7 Critical Structural Components Third-Party Home Inspectors Often Miss During New Construction Evaluations
7 Critical Structural Components Third-Party Home Inspectors Often Miss During New Construction Evaluations - Foundation Anchor Bolt Spacing and Missing Wall Ties Below Grade
During inspections of newly constructed homes, it's crucial to carefully examine the foundation's anchor bolt placement and the existence of wall ties beneath the ground level. These elements are fundamental to the building's structural integrity. Anchor bolts, which must penetrate at least 7 inches into the concrete, play a key role in counteracting upward forces. Proper spacing of these bolts is essential, particularly in regions with strong winds or earthquakes, and it's typically limited to no more than 6 feet for one- or two-story structures, and even tighter for taller buildings. Furthermore, the absence of wall ties below grade can jeopardize the overall stability of the house since they're meant to firmly connect the walls to the foundation. This is a common oversight in third-party inspections and is an issue that should not be ignored. Confirming that these elements meet established building codes and standards is crucial not only to bolster structural soundness, but also to prevent future safety risks that often stem from overlooking such essential details during construction.
Foundation anchor bolts, essential for securing the structure to the concrete foundation, are often overlooked during inspections. While building codes typically specify a minimum diameter of 1/2 inch and a 7-inch embedment depth, the spacing requirements can differ based on the building's height and local conditions, usually ranging from 4 to 6 feet. This seemingly minor detail influences a building's ability to withstand lateral forces, highlighting the importance of adhering to code.
The crucial role of wall ties, especially those below grade, in connecting the foundation and the wall system is often underestimated. Their absence or incorrect installation creates a vulnerability in the structure, as they are responsible for preventing wall movement and potential collapse, a serious concern in new construction where these issues might not be immediately evident. It's alarming how readily this component can be missed, especially when dealing with a below-grade portion of a foundation.
The type of anchor used, whether it's a traditional J-bolt, a threaded rod, or a manufactured anchor, also matters. However, regardless of type, they should provide adequate strength for the specific load requirements, including resisting uplift forces. This is particularly true in regions with high wind or seismic activity where uplift forces can create significant strain. Yet, proper installation and the choice of materials are critical, as corrosion in the anchor bolt can significantly weaken the foundation.
Understanding the forces at play when designing the foundation is vital. It's not merely about the strength of the anchor but also about how it interacts with the concrete and the soil conditions. Soil movement and moisture can impact the effective bearing strength of the foundation and must be factored into the design and construction. This can be overlooked by builders who might focus solely on the immediate needs of the project, not the long-term impact of soil variability.
A consistent and thorough training program for construction workers on proper anchor bolt installation is also lacking. This leads to variability in installation practices and an increased risk of errors that can impact long-term safety and structural integrity. While anchor bolts and wall ties are not always readily visible, a third-party inspection should consider their placement, spacing, and installation practices to ensure the foundation and wall system are securely bound together, preventing future problems. The failure to consider the interaction of these components with the wider structural and soil environment can have substantial and possibly expensive consequences.
7 Critical Structural Components Third-Party Home Inspectors Often Miss During New Construction Evaluations - Post Tension Cable Placement and Tensioning Documentation Gaps
Post-tension cables are a key element in reinforcing concrete structures, boosting their strength and ability to bear weight. However, a common issue in new construction is a lack of thorough documentation regarding how these cables are placed and tensioned. This oversight, frequently missed by third-party inspectors during their evaluation, creates a potential vulnerability in the building's structural soundness. The design process dictates the spacing and tensioning of these cables based on the anticipated loads and structural requirements, and deviations from this can result in problems like excessive bending or cracking later on. Ensuring that the cables are properly shielded from weather conditions, especially before the concrete is poured, is crucial to protecting their integrity. It's also essential to have the tendons thoroughly inspected and documented before the concrete is in place, as any repair work becomes far more complicated after. Skipping these crucial checks not only diminishes the benefits that post-tensioning is meant to offer but also potentially compromises a building's structural performance and long-term safety.
Post-tensioned cables are a valuable tool for enhancing the strength of concrete structures, similar to traditional reinforcement, but they provide a higher level of structural integrity and load-bearing capacity. However, a consistent issue arises in the form of inadequate documentation regarding cable placement and tensioning procedures. This lack of detailed records can cause significant problems down the line.
One key concern is the potential for inaccurate load distribution. When tensioning procedures aren't properly recorded, the load forces within the structure might not be distributed as intended by the structural engineer. This can increase the risk of unexpected structural failure or damage over the structure's lifespan. Furthermore, inconsistencies in the actual cable placement during the construction phase can deviate from the design intent, further complicating any subsequent structural analysis and possibly violating established safety protocols.
Another issue is the potential for material degradation. Post-tension cables are not immune to the impacts of the surrounding environment, including water exposure and corrosion. Sadly, many inspection practices don't prioritize documenting the cable materials and any protective measures employed, potentially leading to premature cable failure and related structural issues.
Furthermore, future renovations or repairs are often carried out with limited knowledge due to a lack of thorough documentation. Decisions are often made based on assumptions instead of precise field measurements and information about how the system was originally installed. This can compromise the structural integrity of the building in the long run.
Another factor is the variability of initial tensioning tolerances. While there are accepted ranges for initial cable tension, many construction sites don't have consistent practices for documenting these values. This can lead to excessive stress on the concrete, possibly resulting in cracks or deformation over time. The lack of uniform training in post-tensioning techniques further contributes to errors in both cable placement and tensioning practices. Workers who haven't been adequately trained may inadvertently neglect essential aspects, increasing the long-term risk to the structure.
Many construction projects also fail to incorporate continuous monitoring of post-tension cables after the initial tensioning process. Without this ongoing inspection, potential issues can remain hidden until it's too late to take corrective action. Additionally, compliance with local building codes is challenging without precise documentation. Gaps in compliance not only threaten structural safety but can also lead to legal difficulties for builders and inspectors. Finally, having accurate records about cable placement and tensioning is critical for predicting a structure's long-term performance. Without detailed documentation, accurately assessing and evaluating the structural behavior in the future can be a complex undertaking, making maintenance and inspection processes much more difficult.
These documentation gaps highlight a critical area where third-party inspectors often miss opportunities to identify potential future problems. This information is essential to ensuring the long-term stability and safety of the structure and is often overlooked during standard inspection processes.
7 Critical Structural Components Third-Party Home Inspectors Often Miss During New Construction Evaluations - Load Path Transfers Between Floor Systems Missing Metal Connectors
Load paths are essential for transferring forces throughout a building, ensuring that loads from upper floors and the roof are effectively distributed down to the foundation. These paths rely on a network of structural components working together, and a key part of this system are the metal connectors that link floor systems to one another and to other parts of the building. If these connectors are missing, or not installed as intended, the load path is interrupted, leading to a weakened structure.
This is a frequent oversight during third-party home inspections, primarily because these connections might be hidden within walls or ceilings. The absence of these connections compromises the ability of the building to resist things like wind uplift or other lateral forces, which become more significant in taller structures or those located in areas prone to strong winds. Since these connectors are essential for holding the building together, overlooking them could create issues that only become obvious later, such as cracking or even structural failure in severe conditions.
Essentially, it's like the missing link in a chain. It might look complete at first glance, but its absence makes the entire system less resilient. While it is often hard to see these connectors, a thorough inspection should pay close attention to how the various levels of the building are connected, and whether the appropriate connectors exist to ensure the stability and integrity of the entire load path. A simple oversight during construction can have significant and lasting consequences later.
Imagine the skeletal framework of a house. Load paths are like the pathways along which forces—from the roof, upper floors, and even wind—travel down to the foundation. For this system to work correctly, a continuous flow of force is essential. However, when we're talking about transfers of loads between floor systems, missing metal connectors can disrupt this crucial flow, potentially leading to a cascade of problems.
These connectors, which can take the form of shear clips, beams, or joists, are meant to ensure a smooth transition of force. Without them, the load path might rely on weaker mechanisms like friction, which may not hold up against strong lateral forces (like those experienced in earthquakes or high winds). Think of it as a chain—if one link is weak, the entire chain could fail.
This missing link can have a direct impact on floor performance. Floors are designed to be rigid, but without proper connectors, they can start to deflect or vibrate excessively. This not only makes the house less comfortable to live in but can also present a safety hazard. It's even more critical during construction as floors lacking proper connections are more prone to warping or even partial collapse before the house is even finished.
The problems don't always show up immediately. Over time, these connections can corrode or weaken due to weather and environmental conditions. This is even worse if they weren't correctly installed in the first place. Repairs or replacement become complex and costly down the road.
Furthermore, many building codes explicitly require metal connectors for load transfer, so failing to use them can be a legal issue for the builders, leading to fines or other issues. This is also a matter of system interdependence—the failure of one element, such as a metal connector, can cause issues elsewhere. It's all connected.
Third-party inspectors often miss these connectors simply because they are hidden within walls or floors. They need to be more diligent and specifically request access to these hidden areas to make sure everything is up to code. Ultimately, the absence of these connectors can lead to costly repair or rebuild expenses years down the road, making early detection crucial. This highlights the importance of thorough inspections during construction to avoid these kinds of issues, as they are often not immediately apparent. The long-term consequences of skipping a few connectors can be quite substantial.
7 Critical Structural Components Third-Party Home Inspectors Often Miss During New Construction Evaluations - Roof Truss Bracing and Gable End Wall Connections
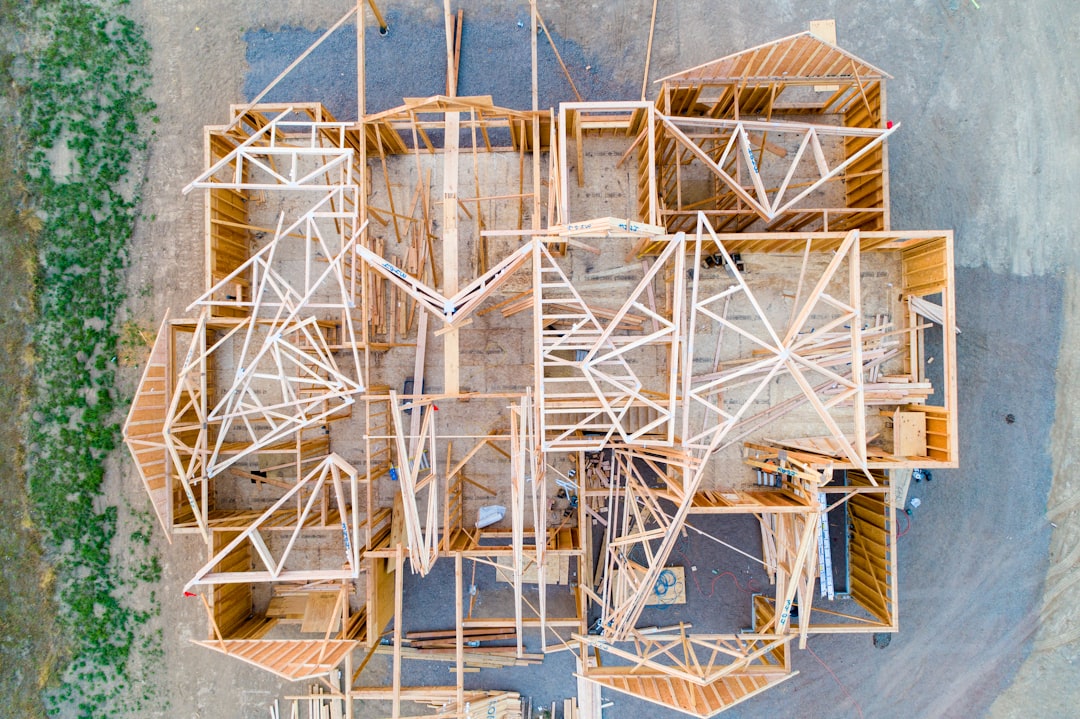
During inspections of newly constructed homes, a frequent oversight involves the bracing of roof trusses and the connections to gable end walls. These elements are critical for ensuring the stability and integrity of the roof system, particularly when subjected to wind loads.
The absence of proper engineering review or a thorough understanding of the relevant building codes can lead to insufficient bracing within the roof truss system. This can compromise the roof's ability to resist wind forces, potentially causing structural damage.
Furthermore, the interface between the gable end walls and the roof trusses is crucial, as it's the point of transfer for a significant amount of load. These connections must be properly engineered and built to handle anticipated loads, especially for homes in areas with strong winds or severe weather patterns. In many cases, specific methods of bracing are required to ensure that these connections are adequately reinforced, which can be easily missed if proper attention to detail is absent during construction.
Without sufficient bracing at the gable end walls and within the roof truss system, the structure becomes vulnerable to wind uplift and potential failure. It's important that inspections are thorough in reviewing these elements because the long-term stability and structural performance of the home are directly dependent on the quality and compliance with code of these connections and bracing systems. Builders and inspectors should prioritize these areas and ensure that all connections and bracing adhere to design specifications and local building regulations. Failing to do so can have severe consequences for the integrity and safety of the house, emphasizing the need for stringent scrutiny during new construction evaluations.
Roof truss bracing and the connections at gable end walls are often overlooked during new home construction inspections, yet they are critical for a building's overall stability and safety. The International Residential Code (IRC) mandates that exterior elements, including attachments, can resist anticipated wind pressures. This places a heavy emphasis on how well gable end walls are attached to the roof truss system. In high-wind areas, even the framing method, like balloon framing, might need adjustment to accommodate these forces.
Roof trusses themselves rely on internal bracing to remain stable. Unfortunately, in many homes, there isn't much engineering scrutiny of the finished roof system, leading to potential problems. The framing of the gable end walls acts as support for the truss, and connections must be strong enough to handle wind, especially at areas like overhangs.
Sometimes the plans call for specific bracing patterns, like T or L bracing, and these need to be followed precisely. It's crucial to ensure that the connections between the gable end walls and the truss system are strong enough, especially in situations with longer roof spans. This is a common weak point in many structures, where failures can start and spread through the entire system.
Proper temporary bracing is important for the early construction phases of installing gable trusses, ensuring their stability. However, it seems like many builders don't fully grasp the importance of proper bracing for the gable end walls, possibly due to a lack of clear guidelines and instructions in the initial building designs. It's worth considering that builders aren't always experts in structural engineering, so this responsibility often falls to the designer who should provide clear instructions for bracing to guarantee that all parts, including the gable end walls, are properly designed for local conditions.
A deeper investigation into the bracing choices is warranted as it can significantly impact the roof's ability to handle various loads. Understanding the nuances of load transfer and potential issues with material performance related to bracing, such as the impact of humidity or dynamic loading, can be beneficial. Furthermore, there appears to be an occasional disconnect between design intent and actual construction when it comes to bracing details, leading to possible future risks. This suggests that the overall quality assurance process could be strengthened with a focus on bracing practices throughout the building process, not just at the design phase. Perhaps an improved emphasis on proper bracing methods and the consequences of inadequate bracing in educational and training programs for construction workers might lead to better quality control on the construction site.
7 Critical Structural Components Third-Party Home Inspectors Often Miss During New Construction Evaluations - Shear Wall Nailing Patterns and Hold Down Installation
During new construction inspections, the way shear walls are built, particularly how they're nailed and how the hold-downs are installed, is really important. These walls are essential for handling sideways forces that can push or pull on a house, but if the nails aren't put in correctly, they won't work as well as they should. This means following specific nail patterns and making sure hold-down devices are correctly spaced. These details are crucial for safely transferring loads from the walls down to the foundation, especially when the house experiences strong winds or other kinds of pressure. Unfortunately, many third-party inspectors don't pay enough attention to these details, and this can lead to hidden structural weaknesses that might not show up until there's a problem. Doing a complete inspection that checks if these installation processes are done correctly can prevent future headaches and ensure the house is built strongly and safely.
Shear walls are fundamental for resisting wind and other lateral forces that can severely impact a building's safety. However, their effectiveness hinges on proper installation, especially the nailing patterns and the hold down devices. The nailing pattern isn't a random design choice; it must align with specific guidelines to ensure the wall can handle the forces it's designed to resist. If a builder deviates, the shear wall might not perform as intended, particularly during a seismic event, putting the entire structure at risk.
Hold down brackets are critical for preventing the shear wall from tipping over during high winds or earthquakes. These brackets need to be appropriately sized for the expected loads, and their placement matters. Ignoring these requirements compromises the safety of the structure, making it susceptible to instability during extreme conditions.
Local building codes often dictate specific nailing patterns and the locations of hold down brackets, factors that can vary depending on factors like the shear wall's height and the seismic activity in the area. Following these codes isn't just a formality; it ensures that the shear wall performs as intended. If the design doesn't adhere to code, structural vulnerabilities may emerge, causing issues that may be hard to fix later.
Moreover, how the shear walls connect to other parts of the building is essential, like the connection between the shear walls and the floor or roof systems. It's critical that these connections smoothly transfer loads across the structure. Without the proper metal connectors in these areas, forces could be unevenly distributed, leading to unexpected weaknesses that compromise the building's integrity.
A quick visual check of the nailing pattern can reveal if it aligns with the structural plans. Any discrepancies may suggest a more significant issue with construction practices, possibly not easily correctable after construction is complete. The quality of the materials used in the shear wall system is also important. For example, using inferior or improperly treated wood can compromise the wall's capacity to resist lateral loads, making the wall more prone to failure under stress.
Installation errors often crop up around areas like windows and doors, where shear walls transition. These locations require extra care, as improper nailing or missing hold downs can severely reduce the wall's overall performance.
Despite its importance, performance testing for shear walls and their hold down systems isn't a common practice. This means potential weaknesses might not be uncovered before it's too late. Current structural engineering practices are starting to focus on improving shear wall connectivity through advanced nailing techniques and enhanced hold down designs, all aimed at better managing forces across the structure. This is a departure from traditional practices that often don't pay enough attention to these details.
The timing of an inspection also plays a role. Early inspections during framing can help reveal errors before they are concealed within completed walls. However, once walls are fully finished, finding critical issues is more difficult. This emphasizes the need for meticulous scrutiny during the early stages of construction.
This information is purely for educational purposes and does not constitute any endorsement of particular products, companies, or services. The insights provided are intended for general awareness and should not be considered professional engineering advice. Always consult with a qualified professional before making any structural decisions.
7 Critical Structural Components Third-Party Home Inspectors Often Miss During New Construction Evaluations - Structural Steel Moment Frame Connection Details and Welding
Within the broader context of structural integrity, the intricacies of **structural steel moment frame connection details and welding** often escape the scrutiny of third-party home inspections during new construction. These connections, critical for transferring bending moments and enhancing a structure's resistance to seismic forces, are frequently overlooked. While both bolted and welded connections can be utilized, welded connections, often utilizing extended end plates, provide the advantage of full moment continuity. However, this comes at the cost of increased fabrication complexity and potential for errors if not executed meticulously.
Standards like AISC 358 provide crucial prequalification guidelines for connections designed to withstand specific seismic loads. Yet, it's disconcerting how often these guidelines are overlooked in construction. The consequences of improper welding or connection detailing can be severe, particularly in areas prone to earthquakes. Failure to meet the demands of seismic design can lead to structural weaknesses that may not reveal themselves for many years, potentially resulting in catastrophic failure.
This underscores the vital role of comprehensive third-party inspections that consider not just the visible aspects of the structure, but also the often-hidden complexities of these connections. It's during these inspection processes that the potential for future structural issues, directly linked to the quality of these details, can be revealed. Without a thorough evaluation of these critical connections, new homes might unfortunately inherit vulnerabilities that remain hidden until a major event, like an earthquake, exposes them, demonstrating the urgent need for more rigorous inspection practices.
Moment frame connections, often a focal point in steel structures, typically involve extended end plates welded to a beam's end and then bolted to a column, facilitating the transfer of bending moments. The design of the cover plates needs to consider how shear is distributed through the beam's web and the position of the bolt group that resists the shear, as this eccentricity can significantly impact the moment transferred. The American Institute of Steel Construction (AISC) provides prequalified connection details in AISC 358 for both special moment frames (SMF) and intermediate moment frames (IMF) connections, aiming to ensure they meet specific seismic resistance demands.
While both bolted and welded connections can be utilized to resist moments, welding delivers full moment continuity. However, it typically leads to higher fabrication costs and complexity. For instance, reduced beam section (RBS) connections, often used in seismic design, need to adhere to strict guidelines to function properly under such extreme loads.
Standards like AISC 341 and AISC 358 underscore the critical role these connections play in maintaining the overall stability and earthquake resistance of steel moment frames. However, the robustness of the column itself can also influence the performance of the connection, highlighting that specialized connection designs might be required if a cantilever moment necessitates balancing.
Home inspectors often overlook the subtleties of these connections during new construction evaluations, raising concerns about the overall structural integrity. In the United States, field welded connections are commonplace for moment connections and are standard practice in seismic design, as outlined by AISC. Various connection designs, encompassing bolted splices and welds, are detailed in structural engineering standards, seeking to ensure construction practices prioritize safety and durability. It's a complex topic, and the devil is often in the details, which inspectors and builders alike need to better understand. The consequences of an oversight can be significant, ranging from minor repairs to full reconstruction in extreme cases, reinforcing the need for a cautious and attentive approach during inspections.
7 Critical Structural Components Third-Party Home Inspectors Often Miss During New Construction Evaluations - Engineered Floor System Load Distribution and Blocking Requirements
Engineered floor systems rely on a well-defined distribution of loads and proper blocking to maintain their integrity. These systems, often incorporating I-joists and other engineered wood products, demand careful attention to how loads are transferred throughout the structure. The role of blocking, using components like TJI joints or Structural Composite Lumber, is to distribute both vertical and horizontal forces within the floor assembly. This proper transfer of forces is crucial for preventing areas of unsupported loading that can compromise the structural integrity over time.
A consistent problem during inspections is the lack of attention given to how these engineered systems distribute loads and the placement and adequacy of blocking components. These often-overlooked aspects can lead to significant problems in the future, such as excessive deflection or even structural failure. Ensuring these engineered floor systems are designed and constructed to accommodate both permanent and temporary loads, referred to as dead and live loads respectively, is also a challenge. These loads are critical to the performance and structural integrity of the floor system. The proper design and execution of the blocking system must consider these loads. The impact of neglecting this step is a common oversight, increasing risks for homeowners in the long run. To ensure both short and long-term structural integrity, it's crucial that inspectors evaluate engineered floor system designs and, during construction, verify the correct application of these blocking systems and load transfer considerations. Failing to recognize these hidden aspects creates a situation where even small oversights can have costly consequences.
Engineered floor systems, often relying on I-joists or other engineered wood products, present unique challenges for load distribution and require careful consideration of blocking requirements. The goal is to optimize load transfer and structural performance, which can be easily compromised if not implemented correctly. It's intriguing how easily the crucial role of blocking can be overlooked. Blocking panels, commonly made from materials like TJI joints or Structural Composite Lumber (SCL), serve a vital function: transferring both vertical and horizontal forces within the engineered floor system. The lack of adequate blocking can lead to unsupported loads, which compromises the structural integrity of the entire floor.
It seems apparent that building codes establish minimum design loads for buildings, which often include specific guidelines for blocking requirements and material specifications. However, these requirements are often missed by inspectors due to the fact that blocking is usually concealed within the structure. This oversight could lead to unforeseen issues down the road.
Interestingly, the interplay between dead loads (permanent fixtures and finishes) and live loads (occupancy, furniture) must be considered when designing the floor system. The structural requirements of the system, alongside considerations of finish floor compatibility, are crucial to preventing future issues.
It's important to understand how load distribution is essential to the overall performance of the floor. Poor blocking or inappropriate material selection can lead to problems with excessive deflection and deformation of the lumber beams and headers, potentially indicating a larger structural concern. Blocking not only handles load distribution but also plays a role in how the structure transmits loads from stacked bearing walls above to the supports below. It's as if the blocking is creating a continuous path for force to travel through the structure.
It's evident that even in a new home, there's still the potential for deficiencies in structural components, and often these are overlooked. This is why a thorough understanding of how engineered floor systems are designed and constructed is essential for both building professionals and home inspectors. It seems that without a clear understanding of how loads are distributed through blocking and how it interacts with the overall structural system, the long-term stability and safety of these systems could be put at risk. The failure to consider the interaction of the different components within the floor system, such as the joists and bearers, with the wider structure can have substantial consequences.
This is solely for educational and informational purposes and should not be taken as professional engineering advice. The insights provided are for general knowledge and understanding. Consulting with a qualified structural engineer is always advisable for any structural matters.
More Posts from aistructuralreview.com: