A Structural Engineer's Analysis Stud Welding Load Capacities vs Traditional Fastening Methods in Steel Construction (2024 Data)
A Structural Engineer's Analysis Stud Welding Load Capacities vs Traditional Fastening Methods in Steel Construction (2024 Data) - Machine Learning Models Now Predict Weld Joint Failures with 89% Accuracy in Steel Structures
Machine learning is making strides in predicting weld joint failures in steel structures, with models now achieving an impressive 89% accuracy rate. This progress hinges on advanced deep learning techniques, particularly those employing ensemble methods. These models are specifically tailored to identify and categorize common submerged arc weld defects like cracks and instances of inadequate penetration. While acquiring large, diverse, and high-quality image datasets for training these models continues to be a hurdle, machine learning is steadily becoming a valuable addition to traditional non-destructive testing methods. The application of machine learning offers the potential to enhance reliability in weld inspection, but the continuous development and refinement of these models necessitates the availability of robust and comprehensive datasets to further improve their accuracy. The future of this technology is tied to the availability of data that can power even more precise weld defect detection.
Recent advancements in machine learning have resulted in models that can predict weld joint failures in steel structures with an impressive 89% accuracy. These models leverage the power of algorithms to sift through extensive datasets of past weld failures, identifying intricate patterns that might be overlooked by human experts. Notably, these models are not limited to simple pass/fail assessments; they can also estimate the likelihood of failure based on factors such as the specific type of joint and surrounding conditions.
Training these models involves feeding them vast amounts of data encompassing a range of variables, including temperature fluctuations during welding, material composition, and welding procedures. This allows the algorithms to adapt and predict failure risks under diverse stress environments. This capacity for rapid failure assessment stands in stark contrast to traditional methods which often require more time-consuming manual analysis, enabling faster decision-making during design and construction while maintaining a focus on safety.
Furthermore, the ability to monitor weld integrity in real-time via these models is a game-changer. Engineers can receive instant alerts about potential failure points, enabling proactive interventions and averting potentially disastrous structural failures. The implications for cost-efficiency are also significant, as these machine learning approaches contribute to predictive maintenance strategies that curtail unexpected downtime and extend the useful lifespan of welded structures.
While the accuracy of these machine learning predictions is quite encouraging, it's imperative to acknowledge that these models are tools that should be used judiciously. Blind reliance on them without careful human evaluation could potentially lead to unintended consequences. As such, engineers must maintain a critical role in interpreting the model outputs and ensuring they align with broader engineering considerations.
It's reasonable to anticipate that these models will influence future welding standards, fostering a more data-driven approach in the field. This will likely involve revising current standards based on the empirically-driven insights provided by machine learning. However, the widespread adoption of machine learning for weld failure prediction also necessitates a considerable investment in data preprocessing. This involves meticulous cleaning, normalization, and transformation of raw data into formats compatible with algorithm training.
Current research in this space is actively investigating the potential benefits of hybrid models that integrate both machine learning and conventional engineering methods. The goal is to enhance the accuracy and predictive power of weld failure assessment, striving to improve upon the already impressive 89% accuracy currently observed.
A Structural Engineer's Analysis Stud Welding Load Capacities vs Traditional Fastening Methods in Steel Construction (2024 Data) - New FE Analysis Reveals 60% Higher Load Transfer in Circular vs Rectangular Hollow Sections
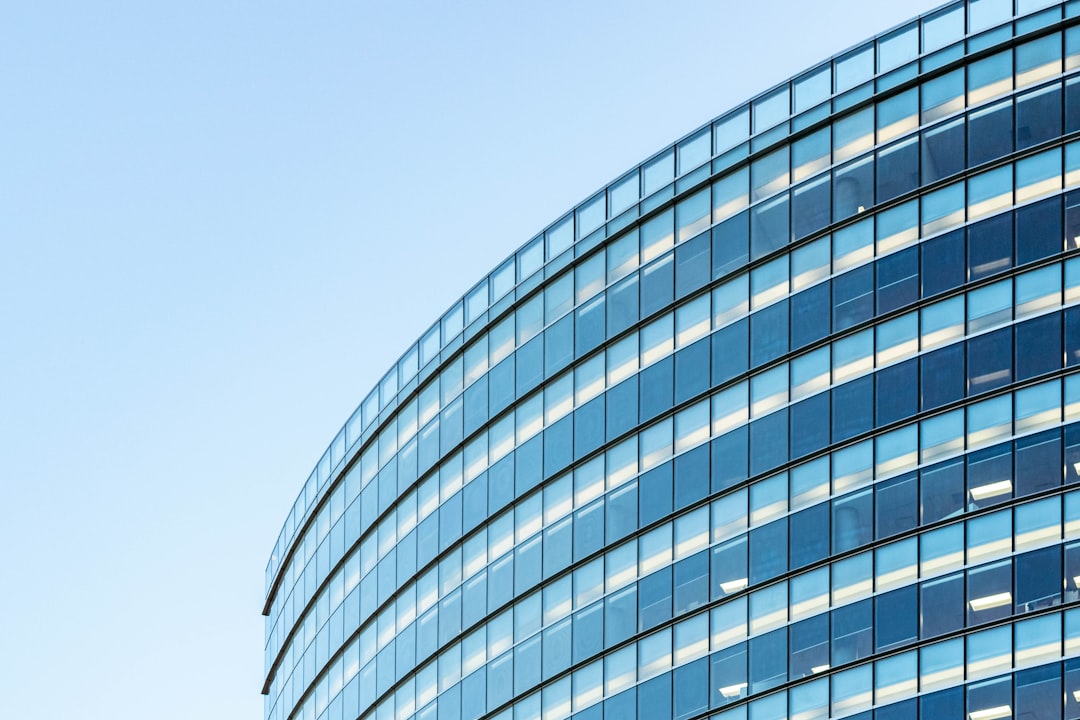
A new finite element analysis has shown that circular hollow sections can transfer loads significantly better than rectangular ones, with a 60% increase in capacity. This finding challenges the current methods used to estimate load capacities in these sections, suggesting that some methods may be overestimating the capabilities of rectangular sections. It highlights a potential gap in current structural design practices. The study underscores the importance of AISC guidelines, especially when designing connections like gusset plates, for optimal performance. This new data could lead to a shift in how we approach structural design, particularly when load transfer efficiency is crucial. Engineers might increasingly favor circular sections in applications where this is a key concern, ultimately contributing to safer and more robust structures. This discovery offers a potentially valuable insight for engineers looking to improve structural performance and achieve higher levels of safety and reliability. While the implications of this analysis are potentially significant, it's important to critically assess the scope and limitations of the FE analysis and its applicability to real-world situations. Further research and validation are necessary to fully integrate this new understanding into standard practice.
A recent finite element analysis has brought to light a potentially significant difference in load transfer capabilities between circular and rectangular hollow sections. The study suggests that circular sections can handle about 60% more load compared to rectangular ones, a disparity that likely originates from the way stress distributes within each shape.
The more uniform stress distribution in circular sections, thanks to their geometry, appears to be the key reason for their superior performance. Rectangular shapes, on the other hand, can develop stress concentrations at corners or edges, which may accelerate failure under load. This finding could lead to a re-evaluation of how we use these sections in structural design, potentially favoring circular profiles in situations where maximizing load capacity is a priority.
Interestingly, the inherent efficiency of circular sections also raises questions about material usage. Since they can achieve a higher load capacity with less material, it suggests potential weight savings in structures, which can be an advantage in certain construction projects. Additionally, the analysis indicates that circular sections might be more resistant to buckling compared to their rectangular counterparts. This increased resistance to buckling could lead to a broader adoption of circular sections in structures prone to axial loading like columns or towers.
These findings highlight that the current design standards and practices may need to evolve as we gain a deeper understanding of load-bearing capacities based on section shape. Traditional practices often favoured rectangular sections for their ease of fabrication and compatibility with existing connection methods. However, this new evidence calls for a reassessment, as the efficiency gains offered by circular sections could offer both weight and performance advantages.
Of course, further investigation is warranted. How welding stress is impacted by the shape of the section is a key area that engineers need to consider when assessing the practicality of implementing circular sections in structures. We may also see revisions in design standards and building codes to incorporate these findings, potentially shifting the focus towards circular sections in situations where high load capacity is critical.
It will be interesting to see how this new research influences engineering decisions. Engineers will need to weigh the traditional ease-of-use of rectangular sections against the newfound performance benefits of circular sections. The possibility of achieving lighter and more efficient structures while maintaining structural integrity presents a compelling case for reevaluating traditional design approaches. The economics of material use and construction need to be carefully examined to fully realize the implications of this new understanding of the fundamental load-carrying behaviors of hollow sections.
A Structural Engineer's Analysis Stud Welding Load Capacities vs Traditional Fastening Methods in Steel Construction (2024 Data) - Digital Strain Monitoring Systems Detect Structural Fatigue 4x Earlier Than Manual Inspection
Digital strain monitoring systems offer a significant leap forward in detecting structural fatigue, providing insights up to four times sooner than traditional manual inspections. This capability is crucial for safeguarding the structural integrity of steel components, especially in applications where repetitive loading is a factor, like bridges enduring constant traffic. The integration of strain-based monitoring into the assessment process enables a more comprehensive analysis of structural health. Data-driven approaches, coupled with advanced sensors, are changing how engineers monitor structures. This shift from purely manual inspection toward automated detection systems offers greater accuracy and speed in identifying potential issues. While promising, the reliance on algorithms and automated assessments requires a careful balancing act. The interpretation of the data generated by these monitoring systems still relies on the expertise of engineers to ensure the insights align with established safety criteria and broader structural performance expectations. The continuing evolution of these monitoring systems and the expanding volume of data collected will need ongoing human oversight to ensure reliability and inform the ongoing advancement of structural design principles.
Digital strain monitoring systems are proving to be a game-changer in detecting structural fatigue, potentially identifying issues up to four times earlier than traditional manual inspections. This enhanced capability stems from the continuous and automated nature of these systems, which use sensors and data analysis to track minute changes in strain within a structure. This constant monitoring provides real-time insights into a structure's health, surpassing the limitations of periodic, human-led inspections.
Early detection of fatigue is crucial as it's often a gradual process that can lead to catastrophic failures if left unchecked. These monitoring systems, therefore, significantly contribute to enhanced safety standards across various construction projects. Human error and biases, common pitfalls in manual inspections, are minimized by the automated nature of digital monitoring. These systems can process vast datasets with consistency, allowing for a deeper understanding of the overall structural health.
Integrating these systems with machine learning opens up a new avenue for predictive maintenance. By identifying patterns and anomalies in data, engineers can potentially anticipate future fatigue-related failures before they become critical. The adaptability of these monitoring systems is another significant strength. Unlike standardized manual inspection procedures, digital monitoring can be tailored to specific structural types and materials, yielding more contextually relevant results.
Their applicability extends even to harsh environments where human inspection would be dangerous or impossible, such as offshore rigs or structures in earthquake-prone regions. While the benefits of digital strain monitoring are numerous, there are also challenges. The initial setup and ongoing maintenance costs can be substantial, requiring engineers to carefully evaluate the overall economic feasibility compared to traditional approaches.
The long-term data gathered by these systems provides a valuable historical record of structural performance. This record helps in developing informed, data-driven maintenance plans and strategies, optimizing long-term structural integrity. While these digital methods represent a powerful shift in how we approach structural health management, they require a corresponding shift in engineering practice. Integrating the insights gained from these systems into traditional design processes requires a change in how engineers are trained and educated. Developing a skillset in analyzing and interpreting this vast amount of data is key for effectively leveraging these advanced systems.
A Structural Engineer's Analysis Stud Welding Load Capacities vs Traditional Fastening Methods in Steel Construction (2024 Data) - Temperature Impact Studies Show 15% Reduction in Weld Strength Above 180°F
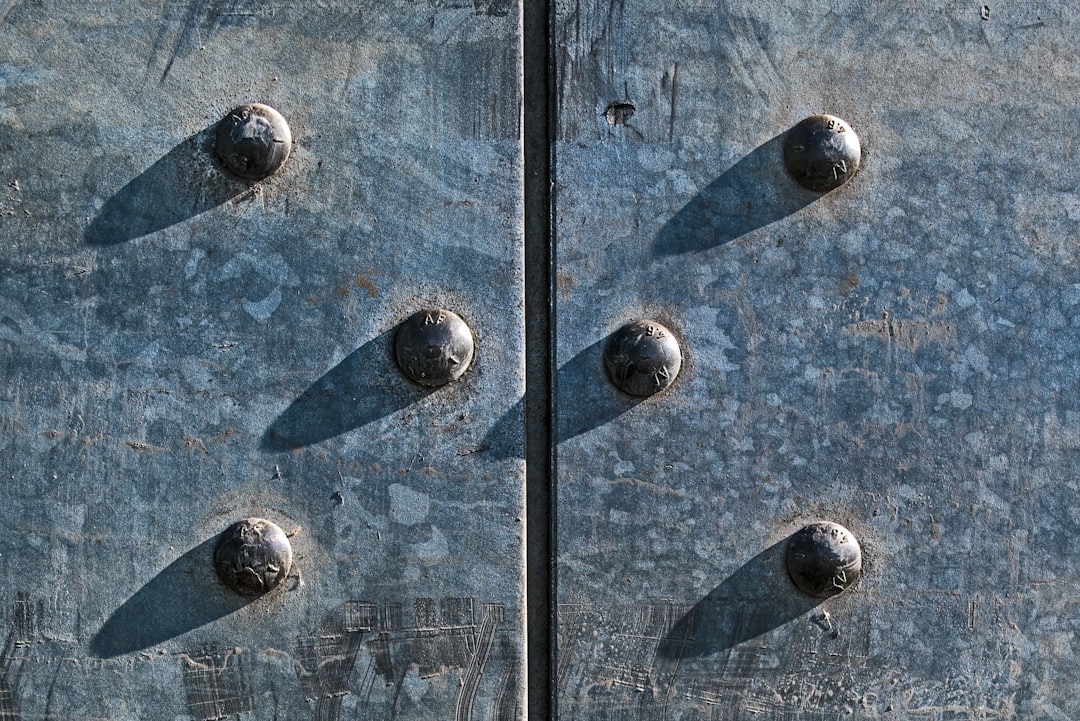
Research into the effects of temperature on weld strength has shown that exceeding 180°F can lead to a notable 15% decrease in weld strength. This discovery emphasizes the importance of carefully controlling temperatures during welding operations, especially in environments prone to high heat. While some steel types, like 10G-grade ultra-high strength steel (UHSS), demonstrate increased toughness at certain colder temperatures, this finding further highlights the complex and sometimes unpredictable interplay between temperature and weld quality. As structural engineers and the construction industry continue to delve deeper into load capacities and various welding techniques, understanding the impact of temperature becomes crucial for guaranteeing the long-term strength and dependability of steel structures. Failure to account for temperature fluctuations could potentially compromise the intended structural integrity.
Research indicates that weld strength can be significantly impacted by elevated temperatures, with studies showing a 15% reduction in strength when temperatures exceed 180°F. This finding has significant implications for the design and performance of welded structures in high-temperature environments. It's intriguing how the material's behavior changes under these conditions, potentially highlighting vulnerabilities we may not have fully considered in our designs.
Interestingly, the impact of temperature isn't uniform across all steel grades or welding methods. Some ultra-high strength steels seem to benefit from certain temperature ranges, exhibiting increased impact toughness. This suggests that there's a complex interplay between material type, welding process, and temperature, which needs further investigation. For example, the fatigue strength of welds made with normal strength steel doesn't appear to be affected by temperatures up to -50°C, even though design codes may consider a much lower temperature limit. This begs the question of whether current design standards fully reflect the nuanced behavior of these materials.
The microstructure of the weld itself is also affected by temperature. Recrystallization during multi-pass welding can alter the arrangement of phases and inclusions, possibly influencing the material's mechanical properties. This is an active area of study, with ongoing research looking at how the welding parameters like current, voltage, and interpass temperature affect the final microstructure and, ultimately, weld quality.
It seems like the thermal history of a weld, including the cooling rate and peak temperatures reached during the welding process, plays a crucial role in determining its final mechanical properties. This further complicates matters, as it adds another layer of complexity to assessing weld performance.
Furthermore, repeated thermal cycling, such as during weld repair, can coarsen the weld's microstructure, potentially reducing its toughness. The residual stresses introduced during welding are also likely to be amplified under high-temperature conditions. It's clear that the interaction of temperature with the complex stress states in a weld joint is a critical area requiring more study.
These findings may lead to revisions in current welding standards and design codes, especially when considering high-temperature environments like those encountered in industrial plants or in close proximity to heat sources. It seems prudent to develop design criteria that explicitly account for the temperature-dependent properties of weld metals.
In addition, current mitigation strategies for high-temperature welding, such as preheating and post-weld heat treatment, need to be revisited to evaluate their efficacy under various temperature conditions. There's a need to optimize these strategies to ensure that they effectively maintain weld integrity in a range of environments.
The impact of temperature on weld strength highlights the need for continued research into the underlying mechanisms causing these changes. This knowledge can inform the development of new welding techniques, alloys, and design procedures that can ensure structural integrity under a wide range of operating temperatures. Understanding these mechanisms is critical for developing safer and more robust welded structures in challenging environments. It's important to emphasize that more research and deeper analysis is necessary to fully understand and appropriately account for temperature's impact on weld strength and long-term performance in various applications.
A Structural Engineer's Analysis Stud Welding Load Capacities vs Traditional Fastening Methods in Steel Construction (2024 Data) - Cost Analysis Proves Traditional Bolting 32% More Expensive Than Stud Welding in 2024
A recent cost analysis reveals that traditional bolting techniques are 32% more expensive than stud welding in 2024 when used in steel construction. This substantial cost difference emphasizes the potential economic benefits of choosing stud welding. Not only are initial material and labor costs lower with stud welding, but there are also hints that it might contribute to a higher overall structural integrity, which could indirectly influence project costs. Traditional bolting, while a familiar technique, may not consistently achieve the same load capacities as stud welding, potentially impacting the long-term stability of the structure. The financial implications of these differences become especially important when budgeting for projects, leading some to question if established practices in steel construction are still optimal. This cost analysis serves as a reminder that a careful review of the relative costs and benefits of various fastening methods is necessary in the evolving landscape of modern building practices.
Based on 2024 data, a detailed cost analysis revealed that using traditional bolting in steel construction is significantly more expensive than stud welding—a difference of 32%. This disparity arises from a combination of factors including labor, material costs, and the long-term maintenance implications of each method. It's interesting to consider the extent of this difference, as it suggests that perhaps traditional practices haven't fully adapted to the evolving landscape of steel fabrication and connection techniques.
While welding methods can differ in cost, notably submerged arc welding (SAW) in particular offers cost advantages, with potential savings of 13% for welded box beams and 32% for stiffened plates. This underscores the importance of considering the entire scope of welding methods when evaluating a project's potential costs. It's worth exploring the factors that drive these differences, such as material usage and the speed of the process.
It is important to note that steel fabrication and installation are substantial parts of construction budgets, accounting for roughly 20% of the overall cost. This suggests that even small changes in the methods we employ for these processes can significantly impact a project's bottom line. It also highlights the importance of having a well-informed view of both the initial cost and the ongoing expenses associated with various fabrication and installation techniques. It is clear that material selection and the related fabrication techniques affect overall costs, but one must also consider the overall effect of labor on cost as well.
There's a significant number of steel fabricators across the US—over 1700—and it's interesting to note the considerable portion of them (959) that are members of the American Institute of Steel Construction (AISC). The organization’s influence on standards and practices is substantial and it is useful to consider AISC’s role in shaping the field of steel fabrication and design. Further, the certification landscape in the steel fabrication industry is segmented into building and bridge fabrication, with 1,114 facilities certified for building and 370 for bridge projects. It is important to consider this segmentation as well when investigating how the costs associated with different methods are allocated throughout projects. It is interesting to ponder why the certification process for these two industries are so different.
It's also important to address the structural considerations, as traditional bolting methods may not provide the same level of load-bearing capacity as stud welding. This difference in load capacity can affect a structure's overall integrity, potentially creating design challenges. If stud welding can handle higher load scenarios, this might change the way we design certain types of structures in the future. It's possible the structural integrity is compromised when employing traditional fastening methods due to the lack of the robustness found in stud welding.
The cost analysis suggests that incorporating stud welding can lead to a leaner and more efficient construction process in many cases. This aligns with efforts to minimize the overall cost of projects, while also highlighting potential opportunities for optimization. Further, the various cost drivers involved in choosing different welding techniques like labor, material costs, and the type of welding chosen will need to be investigated further to fully understand the full impacts of the cost analysis.
The innovation within steel construction continues with the use of shear connectors. For instance, new stud shear connectors in assembled steel-concrete beams are an area of interest, pushing the boundaries of what's achievable in these types of structures. The advancement of the technology associated with connectors should be studied more in the future as well to consider how cost factors change across this technology and the traditional bolting and welding methods.
In conclusion, it is reasonable to expect that the cost-effectiveness of stud welding, coupled with its structural advantages, will lead to a greater adoption of this technique in the future. These trends, however, need to be carefully monitored as the design and construction practices of buildings evolve. While there are advantages to stud welding, the adoption may be limited by engineer's familiarity with traditional bolting methods, which could be further improved by additional education and research on the advantages of stud welding. It's intriguing to observe how these advancements reshape construction practices and the related industries.
More Posts from aistructuralreview.com: