Galvanic Corrosion Between Stainless Steel and Aluminum Mechanisms and Prevention Strategies in 2024
Galvanic Corrosion Between Stainless Steel and Aluminum Mechanisms and Prevention Strategies in 2024 - Understanding the Mechanism of Galvanic Corrosion in SS-Al Pairs
When stainless steel and aluminum are in close proximity within a corrosive environment, a galvanic cell forms due to their dissimilar electrochemical potentials. This cell accelerates corrosion, primarily impacting the aluminum component, particularly when stainless steel grades like SS316 are involved. Understanding the intricacies of this process necessitates a thorough investigation into the localized corrosion mechanisms that develop. The rate at which the corrosion occurs is directly tied to the kinetics of the electrochemical reactions between the two metals. The formation of these galvanic cells, the nature of localized corrosion, and the pace of the reactions all contribute to the overall deterioration of the materials.
To mitigate this galvanic corrosion, protective coatings and design modifications become paramount. By implementing protective measures like specialized coatings, we can create barriers that shield the aluminum from the corrosive environment. In addition, strategically designing components to reduce or eliminate direct contact between the stainless steel and aluminum helps to minimize the likelihood of galvanic cell formation.
Emerging technologies like machine learning are offering fresh avenues for research into galvanic corrosion prediction. This promises to provide more accurate assessments of the behavior of these material combinations, leading to improvements in design and maintenance practices. Further research into this vital area is essential to ensure the long-term reliability of structures utilizing these material pairings.
When stainless steel and aluminum are in contact within a corrosive environment, their differing electrochemical tendencies create a galvanic cell. This cell accelerates the corrosion of aluminum because stainless steel, having a higher electrode potential, acts as the cathode, while aluminum becomes the sacrificial anode, experiencing accelerated material loss.
The severity of this corrosion is significantly impacted by the presence of an electrolyte, like moisture or even small amounts of salt, which enhances electrical conductivity and promotes corrosion. It's a common mistake to assume aluminum is inherently more corrosion-resistant than stainless steel. However, within a galvanic couple, aluminum's lower position in the galvanic series makes it much more vulnerable to localized corrosion, especially pitting.
The specific alloying elements within both the stainless steel and the aluminum can significantly alter how they behave in a galvanic cell. Certain alloys might either lessen or amplify the corrosion, emphasizing the importance of careful material selection. Protective surface treatments, like anodizing for aluminum or passivating stainless steel, can provide a barrier against corrosion by forming protective oxide layers. However, any damage to these layers can severely compromise their effectiveness.
The design of the joint itself matters. Close contact areas between the two metals can trap water, fostering localized corrosion even without direct electrical contact. Temperature is a key factor, as higher temperatures generally accelerate the corrosion process, whereas lower temperatures slow it down. These considerations are essential during design, highlighting the need for careful environmental control.
The frequency of maintenance and inspections is crucial in the long-term performance of stainless steel-aluminum structures. Failure to promptly address corrosion can result in catastrophic failures due to unforeseen and potentially severe degradation. Additionally, understanding the intricate local conditions surrounding the joint can yield valuable insights. Factors such as microbial activity, biofilm formation, and the presence of industrial pollutants can drastically alter corrosion behavior, potentially leading to unexpected corrosion rates and patterns that are not initially predicted. This points towards the necessity of meticulous design and assessment of potential environmental influences in these structural pairings.
Galvanic Corrosion Between Stainless Steel and Aluminum Mechanisms and Prevention Strategies in 2024 - Environmental Factors Accelerating Corrosion in Aerospace Structures
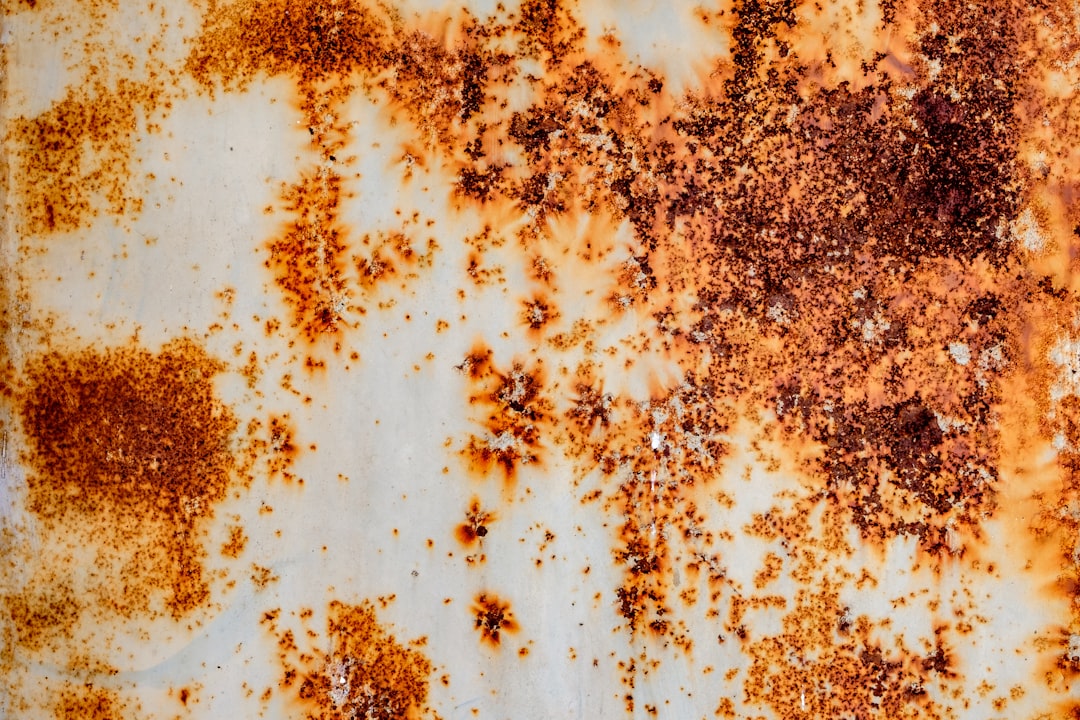
The environment surrounding aerospace structures significantly impacts the rate of corrosion, especially when materials like aluminum and stainless steel are in contact. Elevated humidity, which introduces electrolytes that enhance electrical conductivity, fuels galvanic corrosion. In this process, aluminum, due to its lower electrochemical potential, tends to corrode preferentially compared to stainless steel. Fluctuations in temperature and humidity can further accelerate the deterioration, increasing the risk of stress corrosion cracking. Crevice corrosion, where trapped moisture and contaminants promote localized corrosion, can also escalate the issue, adding complexity to the corrosion landscape. These environmental factors can significantly impact the integrity of aircraft structures and lead to increased maintenance requirements. To improve the longevity and safety of aerospace structures, ongoing research is crucial to better understand how specific environmental conditions contribute to corrosion in these complex systems. This includes not just improving material selection but also developing more sophisticated preventive measures to mitigate environmental influences and extend the operational life of aerospace components.
The severity of galvanic corrosion in aerospace structures is heavily influenced by the surrounding environment. The concentration of electrolytes, particularly chloride ions, can dramatically accelerate corrosion, even in seemingly minor quantities. This is particularly true in environments with high humidity or near saltwater, where the presence of moisture readily enhances the conductivity required for corrosion.
The role of microorganisms, especially sulfate-reducing bacteria (SRB), shouldn't be overlooked. These bacteria can accelerate corrosion through their metabolic processes, generating corrosive byproducts and forming biofilms that create hard-to-detect, localized corrosion hotspots. It’s becoming increasingly apparent that biological factors should be taken into account in the overall corrosion assessment.
Rapid temperature variations can introduce thermal stresses in aircraft structures, potentially leading to the development of microcracks—perfect locations for corrosion to initiate and intensify. This phenomenon is especially crucial for structures subjected to diverse temperature cycles, highlighting the importance of designing materials to withstand such stresses.
The surface finish of materials can significantly impact their susceptibility to corrosion. Rougher surfaces, due to manufacturing processes or environmental wear, can trap moisture and pollutants more efficiently, leading to localized corrosion. This emphasizes the significance of surface finish considerations during design and material selection.
Anodizing, a widely used technique to protect aluminum, provides an oxide layer that offers some resistance to corrosion. However, this protection is not foolproof. Any damage to the coating, such as scratches or inadequate thickness, can compromise its effectiveness. Therefore, careful evaluation and testing of anodized layers in various environments are needed to ensure sufficient protection over time.
Isolation methods, which aim to separate dissimilar metals using insulation, can potentially fail due to degradation caused by environmental factors. If insulation breaks down, it can inadvertently promote galvanic corrosion by allowing electrical contact between the metals. This serves as a reminder that strategies aimed at prevention must be robust enough to withstand long-term environmental exposures.
Protective coatings, though intended to mitigate corrosion, can themselves become problematic if applied improperly. Issues like trapped moisture under the coating can lead to corrosion instead of preventing it. It highlights the criticality of rigorous quality control and inspection procedures to ensure coatings perform their intended role reliably.
The type of stainless steel used also plays a role in galvanic interactions with aluminum. Stainless steels with high chromium content can intensify localized corrosion due to their increased nobility relative to lower-chromium grades. Selecting materials wisely within the context of the operational environment is crucial.
High humidity, a primary concern for aviation, can be both a facilitator and an accelerator of corrosion. Not only does it create a conducive environment for corrosive electrolytes, but it can also promote condensation in micro-cracks or crevices between different metals, accelerating localized corrosion processes. This highlights the complexity of the challenges in high humidity environments.
Certain aluminum alloys can undergo an age-hardening process that modifies their microstructure and unfortunately, can increase their susceptibility to galvanic corrosion. Understanding this effect is particularly important when designing structures that combine age-hardened aluminum with other materials.
The insights highlighted underscore that understanding the interaction between environment and material pairings in aircraft is critical for preventing corrosion. While there have been significant strides in corrosion mitigation, it's clear that ongoing research and a deeper appreciation for environmental complexities will remain a significant aspect of ensuring the long-term integrity of aerospace structures.
Galvanic Corrosion Between Stainless Steel and Aluminum Mechanisms and Prevention Strategies in 2024 - Composition and Performance of B8M Stainless Steel Fasteners
B8M stainless steel fasteners, meeting the ASTM A193 Grade B8M standard, are designed for demanding environments where high corrosion resistance is paramount. These fasteners are typically fabricated from 316 stainless steel, a material with a specific chemical makeup that contributes to both high strength and resistance to corrosion processes like pitting and scaling. Their suitability for severe conditions, such as those found in pressure vessels and pipelines, highlights their ability to withstand high tensile loads and elevated temperatures. However, concerns arise when B8M fasteners are used in conjunction with dissimilar metals, specifically aluminum, as this can create conditions that lead to galvanic corrosion. It becomes crucial to understand the unique properties of B8M stainless steel and the way it interacts with its surrounding environment to implement effective strategies for minimizing or preventing corrosion in structural assemblies that utilize these fasteners. Design choices and a proactive maintenance plan are vital for ensuring the integrity of these structures and minimizing the risk of deterioration caused by galvanic interactions.
B8M stainless steel fasteners, frequently employed in structural applications, are composed of nickel (ranging from 8 to 10.5%), chromium (18 to 20%), and a notable amount of manganese. This particular mix gives B8M a slightly enhanced resistance to pitting and crevice corrosion compared to typical austenitic stainless steels.
The B8M grade offers a minimum tensile strength of 100 ksi (about 690 MPa), making it a strong choice for structural elements. This strength is complemented by its ductility, which means it performs better under variable loading scenarios.
Differing from lower grades, B8M commonly undergoes a solution annealing process that significantly enhances both its corrosion resistance and overall mechanical characteristics. This process involves heating the steel to at least 1900 °F (1040 °C) followed by rapid cooling.
When stainless steel and aluminum come into contact, B8M can act more nobly than other grades due to its chromium content. This can make the rate of aluminum oxidation faster, even without significant outside electrolytes.
B8M's composition grants it better resistance to corrosion in chlorine-rich environments than common grades like SS304. This improved performance is particularly advantageous in coastal and chemically harsh atmospheres.
The quality of the finish on a B8M fastener significantly impacts its corrosion resistance. A passivated surface improves the protective oxide layer, which, in turn, reduces the chance of localized corrosion when paired with aluminum.
Though classified as an austenitic stainless steel, B8M can show slight magnetic properties. This can stem from the cold working or the solidification process during production and is unusual for this type of steel. It's important to consider this characteristic in specific applications where magnetic permeability is critical.
Despite its robustness, B8M can succumb to stress corrosion cracking in chloride-containing environments, particularly when subjected to high tensile stresses or high temperatures. This emphasizes the need to be cautious about the operating conditions.
B8M fasteners are created with precise dimensional control, generally adhering to standards like ANSI/ASME B18.2.1. This precision makes them well-suited for integration into designs requiring exact specifications.
The cost of B8M fasteners is usually higher than more common stainless steel choices due to the alloying elements. This can become a critical factor in budget-conscious projects while aiming to maintain optimal performance. This cost trade-off should be carefully weighed.
Galvanic Corrosion Between Stainless Steel and Aluminum Mechanisms and Prevention Strategies in 2024 - Isolation Techniques for Preventing Metal-to-Metal Contact
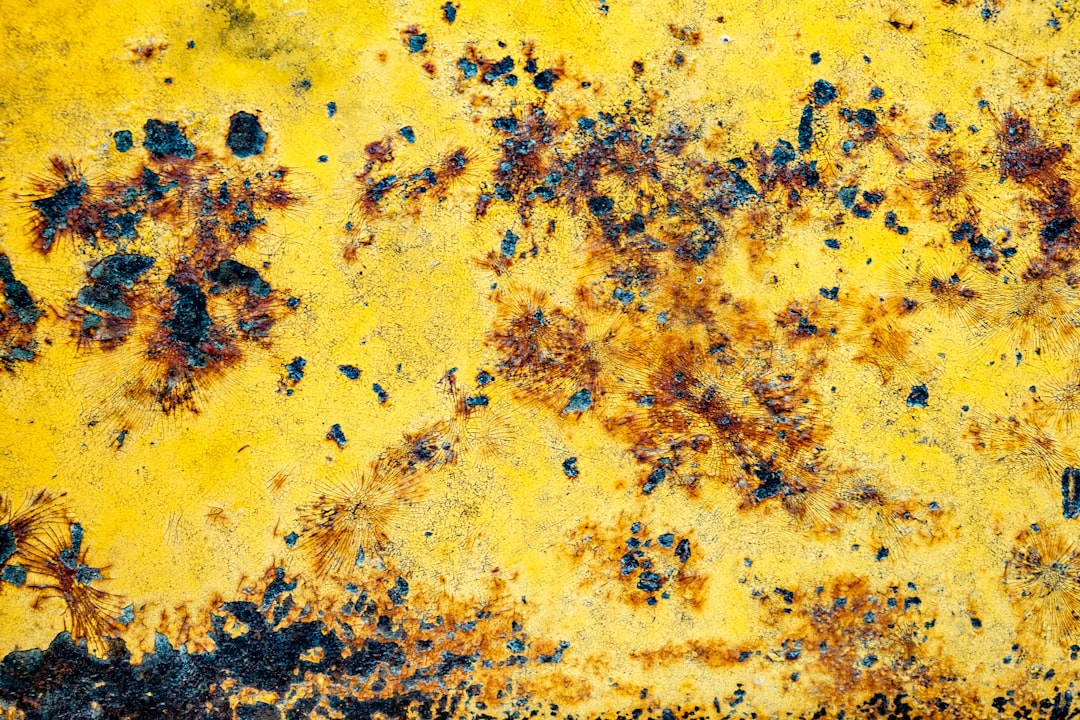
Preventing direct contact between stainless steel and aluminum is crucial in mitigating galvanic corrosion. Isolation techniques, implemented through the use of non-conductive materials, serve as a primary defense against the formation of galvanic cells. This can be achieved through the use of insulating materials like plastic or rubber washers, gaskets, or sleeves strategically placed between the metals. The goal is to interrupt the electrical pathway that drives the corrosive process.
Furthermore, applying protective coatings to both metals—such as paints, powder coatings, or anodizing—can create a physical barrier against corrosive environments, offering another layer of isolation. However, a crucial caveat is that the integrity of these isolation measures relies on maintaining the durability of the insulation materials. Any degradation or failure of the insulation can reinstate direct metal contact, leading to a renewed risk of corrosion.
It's also worth noting that simply choosing materials that are closer together in the galvanic series can help reduce the magnitude of the galvanic potential difference, lessening the driving force behind the corrosion process. However, in many cases where structural integrity is paramount, isolation techniques are a necessary safety measure to be incorporated into the design. Ultimately, a robust strategy involves combining material selection with thoughtful application of reliable isolation methods, ensuring the long-term performance and minimizing the risk of failure in structures that combine stainless steel and aluminum.
When aiming to prevent metal-to-metal contact between stainless steel and aluminum to mitigate galvanic corrosion, the choice and implementation of isolation techniques are critical, but not without their own set of challenges. The effectiveness of insulation materials, such as nylon or Teflon, can be compromised by environmental factors like UV light or extreme temperature changes. This degradation can lead to a breakdown of the insulation and the potential for galvanic corrosion to occur.
Furthermore, not all insulating materials offer the same level of electrical resistance. This variation can affect their ability to prevent electron flow between dissimilar metals, highlighting the importance of selecting the appropriate insulation material and thickness. The thermal expansion differences between stainless steel and aluminum can also introduce mechanical stresses on the insulating layer. As the metals expand and contract at different rates, the insulation can crack or shift, creating unwanted pathways for corrosion.
It's not sufficient for insulation simply to prevent direct contact, it must also guard against moisture accumulation. Moisture trapped within an insulation layer can act as an electrolyte, encouraging the very corrosion we are trying to prevent. Similarly, the surface quality of the insulating material influences its adhesion to the underlying metals. Poor surface preparation leading to inadequate adhesion can result in insulation delamination over time, diminishing its ability to prevent galvanic corrosion.
Sometimes, surface coatings on stainless steel can inadvertently create issues. If these coatings aren't compatible with the isolation materials, their breakdown can expose bare metal to the aluminum, leading to localized corrosion cells. Also, insulating materials have a range of thermal conductivities, which is significant in applications where heat dissipation is a design concern. Poor heat management can produce localized hotspots that alter the metals' electrochemical behaviors and impact corrosion rates.
Dynamic loading conditions, such as vibration from operating machinery, can also cause problems. The insulation can be shifted or degraded, potentially leading to metal-to-metal contact. The isolation strategy must be carefully considered with these potential dynamic stresses in mind. Effective isolation is not simply about placing a piece of insulator between two metals; the design needs to ensure the insulator remains protected from both environmental influences and physical damage.
Ultimately, while insulation techniques offer a valuable pathway to preventing galvanic corrosion, they require ongoing monitoring to ensure they remain functional. Over time, insulation can fail, permitting unintended metal contact that can lead to significant material degradation and possible structural failures. Regular inspections of insulation are thus crucial for maintaining the integrity of stainless steel-aluminum structures and preventing unwanted consequences of galvanic corrosion.
Galvanic Corrosion Between Stainless Steel and Aluminum Mechanisms and Prevention Strategies in 2024 - Impact of MAO Treatment on Aluminum's Corrosion Resistance
Microarc oxidation (MAO) treatment enhances aluminum's ability to resist corrosion by creating a protective ceramic coating. This coating, primarily composed of aluminum oxide (Al2O3), provides a barrier against wear and corrosion in harsh environments. The MAO process involves applying a voltage higher than the breakdown voltage of the gas layer surrounding the aluminum, resulting in the formation of this robust ceramic layer. This ceramic layer helps significantly in mitigating galvanic corrosion, which occurs when aluminum is in contact with more noble metals like stainless steel, especially in environments like seawater where corrosion is accelerated. The success of this MAO treatment hinges on the quality of the formed Al2O3 layer, including its thickness and hardness, influencing its ability to withstand corrosion and wear. Understanding how these factors interplay with the environment is crucial to optimizing the design and maintenance of aluminum structures that might be coupled with stainless steel components, especially in demanding applications.
The surface treatment of aluminum, like anodizing, is a common way to improve its resistance to corrosion. However, the effectiveness of these anodized layers hinges on factors like their thickness and consistency. Any localized damage can weaken their protective function, potentially causing accelerated corrosion in the exposed areas.
Micro-arc oxidation (MAO), sometimes referred to as plasma electrolytic oxidation (PEO), can generate a much thicker alumina layer compared to standard anodizing techniques, resulting in superior resistance to galvanic corrosion. This process essentially creates a ceramic-like surface on the aluminum, strengthening the underlying material and forming a dense, yet porous, oxide layer. Adding specific chemicals during the MAO process can further enhance the protective properties of the coating.
The presence of an MAO layer modifies aluminum's electrochemical behavior. Its increased surface resistance can influence the cathodic and anodic reactions that contribute to galvanic corrosion, potentially affecting the overall corrosion rate when in contact with materials like stainless steel.
The MAO process itself alters the aluminum's microstructure, creating a more intricate pore structure. This can impact the way protective coatings adhere. While this increased complexity might help trap contaminants, depending on the environmental conditions it could also potentially exacerbate localized corrosion.
Besides corrosion resistance, MAO treatment can also improve the fatigue life of aluminum components, which is crucial in engineering applications subjected to repetitive loading cycles. This enhanced durability contributes to a reduced risk of unexpected failures.
The composition of the aluminum alloy can significantly impact the characteristics of the MAO layer. Some alloys might produce stronger, thicker layers, while others might make the aluminum more susceptible to corrosion in a galvanic couple due to the vulnerability to aggressive elements like chloride.
MAO oxide layers are generally more resistant to wear and corrosion over time than traditional anodized coatings, making them a more reliable option in many cases. However, physical damage to the MAO layer can rapidly lead to corrosion, highlighting the importance of careful handling and installation during construction.
While MAO significantly increases aluminum's resistance to corrosion, it's not a perfect solution. Exposure to extreme temperatures or highly aggressive chemicals can still compromise the treated layer's protective qualities.
Combining MAO treatment with other protective coatings can establish a multi-layered defense against galvanic corrosion. This approach offers the potential for higher durability, but careful consideration must be given to ensuring compatibility between these layers to achieve optimal performance.
The initial cost of MAO treatment might be higher than conventional methods. However, the long-term benefits of extending the life of aluminum components in harsh environments, particularly in demanding applications like marine and aerospace engineering, can offset this initial investment.
Galvanic Corrosion Between Stainless Steel and Aluminum Mechanisms and Prevention Strategies in 2024 - Role of Electrolytes in Galvanic Corrosion and Control Strategies
Electrolytes play a crucial part in accelerating galvanic corrosion, especially when aluminum and stainless steel are in contact. This happens because these metals possess different electrochemical potentials, leading to a flow of electrons and, ultimately, material deterioration, mainly affecting aluminum. The presence of a conductive medium, such as moisture containing dissolved salts, is critical. It acts as a pathway for electron transfer from the aluminum (acting as the anode) to the stainless steel (which becomes the cathode), thus fueling the corrosion reaction. Factors such as the specific electrolyte composition, humidity levels, and temperature significantly influence the corrosion rate.
To counter this issue, different strategies are employed. One approach is careful material selection, minimizing the electrochemical potential difference between coupled metals. Another is using protective coatings, creating a physical barrier that shields the aluminum from the corrosive environment. Isolation techniques, such as the use of insulating materials, also play a role in preventing direct contact and hence, galvanic corrosion. A thorough understanding of these factors helps in designing more robust structures where aluminum and stainless steel are combined, ensuring their long-term integrity and performance. While progress has been made, ongoing research and a continued understanding of these interactions remain crucial for extending the lifespan of such structures.
1. The presence of even trace amounts of dissolved salts in water can significantly boost the conductivity of electrolytes, which in turn accelerates the rate of galvanic corrosion between stainless steel and aluminum. This is especially concerning in marine settings or areas prone to salt spray, where the heightened risk of corrosion can lead to unforeseen structural failures.
2. Different stainless steel grades exhibit varied electrochemical potentials, which can impact the severity of galvanic corrosion when paired with aluminum. For instance, stainless steels with higher chromium content tend to be more noble, potentially increasing the corrosion rate of adjacent aluminum due to their elevated electrode potential.
3. The pH of the electrolyte plays a major role in galvanic corrosion. Acidic environments can drastically increase corrosion rates, while alkaline conditions may offer some degree of protection to the aluminum. Engineers must carefully consider the surrounding chemical environment during the design phase to prevent premature component failure.
4. Microbial activity, particularly the presence of sulfate-reducing bacteria, can induce localized corrosion that's far more intense than anticipated. These microorganisms produce corrosive byproducts and form biofilms, adding complexity to the corrosion landscape and challenging material selection and maintenance strategies.
5. Temperature fluctuations can significantly alter the kinetics of electrochemical reactions involved in galvanic corrosion. For example, corrosion rates can double with every 10°C rise in temperature, highlighting the importance of careful thermal management in design to mitigate associated risks.
6. Surface finish plays a critical role; rougher surfaces on aluminum can trap electrolytes and promote localized corrosion. Engineers need to ensure proper machining and surface preparation to minimize these vulnerabilities, as surface texture has a direct impact on corrosion behavior.
7. Protective measures must consider the long-term performance of isolation techniques. Insulating materials can degrade over time due to UV exposure or differences in thermal expansion, potentially leading to unexpected metal contact that initiates galvanic corrosion if not routinely monitored.
8. When dealing with aluminum alloys, it's essential to remember that certain alloying elements can either enhance or diminish galvanic corrosion resistance. For example, the presence of magnesium in aluminum alloys can make them more susceptible to corrosion when paired with stainless steel, underscoring the need for careful alloy selection.
9. Anodized coatings might not always provide complete protection against corrosion. Any defects or imperfections in the coating can act as initiation sites for corrosion, highlighting the need for stringent quality control during the coating application process.
10. Interestingly, the presence of specific alloying elements in both stainless steel and aluminum can influence electrochemical behavior within galvanic couples. For instance, the inclusion of copper in aluminum can lead to increased corrosion rates—a fact often overlooked in materials selection for structural applications.
More Posts from aistructuralreview.com: