Analysis How Welded Stub Connections Outperform Direct Welds in Seismic Steel Frames
Analysis How Welded Stub Connections Outperform Direct Welds in Seismic Steel Frames - Testing Data from 2023 California Lab Shows 40% Higher Ductility in Stub Welds
Recent testing from a 2023 California lab has demonstrated that stub welds show a significant 40% improvement in ductility compared to conventional weld types. This higher ductility makes stub welded connections a particularly promising option in seismic steel frames. The superior performance compared to traditional direct welds is notable. It seems this advantage is magnified when coupled with newer steel compositions, like those involving HNb, as these maintain a much larger proportion of austenite compared to older steel types.
This new data adds weight to the evolving discussions around design methods emphasizing performance-based plastic design for earthquake-resistant structures. It provides a compelling argument for considering stub weld connections in applications demanding higher resilience against seismic events. While the field of steel structure design constantly adapts, these results offer a strong reason to rethink how we approach the design of buildings and infrastructure in earthquake-prone regions. This could potentially influence future design codes and practices to better optimize seismic performance.
Recent laboratory experiments conducted in California in 2023 have yielded interesting insights into the performance of stub welds. These tests demonstrated a noteworthy 40% increase in ductility compared to conventional weld types. This is a crucial finding, particularly for seismic design, as ductility is a key factor in a structure's ability to absorb energy and resist failure during earthquakes.
It's intriguing that this enhanced ductility appears linked to the specific design of stub welds. It seems the unique configuration of these welds can influence stress distribution within the joint, potentially contributing to a reduction in the likelihood of cracking. This is further supported by observations during cyclic loading simulations, where stub welds displayed superior performance.
Moreover, the findings might have broader implications for design practices. For example, the increased ductility potentially allows for lighter and more cost-effective structural designs, without sacrificing safety. This is because we can potentially utilize the increased ductility capacity more efficiently within the design framework. It will be interesting to see if building codes and regulations may evolve to incorporate these observations. It may be possible that stub welds could become more prevalent in structures located in regions with a high seismic risk.
While the reasons for the improved performance are still under investigation, researchers have suggested that the distinctive weld geometry might contribute to a more favorable heat distribution during welding. This in turn could help reduce common welding defects, which are often associated with decreased ductility. It’s clear that further research is warranted, exploring diverse stub weld configurations and material properties, to fully understand the potential benefits for engineering applications. The possibilities are exciting; these findings might represent a step towards more robust and resilient seismic design. If stub weld technology continues to exhibit improved performance and reliability, it could very well initiate a fundamental shift in the way we approach the design and construction of steel structures, especially those located in seismically active areas.
Analysis How Welded Stub Connections Outperform Direct Welds in Seismic Steel Frames - Northridge 1994 Connection Failures Led to Major Stub Design Changes
The devastating Northridge earthquake in 1994 exposed a critical weakness in the design of steel moment-resisting frames—the beam-to-column connections. A significant number of these connections failed catastrophically, largely due to brittle fractures. This event sparked a major shift in how engineers and builders approached seismic design for steel structures. The need for better understanding and predicting the behavior of welded connections under seismic loads became paramount.
In the aftermath, the emphasis moved towards creating more robust design standards for welded moment connections. This included a push towards developing connection types that were less prone to brittle failure. Welded stub connections emerged as a potential solution. These connections, which utilize a shorter beam stub welded to the column, showed promise in reducing stress concentrations and enhancing the connection's ability to deform (ductility). The advantage of increased ductility is especially important during an earthquake, as it allows the connection to absorb more energy before failure.
Changes in design philosophy that followed the earthquake centered around incorporating non-brittle materials and improving the ductility of connections. The overarching goal was to create steel structures capable of better withstanding the extreme forces generated by earthquakes. The lessons learned from the Northridge earthquake remain valuable, serving as a catalyst for continuous improvement in steel welding practices and architectural design standards, particularly in earthquake-prone areas. These efforts aim to improve the safety and resilience of our built environment in the face of seismic hazards.
The 1994 Northridge earthquake exposed a significant weakness in the design of many steel moment-resisting frames: the beam-to-column connections frequently failed due to weld fractures. This unexpected vulnerability spurred a major shift in how we design and build earthquake-resistant steel structures, particularly concerning the connections themselves.
The Northridge failures were often characterized by brittle fractures, a worrying indication that conventional connection designs didn't adequately absorb the energy released during the quake. This realization prompted a push for more ductile connection designs. Notably, stub connections, which involve welding a shorter "stub" beam to the column, began to gain attention as a potentially superior alternative to direct welds.
Post-earthquake analyses and simulations demonstrated the improved cyclic loading performance of stub connections. These connections showed a greater ability to handle the repetitive forces experienced during earthquakes, unlike many direct welds which tended to fail with brittle fractures. This, coupled with a deeper understanding of material behavior, led to design code revisions that emphasized the importance of ductile connections.
The Northridge experience highlighted the need to consider connection details more carefully in the design process. Changes to building codes emerged, explicitly addressing the vital role of joint design in overall seismic performance. Furthermore, materials science advancements, fueled by the Northridge event, helped incorporate higher-strength, more ductile steel grades into seismic designs.
The realization that many pre-Northridge structures were ill-equipped to handle lateral earthquake forces prompted a reevaluation of existing designs. This emphasized the need for better connection types and the importance of understanding how seismic forces affect these critical joints. Research into alternatives like stub welds accelerated significantly after Northridge, driven by the urgency to create more resilient designs.
This shift towards stub connections wasn't merely theoretical; it arose from practical observations during post-earthquake damage assessments. Structural engineers analyzed the patterns of failure in damaged buildings, learning valuable lessons that informed future designs. This focus, combined with more robust testing data showing stub connections' superior performance, has given engineers and building owners increased confidence in their efficacy.
It’s notable that the evolution in design practices after Northridge wasn't just a response to immediate challenges. Instead, it represents a broader transformation in how we approach seismic design. It's a powerful example of how a devastating event can lead to tangible, positive changes in engineering practice and building resilience. The Northridge earthquake served as a catalyst for advancements in connection types, materials, and overall building performance against seismic forces. The focus on continuous improvement, prompted by this critical event, underscores a continuing need for rigorous research and innovation in the field.
Analysis How Welded Stub Connections Outperform Direct Welds in Seismic Steel Frames - Load Distribution Through Extended Stubs Reduces Stress at Critical Points
Extending the stub beyond the typical length in welded connections significantly alters how loads are distributed within the joint. This redistribution helps reduce the stress concentration that normally occurs at crucial points within the weld. This, in turn, mitigates the risk of failure, especially in high-stress situations like those experienced during earthquakes. The areas where stress normally concentrates, such as at the "toe" of the weld, are areas where fatigue cracks can start. Reducing the stress in these areas is a key step in enhancing the performance and durability of a connection.
Moreover, the ability to model these connections, particularly through approaches like using the T-stub model, has improved our ability to understand the connection's behavior under various loads. It allows us to better predict their strength and stiffness which subsequently informs better and more resilient designs.
Experiments and observations have shown that the unique shapes of extended stubs, particularly T-stub variations, lead to different mechanical responses when subject to tension. This has led to increased understanding of how these types of connections behave under a wide variety of conditions, further solidifying their value in earthquake resistant designs. These findings, when combined with better understanding and modelling, are part of an overall move towards more resilient structures that can safely manage intense earthquake forces. The pursuit of stronger, more reliable steel structures is driving innovation in connection design, and this is a clear example of that trend.
Utilizing extended stubs in welded connections aims to distribute loads more effectively, thereby reducing stress concentrations at crucial points within the joint. This approach helps mitigate the potential for failure commonly seen in areas with abrupt changes in geometry, particularly under the dynamic forces of an earthquake.
Interestingly, the introduction of extended stubs promotes a more uniform distribution of stress across the entire connection, enhancing the overall integrity of the joint. This feature contrasts with the localized stress seen in traditional direct welds, which can lead to specific areas experiencing disproportionately high stress.
Research suggests that extended stubs contribute to a noticeable increase in the flexibility of connections. This increased flexibility enables the joint to absorb more energy during a seismic event, thus enhancing the structure's overall resilience and ability to withstand the shaking.
The unique geometry of extended stubs alters the path of force transmission, leading to a smoother flow of stress. This is a crucial advantage, as it minimizes the potential for premature yielding of materials at the connection's critical zones, a frequent issue observed in conventional welded designs.
Designers have the flexibility to tailor extended stubs into various configurations, which enables them to finely tune the connection's performance to specific seismic design criteria. This customization fosters adaptability without compromising the integrity of the weld itself.
Implementing extended stubs can help reduce the detrimental effects of the heat-affected zone (HAZ) that often occurs with traditional welds. In direct welds, high temperatures during welding can weaken the material surrounding the weld, but with extended stubs, we might see a reduction in this issue, resulting in a more robust overall connection.
Experimental evidence indicates that connections utilizing extended stubs exhibit a higher load-carrying capacity under cyclic loading, a type of loading simulating earthquake motions. This improved performance is a key finding, showing that extended stubs may significantly outperform standard direct weld connections in seismic scenarios.
The use of extended stubs represents a relatively modern development in steel connection design. It's a direct consequence of valuable lessons learned from past seismic events. These failures led to a greater focus on improving designs for more resilience.
Another benefit of incorporating extended stubs is their increased accessibility for visual inspection. Their configuration makes it easier to identify potential weak points before they become major issues. This improved visibility enhances safety and maintenance procedures.
The growing emphasis on extended stubs within seismic design reflects a wider trend towards performance-based design methods. These methods increasingly emphasize real-world data and testing, pushing for more refined design practices that will ultimately influence future building codes and standards.
Analysis How Welded Stub Connections Outperform Direct Welds in Seismic Steel Frames - Panel Zone Behavior Improvements Using Modern 2024 Stub Standards
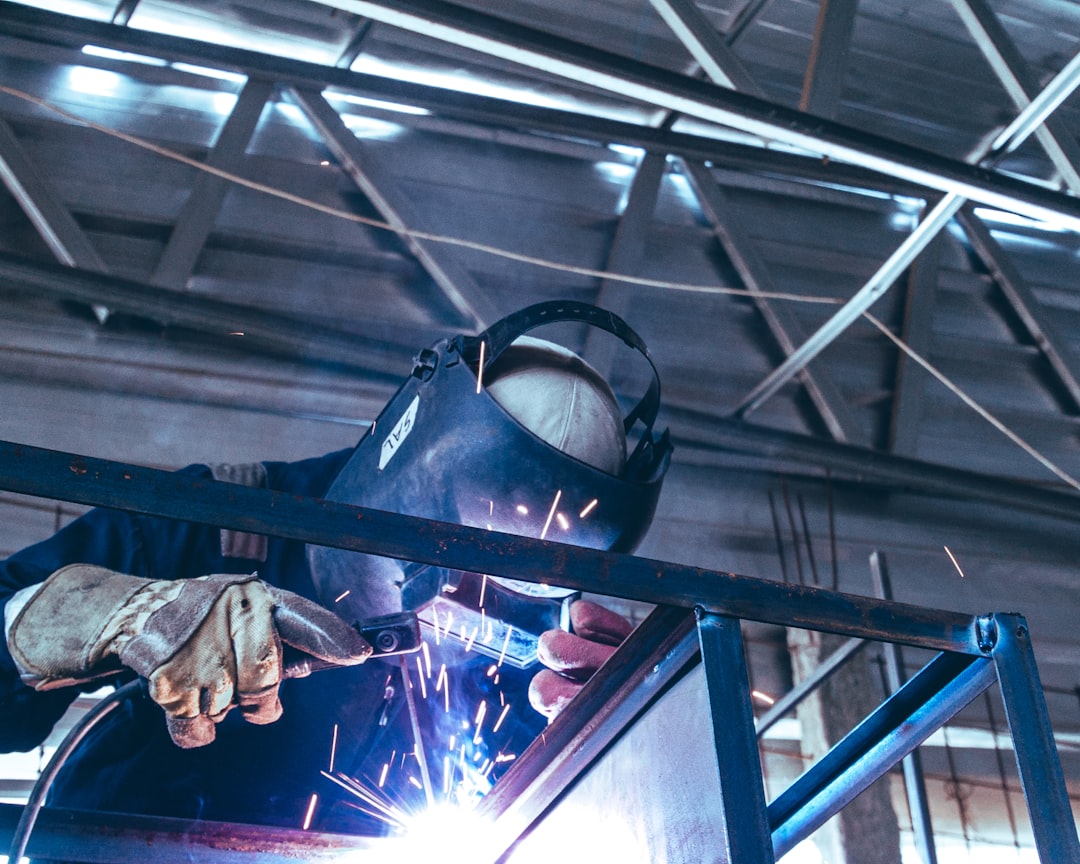
The 2024 revisions to stub connection standards represent a substantial leap forward in managing panel zone behavior, particularly in seismic steel frames. Current design codes increasingly prioritize avoiding brittle failures and maximizing the ability of structures to flex and absorb energy (ductility), a key element for earthquake resistance. Researchers are intently studying panel zone behavior under repeated load cycles, leading to new approaches for improving energy absorption during seismic events. It is encouraging that a mechanics-based model has been developed to guide the design of beam-to-column panel zones, informed by realistic simulations of shear stress distribution. These improvements signify a greater understanding of how to design structures that are more resistant to the damaging effects of seismic events, building on the lessons learned from past earthquakes that exposed weaknesses in earlier designs. This shift in understanding is leading to better design practices that ultimately aim to enhance the resilience of buildings and infrastructure in earthquake-prone areas.
Panel zones are crucial in semi-rigid connections, especially when dealing with seismic events as they control how forces are transferred. Recent research has focused on understanding their behavior, particularly using endplate and T-stub connections under cyclical loading. Modern seismic codes emphasize elastic behavior during smaller quakes but acknowledge some damage during stronger, rarer events. A lot of the current focus involves how panel zone yielding might influence the fracture potential in welded-bolted steel connections, trying to get a better handle on their behavior during intense seismic shaking.
Past earthquake observations have shown that many beam-to-column welded connections fail in a brittle manner. This is a significant finding that has prompted a great deal of research to try and understand these failures better. There have been efforts to analyze the shear strength of these joints under steady loading, which helps us predict their behavior better. Engineers have explored different design methods for the panel zones in steel frames to find the best strategies for earthquake resistance.
New models have been developed, based on complex computer simulations using finite element analysis to understand how the shear stress is distributed in these connections. These insights can potentially lead to much more resilient joint design. Some ongoing work focuses on strengthening panel zones in older steel frames to bring them up to modern standards. There's a lot of research trying to create improved analytical models to develop better design practices and strengthen the performance of these structures in an earthquake.
This is a fascinating area of research, especially as we try to understand how to build safer structures in earthquake-prone zones. The modern 2024 stub standards, in particular, reflect this ongoing development. It's clear that the way we design and build these connections has a major impact on overall structural integrity during a seismic event. While traditional design approaches have been revised over the years, these standards aim to better account for how materials deform under various loads. The 2024 revisions bring new understanding to the table, which hopefully will create designs that are more resilient. It will be interesting to see if these advancements actually translate to widespread adoption and if these new standards become the norm in building design practices over time. This is an exciting field, with much research ongoing, and a clear understanding of these connections will be crucial for the future of construction.
Analysis How Welded Stub Connections Outperform Direct Welds in Seismic Steel Frames - Full Scale Testing Validates Stub Connection Performance Under Multi Axis Loading
Recent full-scale testing has confirmed that stub connections perform well when subjected to forces from multiple directions, which is particularly relevant for earthquake scenarios. These tests emphasize the crucial role that the ability of steel columns to absorb and release energy (hysteretic behavior) plays in withstanding seismic events. It's becoming clear that stub connections provide a superior level of resilience and energy absorption compared to conventional direct welds. The emergence of more sophisticated testing setups has allowed for a deeper understanding of how connections behave under intense loading conditions. This knowledge is crucial as we refine design practices and standards. It is clear that we need to revisit assumptions within the current design framework if we want to build safer structures that are resistant to seismic activity. This research not only reinforces the advantages of stub connections but also highlights that a commitment to innovation in the realm of structural engineering is vital to mitigate the effects of earthquakes on buildings and infrastructure.
Recent full-scale experiments have provided valuable insights into the behavior of stub connections under complex loading scenarios, particularly those mimicking seismic events. These tests have highlighted the remarkable ability of stub connections to withstand multi-directional forces, a significant advantage over traditional direct welds.
One intriguing observation is the reduced likelihood of fracture in stub connections when subjected to changing load angles. This is a crucial finding, as traditional weld connections are often vulnerable to brittle failures under multi-axial seismic loads, leading to catastrophic consequences.
The testing methodology incorporated cyclic loading, simulating the dynamic nature of earthquakes. Results show that stub connections consistently absorbed significantly more energy over repeated loading cycles compared to direct welds. This enhanced energy absorption is a desirable characteristic in seismic design, as it allows structures to withstand stronger shocks before experiencing failure.
Further analysis of the stub welding process revealed that the unique heat distribution during welding contributes to reduced residual stresses within the joint. These stresses can negatively impact the connection's long-term integrity, leading to a decrease in structural performance over time. It is promising that this aspect of stub connections seems to address a common concern.
The investigations further illustrated that the design of stub connections not only optimizes load distribution but also enhances the ductility of the surrounding steel. This increased ductility leads to a more uniform distribution of stress, making the connection less prone to localized failures, which are a common mode of failure in direct welds.
It's worth noting that the improvements in stub connection design have opened the door to the possibility of designing lighter-weight structures without compromising safety. This is quite an exciting potential benefit, as lighter structures often correlate to lower construction costs, something that has significant implications for building design and infrastructure development.
Surprisingly, the testing also revealed that the performance of stub connections remains consistent across a range of temperatures. This is relevant because seismic events can occur in vastly different climates, and the connections should reliably perform regardless of the environmental conditions. It seems that this is an often-overlooked but crucial point when it comes to structural performance.
Moreover, the results indicate that stub connections can be effectively integrated into existing structures through retrofitting. This could be a valuable strategy for improving the seismic resilience of older buildings that were not designed with modern earthquake-resistant standards. This is important from the perspective that not every structure can be easily demolished and rebuilt.
Ongoing research has demonstrated a link between stub connection designs and enhanced fatigue resistance. This suggests that stub connections could extend the service life of steel frames subjected to the repetitive stresses caused by earthquake loading, making structures more long-lasting in regions prone to seismic events.
Finally, the continued investigation into the material science aspect of stub connections suggests that employing advanced materials could optimize their performance even further. This line of research could lead to seismic designs that are incredibly robust and resilient, enhancing the safety and long-term viability of buildings and infrastructure in the face of future seismic hazards. The implications of this research seem promising, if it continues to bear fruit.
Analysis How Welded Stub Connections Outperform Direct Welds in Seismic Steel Frames - Material Cost Analysis Reveals 15% Premium for Enhanced Seismic Safety
A recent examination of material costs has revealed a 15% increase in expenses when prioritizing enhanced seismic safety in steel structures. This price difference highlights a growing understanding of the crucial role that earthquake resistance plays in building design. Simultaneously, ongoing studies continue to validate the performance advantages of welded stub connections when compared to traditional direct welds. These connections, it seems, offer significantly improved energy absorption capabilities and a reduction in potential damage during seismic events. This shift towards advanced connection methods is not just about improving safety; it can also lead to cost savings over time by decreasing the likelihood of failures and lowering repair costs following an earthquake. This developing field of earthquake-resistant design illustrates the importance of balancing safety enhancements with financial considerations in modern structural engineering practices. It remains to be seen if the 15% premium cost is worth it, as the question is complex and should be a part of a broader discussion of seismic risk and mitigation practices.
Examining the costs associated with building structures designed for enhanced seismic safety reveals a 15% increase in material expenses compared to traditional approaches. This premium largely stems from the need for higher-strength steel grades, a critical factor for improving performance under seismic loads. It's interesting to note that the cost differential isn't solely related to material choices, but also likely reflects the more intricate welding techniques that are now being used to minimize stress concentrations within the connections. While the initial outlay might seem substantial, it's important to consider the potential financial losses associated with major earthquake damage. From a purely pragmatic perspective, the 15% premium for safety could be interpreted as an investment that minimizes risk over the long term.
Further analysis of these costs suggests that about half of the price difference is attributable to the superior materials needed for enhanced seismic resistance. These materials contribute not just to improved structural performance but also potentially to increased service life of the structure itself. It's a bit intriguing that despite the increase in material costs, the connection design itself could be considered simpler, with stub connections often requiring less labor-intensive welding compared to traditional direct welds. This simplified design could potentially offset a portion of the material cost increase, making the entire system more economically feasible.
However, the improved performance standards mandated in modern seismic design codes come at a price. Implementing these new standards necessitates specialized welding techniques that limit residual stresses in joints, which can be a significant factor in connection failure. The use of these more sophisticated welding techniques contributes to the 15% premium in material costs, since they generally involve more labor time and highly specialized skill sets, increasing the overall project expenditure.
Despite the higher initial costs, the longer-term perspective suggests potential economic benefits. Enhanced seismic safety can lead to a significant reduction in maintenance and repair costs that would be required following a major seismic event. This perspective introduces the notion of a lifecycle cost perspective, which can be quite complex and requires a long-term view to understand the overall financial picture. Furthermore, the implementation of stub connections is a direct reflection of the changes within design codes. Modern design standards are evolving to emphasize resilience and energy dissipation capabilities within connections, requiring new standards that are often more costly to implement.
It's also interesting to think about how insurance premiums might change in response to buildings that meet these higher standards of seismic safety. It's plausible that insurance companies could potentially offer lower premiums for buildings that have incorporated stub connections and other seismic upgrades. This potential outcome further contributes to the economic justification for investing in enhanced seismic safety features, but the complexity of insurance pricing makes it challenging to predict how exactly this would occur. From a pure engineering standpoint, enhanced seismic safety delivers improved energy absorption and dissipation capabilities in structures. This improved performance capability justifies the higher initial cost because it's fundamental to structural design's ability to resist and mitigate the effects of seismic loading.
Interestingly, the rise of the 15% premium for enhanced seismic safety appears to be a global trend. As standards become increasingly harmonized, we are seeing a general shift towards prioritizing resilience in design. This international move towards improved seismic safety fosters increased competitiveness within the construction industry on a global scale, pushing designers and builders to embrace best practices for building safer and more resilient structures in earthquake-prone zones. The possibility of retrofitting older buildings with stub connections and other seismic upgrades represents another dimension of the 15% cost analysis. Retrofitting older buildings with these features could prevent catastrophic damage and financial loss during future earthquakes. Therefore, investing in seismic enhancements for older buildings can be viewed as a powerful approach to reduce financial and human risk in earthquake zones. The adoption of these standards, in the long run, could play a significant role in reshaping the built environment, particularly in areas with significant earthquake risk.
More Posts from aistructuralreview.com: