Engineering Strain Formula A Cornerstone in Structural Analysis and Material Testing
Engineering Strain Formula A Cornerstone in Structural Analysis and Material Testing - Understanding the Engineering Strain Formula
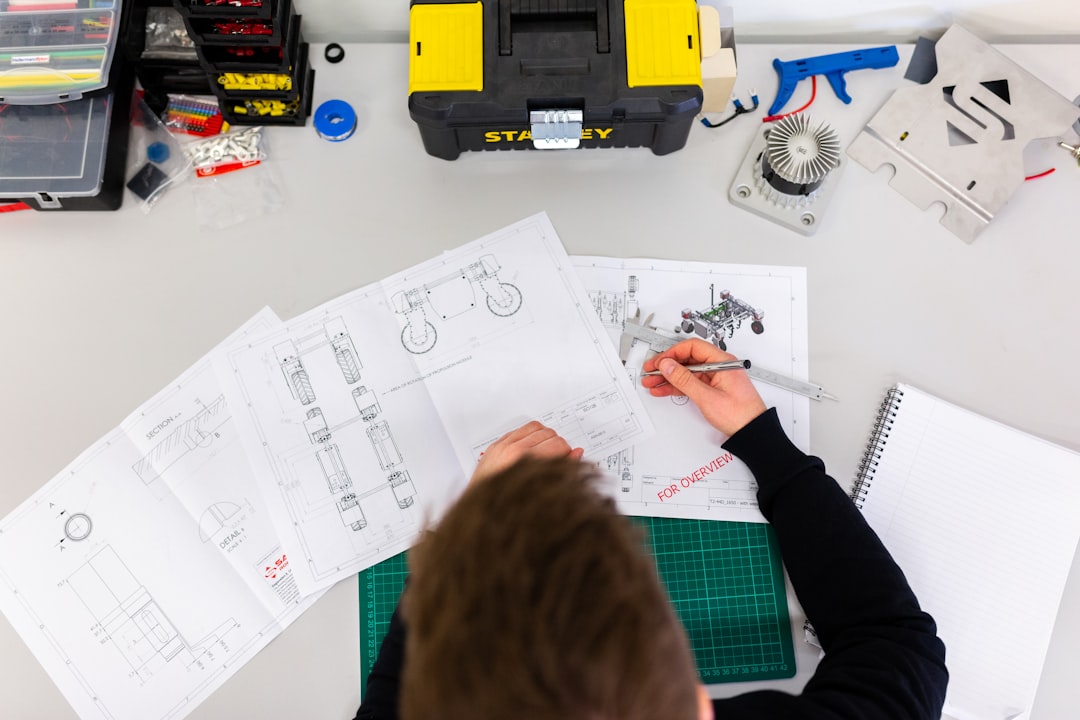
Understanding the engineering strain formula is essential for effectively analyzing materials under stress. This formula provides a quantitative measure of deformation, expressing it as the ratio of the change in dimension to the original dimension. However, while engineering strain is a valuable tool for initial analysis, it can become inaccurate in situations of significant deformation, which necessitates the use of true strain for greater precision. The fundamental relationship between stress and strain, as revealed by the engineering strain formula, serves as a cornerstone for evaluating the behavior of materials under stress. It allows engineers to gain insights into a material's performance and, subsequently, make informed decisions about the safety and durability of structures. The engineering strain formula, in essence, provides a critical lens through which we can understand and predict the behavior of materials under load.
The engineering strain formula, a core concept in material science and structural analysis, is simple enough to grasp: change in length divided by original length. Yet, its implications are surprisingly profound. This formula reveals how materials react to external forces, providing crucial insights into their elastic and plastic properties. While straightforward in principle, the nuances of strain reveal themselves in various forms, depending on the type of applied force and the material itself. For instance, normal strain occurs under axial forces, while shear strain arises from forces parallel to a surface. Recognizing these different types allows us to better predict the potential failure points in a structure, enabling the design of safer and more efficient constructions.
However, the application of strain analysis is not always straightforward. For instance, the choice of gauge length in strain measurement plays a significant role. While a longer gauge length provides an average of the strain across a larger area, shorter lengths offer a more detailed insight into localized strain phenomena. Additionally, strain analysis becomes even more complex when dealing with materials that exhibit viscoelastic behavior. In such materials, strain becomes dependent on the rate of loading and the duration of the applied force, challenging predictions for long-term structural integrity.
Furthermore, it's crucial to account for the influence of temperature variations, which can induce thermal strain in materials. This factor plays a critical role in design considerations, particularly in applications exposed to extreme temperature fluctuations. History provides valuable lessons in the significance of strain analysis. The collapse of the Tacoma Narrows Bridge serves as a stark reminder of the importance of understanding dynamic loading conditions and avoiding resonant frequencies, which can significantly amplify strain.
Finally, understanding that the relationship between stress and strain is not always linear, especially when dealing with materials that experience plastic deformation, is crucial for accurate modeling and analysis. This non-linear behavior adds another layer of complexity to the already intricate world of strain analysis, further emphasizing the ongoing need for robust research and understanding in this crucial field.
Engineering Strain Formula A Cornerstone in Structural Analysis and Material Testing - Applications in Structural Analysis and Design
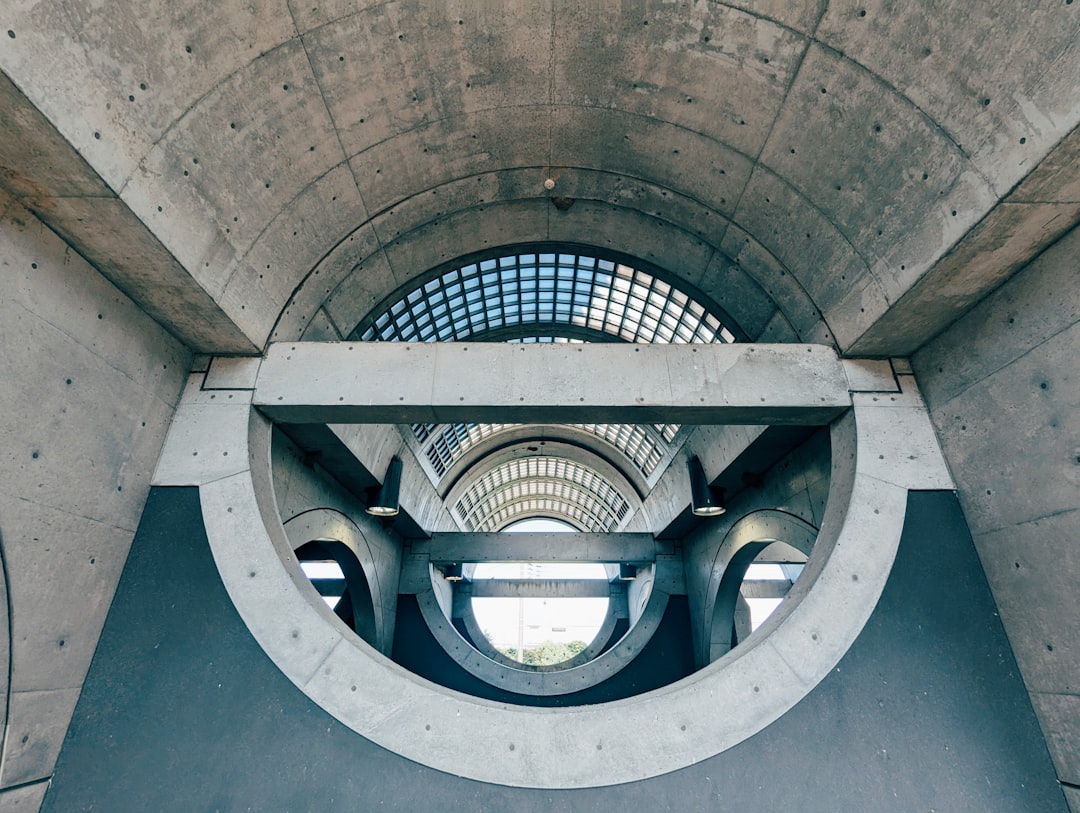
The ability to predict how structures will behave under stress is a cornerstone of safe and effective design. The concept of strain, a measure of deformation, plays a crucial role in this analysis. Understanding how strain develops within a material under different loads allows engineers to evaluate its performance and predict its longevity.
Stress-strain curves, which illustrate the relationship between these two concepts, are especially important for analyzing material fatigue, which is the gradual weakening of materials due to repeated loading. Knowing how a material will behave under fatigue conditions is vital for designing structures that can withstand the demands of their intended use.
Furthermore, structural analysis requires consideration of dynamic loads, such as vibrations or impacts. These forces can significantly influence how a structure behaves and requires precise modeling to ensure the safety of the design. It's also essential to account for external factors, such as temperature fluctuations, which can induce strain in materials and influence their performance over time.
In conclusion, understanding the principles of strain and stress is paramount in structural analysis and design. These fundamental concepts allow engineers to predict material behavior, assess structural integrity, and ensure the safe and efficient construction of a wide range of structures.
The concept of strain extends beyond simple linear deformation. Volumetric strain, for instance, quantifies the change in volume relative to the initial volume of a material. This becomes critical in situations involving compressible materials or fluid mechanics. Understanding strain doesn't only predict failure points in structural design but also allows engineers to assess a structure's overall functionality. This involves evaluating deflections and vibrations, which, while not leading to outright failure, can negatively impact a structure's usability and user comfort.
The engineering strain formula acts as a foundation for more sophisticated analyses, such as finite element analysis (FEA). FEA relies on strain calculations to simulate a structure's response to various loads, creating detailed insights that streamline the design process. However, historical structures often exhibit unexpected behavior, attributable to strain factors not fully considered during design. The collapse of ancient Roman aqueducts provides a stark example, demonstrating the need for meticulous strain analysis to account for both static and dynamic environmental influences.
Strain gauges are instrumental in measuring deformation, employing the principle of electrical resistance change. This technology allows for real-time monitoring of structural integrity, enabling the assessment of health and safety in existing constructions, particularly in critical infrastructure. The nonlinear relationship between stress and strain, most apparent in metals at high temperatures or composites subjected to complex loading, can result in unexpected structural behavior. This phenomenon challenges traditional design assumptions that rely on linear models.
Advanced algorithms and machine learning are being harnessed to predict strain in intricate structures, leveraging massive datasets for improved modeling. This technological advancement enables predictive maintenance strategies to prevent catastrophic failures. Strain-induced phase transformations in specific materials, such as shape memory alloys, introduce exciting applications in actuation and sensing technologies, expanding the scope of traditional structural analysis.
Engineers often design for the worst-case scenario, encompassing the strain under multiple simultaneous load conditions. This approach ensures that structures can withstand not only static weights but also dynamic forces like earthquakes or wind loads. The theoretical understanding of strain and stress dates back to pioneering work by engineers like Galileo and Hooke, but it continues to evolve. Modern applications now incorporate quantum mechanics concepts to understand materials at the atomic level, leading to more accurate predictions of structural performance.
Engineering Strain Formula A Cornerstone in Structural Analysis and Material Testing - Material Testing Methodologies Using Strain Measurements
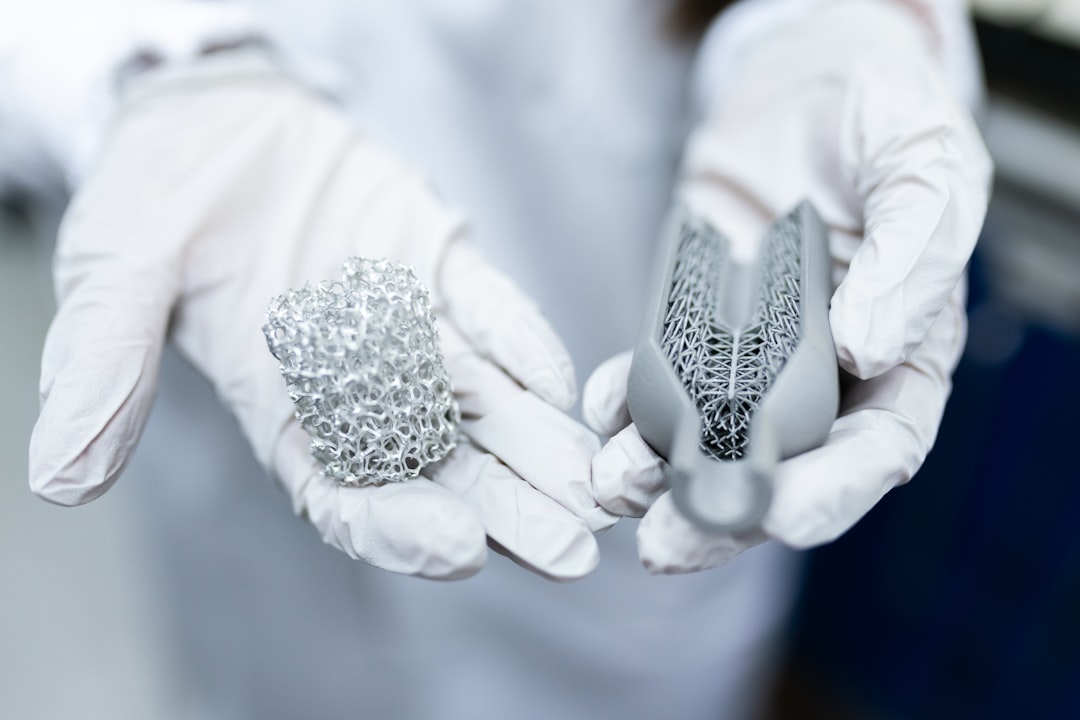
Strain measurement methodologies are becoming more sophisticated as engineers seek to precisely evaluate materials under diverse loading conditions. Current mechanical testing methods often lack standardized procedures and fall short in clearly defining measurement uncertainties, increasing the importance of accurate strain measurement. New advancements, like digital image correlation (DIC) and enhanced extensometer techniques, are revolutionizing strain analysis by offering full-field strain data, revealing insights previously out of reach. These methodologies are also being integrated into structural health monitoring systems, improving our ability to assess deformation and pinpoint potential problems in real-time. The growing complexity of materials and their responses to stress demands a robust approach to strain measurement to ensure the safety and reliability of engineering design and analysis.
While the engineering strain formula provides a foundation for understanding material behavior, the real world throws in numerous curveballs. The way strain manifests itself in different situations is often more complex than simple calculations might suggest.
New technologies are providing a more complete picture of how materials deform. Digital image correlation (DIC) allows us to see strain patterns across large areas in real-time, offering a much broader view than traditional point measurements with strain gauges. Techniques like Moire interferometry can even achieve nanometer-scale precision, revealing intricate details that were previously hidden.
However, many materials are not as well-behaved as we might hope. Their elastic behavior can be nonlinear, meaning the relationship between stress and strain isn't always predictable. This adds complexity, especially when working with large-scale structures. And some materials, like polymers, are strain-rate sensitive, meaning their behavior depends on how quickly the load is applied. This is a crucial factor to consider in dynamic environments like aerospace or automotive applications.
Then we have to factor in things like temperature changes, which can induce substantial thermal strain in materials. This has to be considered when designing for extreme environments. And viscoelastic materials, like rubber, exhibit time-dependent behavior – their strain response can change over time.
Even the geometry of a structure can impact strain. Notches or holes can act as strain concentrators, leading to localized increases in stress that could lead to failure.
We are exploring new ways to tackle these complexities. Machine learning algorithms can be used to analyze strain data from different sources, revealing patterns that might be missed by traditional methods. This could significantly improve structural integrity assessments.
Understanding hysteresis is also essential. This is the phenomenon where materials don't return to their original state after cyclic loading, leading to energy loss over time. This is particularly important in fatigue analysis, where we are concerned with a structure's longevity.
Finally, different materials have distinct thresholds for elastic and plastic deformation. Understanding these thresholds is key to selecting the right materials for a job and predicting failure points.
While the engineering strain formula might seem straightforward, it's a gateway to a fascinating world of complex material behavior. As engineers, we constantly strive to better understand this intricate dance between stress and strain to design safer and more durable structures.
Engineering Strain Formula A Cornerstone in Structural Analysis and Material Testing - Relationship Between Stress and Strain in Engineering
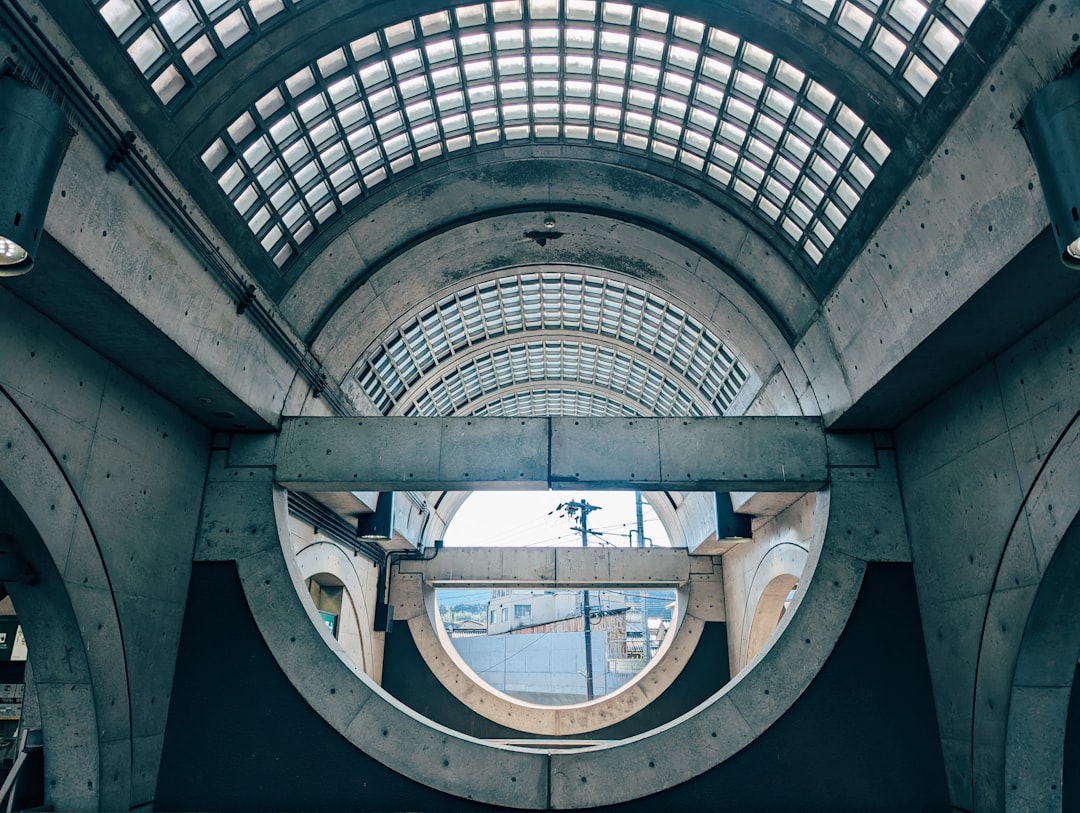
The relationship between stress and strain lies at the heart of understanding how materials behave under load in engineering. Stress, essentially the internal force acting on a material per unit area, interacts with strain, which quantifies how much the material deforms in response to this stress. This intricate dance between stress and strain is often represented graphically by stress-strain curves. These curves not only reveal key material properties like Young's modulus, indicating the material's stiffness, and yield strength, the point where permanent deformation starts, but also showcase the nuances of material behavior.
This relationship between stress and strain becomes increasingly complex in the nonlinear region, where the material undergoes permanent deformation. Recognizing that materials exhibit unique responses to stress is vital for accurate structural analysis and design. Further complicating the picture, engineers need to consider factors like strain rate sensitivity, meaning how quickly a load is applied influences the material's response, and thermal strain, which arises due to temperature fluctuations.
Ultimately, a deep understanding of the relationship between stress and strain is critical for engineers to predict how a structure will perform and to ensure the safety of all engineering applications.
The relationship between stress and strain, while seemingly straightforward, reveals a complex interplay of forces and deformation within materials. Stress represents the internal resistance of a material to an applied force, while strain quantifies the resulting deformation. This duality is fundamental to engineering mechanics, but it's often overlooked that the microscopic structure of a material can significantly influence both stress and strain.
While elastic materials exhibit a linear relationship between stress and strain, this linearity breaks down as materials yield and transition into the plastic phase. Identifying this critical point is essential for accurately predicting failure in engineering applications.
Furthermore, the rate at which a load is applied can dramatically alter material behavior. Some polymers, for example, display significant strain changes based on strain rate, presenting challenges in environments subject to rapid loading.
Temperature fluctuations must also be accounted for, as they can induce thermal strain within materials, impacting overall stress. Neglecting this factor can lead to inaccurate predictions of a material's performance under varying temperatures.
Beyond material choice, the geometric features of structural components play a significant role in strain distribution. Notches or holes, for instance, can concentrate stress, increasing failure risk if not properly factored into engineering calculations.
The complexities only deepen when considering viscoelastic materials, which exhibit time-dependent strain responses influenced by the duration of applied loads. This behavior makes predicting long-term structural integrity more challenging.
In addition, materials under multi-axial loading conditions experience intricate stress states. Accurately understanding how different stress components interact is crucial for precise strain analysis in structural applications.
Cyclic loading can lead to hysteresis, where materials do not return to their original state after unloading. This phenomenon is especially important in fatigue testing, influencing the long-term longevity of materials.
Fortunately, advancements in measurement techniques, such as digital image correlation (DIC), have revolutionized strain analysis. This technology enables real-time, full-field analysis, providing a more comprehensive understanding of strain distributions than traditional point measurements.
At high temperatures, metals often display pronounced non-linear stress-strain responses, complicating thermal management in many applications. This necessitates advanced modeling techniques to accurately predict material behavior under these conditions.
In conclusion, while the engineering strain formula provides a foundation for understanding material behavior, the reality of strain is much more intricate and challenging to fully predict. This ongoing exploration of the complex interplay between stress and strain continues to drive innovation in materials science and engineering design.
Engineering Strain Formula A Cornerstone in Structural Analysis and Material Testing - Fatigue Analysis and Stress-Strain Curves
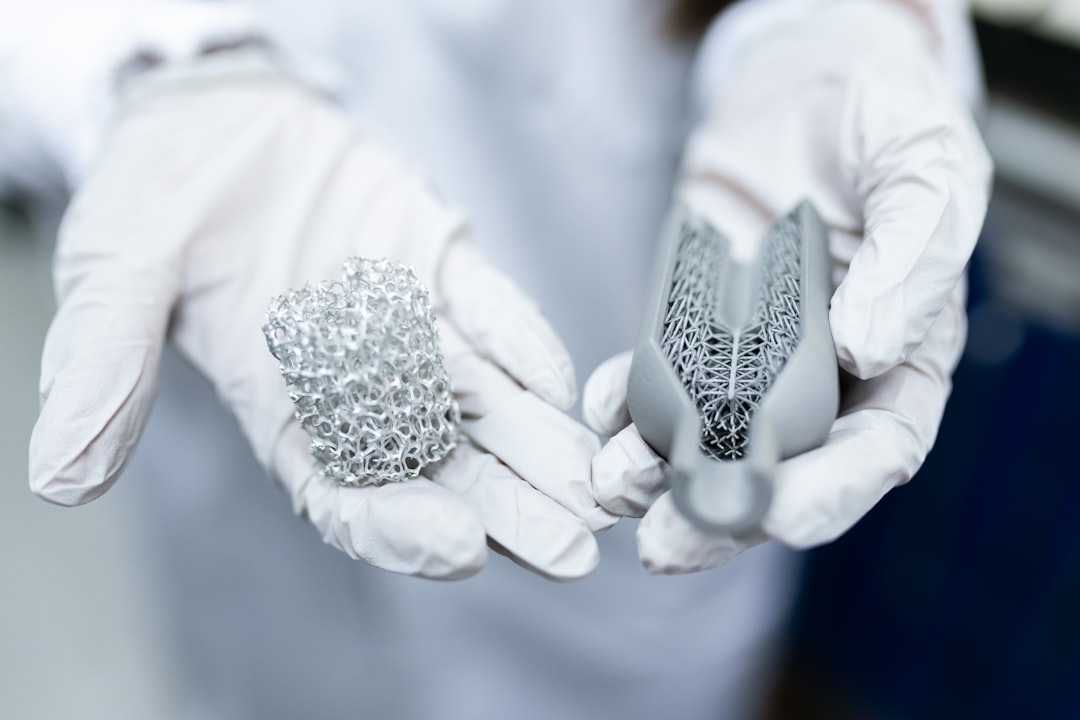
Fatigue analysis is an essential part of designing structures that can withstand repeated stresses. Stress-strain curves are powerful tools that allow engineers to see how materials behave when they are repeatedly loaded. These curves help to predict fatigue failure, which is a major cause of problems in engineering.
The classic approach to fatigue analysis is called the stress-life (S-N) method, but modern techniques offer more detailed insights. The local stress-strain approach, for example, takes into account the actual shapes of components, allowing engineers to simulate strain histories under real-world conditions.
The relationship between stress and strain is complex, especially when it comes to cyclical loading. This includes understanding how the mean stress affects fatigue life. By carefully examining these factors, engineers can design structures that last longer and are safer.
Fatigue analysis, a crucial aspect of structural design, relies heavily on understanding the relationship between stress and strain within materials. While the engineering strain formula provides a foundational understanding, exploring the nuances of this relationship is essential to predict a material's behavior under repeated loading.
One of the key considerations is the fatigue limit, representing the maximum stress level a material can endure for an infinite number of loading cycles without failing. This limit is not a fixed value and can vary significantly based on factors like material composition, manufacturing processes, and even subtle microstructural differences. This highlights the need for rigorous testing to determine accurate fatigue limits for specific applications.
Another critical aspect is hysteresis, a phenomenon where materials do not return to their original state after cyclic loading, resulting in energy dissipation. This energy loss is crucial to consider in fatigue analysis as it affects the material's long-term durability, particularly in structures subjected to repeated stress cycles.
Further complexities arise when considering geometric features within a structure. Notches and holes can act as stress concentrators, leading to localized increases in stress that can significantly impact fatigue life. This localized stress intensification can dramatically decrease the material's ability to withstand fatigue, making it essential for engineers to understand and account for these effects during design.
The impact of loading speed also comes into play, as some materials, particularly polymers and certain metals, exhibit strain rate sensitivity. This means their deformation behavior changes depending on the rate at which the load is applied. This is crucial in dynamic applications like aerospace or automotive, where loads can be applied rapidly, potentially altering the material's response.
Additionally, temperature variations can drastically alter the relationship between stress and strain, influencing a material's performance. Elevated temperatures can soften materials, shifting their yield strength and ductility, making accurate predictions for extreme environments critical.
Furthermore, most materials exhibit a non-linear stress-strain relationship under high stress levels or significant deformations, particularly in softening materials. This nonlinear behavior presents challenges in accurately predicting failure, underscoring the need for sophisticated modeling techniques.
Beyond this, materials like composites or crystals display anisotropic behavior, meaning their stress-strain response differs depending on the direction of the applied force. This anisotropic property requires careful consideration during design to ensure accurate predictions of strength and potential failure points.
Understanding the mechanisms of fatigue crack propagation is also crucial, as it can be influenced by microstructural features and imperfections. The intricate analysis of stress-strain curves over time is essential to understand how cracks grow under cyclic loading, emphasizing the importance of continuous monitoring for early detection and prevention of potential failures.
The stress-strain behavior of materials under cyclic loading can also lead to different failure mechanisms compared to static loading. Engineers must consider these differences when designing structures that will be subjected to repeated stress, such as bridges, aircraft, and other critical infrastructure.
Finally, the emergence of advanced technologies like digital image correlation (DIC) has revolutionized strain analysis. DIC allows engineers to visualize strain across entire surfaces, providing a more comprehensive understanding of deformation patterns than traditional point measurements. This full-field analysis enhances fatigue analysis and contributes to more effective design strategies.
As engineers continue to push the boundaries of material science and structural design, a deep understanding of the intricate relationship between stress and strain remains paramount. This complex interplay is essential for predicting a material's behavior under varying conditions, enabling us to create more durable and reliable structures, from bridges to aircraft and beyond.
Engineering Strain Formula A Cornerstone in Structural Analysis and Material Testing - Experimental Techniques for Strain Measurement in Structures
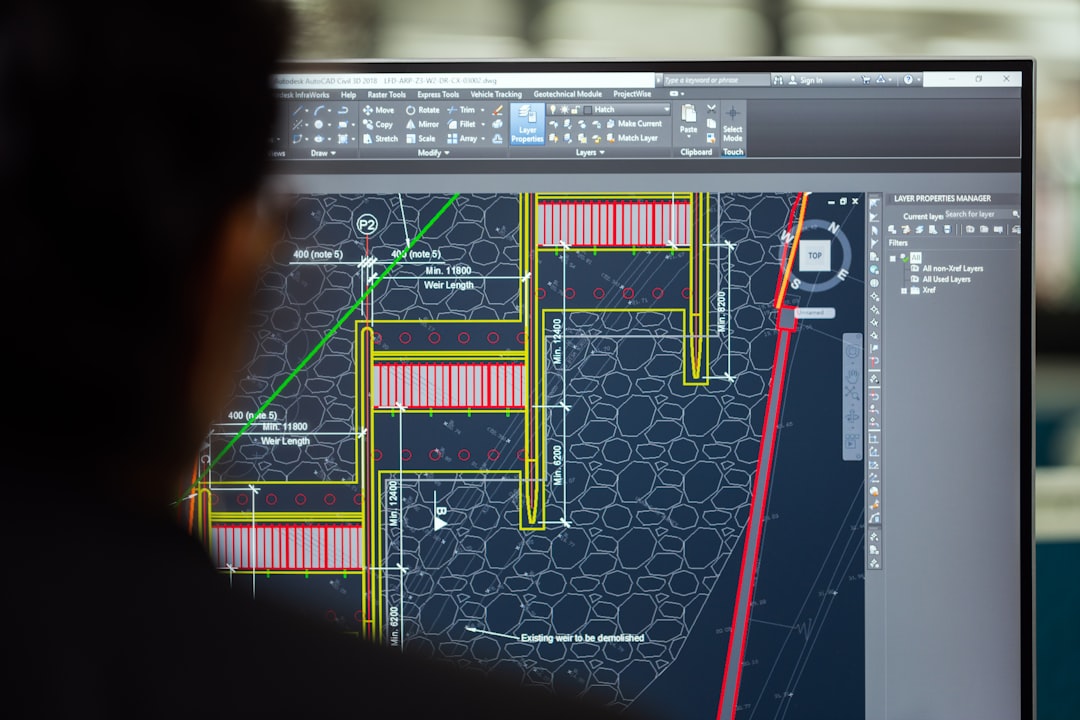
Experimental techniques for measuring strain in structures are essential for understanding how materials behave under stress. While traditional strain gauges are widely used, particularly in critical applications like aerospace, they have limitations, such as their reliance on accessible surfaces. Emerging technologies, like digital image correlation, provide a more comprehensive picture by capturing strain across entire areas, revealing previously hidden insights. This shift towards full-field strain analysis is vital for accurate structural modeling and has led to the integration of these technologies in structural health monitoring systems, enhancing our ability to assess and maintain the integrity of structures.
Experimental techniques play a critical role in understanding how structures behave under stress. While the engineering strain formula provides a foundational understanding, these techniques offer a deeper insight into the complex interplay between stress and strain in real-world scenarios.
Strain gauges, based on the piezoresistive effect, provide incredibly precise measurements of strain, allowing engineers to detect even minute deformations that could precede failure. This technology allows for real-time monitoring of structural integrity, ensuring safety and longevity in critical applications. However, the accuracy of strain gauge measurements is heavily dependent on the gauge length chosen. Short gauge lengths capture local strain variations, while longer gauges offer an average, potentially overlooking critical localized effects.
Digital Image Correlation (DIC) has revolutionized strain measurement by providing full-field strain data, offering a comprehensive understanding of material behavior. This technique compares images of a material's surface before and after deformation, revealing strain distributions across a large area. It's particularly valuable for visualizing how stress concentrates at specific points in structures, helping to predict potential failure points.
However, materials often exhibit non-linear behavior under significant loads, making strain analysis more complex. The relationship between stress and strain becomes unpredictable, demanding advanced techniques like finite element analysis to accurately assess failure scenarios. This complexity is further compounded by the fact that many materials exhibit anisotropic behavior, meaning their response to stress varies with direction. Understanding these nuances is crucial for designing structures that can withstand varying loads and temperatures.
Understanding the impact of cyclic loading is also critical in fatigue analysis. Under repeated stresses, materials exhibit unique fatigue phenomena, leading to a completely different stress-strain response compared to static loads. This altered response can affect the long-term durability of structures, necessitating accurate predictions based on fatigue testing and sophisticated modeling techniques.
Furthermore, materials often exhibit changes in their stress-strain characteristics at elevated temperatures. Understanding these changes, especially for materials like steel and composites, is essential for ensuring safe performance in applications involving extreme thermal conditions.
Finally, the microscopic structure of a material significantly influences its strain response. Processing methods and grain size variations can affect mechanical properties, highlighting the importance of accounting for these microstructural influences when selecting materials for specific applications.
Overall, the development of new techniques and advancements in existing technologies continues to refine our understanding of strain behavior in structures. While the engineering strain formula provides a valuable starting point, it's through meticulous experimentation, sophisticated modeling, and a deeper understanding of material behavior that engineers can create truly resilient and durable structures.
More Posts from aistructuralreview.com: