Understanding Steel Concrete Friction for Enhanced Design Safety
Understanding Steel Concrete Friction for Enhanced Design Safety - Understanding the Variable Nature of Steel Concrete Contact
Understanding how steel and concrete behave where they meet is fundamental for reliable structural performance. The way these materials interact at their interface, particularly concerning friction, is not a simple, fixed value but rather varies based on several factors. Conditions such as the presence of water or moisture at the joint, the specific texture or finish of the steel surface involved, and the level of pressure pressing the materials together all play a significant role in determining the frictional resistance. It is also recognized that as relative movement occurs, processes like abrasion or 'grinding' can alter the interface characteristics and thus the effective friction over time. Engineers are increasingly using advanced computational models that attempt to capture this dynamic and complex interaction, moving beyond simplified assumptions. This acknowledged variability means design considerations must be thorough, accounting for potentially wide ranges of friction depending on the specific environmental and load conditions, rather than relying on a single coefficient. Properly incorporating this nuanced understanding is critical for ensuring the safety and longevity of composite steel-concrete structures.
As of 07 Jun 2025, when considering the interface between steel and concrete, it quickly becomes apparent that describing its behaviour using a single friction coefficient feels... inadequate. The reality is far more intricate and variable than often captured in simplified models. Here are a few aspects that highlight this inherent complexity:
For one, the notion of a 'contact area' is quite misleading. On a microscopic scale, the surfaces of steel and concrete are far from smooth. Contact occurs only at the peaks of microscopic roughness, or asperities. The true, load-bearing contact area is orders of magnitude smaller than the visible surface area. This concentration of load onto tiny points means localized pressures can be immense. Crucially, this real contact area is dynamic; it constantly shifts, deforms, and changes configuration as loads are applied, making the interface resistance inherently non-uniform and time-dependent.
Furthermore, the presence of even trace amounts of moisture introduces considerable uncertainty. Water at the interface can initially act as a lubricant, potentially reducing resistance, but its long-term effects are complex. It can promote corrosion on the steel surface, changing its topography and thereby altering the frictional characteristics over time. Environmental humidity and exposure conditions are not merely external factors; they directly influence the physical and potentially chemical state of the interface.
The speed at which forces are applied also plays a significant role. The behaviour under rapid loading (dynamic) can differ substantially from that under slow or sustained loading (static). This isn't just about different coefficient values; it's about potentially different underlying resistance mechanisms engaging. Compounding this, time-dependent deformations in concrete, like creep, can cause stresses at the interface to redistribute over extended durations, further modifying the contact state and load transfer efficiency over the structure's lifespan.
Fundamentally, the variable nature is driven by the ongoing interaction of those microscopic high points – the asperities – on both materials. As relative movement occurs, these features deform plastically, interlock, or even fracture. This continuous micro-mechanical process reshapes the contact geometry and alters how load is transferred through direct bearing and shear resistance. It's a perpetual state of surface evolution, not a static interaction, which makes predicting its exact behaviour challenging.
Finally, over prolonged periods, there's the possibility of subtle chemical interactions or micro-adhesion developing between the materials. This isn't the intended bond from rebar deformations, but potentially weak, localized forces that develop spontaneously. If present, this adds a potentially time-dependent 'adhesive' component to the overall interface resistance, distinct from mechanical friction, contributing another layer of variability that standard friction models might not capture.
Understanding Steel Concrete Friction for Enhanced Design Safety - Code Provisions Meet Empirical Evidence
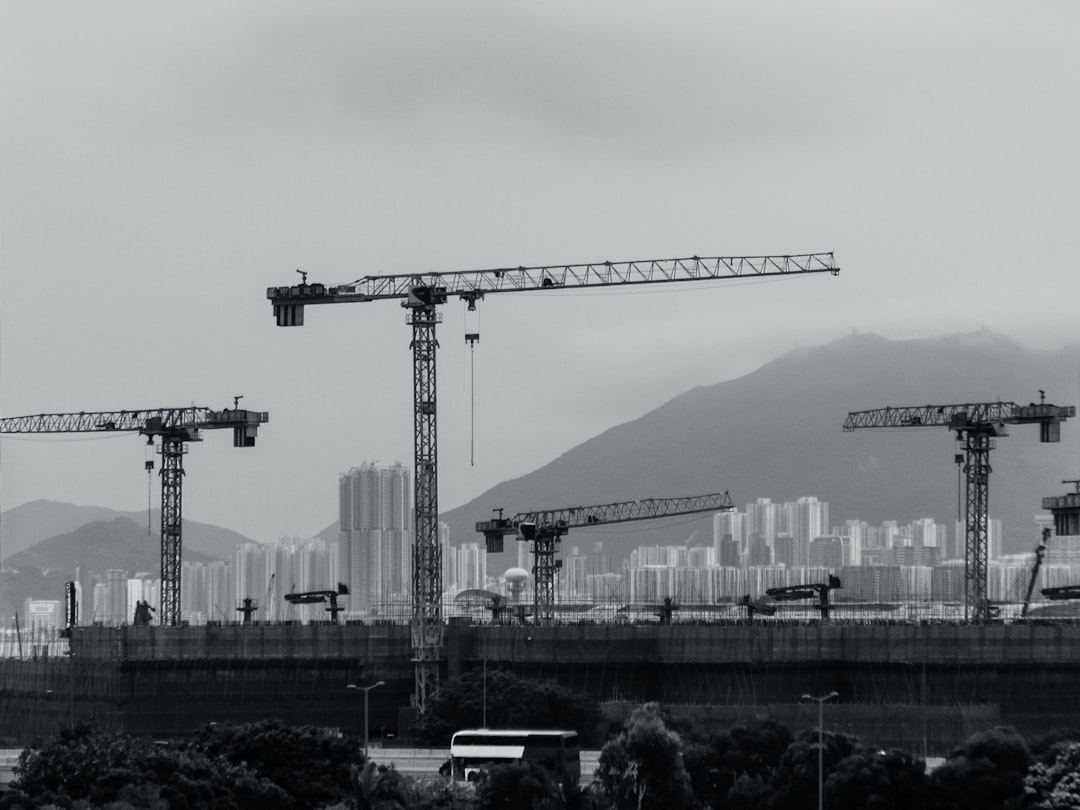
Studies delving into how steel and concrete transfer forces at their interface are continuously driving reassessments of current design regulations. There's a growing consensus that the rules structural engineers currently rely on sometimes need to catch up with the insights gleaned from experimental observations. Recent empirical findings, particularly around the mechanics of shear force transfer, highlight instances where present code provisions may not fully account for critical influences, such as how the size of a structural component affects its behavior. These disparities challenge the simplicity of some traditional design methods, suggesting a more detailed approach is needed to adequately address the complexities of how friction and shear resistance actually manifest, especially under varying real-world conditions. As extensive databases of physical tests are analyzed, the patterns observed often reveal behaviors not completely anticipated by existing code formulations. This ongoing process of evaluating codified practices against rigorous empirical evidence is fundamental to identifying where design standards require evolution to better reflect the actual performance of these composite structures.
As of 07 Jun 2025, when we look at how structural design codes handle the fascinating, albeit complex, phenomenon of steel-concrete interface friction in light of gathered empirical data, a few points stand out as quite interesting and, perhaps, a little surprising.
For one, despite a wealth of experimental research over the years demonstrating the highly dynamic and variable nature of how steel and concrete rub against each other, the foundation of most common design codes still tends to rely heavily on using singular, somewhat fixed friction coefficient values. These are often results from specific, controlled lab tests, which don't always capture the full range of real-world conditions.
It's also intriguing to see how the substantial global safety factors required by many structural design codes implicitly act as a significant cushion. They seem to help manage the acknowledged large uncertainties and the wide spread often observed in steel-concrete friction test results, rather than the codes themselves explicitly detailing or providing methodologies to account for the inherent *variability* of friction during the design process.
Empirical studies repeatedly show that the actual measured friction values at a steel-concrete interface can fluctuate wildly – by hundreds of percent depending on crucial factors like how the surfaces were prepared, whether moisture is present, or the exact pressure pushing them together. Yet, the values typically found in code tables or underlying standard calculations fall within a considerably narrower range, which while often conservative for safety, might not fully represent the spectrum of potential behavior observed in testing.
Another point to consider is that some of the core empirical foundations, or even specific friction coefficients commonly cited or embedded within current standard code provisions, trace their origins back to experimental programs conducted several decades ago. One has to ponder if these still accurately reflect the behavior we see with the modern variations in concrete mix designs, admixtures, or the different surface treatments and finishes common for steel elements today.
Finally, while empirical evidence, especially from long-term or dynamic testing, makes it clear that factors like the speed at which loads are applied (dynamic vs. static) and the time-dependent deformation (creep) in concrete can notably alter how the steel-concrete interface behaves over extended periods, the standard code provisions for calculating friction-based resistance generally do not explicitly incorporate these time-dependent effects into their standard calculation methods. It often feels like a simplification that doesn't quite align with the nuanced picture emerging from ongoing research.
Understanding Steel Concrete Friction for Enhanced Design Safety - Factors That Actually Govern Interface Performance
Pinpointing the true factors that govern the performance at the interface between steel and concrete is fundamental for ensuring structural safety. Moving beyond simple assumptions about friction, the reality is driven by a complex interplay of influences. While factors like surface texture or the presence of moisture certainly contribute, performance is also critically dependent on the specific mechanical properties of the materials themselves, particularly the distinct characteristics of the concrete matrix immediately adjoining the steel surface. The effectiveness of force transfer isn't solely frictional; it relies significantly on the interface bond strength, which experimental studies continue to refine, sometimes identifying parameters like fracture energy release rates as important indicators. Traditional design views, often grounded in simplified coefficients, can struggle to fully capture how these diverse factors interact, or how interface behavior might change based on nuances in material composition or the actual rate and duration of applied loads. Acknowledging these multifaceted influences – spanning from the micro-structural features to the overall loading conditions – is crucial for developing more accurate and dependable predictions of composite behavior.
When we dig into what truly dictates how steel and concrete behave at their boundary, moving force from one to the other, it gets quite nuanced. It’s not just about a simple rub; there are some perhaps less obvious aspects that critically govern performance.
It's worth noting that the actual shear resistance isn't primarily about bulk sliding. Instead, it's fundamentally determined by the persistent conflict and eventual distress – yielding or fracturing – of the tiny, interlocking peaks and valleys, the asperities, on both the concrete and steel surfaces under the applied pressure. This microscopic engagement is the core physical mechanism.
Once relative motion begins, the process of these surface textures grinding against each other generates fine debris. This isn't just dust; these particles form a dynamic 'third body' layer between the steel and concrete. The properties and behavior of *this* intervening layer, rather than the original surfaces, can rapidly become the dominant factor controlling the subsequent frictional resistance and overall interface performance.
Surprisingly, while fresh moisture might act as a short-term lubricant, prolonged exposure to damp conditions can, counter-intuitively, sometimes *increase* the interface friction over time. If moisture leads to corrosion on the steel surface, the resulting rust layer is often quite rough and abrasive, essentially changing the steel's effective texture and creating new points of mechanical interlock with the concrete, altering the governing mechanism.
Furthermore, the subtle, long-term deformation characteristic of concrete – creep – isn't just a material property; it's a governing factor for the interface. As concrete slowly deforms under sustained loads over months or years, it subtly redistributes the internal stresses, altering the effective normal pressure pressing the steel and concrete surfaces together, thereby changing the available frictional resistance over the structure's lifespan.
Finally, the speed at which loads are applied significantly changes the interface's behavior. Under very rapid, dynamic loading conditions (like those during seismic events), the failure mode at the interface can shift dramatically from the more ductile ploughing and deformation of surface asperities seen under slow loading to sudden, brittle fracture of these features. This fundamentally changes the energy absorption capacity and load transfer mechanism, governing performance in transient events differently than under static design loads.
Understanding Steel Concrete Friction for Enhanced Design Safety - How Friction Influences Structural Connections
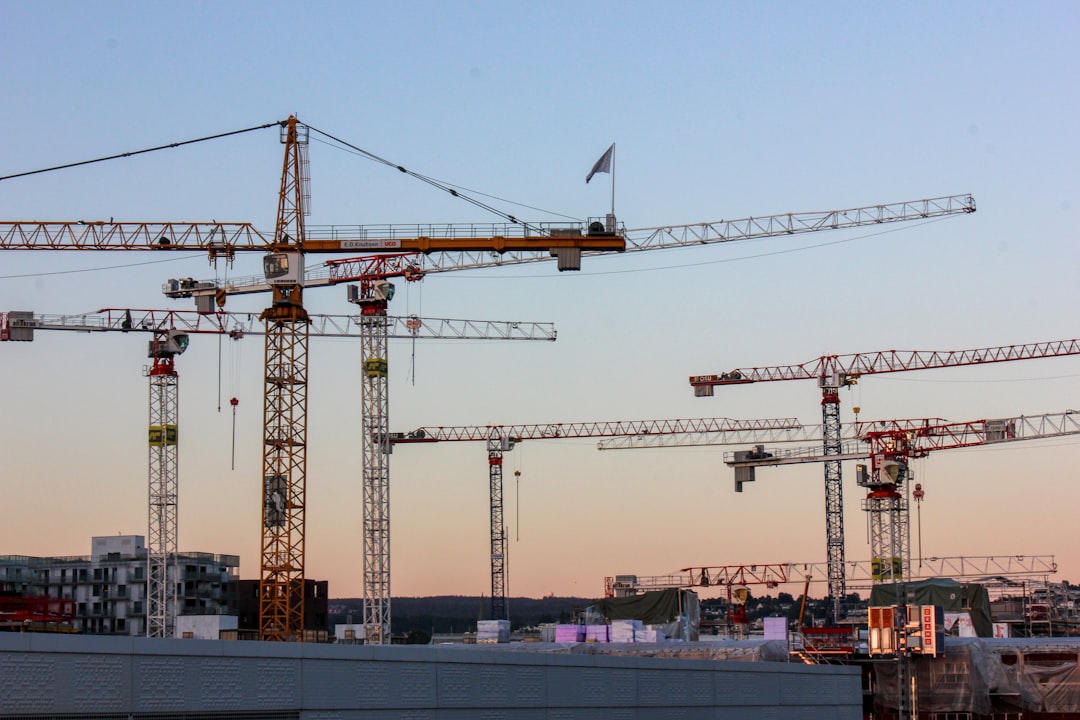
The transfer of load across the boundary between steel and concrete elements is fundamentally impacted by the level of friction present. This interface friction doesn't behave predictably; its resistance fluctuates based on conditions met during service. These fluctuations introduce considerable uncertainty into predictions of how composite connections will carry applied forces. The mechanical characteristics at this boundary can evolve not only instantaneously under load but also gradually over the structure's service life. This inherent variability means reliance on singular, constant friction values in design presents a simplification that doesn't fully capture real behavior. Consequently, accurately anticipating the actual load paths and failure modes within steel-concrete connections demands a deeper understanding that moves past generalized assumptions.
When examining the interface between steel and concrete and trying to understand its actual performance in a structural connection, some aspects emerge that might seem less obvious than just 'how slippery' the surfaces are.
It turns out that the very granular nature of the concrete mix itself, particularly the largest size and type of aggregate used, plays a surprisingly central role in how well the interface resists sliding forces. The aggregate particles exposed at the surface form the critical features – the 'teeth' – that interlock with the steel's roughness. The scale and inherent strength of these aggregate-defined protrusions dictate the fundamental capacity for mechanical interlock, directly influencing the achievable shear resistance, often more so than the bulk concrete strength might suggest in isolation.
Furthermore, the capacity of the interface to resist shear isniesn't solely about friction in the pure sense of sliding along a plane. As the rough surfaces try to ride over one another under shear load, they attempt to push apart, or 'dilate'. A significant portion of the shear resistance comes from the ability of the surrounding concrete or external restraints (like bolts, studs, or confining reinforcement) to effectively prevent this dilation. Without this crucial confinement maintaining pressure, the surfaces simply separate instead of generating the high contact forces needed for shear transfer through interlocking and friction.
There's also the intriguing observation of a 'scale effect'. When we run carefully controlled tests on small coupons or simple laboratory samples, we might measure an 'interface friction coefficient'. However, applying that same coefficient directly to predict the behavior of large-scale structural components like a massive beam or deep foundation element can be misleading. On larger scales, the dominant failure mode might shift; instead of failure occurring precisely *at* the steel-concrete boundary, it could happen as a shear failure within the concrete *immediately adjacent* to the interface. This material failure changes the effective resistance mechanism entirely, suggesting that interface performance isn't a simple linear scaling of small-sample results.
Another factor that often escapes simplified analysis is the long-term influence of temperature variations. Because steel and concrete have different coefficients of thermal expansion, environmental temperature cycling causes them to expand and contract at different rates. Over time, these differential movements can induce fluctuating normal stresses across the interface, potentially leading to a gradual reduction in sustained contact pressure or even causing cumulative micro-damage to the concrete's surface layer, subtly degrading the interface's load transfer capacity over the structure's lifespan.
Finally, a particularly critical, yet often overlooked, aspect is the nature of the Interfacial Transition Zone (ITZ). This is a thin layer of concrete, typically a few tens of micrometers thick, immediately adjacent to the steel surface, characterized by a higher water-cement ratio, more porosity, and weaker bonds than the bulk concrete further away. The structural integrity and shear strength of *this specific zone* are frequently the weakest link controlling the initiation of shear failure at the interface, rather than the strength of the main concrete body. Understanding and characterizing the ITZ is thus paramount for predicting true interface behavior.
Understanding Steel Concrete Friction for Enhanced Design Safety - The Ongoing Quest for Predictable Behavior
Structural engineers continue to heavily investigate how steel and concrete behave at their boundary in a constant effort to make structural performance more predictable. Despite numerous studies and improved computational tools over recent years, forecasting the exact force transfer at this critical interface remains challenging due to the inherently inconsistent nature of friction. This unpredictability stems from a confluence of influencing factors, from the microscopic surface conditions of both materials to the environmental interactions they experience, which often make reliance on static, simplified parameters inadequate for design. The complex interplay of forces, how they change with loading patterns, and the gradual alterations occurring at the interface over time further compound this difficulty. Addressing the variable character of this contact zone effectively is fundamental for confidently ensuring the safety and durability of structures incorporating these composite elements.
Achieving truly predictable behavior at the steel-concrete interface remains a significant research and engineering challenge, perhaps more so than initially anticipated decades ago. A few critical aspects highlight the difficulty inherent in this ongoing quest.
For one, developing computational models that accurately capture the interaction requires simultaneously tackling phenomena spanning vastly different physical scales. Trying to model the yielding and fracture of microscopic surface asperities and the properties of the nanoscale Interfacial Transition Zone while also simulating the force flow and deformation in a multi-meter structural element is a monumental task, involving immense computational power and theoretical hurdles in bridging these scales.
Furthermore, translating findings from controlled laboratory experiments to real-world performance is persistently challenging. Construction involves inherent variability in materials, workmanship, curing conditions, and site environments that are simply impossible to replicate perfectly in a lab setting. This disconnect means even the most meticulous research findings carry an inherent uncertainty when applied to actual structures, making guaranteed predictable performance difficult.
Surprisingly, using advanced measurement techniques like Digital Image Correlation reveals that interface slip isn't a uniform process. Instead, deformation is highly non-uniform, concentrating in localized zones. This level of micro-scale complexity means average measurements might mask critical local failure mechanisms, adding another layer of difficulty to developing accurate, predictive models based on bulk behavior.
The complexity escalates dramatically when considering the long-term behavior over a structure's lifespan. Predicting interface performance over decades requires understanding the coupled and interacting effects of time-dependent concrete creep, potential steel corrosion progression, and cyclical environmental changes (like temperature fluctuations). Simulating these slow, cumulative processes and their impact on the interface condition presents a formidable predictive challenge.
Finally, the 'quest' for predictability isn't solely analytical; it's moving towards proactive control. Acknowledging the inherent variability of naturally formed interfaces, researchers are increasingly exploring ways to engineer the boundary itself – perhaps through novel steel surface treatments or coatings – to create an interface with more stable, defined, and thus potentially more predictable mechanical properties, aiming to build predictability in from the start rather than just predicting the variability of a natural process.
More Posts from aistructuralreview.com: