Pavement Longevity Slurry Seal Versus Seal Coat Differences
Pavement Longevity Slurry Seal Versus Seal Coat Differences - Composition matters beyond the surface color
When considering how best to preserve pavement surfaces, what they are actually made of is far more important than just the superficial color they provide. While simple seal coats are largely aimed at cosmetic improvement and offering basic protection to pavements already in good condition, slurry seals are formulated with aggregate mixed in. This isn't merely an ingredient difference; it fundamentally changes the treatment's function. That aggregate helps fill minor surface cracks and voids, contributing to a more even and potentially more structurally sound layer on top of the existing pavement. This functional capability, derived directly from its composition, allows a properly designed and applied slurry seal to potentially add significant years to the pavement's useful life, offering more than just a visual seal. How these treatments perform and contribute to longevity is intrinsically linked to their specific material makeup, making a clear understanding of these compositional differences essential for informed maintenance choices.
Looking past the visual application of a pavement surface treatment, several less obvious factors rooted in its fundamental composition wield significant influence over its long-term performance. Here are some intrinsic properties that, while unseen from the curb, critically shape pavement longevity:
The geometry of the aggregate particles – specifically how angular or rounded they are – is not merely a matter of visual texture. Internally, angular particles create a more rigid, interlocking skeletal framework. This hidden internal architecture provides much of the layer's resistance to shifting under traffic loads and fighting permanent deformation, a function distinct from what appears on the surface.
Trace elements or modifiers incorporated into the binder, often accounting for a very small fraction of the total mix, can drastically alter its inherent characteristics. For instance, select polymer additives can enhance the binder's elastic recovery and its affinity for aggregates, improving resilience against temperature-induced cracking and preventing particles from loosening. These functional improvements occur without necessarily changing the layer's initial appearance.
The volumetric balance between the asphalt binder and the carefully proportioned aggregates is a critical internal design parameter. This ratio determines the effective film thickness coating each aggregate particle. An incorrect ratio, difficult to discern visually once placed and compacted, is an intrinsic flaw that can predispose the pavement to issues like premature aggregate loss (raveling) if the film is too thin, or flushing/bleeding of excess binder to the surface if it's too thick.
For treatments delivered as emulsions, the precise chemical formulation dictates the complex "breaking" process – the point at which water separates from the asphalt particles, allowing the binder to cure and develop its adhesive and cohesive strength. This invisible internal chemical reaction, rather than just the rate of water evaporation, fundamentally controls how well the new layer bonds to the existing surface and the ultimate development of the binder's performance properties.
The way different aggregate particle sizes are combined, referred to as grading, defines the interconnected network of empty spaces – the internal void structure – within the finished layer. This hidden porosity, independent of the surface texture you feel, governs how readily water can permeate the treatment and whether it provides adequate resistance to damage from moisture infiltration and freeze-thaw cycling, factors crucial for durability, especially in climates subject to significant temperature variations.
Pavement Longevity Slurry Seal Versus Seal Coat Differences - Predicting service life A look at typical results
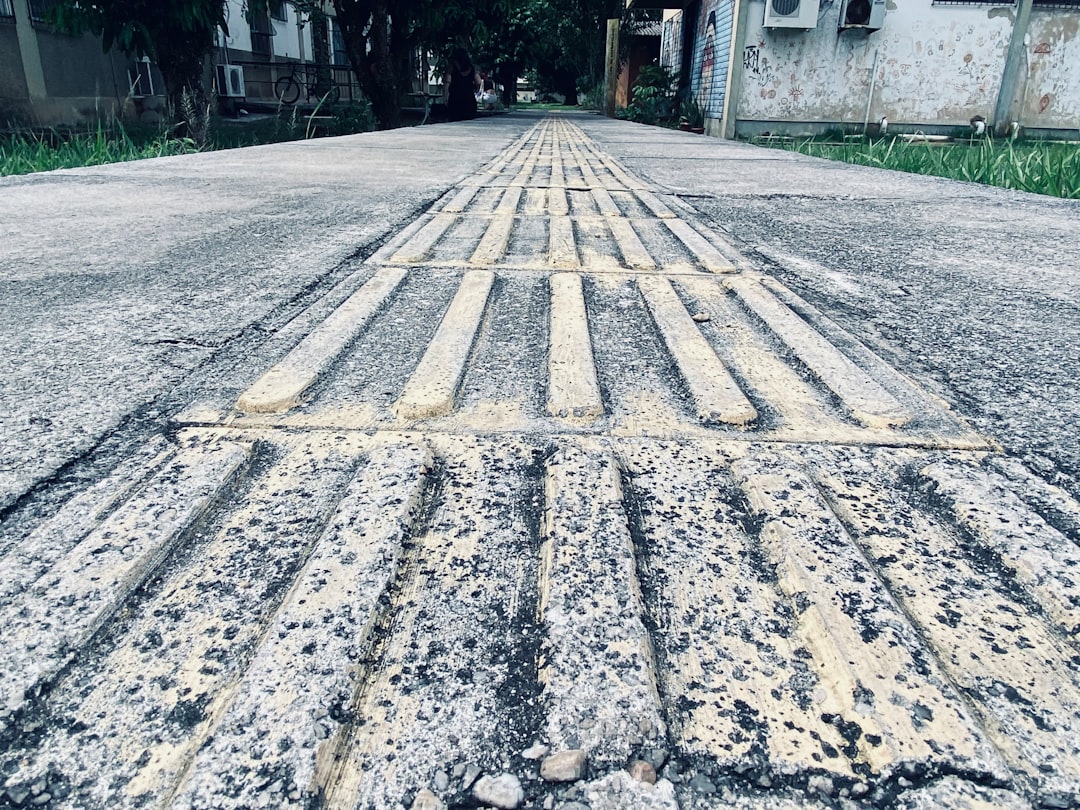
Predicting precisely how long a pavement treatment will extend its useful life is rarely an exact science. While figures are often cited as typical results, these are estimates highly dependent on numerous factors. The inherent properties of the treatment material itself, the condition of the pavement surface when it's applied, the intensity of traffic it subsequently endures, and the specific environmental conditions – from temperature extremes to moisture exposure – all significantly influence the actual outcome. For instance, treatments like slurry seals, designed with aggregates to mend surface issues and contribute more structure, are commonly associated with expected service lives ranging from several years, often cited around five to seven under favorable conditions, although results can vary widely. In contrast, treatments primarily intended for superficial sealing and initial protection tend to offer less significant, if any, long-term structural benefit or comparable life extension, serving a different, more immediate purpose. Consequently, relying solely on a single "typical" number for service life overlooks the complex interplay that ultimately determines real-world performance.
Attempting to forecast the lifespan of pavement surfaces treated with applications like slurry seals or seal coats proves a challenging exercise, extending beyond the basic understanding of their constituent materials or typical wear patterns. One significant hurdle lies beneath the new layer – the actual condition and structural integrity of the existing pavement itself. This base is frequently heterogeneous, with accumulated damage and fatigue not always apparent or fully characterized, yet it dictates how well the new surface can perform and how quickly underlying distresses will reflect through. Furthermore, the interaction with traffic is far from uniform. Standard predictions often rely on average traffic volumes, but the destructive potential scales dramatically with axle load; a small increase in weight can cause disproportionately large amounts of damage. Accurately predicting when and where this critical loading occurs is inherently difficult. Even seemingly minor inconsistencies during the construction process – perhaps subtle differences in application thickness, temperature during placement, or compaction effort – can introduce points of localized vulnerability. These subtle variations, practically invisible once the work is complete, can become initiation sites for premature failure, accelerating wear in specific areas differently than predicted for the overall surface. Additionally, environmental factors initiate degradation in complex ways. Ultraviolet radiation from the sun, for example, primarily affects only the very top micro-layers of the asphalt binder, causing photo-oxidation and embrittlement. While shallow, this surface alteration creates conditions ripe for the formation of early microcracks, which then propagate deeper over time under traffic and thermal cycles, becoming the source of more significant problems not simply due to bulk material fatigue, but due to this surface-initiated process. Consequently, stated service lives, whether five or seven years for a slurry seal, are often broad statistical averages masking significant variability driven by these difficult-to-predict underlying conditions, load spectrum realities, construction nuances, and nuanced environmental interactions.
Pavement Longevity Slurry Seal Versus Seal Coat Differences - Cost implications Examining the investment per year of life
When evaluating maintenance strategies for pavement surfaces, understanding the true financial impact extends beyond the immediate expense. A more useful perspective examines the actual investment required for each year of functional life a treatment provides. Applications like slurry seals, often representing a higher initial expenditure than simple seal coats, are designed to offer more substantive surface restoration and potentially a longer service duration. This capability *can* mean that, despite the higher upfront cost, spreading that cost over the extended years of enhanced pavement performance might result in a lower average annual outlay over time. In contrast, basic seal coats, while cheaper to apply initially and serving a valuable purpose for minor protection, typically have a shorter functional life relative to their cost. Their primary benefit is more immediate, and relying on them alone might necessitate more frequent treatments or lead to earlier deterioration requiring more significant, and thus more costly, repairs down the line. Consequently, truly assessing which option offers better value necessitates a comprehensive view of costs projected across the pavement's entire service period, rather than focusing narrowly on the price of the surface treatment application itself. This approach highlights the importance of long-term economic efficiency in pavement management decisions.
Shifting our focus from the materials science and performance prediction nuances, the practical implication for those managing road networks inevitably circles back to cost – specifically, the return on investment over time. Examining the financial outlay in terms of the cost per year of service gained provides a clearer picture than just comparing upfront costs. It's somewhat counterintuitive, but minor deviations in the actual achieved service life compared to our initial estimates – even just missing or gaining a year or two – can lead to a surprisingly disproportionate shift in that calculated annual cost effectiveness. This inherent sensitivity underscores just how crucial our predictive capabilities truly are for sound economic evaluation, and perhaps how fragile our financial forecasts can be if based on overly optimistic or generalized life expectancies.
When delving into the economics of pavement preservation, standard cost-benefit analyses often primarily capture the direct expenses borne by the managing agency: the cost of materials, labor, and equipment. However, a more comprehensive view reveals that the indirect costs imposed upon the road users and the broader public – things like increased fuel consumption from stop-and-go traffic caused by deteriorating surfaces, the wear and tear on vehicles, and the economic drag from prolonged travel times due to maintenance work or poor road conditions – can, over the entire life cycle, rival or even significantly exceed the agency's direct expenditures. Ignoring these user costs provides an incomplete, perhaps even misleading, assessment of the total societal investment required per year of functional road life.
A particularly compelling observation arises when comparing the economics of applying preventive treatments to pavements still in relatively good shape versus waiting until significant distress manifests. Undertaking a timely intervention, like a slurry seal on a surface with minor issues, often translates to an exceptionally low cost per year of the added service life gained. The investment is small, the life extension potentially substantial, leading to high economic efficiency. Conversely, delaying action until reconstruction or extensive rehabilitation becomes necessary results in a dramatically higher cost per year of service. The initial cost is massive, and while it provides a longer life extension than a simple preventive treatment, the annual efficiency is significantly diminished because we're rebuilding failure, not preserving existing value. This pattern strongly argues against deferred maintenance from a purely economic standpoint; the penalty for waiting is steep.
Furthermore, the economic models used to assess these strategies, often formalized within Life Cycle Cost Analysis (LCCA) frameworks, are subtly but profoundly influenced by the financial parameters selected. For example, the discount rate used to adjust future costs and benefits back to their present value plays a critical role. A higher discount rate inherently devalues benefits received or costs incurred far into the future relative to those closer in time. This mathematical adjustment can, depending on the chosen rate, make long-term pavement strategies with benefits accruing over many years appear less financially attractive compared to solutions offering shorter-term fixes, even if those short-term fixes yield fewer total years of service over the analysis period. It's a technical detail, perhaps, but one that warrants careful consideration and transparent reporting, as it can tilt the scales in favor of certain types of investments.
Finally, the simple fact is that applying the same treatment – say, a specified slurry seal – to a pavement classified in 'good' condition versus one in 'fair' condition does not yield the same economic return. While the per-square-yard application cost might be similar, the years of additional service gained are typically fewer and potentially more uncertain on the already more distressed surface. This means the calculated cost per year of gained life is notably higher for the treatment applied to the 'fair' condition pavement. This highlights that the condition-specific effectiveness, tied back to those earlier points about underlying pavement health, directly impacts the investment's annual efficiency, reinforcing that condition assessment is as critical for economic analysis as it is for predicting physical performance.
Pavement Longevity Slurry Seal Versus Seal Coat Differences - Matching the method to the traffic demands
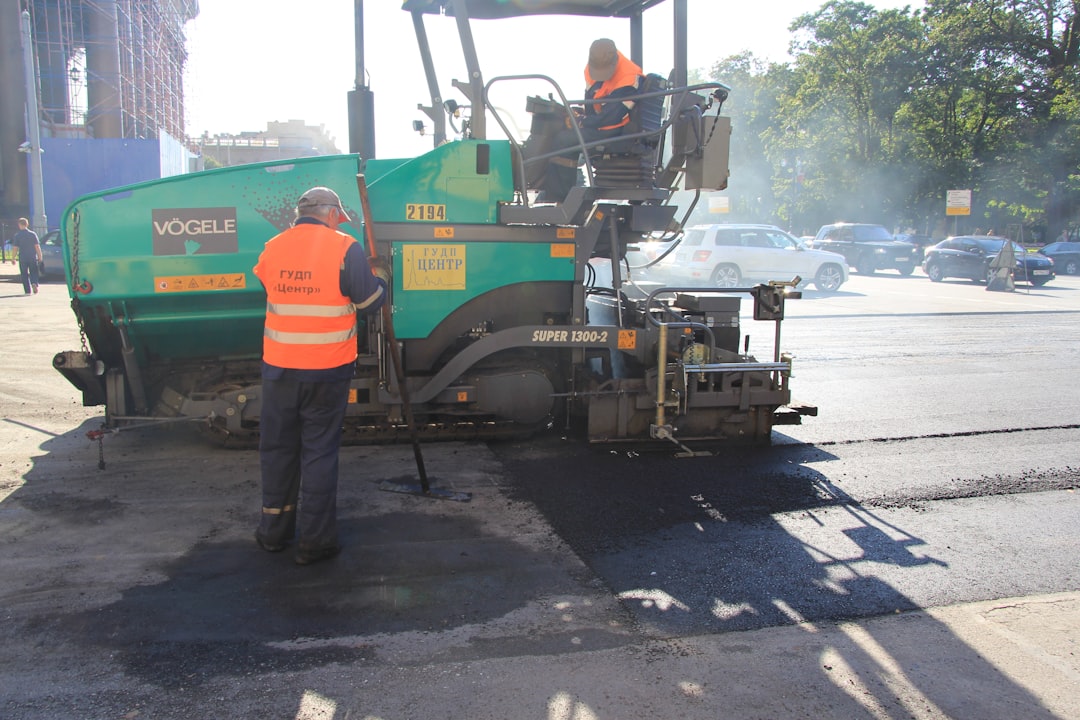
Selecting the appropriate pavement surface treatment fundamentally hinges on the expected intensity and nature of the traffic it will bear. It's not a one-size-fits-all decision. For pavements carrying lighter volumes of vehicles or primarily experiencing only surface-level wear, simpler seal coat applications can provide adequate initial protection and surface sealing. Their utility is generally limited in their capacity to withstand significant structural loading or abrasion beyond minor surface distress.
Conversely, pavements subjected to higher traffic volumes, including primary routes or areas like airport aprons which endure both numerous passes and heavy loads, demand a more robust solution. Here, treatments incorporating aggregate, such as slurry seals or even specialized variations like micro surfacing, become necessary. These methods are designed with greater material substance and structural integrity relative to basic seal coats, intended to resist the higher sheer stresses, rutting forces, and overall physical abrasion imposed by heavy traffic over time. A mismatch – applying a less durable treatment to a high-traffic area – will likely lead to premature failure, offering minimal long-term benefit. Therefore, the volume and type of traffic aren't just variables; they are primary drivers determining the minimum performance characteristics required of the maintenance intervention. Consideration of traffic needs alongside the pavement's current state guides the selection toward methods capable of surviving the specific demands of the environment they are meant to protect.
Considering how various surface treatments stand up to the relentless impact of vehicles reveals a crucial point: the traffic demands imposed upon a pavement surface fundamentally dictate the suitability of the chosen treatment. Simple seal applications, while offering a thin protective barrier, inherently lack the resilience necessary to cope with significant or repetitive loading. When subjected to the shearing forces generated by turning or braking traffic, particularly at intersections, these thin films struggle to maintain integrity, prone to displacement or rapid wear. Treatments incorporating a structured aggregate matrix, in contrast, are significantly better equipped to resist these destructive shear stresses. Furthermore, the persistent concern of binder tracking or flushing under sustained traffic, especially during warmer temperatures, is markedly reduced when the vehicle tire interacts with a stable, aggregate-rich surface rather than primarily a binder film. For roads experiencing moderate to heavy traffic volumes, materials without this internal structure simply aren't viable long-term solutions; they lack the intrinsic capability to distribute loads and resist the abrasive and deforming effects of continuous wheel paths that an integrated aggregate skeleton provides. This isn't merely about application; it's about whether the underlying physical structure of the applied layer can withstand the real-world forces it will face daily. The differing abilities of these treatments to handle traffic load also has practical implications for road management; treatments that allow a quicker return to service without risks like aggregate 'whip-off' offer operational advantages on busy networks, a property often linked to how effectively aggregate is bound within the matrix from the outset. Ultimately, maintaining functional skid resistance over time, critical for safety, is influenced by how the surface texture evolves under wear; treatments where aggregate is integral and resists embedment or rapid loss tend to provide more consistent frictional properties than those relying on a less robust surface. The question isn't just what the treatment looks like, but whether its fundamental makeup is engineered to bear the specific burden of the traffic it's expected to carry.
Pavement Longevity Slurry Seal Versus Seal Coat Differences - Getting it down and drying Differences in process
Getting the material onto the road surface involves distinct handling and setting processes for slurry seals and seal coats. For what is termed a slurry seal application, the process is often described as involving the initial placement of a mixed material containing aggregate, followed by the application of a sealant layer. This sequence means there isn't just one material curing; you have multiple components or layers that must transition from a wet, workable state to a solid, cohesive layer. The complexity of this phase change means the drying process is highly susceptible to ambient conditions – factors like air temperature, humidity levels, and whether the area is shaded or exposed to direct sun can significantly alter how quickly each part cures and bonds. Uneven conditions across a job site can easily lead to variability in the finished product's initial set and overall integrity during this critical early period.
In contrast, a typical seal coat application is a more straightforward affair, generally involving the application of a single layer of material. This simpler, single-stage process means the material undergoes a more unified drying and curing sequence, primarily driven by water evaporation from the emulsion and subsequent binder curing. While still sensitive to environmental conditions, the absence of multiple layers or aggregate particles that must individually be coated and locked into place during the setting process generally allows for a quicker, less complicated transition to a traffic-ready state. However, this inherent simplicity in application and curing also reflects a difference in the material's fundamental nature and what it's intended to achieve once placed, focused more on sealing than on building a complex matrix that cures and hardens in layers. Understanding these process-level distinctions in application and initial setting is fundamental to appreciating how these treatments begin their service life on the pavement surface.
The methods by which these surface treatments are placed and allowed to stabilize reveal distinct technical challenges and sensitivities.
For emulsion-based systems, like slurry seals, seemingly minor adjustments to chemical composition dictate the precise timing of the 'break' – the crucial moment when the asphalt particles coalesce. This isn't just passive drying; it's a controlled chemical process. Manipulating this breaking time allows for finer control over workability and, crucially, how quickly the treated surface can accept traffic without tracking, a significant operational factor on busy networks. Yet, getting this chemical balance wrong or encountering unexpected site conditions can delay the break or result in an inconsistent application.
In surface treatments where aggregate is applied separately, like conventional seal coats (often termed chip seals elsewhere), achieving adequate bond and embedment of the aggregate into the binder film isn't instantaneous upon application. It critically depends on the subsequent compaction effort by rolling and, perhaps more surprisingly, the sustained kneading action of early traffic. This reliance introduces a variability that can affect aggregate retention – a primary failure mode – and means the layer is in a somewhat vulnerable state until sufficient embedment occurs, a stark contrast to systems where aggregate is pre-mixed and bonded upon initial placement.
Environmental factors during the crucial setting and curing phase present significant hurdles. High ambient humidity, for instance, can dramatically impede the evaporation of water from emulsion-based treatments, even after the chemical break has occurred. This prolongs the period before full film development and strength gain, extending closure times and leaving the fresh treatment susceptible to damage from unexpected moisture or early loads, highlighting how sensitive these processes are to local atmospheric conditions beyond simple temperature.
Successfully applying these treatments is highly contingent on staying within specified temperature ranges during construction. Deviating from these narrow windows can compromise fundamental material transformations. Too cold, and the emulsion may not break correctly or the binder viscosity remains too high for proper film formation and aggregate wetting. Too hot, particularly with conventional hot binders in chip seals, and the binder can drain off the pavement surface before aggregate application, leading to inconsistent coverage and poor chip retention – issues that directly impact initial quality and subsequent durability.
Finally, distinguishing between initial 'set' – when the surface is dry enough to touch or cautiously walk on – and full 'cure' is critical but often blurred in practice. The full development of the binder's adhesive and cohesive properties, essential for load resistance and durability, is a much longer process extending days or even weeks after initial placement. Opening to traffic prematurely, even if the surface appears ready, can disrupt the final molecular alignment and bonding within the binder film, potentially compromising the layer's ultimate performance and lifespan compared to what the material is engineered to achieve.
More Posts from aistructuralreview.com: