New Features in ANSYS LS-DYNA 2024 A Deep Dive into Enhanced Multiphysics Capabilities
New Features in ANSYS LS-DYNA 2024 A Deep Dive into Enhanced Multiphysics Capabilities - Fast Lanczos Eigenmodes Solver for Large Model Computation
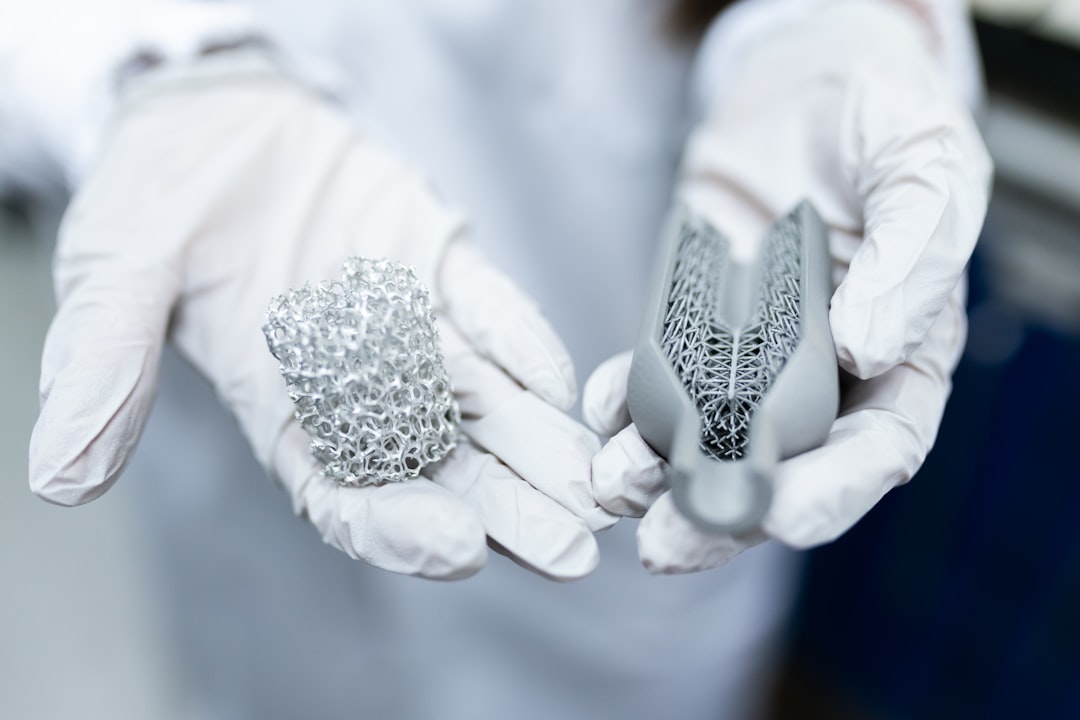
ANSYS LS-DYNA 2024 introduces a new Fast Lanczos Eigenmodes Solver specifically designed to tackle the challenges of calculating eigenmodes in very large models. This new solver promises a substantial performance boost, with reports suggesting it's about eight times faster than previous approaches. This speed improvement is particularly valuable in fields like Noise, Vibration, and Harshness (NVH) analysis, where a large number of eigenmodes are often needed. The Fast Lanczos solver achieves this speed by employing the Block Shift and Invert Lanczos algorithm, which optimizes the process of extracting multiple eigenmodes while maintaining acceptable accuracy. Moreover, the existing PCG Lanczos eigensolver has been refined to further enhance the process of finding eigenvalues and eigenvectors, now utilizing multiple iterative solutions. The integration of these new and improved algorithms demonstrates a noteworthy advance in LS-DYNA's capabilities for dynamic analysis and complex structural simulations. While the speed increase is promising, users should carefully evaluate the accuracy trade-offs, particularly when working with highly complex systems.
LS-DYNA 2024 R1 introduces a new Fast Lanczos Eigenmodes Solver, a welcome addition for handling very large models. This solver utilizes the Block Shift and Invert Lanczos algorithm, which has shown promise in significantly reducing computation time, achieving around 8x speedup in some cases like an electric vehicle model. This performance boost is especially valuable when focusing on calculating a large number of eigenmodes, a crucial step in NVH (Noise, Vibration, and Harshness) studies. While faster, it's important to note that this approach prioritizes speed, and one should always consider if the slight potential reduction in accuracy is acceptable for their specific application.
The implementation doesn't stop with the new solver. LS-DYNA's existing PCG Lanczos eigensolver has received updates as well, enhancing the ability to extract eigenvalues and eigenvectors using iterative solves. This improvement adds to a suite of existing methods like Block Lanczos, Supernode Subspace, and QR damped, which are now joined by the fast Lanczos.
One of the intriguing aspects of this development is the integration with Ansys Sound Pro, which creates a powerful NVH workflow. In addition, LS-DYNA's capabilities expand further with the incorporation of fluid added mass modeling, potentially enriching analyses of structural vibration simulations in complex environments. It's interesting to consider the combined impact of these advancements on the future of fluid-structure interaction analyses.
The core math behind LS-DYNA's eigenvalue solutions remains the traditional approach of solving the classical eigenvalue problem, which relies on stiffness and mass matrices. The new solver, however, leverages sparse matrix methods to enhance efficiency, making it more memory-friendly for those large models that were becoming prohibitive. This improvement in the handling of large matrix problems is a testament to the evolution of numerical methods, pushing the limits of what can be feasibly simulated. However, this ongoing advancement in numerical methods also begs the question of how to continually verify and validate the results as problem complexity increases.
New Features in ANSYS LS-DYNA 2024 A Deep Dive into Enhanced Multiphysics Capabilities - Machine Learning Enhanced Deep Material Network
ANSYS LS-DYNA 2024 introduces a new approach to material modeling with the Machine Learning Enhanced Deep Material Network (DMN). This innovative framework leverages machine learning to understand the intricate microstructures found in materials like Short Fiber Reinforced Composites (SFRC). These composites present unique challenges for conventional material models due to their complex, nonlinear, and anisotropic behavior. The DMN tackles these complexities by essentially learning the material's behavior from detailed simulations of representative volume elements (RVEs).
The DMN uses a four-layer deep learning structure to capture the relationships between the microstructural features and the overall material response. By training the model on high-fidelity RVE data, LS-DYNA can more accurately predict the material's behavior under various loading conditions. This approach promises more efficient multiscale modeling, allowing for improved simulations of lightweight structures in demanding applications, like those found in the automotive and electronics industries.
While the DMN offers significant improvements in material modeling, there are also some considerations. Because the training data and underlying code are proprietary, the transparency and verifiability of the DMN's models are somewhat limited. Further research and development might be needed to fully address these aspects. Nevertheless, the DMN represents a notable step forward in the evolution of multiscale material modeling within LS-DYNA, promising more accurate and efficient simulations of complex composite materials.
ANSYS LS-DYNA 2024 introduces a new capability called the Deep Material Network (DMN), which leverages machine learning to model material behavior in a more sophisticated way. It's designed to capture the intricate internal structures of materials, particularly composites, by using representative volume elements (RVEs). This allows the software to simulate the complex, nonlinear responses of these materials, especially short fiber reinforced composites (SFRCs), which are difficult to handle using traditional micromechanical models.
The DMN is trained using data from high-fidelity RVE simulations, essentially teaching the model how these materials behave under different conditions. The network itself has a four-layer deep learning structure, making it efficient for multiscale simulations. One interesting aspect is that the DMN can help us understand the parameters involved in material modeling, leading to better predictions across a wider range of material and geometric complexities. This could be particularly beneficial in lightweight structural designs, important for areas like automotive and electronics where SFRCs are becoming popular.
The combination of machine learning with conventional simulation methods is showing a lot of promise. Initial results suggest that it can be quite accurate. However, it's worth noting that the training data and LS-DYNA's source code are proprietary, meaning the specific details behind the DMN are not publicly available. This aspect hints at the ongoing development and refinement of this technology.
Overall, the DMN represents a major step forward in multiscale modeling, particularly for composites. It's exciting to see how this integration of machine learning is improving the ability to predict the behavior of complex materials. While promising, researchers will likely want to keep exploring the limits of the approach and rigorously validate its accuracy, especially when dealing with highly complex scenarios. It'll be interesting to see how the DMN develops further, what limitations may emerge, and how it might reshape the field of material modeling over time.
New Features in ANSYS LS-DYNA 2024 A Deep Dive into Enhanced Multiphysics Capabilities - Extended ID Limits in Double Precision Version
ANSYS LS-DYNA 2024 introduces an expanded range of IDs in its double precision version. Part, material, and property IDs can now exceed 10 digits, providing more flexibility for handling very complex simulations with a large number of individual parts. This change can be useful for organizing large, intricate models. However, this increase in ID capacity brings with it a few complications. Since the double-precision version generates larger plotfiles by default, users may encounter size issues during the post-processing stage. As a result, it's generally recommended to save output files in the 32-bit format to avoid any difficulties. Furthermore, simulations using double precision typically experience a 15-30% increase in runtime. To address this performance overhead, it's generally suggested to run a two-step process, starting with domain decomposition in double precision and then transitioning to single precision for the remainder of the simulation. Although these features increase the complexity of models that can be addressed, users must carefully weigh the added capabilities against the impacts on simulation runtime and data management.
ANSYS LS-DYNA 2024 introduces an extended limit for identifiers like Part, Material, and Property IDs when using the double precision version. This change allows for IDs exceeding 10 digits, a significant jump from the previous limitation. While this opens up possibilities for far more complex models, it's important to understand the ramifications.
To handle these extended IDs, LS-DYNA provides a special double precision version of LS-PrePost (version 410 and later). This version is essential for managing input files or D3PLOT files that utilize the extended IDs. However, this introduces a potential concern: plot files written in double precision by default can be substantially larger, possibly leading to problems during postprocessing. To avoid this, it's generally recommended to save these files in 32-bit format.
Interestingly, running simulations in double precision, while providing increased accuracy, comes at a cost – a performance hit of roughly 15-30%. To mitigate this, a two-step approach might be more efficient: initial domain decomposition can be done in double precision, and then the remainder of the simulation run in single precision. This balances precision with reasonable run times.
The broader context of these changes is LS-DYNA's continued focus on enhancing crash safety features. This includes providing insights into which keyword features contribute to memory consumption, enabling users to refine their models and avoid potential problems. They're taking steps to help engineers address these issues systematically, which is a promising development.
Moreover, the emphasis on multiphysics simulation capabilities continues, following the trajectory set in previous releases. This focus on complex simulations is underscored by efforts to streamline input file management, making it easier to handle large jobs. The ability to split entire input files into smaller, more manageable sub-files can be a major productivity boost for handling increasingly complex models. This dovetails nicely with the support for high-performance computing (HPC) and Ansys Cloud, enabling simulations of a scale previously challenging to achieve.
LSOPT and LSTaSC, tools utilized in optimization and design of experiments, respectively, have received updates related to the transitions between single and double precision. While it’s not immediately clear how significant these updates are, they are a sign of ongoing development and improvements to the broader workflow.
Overall, the extended ID limits, while beneficial, should be considered alongside the potential performance trade-offs and the potential complexities introduced during postprocessing. Nevertheless, the ability to build and simulate larger, more detailed models is a significant advancement for LS-DYNA. It will be fascinating to see how this expanded capability impacts various engineering fields in the years to come.
New Features in ANSYS LS-DYNA 2024 A Deep Dive into Enhanced Multiphysics Capabilities - New Optimization Algorithms and Multifile Import Options
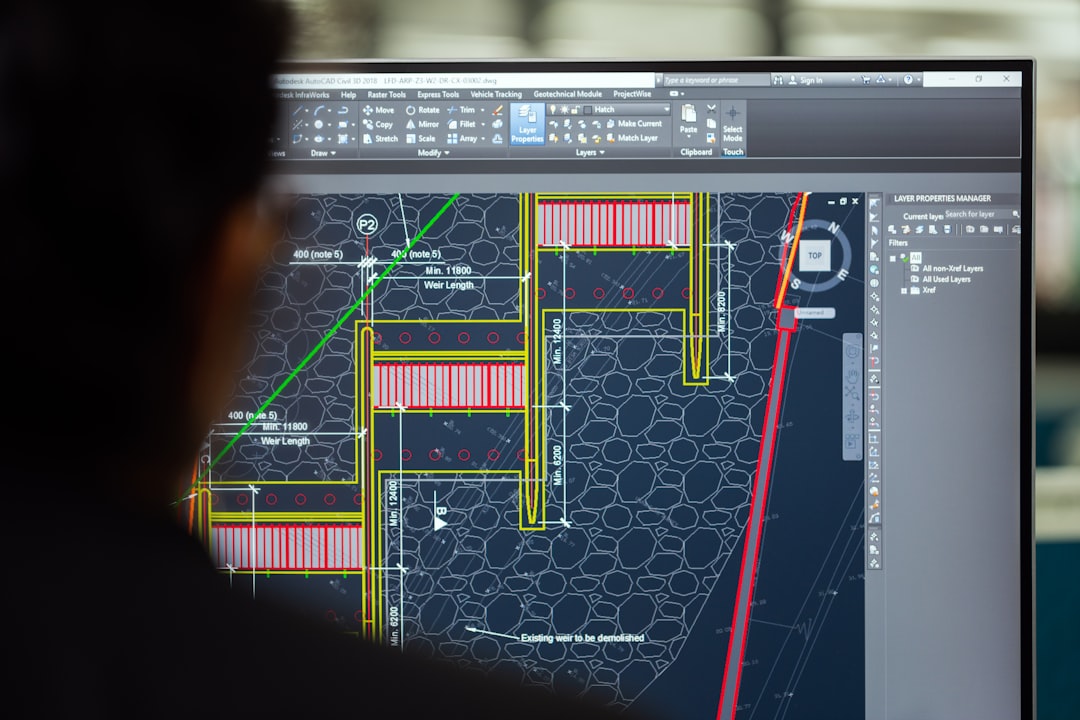
ANSYS LS-DYNA 2024 includes several enhancements to optimization and file handling capabilities, contributing to its growing multiphysics simulation prowess. The update introduces new optimization algorithms, particularly a sequential global optimization method based on Radial Basis Function networks (found in LSOPT Version 42). This approach aims for better performance, especially in complicated simulations, and incorporates improved user interfaces for parameter identification and metamodel visualizations within LSOPT Version 32.
Furthermore, LS-DYNA now accommodates multifile import, a feature allowing users to divide large input files into smaller, more manageable sections. This can be a significant asset for handling large and complex simulation setups, fostering improved workflow management. While these features represent a step towards tackling even more elaborate simulations, users should be aware of the potential impact on simulation performance and data management when employing them. It remains to be seen how effectively these features integrate into real-world projects and whether they will lead to widespread adoption due to their increased complexity.
ANSYS LS-DYNA 2024 introduces some intriguing new optimization algorithms, aiming to make complex multiphysics simulations more efficient and adaptable. It's interesting to see how they've tackled the challenges of managing these complex simulations, especially with the new multifile import options. This new capability lets users break down large LS-DYNA input files into smaller, more manageable chunks, potentially leading to better organization and control over the entire simulation process. It's a welcome change, but whether it genuinely improves the workflow for all types of simulations remains to be seen.
It's also worth noting that the double-precision version now supports longer Part, Material, and Property IDs, which could be useful for handling extremely complex models. However, it comes with a few caveats. Plot files in this version are larger by default, which can cause headaches during postprocessing. There's also a performance hit of roughly 15-30%, suggesting that users might want to explore using a hybrid approach – double precision for the initial stages and then switching to single precision for the remainder of the simulation. The effectiveness of this workaround likely depends on the specific problem, and it might not be a viable solution for every case.
One of the most interesting developments is the sequential global optimization strategy using Radial Basis Function networks within LSOPT Version 42. The validation through comparative studies suggests that this approach might significantly improve performance. LSOPT Version 32 also incorporates new GUI features related to parameter identification and metamodel plotting. These updates are intriguing, but I'm curious to see if these enhancements are genuinely useful for a wide range of engineering applications.
Another important development is the introduction of two-scale co-simulation capabilities. This approach aims to improve efficiency in explicit dynamic analysis by separating the problem into a local-scale and global-scale component. It's an intriguing concept, but its practical implications for real-world applications need to be thoroughly evaluated. Overall, the updates related to optimization tools highlight a growing trend: they are being designed for multidisciplinary optimization, fostering the possibility of integrating LS-DYNA with non-LS-DYNA solvers. It's a forward-looking move that suggests the software is aiming to integrate with a wider range of simulation tools.
Additionally, the update includes advanced implicit and explicit solvers, offering improved workflows for handling complex simulation scenarios. This is an ongoing trend in simulation software, as the field demands increasingly robust capabilities for tackling modern engineering challenges. The continued emphasis on multiphysics simulation in this release suggests that ANSYS is keen on expanding the software's application in a diverse array of engineering domains. It's exciting to consider the potential impact of these new features as the field continues to evolve and become more sophisticated. While the promise of enhanced simulation capabilities is exciting, careful validation and evaluation will be crucial to ensure that these new tools truly deliver on their potential in practical applications.
New Features in ANSYS LS-DYNA 2024 A Deep Dive into Enhanced Multiphysics Capabilities - Addition of Three Multiphysics Solvers Expanding Application Range
ANSYS LS-DYNA 2024 introduces three new multiphysics solvers: incompressible computational fluid dynamics (ICFD), electromagnetics (EM), and compressible CFD. This addition significantly broadens the software's capabilities, allowing simulations across a wider array of engineering fields. The goal is to create a more unified simulation experience, fostering better integration between previously distinct disciplines. The new ICFD solver stands out with its streamlined workflow, requiring only surface meshes for defining the geometry instead of the usual volume meshes, thus simplifying setup and potentially speeding up simulation time. Additionally, improvements in fluid-structure interaction (FSI) extend the software's reach into areas like crash simulations and other complex multiphysics scenarios. While this offers substantial potential, users may need to contend with the challenges of properly configuring hardware for optimal simulation performance. Overall, the inclusion of these solvers demonstrates a commitment to enhancing LS-DYNA's role as a powerful tool for various industries relying on advanced computational simulation. It remains to be seen how fully these new capabilities address the specific needs and complexities of various engineering fields.
ANSYS LS-DYNA 2024 has introduced three new multiphysics solvers: Incompressible CFD (ICFD), Electromagnetics (EM), and Compressible CFD. This addition expands the simulation capabilities of LS-DYNA into a wider range of applications where understanding the interplay between different physical phenomena is critical. The aim is to create a unified simulation environment, moving towards a more integrated approach for multiphysics analyses. It seems this trend is intended to make it easier for users to explore complex phenomena and reduce the need for separate software tools. It's important to see how this strategy translates to real-world problems and whether it's as seamless as it seems from the software's perspective.
LS-DYNA also has a new version of LSPrePost (4.1.1) to accommodate these changes, particularly the ability to handle longer part, material, and property IDs—now exceeding 10 digits—which is needed for some of these complex simulations. However, this extended ID support is tied to the double-precision version, and it generates larger plot files which could potentially lead to issues with post-processing if not managed properly. It's interesting how this increased precision comes at the expense of file sizes, highlighting a tradeoff between accuracy and post-processing efficiency that engineers need to consider carefully.
There's a continued effort to improve the user experience and leverage AI in the broader ANSYS suite, including optimization tools and material modeling. This can be helpful, but one might wonder if it might add another layer of complexity that requires deeper knowledge of the AI methods being employed. On the other hand, improved integration with hardware is also underway. The LS-DYNA team claims that integrating NVIDIA and Supermicro hardware can help to optimize these multiphysics simulations, although configuring the hardware for ideal performance might be a hurdle itself.
The software also supports fluid-structure interaction (FSI) simulations, which is a significant capability. This has implications for crash simulations and more advanced multiphysics interactions in areas like robotics and aerospace. In a separate development, ANSYS' collaboration with TSMC allows for optimization of multiphysics for photonics, which has exciting potential in the development of cutting-edge semiconductor technology.
Ultimately, the driving force behind these additions is the desire for a more scalable and accurate way to predict engineering behaviors across a wider array of industries. It's stated that the long-term goal of this strategy is to meet the needs of increasingly important fields like AI, cloud computing, and HPC communication, all of which rely on sophisticated simulation and modeling tools. It's important to follow how effectively LS-DYNA's enhanced capabilities address these specific domains, as the challenges can be quite varied. This is certainly a development worth watching in the coming years.
New Features in ANSYS LS-DYNA 2024 A Deep Dive into Enhanced Multiphysics Capabilities - LSPrePost Tool Updates for New Input Formats and Double Precision
LS-DYNA 2024's LSPrePost tool has undergone improvements, notably incorporating double precision capabilities. This allows for handling longer IDs for parts, materials, and properties, extending beyond the previous limit of 10 digits. While beneficial for intricate models with many components, it comes with a caveat: the double precision version produces larger plot files by default. To avoid potential problems during post-processing, it is recommended to output files in a 32-bit format. Furthermore, while double precision increases accuracy, it also tends to increase simulation runtime. To potentially improve efficiency, a two-step approach might be suitable: using double precision for the initial domain decomposition and transitioning to single precision for the remaining calculations. These changes highlight LS-DYNA's ongoing effort to optimize for large-scale simulations while managing computational costs and maintaining usability. It remains to be seen how these trade-offs impact real-world workflows and whether they ultimately lead to a net benefit for users.
LS-DYNA 2024's double precision version introduces a significant change: the ability to use Part, Material, and Property IDs with more than 10 digits. This increased capacity is a boon for handling highly complex models with a vast number of individual components, making organization much easier. However, this improvement comes with the side effect of larger plot files generated by default. These larger files can lead to post-processing slowdowns and storage issues, making it crucial for users to be mindful of file sizes and potentially utilize 32-bit output formats to minimize these problems.
Furthermore, achieving this higher precision comes at a price—simulation runtime increases by around 15-30%. This trade-off between accuracy and speed might require a rethinking of how simulations are conducted. A hybrid strategy seems promising—using double precision for initial decomposition and then switching to single precision for the rest of the run. This approach could help manage the performance burden without sacrificing much accuracy.
Fortunately, LSPrePost has also been updated (version 4.1.1) to handle these new complexities, specifically the extended IDs and larger files. While it's a needed update, it emphasizes the growing complexity of the software. Users will have to familiarize themselves with these changes to keep their post-processing workflow running smoothly.
The impact of these changes ripples through the entire multiphysics simulation domain. It allows for more sophisticated analyses, particularly in applications like automotive and aerospace, where engineers need to model a wider range of interactions. It's clear this extended ID capacity and precision is enhancing LS-DYNA's capabilities for multiphysics problems.
But with this expansion in capacity comes a growing reliance on more specialized skills in data management and post-processing. Engineers will need to develop a good understanding of the latest tools and techniques to ensure that the insights from these more detailed simulations are easily accessible. The software is also pushing toward a more integrated environment, with optimization and design tools gaining greater prominence. While potentially beneficial, this trend might create a steeper learning curve for users accustomed to a less tightly integrated workflow.
The update also shows a continued focus on simplifying the management of very large models. The ability to split complex input files into smaller sections is particularly helpful for larger teams or projects. The developers also appear to be placing increased emphasis on crash safety, which makes sense given the growing importance of that area in various industries. This effort includes helping users identify how different keyword settings contribute to memory usage, a useful feature for optimizing the performance of complex simulations.
Overall, these updates, while pushing LS-DYNA into new territories of simulation detail and complexity, emphasize the crucial role of careful planning and attention to detail. The trade-offs between precision, speed, and data management are unavoidable and need careful consideration. It will be interesting to see how these new features are embraced and integrated into the daily work of researchers and engineers, as well as the direction this trend takes in future releases.
More Posts from aistructuralreview.com: