Mitigating Galvanic Corrosion New Insights on Aluminum-Stainless Steel Interfaces in Structural Applications
Mitigating Galvanic Corrosion New Insights on Aluminum-Stainless Steel Interfaces in Structural Applications - Understanding the Mechanism of Galvanic Corrosion in Aluminum-Stainless Steel Couples
Galvanic corrosion presents a significant challenge when aluminum and stainless steel are in contact, especially within structural frameworks. This phenomenon arises from the formation of a galvanic cell, where aluminum, possessing a lower corrosion potential, acts as the anode and suffers accelerated corrosion. The presence of moisture further accelerates this process, as it acts as an electrolyte, facilitating the flow of electrons between the dissimilar metals. The specific type of stainless steel used also plays a role, with different grades exhibiting varying corrosion potentials and consequently impacting the severity of the galvanic corrosion.
Advanced modeling approaches, like those employing the Nernst-Planck equations, provide deeper insights into the mechanisms that govern the behavior of these coupled systems, allowing for a more thorough understanding of the interaction between aluminum and stainless steel. While protective coatings can offer some protection against galvanic corrosion, their success is heavily dependent on their ability to remain intact and compatible with the stainless steel counterpart. The efficacy of these coatings in diverse environments and for extended durations continues to be a critical area of study.
Designing with these two materials, especially in complex multi-material structures, presents a significant challenge, as joining methods can inadvertently introduce pathways for enhanced corrosion. This complexity highlights the need for a thorough understanding of the interactions and corrosion mechanisms to ensure the long-term integrity of these structures.
When aluminum and stainless steel come into contact within a corrosive environment, like the presence of moisture or seawater, a phenomenon known as galvanic corrosion can take place. This occurs because these two metals have different electrochemical potentials, resulting in the formation of a galvanic cell. Aluminum, with its lower potential, typically acts as the anode, becoming preferentially corroded in comparison to the stainless steel cathode. This is a significant concern, especially in applications where these two metals are frequently paired, such as in aerospace structures using stainless steel fasteners.
The rate of corrosion can be influenced by several factors, including the surface area ratio of the metals. A small area of aluminum in contact with a larger area of stainless steel can accelerate corrosion, as the larger cathodic area enhances the electrochemical reactions. The presence of protective oxide layers on aluminum can initially offer some protection, but these layers can be damaged in certain environments, leaving the aluminum vulnerable to corrosion. Even when the stainless steel is in a passive state, meaning it exhibits very little corrosion on its own, the galvanic coupling with aluminum can still initiate localized corrosion, especially pitting corrosion, predominantly on the aluminum surface.
Beyond these fundamental concepts, further complexity arises from factors like temperature, alloying elements, and the application of corrosion mitigation strategies. Elevated temperatures can speed up corrosion due to increased ionic activity in the electrolyte, accelerating the electrochemical reactions. Different stainless-steel grades, particularly those with variations in alloying elements like molybdenum, can impact the galvanic potential and subsequently alter the severity of corrosion in coupled systems. Additionally, the effectiveness of corrosion inhibitors can vary considerably when attempting to mitigate galvanic corrosion at aluminum-stainless steel interfaces. Some inhibitors may provide protection to one metal while inadvertently accelerating corrosion on the other.
Surface treatments, such as anodizing, can be beneficial in reducing the risk of galvanic corrosion, as they form a thicker, protective oxide layer on the aluminum. Nevertheless, the selection of the surface treatment should be tailored to the specific environmental conditions and how it influences the migration of ions. Ultimately, careful consideration of the design and geometry of aluminum-stainless steel interfaces is critical for minimizing the risk of galvanic corrosion. Tight joints, for instance, may trap moisture and electrolytes, creating localized corrosion hotspots, while well-designed gaps can improve drainage and reduce the likelihood of corrosion. A thorough understanding of these mechanisms and influencing factors is essential for developing durable and reliable structures that incorporate both aluminum and stainless steel components. The research community continues to explore the complexities of this interaction, using advanced modelling techniques like Nernst-Planck equations to gain a deeper insight into the fundamental principles governing the corrosion behaviour of these material couples.
Mitigating Galvanic Corrosion New Insights on Aluminum-Stainless Steel Interfaces in Structural Applications - Impact of Different Stainless Steel Grades on Corrosion Rates of Aluminum
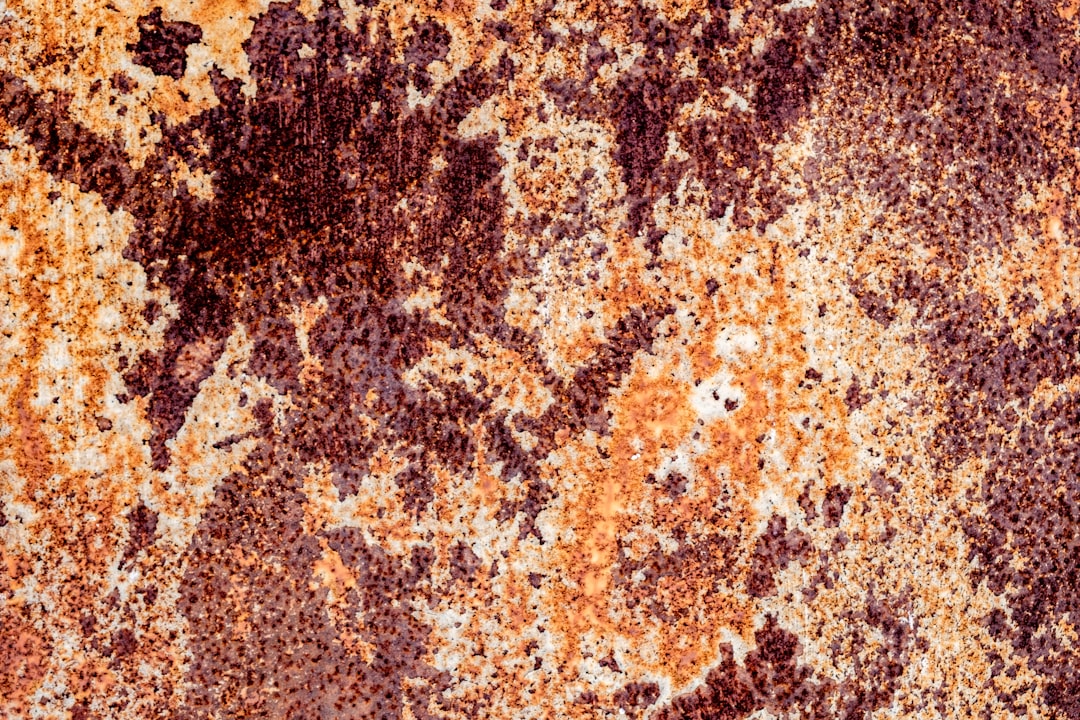
The corrosion rate of aluminum can be significantly impacted by the specific grade of stainless steel it's coupled with, making this a crucial factor in structural design. Different stainless steel grades, such as austenitic, duplex, and super duplex, have varying electrochemical potentials. This difference in potential can lead to galvanic corrosion, where aluminum, having a lower potential, becomes the anode and suffers accelerated corrosion. This effect is particularly pronounced when aluminum is in contact with more noble grades like SS316, especially in humid conditions. These circumstances often lead to localized corrosion, a concern for structures that combine these metals.
Recent studies have highlighted the role of the aluminum alloy's microstructure in the corrosion process. The size and distribution of second-phase particles in these alloys can greatly influence the galvanic corrosion reaction. This suggests that controlling and understanding the microstructure of aluminum is essential for minimizing corrosion in multi-metal structures. The complex interactions at the aluminum-stainless steel interface are thus critical to understanding and mitigating corrosion. A clear grasp of the electrochemical behavior at these interfaces is imperative for predicting the long-term durability and reliability of structures using both materials. Failing to consider this can lead to unexpected and potentially severe corrosion, reducing the lifespan and safety of the structure.
The selection of stainless steel grade significantly influences the corrosion behavior of coupled aluminum systems. Austenitic grades, such as 304 and 316, tend to be more resistant to galvanic corrosion compared to ferritic grades due to their inherently more noble electrochemical nature. The presence of specific alloying elements, like molybdenum, can further enhance corrosion resistance, especially against pitting, which is often a concern when aluminum and stainless steel are in contact with corrosive agents.
Surface conditions of the stainless steel also play a role. Rougher finishes might exacerbate localized corrosion on the aluminum surface by promoting crevice formation and trapping corrosive electrolytes. This observation highlights the importance of controlling surface quality in structural applications.
Higher temperatures can amplify galvanic corrosion rates. Increased kinetic energy at higher temperatures leads to faster ionic reactions within the electrolyte, accelerating the corrosion process on the aluminum component.
There's a curious aspect to protective coatings. Some anodized aluminum coatings, while intended to protect, can become a problem if they are damaged. This exposes the aluminum directly to the stainless steel, and inadvertently enhances galvanic corrosion. This underlines the necessity of careful coating selection and consistent inspection of their integrity.
The relative surface area of the two metals is a critical factor. If the stainless steel has a significantly larger surface area compared to the aluminum, the rate of corrosion on the aluminum can increase dramatically. This factor should be accounted for during the design phase to ensure appropriate material ratios.
The use of corrosion inhibitors in multi-material systems like these can be tricky. Some inhibitors specifically designed for stainless steel can, counterintuitively, accelerate corrosion on the aluminum. This presents a challenge in selecting the appropriate corrosion management strategy.
Even stainless steels that passively form a protective oxide layer are not always immune to galvanic corrosion issues. In conditions that disrupt the protective oxide layer, they can still contribute to corrosion on the aluminum, emphasizing the need for ongoing maintenance and monitoring.
A rather unexpected consequence of the coupling is that it can increase the likelihood of stress corrosion cracking in aluminum, particularly under specific environmental conditions. This effect can lead to failures that might not be readily anticipated in structural designs.
Finally, recent research indicates that precisely measuring electrochemical potential differences between specific stainless steel grades and aluminum can provide a valuable tool to more accurately predict corrosion behavior. This understanding can be utilized to enhance structural design and implement tailored mitigation strategies in these common multi-material systems.
Mitigating Galvanic Corrosion New Insights on Aluminum-Stainless Steel Interfaces in Structural Applications - Innovative Fastening Strategies to Reduce Galvanic Corrosion Risk
When joining aluminum and stainless steel, the risk of galvanic corrosion—a consequence of their differing electrochemical potentials—becomes a central concern. Innovative fastening strategies are crucial for managing this risk. One approach involves selecting fastener materials that are electrochemically compatible, minimizing the potential difference and thus reducing the driving force for corrosion. Joint designs that facilitate water drainage and minimize areas where moisture can become trapped are also important. Preventing direct contact between the two metals through isolation techniques can help to reduce the severity of localized corrosion that often occurs in these pairings.
A deeper understanding of the interplay between fastening methods, joint design, and material selection is paramount for achieving durable structures where these two metals are used together. The field of materials science and engineering is continuously evolving, leading to improved techniques for preventing galvanic corrosion and enhancing the lifespan of structures employing aluminum and stainless steel. These ongoing advancements hold the key to optimizing fastening strategies and ensuring improved resistance to galvanic corrosion.
When considering the connection of aluminum and stainless steel, the choice of fasteners isn't solely about mechanical strength. Fastener design itself can influence the likelihood of galvanic corrosion. For example, using non-metallic washers or applying specific coatings can act as barriers, limiting direct contact between these dissimilar metals and hindering the formation of a galvanic cell.
Exploring novel approaches to fastening, such as employing composite materials or thermoplastic fasteners, could potentially interrupt the direct pathways for corrosion. These strategies can effectively break the galvanic circuit, preventing the flow of electrons that accelerates aluminum's degradation.
However, we've found that sometimes, seemingly protective choices can have unexpected consequences. Zinc-coated fasteners, while initially offering some protection, might introduce long-term complications. Since zinc sits lower than aluminum on the galvanic series, it's more prone to corrosion. This could destabilize the interface over time, potentially creating a more complex corrosion problem than if no coating was present.
Innovative joint designs, such as those incorporating nested fasteners, show promise in managing moisture. By carefully directing the flow of water away from the critical areas of the connection, we can potentially minimize the environment that promotes galvanic corrosion.
The selection of the bolt material itself has a significant effect. Subtle changes in alloy composition, even seemingly minor ones, can introduce unpredictable galvanic behavior. For instance, the presence of nickel in some fasteners has been shown to unexpectedly accelerate corrosion under specific conditions.
Treating fastener threads with advanced surface coatings that are chemically inert can offer substantial benefits. This approach helps minimize the likelihood of galvanic coupling at stress concentration points, the regions where corrosion is most likely to initiate in aluminum-stainless steel connections.
Recent studies suggest that the microscopic texture of a fastener's surface plays a role. Textures that mimic the patterns found in some biological systems may be particularly useful. These mimicry designs could promote better drainage and reduce moisture retention in the assembly, minimizing corrosion hotspots.
It's crucial to consider that thermal expansion differences between aluminum and stainless steel can create significant mechanical stress within fasteners. This stress concentration can exacerbate localized corrosion, potentially undermining traditional design approaches that do not account for these thermal effects.
The use of electrically insulating materials offers a promising path forward, particularly in more demanding applications. These materials, if capable of enduring high temperatures and pressures, offer the possibility of preventing galvanic currents altogether. This could lead to significant improvements in the design of high-stress structural applications.
The integration of sensors within fastener designs would allow for the continuous monitoring of corrosion rates. This capability is very useful. By providing real-time data on the progression of galvanic corrosion, we can implement proactive maintenance procedures. This helps us preserve the integrity of structures using aluminum and stainless steel together.
Mitigating Galvanic Corrosion New Insights on Aluminum-Stainless Steel Interfaces in Structural Applications - Experimental Findings on Weight Loss in Mixed Metal Assemblies
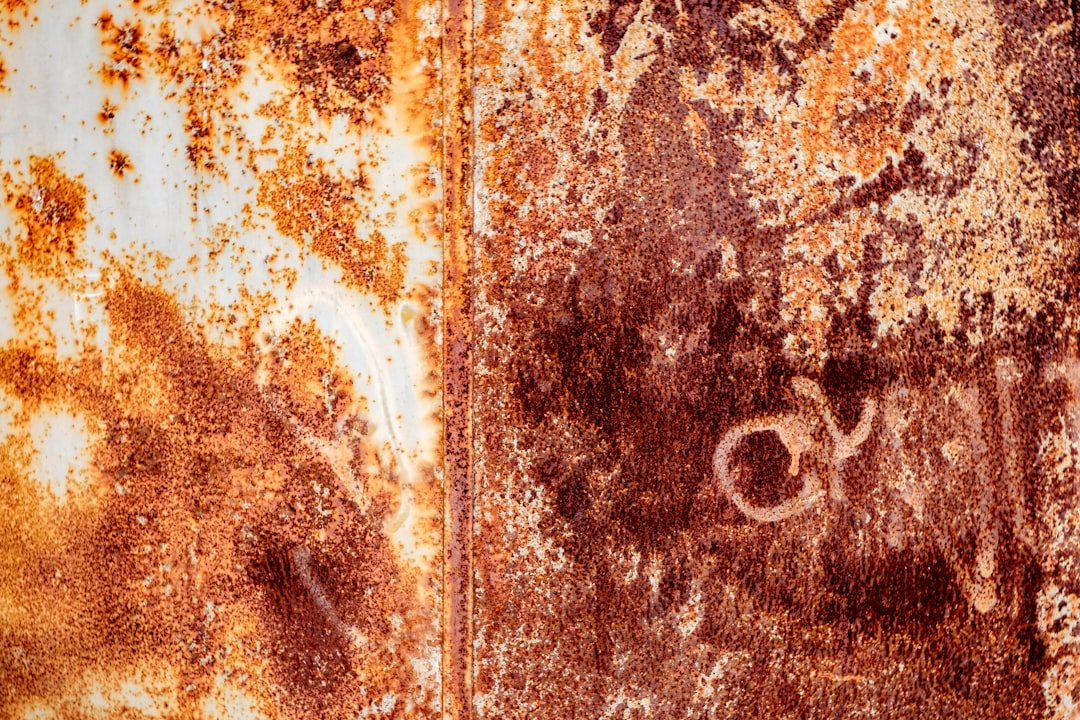
Studies examining mixed metal assemblies, specifically those incorporating aluminum and stainless steel, have unveiled a crucial link between weight loss and the phenomenon of galvanic corrosion. Experimental methods involving weight loss measurements have demonstrably shown a substantial acceleration of corrosion when aluminum is coupled with stainless steel. In certain instances, weight loss increased as much as 45-fold, a clear indication of aluminum's role as a sacrificial anode.
Quantitative analyses further revealed that some aluminum alloys, when coupled with stainless steel, suffered significantly greater weight loss, up to three times more after extended exposure to salt spray environments. The detailed investigation into the kinetics of corrosion using power functions provides further evidence that different metal combinations exhibit varying corrosion rates and behaviors. These observations are significant as they raise concerns about the longevity and structural integrity of assemblies incorporating aluminum and stainless steel. Consequently, the need for innovative and effective methods to mitigate galvanic corrosion in such applications is increasingly critical.
1. The combination of aluminum and stainless steel in structural assemblies can create a heightened risk of corrosion at their interface, especially when considering their different thermal expansion behaviors. The mismatch in how they expand and contract with temperature fluctuations can induce mechanical stresses, which, in turn, can amplify localized corrosion, leading to unexpected issues.
2. One intriguing finding is that even when using stainless steel grades known for their passive nature, localized pitting corrosion can still occur on the aluminum surface if the stainless steel's protective oxide layer becomes compromised. This underscores the importance of ensuring and maintaining the surface integrity of both materials within coupled systems to avoid such problems.
3. Interestingly, mathematical models used to explore corrosion processes have shown that even minuscule variations in the composition of the surrounding electrolyte can cause significant changes in the corrosion rates. This sensitivity highlights the critical need to carefully control and manage environmental conditions in any structural design that uses these metals together.
4. The internal structure of aluminum alloys, including factors like grain size and the distribution of different phases, plays a key role in how susceptible they are to corrosion when paired with stainless steel. This indicates that when designing alloys for use in such multi-metal assemblies, careful consideration of the microstructure is needed to build in resistance to galvanic corrosion.
5. Research suggests that the presence of certain alloying elements in stainless steel, such as chromium and nickel, which are often used to improve the stainless steel's properties, might inadvertently increase the rate of corrosion of nearby aluminum through localized galvanic effects. This observation presents a bit of a surprise and emphasizes that the positive aspects of these elements can come with unexpected downsides in certain contexts.
6. It's surprising that a somewhat counterintuitive approach—roughening the aluminum surface—can be effective in mitigating galvanic corrosion. While we usually aim for smooth surfaces, creating specific patterns of roughness can enhance the adhesion of protective coatings, leading to better protection of the aluminum and preventing corrosion in multi-material structures.
7. The choice of materials used for bolts in aluminum-stainless steel assemblies has a big influence on the risk of corrosion. Bolts containing high amounts of nickel, for example, have been shown to sometimes speed up the corrosion process under specific circumstances. This indicates the importance of being cautious when choosing the type of fastener for these connections.
8. Protective coatings that are applied to aluminum surfaces can sometimes become a liability when they are exposed to very aggressive environments. Tiny imperfections in the coatings can allow corrosive substances to sneak through, neutralizing the beneficial effects of the coating. This observation highlights the need for regular inspections and maintenance of such coatings in structural applications to ensure they are still protecting the metal.
9. Interestingly, the length and shape of the joint in an assembly can have a noticeable impact on galvanic corrosion rates. Joint designs that encourage good drainage can significantly reduce moisture retention and help reduce localized corrosion.
10. Recent experimental results show that using electrically insulating fasteners can efficiently halt the flow of electrical current in aluminum-stainless steel assemblies. This "breaks" the galvanic circuit and offers a straightforward way to significantly improve corrosion resistance without changing the fundamental material composition of the assembly.
Mitigating Galvanic Corrosion New Insights on Aluminum-Stainless Steel Interfaces in Structural Applications - Role of Moisture and Coating Integrity in Accelerating Corrosion
Moisture plays a crucial role in accelerating corrosion when aluminum and stainless steel are in contact, especially within structural frameworks. Acting as an electrolyte, moisture facilitates the flow of electrons between the dissimilar metals, driving the corrosion process. The effectiveness of protective coatings in preventing corrosion hinges on their ability to remain intact and compatible with both aluminum and stainless steel. Any disruption or damage to these coatings can significantly increase the rate of corrosion.
The development of new coating technologies, incorporating features like self-healing and multifunctional properties, shows promise in enhancing corrosion resistance. Nevertheless, ensuring proper application and ongoing maintenance of these coatings is essential for their effectiveness. A deeper understanding of how moisture influences coating performance and the interactions between the metals is vital for the design of more effective corrosion mitigation strategies. As research continues, a greater emphasis on the interplay between moisture dynamics and coating integrity will lead to improved methods for managing galvanic corrosion in aluminum and stainless steel coupled systems.
1. Moisture acts as a crucial catalyst in galvanic corrosion, functioning as an electrolyte that bridges the electron flow between dissimilar metals like aluminum and stainless steel. This can drastically accelerate corrosion, especially in environments with high humidity.
2. Maintaining the integrity of protective coatings on aluminum is paramount. If these coatings fail, they expose the aluminum to direct contact with stainless steel, amplifying the likelihood of localized galvanic corrosion. This can happen even in environments that are typically considered protective.
3. It's interesting to note that some elements added to stainless steel, like chromium and nickel, while enhancing the steel's properties, might paradoxically boost corrosion rates in adjacent aluminum due to localized galvanic interactions. This illustrates the intricate interplay between different materials in a structure.
4. An unexpected finding is that surface roughness can be engineered to enhance the protection of aluminum. By creating controlled textures, we can improve the adherence of protective coatings and improve corrosion resistance. This contradicts the traditional approach of striving for smooth surfaces.
5. Research suggests that even minute changes in the surrounding environment, such as slight variations in pH or ionic concentration, can profoundly influence corrosion rates in coupled materials. This highlights the importance of precise environmental control in real-world applications involving aluminum-stainless steel pairs.
6. The grain structure and composition of aluminum alloys can significantly affect their vulnerability to corrosion when paired with stainless steel. Coarser grains or less uniform phase distributions in the aluminum can exacerbate the corrosion when in contact with stainless steel. This emphasizes the importance of choosing the right aluminum alloy for these applications.
7. It’s counterintuitive, but purposefully roughening the surface of aluminum can improve the effectiveness of protective coatings. This reveals a surprising role for texture in mitigating galvanic corrosion.
8. The design of the connection between aluminum and stainless steel is crucial. Joint geometries that promote efficient water drainage can substantially reduce moisture retention at the interface, consequently lessening the risk of localized corrosion.
9. Even stainless steel types known for their corrosion resistance can lead to localized corrosion on aluminum surfaces if their protective oxide layer is compromised. This emphasizes the importance of consistent maintenance and attention to the integrity of both materials within coupled systems.
10. Employing electrically insulating materials for fasteners can interrupt the flow of electrons in aluminum-stainless steel assemblies. This elegantly disrupts the galvanic circuit, leading to a simplified but effective way to reduce corrosion without altering the core material properties.
Mitigating Galvanic Corrosion New Insights on Aluminum-Stainless Steel Interfaces in Structural Applications - Emerging Technologies and Materials for Corrosion Prevention in Structural Applications
The field of corrosion prevention in structural applications is evolving rapidly, with a particular focus on the challenges posed by aluminum-stainless steel interfaces. While traditional approaches like protective coatings and chemical inhibitors remain important, the emergence of new technologies and materials is offering promising solutions. Nanomaterials, for instance, have shown considerable potential due to their unique properties, potentially leading to more effective and environmentally friendly corrosion inhibition. Additionally, the development of "smart coatings" which can adapt to changing environmental conditions is gaining interest as a modern approach to corrosion control.
Beyond material innovations, new fastening strategies are being explored. These strategies focus on minimizing the risk of galvanic corrosion by employing electrically insulating components and carefully designing joints to prevent moisture accumulation. However, it is essential to note that these technologies are still in their developmental stages. A deep understanding of the complex interactions at the aluminum-stainless steel interface remains crucial for realizing their full potential. Further research is needed to address challenges like the long-term performance of these materials and their interactions in complex structures, aiming to ensure the longevity and safety of structures incorporating these two metals. While the current advancements are encouraging, it's important to acknowledge that truly revolutionary changes in corrosion mitigation techniques aren't expected in the near future.
Corrosion prevention in structural applications, particularly where aluminum and stainless steel are used together, remains a vital area of research. Advanced coating technologies, particularly those incorporating nanomaterials, are showing potential. These coatings can be incredibly thin, and some can even repair themselves when damaged, which is beneficial for mitigating the effects of galvanic corrosion where these two materials meet. However, the selection of the aluminum alloy itself can have surprising consequences. For example, some alloys with higher copper content seem to corrode more quickly when paired with stainless steel. This highlights the need for careful material selection, keeping the intended application in mind.
There's increasing evidence that the surface finish on the stainless steel can make a difference in the severity of the corrosion. Highly polished stainless steel might encourage localized pitting on the aluminum compared to surfaces with more roughness. This roughness can promote drainage of moisture and potentially reduce the severity of corrosion. The electrochemical potential difference between the two metals is also affected by changes in temperature. Higher temperatures can boost the speed of ionic activity in the surrounding environment, which increases overall corrosion rates. Surprisingly, even brief exposure to corrosive environments can set in motion long-term corrosion patterns in aluminum alloys. This means the initial conditions of exposure are crucial in predicting how long a structure will last.
Composite materials, especially those including polymers with good thermal expansion matching characteristics, seem to show some promise in reducing galvanic coupling. They essentially act as a buffer between the two metals. But their long-term performance in real-world scenarios still needs to be better understood. Localized corrosion can change the mechanical properties of both metals, sometimes leading to unexpected structural failures. These failures appear to be influenced by the specific environmental conditions near the failure point.
Recent research models are suggesting that stress concentrations near bolt holes can increase localized corrosion. This highlights the importance of smart joint design when building structures with these materials. Thankfully, new sensors are making it possible to monitor corrosion rates in real-time at the interface of aluminum and stainless steel. This offers a chance to be more proactive about dealing with corrosion issues, potentially revolutionizing how we design for maintenance in structural applications.
In a surprising twist, some studies propose using sacrificial anodes made from different metals to divert corrosion away from the aluminum. While this can help to reduce the corrosion on aluminum, it may also complicate the compatibility of materials within the structure. It's still an idea that needs further evaluation. Overall, the field continues to make small, gradual advances. Significant breakthroughs in corrosion mitigation strategies for aluminum-stainless steel coupled systems are not yet anticipated in the near future.
More Posts from aistructuralreview.com: