The Critical Role of Pressure in Structural Integrity
The Critical Role of Pressure in Structural Integrity - Designing Structures to Withstand Internal and External Pressure
Ensuring buildings and other constructions stand firm when subjected to forces from within or outside forms a cornerstone of reliable engineering. This isn't a simple task of 'making it strong enough'; it demands a sophisticated understanding of how different forces—like pulling, pushing, or sliding—manifest within materials and the structure as a whole. Engineers must conduct rigorous analysis, not just selecting materials and sizing components, but critically evaluating load paths to dissipate stress effectively and prevent localized failure points. The reality is that structures encounter a complex mix of static conditions and dynamic, often unpredictable, environmental forces such as significant wind loads or seismic activity. Factoring these variables accurately into the design phase is paramount, and perhaps where the greatest challenges lie, ensuring structural health isn't compromised over decades of service. Ultimately, achieving this resilience requires a disciplined, integrated approach to design and analysis.
Beyond the simple idea of materials being strong enough, handling pressure in structural design involves navigating some rather counter-intuitive challenges.
For structures facing external pressure, particularly those with thin walls, the primary concern isn't always the material's yield strength but rather geometric instability. Instead of the structure simply being crushed, it might suddenly and catastrophically buckle inward. This mode of failure, driven by elasticity or plastic deformation interacting with shape, demands analytical methods distinct from straightforward stress-versus-strength checks, often requiring complex non-linear simulations to predict accurately.
Even seemingly minor features like access hatches or windows introduce significant complexities. Under pressure differentials, these discontinuities act as stress concentrators, potentially magnifying local stresses to several times the levels found in the surrounding structure. Managing these peaks through careful detailing and reinforcement is essential, as they represent vulnerable points for fatigue damage and potential crack propagation over time.
Furthermore, the long-term performance of materials under sustained pressure and elevated temperatures presents a unique hurdle: creep. This slow, time-dependent deformation means that a structure might gradually change shape or experience stress relaxation over years or decades, even if initially designed within elastic limits. Predicting and accommodating this viscous-like behavior necessitates sophisticated material models and a design philosophy that considers the full service life, not just immediate conditions.
Consider a common scenario like a cylindrical pressure vessel under internal load. Basic mechanics reveal a fundamental asymmetry: the stress acting circumferentially around the cylinder (hoop stress) is roughly twice the stress acting along its length (axial stress). This dictates that the material's strength in the hoop direction is typically the critical factor limiting the vessel's working pressure, a relationship designers must always keep in mind.
Finally, designing a structure to contain a vacuum is often as demanding as designing for high internal pressure. The force isn't internal pushing out, but the full external atmospheric pressure pushing inward. Without internal pressure to counteract it, the structure must possess sufficient inherent stiffness and strength to resist collapse or implosion under this external loading, presenting a mirror image of the challenges faced with positive internal pressure.
The Critical Role of Pressure in Structural Integrity - Analyzing How Pressure Induces Stress and Strain in Materials
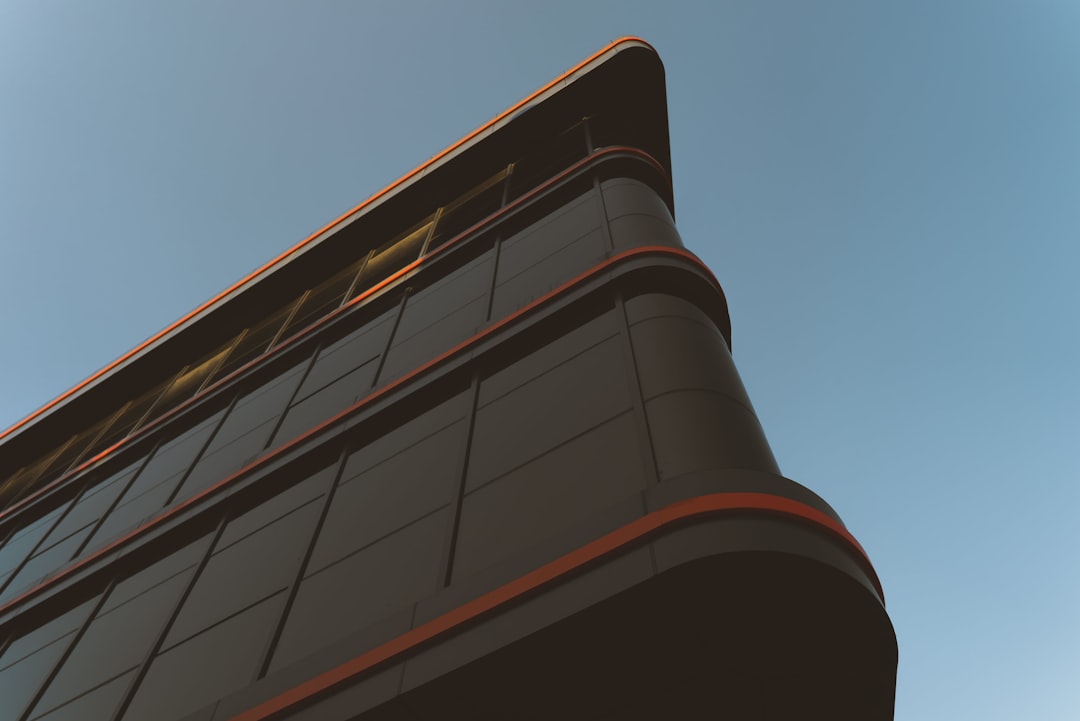
Unpacking how applied pressure translates into stress and strain within materials is fundamental to ensuring structural integrity, particularly in critical components like pressure vessels or structural members. Such loading regimes induce intricate internal force distributions that can precipitate failure modes ranging from unwanted deformation and fatigue damage to outright material rupture if local stress levels exceed critical material limits, like yield strength or ultimate tensile strength determined through analysis. While foundational principles highlight general patterns, such as the higher circumferential stresses seen in cylindrical forms, applying this knowledge to actual, complex geometries incorporating features like nozzles or experiencing temperature fluctuations requires sophisticated analytical and computational techniques, notably finite element analysis, to accurately map stress concentrations and predict potential failure points. Assuring structural health over a long service life also demands consideration of time-dependent effects and, looking ahead, improved integration of predictive models with real-time condition monitoring, underscoring the continuous evolution required in this critical engineering discipline.
Delving deeper into how pressure loads translate into internal forces and deformation within a material reveals several less-discussed but critical aspects we often encounter. It's not simply about the externally applied force, but how the material itself interacts with its environment and internal state.
One often overlooked factor, particularly relevant for porous materials like certain ceramics or concrete, is the pressure of fluids trapped within tiny internal voids. This pore pressure can exert significant internal stresses, effectively pushing back from within. When external pressure is applied, the pore pressure contributes to the overall internal stress state, potentially lowering the material's effective strength or stiffness against that external load. Accurately characterising these pore networks and fluid behaviour under load adds a complex layer to predictive modelling.
Another phenomenon that complicates the picture is the existence of internal stresses locked into a material before any external load is applied. Residual stresses, often a consequence of manufacturing processes such as welding, cooling, or forming, can be significant. They combine with the stresses induced by applied pressure, meaning the total stress state is a superposition of these internal, pre-existing forces and the operational loads. This superposition can either beneficially reduce peak stresses or, critically, push localized regions over their limit prematurely if the residual stresses are tensile and additive to the applied stress.
When pressure is truly uniform and hydrostatic – pushing equally from all directions, like submerging a material in a fluid under pressure – the primary effect isn't necessarily reaching the yield strength governed by shear stress. Instead, the dominant response is a change in volume, related to the material's bulk modulus. While the material *does* experience stress internally, predicting failure solely based on yielding becomes less straightforward under such conditions; we're often dealing with bulk compressibility rather than shape change failure modes until deviatoric stresses are also introduced.
Furthermore, many advanced engineering materials aren't mechanically uniform in all directions. They are anisotropic, meaning their strength and stiffness properties vary depending on the orientation. For these materials, like composites with layered fibers or some alloys with directional grain structures, the direction of the principal stresses induced by pressure relative to the material's inherent structural orientation is paramount. Predicting deformation and potential failure under pressure requires aligning the stress state with the material's specific anisotropic constitutive laws, a step beyond simple isotropic models.
Finally, it's fascinating and sometimes problematic that sufficiently high pressures can fundamentally alter a material's internal structure. Pressure-induced phase transformations can occur, causing a sudden shift in crystal lattice structure and, consequently, a dramatic change in mechanical properties – sometimes becoming stronger, sometimes weaker or more brittle. For applications involving extreme pressures, we must consider not just elastic or plastic limits, but the possibility of the material transitioning into an entirely different state with potentially unpredictable behaviour under subsequent load.
The Critical Role of Pressure in Structural Integrity - Identifying and Managing Defects in Pressurized Components
Sustaining the integrity of structures under pressure, from expansive pressure vessels to critical welded connections, demands a diligent focus on identifying and managing defects that inevitably arise post-manufacture or during service. Flaws like cracks or subtle material anomalies represent clear threats to a component's ability to withstand operational loads safely over its intended lifespan. Simply designing for perfect material is unrealistic; consequently, advanced non-destructive examination techniques have become indispensable tools for locating these imperfections before they propagate to critical size. Once a defect is found, assessing its significance isn't trivial. It involves rigorous structural integrity evaluations, often leveraging methodologies like fitness-for-service or remaining useful life assessments informed by principles of fracture mechanics. A pragmatic, risk-based approach guides maintenance and inspection efforts, ensuring resources are directed where the potential impact of a defect is greatest. The ongoing challenge lies in further integrating sophisticated data analytics and real-time monitoring capabilities to transition towards more predictive defect management strategies for pressurized systems.
Shifting focus to the flaws that inevitably manifest in these components, identifying and managing defects within pressurized systems is a constant challenge, demanding a level of vigilance beyond simply ensuring the initial design meets theoretical requirements. It's a recognition that materials and structures aren't perfect, and operational life introduces complexities. Here are some aspects that often strike me as particularly noteworthy or perhaps counter-intuitive when grappling with this reality in engineering practice:
Consider, for instance, the peculiar behaviour small cracks can exhibit under significant internal pressure. Far from being more obvious, high internal pressure can actually press the faces of fine cracks together, a phenomenon that can inadvertently make them harder to detect reliably with conventional non-destructive techniques, such as certain ultrasonic methods that rely on the presence of a discernible gap or interface. It sometimes feels like the very condition we're concerned about can actively hinder our ability to find the evidence of its existence, necessitating the exploration of more specialized or phased inspection approaches.
Then there's the critical concept of how a sharp defect, say a crack or a similarly tight notch, fundamentally alters the local stress field. At the very tip of such a flaw, stress is intensely concentrated – magnified far beyond the nominal stress levels elsewhere in the component. This isn't merely academic; if this amplified stress intensity, a quantifiable measure, reaches a specific material property known as fracture toughness, the crack can propagate rapidly and unstably. What's critical here is that this brittle failure can occur even when the average stress in the component is well below the material's yield strength. Understanding and assessing this potential for sudden, catastrophic fracture based on defect size and geometry is absolutely central to managing integrity.
Perhaps less intuitively for those outside the field, the presence of defects in pressurized equipment isn't automatically grounds for retirement or immediate repair. International standards and accepted engineering practice often permit components with known flaws – minor wall thinning, small cracks, etc. – to remain in service. This isn't complacency; it's based on rigorous "fitness-for-service" engineering assessments. These involve detailed analysis and prediction, aiming to demonstrate with confidence that the defect will not grow to a critical size or otherwise compromise safety throughout the planned operational life under anticipated pressure cycles and environmental conditions. It’s a pragmatic approach, certainly, but relies heavily on the accuracy of predictive models and often requires enhanced monitoring.
A somewhat surprising interplay occurs between defects like small pits or crevices and the service environment, particularly where corrosive media are present. The pressure difference *across* such a small opening can influence the local chemistry or ingress of fluids, sometimes dramatically accelerating localized corrosion rates precisely at these defect sites compared to areas of uniform exposure. It's a complex synergy between the mechanical stress/pressure effects and the electrochemical processes that drives aggressive material loss in highly specific, vulnerable zones within the pressurized boundary, complicating long-term degradation predictions.
Finally, while traditional non-destructive testing offers snapshots in time, some advanced techniques allow us to 'listen' to the structure as it operates under pressure. Sensitive acoustic emission sensors can be deployed to detect minute stress waves released by events like crack initiation, slow crack growth, or plastic deformation occurring within the material. This approach offers the potential for real-time or near-real-time monitoring of active defect evolution, providing valuable insights into how flaws are behaving under actual operational loads and potentially serving as an early warning system, though signal interpretation in noisy environments remains a challenge.
The Critical Role of Pressure in Structural Integrity - Confirming Structural Soundness Through Pressure Testing Methods
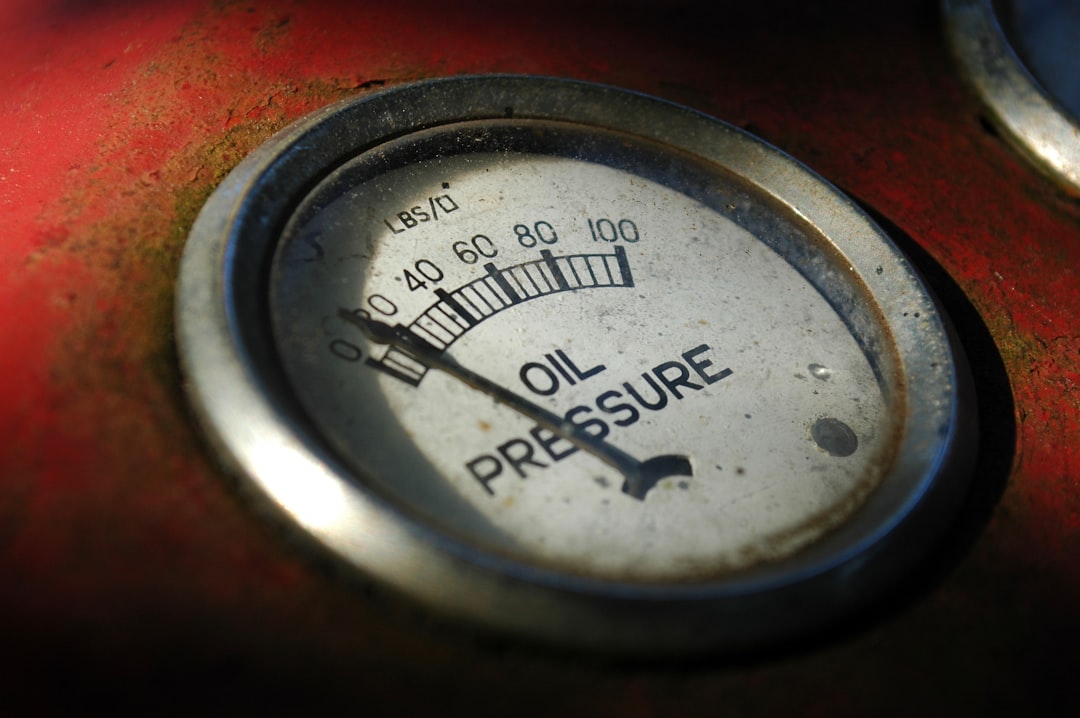
Applying pressure deliberately, often referred to as pressure testing, stands as a cornerstone method for empirically verifying the structural soundness of vessels, pipelines, and other pressurized equipment. Techniques like hydrostatic testing, utilizing incompressible liquids to minimize energy release in case of failure, are commonly employed. These tests serve as a practical demonstration that the manufactured item, despite design calculations and material specifications, can actually hold the required pressure without catastrophic failure or unacceptable leakage under controlled conditions. While no test guarantees perfection, pressure testing exposes gross flaws or deficiencies that might have been missed during manufacturing or subsequent inspections, providing a critical safeguard before operational stresses are encountered. It's a necessary checkpoint, offering confidence in fitness for service after construction, significant repairs, or as part of periodic reassessment programs, aiming to ensure integrity isn't compromised by unforeseen issues or cumulative damage during its working life.
Venturing into confirming a structure's fitness by pushing its pressure boundaries reveals layers of complexity beyond simple pass/fail. Here are a few points that often stand out when considering how we actually verify the soundness of pressure systems:
Working with gases for testing, known as pneumatic testing, carries inherently more stored energy at comparable pressure levels than using liquids like water (hydrostatic testing). This means that while a failure can be dramatically more hazardous due to the potential for rapid energy release, it offers a counter-intuitive advantage: even tiny leaks manifest as easily detectable phenomena like audible hissing or visible bubbles in a detection fluid, sometimes making it more sensitive to minute through-wall flaws that hydrostatic tests might miss due to surface tension or capillary effects.
While a successful pressure test, hydrostatic or pneumatic, confirms that a component possesses sufficient strength and integrity *at that specific moment* under the test conditions, it fundamentally doesn't predict its long-term performance. It's a crucial snapshot, certainly, verifying resistance to initial or operational pressures, but it offers limited direct insight into how the material might behave years down the line under sustained load, fluctuating temperatures, or repeated operational cycles which could drive time-dependent degradation mechanisms.
Pushing a component intentionally beyond its anticipated operating pressure during a "proof test" is sometimes employed to provide added assurance, but it's not without potential drawbacks. This over-pressurization, while validating a minimum burst strength margin, can paradoxically induce localized plastic deformation or even initiate micro-scale damage, perhaps microscopic cracks or void formation at material imperfections. Such subtle changes might not cause immediate failure during the test but could potentially reduce the component's fatigue life or become initiation sites for future crack growth under subsequent operational pressure cycles, a trade-off requiring careful consideration.
The physical properties of the test medium itself critically influence detection capabilities. For instance, employing a tracer gas with extremely small molecules, like helium, during a pressure test allows for the detection of leaks through pathways far too small for even water molecules to penetrate. This highlights how simply applying pressure isn't enough; the selection of the test fluid and detection method must be precisely matched to the expected size and nature of potential flaws to ensure comprehensive coverage.
In certain high-pressure vessel designs, a calculated over-pressurization procedure, termed autofrettage, is deliberately applied. This isn't purely a test; it's a manufacturing process where the component is pressurized beyond its yield strength near the bore. The purpose is to induce residual compressive stresses in the inner layers upon pressure release. These beneficial compressive stresses then counteract subsequent tensile stresses from operational internal pressure, significantly enhancing the component's resistance to fatigue crack initiation and improving its overall service life under cyclic loading, a clever manipulation of material behavior through controlled pressure application.
More Posts from aistructuralreview.com: