Understanding Section Modulus A Practical Guide to Beam Cross-Section Efficiency in Structural Design
Understanding Section Modulus A Practical Guide to Beam Cross-Section Efficiency in Structural Design - Calculating Section Modulus Basic Math and Critical Formulas
Calculating the section modulus is fundamental to understanding how a beam's cross-section will resist bending. It's a geometric property that essentially quantifies the beam's ability to withstand bending stresses. This property is derived from a simple yet powerful formula: Z = I/c. Here, Z represents the section modulus, I signifies the moment of inertia, and c is the distance from the neutral axis to the outermost fiber. The moment of inertia itself depends on the shape of the cross-section. For common shapes like rectangular sections, we have established formulas to calculate I, like I = (b * h^3) / 12, where b is the width and h is the height.
It's crucial to remember that the behavior of a material under stress influences the type of section modulus used in calculations. Elastic section modulus applies up to the material's yield point, while plastic section modulus becomes relevant beyond that point. Understanding this distinction and how to calculate both is vital for designing structures that can withstand loads safely and efficiently. The choice of a suitable section modulus directly affects a structure's overall design and efficiency, highlighting the importance of these calculations in ensuring structural integrity.
The section modulus is a foundational concept in structural design, quantifying a beam's resistance to bending. Essentially, it's the ratio of a cross-section's moment of inertia (I) to the distance from the neutral axis to the outermost fiber (c), mathematically expressed as Z = I/c. It's a measure of how efficiently a beam's cross-section can handle bending forces.
A larger section modulus translates to a more efficient beam, allowing it to withstand the same bending load while requiring less material. This translates into more cost-effective and lighter structures. For a basic rectangular beam, calculating the section modulus is straightforward using the formula Z = (b * h^2) / 6, where b is the width and h the height. This highlights how subtle changes in dimensions can significantly alter a beam's strength.
The benefits of an optimized section modulus are evident in the design of I-beams (or H-beams). Due to their geometry, they offer a far greater section modulus compared to a solid rectangular beam of equivalent weight, maximizing bending resistance.
Interestingly, the concept of section modulus isn't confined to simple shapes. Complex cross-sections can be tackled using computational methods, although these generally demand specialized software and a solid grasp of finite element analysis. However, relying solely on the section modulus in design can be problematic. It exclusively focuses on bending stress, and overlooking shear stresses can lead to unsafe designs if the beam's shear capacity isn't properly evaluated.
The relationship between the section modulus and allowable bending stress in materials like steel is established through the formula σ = M/S, where σ represents the bending stress, M the bending moment, and S the section modulus. Through this formula, designers can estimate the stress experienced by the beam under a given loading scenario.
Furthermore, by utilizing the section modulus, designers gain insights into potential failure points, resulting in more conservative safety factors, particularly for structures dealing with dynamic loading such as bridges or high-rise buildings.
It's important to remember that the section modulus can change depending on the orientation of the structural member. It's crucial to consider the loading direction when calculating the section modulus to ensure reliable structural behavior.
Finally, it's worth noting that any modifications to a beam's cross-section, like welding on attachments, inherently alter the section modulus. These changes necessitate a recalculation of the section modulus to ensure structural integrity under anticipated loads.
Understanding Section Modulus A Practical Guide to Beam Cross-Section Efficiency in Structural Design - Section Shape Effects Simple Cross Section Areas vs Complex Geometries
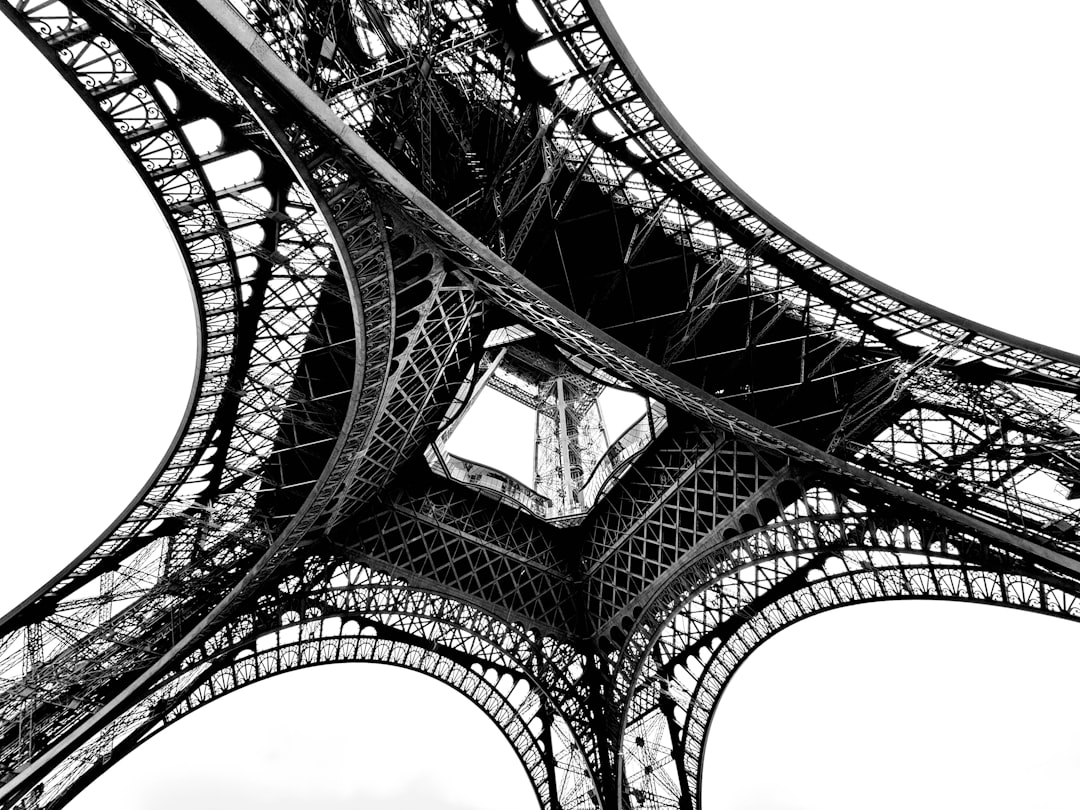
The efficiency of a beam's cross-section in resisting bending and other stresses is heavily influenced by its shape. Simple cross-sections, like rectangles, are relatively easy to analyze, while more complex geometries—like those found in I-beams or custom-shaped sections—require more sophisticated calculations. Understanding how the shape impacts both the section modulus and the cross-sectional area is crucial. Deeper sections generally offer improved stiffness and bending resistance, but the benefits of complex shapes sometimes come with the challenge of more intricate analysis.
The relationship between the section modulus (a measure of bending resistance) and the cross-sectional area (linked to axial stress) is vital for engineers. By understanding and optimizing both properties, they can achieve design efficiency, balancing the need for strength and the desire to minimize material usage. Although complex shapes can offer significant benefits, they often require computational methods, which can increase design complexity. Striking a balance between the geometric advantages and practical considerations of using a variety of section shapes is a key skill for achieving safe and effective structural designs.
The elegance of simple cross-section areas, like rectangles, in calculating section modulus starts to break down when we encounter complex geometries. These intricate shapes often lead to non-uniform stress distributions, meaning stress is not evenly spread across the cross-section. This can potentially create failure points in unexpected locations, something not easily predicted with just basic section modulus calculations.
When faced with these intricate sections, computational tools like finite element analysis (FEA) become increasingly important. FEA allows us to investigate stress and strain across the entire cross-section with much higher precision than relying on basic formulas. This becomes particularly critical as it allows engineers to gain insights into the effects of different shapes on the distribution of stresses across the entire cross-section which may not be apparent in the simplified calculations.
The shape factor, a property that relates the plastic and yield moments, also plays a more crucial role in complex shapes, particularly asymmetric ones. Two shapes with identical moments of inertia can exhibit dramatically different behaviors when under load if their shape factor is ignored or if the application of load is not fully considered. This further highlights the difficulty in applying simplified rules in a broader context.
Further, the material a cross-section is made from matters significantly, even when using the same geometry. Steel and aluminum, for instance, will not behave identically when under stress, affecting how the section modulus is actually applied. This factor must be considered for accurate assessments, otherwise an incorrect assumption about a material's properties could result in dangerous miscalculations.
In complex geometries, shear forces can become the dominant factor, potentially overshadowing the effects of bending moments often exclusively focused on in section modulus calculations. This can lead to overlooking a key element of structural integrity—shear—if we only rely on section modulus. A structural failure may be a result of a design that didn't account for the interplay of bending and shear stresses.
When dealing with dynamic loads, such as from earthquakes or strong winds, complex structures require a much more detailed investigation of their section properties. Simplistic reliance on the section modulus can be a dangerous approach and might lead to an overly simplified approach when we need to consider both static and dynamic loads that act upon the system.
The orientation of the cross-section also significantly influences the section modulus. Changes in the orientation of a cross-section change its moment of inertia, which in turn, modifies the section modulus. This aspect must be taken into account when designing, ensuring the orientation is considered with the expected loads that act upon the element.
Adding things like cutouts or holes to a cross-section can significantly alter its load-carrying capacity. Even seemingly minor modifications can lead to substantial reductions in the section modulus, which, in turn, impacts the overall performance of the beam.
Where different sections meet, as in connections or joints, stress concentrations often occur. These points require careful scrutiny as they can create regions where stresses are much higher than anticipated from simple section modulus calculations. The design must address these types of stress concentrations to ensure performance and structural integrity.
Lastly, while calculations are a powerful tool, testing remains paramount. Experimental data collected on real-world structures with complex cross-sections often show discrepancies between what theoretical calculations predict and the actual behavior. It highlights that there can be unexpected or unmodeled properties of a material or geometry that would affect a structure under load. Therefore, incorporating experimental data can enhance the accuracy of structural designs and aid in ensuring structures meet safety standards.
Understanding Section Modulus A Practical Guide to Beam Cross-Section Efficiency in Structural Design - Material Properties and Their Impact on Section Modulus Values
The material a beam is made of significantly impacts its section modulus and, consequently, its ability to withstand bending. Properties like Young's modulus, which describes a material's stiffness, and Poisson's ratio, which characterizes its tendency to deform in one direction when stressed in another, directly influence how a beam reacts to bending loads. This means that even if two beams have the same shape, but are made of different materials (e.g., steel versus aluminum), they will behave differently under the same bending stresses. Understanding these material characteristics is crucial for engineers. They use this knowledge to optimize beam designs and ensure the structure can safely withstand anticipated loads. Overlooking the influence of these material properties when calculating section modulus can lead to flawed designs and compromise a structure's safety and performance. Thus, the relationship between material properties and section modulus is a fundamental aspect of safe and efficient structural design. It needs to be carefully considered in order to ensure that a structure can withstand real world conditions.
The section modulus, while a valuable tool, doesn't exist in a vacuum. It's intricately tied to the material properties of the beam it describes, and neglecting these can lead to inaccuracies and potentially unsafe designs. For instance, materials like high-strength alloys possess much higher yield strengths compared to standard structural steel. This difference in yield strength has a direct impact on the section modulus needed to resist a specific load. Seemingly similar cross-sections made from these different materials would necessitate quite different section modulus values to ensure adequate safety factors.
Temperature plays a role too. Materials expand and contract with heat, altering their stiffness and yield strength. These changes, if not carefully considered, can lead to variations in the effective section modulus. Designs overlooking thermal effects could lead to unexpected structural behaviors and potential failures.
Material composition can also impact the section modulus. Adding trace elements to metals, like copper or molybdenum to steel, can significantly enhance their strength. This means the section modulus needs to be recalculated to reflect these enhanced material properties.
The directionality of material properties, especially in anisotropic materials like some composites, presents additional challenges. Unlike isotropic materials, where properties are uniform, anisotropic materials display variability based on the direction of loading. Calculating the effective section modulus in such cases becomes more complex, requiring careful consideration of the fiber orientation and the expected load direction.
Furthermore, the section modulus itself is not a complete picture. It focuses primarily on the beam's resistance to bending. However, structures often experience combined loading including shear, which can lead to premature failure if not carefully considered. Additionally, the inherent resistance to fatigue—the tendency of materials to weaken under repeated loading—is not reflected in the section modulus. This necessitates separate analysis to ensure materials can withstand the expected number of load cycles.
The way materials deform under stress—ductility or brittleness—also significantly influences how the section modulus is interpreted. Ductile materials can undergo significant deformation before failure, whereas brittle materials can fail abruptly. These material-specific behaviors should be factored into design decisions based on the section modulus.
Moreover, manufacturing processes like welding, forging, and casting can introduce internal stresses and microstructural variations that affect the material's mechanical properties. These hidden aspects need to be accounted for because they can significantly alter the material's response to loads and thus the effective section modulus. Similarly, residual stresses, commonly present after processes like welding, can impact the material's behavior and may alter the section modulus.
Understanding the nuances of how load types affect a material's behavior is also important. A material might be highly resistant to bending but may show limited ability to resist shear or torsion. Designers must evaluate these load-specific responses to ensure the structure can safely handle all potential forces.
In conclusion, the section modulus, while fundamental, serves as a starting point for understanding beam behavior. It's crucial to recognize its limitations and acknowledge the intricate interplay between material properties and section modulus. A deeper understanding of these factors is critical to ensuring designs are both safe and efficient. Failing to account for material variations can lead to miscalculations, impacting the structural integrity of designs and highlighting the need for a comprehensive approach during structural design.
Understanding Section Modulus A Practical Guide to Beam Cross-Section Efficiency in Structural Design - Load Distribution Analysis Through Cross Sectional Properties

Understanding how loads distribute across a beam's cross-section is fundamental to designing efficient and safe structures. The cross-section's ability to resist bending is intrinsically linked to its moment of inertia and section modulus. These properties give us a sense of how the beam will behave under load. However, the way a beam distributes stress is largely governed by the shape and arrangement of its cross-section. While simple shapes are relatively easy to analyze, complex geometries can create uneven stress distributions. This complexity often necessitates the use of more advanced analysis techniques like finite element analysis, which provides a much more detailed understanding of stress patterns across the section.
Crucially, the material the beam is made from also significantly impacts load distribution. Different materials possess distinct properties regarding stiffness, strength, and response to stress. This means a steel beam and an aluminum beam with the same cross-sectional shape will behave differently under the same load. It's the interplay of both the geometry of the cross-section and the material properties that determines the actual load distribution and, ultimately, the beam's strength and stability.
The consequence of ignoring either the complex geometry or the material properties in these calculations can be significant. It can lead to designs that don't perform as expected and potentially introduce safety concerns. A robust understanding of how cross-section properties interact with loading and material behavior is critical for effective structural design. Without a thorough analysis of the cross-section's interaction with the applied load and material response, there is an inherent risk of making inaccurate design choices.
The way loads distribute across a beam's cross-section is rarely uniform, leading to concentrated stresses that can be higher than what simple section modulus calculations predict. This is especially true in areas where the beam's shape changes or at connections, highlighting the need to consider stress concentrations carefully during design.
In complex shapes, the material a beam is made of can influence load distribution more than the shape itself. For instance, a beam made of high-strength steel may distribute stresses differently than one made of mild steel, changing the effective section modulus we might calculate using basic methods.
The idea of an "effective flange width" comes up when analyzing I-beams under load. The effective width might be smaller than the actual flange width depending on shear and bending, which requires us to adjust section modulus calculations to get a better understanding of the load distribution.
When a structure like a cantilever beam is loaded from the side, it can twist or experience torsional effects. This introduces a complex interaction between bending and shear forces, making load distribution analysis more challenging and questioning the assumption that axial forces are the primary drivers of section modulus.
Repeated loads can lead to material fatigue and unexpected failure, which are not predicted by initial section modulus calculations. This is crucial to understand, especially for structures that experience repeated loads. Fatigue can cause progressive damage over time under cyclic loading conditions.
Beams with a changing height, like tapered beams, show non-linear behavior when bent. This uneven distribution of material leads to variations in the section modulus and requires advanced analysis methods to capture how loads are dispersed throughout the beam.
Shear deformation can be substantial in short beams or beams with heavy, concentrated loads, influencing the overall load distribution. Typical section modulus calculations often ignore these effects, which can lead to underestimating deflections and stress responses under real loads.
Residual stresses from manufacturing, or thermal expansion in composites, can create unforeseen load paths. This means that relying solely on classical mechanics might not fully capture the load distribution within a beam's cross-section.
We can use the principle of superposition to analyze the load distribution in beams subjected to various loads. However, the resulting stress distributions aren't always a simple combination of the individual effects, especially in complex or overlapping shapes. This can introduce inaccuracies when we try to predict the section modulus under combined loading.
In applications like bridge design, dynamic loads, like those caused by traffic, can significantly change how loads distribute across a section. This is something that basic static analysis can't predict. To ensure safety and longevity, engineers need to include advanced dynamic analysis in their load distribution evaluations.
Understanding Section Modulus A Practical Guide to Beam Cross-Section Efficiency in Structural Design - Elastic vs Plastic Section Modulus Real World Applications
The practical use of elastic and plastic section moduli hinges on how materials are expected to behave under load. Elastic section modulus is typically employed in initial design phases, ensuring safety and functionality within the elastic limits of the material. Conversely, plastic section modulus is critical for evaluating a beam's ultimate capacity, especially when the cross-section experiences complete yielding. Understanding the differences between these two concepts helps engineers make better design choices, optimize beam performance, increase safety margins, and respond effectively to varying load conditions. Effectively, the careful use of both concepts is necessary to create structurally sound and efficient designs within the field of structural engineering. The goal is not only efficient designs, but also resilient structures.
1. **Elastic vs. Plastic Behavior:** The distinction between elastic and plastic section moduli hinges on the material's response to stress. The elastic section modulus (Zₑ) is applicable only within the elastic range, up to the material's yield point. However, when stresses exceed the yield strength and the material enters plastic deformation, the plastic section modulus (Zₚ) becomes relevant. This highlights the importance of considering both aspects in structural design, especially for ductile materials that can undergo significant deformation before failure.
2. **Tension and Compression:** While the elastic section modulus often takes center stage in tension applications, the plastic section modulus proves crucial for compression members. This is particularly true when concerns about buckling arise. Understanding how materials respond under tension versus compression is essential for crafting reliable designs that can handle a variety of loading scenarios.
3. **The Role of Length:** The influence of a beam's length on its elastic and plastic section moduli shouldn't be overlooked. Longer beams, particularly those subject to bending or experiencing critical buckling loads, can have distinctly different effective section moduli compared to shorter ones. This is because the manner in which loads are distributed changes with length, and hence the ability to withstand those loads also changes.
4. **Temperature's Impact:** Temperature can significantly affect a beam's section modulus, especially for materials like steel. Elevated temperatures can lead to a decrease in yield strength and can modify the elastic characteristics of the beam. These changes, particularly in scenarios like fire exposure, necessitate reevaluation of the section modulus to ensure the structure's safety and integrity under challenging conditions.
5. **Complex Load Paths:** In intricate structural systems with multiple load paths, the interaction between individual beams can create non-linear behaviors. This complexity challenges the direct application of simple section modulus calculations. It often necessitates more advanced computational techniques or specialized software to accurately capture the beam's behavior under such complex loading scenarios.
6. **Anisotropic Materials:** Composite materials often exhibit anisotropic behavior, meaning their properties vary depending on the direction of the applied load. This property significantly complicates calculations for both the elastic and plastic section moduli. To make accurate assessments, designers must consider the orientation of the reinforcing fibers within the composite and the specific loading conditions the beam is expected to encounter.
7. **The Interplay of Shear and Bending:** While the section modulus focuses on bending stresses, a thorough analysis of a beam's capacity also needs to consider the interaction between shear and bending stresses. This is especially important for short beams or those carrying heavy concentrated loads. Neglecting the effects of shear can lead to underestimations of the beam's actual load-carrying capacity and potentially to overlooked failure modes.
8. **Understanding Failure Modes:** Elastic and plastic material behaviors result in distinct failure modes. Elastic failures are often sudden and brittle, while plastic failures are more gradual and are characterized by significant deformation. This understanding of the failure mechanisms allows engineers to design more resilient structures by proactively identifying potential failure points based on the expected loading conditions and material properties.
9. **Dynamic Loads and Structural Behavior:** When designing structures that will experience dynamic loads—such as those from machinery or seismic events—the section modulus needs careful consideration. These dynamic loads can introduce stresses beyond those anticipated under static conditions, necessitating a more in-depth assessment of the elastic and plastic section moduli to ensure safety.
10. **The Effect of Reinforcement:** Adding reinforcement elements, such as stiffeners or ribs, can fundamentally alter a beam's effective section moduli. These additions redistribute forces within the beam and can greatly improve performance. However, these changes also require recalculating the section moduli to reflect the altered elastic and plastic properties of the modified beam.
Understanding Section Modulus A Practical Guide to Beam Cross-Section Efficiency in Structural Design - Optimizing Beam Design Using Section Modulus Calculations
Optimizing beam design hinges on effectively utilizing section modulus calculations. The section modulus essentially represents a beam's capacity to withstand bending forces, a critical factor in structural integrity. Understanding how a beam's cross-sectional shape and the material it's made from affect the distribution of these forces is key. The section modulus provides a measure of a beam's efficiency, which allows engineers to balance strength with material usage. While basic calculations provide a foundational understanding, complex geometries and loading scenarios demand more sophisticated methods like finite element analysis. These methods offer a deeper insight into stress concentrations and failure modes, crucial for ensuring structural safety, especially in dynamic environments. Ultimately, the goal is to create structures that are not only strong and stable but also use materials efficiently. This involves a careful balancing act where the section modulus serves as a guidepost for developing optimized and resilient structural designs.
1. **The Delicate Nature of Section Modulus:** Even subtle tweaks to a beam's shape, particularly its height and width, can significantly alter its section modulus. This sensitivity emphasizes the importance of precise design parameters.
2. **Orientation Matters:** The section modulus isn't a fixed value; it's dynamic, changing based on how the beam is oriented. Rotating a beam can lead to a different effective section modulus due to variations in its moment of inertia, making orientation a key consideration during design.
3. **Load Type Impacts:** Different types of loads (static versus dynamic) place distinct demands on a beam's section modulus. For instance, structures in earthquake-prone areas may require larger plastic section moduli to account for energy dissipation during seismic events.
4. **Complex Shapes, Complex Calculations:** While intricately shaped beams can offer enhanced load-bearing capacity compared to simple rectangular beams, analyzing them usually necessitates sophisticated tools like finite element methods. Standard section modulus calculations don't adequately capture the behavior of these irregular geometries.
5. **Material Matters a Lot:** The material a beam is made of can introduce significant unpredictability into section modulus calculations. For example, composite materials with directional properties necessitate a tailored approach to calculating an effective section modulus that accurately represents their unique stress responses under load.
6. **Predicting Failure:** Understanding the differences between elastic and plastic section moduli is vital for predicting potential failure modes. Elastic failures tend to be sudden and brittle, while plastic failures involve a more gradual yielding process. This distinction guides design choices based on expected loading conditions.
7. **Buckling Concerns:** In long, slender beams, the role of the elastic section modulus becomes even more critical when buckling is a possibility. Designs need to explicitly account for this instability, demanding a thorough understanding of section modulus behavior under compressive loads.
8. **Dynamic Behavior Analysis:** Structures experiencing dynamic loading, like bridges subjected to traffic, necessitate a more holistic evaluation of both elastic and plastic section moduli to properly assess their dynamic response over time and prevent premature failures.
9. **Manufacturing's Influence:** The manufacturing process can introduce residual stresses and distortions into a beam, potentially modifying its section modulus. These effects must be considered during design to prevent inaccurate estimations of load-carrying capacity and maintain structural integrity.
10. **Don't Forget Shear:** Often, section modulus calculations focus primarily on bending moments, inadvertently neglecting shear forces. This can result in an underestimation of a beam's true performance, particularly in shorter beams or when concentrated loads are applied.
More Posts from aistructuralreview.com: