Understanding Motor Service Factors A Key to Optimal Performance in 2024
Understanding Motor Service Factors A Key to Optimal Performance in 2024 - Calculating Motor Power to Size Ratio for Accurate Service Factors
Optimizing motor performance hinges on accurately calculating the power-to-size ratio, a crucial step in establishing reliable service factors. This calculation involves a close examination of the interplay between torque and speed, acknowledging that motors can handle temporary overloads within defined service factor limits. This process is essential to prevent operational inefficiencies and premature motor degradation, particularly when faced with changing operating conditions. It's crucial to remember that motor sizing needs to align with the typical load to maintain a healthy power factor and avoid potential instability. Inadequate matching can lead to increased energy consumption and operational costs. As industries evolve and demands shift, the accuracy of these calculations becomes more critical to ensure both operational efficiency and sustainability in motor operations.
Understanding the relationship between motor power and its physical size is crucial for efficient system design. The service factor (SF), a multiplier indicating a motor's overload capacity, plays a pivotal role in this calculation. While generally ranging from 1.15 to 1.5 for smaller motors, the SF can vary significantly based on the motor's intended duty cycle and load characteristics. A motor's torque output, for instance, is a significant design parameter that impacts the power-to-size ratio. Higher torque at a smaller size can be beneficial, particularly in situations demanding compact solutions and potential for improved efficiency.
However, operational efficiency is not always linearly linked to SF. Motors operating close to their rated capacity, even within the defined SF, might suffer from increased losses, like heat dissipation, leading to reduced overall efficiency. In essence, the design, not just the rating, dictates this interplay. It's intriguing that two motors with the same horsepower might differ dramatically in their physical characteristics, highlighting the need for a comprehensive analysis of materials and construction to get the desired ratio for specific applications.
Furthermore, this analysis cannot neglect thermal considerations. While the horsepower rating is a key parameter, the ability of the motor materials to withstand prolonged elevated temperatures due to increased load is critical to prevent premature degradation. The "1.0 rule" provides a simplistic starting point for SF estimation, but it's inadequate for many cases. Factors like load variability and repeated start-stop cycles should be meticulously accounted for, particularly when dealing with high-inertia loads as suggested by IEC standards. This might involve SF values outside standard ranges.
It's important to remember that manufacturer's SF ratings stem from empirical data. While valuable, real-world applications can deviate, emphasizing the need for specific testing during design to refine the power calculation and associated SF. This becomes even more critical when one considers how the power-to-size ratio impacts installation expenses and overall system architecture. In industrial environments with spatial constraints, an improperly sized motor can translate to higher costs and more complex installations.
Finally, a crucial distinction exists between motor types like asynchronous and synchronous motors in terms of their power-to-size characteristics. Deeper understanding of the underlying rotor design and its influence on these ratios offers potential for improved efficiency and greater versatility in applications. This is a dynamic area of research with potential for optimized design moving forward.
Understanding Motor Service Factors A Key to Optimal Performance in 2024 - Impact of Voltage, Current, and Temperature on Motor Efficiency
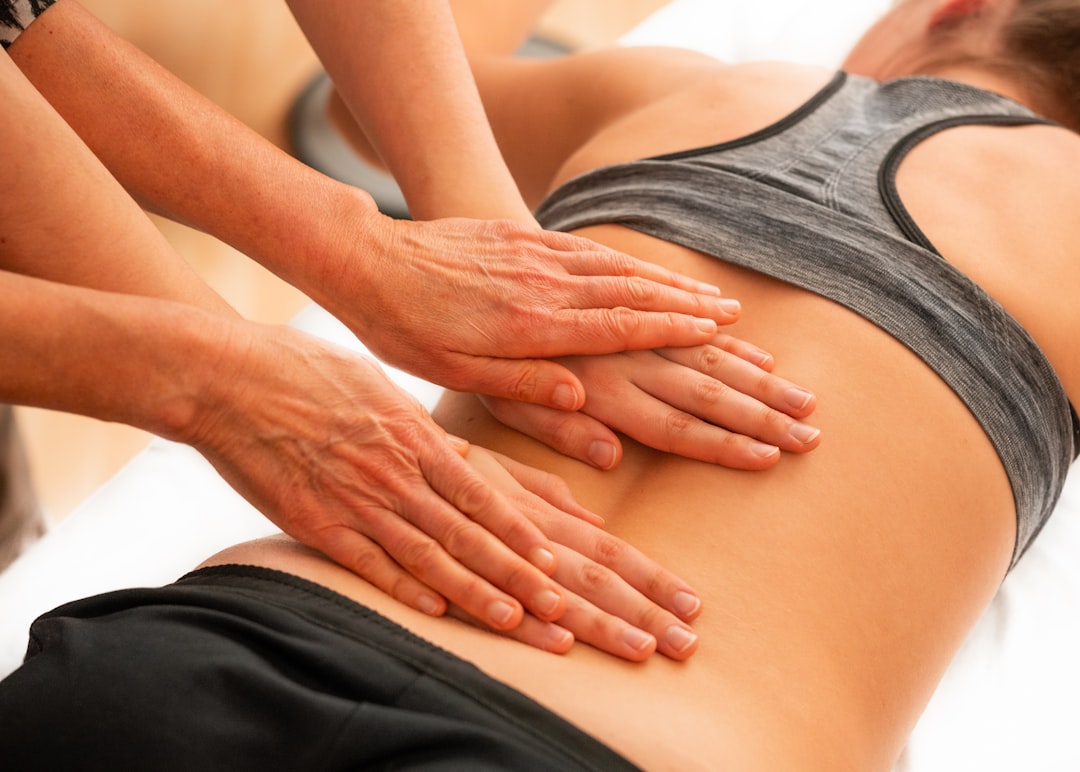
Motor efficiency is significantly impacted by voltage, current, and temperature. Changes in these factors directly influence motor performance. For example, higher temperatures increase the resistance within motor windings, causing a decrease in crucial parameters like torque and voltage constants, ultimately reducing efficiency. Keeping motors operating within their recommended voltage and current ranges is vital to ensure their long-term reliability and avoid premature damage. Given the significant role motors play in global energy consumption, even small improvements in efficiency can translate into substantial energy savings. The growing emphasis on energy efficiency across industries further underscores the importance of understanding and managing these relationships. Optimizing motor service factors relies heavily on comprehending these interactions, making it a key aspect of modern industrial practices.
Electric motor efficiency is significantly influenced by factors such as voltage, current, and temperature. Even small voltage deviations, around 10% from the rated value, can cause a noticeable drop in efficiency, potentially reducing it by 5-10%. Maintaining stable voltage within the recommended range is paramount for optimal performance.
Interestingly, the relationship between current and efficiency isn't linear. While increased mechanical loads naturally lead to higher current draw, this does not proportionally translate into output torque. Instead, exceeding a motor's optimal operating range can cause overheating and substantial efficiency losses. It seems that doubling the current doesn't necessarily double the output.
Motor temperature is another critical factor, with higher operating temperatures potentially leading to insulation breakdown, a precursor to premature wear and tear, and ultimately a reduction in efficiency. It's a reminder that thermal management strategies are crucial for extending motor lifespan. Furthermore, ambient temperature plays a significant role in motor performance. It appears that each 10°C increase in ambient temperature can reduce efficiency by about 1%.
The interplay between current, voltage, and the power factor also influences efficiency. Lower power factors can indicate inefficiencies, which increase the current draw, resulting in excessive heating and decreased overall motor efficiency. It's an intriguing area of exploration, as it highlights the importance of efficient conversion of electrical to mechanical power.
Efficient cooling mechanisms can play a major role in optimizing efficiency. Motors designed to operate with limited cooling are prone to greater efficiency losses compared to those with robust cooling systems. This underscores the importance of thermal design, especially in applications involving continuous operation.
Resistance of winding materials, like copper, increases with temperature. This leads to higher resistive losses (I²R losses), contributing to further efficiency decreases. It suggests that the choice of winding materials based on the anticipated operational temperatures is a key factor to consider. It seems that even when using well-established materials like copper, there is a trade-off in various applications.
The service factor, which reflects a motor's capacity to handle overloads, also has thermal implications. Motors routinely operating near their service factor limits often experience notable efficiency declines due to overheating, a phenomenon that standard operating procedures might not sufficiently address.
Different motor designs, like squirrel cage and wound rotor, respond differently to changes in voltage, current, and temperature. Understanding these individual responses is vital for selecting the appropriate motor for a specific application and optimizing its efficiency. The ability to use the proper motor type seems highly significant in regards to overall energy use and efficiency.
Finally, the startup current of a motor, potentially reaching 7-10 times its rated current, poses a major thermal challenge and results in immediate inefficiencies. Implementing soft starters or variable frequency drives (VFDs) could potentially mitigate the initial thermal stress and reduce operational inefficiencies during startup. This illustrates the potential benefits of newer motor control systems.
In conclusion, understanding the complex relationship between voltage, current, temperature, and motor efficiency is crucial for optimizing energy consumption and extending motor lifespan. There is still much to discover in the field of motor engineering, and as technology and operational needs continue to evolve, it's important that researchers and engineers continue to refine their understanding of these various factors in order to realize optimal motor performance in the years to come.
Understanding Motor Service Factors A Key to Optimal Performance in 2024 - Full Load Current Analysis for Machinery Performance Optimization
Full Load Current Analysis (FLA) plays a crucial role in optimizing how machinery operates. It measures the current a motor draws when working at its intended power output. This measurement provides valuable information about motor efficiency and lifespan, revealing how well electrical energy is transformed into mechanical work. Furthermore, understanding FLA alongside the Motor Service Factor (SF) unveils how motors perform across a range of load situations. This knowledge is essential for fine-tuning motor operation, maximizing efficiency, and minimizing energy waste. Examining the motor's behavior during periods of peak demand, alongside the complexities of thermal management, can further improve overall machine performance. This involves mitigating the risks of overheating and associated inefficiencies. Given the increasing focus on sustainability and energy conservation across various industries, prioritizing FLA analysis is becoming more important for industrial applications that use motors.
Full load current (FLC) represents the current a motor draws when operating at its rated power output. It's a fundamental parameter for assessing motor efficiency and durability. Understanding FLC variations is crucial for optimizing motor performance, as it dictates how effectively power is converted into useful work. Interestingly, even motors with the same horsepower rating can have vastly different FLCs, sometimes by up to 30%, due to design nuances and efficiency characteristics.
The service factor (SF), as defined by the National Electrical Manufacturers Association (NEMA), provides a measure of the motor's capability to handle overloads beyond its rated power. The relationship between SF and motor operation is complex, and it's not just about the rating; a motor's design and cooling capabilities play crucial roles. In essence, a higher SF might allow for more load but can strain cooling systems, leading to potential overheating if not carefully managed.
Motor startup presents a unique challenge regarding FLC. The initial surge of current can be extraordinarily high, often 7 to 10 times the rated value. This enormous surge stresses both the motor’s electrical and mechanical components, increasing the risk of damage or failure if it isn’t mitigated through appropriate measures like soft starters. It’s remarkable how significant these initial peaks are compared to the normal running conditions.
The type of materials used for the windings has a direct impact on FLC and the thermal management requirements. Using copper is generally more efficient but also more expensive than materials like aluminum. There's a trade-off to be considered when selecting materials for specific applications. While using aluminum lowers costs, it often introduces higher resistance, leading to more heat and efficiency losses.
Beyond motor construction, load characteristics are paramount when optimizing FLC. For instance, variable or dynamic loads, common in processes like conveyor systems, require a detailed analysis to ensure that the motor's capabilities aren't exceeded. We need to understand the load type not just for basic sizing, but also for the operational range.
The relationship between FLC and efficiency isn't simple. It seems that operating at about 80% of the FLC is often the most efficient point of operation. Consistent full load operation can introduce inefficiencies and increase stress on the motor, emphasizing the need for thoughtful operational practices and load management.
Continuously operating near or exceeding the FLC can lead to a phenomenon called thermal runaway. As temperatures rise, resistance increases, leading to a higher current draw, creating a cycle that causes harm to the motor if not properly addressed. It's a cautionary reminder of the limits of operation and the importance of regular maintenance.
Ambient conditions can also affect the FLC. For instance, operating a motor at higher altitudes, where the air is thinner, can negatively affect cooling efficiency. This might lead to a need for derating the motor to avoid overheating issues. It's another reminder that we need to consider all conditions for optimized performance.
The load current doesn't increase linearly with increases in load, making performance analysis more complex. Interestingly, there seems to be a more significant current rise around 70-80% of the FLC, indicating critical points in the motor’s operating range that require close monitoring.
Because SF ratings are often based on empirical data, relying solely on manufacturer specifications might not provide an accurate picture of the actual operational characteristics. It appears that thorough testing in realistic environments is crucial to ensure design expectations meet actual performance capabilities. This becomes increasingly important as operational conditions can vary widely in industrial settings.
In conclusion, analyzing FLC across a variety of conditions is critical for optimized motor performance. As with all other aspects of motor engineering, there are limits and trade-offs to be considered. A better understanding of these interdependencies allows us to achieve a more efficient and robust motor performance for machinery across a wider range of applications.
Understanding Motor Service Factors A Key to Optimal Performance in 2024 - Digital Maintenance Strategies for Electric SUVs in 2024
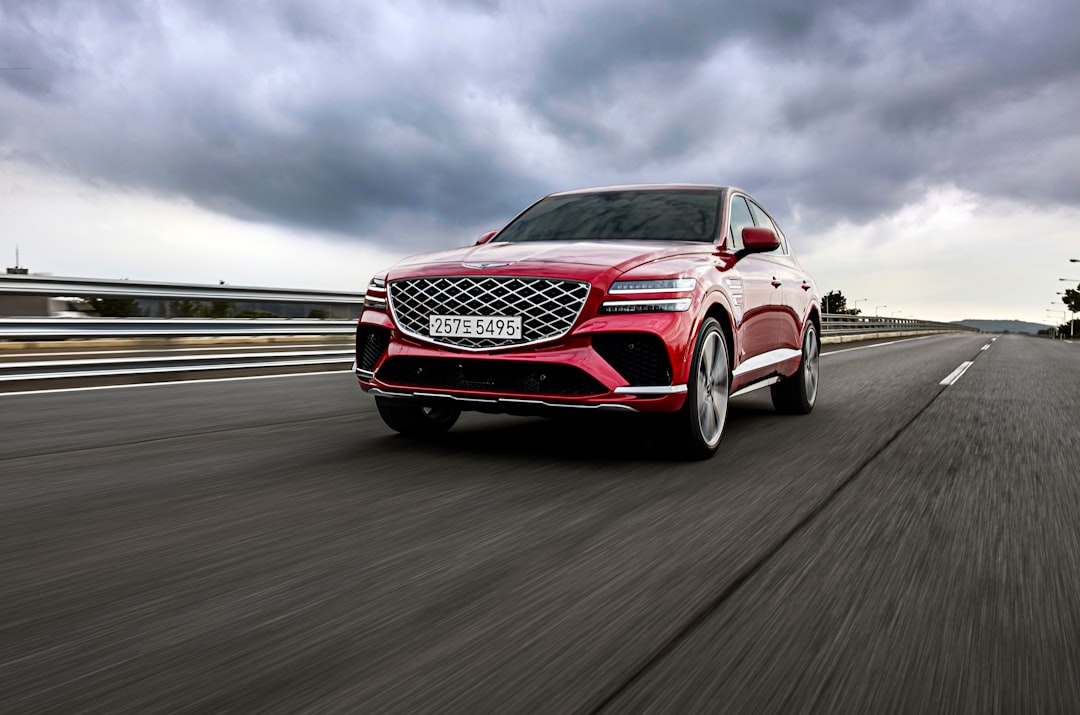
Electric SUVs in 2024 present a new set of maintenance challenges due to their complex software and advanced technologies. Maintaining optimal performance now requires a shift towards digital maintenance strategies. The intricate software systems within these vehicles necessitate specialized technicians who can effectively troubleshoot and resolve software-related issues. Furthermore, the battery, being the heart of the electric drivetrain, demands careful attention and management to maximize its lifespan and ensure peak vehicle performance.
The move toward data-driven, predictive maintenance, leveraging machine learning, is transforming the maintenance landscape. This approach allows for proactive interventions, anticipating potential issues and minimizing downtime. However, the cost-effectiveness of these digital solutions becomes increasingly important as the automotive industry adopts automated driving and other complex drivetrain technologies.
A comprehensive approach to maintaining electric SUVs, which includes regularly scheduled assessments and timely service interventions, is becoming increasingly important. This comprehensive strategy not only extends the vehicle's lifespan but can also play a major role in reducing overall maintenance costs, making electric SUVs a more appealing option for consumers.
Electric SUVs, particularly those rolling off the assembly lines in 2024, are intricate systems driven by complex software and, of course, the battery. This necessitates a shift away from traditional reactive maintenance practices towards more proactive and data-driven approaches. The sheer volume and variety of data generated by these vehicles, often referred to as telematics data, is proving crucial. Analyzing this data in real-time allows for a more nuanced understanding of how each vehicle is performing and its potential needs. This is a departure from traditional fixed-interval maintenance schedules that may not fully align with the vehicle's actual usage patterns.
Artificial intelligence (AI) is playing a larger role in this space. AI-powered predictive maintenance strategies use historical data and machine learning to anticipate potential failures before they impact operation. This type of proactive maintenance, while still under development, has the potential to improve reliability and reduce unexpected breakdowns. This kind of predictive capability is most visible in battery management systems (BMS), where the AI algorithms are analyzing charging cycles, temperature fluctuations, and cell balancing to optimize overall battery health and extend lifespan. Battery replacement in electric vehicles can be costly, so strategies aimed at maximizing battery performance are of great interest.
The integration of electric SUVs into smart city infrastructure presents another interesting development. Vehicles can now communicate with charging stations and traffic management systems, which can dynamically adjust charging schedules and route optimization based on real-time data. This creates efficiencies not just in energy usage, but also in overall vehicle operation.
Remote diagnostics also have a growing role to play in minimizing downtime. Built-in features allow technicians to perform assessments and troubleshoot some issues remotely. This means faster response times and potentially fewer service visits. Additionally, manufacturers are equipping electric SUVs with advanced user interfaces (UIs), making it easier for owners to monitor vehicle health and schedule maintenance. This increased owner interaction with the vehicle’s internal systems has the potential to lead to a greater sense of ownership and deeper understanding of their vehicle’s status.
It's apparent that the traditional 'check engine' light is not enough in an era of complex, integrated electric drivetrains. Instead, we are moving towards a much more fine-grained understanding of component performance, from electric motors to the regenerative braking systems. This level of detail in diagnostics allows for more targeted maintenance, reducing costs and hopefully improving reliability. This approach is being further refined with the introduction of usage-based maintenance schedules. These models are based on the idea that vehicles used in similar ways are likely to have similar maintenance needs. This dynamic approach has the potential to reduce costs and minimize the frustration associated with unnecessary maintenance visits.
Some companies are exploring more novel approaches to service records, like the application of blockchain technology. This secures the integrity of vehicle histories, enhancing transparency and fostering trust between owners, repair facilities, and potentially future buyers. It’s still early days for this implementation, but the potential benefits for resale value and warranty claims seem significant.
Ultimately, the growing adoption of these digital strategies in the electric SUV space signifies a departure from the traditional automotive maintenance paradigms. This change is driven by the increased complexity of electric drivetrains, the importance of battery health, and the pursuit of increased efficiency and reliability. It's clear that the future of automotive maintenance is intrinsically tied to the effective use of software and data analysis. However, the long-term viability and efficacy of these new strategies remains a research question as we navigate the challenges and complexities of implementing these solutions in the ever-changing world of electric vehicles.
Understanding Motor Service Factors A Key to Optimal Performance in 2024 - Data Integration Trends Shaping Automotive Industry Performance
The automotive industry's performance is being significantly altered by the integration of data, particularly as the shift towards electric vehicles (EVs) accelerates alongside the development of autonomous driving capabilities. The year 2024 sees a notable increase in reliance on connectivity through the Internet of Things (IoT), which has the potential to foster stronger customer interactions and improve decision-making processes. Despite this potential, the sector faces substantial hurdles in implementing these advancements, including navigating the complexities of software integration within vehicles and establishing a comprehensive infrastructure to support the increasing need for electrified powertrains. While overall growth in the automotive industry is projected to be moderate, with global vehicle sales anticipated to reach a high point, the focus on eco-friendly practices and data-driven insights will likely play a key role in determining long-term success for manufacturers. The integration of advanced technologies not only reshapes how customers experience vehicles but also necessitates a critical reassessment of service and maintenance approaches, aiming to maximize efficiency and extend the operational lifespan of these evolving automotive systems. While the industry faces headwinds with these integrations, the ultimate potential for improved outcomes is undeniably substantial.
The automotive landscape is being reshaped by the sheer volume of data generated by today's vehicles, exceeding 30 terabytes annually. This data deluge necessitates sophisticated data integration systems to effectively analyze and utilize this information. We're seeing a move away from the traditional 'wait-and-see' maintenance approach, which often led to larger repairs. Instead, electric vehicles can now leverage data integration to provide real-time diagnostics, empowering a more proactive maintenance approach.
The convergence of the automotive industry with the Internet of Things (IoT) is gaining traction. This interconnectivity allows seamless communication between vehicles, charging networks, and traffic management systems, offering improvements in efficiency and the overall user experience. Machine learning techniques embedded within data integration are enabling predictive maintenance, where potential vehicle failures can be anticipated and avoided through data analysis. It's fascinating how this data-driven approach is transforming maintenance practices.
In the fast-paced world of auto manufacturing, unplanned downtime can be incredibly costly – estimates place the losses as high as $250,000 per hour. It’s clear why robust data strategies that promote operational uptime are crucial. Moreover, managing battery lifespan, often the most expensive component in an electric vehicle, is greatly facilitated by data integration. By analyzing charging patterns and temperature shifts, battery management systems can optimize the performance and extend the life of these crucial components.
Traditionally, automotive maintenance schedules have followed fixed intervals. However, telematics data integration is allowing manufacturers to tailor these service schedules based on real-world usage patterns. This is a more personalized and potentially more cost-effective approach compared to the traditional method that could result in either over-servicing or under-servicing. It's evident that user engagement is also increasing thanks to the integration of advanced interfaces that provide vehicle health insights and driver behaviour analytics. It’s creating a new kind of informed vehicle ownership.
The industry is even exploring innovative applications of blockchain technology to manage and secure vehicle service records. This creates a novel avenue for increasing transparency and trustworthiness within the automotive service sector. However, there are challenges that come with this transition. The complexity of modern vehicle systems requires technicians to possess both strong mechanical skills and the ability to troubleshoot software issues. It's a stark indication of the evolving skillset demands in the electric vehicle era.
In conclusion, data integration is pivotal in shaping the automotive industry’s future. We’re seeing a clear trend toward data-driven decision-making that extends from the design stage to the maintenance and end-of-life considerations. It's a dynamic and complex field, and the interplay between software, data analysis, and vehicle performance will continue to evolve in the coming years, undoubtedly impacting how we interact with vehicles and the environment in which they operate.
Understanding Motor Service Factors A Key to Optimal Performance in 2024 - Historical Motor Advancements Informing Modern Power Calculations
The history of electric motors has significantly shaped how we calculate their power capabilities today, particularly when it comes to optimizing service factors for peak performance. The emergence of the three-phase induction motor during the industrial revolution was a pivotal moment, laying the groundwork for much of the current motor technology in use. It's no coincidence that this type of motor continues to dominate, accounting for roughly 70% of industrial electricity use.
More recently, motor design has incorporated sustainability and high efficiency as central goals. This emphasizes not only maximizing performance but also minimizing environmental impact. The evolution of different motor types, including the improved efficiency of permanent magnet synchronous motors, highlights a growing focus on optimizing the power output relative to the size and type of application. The design and control technologies paired with these motors have a big impact on the overall system.
Understanding these historical advancements in motor design is crucial to performing accurate power calculations in today's applications. This historical knowledge helps ensure that service factors are correctly accounted for in order to achieve optimal performance across a range of operating conditions. It's a reminder that simply looking at the rated horsepower is not enough for many situations, and that motor performance is influenced by its design and control technologies.
The evolution of electric motors, starting in the 19th century, has seen a remarkable journey from relatively inefficient designs with around 50-60% efficiency to today's highly refined motors capable of exceeding 90% efficiency. This improvement is due to technological and material advancements that have redefined the field. It's intriguing to consider that early designs likely had limitations in materials and understanding of the fundamental principles of electromagnetism, compared to our current understanding.
The introduction of brushless motor designs, a hallmark of modern motor engineering, has its roots in earlier historical attempts to minimize friction and enhance performance. These early insights are critical for today's applications where thermal management and operational speed are paramount, especially in industries such as automotive and robotics. It's evident that a focus on minimizing heat generation has become crucial as motors are integrated into increasingly compact systems.
Nikola Tesla's invention of the induction motor in the late 1800s proved revolutionary, making widespread industrial adoption possible due to its simple design and reduced maintenance requirements. Understanding how it operates is fundamental to determining service factors in contemporary motor applications. One might wonder if the simplicity and robustness of that design were a product of the era or a testament to Tesla's insightful understanding of motor physics.
The concept of service factors, although more formalized in the 20th century, can be traced back to early observations of motor behavior under various conditions. Early engineers and operators discovered that even slightly oversizing motors could help extend their operational lifespan, giving rise to the concept of using a safety margin to improve reliability. Perhaps the limitations of early materials and manufacturing processes encouraged a conservative approach, resulting in what we consider service factors today.
Motor sizing and performance metrics, including the relationship between power and physical size, are heavily indebted to early experimentation with materials and manufacturing. Trial and error were essential during these formative years of motor design. The transition from these early practices to modern rigorous testing protocols has been driven by the necessity of optimal material selections and construction techniques for various applications. One can only imagine the number of failures and unexpected outcomes that led to this transition.
The evolution from mechanically controlled motor speeds to electronic speed control has profoundly influenced how engineers calculate power. Early motors used purely mechanical approaches, which naturally came with limits on speed variability and control precision. The shift to electronic control strategies enhances control, improves motor responsiveness, and, importantly, offers opportunities to reduce energy waste. One wonders how much energy was lost in the earlier designs with crude mechanical control systems.
The history of electricity generation and the development of motor technology are deeply intertwined. The rise of AC power systems not only expanded electrical grid capabilities but also impacted motor design. Motors designed for AC were favored because they allowed for efficient operation over varying loads. This interdependency between electricity generation and motor design exemplifies how engineering disciplines aren’t isolated entities but instead influence each other in powerful ways.
Changes in industrial needs over time have influenced motor design, with historical eras typically defining motor specifications based on dominant technologies. Today's motor engineers must carefully consider these historical factors to accurately apply and adjust service factors for future applications. It is a testament to the constant change that occurs in our society and how historical practices can still hold relevant clues.
The service factor concept has been refined further through lessons learned from various historical instances of motor failures. Engineers have observed that real-world motor performance often doesn't perfectly match theoretical expectations. These observations have led to a deeper understanding of failure modes, which is incorporated into predictive models to enhance service factor implementation. There is an intriguing connection between empirical observations, historical failures, and modern design processes, which points to a continuous cycle of refinement and optimization.
Historically, the most robust motors were often those designed for harsh environments, like those found in mining or marine applications. The lessons learned from the design and operational resilience of these robust motors are now informing modern practices, as engineers are setting higher benchmarks for service factors even in environments with less demanding operating conditions. This underscores a trend towards a higher overall quality standard for modern motor design, even if they won't be subjected to extremely harsh conditions.
This examination of how historical motor design advancements have impacted modern power calculations offers a fascinating insight into the evolution of motor engineering. By continuing to examine historical insights, researchers and engineers will likely continue to refine and optimize service factor applications for even more advanced and efficient motor systems in the future.
More Posts from aistructuralreview.com: