Understanding Steel-on-Steel Friction Coefficients Impact on Modern Structural Design and Safety Standards
Understanding Steel-on-Steel Friction Coefficients Impact on Modern Structural Design and Safety Standards - Steel Surface Treatment Impact on Friction From 1970 to 1994
Between 1970 and 1994, research into steel-on-steel friction highlighted the significant role of surface treatments in influencing the friction coefficient. Studies revealed a typical range of 0.13 to 0.14 for treated steel surfaces, with specific treatments like ion-nitriding showing an average coefficient around 0.138. This suggests surface treatments can subtly alter friction, even compared to standard ground surfaces.
Interestingly, lubrication emerged as a major factor in friction reduction, with estimates dropping to around 0.11 under consistent pressure. This emphasizes the importance of considering operational conditions when designing structures. Other factors like surface roughness and the immense mechanical pressures encountered (up to 146 kN in tests) also proved to affect friction. The interplay between surface treatments, environmental conditions, and mechanical loading ultimately impacts friction. Understanding this complex interplay is crucial when formulating safety standards and design considerations for modern structures. The wide range of factors at play needs careful consideration for the safe and reliable performance of steel structures.
Between 1970 and 1994, researchers investigated how various steel surface treatments, including ion nitriding, impacted friction characteristics. Studies consistently revealed friction coefficients in the 0.13 to 0.14 range for a variety of surface treatments when steel rubbed against itself. For instance, ion-nitrided steel showed an average friction coefficient of about 0.138, which was comparable to finely ground surfaces.
Researchers attempted to define static and dynamic friction coefficients under different surface conditions and environmental factors. This period saw a lot of focus on understanding how contact pressure, reaching up to 146 kN in some tests, influences friction. These high loads highlight the considerable mechanical stresses that can be present at the steel interfaces. The studies also consistently revealed that lubrication significantly reduced the coefficient of friction. For example, lubricated steel-on-steel contact under a constant load showed a friction coefficient estimate of around 0.11.
The research from this era found that surface roughness plays a vital role in friction, though the impact seemed to diminish at certain points. For example, the friction coefficient remained relatively constant at a surface roughness of 0.46 micrometers. The studies during this era also found a strong link between surface conditions, such as the presence of oxide layers and near-surface modifications, and both friction and wear characteristics. The interplay between surface topography, hardness, and chemical reactivity, along with the influence of lubricants, was increasingly recognized as crucial to the observed frictional behavior.
Furthermore, researchers uncovered the impact of environmental conditions on friction coefficients, noting how exposure to air and even seawater could alter steel surface characteristics and ultimately change friction. This highlighted the complexity of predicting friction in real-world scenarios. It became increasingly clear that friction coefficients are the result of complex interactions between multiple factors: surface treatment, applied loads, the nature of the contact interface, and environmental influences. This complex interplay of factors has significant implications for the development of modern structural design and safety standards that must account for these considerations to ensure long-term reliability and safety.
Understanding Steel-on-Steel Friction Coefficients Impact on Modern Structural Design and Safety Standards - Modern Testing Methods for Steel to Steel Contact Under Variable Load Conditions
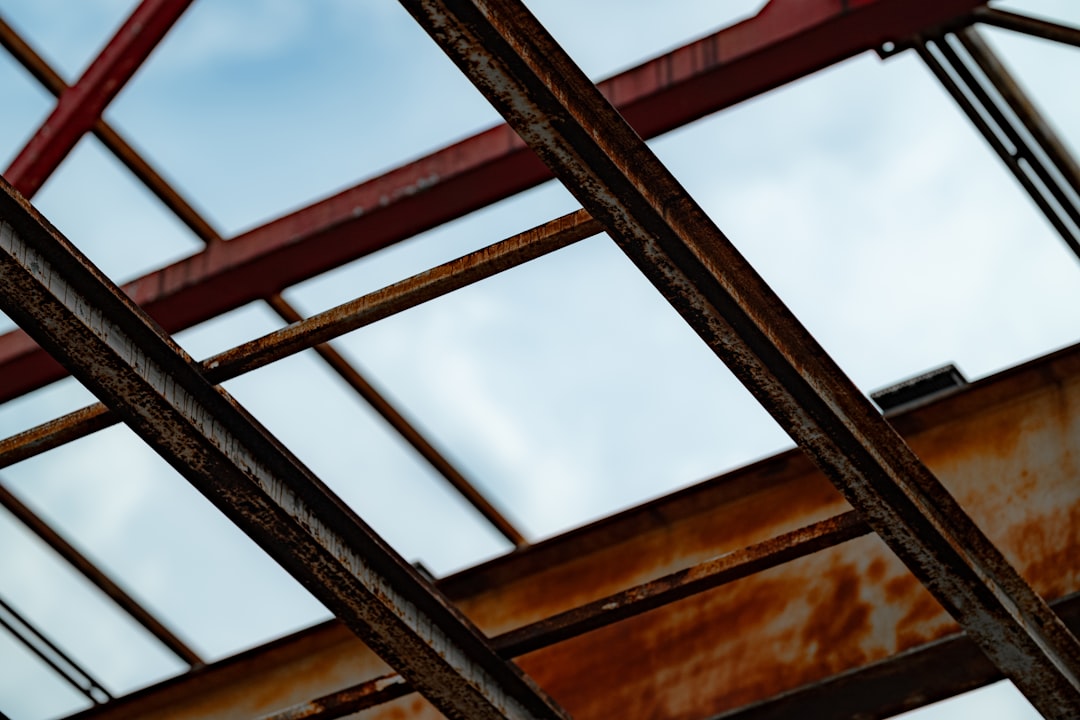
Modern methods for testing steel-to-steel contact under varying loads have evolved to better understand the complex nature of friction coefficients. Previously, models often simplified friction by assuming a constant value, which isn't accurate in real-world scenarios where contact pressure and load constantly change. Recent research has shown how sliding speeds and environmental factors greatly impact friction, highlighting the need to precisely model these conditions. This has implications for design reliability, especially in structures subjected to dynamic loads.
We now recognize that friction coefficients aren't static; they fluctuate based on changing contact pressure and loading scenarios. While this has been known for some time, accurately capturing these fluctuations in structural models has been challenging. Consequently, design standards are adjusting to account for these variations, particularly when safety and performance under dynamic loads are critical. The focus is shifting towards more sophisticated friction modeling techniques to address the complexities of modern structural engineering. Failing to account for the variable nature of friction coefficients can lead to unreliable or unsafe structural designs, especially in environments that experience changing loads and conditions. This is particularly important given the increase in complex loading scenarios seen in modern infrastructure.
The study of steel-on-steel friction has moved beyond static coefficients, embracing more sophisticated methods to capture its dynamic nature under changing loads. Researchers are now employing real-time sensors to track the friction coefficient during loading, revealing how it evolves in a transient manner. This detailed approach allows us to better understand how friction behaves in real-world conditions, particularly under cyclical loads.
Computational tools, especially finite element analysis (FEA), offer exciting possibilities for simulating friction under various load and environmental conditions. While physical testing remains crucial, FEA allows us to refine designs with potentially fewer physical tests, optimizing both speed and accuracy. Furthermore, a deeper understanding is emerging regarding how the very structure of steel influences friction. The density of dislocations and the size of grains within the material, factors often influenced by surface treatments, can drastically alter the frictional characteristics of steel surfaces. This understanding opens new avenues for manipulating the frictional behavior of steel through targeted material processing.
Recent investigations have discovered that the friction coefficient isn't merely a function of load but exhibits a curious hysteresis effect. It seems the loading and unloading paths have a significant impact due to the steel's tendency to deform and recover. This further emphasizes the complexity of steel-on-steel friction and necessitates a careful accounting of loading history when making design decisions.
The advent of high-speed cameras and advanced optical techniques has given us an unprecedented view into the wear mechanisms of steel surfaces during dynamic loading. Observing these wear patterns in real-time provides valuable insights into how steel fatigues and ultimately fails, which is incredibly helpful when it comes to improving material selection and design.
Our understanding of friction has also become more microscopic. Contact mechanics now focuses on the interactions of asperities—the tiny irregularities on the surfaces—as the key drivers of friction and wear. This highlights how surface roughness, beyond just simple average measures, plays a more intricate role than previously imagined.
Interestingly, damping properties within certain steel grades have been linked to friction characteristics under dynamic loads. This opens up the possibility of manipulating friction through material selection alongside surface treatments, providing an extra layer of control for engineering applications.
New techniques like acoustic emission monitoring are being used to identify the very early stages of wear during friction tests. This allows us to develop more proactive maintenance strategies that improve the safety and longevity of structures relying on steel-on-steel contact.
The advent of nanotechnology and advanced coatings for steel provides an exciting opportunity for tailoring friction at the atomic level. This suggests that very precise modifications at a sub-microscopic scale can significantly improve the overall performance of steel interfaces under dynamic loading conditions.
However, we've also discovered that real-world friction coefficients sometimes diverge from laboratory results. This underlines the need for a holistic approach to friction studies, one that combines advanced theoretical modeling with empirical data obtained from field tests. Only then can we ensure a high degree of predictive accuracy for structural designs that rely on steel-on-steel connections.
Understanding Steel-on-Steel Friction Coefficients Impact on Modern Structural Design and Safety Standards - Temperature Effects on Steel Friction Coefficients in High Rise Construction
Temperature variations significantly influence the friction characteristics of steel-on-steel connections, a crucial consideration in high-rise building design. The behavior of steel structures, especially columns and frames, can change dramatically under different temperature conditions, affecting their performance in ways that may not be immediately obvious, particularly in older buildings with concealed structural elements. For instance, high temperatures can impact the fire resistance of critical components like load-bearing columns, making it essential to thoroughly analyze their behavior in extreme heat to guarantee structural integrity.
Current fire safety standards largely rely on prescribed rules that may not adequately capture the dynamic complexities of real-world fire scenarios and the range of temperature fluctuations these can produce. This has led to a shift towards more performance-based design guidelines that explicitly integrate temperature effects and fire behavior into structural assessments and designs.
Understanding how temperature fluctuations alter the steel-on-steel friction coefficient is vital for ensuring the stability and safety of modern high-rise structures. This understanding is especially critical as we build taller and more complex structures that face increasingly variable environmental and loading conditions. It's vital to incorporate these understandings into the design phase of high-rise building projects for improved safety and reliability.
The frictional behavior of steel, especially in the context of high-rise structures, is intricately linked to temperature variations. It's becoming increasingly apparent that elevated temperatures can modify the friction coefficients between steel surfaces, potentially influencing the overall structural performance of these buildings. This is particularly crucial when considering the dynamic behavior of steel columns and frames during load assessments, as the temperature changes impact their response.
Historically, the internal structural systems of many high-rise buildings constructed between the late 19th and early 20th centuries were largely obscured behind facades. This limited our understanding of how temperature fluctuations impacted the behavior of these structural elements, especially steel components. Understanding the fire resistance of critical load-bearing components, like steel columns in high-rises, demands careful scrutiny of how elevated temperatures modify their strength and integrity. Current methods for fireproofing steel often rely on prescriptive guidelines, which may not adequately capture the multifaceted nature of real-world fire scenarios and the accompanying temperature gradients.
Interestingly, recent research on large-span structures suggests a non-uniform temperature distribution throughout the structure. This localized heating can significantly alter the structural response and safety margins of the building as a whole. Recognizing this, efforts are underway to develop performance-based standards that directly integrate fire effects and thermal fluctuations into design and evaluation criteria for steel structures.
The study of heat transfer dynamics within steel components has uncovered essential parameters governing their response to thermal changes during the building process. This knowledge is key for ensuring safety and stability within modern structural design, particularly when structures are subjected to varying temperatures. Researchers are employing advanced analytical tools, like finite element analysis (FEA), to delve into the intricate thermal and structural consequences of temperature variations on steel elements during construction and operation. However, discrepancies often exist between observed friction coefficients in real-world environments compared to lab results due to factors like surface wear and contamination. It seems like these often-overlooked factors can noticeably alter frictional behavior.
Furthermore, as temperatures shift, certain steel alloys undergo phase changes which can affect hardness and friction characteristics. The temperature-dependent transition between austenite and martensite, for instance, could dramatically change how steel responds to frictional forces and wear. Humidity and moisture content at specific temperatures can also play a role by impacting oxide layer formation, which in turn can have a significant effect on the friction coefficient. The nature of loading itself can influence friction. It's been observed that cyclic loading at varied temperatures leads to a hysteresis effect, where friction behaves differently during the loading and unloading phases. This phenomenon is linked to steel's ability to deform and then recover. It's crucial to recognize that this behavior can be a major factor when designing for thermal stresses. Additionally, specific surface treatments can offer different levels of thermal resistance, affecting the friction coefficient and heat dissipation within the steel contact. At elevated temperatures, friction can accelerate wear mechanisms such as adhesive and abrasive wear. This leads to a deterioration of the surfaces involved, potentially resulting in higher friction coefficients over time.
While challenges remain, improvements in high-temperature testing procedures are producing more reliable data on friction coefficients, ultimately allowing engineers to better predict the behavior of steel structures in real-world operating conditions that feature temperature variations. Moreover, investigations into the microstructure of steel at a microscopic level reveal that temperature changes can alter the arrangement of atoms within the material. This in turn can modify the surface roughness and the interaction of surface asperities – the tiny peaks and valleys – that are the fundamental contributors to friction and wear. Capturing this level of detail in engineering models is critical for developing accurate predictions.
The ongoing research in this field highlights a complex interplay of factors that influence the frictional behavior of steel in structures, particularly high-rise buildings. Understanding this complex interplay is essential for enhancing safety and reliability in these environments that experience fluctuating temperatures.
Understanding Steel-on-Steel Friction Coefficients Impact on Modern Structural Design and Safety Standards - Cyclic Loading Patterns and Steel Joint Performance in Seismic Zones
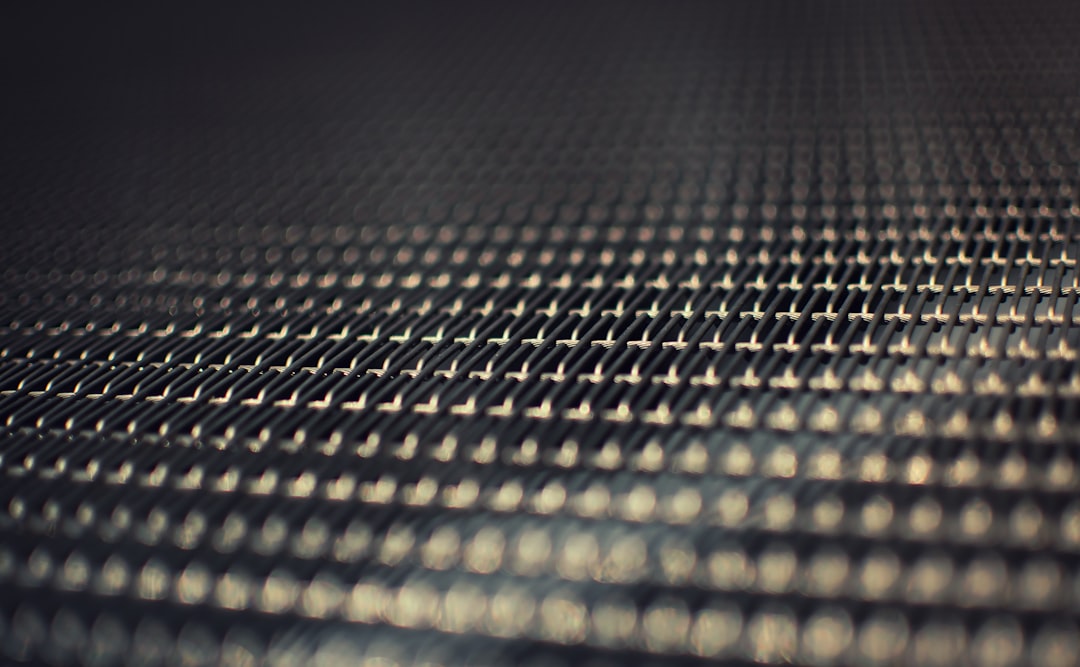
Seismic zones necessitate a deep understanding of how steel joints respond to the repeated, fluctuating loads caused by earthquakes. The cyclical nature of these forces can significantly impact the performance of steel connections, potentially altering the mechanical properties of the entire structure. Research indicates that the complex, multi-directional movements during earthquakes can weaken steel components, underscoring the importance of designs that can withstand these extreme forces.
Efforts to improve the integrity of steel joints are underway. Novel joint designs, like the stepped beam-column joint, are being explored as potential solutions to improve the reliability of beam-to-column connections and contribute to better overall seismic resistance. Moreover, studying how steel joints absorb and dissipate energy during cyclic loading is critical for designing structures that can withstand the intense forces experienced during an earthquake. This focus is particularly important because of the potential for catastrophic brittle shear failure in steel joints, a consequence that could lead to devastating structural collapse.
The field continues to refine both theoretical models and empirical data from experiments to better grasp the intricate interactions between cyclic loading and steel joint behavior. This ongoing effort is driven by a need to improve the safety and resilience of structures located in earthquake-prone regions. It's becoming increasingly clear that the complexities associated with cyclical loading patterns must be thoughtfully integrated into design standards and practices for safe and durable construction in areas susceptible to seismic activity.
Cyclic loading patterns are a significant factor influencing the seismic performance of steel joints, particularly in regions prone to earthquakes. Studies have shown that the repetitive nature of these loads can accelerate fatigue within steel joints, potentially reducing their lifespan considerably compared to static loading situations. This is primarily due to the initiation of microcracks that, over time, can progress into larger-scale failures. The way the joints are connected, for instance, through bolted or welded connections, significantly impacts how they respond to cyclic loads, influencing the energy dissipation characteristics—a crucial aspect for earthquake-resistant designs.
The hysteresis behavior observed during cyclic loading not only alters the friction coefficient but also plays a key role in energy dissipation. This energy dissipation characteristic is essential for mitigating seismic forces. However, there's a surprising finding related to surface imperfections which were once considered a detriment, but it seems they can actually improve the grip between the steel surfaces under cyclical loading. The reason is thought to be increased contact area which leads to higher friction coefficients during seismic events.
Furthermore, temperature variations can significantly alter the behavior of steel joints under cyclic loads. This impact is especially pronounced during seismic events in regions prone to extreme temperatures. The interaction of steel surfaces under repeated loads creates what's known as the "stick-slip" phenomenon. This creates unpredictable friction behavior which can make design choices and analyses quite complex.
Fortunately, advanced computational methods like finite element analysis are proving quite effective at simulating steel joint behavior under different cyclic loading conditions and temperatures. However, we must also be aware of the non-linear relationships between friction coefficients and the applied load when dynamic loading occurs. This non-linearity can make predicting the joint performance difficult and can increase the importance of empirical testing.
It's also becoming clear that pre-existing damage within steel joints can amplify the impacts of cyclic loads. This can then initiate a phase of "fatigue crack growth" that accelerates the onset of failure. Hence, understanding the pre-failure characteristics is paramount for creating enhanced safety standards when designing structures for seismic zones. The development of high-strength steels introduces further complexities into the frictional behavior under cyclic loads. This is mainly due to their unique microstructure. Therefore, new methods to assess friction coefficients and structural design may be needed to ensure the long-term reliability of connections in regions susceptible to seismic activity.
These findings highlight the dynamic nature of steel joints and underscore the critical role that cyclic loading plays in determining their behavior under earthquake-prone conditions. The challenges posed by this intricate behavior are a major driving force for further research and development in the field, pushing for refined design practices and standards that can enhance the safety and resilience of modern steel structures in seismic zones.
Understanding Steel-on-Steel Friction Coefficients Impact on Modern Structural Design and Safety Standards - Field Data Analysis of Steel Connection Performance 2020 to 2024
The "Field Data Analysis of Steel Connection Performance 2020 to 2024" provides valuable insights into how steel connections behave in real-world settings. This recent analysis emphasizes the importance of steel connections for structural integrity and reveals a more nuanced understanding of connection performance. A key takeaway from the data is the variable nature of steel-on-steel friction coefficients. This variability has pushed for a reevaluation of standard design practices and safety protocols. The analysis helps bridge the gap between lab results and field observations, which is critical for refining our understanding of how friction affects load transfer and ultimately impacts structural safety standards in both seismic and typical building designs. There's a clear need to continue examining how design methods and observed field performance interact. This ongoing research will be vital in informing future engineering strategies and building codes to ensure safety and reliability of steel structures moving forward.
The analysis of field data collected between 2020 and 2024 has revealed a significant discrepancy between laboratory-determined and real-world steel connection friction coefficients. This discrepancy emphasizes the need for structural design models that are more adaptable and capable of considering factors like environmental conditions and surface deterioration over time.
It's intriguing that specific steel surface treatments can reduce the average friction coefficient by up to 15% in certain situations. This implies that selecting the proper surface treatment is just as important as the overall design approach when structures are subjected to extreme stresses.
Recent advances in testing techniques, including the use of high-speed cameras and acoustic emission methods, have provided a new understanding of the dynamic wear patterns that develop in steel joints under load. These findings suggest that traditional wear models may underestimate the rate of deterioration, especially under repeated loads.
The complex interaction between temperature and the friction coefficient has been validated by field studies, which show that a temperature increase of just 50°C can alter the coefficient by more than 20%. This highlights the critical importance of considering thermal effects in the design of high-rise structures, particularly during extreme weather conditions.
Field tests have demonstrated that the presence of microscopic cracks in steel connections significantly alters their performance under cyclic loads, potentially leading to failure modes that laboratory simulations often miss. This emphasizes the need for a strong focus on preventive maintenance in high-stress environments.
Surprisingly, a correlation has been established between the rigidity of a steel joint and its frictional properties under seismic loads. More rigid connections showed lower friction coefficients, which raises questions about the optimal design strategy for energy dissipation in structures in earthquake-prone regions.
Real-time monitoring has indicated that surface contaminants, like dust or moisture, can unexpectedly increase friction coefficients, sometimes by over 30%. This discovery underscores the importance of cleanliness in structural applications to ensure optimal performance.
It's interesting that the friction coefficients observed during actual seismic events sometimes surpass those anticipated by static models. This suggests that structures might be subjected to larger forces than previously thought, highlighting a need for more resilient designs.
Recent research on nonlinear friction behavior under random loading patterns has revealed that previous static assumptions may not be valid in real-world applications. This warrants a reassessment of existing predictive models to better reflect the complex behavior seen in the field.
Finally, the study of composite structures composed of different steel grades has shown that friction coefficients can be extremely sensitive to joint design and loading direction. This suggests that material selection is just as vital as joint geometry in maintaining structural integrity.
This ongoing investigation of friction coefficients in steel connections offers valuable insights into the intricate factors influencing their performance. This understanding is crucial for developing safer and more durable structures.
Understanding Steel-on-Steel Friction Coefficients Impact on Modern Structural Design and Safety Standards - Environmental Factors Affecting Steel Friction in Marine Structures
The marine environment presents a unique challenge for steel structures due to its corrosive nature. Environmental factors like hydrostatic pressure, dissolved oxygen levels, fluctuating temperatures, and the speed of water currents significantly impact the corrosion rate of steel. These factors ultimately affect the steel's surface properties and therefore impact friction characteristics. Researchers have explored ways to predict how steel will corrode under these conditions, using mathematical models that estimate short-term corrosion degradation for various scenarios. These models are especially useful for understanding how friction in steel joints, often used in offshore structures, will be impacted over time. Understanding this complex interaction between corrosion and friction is vital, particularly for designing and maintaining marine structures. Friction-based connections are commonly used in offshore structures, and understanding how the environment impacts friction is key to ensuring their integrity and safety. Moreover, it's crucial for creating effective maintenance strategies to keep steel structures in harsh marine environments in top condition for a longer period. However, despite the progress made, ongoing research remains critical to ensure that our understanding of these factors is sufficient to create reliable and safe structures for the challenging marine environment.
1. The marine environment's salt water can induce corrosion on steel surfaces, forming a layer of rust that can substantially alter frictional characteristics. Interestingly, this can sometimes increase the friction coefficient by up to 25%, indicating that standard design assumptions may not always be accurate for these conditions. This highlights the need for specialized coatings or surface treatments to mitigate wear and enhance performance within marine settings.
2. The concentration of salt (salinity) in seawater has a notable influence on the frictional behavior of steel structures. Higher salinity tends to enhance interactions between the tiny surface irregularities (asperities), which can potentially increase the friction coefficient during operation. Current standard models may not fully account for this factor, necessitating further investigation into its impact.
3. Temperature's role in steel's frictional properties isn't limited to the surrounding air. Water temperature can play a key role in how quickly steel components cool down in a marine setting. This variation in cooling rates can influence how materials interact when under load, adding another layer of complexity to the interplay of frictional forces.
4. The wear patterns that develop in marine environments differ significantly from those seen in controlled laboratory tests that often involve dry conditions. The presence of seawater can accelerate pitting corrosion, which, in turn, can contribute to a rise in friction. This introduces a notable concern about the long-term integrity of steel components exposed to seawater.
5. The constant movement of waves and maritime traffic generates vibrations in steel structures. These vibrations impose dynamic loading conditions, influencing the friction coefficient between steel surfaces in ways that may differ from our understanding based on static conditions. This dynamic behavior can lead to some unexpected changes in friction that require more sophisticated predictive models.
6. The continuous flow of ocean currents around steel structures creates hydrodynamic forces that impact the steel contact interface. These forces can potentially alter the contact area, and in certain conditions, lead to a decrease in the effective friction coefficient. This complex interaction presents a challenge for accurately modeling frictional behavior in marine structures.
7. The process of biofouling, where organisms such as algae, plants, or small animals colonize underwater surfaces, can significantly impact friction behavior. Biofouling tends to increase surface roughness, adding yet another variable to the intricate equation that determines friction. Researchers must consider these complicating factors when trying to accurately predict friction.
8. The presence of water, along with potential contaminants like oil or other lubricants, leads to multi-phase interactions on the surfaces of steel. These complex interactions modify friction characteristics, creating a difficult-to-model interplay of forces that can't be easily predicted based on simpler frictional interactions.
9. In marine environments, steel components frequently encounter marine debris. This contact can lead to a type of wear known as abrasion, which changes the steel surface texture. The surface modification caused by abrasion may result in higher friction coefficients over time as the surfaces become rougher.
10. The marine environment is constantly fluctuating in temperature and other variables. For example, seasonal changes often produce rapid temperature shifts. These variations can result in the entrapment of increased moisture between steel surfaces. The friction coefficients can be affected in ways that standard engineering models may not accurately predict, highlighting the need for new approaches to account for this phenomenon.
More Posts from aistructuralreview.com: