Finite Element Analysis Enhancing Construction Safety and Efficiency
Finite Element Analysis Enhancing Construction Safety and Efficiency - Streamlining design iterations for resource management
Improving the process of refining structural designs is critical for managing resources effectively within construction, particularly when computational tools like Finite Element Analysis are employed. Integrating FEA into the design loop allows engineering teams to rapidly simulate performance under various conditions virtually, providing valuable feedback that minimizes the need for slower, more resource-intensive physical validation methods. This virtual testing capability aids in making informed decisions earlier, thereby conserving material, time, and labor – key resources on a project. While this approach can certainly sharpen design accuracy and contribute to heightened efficiency and safety standards on site, it’s crucial to critically assess the output. Simulation results are dependent on the underlying models and assumptions, which may not always perfectly capture real-world complexities. Navigating the future involves skillfully leveraging powerful analytical techniques alongside rigorous engineering scrutiny to ensure robust and responsible design evolution.
Delving into the application of finite element analysis during the design phase reveals some interesting avenues for managing resources more effectively in construction projects:
The sophisticated capabilities now present in FEA packages offer the potential for what's termed topology optimization. This isn't just about checking if a design works; it's about the software proposing forms that use the absolute minimum amount of material – be it concrete or steel – necessary to carry the anticipated loads under various conditions. The idea is to move beyond traditional section checks towards structures where every ounce of material serves a precise purpose, directly aiming to reduce the embodied resource footprint from the outset. One might ponder, however, how readily these often unconventional shapes translate into practical, cost-effective construction processes on site.
Consider the long game: FEA models can incorporate material behaviors that change over time, like the creep and shrinkage inherent in concrete. By accounting for these effects early in the design iterations, engineers can potentially fine-tune details or overall structural schemes to minimize the stresses or deformations that would otherwise necessitate significant repair or maintenance down the line. This forward-thinking approach to design seeks to conserve resources not just during construction, but over the decades a structure is intended to stand, reducing the need for materials and labor in future interventions.
A more immediate, practical benefit stemming from FEA-driven design precision is the potential reduction in material waste generated on the construction site. By enabling engineers to specify material quantities with greater accuracy – understanding exactly how much concrete or steel is needed for optimized elements – there should theoretically be less over-ordering. Furthermore, a clearer picture of required cuts and component sizes could lead to more efficient use of raw materials delivered to the site, reducing scrap and the associated disposal burdens.
Looking specifically at steel structures, optimizing the size and geometry of structural elements and their connections through iterative FEA can have a ripple effect on the fabrication process. Simpler connections, fewer unique components, and perhaps more standard sizes where possible could lead to less complex work in the fabrication shop. This streamlining means potentially fewer specialized processes, less labor time spent on intricate detailing, and thus a reduced resource requirement during the manufacturing stage before anything even arrives on site.
Finally, even the temporary aspects of construction are ripe for optimization through FEA. Simulating complex construction sequences, heavy lifting operations, or the loads on temporary shoring allows engineers to design these temporary works themselves more efficiently. This foresight means avoiding the need to over-engineer temporary structures 'just in case', saving on the materials (like temporary steel or timber), labor, and equipment time required for these non-permanent, yet resource-intensive, parts of the construction process.
Finite Element Analysis Enhancing Construction Safety and Efficiency - Where FEA provides insight into complex structures
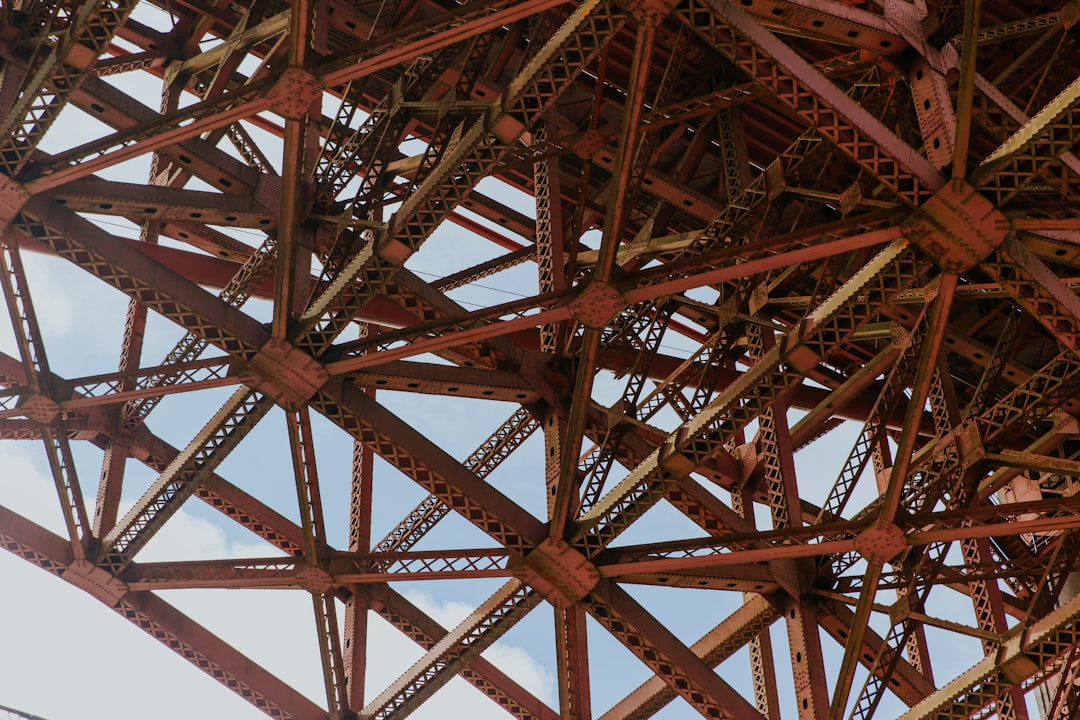
For designs that move beyond standard practice or feature intricate geometry, finite element analysis offers a powerful lens into structural response. The approach involves numerically dissecting a complex form into numerous simpler pieces, allowing engineers to simulate how the overall system behaves under diverse physical influences, including complex loading conditions. This capability is particularly valuable when traditional methods face limitations in predicting detailed stress distributions or deformation patterns in unconventional structures. However, the validity of the analytical outcomes inherently relies on the assumptions built into the model and the quality of the input data, requiring experienced interpretation. Ultimately, FEA provides deep insights into structural integrity and potential vulnerabilities, contributing significantly to understanding how a complex design might perform in the real world.
One area where finite element analysis truly distinguishes itself is in peeling back the layers of complexity inherent in modern structural forms and loading scenarios. Traditional hand calculations or simpler analytical methods often struggle to provide sufficient resolution for assemblies that deviate from standard shapes or experience non-uniform environmental effects.
For instance, FEA allows an engineer to scrutinize localized stress peaks that might arise from intricate joint details or sudden changes in material sections – areas where failure might initiate unexpectedly under load. It provides a detailed picture of how stresses are distributed, helping to identify potential weak points that aren't immediately obvious from an overall design perspective.
Furthermore, moving beyond static conditions, FEA is indispensable for exploring how structures behave dynamically. It can predict a structure's natural tendencies to vibrate or sway at certain frequencies and simulate its response to transient, time-varying forces such as wind buffeting or seismic ground motion. This insight is crucial for ensuring serviceability and safety under fluctuating real-world conditions, not just peak static loads.
Understanding temperature effects is another significant application. By modeling thermal gradients and expansion/contraction characteristics, FEA can reveal how temperature variations induce internal stresses and deformations, particularly in large structures or those combining materials with different thermal properties. This helps in designing appropriate provisions like expansion joints to mitigate potential thermal-induced problems.
The method is also powerful in uncovering buckling instabilities. For slender elements or complex arrangements under compressive forces, FEA doesn't just flag a potential buckling issue; it can illustrate the specific modes, or shapes, that the structure might assume as it becomes unstable, allowing engineers to precisely target stiffening or geometry modifications.
Finally, FEA provides a valuable visualization of the intricate paths that loads follow as they travel through a structural system. This helps clarify how forces are distributed across interconnected elements and identifies areas or members that might be carrying unexpectedly high or unusual combinations of forces, offering a clearer understanding of the structural behaviour beyond simplified assumptions.
Finite Element Analysis Enhancing Construction Safety and Efficiency - Considering the model limitations in practical application
Even as Finite Element Analysis becomes more integrated into construction workflows, it's crucial to maintain a clear perspective on the inherent boundaries of the models used. While offering significant power to simulate complex structural responses, these models are by necessity simplifications of the intricate reality of a building site and the materials themselves. Relying solely on the numerical output without a deep understanding of the assumptions made about material behavior, connections, and applied loads can potentially lead to designs that appear sound on screen but encounter unexpected challenges, inefficiencies, or even safety risks during actual construction. The ease and speed with which simulations can be run might, at times, create an impression of definitive truth, potentially overshadowing the need for practical engineering judgment and, where possible, validation against empirical data or site observations. Ultimately, navigating the practical application of FEA effectively requires critically assessing what the model represents, what it omits, and how those limitations could manifest when the design moves from the digital realm to physical execution, influencing both the safety of the process and the efficiency of resource use.
Stepping back from the impressive capabilities of finite element analysis, it's crucial to confront the inevitable gap between the tidy digital model and the often untidy reality of construction. One immediately grapples with defining boundary conditions; translating the complex interaction of a footing on variable soil or the semi-rigid behavior of a bolted connection into the perfect pins and fixed points of the software is a simplification fraught with potential inaccuracies that can profoundly skew results. Likewise, while FEA demands precise values for material properties, actual concrete cures with varying strength, and steel exhibits batch-to-batch inconsistencies and residual stresses from manufacturing processes – variability the deterministic model struggles to capture without advanced statistical methods. The intricate dance of contact between different structural components, like floor slabs bearing on beams or precast panels meeting, presents another significant challenge; accurately modeling these surfaces touching, sliding, and potentially separating requires immense computational effort, often forcing engineers towards simplified assumptions that might miss crucial localized stress concentrations or load transfer nuances. Furthermore, the ideal geometries assumed by the software overlook the inevitable imperfections present in constructed elements – the slight out-of-straightness of a column, the misalignment of a beam – which, particularly for slender members, can dramatically reduce actual buckling capacity compared to the pristine model prediction. Ultimately, truly validating complex FEA models against full-scale reality remains a significant hurdle, as acquiring the detailed, distributed strain, displacement, and force data needed from actual operational structures to prove or disprove the simulation's fidelity is logistically and economically challenging. The model is a powerful tool, certainly, but its output must always be viewed through a lens of informed skepticism, acknowledging these inherent translation difficulties from the physical world into the computational realm.
More Posts from aistructuralreview.com: