Comprehensive Guide 7 Essential Tests for Electric Motor Performance and Reliability
Comprehensive Guide 7 Essential Tests for Electric Motor Performance and Reliability - Insulation Resistance Test for Winding Integrity
The Insulation Resistance Test is fundamental for assessing the health and reliability of a motor's winding insulation. This test, often utilizing instruments like a Megger, is designed to detect degradation or damage in the insulation system that separates the energized windings from the motor's core and frame. It's a critical diagnostic tool for preventing electrical failures stemming from insulation breakdown. While various methods, like spot reading and time-based resistance measurements, can be employed, interpreting the results often requires a skilled technician's expertise. Factors like the motor's voltage rating, size, and the materials used in construction directly impact the acceptable range of insulation resistance. The test helps to confirm that the insulation remains capable of withstanding the voltage stresses during operation, thereby safeguarding the motor from short circuits, ground faults, and other potentially devastating electrical issues. Unfortunately, there's no universal "pass/fail" threshold for insulation resistance. The "ideal" value varies significantly, making accurate interpretation of the test a challenge. It's not uncommon for a motor with seemingly acceptable insulation readings to still exhibit issues, highlighting the importance of experience in making operational decisions. Ultimately, a comprehensive understanding of the motor's design, operating environment, and the nuances of insulation resistance testing is key for utilizing this valuable diagnostic technique effectively.
1. The insulation resistance test, often a crucial part of motor maintenance, gauges the ability of motor windings to resist electrical breakdown under voltage stress. This capacity, referred to as dielectric strength, is fundamentally important for forestalling short circuits and potential equipment failure.
2. Insulation resistance is typically quantified in megohms (MΩ). Readings falling below 1 MΩ frequently suggest underlying problems that could impact motor efficiency or potentially lead to failures. However, it is important to remember that the correlation between resistance and severity is not always linear and interpreting the results requires experience and knowledge of the system.
3. Environmental factors can significantly influence insulation resistance test outcomes. High humidity or the presence of contaminants can decrease measured resistance, potentially leading to misinterpretations if not considered. This necessitates careful control of the testing environment to ensure accurate and meaningful results.
4. Repeated insulation resistance testing on the same winding in quick succession can result in what's known as "electrical fatigue". The repetitive application of voltage can cause localized heating, which can lead to a temporary alteration in resistance values, possibly generating misleading test results.
5. For a more comprehensive assessment of winding integrity, insulation resistance tests are ideally conducted at several voltage levels, such as 500V and 1000V. This is because certain defects might only become apparent at higher voltages, which provides a more detailed understanding of the insulation condition.
6. Different insulation materials have unique resistance properties. Synthetic insulation materials generally provide superior insulating characteristics compared to naturally derived materials. This difference can significantly impact the test results and needs to be taken into consideration when evaluating the results.
7. Factors like the motor's age, contamination by lubricants or cooling fluids, and mechanical stress can lead to substantial variations in insulation resistance over time. This highlights the crucial importance of regularly conducting insulation resistance tests as a proactive maintenance strategy.
8. The "Megger" test, a widely-used method for assessing insulation resistance, involves applying a standardized voltage and carefully monitoring the stabilization rate of the resistance. This aspect of the test provides valuable insight into the integrity of the windings. However, it's worth noting that the standardized nature can sometimes limit the accuracy depending on the specific characteristics of the motor and windings.
9. It's important to acknowledge that while the insulation resistance test reveals potential insulation issues, it doesn't directly identify inter-turn faults within the winding. These inter-turn faults, while potentially not indicated by this test, can still lead to reductions in motor performance and efficiency. Further testing is often needed for a complete diagnosis of the winding health.
10. Implementing a routine program of insulation resistance testing can considerably extend the lifespan of a motor. By facilitating the early detection of insulation degradation, this practice helps to avoid catastrophic, unexpected failures and expensive repair costs. Regular testing also allows for the development of a baseline of the motor's health that provides a valuable data resource in long-term monitoring efforts.
Comprehensive Guide 7 Essential Tests for Electric Motor Performance and Reliability - No-Load Test to Measure Core Losses
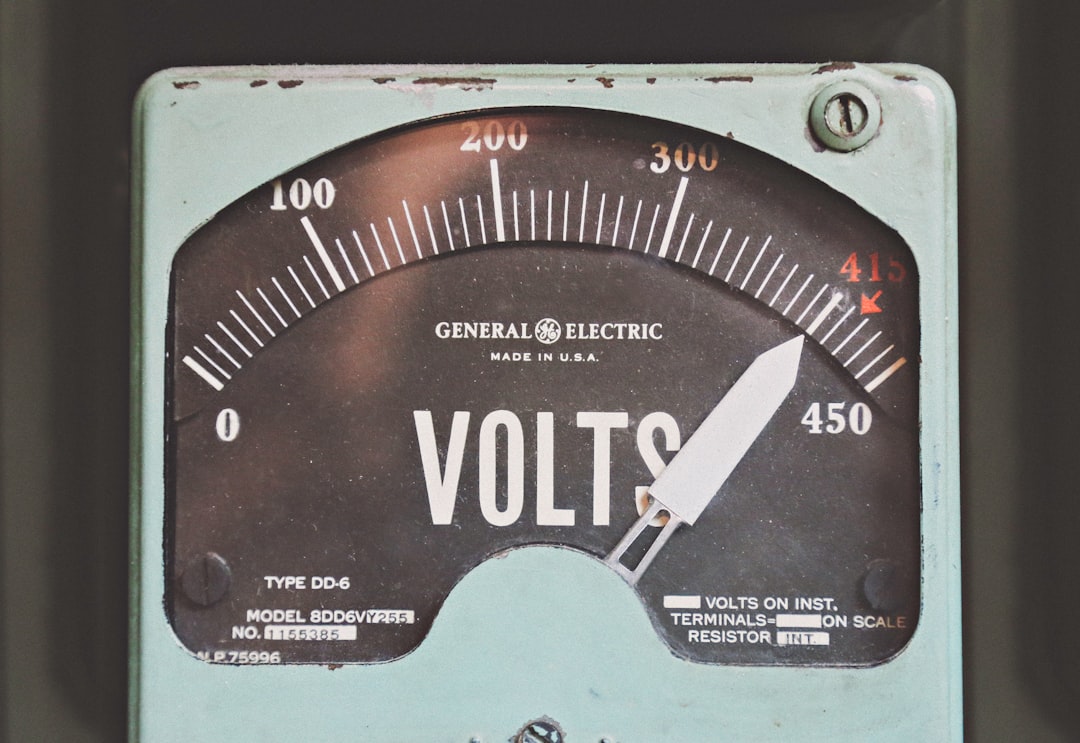
The no-load test is a fundamental method for assessing core losses within an induction motor. It's performed by running the motor at its synchronous speed without any external load applied. This allows for the isolation and measurement of losses that occur even when the motor isn't doing any work. These losses include core losses, as well as friction and windage losses. These losses are crucial to understand as they can be influenced by various factors, including magnetic saturation within the motor's core and the specific design of the rotor. The efficiency and overall performance of the motor are impacted by these inherent losses.
The no-load test also has similarities to the way transformers are tested, where the primary focus is on identifying losses at no-load and determining specific equivalent circuit parameters. These parameters help in understanding how the motor will behave under different operating conditions. Furthermore, sophisticated methods like finite element modeling can be utilized to gain a more detailed understanding of the spatial distribution of core losses. This deeper understanding can be valuable in refining motor designs and ensuring reliable performance across a range of operating conditions. While the no-load test is a standard procedure, there are practical considerations. Small motors might be tested with simple load applications, but larger motors often necessitate specialized equipment and procedures for accurate results.
### Exploring the No-Load Test for Core Loss Measurement
1. **Understanding Core Losses**: The no-load test is a cornerstone for identifying core losses, also referred to as iron losses, which are primarily composed of hysteresis and eddy current losses. Notably, these losses are present regardless of the motor's workload, making this test valuable for evaluating motor efficiency in a controlled, unloaded state.
2. **Frequency's Impact**: A key aspect of core losses is their dependency on the operating frequency. Higher frequencies result in greater core losses. This frequency sensitivity needs to be taken into account when interpreting the no-load test data to ensure a meaningful analysis.
3. **Material Matters**: The magnetic properties of the core materials, often electrical steel designed to minimize losses, significantly influence the magnitude of core losses. The choice of these materials directly impacts motor efficiency and lifespan.
4. **Temperature's Role**: Temperature fluctuations can subtly impact core losses due to alterations in the magnetic characteristics of the core materials. For consistent and comparable results, it's critical to maintain a stable temperature during no-load testing.
5. **Voltage's Effect**: The voltage applied during the no-load test also affects the core loss readings. Increased voltage typically leads to higher core losses. It's crucial to rigorously adhere to the prescribed voltage levels during testing to ensure accuracy and avoid biased results.
6. **Wattmeter Precision**: Wattmeters are essential for measuring the power input during the no-load test and calculating core losses. However, it's important to acknowledge that the precision of these measurements can be sensitive to issues like power supply harmonics. This highlights the need for careful calibration of the equipment for reliable data.
7. **Contrasting No-Load and Load Tests**: While both no-load and load tests are valuable, they target different loss components. The no-load test specifically targets core losses, whereas load tests are used to assess copper losses under various load conditions. Recognizing the differences between these tests is crucial for building a holistic understanding of motor efficiency and performance across operating conditions.
8. **Optimization Challenges**: Striving for the lowest possible core losses in motor design can often encounter diminishing returns. While manufacturers continuously push to optimize materials and designs, the incremental cost of achieving further reductions in core losses can become considerable compared to the relative gains in efficiency.
9. **Motor Development Insights**: During the design and prototyping phases of motor development, the no-load test is a frequently used tool. It offers early insights into the performance characteristics of different core materials and design variations, allowing engineers to make informed choices that affect the final motor performance.
10. **Adherence to Industry Standards**: International standards dictate acceptable levels of core losses for different types of motors. Meeting these standards is essential, as exceeding specified core loss limits can lead to higher operating costs and can even disqualify a motor for use in specific applications.
Comprehensive Guide 7 Essential Tests for Electric Motor Performance and Reliability - Locked Rotor Test for Starting Torque Analysis
The locked rotor test is a crucial technique for assessing the starting capabilities of electric motors, primarily three-phase squirrel-cage induction motors. It mimics the extreme condition of a motor attempting to start under a heavy load by holding the rotor stationary while applying a reduced voltage to the stator windings. This allows engineers and technicians to directly evaluate key electrical parameters, including rotor resistance and leakage impedance, that are essential for predicting a motor's starting torque and the current it will draw during startup. Similar to how a short-circuit test is used on transformers, the locked rotor test provides valuable data that helps designers validate their motor designs and ensure quality control.
However, the locked rotor test can be a source of variability in practice. There isn't a standardized approach to performing this test, leading to potential discrepancies in results between different maintenance facilities. This is partly due to equipment limitations and procedural differences. Furthermore, while the test is incredibly valuable, particularly in critical applications like petrochemical processing where reliable startup is paramount, it isn't always a mandatory test. Organizations that don't adhere to more stringent electrical standards may opt to skip it, potentially overlooking a key indicator of motor performance under stressful conditions. For these reasons, understanding the nuances of locked rotor testing is vital for gaining a truly comprehensive picture of motor performance and predicting how it will behave during the challenging process of starting a heavy load.
### Surprising Facts about the Locked Rotor Test for Starting Torque Analysis
1. The locked rotor test essentially forces the motor into a stalled condition by holding its shaft still and applying voltage. This mimics the motor's behavior when it's just starting up against a heavy load and isn't spinning yet. It provides a direct view of the starting torque and current at zero speed.
2. One notable outcome of this test is the massive inrush current—it can spike to several times the motor's normal operating current. This is something that has to be taken into account when designing the motor's electrical supply to avoid tripping circuit breakers.
3. For induction motors, this test reveals a lot about how the rotor is designed. The way the rotor bars are made significantly affects how much starting torque it can produce. So this test is a good check of the rotor's electromagnetic capabilities.
4. The torque created when the rotor is locked is tied to how much the rotor speed lags behind the motor's intended running speed, which is known as slip. Grasping this connection is key to making the best motor design for a certain application to make sure it can start up reliably.
5. Industry organizations like NEMA and IEC give us a roadmap on how to run the locked rotor test properly. Using these guides keeps the results consistent and reliable across different motor types and uses.
6. The amount of voltage applied during the locked rotor test has a big effect on the starting torque. More voltage gives you more torque. But, be careful, too much voltage can damage the motor's insulation. Careful test practices are vital.
7. When using the locked rotor test to judge a motor's performance, it's essential to think about the load the motor is going to drive. Depending on the load, the motor needs different amounts of starting torque. This impacts which motor you choose for the job.
8. Running the motor with voltage and not letting it turn creates a lot of heat since the current is so high. For safety, the test usually doesn't run for very long to avoid overheating and damaging the motor windings.
9. This test can be used to compare the performance of different motor types, like squirrel cage and wound rotor motors. It provides insights into starting torque which informs decision making on which design best suits particular application needs.
10. The locked rotor test reveals a lot more than just the initial torque. It gives a sense of how the motor will handle tough starting conditions. For motors used in things like conveyors or compressors where high starting torque is critical, this kind of information is valuable.
Comprehensive Guide 7 Essential Tests for Electric Motor Performance and Reliability - Load Test to Evaluate Motor Efficiency
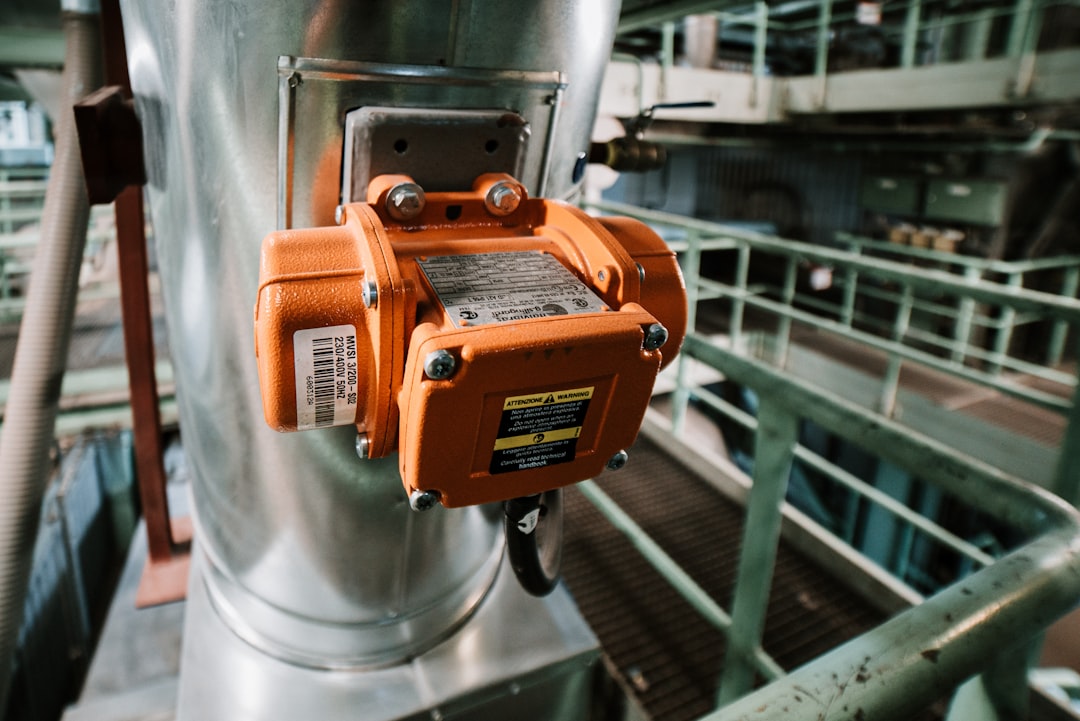
Load testing is a crucial method for evaluating how efficiently an electric motor performs and how reliable it is. This testing helps find problems that might not be apparent during normal operation, potentially improving performance and extending the motor's lifespan. One common approach is using a dynamometer to measure motor performance under a range of controlled loads. The blocked rotor test, on the other hand, simulates the stress of a motor starting under heavy load, which can help determine its starting torque capabilities and its safety under these conditions. By analyzing the power going into and coming out of the motor, we can determine the motor's efficiency. This efficiency is vital for managing energy costs. Regular load tests can also help detect abnormalities that might signify potential issues. This leads to more reliable operation across different industrial uses. Ignoring load testing could lead to unexpected motor failures and costly production stops, so it's vital to include it in routine maintenance and operation plans.
Load testing is a crucial way to understand how well a motor performs and how efficiently it uses energy. By placing the motor under different load conditions, we can see how it reacts and uncover any hidden issues that might lead to failure. A common technique for this is dynamometer testing, where the motor is run under carefully controlled load levels. This gives us insights into how its efficiency changes with the load.
One specific test that mimics difficult operating conditions is the blocked rotor test. In this test, the motor's rotor is kept from spinning, and a reduced voltage is applied to see how it handles a sudden, heavy load. This provides vital information about the motor's starting torque, current, and safety under stress.
Motor efficiency, in simple terms, is the ratio of the power output to the power input. It directly affects energy consumption, and this is a key reason for running load tests. When a motor is in operation, it's vital to conduct tests while it's running under load to get the most accurate view of its performance in terms of power use, speed, and efficiency.
We can also estimate the portion of its full power capability that a motor actually uses through something called the part-load condition. This involves carefully measuring the power being supplied to the motor. Understanding how motors perform at partial loads is important for efficient operation.
Beyond load tests, other tests such as the blocked rotor, no-load, and efficiency tests are part of a more comprehensive evaluation of a motor's health and capabilities. Through consistent testing, we can identify any unusual behavior that suggests a potential issue, ensuring motors remain dependable in demanding industrial settings.
Before diving into more specialized tests, a preliminary check of the motor can be done using relatively simple tools like multimeters. Checking current, voltage, power, and resistance can reveal potential issues, which then may justify further investigations. It's important to note that while these preliminary checks can be helpful, they don't replace the more thorough information gathered through load testing. This type of testing helps us get a complete picture of how the motor is operating and whether it is meeting performance specifications under real-world conditions.
Comprehensive Guide 7 Essential Tests for Electric Motor Performance and Reliability - Vibration Analysis for Mechanical Health Assessment
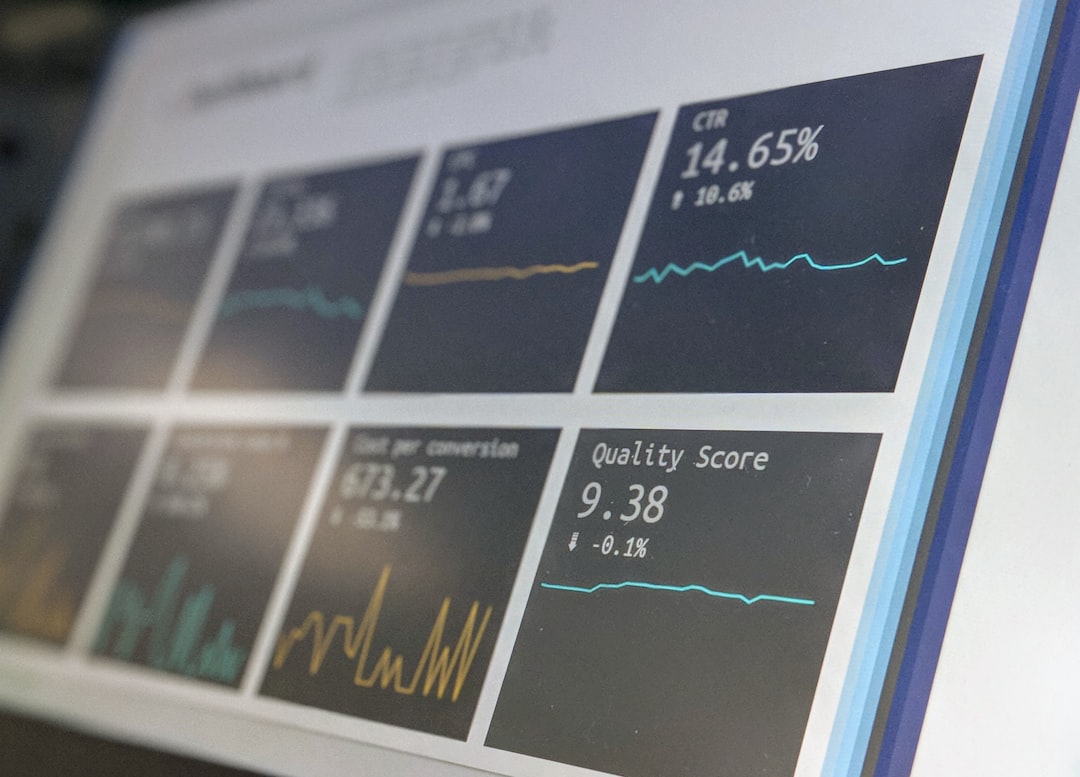
Vibration analysis is a crucial method for evaluating the mechanical condition of electric motors, which is essential for maintaining performance and extending their service life. By continuously tracking vibration levels, engineers can detect early signs of wear and tear, and predict potential problems, such as issues with bearings or misalignment. This allows for proactive maintenance, which improves efficiency by facilitating timely repairs. The method emphasizes the complex relationship between the electrical and mechanical parts of a motor, which highlights the need for a complete understanding of how it behaves in different situations. Although vibration analysis is exceptionally useful, it should be combined with a visual inspection of the motor to ensure a complete picture of its mechanical health and detect any other potential issues.
Vibration analysis is a powerful technique for understanding the mechanical health of electric motors and other machinery. By measuring the vibrations produced during operation, we can uncover early signs of trouble, such as imbalances, misalignments, or wear and tear in bearings, before they lead to major failures. Interestingly, each type of mechanical problem tends to create a unique vibration pattern. For instance, a misaligned motor shaft often generates stronger vibrations along the motor's axis, whereas worn bearings tend to create higher-frequency signals that can even help us pinpoint the precise type of bearing fault.
Sophisticated signal processing methods, like the Fast Fourier Transform (FFT), are used to take raw vibration data from the time domain and convert it into a frequency domain representation. This frequency-based view allows us to easily identify specific vibration frequencies and resonances associated with potential problems. This approach is integral to predictive maintenance programs. These programs help to drastically decrease unplanned downtime. Maintenance actions are then based on the actual condition of the machine rather than on arbitrary schedules or time-based replacements, which are often overly conservative.
The development of portable vibration analysis instruments has revolutionized how we monitor machine health. Now, technicians can diagnose problems right on the factory floor without having to remove equipment from service. This capability greatly improves both operational efficiency and safety.
It's important to consider that vibration patterns are influenced by factors like operating temperature, load levels, and environmental conditions. Therefore, it's not enough to simply measure the vibrations; we need to carefully analyze them within the context of the motor's operational environment to reach reliable conclusions about its mechanical integrity.
Regular vibration monitoring can significantly extend the lifespan of equipment by allowing us to address issues before they become serious. Based on the vibration data, we can schedule repairs and maintenance proactively in a cost-effective manner. This strategy prevents more extensive damage and the expensive repairs that would follow, leading to significant cost savings for companies.
However, we must keep in mind that not all vibrations are inherently problematic. Some machinery vibrates normally as a consequence of its design. This brings the critical need to deeply understand the specific equipment we're monitoring so we can distinguish normal operating vibrations from the telltale signs of a malfunction.
Beyond helping us avoid mechanical failures, vibration analysis can also uncover inefficiencies in energy usage. This opens the door to innovation in motor design and overall system architecture, leading to improved performance and reduced energy consumption. This is particularly beneficial in industries that heavily rely on energy-intensive processes.
The range of vibrations that are deemed acceptable can change dramatically between different kinds of machinery. Thorough understanding of these nuances is key to conducting effective vibration monitoring and timely maintenance actions to maximize the reliability of industrial equipment over the long haul.
Comprehensive Guide 7 Essential Tests for Electric Motor Performance and Reliability - Temperature Rise Test for Thermal Performance
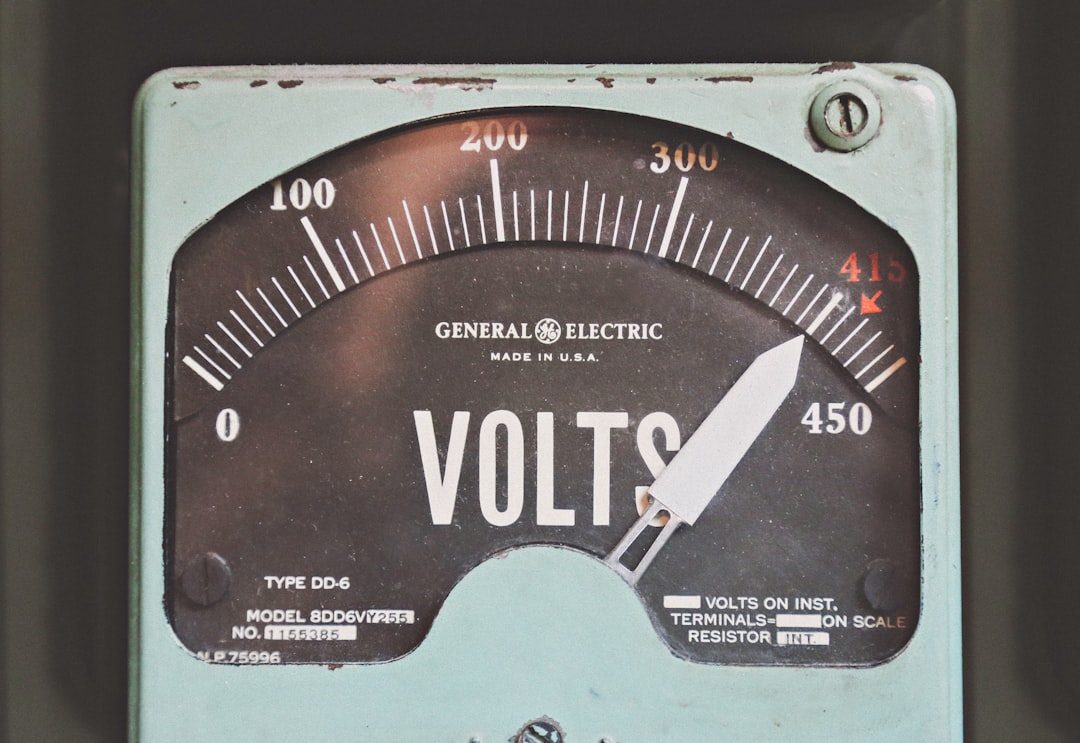
The Temperature Rise Test is a crucial evaluation for understanding how well an electric motor handles heat during operation. It checks if the temperature increase within the motor and its components stays within the safe limits set by the manufacturer. This is especially important because too much heat can hurt the motor's performance, make it less reliable, and even lead to premature failure. The test involves monitoring how the temperature increases, including how it stabilizes in critical parts like the motor's armature. This data helps engineers see how much heat is being generated and how that affects the motor's overall performance. Following industry standards like IEC 60068 helps ensure that the test is done properly. This includes careful planning and clear objectives to get reliable results. It's also vital to keep track of the motor's temperature over time to make sure it stays stable and avoid overheating issues. This is key to making sure the motor stays reliable and lasts a long time in different applications. While the test itself is relatively straightforward, it is foundational to assessing motor reliability.
Temperature rise tests are crucial for determining if an electric motor and its components stay within safe operating temperature limits set by manufacturers. Managing heat effectively is essential for motor efficiency, reliability, and longevity because too much heat can damage performance and cause failures. For example, liquid-cooled motors can generate a significant amount of heat during operation, with temperature rises ranging from 40 to 60°C.
Various tests exist to assess electric motor performance, such as electrical tests for voltage and polarity, mechanical vibration tests, thermal tests for temperature monitoring, and dynamic tests for transient behavior. Thermal resistance is a key factor influencing temperature rise, making heat management strategies crucial for maintaining optimal performance. The IEC 60068 standard provides guidelines for temperature testing, including test preparation, defining specific objectives, and using appropriate equipment for accurate results.
For instance, in transformer temperature rise testing, the low-voltage winding is short-circuited, thermometers are placed at strategic locations, and a voltage is applied until the temperature stabilizes. This approach ensures the transformer meets its thermal limits. It's important to recognize that the stable armature temperature affects motor performance. For example, an increase in armature temperature to 100°C can lead to a rise in terminal resistance and a decrease in magnetic flux density compared to the performance at a temperature of 25°C.
This type of testing isn't just for motors. Electrical switchboards and panels also benefit from temperature testing to pinpoint potential hot spots that could compromise safety and efficiency. Ongoing temperature monitoring and testing are essential for maintaining operational stability, maximizing reliability, and preventing motor and related system overheating. It's fascinating that the specific materials and cooling methods used in a motor's design can significantly impact the temperature rise characteristics. It appears that understanding the interplay of these design factors is critical for engineers to achieve optimal thermal performance, which leads to longer lasting and more reliable electric motors.
Comprehensive Guide 7 Essential Tests for Electric Motor Performance and Reliability - Surge Test to Detect Inter-Turn Short Circuits
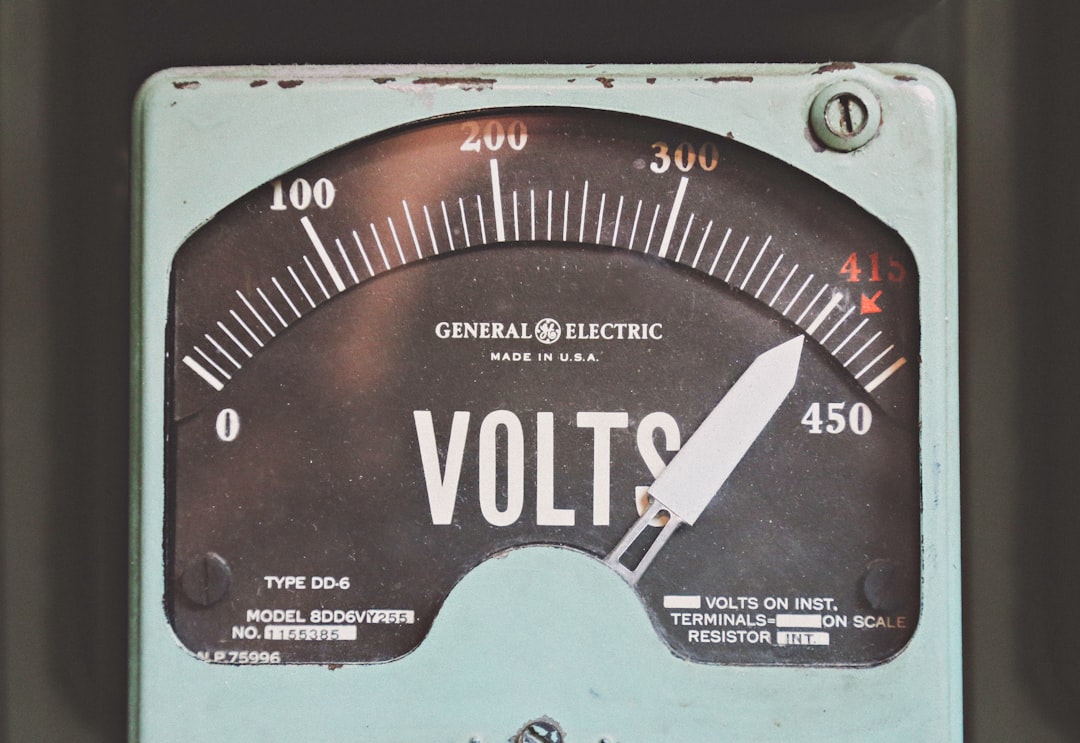
Surge testing is a specialized method primarily used to uncover hidden problems in the windings of electrical equipment, such as motors, generators, and transformers. Its unique value lies in its ability to identify weaknesses in the insulation between individual turns of the windings. This type of insulation failure is a common cause of motor failures. Other things the test can pinpoint include turn-to-turn short circuits, problems between different coils or phases, and overall degradation of the insulation.
Surge tests are especially valuable for pinpointing problems in direct current (DC) motors, helping to identify incorrect internal wiring and potential errors in the number of turns in the windings. Furthermore, the surge test is a proactive measure in a motor maintenance program. It's a good way to predict potential failures and help decide if a repair or a full replacement is the best course of action.
However, the effectiveness of surge testing can be debated amongst experts in motor reliability. Some believe the test results can be difficult to interpret and that a combination of diagnostic techniques provides a better understanding of the motor's true condition. In general, surge tests are best used as part of a broader, comprehensive testing program for motors.
1. The surge test, sometimes referred to as the surge impedance test, utilizes high-frequency voltage pulses to identify hidden inter-turn short circuits within a motor's windings. It's a valuable non-destructive technique that can reveal faults often missed by conventional testing methods.
2. An intriguing aspect of this test is how it leverages the interplay of winding capacitance and inductance. The resulting electrical waveforms can reveal subtle variations that signal insulation breakdown or short circuits, underscoring the importance of understanding a motor's electrical characteristics for accurate diagnosis.
3. While effective, the surge test's susceptibility to environmental factors like temperature and humidity can produce inconsistent results. Controlling these factors during testing is crucial for obtaining reliable and meaningful outcomes.
4. This test can be used on both large and small motors, but the interpretation of results can differ significantly depending on the motor's size. Smaller motors sometimes exhibit unique electrical responses to surges, making experience and knowledge vital for accurately interpreting faults across a range of applications.
5. Unlike insulation resistance tests, which provide a more general overview of winding health, the surge test offers the potential to pinpoint specific inter-turn faults. This localized information can guide more precise repair efforts, saving time and maintenance expenses.
6. Applying high-voltage pulses, often exceeding the motor's normal operating voltage, during a surge test introduces inherent risks. If not performed carefully, it can worsen existing insulation weaknesses or even induce new faults, emphasizing the need for rigorous adherence to testing protocols.
7. It's interesting to consider that some older motor designs may not respond well to the surge test due to limitations in their insulation systems. This can lead to false negatives, highlighting the importance of using a variety of assessment methods for a more comprehensive understanding of a motor's overall condition.
8. The introduction of digital oscilloscopes and advanced data analysis tools has dramatically improved the capability of surge tests. High-resolution waveform analysis can now detect even minor deviations suggestive of developing faults.
9. Surge testing can also be used as an indirect indicator of motor performance, as even minor inter-turn faults can impact efficiency and contribute to overheating. This is of particular concern in high-reliability applications like aerospace or medical devices.
10. It's notable that the surge test serves a dual role: it can act as a diagnostic tool for older motors and a quality control measure during manufacturing. This versatility speaks to its importance for maintaining electric motor performance throughout their operational life cycle.
More Posts from aistructuralreview.com: