Understanding Static vs Dynamic Friction in Steel Bridge Bearing Design A Structural Engineering Analysis
Understanding Static vs Dynamic Friction in Steel Bridge Bearing Design A Structural Engineering Analysis - Principles of Static Friction in Steel Bridge Bearings at Rest
When a steel bridge is stationary, static friction becomes the primary force governing the interaction between the bridge's superstructure and its bearings. This friction acts as a restraining force, preventing any unwanted movement or slippage under the influence of constant loads like the bridge's own weight or other static forces. The magnitude of this static friction is directly tied to the properties of the surfaces in contact. Rougher surfaces, for instance, tend to interlock more effectively, leading to higher static friction. Similarly, increasing the contact area between bearing and superstructure generally enhances static friction, though this relationship is not always linear.
The specific materials used in the bearing design also influence friction characteristics. Understanding these factors is vital when engineers select and design bearings. They must ensure the bearing system can effectively withstand anticipated static loads and remain stable under varying conditions. Following guidelines and standards, like those from design specifications, helps to ensure the bearing system can handle these loads safely and contribute to the overall structural reliability of the bridge. Furthermore, the specific loading environment of a bridge—incorporating dead loads, live loads, seismic forces, and wind loads—must be considered when designing the bearing to maintain performance throughout its lifespan. Neglecting these factors can lead to bearing failure or, at the very least, compromised structural integrity over time.
When a steel bridge bearing is at rest, static friction plays a crucial role in its stability. This friction, significantly stronger than dynamic friction, results from the intricate interlocking of molecules at the contact surfaces. However, this interlocking is easily disrupted once motion begins, explaining the difference in frictional forces.
The coefficient of static friction for steel pairs can vary substantially based on the surface texture and the presence of lubricants, ranging from about 0.5 to 1.0. It's not always easy to predict and can impact the performance of the bearing. For example, temperature variations within the structure can alter the contact area and, in turn, the friction between the surfaces, adding an element of complexity to the system.
Under heavy loads, the steel surfaces deform, leading to modifications in the friction, making precise predictions more challenging. Further, the presence of impurities like moisture or dust can either enhance or diminish the grip between surfaces, highlighting the need for clean bearing surfaces.
A notable phenomenon is "stick-slip", where static friction momentarily maintains an object’s position until it surpasses a certain threshold, causing sudden, potentially harmful, dynamic loads.
Clever design approaches can mitigate high static friction. Using materials like elastomers or laminates can shift the friction and help distribute loads effectively. Similarly, anti-friction coatings are frequently incorporated to decrease friction, but their durability is impacted by environmental conditions. Applying pre-load can create a stable static frictional state, counteracting any unwanted motion under changing loads.
It’s interesting to note that the static frictional state can be negatively affected by factors such as vibration or repeated temperature cycles. This fact emphasizes the importance of selecting appropriate materials and designing for long-term performance. Understanding the interplay of these factors is vital for engineers to design resilient steel bridge bearings that ensure bridge safety and structural integrity.
Understanding Static vs Dynamic Friction in Steel Bridge Bearing Design A Structural Engineering Analysis - Dynamic Friction Effects During Bridge Movement and Load Transfer
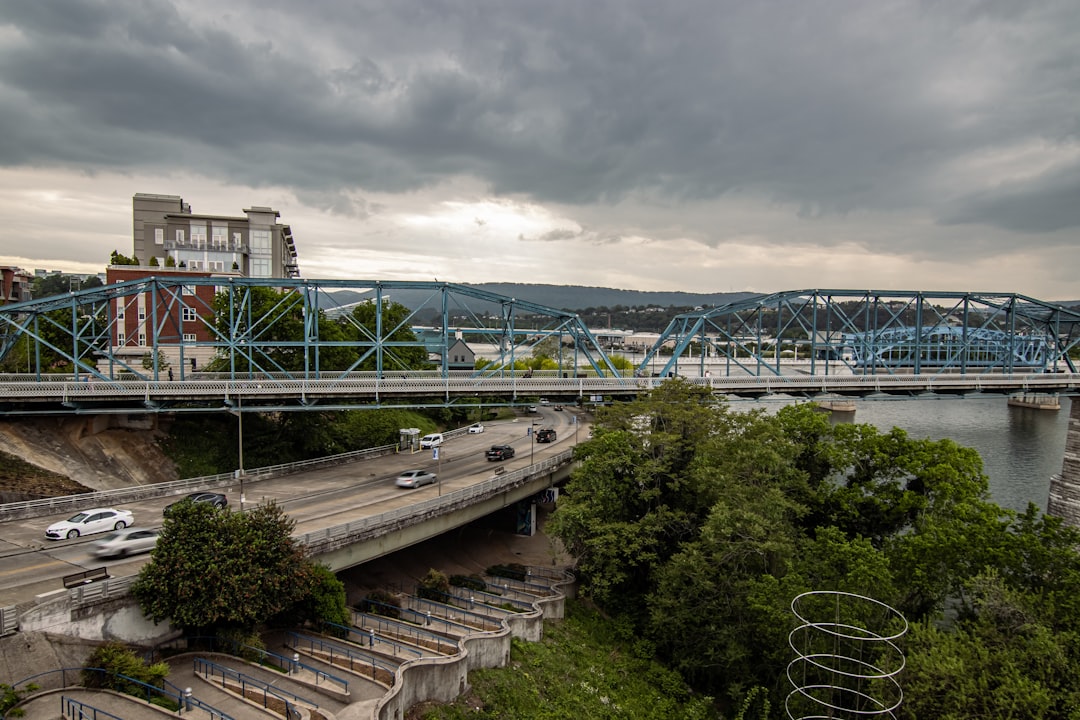
When a bridge is in motion, dynamic friction becomes a key factor in how the structure behaves under changing loads. The impact of moving loads, like traffic, produces a more intense response than stationary loads, influencing the way bearing surfaces wear down. Unlike static conditions, where prolonged contact often leads to a different type of wear, the repeated movement seen under dynamic loads results in a more abrasive kind of wear. The speed at which bearing surfaces slide against each other during these dynamic events can be substantially faster than under static conditions, potentially leading to increased wear and tear.
Engineers must be mindful of this and design bearing systems that minimize friction to reduce stress on components. Additionally, dynamic conditions can introduce challenges, such as repetitive, small movements. This constant motion requires special attention during design to ensure structural integrity over time. By understanding how dynamic friction affects a bridge's movement and load distribution, designers can optimize the bearing system to improve both performance and lifespan of the structure. Failing to consider these effects can lead to accelerated degradation and compromised safety.
The nature of friction changes considerably when a bridge moves, a factor that's crucial to consider during design. Dynamic friction, unlike its static counterpart, tends to be much lower, typically ranging from 0.2 to 0.5 for steel-on-steel contact. This lower resistance can unexpectedly lead to movement during load transfer, a potential source of complications.
The surface finish of the bearing materials heavily impacts dynamic friction. Smoother surfaces usually exhibit lower friction coefficients. While this might seem beneficial, it's vital to ensure the design accommodates such low friction to avoid unwanted sliding and maintain stability.
The dynamic nature of a bridge can introduce resonance frequencies. These resonant vibrations can significantly affect dynamic friction, potentially creating failure modes that are unrelated to the applied load itself.
Temperature changes, a natural occurrence in bridge structures as they undergo loading and movement, induce thermal expansion, causing shifts in bearing alignment. This change in alignment, in turn, affects the dynamic friction coefficients, adding yet another layer of complexity to the design process.
Repeated loading cycles wear down bearing surfaces, which alters the contact conditions between the surfaces. This wear leads to unpredictable changes in dynamic friction, which can potentially affect the overall performance of the bridge.
Introducing lubrication is a common practice to modify dynamic friction. However, it also introduces a risk. Inconsistencies in the lubricant film can cause a rapid shift from a state of static friction to dynamic friction, putting the structural integrity of the bridge at risk.
Similar to lubrication, contaminants such as dust, moisture, or debris can considerably change the dynamic friction a bridge experiences. For example, water can dramatically reduce friction, increasing the likelihood of sliding or unwanted displacement.
The way loads are distributed across the bearings changes under dynamic conditions. This redistribution of loads can lead to localized overloading in certain areas, increasing the risk of localized failure.
The speed at which loads are transferred impacts the dynamic friction significantly. Rapid load transfers, associated with high speeds, can lead to a drastic drop in friction, potentially causing a loss of control over the bridge deck's movements.
Lastly, during load reversal situations, we see hysteresis effects in dynamic friction. This means the load path and the frictional resistance don't perfectly align, which can cause erratic motions that could raise concerns about the structural integrity of the bridge.
It's clear that accurately predicting and controlling dynamic friction is essential to design safe and reliable bridges. These dynamic effects highlight the intricate interplay between surface texture, temperature, speed, and other factors that can significantly impact bridge performance. While engineers use design codes to account for some of these effects, further research is needed to truly understand the intricacies of dynamic friction and ensure future bridges remain safe and durable under a wide range of operating conditions.
Understanding Static vs Dynamic Friction in Steel Bridge Bearing Design A Structural Engineering Analysis - Material Selection and Temperature Control for Bridge Bearing Design
Bridge bearing design necessitates careful consideration of material selection and temperature control to ensure both optimal performance and long-term durability. The materials used directly influence frictional interactions between the bridge superstructure and its supports. These friction characteristics, in turn, are significantly affected by temperature changes, which can alter bearing behavior under load. Engineers must meticulously account for the effects of thermal expansion and contraction on bearing alignment and overall function. This often involves complex calculations and necessitates the selection of materials that can withstand these temperature-induced stresses while maintaining structural integrity. Following industry standards and design guidelines is essential to minimize the negative impact of temperature fluctuations, friction, and other relevant factors on the bearing system. This comprehensive approach not only enhances the longevity of the bridge but can also contribute to cost-effective infrastructure design and construction.
The selection of materials for bridge bearings plays a crucial role in how temperature influences the overall bridge structure. Different materials possess varying thermal conductivities and react differently to temperature shifts, impacting their performance. For instance, steel's expansion rate of roughly 12 microstrains per degree Celsius highlights the need for careful design calculations to prevent thermal stress. Ignoring these changes can result in detrimental structural consequences.
We also observe interesting interactions between moisture and temperature within the bearing environment. For example, moisture can decrease friction in steel bearings, but its evaporation due to temperature increases can surprisingly lead to heightened friction. This emphasizes the importance of understanding how environmental conditions affect the frictional properties of bearing materials.
Temperature differences within a bridge itself can vary significantly, especially between the top and bottom sections. Direct sunlight often heats the upper parts more, creating a gradient that causes differential expansion and puts stress on the bridge's bearings. This complexity adds to the engineering challenge of selecting and designing appropriate bearing systems.
Materials like high-performance polymers react uniquely to temperature changes. These materials can exhibit a decrease in dynamic friction with rising temperatures, which can be advantageous or disadvantageous depending on the loads placed on the bridge. Understanding this relationship is critical for selecting suitable polymers.
Furthermore, certain materials designed for high-temperature environments can become brittle at colder temperatures, necessitating engineers to consider the entire range of operating temperatures throughout the bridge's lifespan to prevent unexpected failures. Balancing friction with temperature changes is crucial for bridge safety.
Allowing a specific range of motion, or 'sliding distance', within the bearing design can help manage thermal expansion. However, this design necessitates a careful consideration of material choice to find a balance between frictional resistance and the expected temperature variations.
Interestingly, materials can age and become more susceptible to temperature fluctuations over time. This aging process can worsen inconsistencies in bearing performance, ultimately affecting the friction and stability of the entire system.
Employing monitoring technologies to track thermal performance can enhance our understanding of bearing material behavior. Temperature data can be used to predict maintenance needs and potentially avert future issues, leading to improved bridge safety.
Finally, unexpected temperature spikes—for instance, those caused by rapid weather changes—can generate thermal shock in bearing materials. This shock can cause sudden and disruptive failures, making continuous thermal assessment a vital practice in bridge engineering.
The complexities of these temperature-related factors underscore the ongoing need for research and development within the field of bridge bearing design to ensure the safety and durability of future infrastructure.
Understanding Static vs Dynamic Friction in Steel Bridge Bearing Design A Structural Engineering Analysis - Load Distribution Analysis Through Steel Support Structures

In the realm of steel bridge design, understanding how loads are distributed through the supporting structures is paramount. This "load distribution analysis" involves meticulously examining how forces travel through different structural elements, like beams and columns, ensuring no single component bears an undue burden. This process becomes more complex when considering both the constant, or static, loads like the bridge's own weight, and dynamic loads like traffic. Furthermore, the possibility of uplift forces at bearing points, where the bridge deck connects to supports, must be accounted for during design.
The effectiveness of load distribution relies on a deep understanding of how loads travel through the structure and how different components interact with each other. A failure to properly consider these interactions could result in localized failure of a specific area, or even a wider instability within the entire bridge. The development and refinement of analytical methods alongside advancements in the materials used for supports contribute to a greater level of safety and resilience in modern bridge design, but there is always the potential for things to be improved as new situations are encountered.
Exploring how loads are distributed through steel support structures reveals that uneven loading can create complex stress patterns. These patterns can lead to localized, potentially severe stress concentrations that might not be readily apparent using basic analytical methods. This can jeopardize the structural integrity of the bridge, highlighting the need for more advanced analysis techniques.
The way connections are designed between support structures and bearings has a significant impact on load distribution. If these connections aren't designed properly, they can inadvertently transfer moments in ways that are unfavorable, possibly resulting in fatigue-related failures over time. Paying careful attention to connection details is crucial to preventing such issues.
Adding reinforcement to specific areas of a support structure can certainly increase its load-carrying capacity. However, this reinforcement can also affect the overall stiffness of the structure. It's important to carefully analyze how these changes impact load transfer through the entire structure to prevent unintended consequences.
Even if using steel of the same grade, material properties can still vary between different batches or even within a single piece. These variations can impact load distribution and the bridge's overall structural response. Maintaining consistent material quality is vital to ensuring the bridge behaves in a predictable and reliable way under different loads.
When considering dynamic loads, like those caused by moving vehicles, the natural frequency and how well the structure dissipates vibrations become incredibly important in understanding load distribution. The bridge's ability to absorb and dampen these vibrations influences how efficiently loads are transferred through the system. It's clear that structural dynamics and the way loads are transmitted are intimately related.
Temperature differences throughout the steel structure can cause uneven expansion and contraction of different parts. This variation in thermal expansion can inadvertently alter the intended path of load transfer and concentrate stress in unforeseen ways. Engineers must carefully consider these effects to prevent these thermal-induced stress concentrations.
Advanced techniques like finite element analysis (FEA) are often used to try to model load distribution under various conditions. However, the accuracy of FEA results hinges heavily on the quality of the input data and the preciseness of the model. Ensuring a model accurately reflects the real-world material properties and geometry is essential to gaining accurate insights through FEA.
In situations where steel support structures are slender, a phenomenon called local buckling can occur. When this happens, it can significantly alter how loads are distributed. Under unexpected load scenarios, this altered load distribution can potentially lead to instability of the entire structure. This suggests local buckling should be carefully considered during design and analysis to minimize risks.
Corrosion damage can occur on bearing surfaces or the supporting steel structure. When this occurs, it changes the way loads are distributed. Corrosion also changes the friction characteristics between surfaces, potentially causing failures prematurely if it's not carefully monitored and addressed during routine maintenance.
Lubricants are sometimes used to reduce friction in bearings. While that is their primary function, they can also affect the effective stiffness of the bearings and the surrounding structure. This change in stiffness alters how loads are transferred, potentially leading to issues with long-term structural integrity if not properly understood and analyzed.
Understanding Static vs Dynamic Friction in Steel Bridge Bearing Design A Structural Engineering Analysis - AASHTO Standards and Technical Requirements for Bridge Bearings
AASHTO standards provide a framework for bridge bearing design, outlining specific requirements and classifications for various bearing types. These include elastomeric, high-load multi-rotational, mechanical, and seismic isolation bearings, each designed for particular structural needs. The standards emphasize certain aspects of bearing design, such as ensuring adequate sole plate extension for ease of installation, and the importance of materials that can handle both static and dynamic loads while resisting temperature changes. The AASHTO guidelines place a strong focus on proper detailing and material selection, which are vital for maintaining bridge performance and durability under diverse loading and environmental conditions. The standards stress the significance of a comprehensive design approach to ensure long-term structural integrity, recognizing that the complex interplay of factors like static and dynamic friction necessitates careful consideration for reliable bridge operation. Compliance with these standards is crucial for managing the potential risks related to bridge bearing behavior.
AASHTO standards for bridge bearings provide a framework for designing these crucial components, which play a vital role in a bridge's overall lifespan and safety. They categorize bearings into four primary types—elastomeric, high-load multi-rotational (HLMR), mechanical, and seismic isolation—each with its own unique set of structural properties and suitability for specific applications. The standards emphasize the importance of the sole plate, which ideally should extend beyond the girder flange to facilitate adjustments during installation. When designing with elastomeric bearings, the shear modulus (G) becomes a critical consideration. It's a material property that significantly impacts bearing performance under variable loading.
Interestingly, the standards also provide guidance on how to consider different types of friction. Static friction, encountered when a load remains stationary, and dynamic friction, present during movement, both have a considerable impact on how a bearing functions. Engineers must design for both situations to ensure the bearing performs consistently across a bridge's lifespan. Design guidelines prioritize accommodating various load types, including longitudinal, transverse, and vertical forces. There's a dedicated Steel Bridge Bearing Design Guide, too, that offers a step-by-step approach, including specifying design criteria, load cases, and choosing the appropriate bearing type.
The AASHTO specifications ultimately aim for cost-effective designs while maintaining functionality and durability during a bridge's construction and maintenance phases. HLMR bearings are specifically engineered to manage substantial movements and rotations under heavy loads. It's a testament to the need for bearings to provide stability and consistent performance in extreme situations. For elastomeric bearings specifically, proper detailing as described in AASHTO LRFD is paramount for ensuring smooth fabrication, installation, and long-term maintenance. There's a surprising amount of nuance here—it’s not just about choosing the right bearing, it’s also about detailing and materials to ensure a successful design.
However, there's always room for improvement. One of the main challenges is the variability in friction coefficients. The coefficients can range considerably between material types and surface conditions, making design a bit of a guessing game. Further research and development is needed to refine the prediction of frictional behavior under dynamic loading, for instance, and account for changing material characteristics across time. Moreover, the standards do not always fully capture the intricate interactions between materials within the bearing system, particularly with the use of coatings or lubricants. A more thorough understanding of how these materials affect friction coefficients could lead to even more reliable and durable bridge designs. Perhaps this will be addressed in future updates.
Understanding Static vs Dynamic Friction in Steel Bridge Bearing Design A Structural Engineering Analysis - Maintenance Strategies and Wear Pattern Assessment Methods
Within the broader context of steel bridge bearing design, particularly when considering the influence of static and dynamic friction, the topics of maintenance strategies and wear pattern assessment methods become critical. The lifespan and reliability of bridge bearings are significantly impacted by wear, which can be accelerated by factors such as improper design parameters, material incompatibility, and environmental conditions. Thus, the implementation of appropriate maintenance protocols becomes paramount. These strategies aim to optimize the performance and extend the functional life of bearings, mitigating the potential for premature failures.
However, effective maintenance isn't just about implementing routine tasks. To truly enhance the bearing's lifespan, we need to understand the mechanisms that cause wear. Detailed assessment methods that evaluate wear patterns play a crucial role in this. By carefully examining the wear patterns present on bearing surfaces, engineers can gain valuable insights into the root causes of degradation. This, in turn, allows for more informed decisions about necessary interventions. Early detection of wear allows for corrective actions that can prevent more significant and costly issues later. Furthermore, through analysis of wear patterns in conjunction with knowledge of maintenance practices and environmental conditions, engineers can gain deeper insights into material behaviour and design approaches that enhance durability.
The relationship between maintenance, wear assessment, and material selection in bridge bearing design is dynamic and interconnected. Recognizing and managing this relationship is essential for minimizing costly repairs and ensuring that bridges remain safe and reliable throughout their intended lifespan. Ultimately, the overarching goal is to enhance the overall performance and resilience of steel bridge bearings in the face of a wide range of operating conditions.
The wear patterns exhibited by bridge bearings are significantly influenced by whether the loading is static or dynamic. In dynamic scenarios, where repeated movements are involved, abrasive wear becomes more pronounced. This leads to the formation of finer wear debris, which can gradually erode the surface integrity of the bearing over time.
It's been suggested that maintaining a very smooth surface finish on steel bearings, specifically aiming for a roughness average (Ra) of less than 0.8 micrometers, can almost double their lifespan. This is primarily due to a reduction in the detrimental effects of micro-pitting, a phenomenon that often gets overlooked during initial design phases.
The coefficient of friction in bridge bearings can be surprisingly variable. It's affected by what we've come to call "friction memory," a phenomenon in which prior loading patterns have a lingering effect on the bearing's frictional behavior. This complicates the predictive models that are often used in the design phase, making things challenging to forecast with accuracy.
Certain bearing materials have critical temperature thresholds that can cause notable changes in their mechanical properties. For example, some polymers can experience a 20% drop in their modulus of elasticity when temperatures exceed 65°C. This sensitivity emphasizes the need for very careful environmental monitoring to ensure materials operate within their intended performance ranges.
When dynamic loads are applied at high speeds, the dynamic friction can decrease unexpectedly, sometimes to coefficients below 0.1. This significant drop in friction poses challenges in controlling the movements of the bearing during quick load transfers, potentially jeopardizing the bridge's structural stability.
The presence of contaminants like oil or dirt can drastically alter friction coefficients, and in some cases significantly increase wear—up to 30%—underlining the vital role that regular maintenance plays in mitigating unforeseen wear escalation.
Repeated cycles of temperature change can lead to fatigue-related deformation within bearing materials. This cumulative effect contributes to long-term wear patterns that might go unnoticed until significant damage has accumulated. This necessitates the development and deployment of monitoring systems that provide early warnings of potential issues.
During loading cycles, steel bearings undergo both elastic and plastic deformation. The latter, in particular, can contribute to localized wear. Understanding these deformation mechanisms is crucial for making informed material choices and extending bearing lifespans.
Current models used for wear prediction frequently fail to fully account for changes in lubrication conditions. The incorporation of bio-inspired lubrication methods, which draw inspiration from natural lubrication systems, is a burgeoning research area that could substantially enhance the accuracy of these models.
Elevated friction in bearings under heavy loads can cause considerable increases in temperature. This, in turn, creates a self-reinforcing cycle, worsening wear patterns and potentially causing localized melting of the bearing surfaces. This is a potential failure mechanism that needs careful consideration during the design phase.
More Posts from aistructuralreview.com: