tanks is evolving with new computed corrosion rate prediction models. These newer models utilize advanced techniques, such as machine learning, to analyze large amounts of information including past corrosion rates, tank materials, and surrounding conditions. However, even with more accurate methods available, many still rely on older, less precise prediction models. This indicates a need for wider adoption of these modern techniques. There's also progress in areas like computer vision, which can automatically identify and locate areas of corrosion, improving how we predict future corrosion. These developments in modeling are important as standards for managing corrosion in storage tanks become more demanding. Ultimately, the goal is to better manage the risk of corrosion-related failures in these crucial facilities.
Corrosion prediction models for crude oil storage tanks have undergone refinements, incorporating a wider range of parameters into their calculations. These updated models now consider factors like pH levels, temperature fluctuations, and electrochemical potentials, leading to a more comprehensive understanding of how corrosion evolves in real-time. This shift reflects a move away from simplistic estimations towards more nuanced approaches to corrosion risk assessment.
While there's been a surge in readily available testing data, the corrosion field still relies heavily on established predictive models. This reliance, however, highlights the persistent need for more accurate tools. This need stems from the recognition that traditional models, though valuable, frequently don't fully capture the complex interplay of chemical and electrochemical processes involved in corrosion within oil and gas infrastructure.
Historically, prediction models for corrosion within pipelines often combine established chemical/electrochemical principles with empirical data obtained from lab studies and on-site observations. However, a significant leap in the sophistication of these models has been the incorporation of computer vision techniques. These techniques, built upon a vast dataset of over 140,000 images, can now classify and pinpoint corrosion locations in pipeline networks.
The field has seen a rising interest in machine learning methods for corrosion detection due to the challenges faced in various industrial settings. The adaptability of machine learning to diverse datasets and its ability to improve prediction accuracy have contributed to its expanding role. These AI and machine learning-based models can handle vast quantities of corrosion-related information, including pipeline materials, environmental circumstances, past corrosion rates, and maintenance records. This ability to integrate extensive data allows the models to potentially offer insights previously unavailable.
Computed Corrosion Rate Prediction (CRP) for crude oil storage tanks adjusts its estimations based on the specific location of the tank, environmental influences, and past experiences. These estimations typically range from 0.05 to 0.125, serving as a point of reference for preventative measures.
Current standards for corrosion rate prediction in the oil and gas industry often employ models like the NORSOK standard, which blend empirical observations with theoretical understandings of corrosion processes. But, established long-term monitoring methods, such as the ISO 9223:2012 standard, are starting to show their limitations. These traditional techniques, relying on annual data, don't provide a detailed enough picture of how corrosion behaviors unfold.
The landscape of corrosion monitoring for crude oil storage tanks has seen notable shifts in 2024, with newer standards encouraging more sophisticated analysis and prediction techniques. This transition reflects the growing awareness that a more granular and comprehensive understanding of corrosion behavior is crucial for proactive risk mitigation within this critical infrastructure. It's an ongoing challenge to balance legacy methods with the newer, more computationally intensive techniques and approaches, especially since some existing infrastructure may not be easily adaptable to these advancements.
New Standards for Corrosion Monitoring in Crude Oil Storage Tanks A 2024 Update - Revised Minimum Allowable Wall Thickness Standards
The revised minimum allowable wall thickness standards represent a crucial change in how we design and inspect aboveground storage tanks, especially those constructed in the field. These updated standards emphasize the inclusion of a corrosion allowance when calculating the minimum thickness of tank walls, a practice mandated by API 650. This move towards stricter standards underscores the need to account for the ongoing degradation of tank materials due to corrosion. While the focus initially is on field-erected tanks, it's likely that these revised standards will eventually encompass other tank types as well. It is important to note that these standards are still developing, with major revisions anticipated in early 2024. These upcoming changes will likely further strengthen requirements for corrosion mitigation and impact the industry's approach to managing these critical structures. Though progress has been made in setting these standards, it will be important to see how the industry adapts to and implements these requirements if the goal of increased tank integrity is to be realized.
The revised minimum allowable wall thickness standards encompass a wider range of considerations compared to previous iterations. This update isn't merely about the base materials; it's also about incorporating real-time corrosion data gleaned from the newer monitoring systems discussed earlier. Whether this approach will indeed lead to better maintenance practices is still under investigation, but the concept holds promise.
Interestingly, the allowable wall thickness isn't a universal value. It varies based on a complex set of factors. Environmental conditions, operational parameters, and the history of corrosion at a given site all influence the appropriate minimum thickness. This variability underscores the difficulty in establishing standardized solutions for a problem as nuanced as corrosion management.
The standards now include explicit considerations for the geometry of storage tanks. Tank shape influences stress concentrations, and this is a key factor affecting corrosion susceptibility. It's quite fascinating how a design detail can have such a significant impact on corrosion rates. Engineers need to carefully analyze tank design in light of these revised standards.
Material science is playing an increasingly important role. The updated standards acknowledge newer alloys that were not previously considered for corrosion resistance. Potentially, this could lead to designs that use thinner walls while still maintaining the necessary integrity and safety. The development of these new materials and their influence on design standards is worth watching.
Remote sensing technologies for wall thickness assessment are becoming more prevalent. These methods allow for more frequent and precise assessments of tank conditions. This reduces reliance on routine, fixed-interval inspections, which can sometimes miss subtle but significant changes in tank integrity.
In an effort to prioritize safety, the standards also advocate for stricter margins of safety. The potential for increased operational pressures and increasingly severe weather events demands a more conservative approach to design and inspection. While potentially adding costs, this focus on safety is understandable in the context of today's operational environment.
A move towards data-driven approaches is clear. Historical corrosion incidents are now integrated into wall thickness calculations. This shift away from theoretical models alone is promising, but raises questions as to how effectively these data-driven models can capture the full range of possible conditions encountered in a real storage tank.
Engineers are being asked to estimate the remaining design life of tanks with more precision than before, factoring in current corrosion rates and trends. This is a critical step towards optimizing maintenance procedures and lifecycle planning. There's still room for improvement in forecasting remaining lifespan, but this revised approach is a step in the right direction.
Predictive analytics has become a central part of the minimum wall thickness calculation. Now, adjustments can be made based on forecasts of future corrosion, rather than just historical trends. This predictive capacity represents a major advance in corrosion management, although there are always uncertainties with any prediction model.
Collaboration between different engineering disciplines is crucial for effectively using these revised standards. Mechanical, structural, and materials engineers all contribute to corrosion management efforts. This highlights the fact that effective corrosion control isn't a specialized area but requires a comprehensive approach across various disciplines within engineering.
New Standards for Corrosion Monitoring in Crude Oil Storage Tanks A 2024 Update - New Focus on Underside Floor Corrosion Prevention
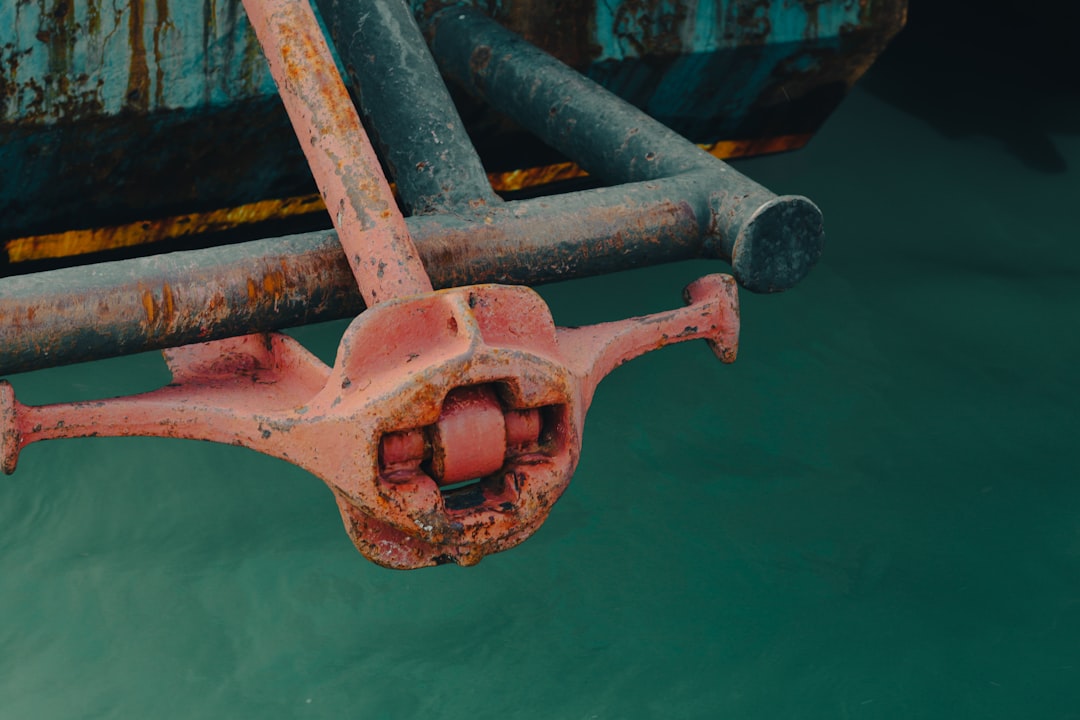
The prevention of corrosion on the underside of storage tank floors has emerged as a crucial aspect of maintaining tank integrity. This heightened awareness is driven by past instances where corrosion, often linked to flaws in cathodic protection systems and water intrusion, has led to tank failures. Traditionally, cathodic protection was the primary method of control, but its effectiveness is increasingly being challenged.
The introduction of double-bottom floors has gained traction as a technological solution to prevent corrosion. This approach, while not universally adopted, illustrates a desire for more proactive measures, particularly concerning soil-side corrosion, which poses significant risks. Soil-side corrosion has proven particularly damaging in some locations, including tanks built on oiled-sand pads, where corrosion rates can be significantly higher.
Furthermore, newly developed risk assessment metrics offer a more refined understanding of the corrosion process in tank floors. These models aim to predict corrosion rates, which vary widely, and provide benchmarks for preventative interventions. While standards related to corrosion protection exist, particularly from organizations like the American Petroleum Institute, continued development and refinement of these standards are critical to effectively combat the issue.
Moving forward, the management of corrosion in crude oil storage tanks will necessitate a holistic approach. This requires a strong understanding of how tank design, materials, and operational parameters interact with the environment to influence corrosion. By acknowledging these interconnections, we can hope to develop more targeted and effective strategies for preventing corrosion and extending the operational lifetime of these vital assets.
Examining the underside of crude oil storage tanks reveals a complex interplay of corrosion mechanisms, including widespread corrosion, localized pitting, and crevice corrosion. These are heavily influenced by the tank's construction materials, the stored crude oil's chemistry, and environmental conditions. It's becoming increasingly evident that even seemingly minor factors like variations in temperature can significantly accelerate corrosion, potentially increasing rates by a substantial 50%. Traditional predictive models often fail to fully capture this temperature-related variability, which raises questions about their long-term accuracy.
One surprising contributor to corrosion is the role of microorganisms. Microbial induced corrosion (MIC) can create localized damage, often hidden from standard inspection methods. These microbes flourish in the anaerobic environments often found within the stratified layers of crude oil, further complicating the corrosion landscape. Similarly, the accumulation of debris, particularly sediment and water, beneath tanks creates an ideal environment for corrosion. Water retention and the presence of various chemicals can accelerate the corrosion process and, interestingly, may contribute to the initiation of localized pitting corrosion.
Protecting the underside of storage tanks relies heavily on the integrity of applied coatings. However, these protective layers can deteriorate over time due to their exposure to the harsh environment of the stored crude, fluctuating humidity, and chemicals. Studies have shown that coatings can lose a substantial portion of their protective abilities, up to 40%, in such environments, underscoring the need for continuous monitoring and periodic assessment.
Properly designed drainage systems are crucial for minimizing corrosion. Water accumulation on tank bottoms accelerates corrosion, so well-functioning drainage is a vital aspect of tank design and maintenance. When these systems fail, corrosion rates often skyrocket. Interestingly, some areas on the underside are particularly vulnerable to the initiation of corrosion. Weld seams and the contact points between the tank and the ground are often weak spots that necessitate careful monitoring and tailored maintenance strategies.
Advanced imaging technologies like infrared thermography are emerging as valuable tools for the early detection of corrosion. These techniques allow for the non-invasive detection of temperature anomalies that can be indicative of corrosion beneath the tank floor. This shows promise for helping move from reactive to more proactive maintenance approaches. However, updating design standards and implementing these new technologies can be challenging because of regulatory compliance issues and integrating new tools with legacy systems.
Recent updates in regulatory standards are pushing for the integration of real-time underside corrosion monitoring into tank design. This shift towards a more data-driven approach aligns with a broader industry trend of shifting from reactive to predictive maintenance strategies. The promise of predictive maintenance lies in reducing long-term costs, with potential savings of up to 30% by preventing major corrosion events. The utilization of data from advanced monitoring systems to guide maintenance schedules is becoming critical for ensuring long-term integrity of the storage tank infrastructure.
This is an evolving area of research, with ongoing studies looking into the best ways to integrate these new technologies and approaches. Balancing older, well-established practices with the need for data-driven, predictive approaches is a constant challenge in this critical area of infrastructure.
New Standards for Corrosion Monitoring in Crude Oil Storage Tanks A 2024 Update - ASTM and AMPP Guidelines for Enhanced Corrosion Control
The ASTM and AMPP have introduced updated guidelines, specifically AMPP Guide 21569-2024, that push for a more robust approach to corrosion control. This new focus is driven by changes in PHMSA regulations outlined in the CFR Title 49 Part 192, which governs gas pipeline safety. This guide aims to help pipeline operators understand and comply with these new requirements, encompassing both gas transmission lines and crude oil storage tanks. A notable aspect is the emphasis on fostering advancements in coatings and protection technologies, driven by the industry's demand for newer materials and sophisticated techniques. As the industry works to align with the PHMSA Gas Mega Rule, these updated standards represent a significant shift in corrosion management, emphasizing the need for continuous improvement in methods of detection and prevention. This signifies an important step toward ensuring safety in this critical infrastructure.
While the updates are intended to enhance safety, it's important to note that the implementation of new standards can sometimes be challenging. Industry may have to adjust to new procedures, acquire new equipment, and retrain personnel, potentially leading to higher upfront costs. Further, integrating these standards into existing systems can be complex, especially with older infrastructure. The ultimate success of these new standards will depend on their effective implementation throughout the industry.
The AMPP Guide 21569-2024 provides a framework for incorporating corrosion control strategies that are aligned with the newest regulations, especially those outlined in the PHMSA's updated pipeline regulations. It's quite interesting that the guide emphasizes the importance of keeping pace with regulatory changes as detailed in the Code of Federal Regulations (CFR) Title 49 Part 192 related to gas pipeline operations. This new guide, developed by the AMPP Standards Committee SC 15 Pipelines and Tanks, focuses on enhancing safety measures for both US and international gas transmission pipelines, particularly concerning those impacted by the PHMSA Gas Mega Rule.
This new guide acts as a roadmap for implementing these safety regulations. It's notable that AMPP is also releasing new standards like AMPP 823-2024, addressing the evaluation of internal plastic coatings, and NACE TM0185-2024, dealing with equipment calibration for coating applications and inspections. The AMPP's goal in developing these standards is to provide pipeline operators with the tools they need to meet the corrosion control requirements for onshore gas transmission pipelines in the US.
It seems AMPP is acknowledging the rapid changes and advancements in technology and materials within the corrosion control field. It's interesting to note that corrosion prevention and mitigation standards are becoming increasingly important. The creation of resources for better corrosion management and the development of related standards help the industry achieve higher levels of performance in materials protection.
While a focus on updating standards is important, it is questionable whether these updates will be universally adopted. The implementation of updated corrosion rate prediction models utilizing advanced techniques, including machine learning, to analyze past corrosion data and environmental conditions, could provide a more accurate prediction of future events compared to older models. Furthermore, incorporating these new standards and technologies into existing infrastructure might be challenging and costly. It remains to be seen how these changes will be successfully implemented across the entire industry. The evolution of design standards and how those interact with existing infrastructure will also be a factor in the success of these updates.
This evolving field necessitates a more comprehensive understanding of corrosion mechanisms. Incorporating data-driven approaches and a broader understanding of the chemical and environmental interactions within storage tanks is crucial. For instance, recognizing that microbial activity can influence corrosion processes in unforeseen ways suggests that strategies should be developed to mitigate risks associated with microbes. Improved material science and the use of advanced coating technologies provide the opportunity to improve tank lifespans. These standards highlight the need to integrate innovative materials into corrosion control designs and consider tank geometry in design decisions.
The future of crude oil storage tank integrity relies heavily on the collaboration between several engineering disciplines. It's encouraging to see that standards encourage a more interdisciplinary approach to corrosion control. The incorporation of real-time corrosion monitoring capabilities into predictive maintenance models and designs promises improved corrosion control, minimizing operational downtime, and increasing tank lifespan. However, implementation may be complex, and these advances need to be integrated into both older and newer systems without compromising safety.
New Standards for Corrosion Monitoring in Crude Oil Storage Tanks A 2024 Update - Acoustic Emission Testing for Tank Bottom Integrity Assessment
Acoustic Emission Testing (AET) has emerged as a valuable technique for evaluating the structural health of tank bottoms in crude oil storage facilities. This non-invasive method works by detecting and analyzing the high-frequency sound waves, or acoustic emissions, that are generated when materials undergo stress or damage, like corrosion or cracking. The primary aim is to identify active corrosion processes, material defects, or potential leaks in real-time. New standards for AET within the context of crude oil tank corrosion monitoring have been established in 2024, reflecting a wider industry recognition of its effectiveness.
A key benefit of AET is its ability to perform diagnostic assessments without the need for intrusive inspections or tank shutdowns, minimizing disruption to operations. Research has shown AET to be a reliable method for evaluating the extent of corrosion and can even be used to justify delaying necessary tank maintenance, potentially saving time and resources. While various guidelines for AET exist, the recent emphasis on the technique highlights its importance in moving toward more proactive tank integrity management. Despite its growing popularity, especially for tanks with flat bottoms, the successful implementation of AET needs careful consideration. Existing practices and infrastructure may need significant adaptation to seamlessly integrate AET into routine monitoring protocols. This integration will be crucial to fully leverage the potential of AET to enhance the safety and extend the operational lifespan of crude oil storage tanks.
Acoustic Emission Testing (AET) is a method used to find active corrosion, flaws in materials, or leaks in the bottom of above-ground storage tanks. It's particularly useful for detecting issues not readily visible during routine inspections, helping to prevent potentially serious failures.
AET works by listening for the high-frequency sound waves, or acoustic emissions, generated when materials are under stress. By analyzing these sounds, engineers can gain real-time insights into the integrity of tank bottoms, which are often difficult to inspect visually.
One of the intriguing aspects of AET is its ability to differentiate between different types of acoustic emissions. This allows for a more precise understanding of the nature of a potential problem. Is it a small surface crack, or something more serious that needs immediate attention?
Research suggests that AET can detect subtle changes in the tank bottom's structural integrity. This sensitivity may allow for earlier detection of corrosion, potentially reducing unplanned maintenance costs significantly.
A key advantage of AET is that it can be performed while the tank is in operation. This avoids the need for costly shutdowns that disrupt production, a significant benefit for the oil and gas industry.
When combined with predictive analytics, AET can further refine proactive maintenance strategies. By associating sound patterns with historical data, we can potentially forecast corrosion and structural degradation with greater accuracy.
Interestingly, AET can also help monitor the impact of environmental factors on tank integrity. For instance, analyzing the changes in acoustic emissions during temperature shifts can provide deeper insights into how external conditions affect corrosion processes.
AET can assess not only the tank bottom's state but also the condition of any protective coatings applied over time. This continuous monitoring helps prevent corrosion issues before they become severe.
Furthermore, the method can evaluate the performance of cathodic protection systems. By pinpointing areas where protection may be inadequate, it allows for more targeted interventions to ensure the systems are doing their job.
While AET offers significant advantages, there are limitations. Interpretation of the acoustic data requires specialized knowledge, highlighting a potential industry-wide skills gap that needs to be addressed to ensure that the technology is implemented effectively and the data is accurately interpreted.
More Posts from aistructuralreview.com: