Calculating Reynolds Number Key Insights for Fluid Flow Analysis in Structural Engineering
Calculating Reynolds Number Key Insights for Fluid Flow Analysis in Structural Engineering - Understanding the Reynolds Number Formula
The Reynolds Number (Re) acts as a pivotal tool in fluid mechanics, effectively quantifying the balance between inertial and viscous forces influencing fluid motion. Mathematically expressed as Re = V * D / ν, it's a dimensionless parameter that serves as a predictor of flow patterns, specifically distinguishing between laminar and turbulent flows. This distinction has substantial implications for engineering designs, as understanding the nature of the flow is crucial for ensuring structural integrity and functional performance. The Reynolds Number is not merely a classification tool for flow regimes, but also a key element in designing systems within various disciplines including structural engineering. Engineers rely on the insights provided by the Reynolds Number to predict factors like drag forces and the dynamic behaviour of fluids in diverse processes. This knowledge, thus, empowers engineers to create designs robust enough to handle the intricacies of actual fluid dynamics in real-world environments. A thorough understanding of the implications of the Reynolds Number is critical for accurate fluid flow analysis and, ultimately, effective engineering solutions across numerous applications.
1. The Reynolds number, being dimensionless, serves as a powerful tool for simplifying the understanding of intricate fluid flow patterns. By classifying flow as either laminar or turbulent, it provides valuable insights into how fluids behave in diverse engineering scenarios.
2. While often associated with a critical value around 2300 in pipes, the threshold between laminar and turbulent flow is sensitive to the exact shape of the flow path and the roughness of its surfaces. This indicates the Reynolds number's inherent sensitivity to specific system characteristics.
3. The Reynolds number formula cleverly encapsulates the interplay of density, velocity, and viscosity. Through this relationship, it effectively quantifies the balance between inertial and viscous forces, a fundamental aspect in achieving accurate fluid system design.
4. Though rooted in engineering, the Reynolds number surprisingly finds applications in understanding biological systems. Examples like blood flow and air movement in the lungs demonstrate how the principles of fluid mechanics can illuminate complex biological processes.
5. Despite its simplified nature, the Reynolds number acts as a predictive tool for numerous flow phenomena. These include flow detachment from surfaces and skin friction drag, which hold significant importance in fields like aerodynamics.
6. Its origins trace back to the experimental work of Osborne Reynolds in the late 1800s, but the relevance of the Reynolds number has expanded substantially since then, becoming an indispensable component of modern engineering practices.
7. In many real-world engineering challenges, temperature fluctuations can alter fluid density and viscosity, thus impacting the Reynolds number. Engineers must account for such thermal influences to ensure their predictions of fluid behavior remain accurate.
8. The transition from orderly laminar flow to chaotic turbulent flow often brings significant changes in system performance and pressure drops. Recognizing this connection is crucial in understanding how the Reynolds number governs efficiency within fluid systems.
9. A common misconception arises when associating higher Reynolds numbers with enhanced performance. While this might seem intuitive, turbulent flow can actually increase drag and energy consumption in specific applications.
10. The Reynolds number has spurred ongoing research in scaling laws within fluid mechanics. This allows engineers to extrapolate findings from smaller-scale models to larger systems while maintaining predictive accuracy, a remarkable advantage in engineering design.
Calculating Reynolds Number Key Insights for Fluid Flow Analysis in Structural Engineering - Significance of Reynolds Number in Laminar vs Turbulent Flow
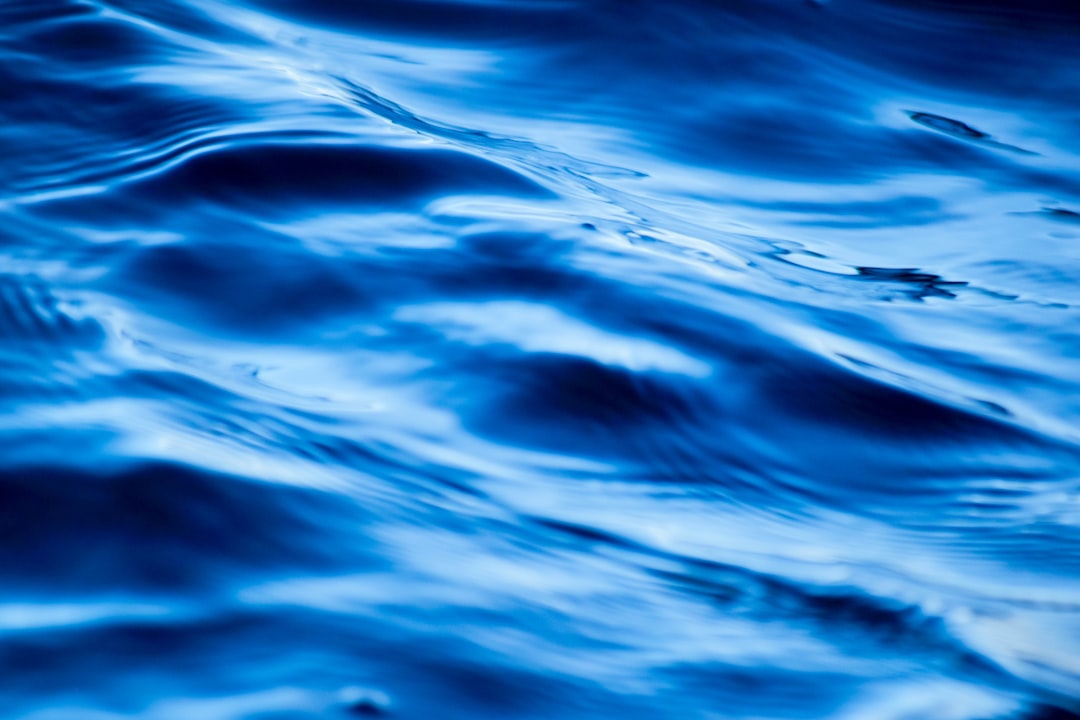
The Reynolds number's core significance lies in its capacity to differentiate between laminar and turbulent flow regimes, a distinction crucial for understanding fluid behavior in engineering applications, especially within structural engineering. When the Reynolds number is relatively low, typically below 2000, the flow is generally laminar. This signifies a smooth, predictable flow pattern where fluid particles move in organized layers. Conversely, Reynolds numbers above 4000 usually correspond to turbulent flow. In this regime, the flow is chaotic and irregular, with inertial forces overriding viscous forces. A crucial aspect lies in the transition zone, the region between these approximate thresholds where the flow can fluctuate between laminar and turbulent states. This transition significantly influences a fluid system's stability and performance characteristics, often impacting efficiency and pressure drops. Therefore, the Reynolds number is not just a simple categorizer of flow types but a foundational parameter for understanding and designing systems that interact with fluid flows, underpinning numerous calculations within structural engineering projects.
1. The shift from laminar to turbulent flow, typically around a Reynolds number of 2300, emphasizes the fragility of flow stability. Even small changes in velocity or pressure can tip the balance from a smooth, ordered flow to a chaotic one. This sensitivity is a key aspect to keep in mind when analyzing flow behaviors.
2. In laminar flow, fluid particles follow relatively straight paths with minimal intermixing, making the flow predictable and relatively easy to manage. Turbulent flow, on the other hand, is characterized by erratic fluctuations and significant mixing, leading to increased energy dissipation and complexity in our understanding of how the fluid will behave.
3. Surface irregularities can have a profound effect on the critical Reynolds number, a reminder that surface design plays a crucial role in flow patterns, alongside fluid properties. This implies that engineers need to consider not just the fluid itself but the surfaces it interacts with.
4. It's intriguing that different fluids can share the same Reynolds number yet show drastically different flow characteristics. This underscores how viscosity acts as a vital factor in influencing the overall flow behavior, going beyond just the simple Reynolds number classification.
5. In applications like aircraft design, carefully controlling the transition between laminar and turbulent flow is paramount. Achieving a state of laminar flow can significantly reduce drag, which is directly relevant to fuel economy and performance. The implications for efficiency and the complexity of achieving this state are critical engineering challenges.
6. Interestingly, some biological systems, like microfluidic devices, actually exploit the laminar flow regime to enhance mixing at a very small scale. This contrasts with large-scale engineering applications where turbulence is often sought for enhanced mixing, but here we see the deliberate manipulation of flow characteristics for specific purposes.
7. The energy losses due to drag in turbulent flow aren't uniform; there can be regions of significantly higher losses associated with specific Reynolds numbers. Engineers must keep this in mind when designing and analyzing systems, ensuring they consider not just average behavior but also potentially adverse scenarios.
8. Maintaining a low Reynolds number also has implications for sound and noise reduction. For example, in applications like HVAC systems, ensuring laminar flow minimizes turbulence-related noise, an important consideration for designing quieter and more comfortable environments.
9. Some engineering systems, such as oil pipelines, are intentionally operated at conditions slightly below the critical Reynolds number. This minimizes turbulence, thereby reducing friction and conserving energy over the extensive distances that these pipelines travel. It's an example of balancing flow characteristics for optimal operational efficiency.
10. The Reynolds number serves as a foundation for creating correlations within fluid mechanics. Many of these correlations are based on experimental observations, allowing engineers to make more accurate predictions about fluid behavior in different flow scenarios. It's a crucial tool in making the transition from basic theoretical understanding to practical applications.
Calculating Reynolds Number Key Insights for Fluid Flow Analysis in Structural Engineering - Critical Reynolds Number Values for Engineering Applications
The critical Reynolds number marks the transition point where fluid flow shifts from a smooth, predictable laminar state to a chaotic, turbulent state. This transition is vital for engineers because it influences how fluids behave in systems and structures. While values like 2300 for pipe flow and 500,000 for flow over flat surfaces are often cited, it's crucial to remember that these are not fixed. The actual critical Reynolds number can vary, influenced by factors like the specific shape of the flow path and the roughness of the surfaces involved. This variability underscores the need for engineers to carefully consider the system's unique geometry when predicting flow behavior.
Understanding these critical values is crucial because they dictate characteristics that affect performance and efficiency in various engineering applications. For instance, engineers must consider these when designing pipelines or aerodynamic structures. Furthermore, the intricate mechanics of the transition from laminar to turbulent flow emphasize the need to go beyond just the fluid's properties. It's equally important to examine design aspects that can alter flow patterns. A comprehensive approach to evaluating the critical Reynolds number is vital for achieving optimal performance and efficiency in fluid systems within the field of structural engineering. The complexity of this transition should not be underestimated and requires careful consideration when evaluating the success of any fluid system.
The critical Reynolds number isn't a fixed number but rather a range that depends on the specific shape of the system and the conditions of the flow. It's crucial to understand the context, as even small changes in a design can have a big impact on how the flow behaves and where the transition between laminar and turbulent flow happens.
While we often hear that 2300 is the critical Reynolds number for flow in round pipes, in the real world, the transition to turbulence can happen at Reynolds numbers as low as 1000 or as high as 3000. This demonstrates the complexities that engineers face when working with fluids.
It's important for engineers to be careful when using estimations of the Reynolds number, especially with fluids that don't behave in a simple way (non-Newtonian fluids). These fluids can have different viscosities depending on how much stress is applied to them and they might have very different flow behaviors despite having similar Reynolds numbers.
The roughness of the surface has a big impact on the critical Reynolds number. When the flow is turbulent, a rougher surface leads to higher drag forces. This means engineers need to be clever in how they treat the surfaces of structures to maximize efficiency.
Interestingly, in some applications, like those involving very tiny flows (microfluidics), it's common to have a Reynolds number much lower than 1. This gives engineers precise control over how the fluid moves. This is especially helpful in biomedical applications where they use laminar flow to perform very specific tasks at very small scales.
We often rely on experimental relationships between the Reynolds number and drag coefficients, but this doesn't account for the variations that can happen because of boundary conditions. This makes it a challenge to calculate accurate drag forces for complex systems.
Experiments show us that when fluids flow past an object and are near the critical Reynolds number, a surprising phenomenon can occur called the "transition bubble". This shows how a delicate balance of forces can lead to unexpected flow behaviors.
The connection between Reynolds numbers and how heat moves within a fluid shows that changes in flow regimes affect not only the mechanical aspects of the flow but also thermal performance. This has implications for the design of heating and cooling systems.
Engineers often adjust the Reynolds number concept for specific situations. For example, they use the Dean number for flows that curve, showing that the original concept is flexible enough to be adapted for complex flow situations.
The idea of the Reynolds number has spurred advancements in computer-based simulations of fluids (CFD). These simulations often rely on the Reynolds number to give more accurate predictions of flow behavior across diverse engineering contexts, bringing together theory and advanced technologies.
Calculating Reynolds Number Key Insights for Fluid Flow Analysis in Structural Engineering - Impact of Fluid Properties on Reynolds Number Calculations
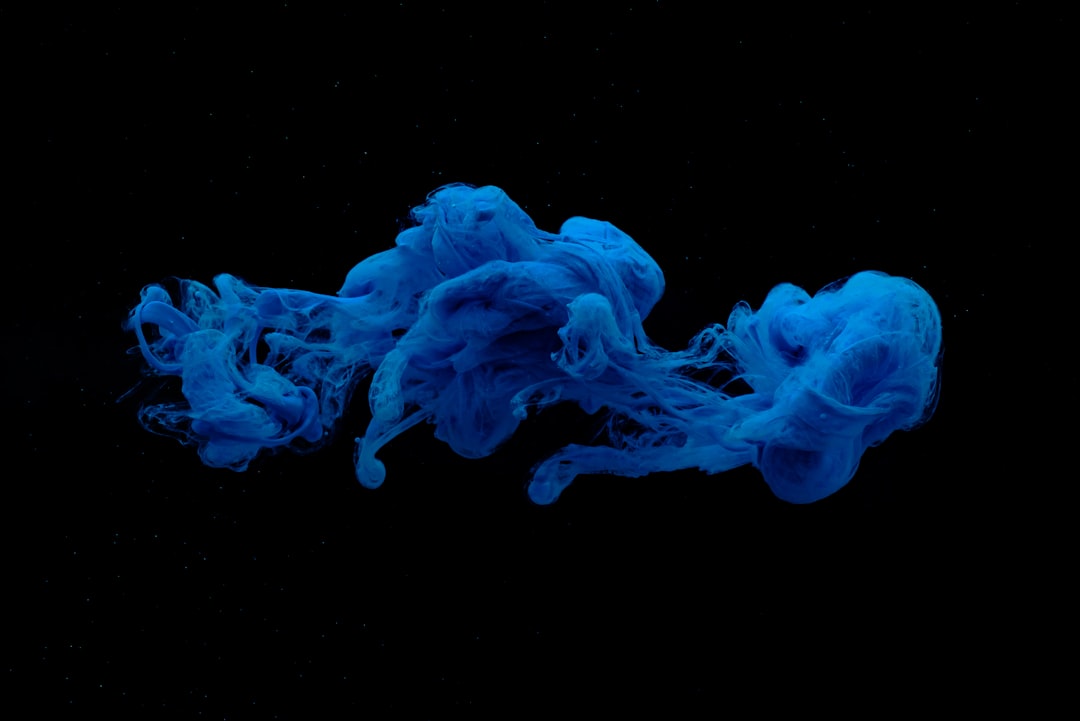
The accuracy of Reynolds Number calculations hinges on a thorough understanding of the fluid's properties. Factors like the fluid's density, its viscosity (how easily it flows), and the speed at which it's moving all have a significant impact on the resulting Reynolds Number. This number, as we've discussed, determines whether the fluid flow will be smooth and predictable (laminar) or chaotic and turbulent. Engineers must therefore carefully account for variations in these fluid characteristics, especially under changing temperatures, to avoid flawed predictions of how the fluid will behave within a given system. Oversimplifying the fluid's properties can lead to inaccurate predictions and, potentially, suboptimal design decisions that affect system performance. It's crucial, then, for structural engineers to adopt a comprehensive understanding of these fluid properties and their influence on Reynolds Numbers when analyzing fluid flow and designing for it, especially in structural engineering applications.
1. Fluid properties like density and viscosity aren't fixed; they can shift dramatically with changes in temperature and pressure. These fluctuations can necessitate recalculating Reynolds numbers, emphasizing the need for precise measurements to ensure accurate predictions of how the fluid will flow.
2. The relationship between shear rate and viscosity becomes particularly complex in non-Newtonian fluids, where the apparent viscosity changes depending on how much stress is applied to the fluid. This adds layers of complexity to Reynolds number calculations and can lead to substantial deviations from the expected flow behavior.
3. In some situations, relying solely on the Reynolds number for flow prediction can be misleading. For instance, even with low Reynolds numbers, viscous fluids might still experience turbulence-like behavior due to other dominant physical factors. This challenges the conventional understanding of the laminar-turbulent flow classification system.
4. The molecular structure of a fluid can significantly influence its flow behavior. For example, polymer solutions can have dramatically different viscosity characteristics compared to simpler, Newtonian fluids, even under the same conditions. This highlights the need to use specialized methods when assessing Reynolds numbers for these more complex fluids.
5. Scale effects play a vital role at different Reynolds numbers. Small-scale systems might exhibit laminar flow even when using high-viscosity fluids, whereas larger systems might become turbulent despite utilizing fluids that typically behave in a laminar fashion.
6. Computational Fluid Dynamics (CFD) often relies on models based on the Reynolds number. However, errors in the input fluid properties can be amplified throughout the simulation, leading to results that diverge significantly from what's actually observed in experiments.
7. The transition point between laminar and turbulent flow (the critical Reynolds number) can be affected by external factors, such as electromagnetic fields, in some specialized applications. This illustrates that engineers need to consider broader influences beyond just the fundamental fluid properties when evaluating flow behavior.
8. When assessing the Reynolds number, it's essential to consider the development of the boundary layer—the region near the surface where viscous forces are dominant. Changes in the boundary layer thickness can lead to unexpected transitions between flow regimes, underscoring the importance of carefully considering the interaction between fluid and structure.
9. In high-speed flow applications, such as those found in aerospace engineering, the Reynolds number alone might not be sufficient to fully capture all the nuances of fluid flow. It becomes necessary to incorporate other dimensionless parameters to gain a more complete understanding of the flow characteristics.
10. The shifts in flow regimes that occur when fluid properties change highlight the need for dynamic modeling techniques in engineering systems. A static analysis based on a single Reynolds number might miss crucial variations that occur during operation, potentially leading to inaccurate or incomplete conclusions.
Calculating Reynolds Number Key Insights for Fluid Flow Analysis in Structural Engineering - Reynolds Number in Computational Fluid Dynamics Modeling
Within the realm of Computational Fluid Dynamics (CFD) modeling, the Reynolds number emerges as a crucial parameter, dictating the nature of fluid flow and guiding the selection of appropriate turbulence models. Essentially, it determines whether a fluid's movement will be smooth and predictable (laminar) or chaotic and irregular (turbulent). This knowledge is fundamental in achieving simulations that accurately mirror real-world fluid behavior. CFD modelers must account for the Reynolds number because it significantly influences the choice of numerical methods employed in their analyses. This, in turn, impacts the overall stability and trustworthiness of their simulations. Additionally, it's important to remember that a fluid's properties can shift due to external factors, like temperature changes. Therefore, consistently refining the Reynolds number calculation is vital to maintain accurate fluid dynamic predictions. This close interplay between fluid mechanics and the Reynolds number ultimately highlights its indispensable role in effective structural engineering design and performance analysis, revealing the intricate relationship between the two domains.
1. The critical Reynolds number isn't a one-size-fits-all value. For instance, a sphere might transition to turbulence around a Reynolds number of 1000, while flow over a flat surface could remain laminar until values exceeding 500,000. This highlights that different flow scenarios require tailored approaches.
2. In fluids with high viscosity, even at relatively high velocities, the Reynolds number might still indicate laminar flow. This happens because the viscous forces are dominant, overriding inertial forces, and leading to unexpected flow behavior compared to our typical assumptions.
3. Temperature changes can significantly alter a fluid's viscosity and thus its Reynolds number. This effect is particularly notable in heating or cooling systems, where variations in fluid temperature relative to the surroundings can cause unexpected shifts in flow regimes.
4. Some cutting-edge biomedical applications make use of Reynolds numbers far below 1. This allows for highly predictable laminar flow and enables precise control over mixing processes at extremely small scales, leading to innovations in things like targeted drug delivery.
5. Surprisingly, flow can sometimes become turbulent even at low Reynolds numbers due to factors like surface roughness or obstacles. This underscores how much more intricate flow behavior can be than a simple Reynolds number might suggest.
6. CFD models rely on the Reynolds number, but their accuracy is heavily dependent on the quality of the input data about fluid properties. Inaccurate fluid data can lead to significant errors in the model's predictions, so it's crucial to ensure thorough validation with real-world experiments.
7. The transition between laminar and turbulent flow can lead to "flow anomalies," where isolated turbulent regions pop up within otherwise laminar flow. This is yet another example of the complex and subtle nature of fluid behavior.
8. The Reynolds number, while a useful tool, can also provide a potentially oversimplified view of flow. For instance, some polymer solutions, even at low Reynolds numbers, display complex flow dynamics due to their unique molecular structure. This shows us there's often more to the story than the Reynolds number alone.
9. Analyzing fluid flow through porous materials often necessitates using modified Reynolds numbers. This is because traditional Reynolds number formulations don't capture the impacts of factors like permeability and porosity, which are essential in understanding flow in such materials.
10. The Reynolds number is essential when dealing with interconnected phenomena, like fluid-structure interaction. In these cases, the flow's dynamic characteristics and the structural response are intertwined, and must be considered together for a realistic understanding of the system.
Calculating Reynolds Number Key Insights for Fluid Flow Analysis in Structural Engineering - Practical Applications of Reynolds Number in Structural Design
The Reynolds Number plays a crucial role in structural design by providing insights into fluid flow behavior, ultimately impacting structural performance and integrity. By predicting whether a flow will be smooth and layered (laminar) or chaotic and irregular (turbulent), engineers can make informed decisions about material selection, structural shapes, and overall design to minimize risks like excessive drag or flow-induced instability. This is especially relevant in applications involving pipelines or aerodynamic components where anticipating transitions between laminar and turbulent flow is critical for optimization. The Reynolds Number also enables the scaling of fluid flow models, allowing engineers to extrapolate observations from smaller-scale prototypes to larger, real-world systems. It's important to remember, however, that relying solely on the Reynolds Number can lead to inaccurate assessments if the complexities of fluid properties and surface characteristics are not considered. This highlights the need for a more comprehensive approach in structural design to ensure that predictions are accurate and designs are robust.
1. The relevance of the Reynolds number in structural design goes beyond simple flow categorization. It's crucial for designing elements like grilles and ducts, where maintaining stable airflow is essential to prevent performance loss and inefficiency. It's intriguing how something seemingly simple like flow stability can have such a big impact on a structure's performance.
2. It's fascinating how the critical Reynolds number isn't a fixed value in isolation. Engineers often find that a combination of design factors, including geometry, surface texture, and the fluid's characteristics, are all interconnected in achieving a desired flow regime. This interconnectedness presents a more intricate challenge than might initially be assumed when trying to design for a specific type of flow.
3. The importance of surface treatment can't be overstated. For instance, using smooth finishes can push the critical Reynolds number to higher values, allowing laminar flow to persist in applications where turbulence would otherwise increase drag. This points towards the fact that surface design and its impact on flow are an integral part of structural engineering considerations.
4. Interestingly, the Reynolds number can also be used as a basis for estimating how long it takes a small change in flow to move through a system. This is crucial for analyzing how systems react to sudden changes or disturbances, a key aspect of structural engineering in dynamic environments. It demonstrates the connections between fundamental fluid behavior and complex, time-dependent structural scenarios.
5. While many engineers might instinctively think that a high Reynolds number will always mean better efficiency, turbulent flow can actually lead to a significant increase in drag and energy use in some cases. This surprising outcome can be a significant challenge when trying to optimize a system for performance and shows that the connections between flow and performance are not always straightforward.
6. Structures with passive flow control devices, like vortex generators, can benefit from using Reynolds number analysis to actively manipulate flow characteristics. This approach has the potential to enhance efficiency and increase the lifespan of these systems. It's a testament to the ingenuity in engineering where a theoretical concept like the Reynolds number can help us influence and improve real-world systems.
7. In some innovative applications, like 3D-printed components, the Reynolds number can be used to predict how the flow through the tiny pores in these structures will affect the overall performance of the material when subjected to dynamic loads. This suggests a widening of the applications of Reynolds number to newer technologies and how it can inform material selection and design.
8. The phenomenon of "flow separation," which can happen even at Reynolds numbers below 2000, highlights a key issue in system design. It reveals that simply classifying the flow as laminar or turbulent might not always give us a truly accurate picture of how well the system will perform. It emphasizes the need for a deeper understanding of flow behaviors that extends beyond simple categorization.
9. Exploring the link between the Reynolds number and resonance in fluid systems can provide us with opportunities to optimize a system's response to frequency changes. This is important for minimizing vibrations that could eventually lead to structural failures. It shows how understanding flow properties can help to design more robust and resistant systems.
10. Since flow regimes are constantly changing, engineers may need to utilize real-time flow monitoring and Reynolds number calculations for critical structures. This approach ensures immediate responses to changes in operating conditions, leading to more adaptive and resilient designs. This points towards the importance of a more dynamic perspective on the application of Reynolds number in structures that might experience a changing operational environment.
More Posts from aistructuralreview.com: