The Impact of Self Drilling Wood Screws on Structural Integrity
The Impact of Self Drilling Wood Screws on Structural Integrity - Examining the Fastening Process and Material Interaction
Analyzing the installation mechanics and the complex relationship between the fastener and the joined materials is fundamental to understanding how self-drilling wood screws perform structurally. The method of installation itself is a key variable; factors like the rotational speed applied during driving can significantly impact how the screw cuts and forms its thread in the material. Furthermore, achieving sufficient screw embedment and ensuring the tip penetrates completely, especially when fastening to underlying steel, is critical for proper load transfer. The screw’s own material characteristics, including the specific metal alloys used and how they are processed to achieve different properties like hardness at the tip and toughness in the shank, are constantly interacting with the properties of the timber and any steel it passes through. This continuous interplay affects everything from thread engagement quality to withdrawal resistance and stiffness under load. Getting these interactions right is vital, as suboptimal processes or material mismatches can lead to connections that underperform structurally or fail prematurely.
The act of driving a self-drilling screw into wood represents a dynamic and somewhat aggressive material interaction, fundamentally differing from the controlled environment of a pre-drilled pilot hole. Instead of a clean bore, the integrated cutting point and subsequent thread advancement actively crush and displace wood fibers, particularly when the screw axis is oriented across the complex anisotropic structure of the timber. This action inherently induces localized micro-fracturing and plastic deformation radially outward from the screw's central path, creating a zone of disrupted material around the fastener.
A significant portion of the torque applied by the driving tool, which is often constrained by maximum speed limits depending on the screw type (as seen with specifications around 1800-2500 rpm for different fasteners when driving into steel, though the wood phase differs), doesn't purely contribute to the screw's axial movement. Much of this energy is dissipated through the mechanical work involved in shearing, crushing, and displacing those wood fibers, as well as generating heat through friction at the screw-wood interface. Understanding this energy distribution is crucial for evaluating installation efficiency and potential wood damage.
Furthermore, the effectiveness of the cutting point and the subsequent fiber displacement by the thread flanks are highly sensitive to the orientation relative to the wood grain. Driving parallel versus perpendicular to the grain presents vastly different resistances and failure mechanisms in the wood, leading to significant variations in insertion torque and, consequently, the pattern and magnitude of residual stresses locked into the material surrounding the screw. Studies on timber reinforcement, for instance, highlight how screw diameter and the angle of inclination relative to the grain profoundly influence internal stress distributions.
The inherent properties of the wood material itself, most notably its moisture content, play a substantial role during this interaction. Elevated moisture levels can effectively plasticize the wood's cell wall polymers. This reduces the energy required for fiber cutting and deformation during the self-drilling process. While potentially lowering insertion forces, this change in material response fundamentally alters the stress field developed around the advancing screw, which has implications for the immediate connection stiffness and the potential for long-term relaxation or creep effects.
The Impact of Self Drilling Wood Screws on Structural Integrity - Key Factors Governing Connection Reliability
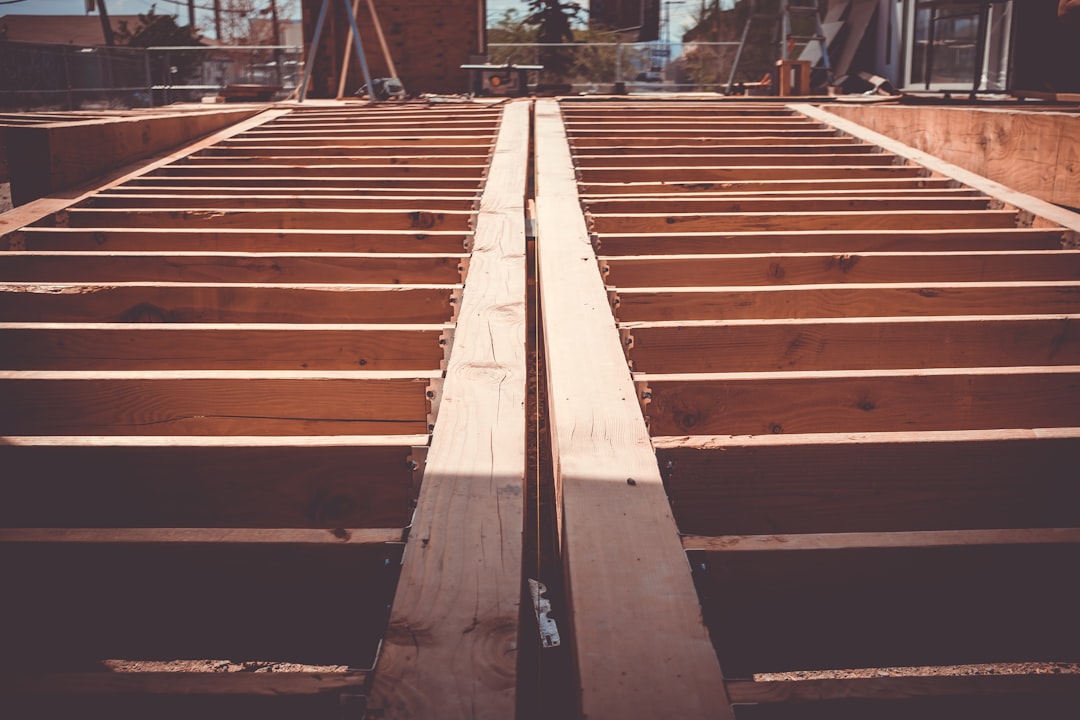
Reliable connections using self-drilling fasteners in wood structures critically depend on several factors, with performance issues often tracing back to neglecting fundamental principles. Getting the installation right is paramount; this involves more than just driving the screw, focusing on outcomes like preventing damage from over-driving and ensuring the fastener's integrated drill tip successfully clears the material path. Beyond the immediate act of installation, the screw's inherent characteristics and its suitability for the specific timber type are crucial. The orientation or angle at which the fastener is embedded within the wood also significantly influences its capacity to resist forces attempting to pull it free or slide the joint. In environments demanding high resilience, such as areas with seismic risk, the consistent reliability of these connections becomes absolutely essential for overall structural safety. Ultimately, achieving durable and dependable structural connections requires meticulous attention to these details throughout the construction process.
Beyond the immediate dynamics of driving the screw into the timber, the long-term reliability of the connection is governed by a complex interplay of factors acting upon the completed assembly. Achieving adequate embedment depth and ensuring the screw is seated correctly – neither proud nor excessively countersunk – appears crucial. Over-driving, for instance, can compress and damage wood fibers around the screw head, reducing the effective bearing area and potentially initiating localized crushing failure under load, rather than allowing the screw to bear efficiently against sound material. The lingering effects of installation choices, such as using high-impact tools which might induce residual stresses or subtle deformations like dimpling in joined metal components, also warrant closer examination regarding their impact on the connection's load distribution capacity over time.
The geometric configuration of the connection and the orientation of the screw relative to the wood grain significantly dictate performance under service loads. While drilling angle was mentioned regarding insertion efficiency, the angle of the seated screw relative to the timber face profoundly influences the composite withdrawal and embedment stiffness of the connection. Engineers often design with screws angled specifically to maximize resistance in critical loading directions, relying on predictive models that account for this grain-angle dependency. Similarly, connections involving gaps between layers, where the screw bridges an void, introduce significant bending forces onto the fastener under shear loads, a scenario where the screw's bending capacity and resistance to combined shear-bending stresses become paramount – a less ideal state compared to snug, fully-bearing connections.
The durability of the fastener material itself against environmental degradation is another critical, though often less visible, factor. While effective corrosion prevention is noted as a benefit in challenging environments, the reality is that electrochemical processes can still occur within the wood, potentially reducing the screw's cross-section or generating expansive corrosion products that stress and split the surrounding timber. This becomes particularly relevant with certain wood species or treatments, underscoring the importance of selecting compatible screw materials designed for the specific application environment.
Furthermore, connections are rarely subjected only to static, perfectly aligned loads. The viscoelastic nature of wood means that even constant loads can induce creep, a gradual deformation of fibers around the threads over time, potentially leading to a subtle reduction in clamping force or connection stiffness. Dynamic or cyclic loading, originating from wind, seismic activity, or operational vibrations, introduces fatigue considerations. The localized stress concentrations and micro-damage potentially induced during the self-drilling installation process itself, combined with the cyclic loading, can initiate and propagate cracks within the wood near the fastener, eventually leading to fatigue failure at loads well below the connection's ultimate static capacity. Finally, the fundamental anisotropy of wood remains a dominant factor in determining ultimate failure modes; even connections with high withdrawal resistance can be catastrophically limited by the wood's low tensile strength perpendicular to the grain, leading to splitting parallel to the grain when subjected to out-of-plane loads. Understanding and accounting for these multifaceted influences, from installation nuances to long-term material behavior and load case specifics, is vital for reliably predicting structural performance.
The Impact of Self Drilling Wood Screws on Structural Integrity - Considerations for Material Density and Thickness
Understanding the nature of the materials being fastened is fundamental, particularly concerning their density and thickness. The inherent density of the wood significantly governs its strength properties – its ability to resist withdrawal forces or deformation under shear loads. Different wood species exhibit wide ranges in density, meaning a screw suitable for a less dense timber might perform poorly or even cause damage in a denser one, and vice versa. Achieving predictable structural capacity hinges on selecting fasteners compatible with the specific material density.
Equally critical is the material thickness. The length of the self-drilling screw must be carefully chosen to ensure adequate penetration into the supporting member, allowing the threads to engage fully and transfer load effectively. Insufficient penetration due to excessive material thickness for the screw length can lead to premature pull-out failures or reduced shear capacity because the connection isn't fully bearing. Conversely, using a screw that is too long might complicate installation or isn't always necessary.
The interaction between the screw's design – its point type, thread pitch, and diameter – and the combined density and thickness of the materials stack determines how readily it installs and how much resistance it encounters. Variations in these material properties necessitate different screw characteristics to prevent issues like stripped threads, inadequate seating, or splitting, particularly when joining multiple layers or dissimilar densities. Effectively managing these material considerations is indispensable for designing robust and reliable connections.
The inherent properties of the wood itself, particularly its density and the thickness of the member being fastened, are non-trivial factors governing how a self-drilling screw performs. One might observe that a higher wood density can, up to a certain point, contribute positively by providing a firmer substrate for the screw thread to form within, potentially leading to enhanced withdrawal resistance. However, this advantage can quickly diminish or even reverse as densities climb higher, as the increased resistance to thread cutting concurrently elevates the risk of splitting the wood member during or after installation, potentially becoming the limiting factor well before theoretical withdrawal capacity is reached. Furthermore, the capability of a self-drilling tip isn't boundless; extremely high-density wood species can challenge or even exceed the screw's cutting ability, potentially necessitating pre-drilling despite the fastener's design intent, raising questions about the 'self-drilling' claim's universality. Beyond density, the actual thickness of the wood member critically influences its capacity to withstand localized bearing stresses and resist splitting around the screw shank when subjected to shear forces, as insufficient thickness simply limits the available cross-sectional volume to effectively distribute these perpendicular-to-grain stresses. Crucially, for connections involving a secondary structural element beneath the wood, the thickness of the wood dictates the remaining screw length available and necessitates adequate penetration *beyond* the primary wood layer to ensure sufficient thread engagement within the receiving material for proper load transfer. Adding another layer of complexity, the density within a single piece of lumber isn't uniform; variations between the less dense earlywood and the harder latewood create localized zones of differing stiffness and strength which non-uniformly influence the localized stress fields surrounding the screw threads, a subtlety that might impact long-term connection integrity.
The Impact of Self Drilling Wood Screws on Structural Integrity - Assessing the Assembly Performance Over Time
Assessing the functional behavior of a self-drilling screw connection extends far beyond the initial installation phase. The capacity and stiffness of these assemblies are not static and are subject to change over time. Evaluating performance requires acknowledging that the complex interplay between the fastener and the wood substrate evolves under service conditions and environmental influences. The enduring reliability hinges on understanding how inherent material properties and the accumulated effects of loading impact the connection's ability to maintain its strength and stiffness profile over years. Therefore, continuous consideration of these long-term dynamics is a fundamental aspect of predicting the lifespan and ensuring the sustained structural contribution of such connections.
Examining the connection's behavior beyond the initial installation phase introduces a different set of complexities, particularly concerning how performance might evolve over extended service periods. One must consider that the immediate stresses locked into the wood fibers by the aggressive threading action of the self-drilling screw are not static; the inherent viscoelastic characteristics of wood mean that these localized stresses are prone to gradual relaxation over time. This stress reduction potentially diminishes the initial intimate contact pressure between the screw threads and the surrounding wood material, subtly altering the connection's load transfer mechanism. Furthermore, the wood structure isn't isolated from its environment. Fluctuations in moisture content, a common occurrence in many structural applications, cause the wood to swell and shrink. This cyclical movement directly translates into repetitive stressing of the wood fibers immediately encasing the screw threads, contributing to localized micro-damage and potentially a slow, cumulative reduction in the overall stiffness of the connection over months and years. Beyond environmental factors, the cumulative effects of the service loads themselves warrant scrutiny. Even loads well below the connection's demonstrated static capacity, if applied repeatedly over millions of cycles (e.g., from wind or foot traffic), can induce fatigue damage in the wood directly surrounding the fastener. This progressive degradation, particularly in the zones of high-stress concentration near the threads, raises concerns about potential failure developing unexpectedly long after the structure has been in service, without an obvious overload event. Chemical interactions also play a role over the long haul. Electrochemical reactions between the screw material and certain wood extractives or introduced moisture can lead to gradual corrosion. A critical aspect of this is the formation and potential expansion of corrosion products within the tight confines around the screw. This expansion exerts internal pressure, physically stressing the adjacent wood and potentially initiating longitudinal splits that can significantly compromise the connection's capacity. Finally, it is worth reflecting on whether the intense localized thermal and mechanical energy input during the self-drilling process itself leaves an indelible mark on the wood's microstructure right around the screw. This altered state might mean the wood in this crucial zone responds differently to long-term loading, potentially affecting its creep behavior or its continued resistance to screw embedment pressure over years of sustained load.
More Posts from aistructuralreview.com: