Streamlining CAD Workflows A Practical Guide to Opening STEP Files in 2024
Streamlining CAD Workflows A Practical Guide to Opening STEP Files in 2024 - Understanding STEP Files in Modern CAD Workflows
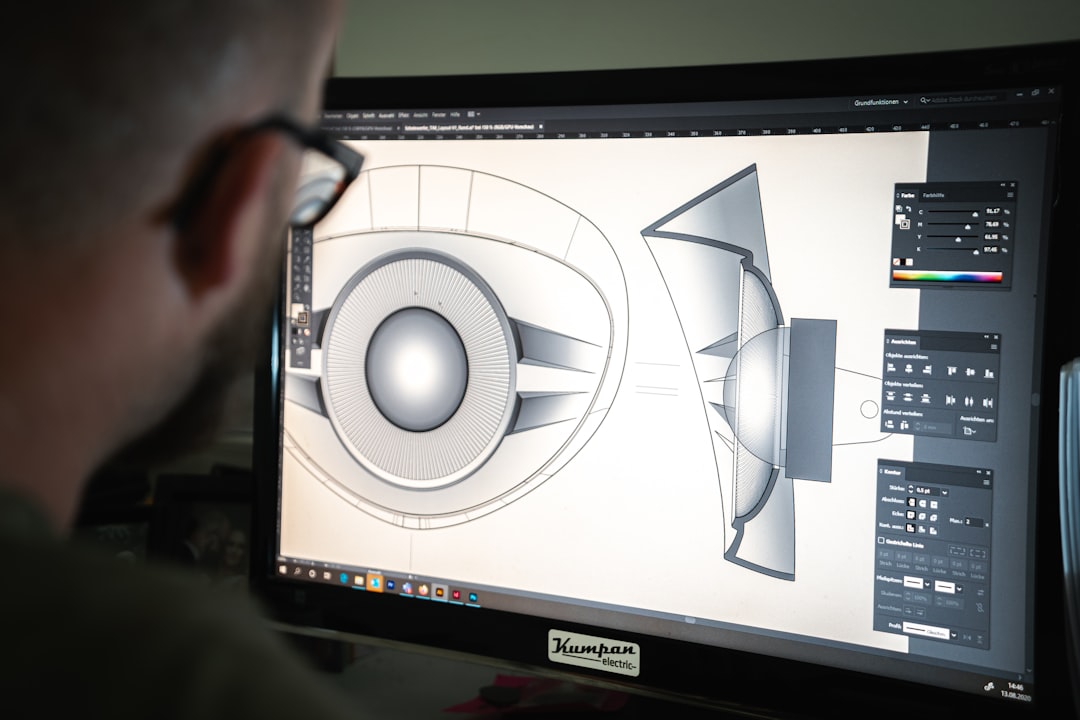
In today's design landscape, understanding STEP files is critical for anyone working with CAD software. They act as a common language, allowing 3D models to be passed between different CAD programs. This is essential when teams use a variety of tools or need to share designs with external collaborators. The format's ability to store detailed geometry and structural information is key to maintaining accuracy when transferring models between systems.
This capability is especially useful in fields like architectural design and 3D printing where precise models are paramount. By using STEP files, professionals can ensure that design intent is accurately conveyed regardless of the CAD system used. However, it's important to acknowledge that successfully utilizing STEP files also involves understanding how to import them properly and manage their data structure. Ensuring the integrity of the model, particularly its features and geometry, is vital to prevent errors in later stages of the workflow. Ultimately, mastering the use of STEP files within a design process can lead to smoother collaborations and a streamlined design workflow. This is especially relevant for individuals and teams wanting to refine and improve their design processes in the coming year.
STEP files, formally defined by the ISO 10303 standard, serve as a bridge for sharing 3D model data between different CAD programs. This standardization is crucial, fostering collaboration across diverse engineering fields. While traditional CAD formats often focus primarily on geometry, STEP files have the capacity to encapsulate a broader range of information—product structure, metadata, and even manufacturing instructions. This broader scope enables a more complete digital representation of a design.
However, the universality of STEP can be a double-edged sword. While many CAD programs support STEP imports, the interpretation and rendering of the data can vary. This variation often leads to inconsistencies and compatibility challenges that engineers must skillfully address. Additionally, while the format supports both solid and surface representations, not all programs fully exploit the advanced capabilities, sometimes resulting in data loss or simplifications of complex designs.
The successful exchange of design data relies on thoughtful export settings when generating STEP files. Unfortunately, overlooking these settings frequently causes issues with scale, orientation, or a loss of the original design intent. Despite these challenges, STEP files offer a distinct advantage in collaborative projects by facilitating version control and tracking changes more effectively than traditional methods. This improved tracking significantly boosts team productivity.
Nevertheless, large and intricate assemblies can lead to voluminous STEP files, making file transfers across slower internet connections an issue. Transitioning from dedicated CAD formats to STEP also presents obstacles. Simplifications during file conversions can lead to inaccuracies, highlighting the need for engineers to comprehend these limitations and adhere to established best practices. Cloud-based CAD solutions are increasingly leveraging STEP files, but this presents a new dimension of responsibility. Engineers need to be conscious of data security and integrity when sharing files via these online platforms.
Finally, the extent to which various software packages support STEP varies considerably. Some offer robust capabilities for handling assembly constraints and annotations, while others provide less comprehensive functionality. Understanding the nuances of different software is crucial for maximizing the benefits of this universal exchange format.
Streamlining CAD Workflows A Practical Guide to Opening STEP Files in 2024 - Compatible Software for Opening STEP Files in 2024
The ability to seamlessly open and utilize STEP files is crucial for streamlining CAD workflows in 2024. Fortunately, several software programs provide this capability, offering a range of features and pricing to suit various users.
Among the options available, GstarCAD 2024 has integrated improved STEP and IGES file import, making it a potentially more convenient tool for those seeking compatibility enhancements. AutoCAD 2024 users can readily import STEP files with a simple command, which can be beneficial for users familiar with this platform. SOLIDWORKS 2024 offers refined tools for integrating STEP geometry, offering greater control over the incorporation of STEP parts into existing assemblies.
For individuals seeking broader options, Autodesk Fusion 360 and FreeCAD are available, representing a blend of commercial and freely available software. However, the successful integration of STEP files can sometimes be unpredictable depending on the software used, with varying levels of accuracy and feature retention. It's important to consider each application's limitations and capabilities when selecting a program for handling STEP data, ensuring the intended design integrity is maintained throughout the process.
Exploring the landscape of STEP file compatibility in 2024 reveals a mix of advancements and lingering challenges. While the STEP format's universality remains a powerful tool for interoperability, its implementation varies across different CAD programs.
One notable observation is the variability in file sizes. Simple designs might be manageable, but complex assemblies can easily become unwieldy, creating issues with both storage and transfer times. Interestingly, some software now employs compression specifically designed for STEP files, potentially decreasing file sizes by a significant margin. This could offer considerable efficiency improvements for large projects, particularly across slower network connections.
However, the way CAD software handles the assembly structure within a STEP file remains inconsistent. It's not uncommon to find that certain applications fail to accurately interpret the relationships between parts, potentially introducing errors during the assembly process. This emphasizes the need for careful verification after importing STEP files.
Further, the capacity of STEP files to store metadata, which could contain crucial information about material properties and manufacturing processes, is often underutilized. This is a missed opportunity, as maintaining and leveraging this metadata could streamline the design to manufacturing process.
On a positive note, the enhanced compatibility offered by STEP has encouraged some organizations to adopt it as a standard output across their CAD systems. This creates a uniform output environment, allowing for smooth workflow transitions between various CAD software within a company and reducing the learning curve for engineers switching tools. Version control also benefits from the use of STEP. Managing different iterations of a design and ensuring consistency across a team becomes more straightforward, minimizing confusion in collaborative projects.
However, despite the format's ability to represent geometric tolerances, the interpretation of these tolerances across different systems often varies. This can create subtle inconsistencies in the geometry of complex parts, underscoring the importance of verifying them after importing.
Specialized tools aimed at enhancing interoperability, especially those focused on STEP, could play a more central role in mitigating some of these difficulties. However, their use seems underutilized in many engineering teams. Moreover, there's a growing trend of incorporating STEP files with Augmented Reality (AR) platforms. This opens up new avenues for visualising and reviewing designs, potentially providing a more intuitive experience for both designers and stakeholders.
Despite the potential benefits, certain issues persist. The export settings in the original CAD software still matter. Many engineers aren't sufficiently aware of the importance of these settings, which can lead to inaccuracies in scaling or orientation after import. It's evident that these settings require careful attention to avoid wasting time on post-import corrections.
In summary, while STEP files remain an essential tool in modern CAD workflows, they're not a panacea. Engineers must navigate their limitations and quirks to maximize their benefits fully. Hopefully, as software development continues, these challenges will be gradually overcome, fostering even greater interoperability in future workflows.
Streamlining CAD Workflows A Practical Guide to Opening STEP Files in 2024 - Step-by-Step Guide to Importing STEP Files in AutoCAD 2024
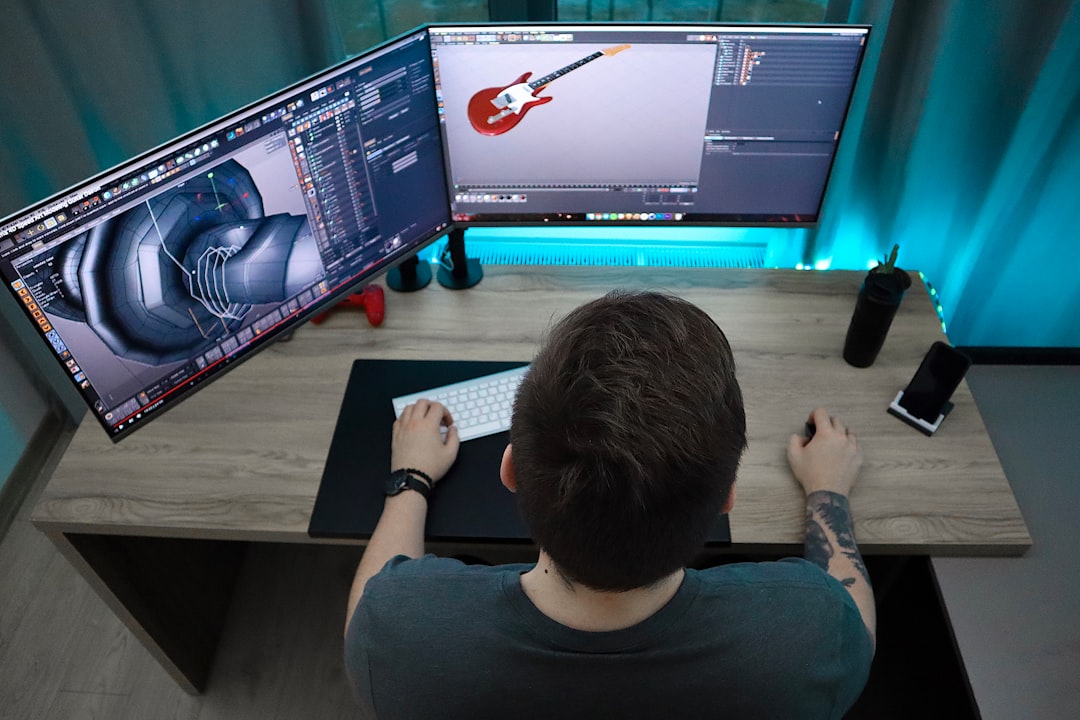
Importing STEP files into AutoCAD 2024 is a straightforward process that begins by entering "IMPORT" in the command line interface. From there, you browse to the file's location and select it. AutoCAD will then signal that the import is in progress, followed by a confirmation message upon completion. You can choose between AutoCAD's legacy import method or a more advanced 3D interconnect engine, which can affect how the imported object is displayed.
Keep in mind that imported STEP files might appear differently from native AutoCAD objects—often with a unique color. The way they integrate into the software environment can be a point of concern, leading to unexpected behavior sometimes. As a result, it's important to carefully consider the import settings and pay attention during the import process itself to ensure that the imported parts behave as expected within your larger design.
While STEP files are intended to provide a common ground for CAD data exchange, it's important to be aware that how they function can vary slightly between CAD programs. This means that it's critical to develop a disciplined approach when incorporating STEP files into AutoCAD 2024 designs to prevent future complications.
1. It's easy to assume that every CAD program can flawlessly handle STEP files, but that's not always the case. I've seen that how a program interprets a STEP file, particularly for complex designs, can lead to unexpected data loss or misrepresentation of the original model. This makes a thorough inspection after importing absolutely necessary.
2. One aspect I found intriguing is how some CAD applications don't always handle the relationships between parts in a multibody STEP file correctly. The result can be parts that are no longer connected as intended in the initial model. It emphasizes the need for immediately assessing the structural integrity after importing.
3. It's surprising how often the ability to store essential metadata about the design (like materials and manufacturing instructions) within a STEP file is overlooked. If engineers embraced using this feature more frequently, it could smooth the transition from the design phase to manufacturing, creating a more efficient process.
4. Recently, I've encountered CAD software that includes compression specifically optimized for STEP files. It's fascinating how they can reduce the size of large files without sacrificing accuracy. This innovation could provide a significant performance boost for projects involving intricate designs, particularly when working with slower network connections.
5. I've discovered that engineers often don't fully appreciate the importance of the export settings when creating a STEP file in the first place. It's clear that neglecting these settings can cause major issues with the scaling and orientation of the model after importing, which can necessitate tedious corrections.
6. While STEP supports geometric tolerances, I've noticed that the way CAD programs interpret these tolerances varies widely. These variations can subtly change the geometry of complicated parts, leading to problems down the line. As a result, engineers must scrutinize the imported design very carefully.
7. Compared to traditional methods, STEP files intrinsically facilitate version control much more effectively. With a standardized file format, managing iterations of a design and keeping consistency amongst team members is significantly easier, thus minimizing confusion in collaborative projects.
8. Interestingly, while specialized tools exist that improve the compatibility and interoperability of STEP files, their adoption among engineering teams appears minimal. These tools could be very useful in bridging the compatibility gaps between different CAD applications and lead to smoother workflows.
9. As STEP files become more prevalent in cloud-based CAD workflows, concerns about the security and integrity of design data arise. It's crucial for engineers to be cautious and safeguard their intellectual property since file sharing vulnerabilities could pose risks to sensitive design information.
10. The increasing use of STEP files with AR platforms is a really interesting development. It offers new ways to visualize and review designs, creating a more intuitive way for both designers and non-technical stakeholders to understand complex geometries. This could lead to better design decisions.
Streamlining CAD Workflows A Practical Guide to Opening STEP Files in 2024 - Optimizing STEP File Handling in SolidWorks
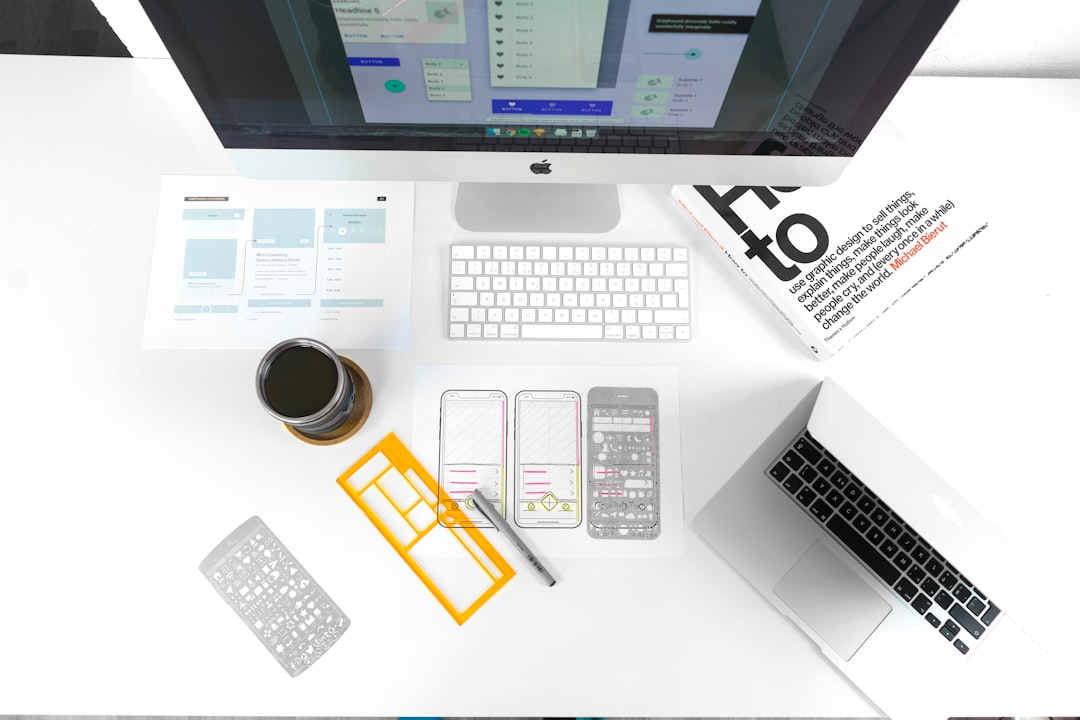
Effectively managing STEP files within SolidWorks is crucial for optimizing CAD workflows. SolidWorks offers a choice between two import methods: the standard import engine and the more advanced 3D Interconnect. Each approach has its own strengths, enabling users to balance import speed and model fidelity based on their project's demands. SolidWorks 2024 has added features like the ability to selectively choose parts to import from complex assemblies, thereby streamlining the entire process.
SolidWorks users can further refine their workflows by leveraging features like the option to load components in a lightweight mode, which can significantly reduce load times, especially when dealing with large assemblies. Handling complex imported geometry efficiently sometimes requires simplification techniques, which can help mitigate potential performance bottlenecks. However, even with these newer capabilities, managing the import of STEP files can still lead to performance issues if not handled carefully. Understanding and utilizing these optimization techniques remains vital for ensuring a smooth and efficient CAD experience.
STEP files continue to be the go-to for sharing designs across different CAD programs, even as CAD software improves its ability to work together. SolidWorks, a popular CAD platform, offers two ways to handle these files: the older Traditional Import Engine and the newer 3D Interconnect. Choosing the right one depends on what you need from the STEP file—fast loading or perfect detail. SolidWorks 2024 has some new features for importing STEP files, making things smoother for users. For instance, you can now pick and choose which parts of complex assemblies to bring in, which is helpful for simplifying large files.
One thing you can do to speed things up is to use the "automatically load components lightweight" option when you import STEP files. This can save a lot of time, especially when dealing with big assemblies. 3D Interconnect, on the other hand, can keep some helpful information intact, like reference planes and user-defined features, which can be beneficial when you need to keep the original design intent. While STEP files can be very helpful, they can also make your computer slow if the geometry is too complex. Techniques for simplifying geometry before importing can be handy in these cases.
Finding solutions to problems you encounter while using STEP files isn't always easy. Many people find troubleshooting the slow loading of complex designs cumbersome, and this can discourage some from even trying to use optimizations. A methodical approach to dealing with STEP files—following a series of steps outlined in user guides—can help refine the import process.
Using metadata more can be advantageous as well. It's surprising how much information can be included with STEP files, like material properties and manufacturing steps, yet many users don't fully use it. The proper use of this feature could be a great benefit for streamlining collaboration. It's also interesting how recent updates to SolidWorks are using smarter compression methods that can reduce file sizes without sacrificing details. Large STEP files can slow down file transfers and storage, so this change is quite helpful.
However, the interpretation of STEP files can be inconsistent between different CAD platforms. Part connections or relationships defined in the STEP file don't always translate correctly. It's important to have a good understanding of how different CAD systems handle STEP files, and that it's essential to carefully review imported models to catch potential problems. As with any type of file sharing, there's also the risk of losing some data during the process. Carefully selecting which software is used for the send and receive can minimize that risk.
Design iterations are also a lot easier to manage using STEP files because they track changes, which can enhance collaboration. But it's important to be disciplined with your version control to keep everyone in sync. Tolerances can be stored in a STEP file, but again, it's not universally interpreted the same way between different CAD applications. It's another area that needs to be carefully validated during model checks. It's essential that engineers remember that the settings you choose when exporting a file in the original CAD platform can have a big impact on how a STEP file will behave in SolidWorks. Poorly configured export settings can lead to problems with scaling and orientation which can result in extra work after import.
One interesting development is how engineers are starting to incorporate STEP files with augmented reality (AR) applications. This is a growing trend that can allow both engineers and clients to examine designs in a 3D interactive space. It could lead to a more streamlined workflow with faster feedback loops and quicker decision making. In essence, while STEP is incredibly useful for sharing designs between different platforms, there are limitations. It's still a relatively young format, and the development of tools aimed at making it even more compatible, streamlined, and widely understood has room for further advancement. Hopefully, in the coming years, engineers will be able to utilize it with even greater effectiveness.
Streamlining CAD Workflows A Practical Guide to Opening STEP Files in 2024 - Common Challenges and Troubleshooting STEP File Imports
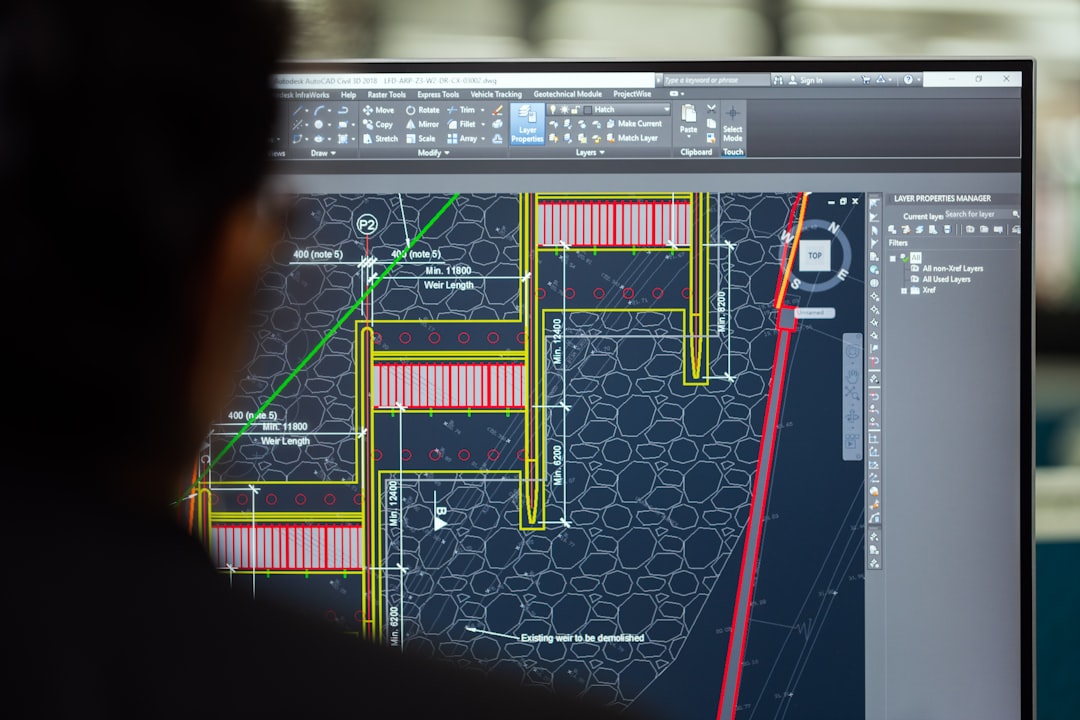
Working with STEP files, especially when dealing with intricate designs and large assemblies, can be challenging. Engineers often face issues like sluggish import times, lost connections between parts within the assembly, and difficulties preserving essential design information, such as material types and manufacturing instructions. To navigate these challenges, leverage the capabilities provided by CAD software. Features like selectively importing components or using lightweight load options can help manage performance issues. Moreover, meticulous attention to the settings used when creating the STEP file in the initial CAD program is crucial. Neglecting these settings can lead to imported models with scaling or orientation errors. By employing a systematic approach to resolving import problems, you can streamline your workflow and gain a greater understanding of how best to handle STEP files.
The flexibility built into STEP files, while intended for broad compatibility, can also introduce challenges during import. Differences in how various CAD systems interpret the data sometimes lead to unexpected inconsistencies. Careful scrutiny during the import process and a thorough post-import inspection are crucial for catching discrepancies that might otherwise go unnoticed.
The ability to embed metadata within STEP files, such as material properties and manufacturing instructions, is often underutilized. Taking full advantage of this capability creates a powerful link between design and manufacturing, potentially creating significant efficiency gains in the overall process.
While STEP supports the inclusion of geometric tolerances, the interpretation of these tolerances varies across different CAD programs. This lack of standardization can cause errors in the final models, underscoring the importance of validating tolerances after importing a STEP file.
Compression methods specifically optimized for STEP files can significantly reduce file size without sacrificing accuracy. This is a helpful development, especially when dealing with large assemblies that might strain network speeds during transfers.
The way different CAD platforms handle the relationships between parts within multibody STEP files isn't always consistent. Parts that were once connected in the original model might lose their connections during the import, emphasizing the importance of confirming the assembly structure after importing.
Engineers sometimes overlook the importance of the export settings when creating a STEP file. If not configured correctly, these settings can lead to problems with scaling and orientation after importing, which can necessitate additional, avoidable rework.
The growing popularity of cloud-based CAD solutions has both advantages and drawbacks when it comes to STEP file handling. Collaboration becomes seamless in many cases, but engineers need to be wary of potential risks to data security, especially when sharing sensitive files online.
While there are dedicated tools designed to improve interoperability and the handling of STEP files, they aren't always used widely. If applied more often, they could help to minimize compatibility issues between different CAD systems, streamlining design workflows and reducing the frustration often associated with file conversions.
The increasing integration of STEP files with AR platforms represents a notable advancement in how engineers visualize and review designs. AR allows engineers and stakeholders to interact with 3D models in real-time, potentially leading to more informed decisions throughout the design process.
Given that different CAD programs handle STEP files in varying ways, understanding each platform's unique capabilities is essential. This is particularly relevant when it comes to assembly constraints, as unexpected behaviors like their loss can create issues further down the line. Recognizing these software-specific idiosyncrasies can help prevent costly errors.
Streamlining CAD Workflows A Practical Guide to Opening STEP Files in 2024 - Leveraging Cloud Technologies for Enhanced STEP File Management
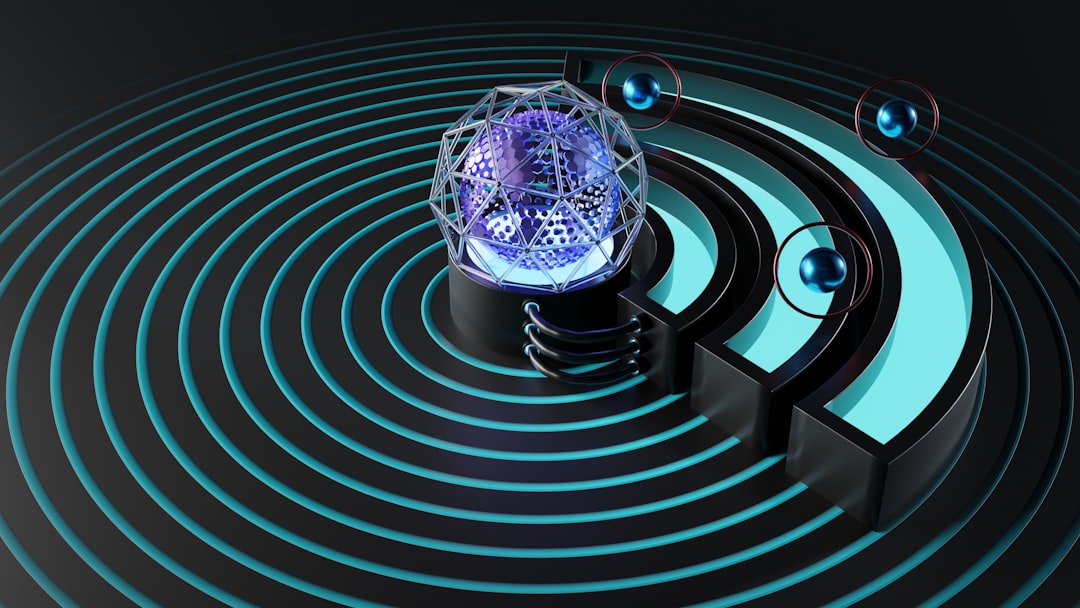
Cloud technologies offer new ways to handle STEP files, providing both benefits and new challenges to consider. Cloud-based CAD systems can make it easier for teams spread across different locations to collaborate on designs, using various software. This accessibility can improve efficiency. However, relying on cloud services for sensitive design data does introduce potential security and data integrity risks that must be thoroughly evaluated and managed.
Cloud environments can also streamline tasks like tracking design changes through version control, helping maintain consistency and reducing confusion in collaborative projects. Yet, it's essential to recognize that how different software applications interpret STEP files can still vary. This potential for inconsistency needs to be taken into account as CAD workflows adapt to cloud solutions. Finding the right balance between leveraging the flexibility of cloud environments and ensuring design accuracy requires careful consideration and a nuanced approach to implementation. Effectively managing STEP files in the cloud demands that teams be both aware of the opportunities and potential pitfalls in order to safeguard design integrity and intent.
Storing and working with STEP files in cloud environments offers several potential upsides, including making them accessible to teams across different locations for real-time collaboration and editing. This approach could potentially accelerate design cycles due to the immediate availability of the latest design iterations. Cloud-based solutions often come with built-in version control systems for STEP files. This can be quite helpful in collaborative settings as it enables everyone to see changes easily and, if needed, revert to older versions. However, it's also important to acknowledge that relying on cloud services introduces questions about data security. It's important to ensure that sensitive design details are not exposed due to improper security protocols.
One of the intriguing aspects of cloud-based CAD is that many platforms utilize clever compression techniques specifically for STEP files. This can greatly reduce the size of files, especially the large ones common in complex assemblies, leading to faster upload and download speeds, even over less-than-ideal internet connections. I find it interesting that cloud platforms seem to be facilitating the better use of metadata within STEP files. There's the possibility to store a greater variety of supplementary data, such as material specifications or manufacturing instructions, directly within the files. This closer linking of the design and manufacturing process could improve efficiency.
While cloud-based solutions can undoubtedly streamline various aspects of the workflow, it's important to remember that they don't resolve all the interoperability challenges inherent in STEP files. There's still a possibility that different cloud platforms will process STEP file data in slightly different ways, potentially leading to discrepancies or unintentional changes that weren't present in the original design. A few cloud services are starting to incorporate AR features for visualizing STEP files. This creates possibilities for exploring 3D models in a real-world context, which could be a major help in explaining the designs to both engineers and non-engineering stakeholders, potentially leading to more informed design decisions.
It's worth being cautious about performance. When dealing with very complex STEP files, some cloud platforms can experience lags in importing and rendering these files. The potential for performance issues is something to keep in mind during design and implementation phases. I think this is an area that could benefit from further innovation. Additionally, seamlessly integrating STEP files with project management tools is becoming more common on these platforms. The closer integration could potentially lead to enhanced tracking of timelines, tasks, and team responsibilities, further improving workflow management.
Finally, I'm intrigued by the possibility for automation using cloud technology in STEP file handling. For instance, it could become standard practice to have error checking or compliance verification happen automatically during file imports. These kinds of automated checks could substantially reduce the need for manual review and inspection, thus enhancing the efficiency of the design process. These automated checks could help to improve data integrity. However, it is important to remember that the success of automation heavily relies on the accuracy of these programs.
More Posts from aistructuralreview.com: