Optimizing Dowel Pin Interference Fits Precision Techniques for Enhanced Structural Integrity
Optimizing Dowel Pin Interference Fits Precision Techniques for Enhanced Structural Integrity - Understanding Interference Fit Mechanics for Dowel Pins
Understanding how interference fits work with dowel pins is fundamental to building robust mechanical systems. The basic idea is to install the pin into a slightly smaller hole, generating a tight, interference fit that resists movement. This secure connection is vital for maintaining structural integrity. The key is finding the right balance in the tolerance between the pin and hole, ideally around 0.002 inches for standard applications. Going beyond 0.005 inches can make installation considerably more difficult. Notably, the Poisson effect also influences how the interference fit functions, especially when the length-to-diameter ratio of the contact area is smaller. This means that the material properties heavily impact the maximum force during installation. Studies, including those using Finite Element Analysis, help us understand the stress and forces generated during installation, allowing engineers to design optimal interference fits that meet specific application requirements. It's through this combination of experimental and theoretical understanding that we can create effective and reliable assemblies.
In the realm of mechanical assembly, interference fits utilizing dowel pins stand out as a technique that generates strong joints. It's a fascinating phenomenon where the pin's diameter is slightly larger than the hole it's intended to fit into. Achieving this tight fit usually involves pushing the pin into an undersized hole, inducing stress within both components.
A standard dowel pin's optimal interference range, based on typical practice, seems to fall within around 0.002 inches. Pushing this range beyond 0.005 inches starts to create installation challenges. The notion of fits, as engineers know, boils down to the permissible variation between two parts, which in turn is driven by material attributes and how much overlap occurs between the pin and its hole. Military standards (like NASM16555) sometimes mandate specific pin diameters, often calling for a small reduction (0.0002 inches) under the nominal dimension.
Researchers often utilize tools like 3D linear Finite Element Analysis (FEA) to investigate interference fits, exploring the stresses created around a pin insertion point. The Poisson effect, which is the tendency of materials to expand in one direction when compressed in another, becomes really crucial in these studies, particularly when the contact length to diameter ratio is low. The level of force applied, along with material properties, will have a large impact on the outcome.
Manufacturers have diverse processes for creating these interference fits. The selection of manufacturing technique depends a lot on whether or not the joint is expected to be taken apart at some point. Dowel pins with interference fits are widely used across many engineering disciplines, which underscores the critical importance of specifying accurate tolerances to assure structural integrity.
To assess how much force it takes to install interference fit dowel pins, researchers often gather data on force and distance during the installation procedure, helping us understand how different materials will behave in real-world conditions. These are only a few of the considerations that are important when designing interference fit assemblies.
Optimizing Dowel Pin Interference Fits Precision Techniques for Enhanced Structural Integrity - Material Selection and Thermal Considerations in Pin Design
When designing dowel pins, the selection of materials and careful consideration of thermal effects are paramount for ensuring the integrity and reliability of the mechanical assembly. The chosen material, whether it's a traditional metal like steel or aluminum, or something more unconventional like plastic or wood, needs to not only meet the strength and stiffness demands of the application, but also its thermal properties. The potential for misalignment or even failure increases if discrepancies in thermal expansion between the pin and its mating hole aren't accounted for. For instance, if the pin and hole expand or contract differently due to temperature changes, the interference fit can be compromised. This is why selecting materials with similar thermal expansion coefficients and precise fitting tolerances are so important. Ultimately, having a comprehensive understanding of the thermal characteristics of the chosen material is crucial for ensuring that the interference fit, which is the source of the joint's strength, remains reliable under different operating temperatures. By integrating these considerations into the design, engineers can improve the reliability and longevity of applications using dowel pins in a variety of fields.
When designing dowel pins for interference fits, it's not just about the fit itself, but also the materials used and how they behave under different conditions. The hardness of the pin material, for instance, can be crucial. Steel pins, known for their strength, can sometimes be brittle depending on the specific grade chosen, possibly causing problems if not well-matched with the surrounding material. It's an interesting area where material selection influences performance significantly.
Temperature changes can cause issues, too, due to the differences in how materials expand or contract. This becomes critical in applications that see fluctuating temperatures since the fit can loosen or become too tight, potentially affecting the structure's integrity. Understanding these thermal expansion characteristics is fundamental to prevent problems later.
The surface roughness of both the pin and the hole influences friction during assembly, potentially affecting the force needed to install the pin. Smoother surfaces reduce friction, but that could also reduce grip if the fit isn't optimized, leading to a weaker joint. It's a delicate balancing act.
Installing the pin creates residual stresses in both the pin and the hole, and how these stresses interact over time can influence the overall durability. Engineers must consider these residual stresses to avoid potential fatigue failures.
Lubricants can be beneficial, reducing the insertion force and improving control over the assembly process. But they must be chosen carefully to avoid interacting negatively with the materials being joined.
Heat treatment affects the microstructure of the pin, influencing hardness and ductility, so understanding how a heat-treated pin will perform under load versus one that's simply cold-rolled is essential.
The load distribution around the contact area is uneven, and engineers can't ignore how mechanical loads concentrate. The interference fit influences the initial assembly, but the loading conditions also play a critical role, and we need to anticipate the possible stress concentration areas that can lead to weak points in the assembly.
Beyond a simple linear response, some materials show non-linear elastic behavior under high stress or strain, particularly in high interference fits. Engineers need to understand when a material goes into the nonlinear regime to properly model and design for these types of applications.
When joining dissimilar metals, the possibility of galvanic corrosion arises due to different electrochemical potentials. This issue, while less likely to occur with some metal combinations, becomes a concern in highly humid or corrosive environments. This is something that must be kept in mind when designing structures for outdoor environments or in situations where corrosion is a possibility.
Lastly, dynamic stresses due to vibrations or shocks can accelerate wear and potentially loosen the dowel pin over time. The design must account for not only static loads but also dynamic loading to prevent issues that can arise in dynamic environments, requiring engineers to incorporate dynamic analyses into their design process.
Essentially, designing reliable interference fits requires a deep understanding of material properties, beyond simply knowing the interference fit value, and taking into consideration a variety of factors that can affect performance and longevity of the assembly.
Optimizing Dowel Pin Interference Fits Precision Techniques for Enhanced Structural Integrity - Precision Hole Preparation Techniques for Optimal Fit
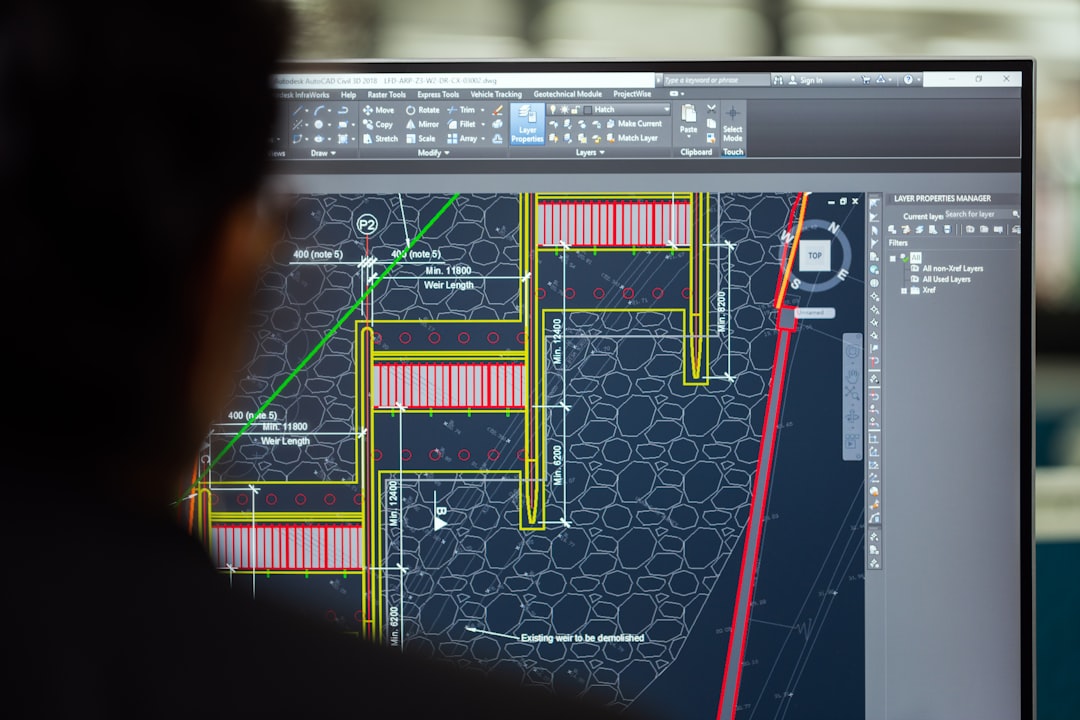
Achieving optimal dowel pin fits hinges on precise hole preparation techniques, which directly influence the functionality and reliability of mechanical assemblies. The process of creating these holes involves careful consideration of factors like drill size, rotational speed, and the cutting fluid used, as these can drastically impact the quality and dimensional accuracy of the hole. Different dowel pin types, such as ground, knurled, or coiled spring pins, require specific hole preparation methods to ensure they properly engage and maintain alignment within the assembly. Furthermore, comprehending the distinction between clearance, interference, and transition fits is crucial, especially for interference fits where precise tolerances are essential for successful assembly while preserving structural integrity. The success of dowel pin assemblies ultimately depends on meticulous hole preparation, a critical aspect influencing both the longevity and performance of the final product. A poorly prepared hole can introduce unforeseen stresses, compromises to the fit, and an overall less stable assembly. While the emphasis is often on the pin itself and the interference fit, the hole's characteristics shouldn't be overlooked.
Achieving optimal dowel pin fits relies heavily on the precision of the hole preparation, and this process is more intricate than it may seem. Surface treatments like laser etching or shot peening can significantly modify the friction between the pin and hole, potentially allowing for less stringent tolerances while still ensuring a strong bond. However, we need to remember that material properties are key. For instance, the elastic limit – the point at which a material transitions from elastic to plastic deformation – varies widely among materials, which means a certain interference fit in steel won't necessarily translate to the same performance with aluminum or a composite. This underscores the need for a customized approach to fit specifications depending on the materials involved.
The residual stresses introduced during the pin's installation can induce unforeseen dimensional changes in the assembly over time, highlighting that even seemingly small variations in insertion pressure can result in significant long-term misalignments. Interestingly, the dowel pin's geometry – its length, diameter, and even shape – plays a substantial role in determining how stress is distributed during assembly. It's an important consideration when designing optimal interference fits, as stress concentration can become a major factor in failure. Additionally, in applications subject to repeated temperature fluctuations, thermal cycling can lead to material fatigue, potentially affecting the initial interference fit. Understanding the thermal expansion characteristics of both the pin and the host material is crucial for long-term stability and preventing performance degradation.
Using high-strength steel dowel pins carries a risk of hydrogen embrittlement under certain circumstances, specifically if they're exposed to specific environments. This emphasizes the need to select suitable material finishes that minimize the chance of hydrogen absorption to prevent unexpected failures. When it comes to installation, the selection of lubricant can significantly impact the insertion force and, surprisingly, sometimes even the final fit itself. Inappropriate lubricants may lead to a worse fit than a dry assembly, underscoring the importance of carefully considering the choice of lubricant.
In applications where cyclical loads are a factor, it's likely that the interference fit will relax over time. Engineers need to consider not just the initial fit but also the long-term behavior under realistic dynamic conditions, which can be quite complex. The level of the interference fit has a strong relationship with fatigue life, with excessive interference increasing stress concentrations, potentially leading to premature failures. It's a delicate balance where achieving a strong joint requires avoiding unnecessary stresses that can shorten the life of the component. Researchers are increasingly turning to tools like real-time digital image correlation to study the intricate behavior of interference fits during assembly, hoping to gain a better understanding that will enable improved design methods and recommendations in future assemblies. It's clear that optimizing dowel pin interference fits is an area ripe for continued investigation, and these techniques promise to provide more reliable assemblies moving forward.
Optimizing Dowel Pin Interference Fits Precision Techniques for Enhanced Structural Integrity - Advanced Installation Methods for High-Interference Assemblies
When dealing with high-interference assemblies, traditional installation methods can be challenging and potentially damaging. This is where advanced techniques become crucial. Methods like ultrasonic-assisted pressing offer a more controlled and accurate way to install components with high interference, helping to avoid damage and ensure a precise fit. Paying close attention to the relationship between the contact area's length and diameter is vital, as this ratio significantly impacts how the assembly performs, especially when subjected to varying loads. Managing wear during installation is also a key concern, especially since high interference fits can lead to increased friction and potential component damage. Preventing such wear and damage ensures that high-interference assemblies last longer and maintain their structural integrity. These advanced methods help to address the growing need for more robust and reliable solutions in demanding applications found in fields like aerospace and precision engineering. The ongoing development of installation methods and techniques continues to refine this crucial aspect of mechanical design.
When dealing with high-interference assemblies using dowel pins, we encounter some interesting challenges. One key issue is the potential for plastic deformation. If the interference is too extreme, it can push the materials past their elastic limits, resulting in permanent changes in shape. This can be detrimental to the assembly's stability, making it essential to be careful about how tightly we fit these pins.
Interestingly, a slight taper in the hole can help with insertion during high-interference assemblies. This is a clever approach to guide the pin in more smoothly and avoid damage during the process. However, it's important to understand how the specific taper influences the fit characteristics.
Installing a dowel pin creates complex residual stresses within both the pin and its surrounding material. It's vital that we understand these stress patterns to avoid long-term issues like fatigue failures. It's a great reminder that even seemingly minor details can have a big impact over time.
The use of lubricants is a point that often surprises people. It turns out that the choice of lubricant, and its application, can surprisingly affect the final fit. Some lubricants can create a slipperiness that reduces the interference fit, which can be counterintuitive for a system that relies on tight fits for strength. It underscores the need to carefully consider every part of the process.
Some materials are simply more complex than others. Anisotropic materials, for instance, have properties that vary based on the direction of the applied force. This introduces another level of complexity when designing interference fits, and we need to account for these differences in material behavior to ensure good outcomes.
Thermal differences between the pin and the hole can create problems in high-temperature applications. Even slight variations in how each expands and contracts with temperature change can cause misalignment and potential damage. It's a constant reminder that we can't ignore environmental conditions.
At higher interference values, we often observe that materials enter a nonlinear elastic range, leading to more intricate stress distributions. This behavior makes design more challenging and requires sophisticated modelling approaches to accurately predict how the assembly will perform.
When subjected to dynamic loads, the interference fit can relax over time. This illustrates the need to think beyond static conditions. We need to consider how the assembly will behave over time, especially if subjected to repetitive loads, as this can change the initial design assumptions.
The pin's shape can significantly impact the distribution of stress. For instance, a tapered or conical end can help to distribute the stresses more evenly, mitigating potential failure points. It's an interesting reminder that even small changes in geometry can lead to substantial performance differences.
Finally, when dealing with high-interference fits, it's essential to develop comprehensive inspection and testing protocols. Methods like ultrasound or X-ray imaging can reveal defects or misalignments that might not be apparent with conventional measurement techniques, ensuring that the assembly meets its structural integrity goals.
It's clear that understanding advanced installation methods for high-interference assemblies is critical to achieving reliable designs. This requires careful consideration of the material properties, geometric factors, and operational environment, all working together to influence the fit and long-term performance of the assembly. It is an interesting area of research and engineering that continually challenges assumptions and pushes towards improved designs.
Optimizing Dowel Pin Interference Fits Precision Techniques for Enhanced Structural Integrity - Stress Distribution Analysis in Interference-Fitted Joints
Understanding how stress is distributed in interference-fitted joints is crucial for creating reliable mechanical assemblies. The way stress is distributed is complex and is influenced by factors such as the material's properties and how loads are applied. This is especially important when working with materials like composites, which can behave differently depending on the direction of the applied load.
Researchers have found that adjusting the stress distribution can potentially improve the fatigue life of a joint, making it last longer when it is subjected to repeated loads. This finding has been supported by both experimental testing and numerical simulations, mostly focused on pin connections. Mathematical tools such as the Lekhnitskii complex potential theory have also helped provide insights into the behavior of interference fits, especially regarding where cracks tend to start. These studies suggest that the pre-stress caused by installing a pin into a hole is key to the overall structural strength.
As engineers continue to push the boundaries of design, particularly in high-performance applications, having a full understanding of stress distribution in interference fits is becoming more critical. This knowledge will be vital for ensuring the reliability and longevity of products across many fields, highlighting the need for ongoing research into the stress dynamics that are present in these kinds of assemblies.
Researchers have found that stress concentrates at the edges of interference-fitted joints, which can negatively impact fatigue life and overall performance when subjected to repeated loading. A deep understanding of how these stresses develop is crucial for designing reliable and durable mechanical assemblies.
When dealing with high interference fits, materials can show nonlinear elastic responses. This means the traditional approaches used to model stresses might not be accurate, potentially leading to design flaws. It's an area where engineers need to carefully consider the assumptions they make in their calculations.
The surface roughness of the pin and the hole can influence friction during installation, affecting the force required for assembly. This suggests that there is a balance that needs to be struck to ensure both a strong and undamaged connection.
The Poisson effect, which describes the tendency of materials to expand laterally under compression, can become more noticeable in situations involving high interference fits. This impact of material properties needs careful consideration to ensure it doesn't negatively affect designs.
It's intriguing that a slight taper in the hole can make installation easier for high interference pins. It provides a gentle guide for the pin during the assembly process, lessening the chance of damage or misalignment. However, it also affects the exact fit, so the design must be thought through carefully.
Installing a dowel pin generates complex residual stresses in both the pin and the hole it's inserted into. These stress patterns are important to understand since they can influence long-term performance, potentially creating weak points that lead to future failure.
Disparities in thermal expansion between the pin and the hole become problematic in high-temperature applications. The mismatch in how they respond to temperature changes can create misalignments, potentially compromising the connection.
For materials whose properties vary depending on direction (anisotropic materials), pin insertion produces even more complex stress distributions. Predicting the outcome in practical applications will likely require specialized modeling techniques.
Engineers must understand how the interference fit behaves under dynamic loads, as this can affect the joint's ability to maintain its initial integrity over time. This involves incorporating considerations beyond static loads, adding complexity to the design process.
Advanced inspection methods such as ultrasound and X-ray imaging can help engineers find defects within the assembled joint that might otherwise be missed. This is important, especially in applications where high reliability is critical. These methods will become increasingly important as we design more complex assemblies.
Optimizing Dowel Pin Interference Fits Precision Techniques for Enhanced Structural Integrity - Long-Term Performance Monitoring of Dowel Pin Connections
Assessing the long-term performance of dowel pin connections is crucial for understanding how these connections hold up over time. Factors such as fatigue, temperature fluctuations, and dynamic forces can impact the durability of these joints. It's important to pay attention to how stress is distributed within the connection, as uneven stress or mismatched materials can lead to early failures.
Careful manufacturing processes and precise installation methods play a key role in ensuring long-term reliability. Furthermore, continuous monitoring is needed to identify any potential issues before they become major problems. The goal is not just to have connections that perform well initially, but also to predict how they'll age and withstand the stresses of their environment. By focusing on these aspects, engineers can significantly increase the reliability of dowel pin connections, making them suitable for demanding applications across various industries. Refining monitoring techniques will continue to be vital in the future, helping us create ever more robust and reliable mechanical designs.
Observing the long-term performance of dowel pin connections is crucial for understanding how these joints hold up over time. It's not uncommon for these studies to span several years, with some pushing into a decade or more to fully grasp the impact of fatigue and material degradation.
When a connection is subjected to repeated loads, it's been observed that the initial tightness of the interference fit can gradually relax, essentially loosening the joint. This is something that designers have to anticipate, especially when dealing with applications that experience significant stress.
Temperature changes can dramatically influence the stress distribution within a dowel pin connection. Surprisingly, even a 10-degree Celsius swing in ambient temperature can noticeably alter the interference fit, revealing just how sensitive these joints can be to their environment.
Once a pin is installed, it creates a noticeable amount of residual stress in the surrounding material. These stresses, if not carefully managed during design, can contribute to unexpected failure modes over the life of the component.
The choice of materials used in the pin and the surrounding structure can have a huge impact on the connection's long-term performance. For example, a steel pin within a polymer sleeve could show stress concentrations that differ by more than half compared to a similar joint made completely of steel under the same load.
It's been discovered that cracks tend to initiate where the pin meets the hole due to high stress concentrations, particularly when the assembly is exposed to dynamic forces. This emphasizes the need for very precise tolerances to minimize the risk of failure at this point.
The lubricant used during installation can have unintended consequences on the long-term performance of the joint. Some lubricants can actually modify the initial interference fit, leading to issues with wear or early failure.
When the interference fit is significant, materials can exhibit nonlinear elastic behavior. This makes stress analysis more complex, requiring more advanced modeling to accurately predict when failure might occur.
Materials with anisotropic properties, like certain composites, introduce further complexities to the dowel pin's behavior. Since stresses can be dramatically different depending on the direction of the load, design approaches need to be tailored to each unique application.
New inspection methods like digital image correlation and non-destructive testing are becoming increasingly useful for keeping an eye on the health of dowel pin assemblies over time. These techniques can detect subtle changes in alignment and structural integrity, helping to maintain reliable performance for the duration of a structure's lifetime.
More Posts from aistructuralreview.com: