Analyzing Soil Excavation Costs A 2024 Breakdown of Factors Influencing Price per Cubic Yard
Analyzing Soil Excavation Costs A 2024 Breakdown of Factors Influencing Price per Cubic Yard - Soil Type and Composition Impact on Excavation Pricing
The nature of the soil significantly impacts the cost of excavation projects. The soil's composition, whether it's loose and sandy or dense and clay-like, directly influences the tools and methods needed for digging. This, in turn, affects the overall price tag.
Excavation projects in areas with challenging terrain, like rocky or uneven land, often require more specialized equipment, leading to higher expenses. This is because specialized machinery or unique techniques may be needed to navigate the difficult conditions and ensure safety.
Furthermore, soil conditions aren't static. They can be altered by seasonal changes, like heavy rainfall or periods of drought, which can impact the stability and workability of the soil. These variations in soil properties can potentially create shifts in excavation costs.
It's clear that having a deep understanding of the soil type and its behavior is critical when planning and budgeting for excavation work. Accurate assessments of soil conditions allow for more precise cost estimates and help in the effective management of project resources. Failing to account for these variables could lead to unforeseen costs and delays.
The characteristics of soil, beyond just its basic type, profoundly impact the financial aspects of excavation. Soil density, for instance, directly influences the machinery needed. Denser materials necessitate more robust and powerful equipment, which naturally leads to increased fuel consumption and faster equipment wear and tear, driving up overall costs.
The presence of groundwater can introduce significant challenges. Managing water during excavation often requires specialized drainage methods, potentially increasing costs by a substantial margin—in certain situations, exceeding 30%. This adds another layer of complexity and cost to the project.
Clay-rich soils present their own unique difficulties. Their inherent tendency to expand when wet and contract during dry periods can destabilize excavation sites, potentially leading to structural problems if not carefully managed. This unpredictable behavior necessitates specific precautions during excavation, increasing both planning and execution costs.
Encountering rock or numerous boulders in the ground fundamentally alters the excavation process. Specialized drilling or even blasting techniques may be required, leading to increased expenses associated with specialized labor and potentially more costly materials than what's typically used in earth moving.
Even the time required for excavation can be affected by soil composition. Highly stratified soils, for example, may demand a more deliberate and time-consuming approach as careful layer removal is necessary. This, in turn, impacts labor costs.
Contamination of the soil introduces yet another hurdle. Specialized handling and disposal procedures are mandatory for contaminated soil, significantly driving up the overall cost. In some instances, contaminated soil can raise project costs by 40% to 50%.
The angle of repose, the maximum stable slope of a soil type, is a factor that varies dramatically depending on the soil composition. This variation has direct implications for excavation site design and can trigger additional engineering costs to ensure stability.
Even the seemingly abstract concepts of friction angle calculations reveal themselves as relevant to excavation pricing. These calculations, vital for understanding a soil’s response to forces, differ substantially between sandy and clay soils. Such differences guide the choice of excavation equipment, further impacting the final cost.
In areas susceptible to expansive soils, the soil's shrink-swell potential becomes a crucial factor influencing project costs. Excavation projects in such regions frequently mandate comprehensive engineering assessments to mitigate risks, which can lead to substantially higher expenses.
Finally, even the temperature of the soil can influence excavation costs. Cold, waterlogged soils can greatly increase the load on excavation equipment, potentially leading to more frequent breakdowns and increased maintenance needs, creating complications for budget forecasting. Understanding these nuances is crucial for creating accurate estimates and avoiding project delays or cost overruns.
Analyzing Soil Excavation Costs A 2024 Breakdown of Factors Influencing Price per Cubic Yard - Equipment Selection and Its Influence on Costs
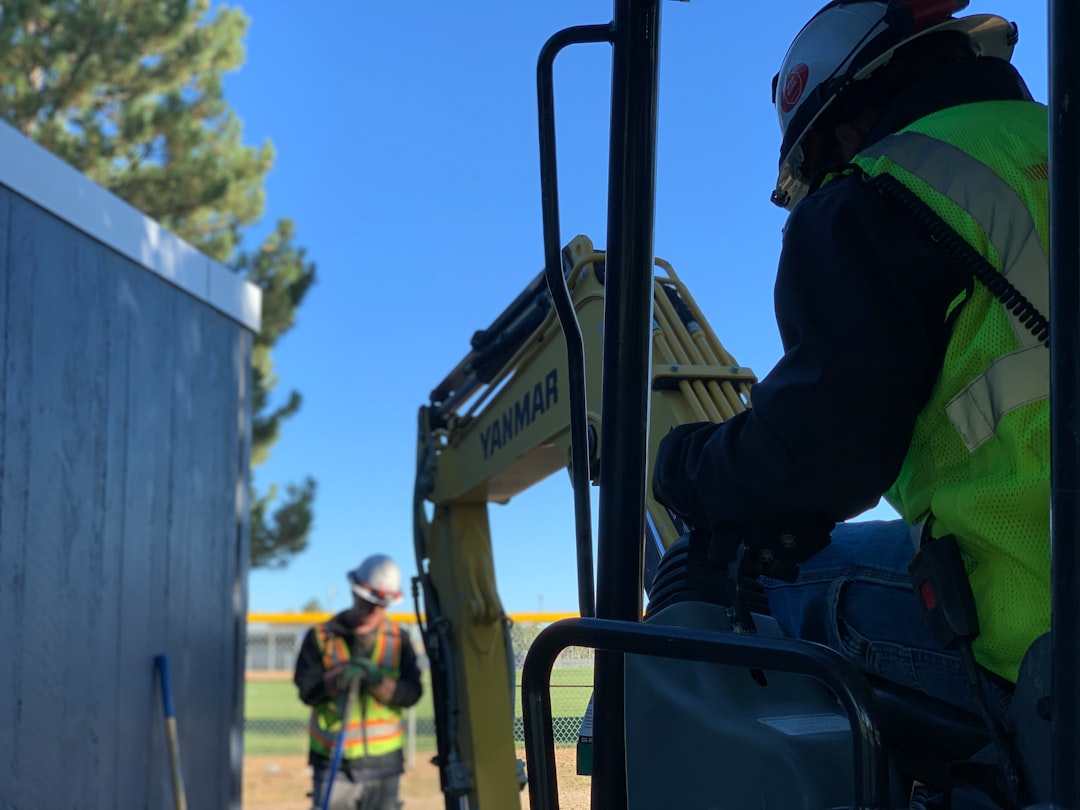
The selection of excavation equipment significantly impacts the financial outcome of a project. The performance characteristics of the chosen machinery, including cycle time and fuel efficiency, directly influence overall productivity and, subsequently, project costs. Different soil types demand varying levels of equipment sophistication. For instance, excavating rocky terrain typically requires specialized equipment that can handle the increased resistance, leading to higher operational costs. Conversely, using underpowered or inappropriate equipment for a given task can extend project timelines and inflate costs due to increased fuel consumption, a higher frequency of breakdowns, and more extensive repair needs. Furthermore, factors like fuel prices, and the inherent characteristics of the soil, such as its density and moisture content, influence the optimal equipment selection for maximizing efficiency. Ultimately, a well-planned approach to equipment selection that considers all the relevant variables can optimize excavation projects and mitigate unexpected cost overruns, leading to a more efficient and successful undertaking.
The selection of excavation equipment significantly impacts project outcomes, influencing both productivity and overall costs. Factors like a machine's power, digging speed, and fuel consumption are key determinants of its suitability and, therefore, its impact on expenses. For example, different excavators can vary considerably in their fuel efficiency, with some models consuming up to 30% more fuel than others due to variations in engine size and design. This difference in fuel use translates directly into higher operational costs over the life of a project.
Furthermore, incorporating advanced technology, such as GPS and telematics systems, into excavation machinery can enhance efficiency and, in turn, help minimize project costs. These automated systems enable greater precision during the excavation process, leading to less unnecessary digging and reduced material waste, potentially saving up to 15% in wasted resources.
However, the cost picture extends beyond fuel consumption and technological advancements. Each type of excavation equipment demands specific maintenance routines and costs. For example, machines relying on hydraulic systems often require more frequent fluid changes, which increases their upkeep compared to mechanically driven counterparts.
A major decision impacting costs is whether to rent or purchase equipment. While renting reduces the upfront financial burden, it can lead to significantly higher expenses in longer-term projects, sometimes adding as much as 20% to the overall cost.
Understanding the load capacity of excavation equipment is paramount. Using equipment with insufficient capacity for the project can result in delays and cost increases due to frequent equipment swaps or failures. This can lead to increased cycle times of up to 25%.
The ratio of labor to equipment usage also influences costs. In scenarios where equipment can operate more autonomously, optimizing the labor-equipment ratio can potentially reduce labor costs by 10% to 15%.
The use of specialized attachments, like hydraulic breakers or augers, can significantly impact both efficiency and costs. While attachments enhance certain tasks, they also add to upfront equipment investment and increase the complexity of maintenance procedures.
Geographic location is a significant consideration when determining overall costs. Transporting heavy machinery to remote sites can increase project costs by 5% to 20%, highlighting the importance of carefully planning equipment logistics.
Operator skill levels are often an overlooked factor. Experienced and well-trained operators can maximize machine performance, reducing operating time and overall costs. In contrast, inefficient operators can increase project costs by as much as 30%.
Equipment downtime due to breakdowns can severely disrupt project timelines and increase costs. Studies have shown that downtime can inflate project costs by up to 25%. To manage these risks, regular preventive maintenance programs are crucial for containing project expenses.
In conclusion, the selection of equipment is an integral aspect of cost control in excavation projects. Considering the factors discussed above, from fuel consumption and technology integration to maintenance needs and operator proficiency, can greatly improve decision-making and contribute to successful, cost-effective excavation projects.
Analyzing Soil Excavation Costs A 2024 Breakdown of Factors Influencing Price per Cubic Yard - Labor Rates and Skilled Operator Availability in 2024
The excavation industry in 2024 faces ongoing hurdles related to labor costs and the availability of skilled operators. A substantial increase in construction projects, fueled by housing shortages and general market demand, requires a significant influx of workers – roughly 723,000 new hires per year. However, a persistent labor shortage exists, putting upward pressure on operator wages. Hourly rates for operators vary, typically ranging from $100 to $300, with the cost depending on whether they supply their own equipment. While many firms plan to expand their workforce, with 69% anticipating hiring more workers, the gap between demand and available skilled labor is likely to keep labor rates volatile. These factors combined highlight the need for excavation contractors to carefully plan and budget for labor costs to avoid potential cost overruns in their projects.
Examining the current labor landscape in 2024 reveals a complex interplay of factors influencing the cost of excavation projects. There's a growing concern about the availability of skilled operators, with some regions potentially facing a 15% shortfall in experienced personnel. This tight labor market is expected to extend project timelines and drive up costs.
We're also seeing a noticeable upward trend in operator wages, with estimates suggesting an 8% increase in 2024. This competitive market for skilled workers is forcing contractors to carefully consider their budget allocations, which could ripple through project costs.
Interestingly, the introduction of automated and AI-driven excavation equipment is altering the skillset demands. While reducing the sheer number of operators needed, it creates a need for workers proficient in managing these advanced technologies. This shift highlights the need for new training programs and initiatives to ensure a skilled workforce for the future.
Furthermore, a tightening of regulations around operator certification is impacting project costs. Projects that fail to employ certified personnel may face a 20% increase in operating costs and potentially face delays due to compliance checks and potential work stoppages. This necessitates a closer look at workforce qualification requirements.
Adding to the labor market complexities, an aging construction workforce is facing a significant retirement wave. Over 25% of skilled operators are expected to retire by the end of 2024, leading to challenges in recruiting and training a new generation of workers. This presents a substantial human resource gap.
We also observe noticeable geographical disparities in labor availability and pricing. Urban areas with vigorous construction sectors are experiencing labor rates that can be 30% higher than rural areas, affecting project budgeting strategies. Contractors need to be mindful of these regional fluctuations when planning costs.
The impact of unions on the labor market is another factor to consider. In unionized markets, wages and benefits tend to be more stable. Conversely, in non-union sectors, hourly rates for operators can be more variable, making project cost forecasting less predictable.
Construction backlogs are also influencing labor costs. With some markets experiencing project backlogs of up to six months, contractors might need to secure operators at a higher cost to ensure timely project completion. This dynamic particularly impacts urgent or time-sensitive projects.
In the wake of the pandemic, a renewed emphasis on health and safety protocols has driven a need for better-trained personnel. Projects failing to meet these stringent safety standards could incur increased costs due to delays and penalties for non-compliance.
Finally, we observe that industries like renewable energy and infrastructure are also competing for skilled operators, exacerbating the labor scarcity. This competitive landscape may force the excavation industry to enhance compensation packages to attract and retain talent.
All these intertwined factors paint a nuanced picture of the labor market in 2024. Recognizing the challenges and opportunities arising from these trends will be crucial for project managers seeking to control costs and ensure successful completion of their excavation projects.
Analyzing Soil Excavation Costs A 2024 Breakdown of Factors Influencing Price per Cubic Yard - Site Accessibility and Location Considerations
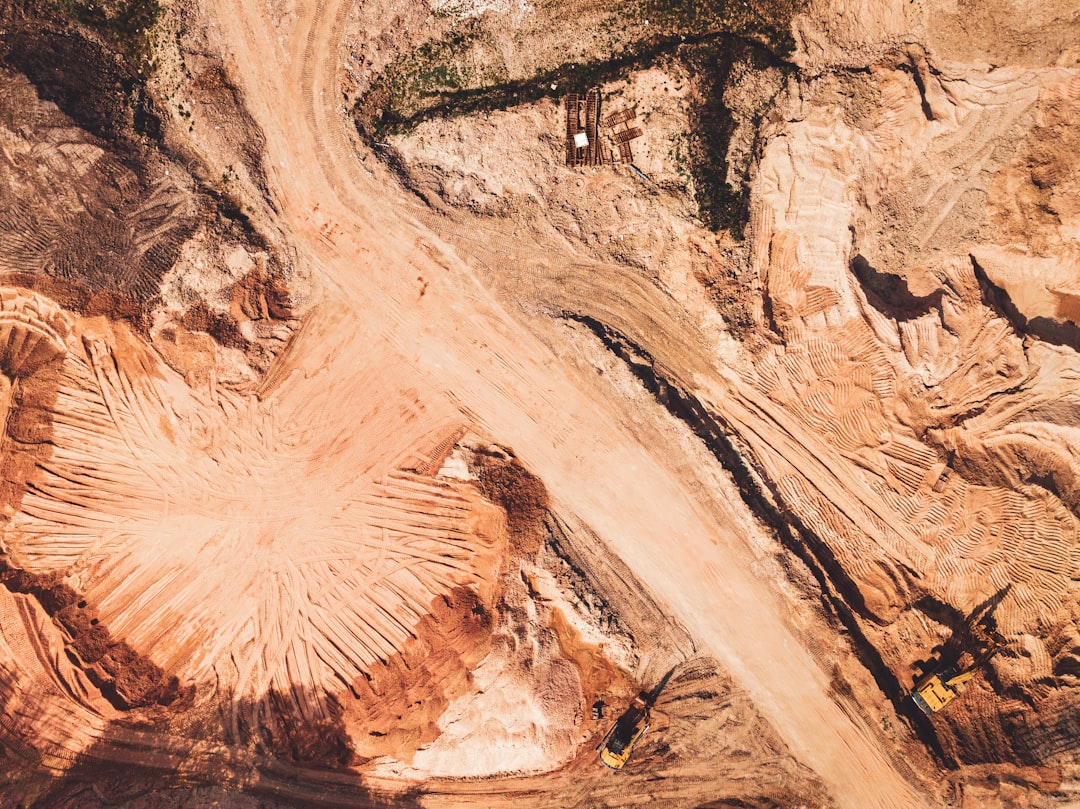
The accessibility of a site and its geographical location play a significant role in determining excavation costs in 2024. Projects in remote or difficult-to-access locations often face increased expenses. This is because transporting equipment and materials to these areas can be costly and time-consuming, and specialized equipment may be needed to handle the terrain. Furthermore, projects closer to urban centers might encounter higher costs due to factors like increased labor rates and the greater demand for equipment and resources. A comprehensive understanding of the site's topography, including any environmental concerns, is essential for anticipating potential issues and properly managing expenses. Failing to factor these elements into project planning can lead to unforeseen costs and schedule delays, underscoring the importance of thorough planning from the start. It's crucial to recognize that these location-related factors can have a significant impact on the overall budget, so considering them early is important to achieve a successful project.
Site accessibility and location are crucial factors influencing excavation project costs beyond the soil itself. Terrain features like steep slopes can complicate equipment selection, potentially necessitating specialized machinery and increasing expenses. Projects near existing infrastructure, like roads and utilities, often require intricate planning to protect those resources, leading to potentially significant cost increases—sometimes as much as a quarter of the total.
Regulations also play a significant role. Excavating in historically or environmentally sensitive zones often triggers more stringent permitting processes, leading to longer planning phases and potentially hefty fines. These restrictions can impact budgets, with costs potentially rising 15% or more. Weather conditions can also create uncertainties in scheduling and potentially necessitate unforeseen engineering assessments, potentially adding a fifth to the overall budget.
The accessibility of the site itself impacts logistics and, consequently, costs. Poor road conditions or remote locations might force contractors to use specialized transport, raising costs by as much as 10%. Local laws, especially labor laws, also shape the financial landscape of projects. Regions with strict labor laws, including minimum wage requirements and working hours, typically have higher excavation costs compared to areas with more relaxed regulations—sometimes as much as 30% higher.
The initial condition of the soil also plays a part. Pre-compacted soils necessitate additional preparatory steps before excavation, adding to labor costs and project timelines. This can lengthen project completion dates by as much as 15% or more. Additionally, the availability and cost of disposing of the excavated material can vary significantly, depending on local regulations. Disposal fees can range from $30 to $100 per ton, making a noticeable impact on a project's budget.
Urban vs. rural settings also influence excavation costs. Urban projects, due to the confined spaces and the density of infrastructure, often require a more meticulous approach, potentially incurring 30% higher costs compared to rural projects. Public sentiment, especially in highly publicized areas, might also impact excavation projects, as local communities or advocacy groups can exert influence through protests or advocacy, leading to unforeseen delays or additional costs in managing public relations. These costs can potentially inflate the budget by a tenth or more.
It's apparent that the broader site conditions significantly interact with soil-related challenges when it comes to excavation cost estimates. While we've already examined the soil's intrinsic properties as a significant cost driver, overlooking these site-specific factors can easily lead to underestimation of the total cost. Understanding this broader context is vital to create realistic budgets and avoid costly surprises during a project.
Analyzing Soil Excavation Costs A 2024 Breakdown of Factors Influencing Price per Cubic Yard - Project Scale and Volume Effects on Per Cubic Yard Rates
The size and the amount of earth moved in an excavation project have a big impact on the price per cubic yard in 2024. Smaller projects often have lower hourly costs, usually around $100. But larger projects can see costs jump to between $1,500 and $5,000 because they become more complicated to manage and require more labor. The scale of a project also changes the type of equipment needed. Larger volumes of soil may necessitate specialized and more expensive machines, further pushing up the cost. Things like how easy it is to get to the site and the terrain conditions also add layers of difficulty. These things can make the costs higher than just a simple calculation of volume times the price per unit. It's very important to consider each project's specific circumstances to avoid being surprised by higher costs. Grasping how project size and volume affect the costs is crucial for creating accurate budgets and for managing excavation projects effectively.
The relationship between the scale of an excavation project and the cost per cubic yard reveals some interesting patterns. While it's intuitive to think that larger projects would simply scale up the cost linearly, the reality is more nuanced. There's a concept called "economies of scale" where, for larger projects, the fixed costs of things like equipment mobilization and initial setup are distributed over a greater volume of excavated soil, leading to a decrease in the per-cubic-yard rate. This can result in savings of 10% to 20% compared to smaller projects.
However, there's a point of diminishing returns. As the project volume surpasses the capacity of standard machinery, we can observe that the cost benefits of larger projects can disappear. For example, a project exceeding the typical capacity of a hydraulic excavator may require multiple units, thus negating any cost advantage from the increased volume. This change in methodology can, in some cases, elevate costs by up to 30%.
The significance of mobilization costs, including moving equipment to and setting it up at the job site, becomes more pronounced for smaller projects. While these costs are fixed and get spread out over larger volumes in larger projects, on smaller projects they represent a much larger fraction of the total cost, increasing the price per cubic yard disproportionately.
It's not just about the total cubic yardage; the relationship between volume and depth can influence the way the excavation is executed. Shallow excavations that cover a large area might call for different types of machinery compared to deeper, more narrow excavations. This shift in equipment leads to variations in the overall cost, often by around 15%.
On larger projects, it's possible to utilize labor more efficiently. You can deploy multiple crews and machines simultaneously, reducing the average downtime per worker, effectively lowering the overall cost per cubic yard by 5% to 10%. The issue of where the excavated material, known as spoil, goes is also significant. Large projects may find it easier to reuse or recycle the spoil onsite, leading to cost reductions of up to 25%. Smaller projects, however, frequently face higher disposal fees per cubic yard.
However, larger projects often mean more complex designs. They often require greater coordination between different subcontractors, which can lead to unexpected cost increases. Managing these complexities during the initial planning phase is critical, as failing to do so can inflate costs by 10% to 15%.
The size of a project can also influence how well teams manage weather-related delays. Larger projects, due to better planning and greater resource allocation, may reduce delays from unexpected weather occurrences. This preemptive planning can help save 5% to 10% in what would otherwise be expected costs in regions with unpredictable weather.
One challenge specific to larger projects is something called "site overlap." This happens when the work of one crew interferes with or inadvertently complicates the work of another. This phenomenon can create delays and increased costs, potentially raising the overall budget by as much as 20%.
Lastly, the administrative overhead related to larger projects can be substantial. Larger excavation projects typically involve more stringent reporting, inspections, and regulatory compliance measures. These administrative costs, often overlooked initially, can contribute 10% to the overall project budget, ultimately impacting the final price per cubic yard.
Understanding these intricacies is important. While basic excavation pricing models often focus solely on volume and soil type, recognizing the implications of project scale can provide a more realistic cost assessment and aid in optimizing project planning and resource allocation.
Analyzing Soil Excavation Costs A 2024 Breakdown of Factors Influencing Price per Cubic Yard - Regulatory Compliance and Permitting Expenses in Soil Excavation
Soil excavation projects in 2024 are increasingly complex, and a crucial, often overlooked factor impacting costs is regulatory compliance and permitting. Meeting regulatory requirements can add a significant expense layer to the overall project, with costs associated with hiring compliance experts, adopting specific software, and training staff. Failing to adhere to regulations can also result in substantial financial penalties and project delays, which can be extremely disruptive. The permitting process itself adds another level of intricacy and cost. Obtaining multiple permits, especially when managing soil removal and disposal, adds a considerable administrative burden and further increases project expenses. With the regulatory landscape constantly changing, it is becoming increasingly important for excavation contractors to factor these costs into their planning and budgeting. Failing to do so could expose them to unforeseen expenses, potentially jeopardizing project viability. A forward-thinking approach to regulatory compliance and permitting is essential for navigating these challenges successfully.
The regulatory environment surrounding soil excavation can be surprisingly complex and adds a layer of cost that's often overlooked during initial project planning. The specific regulations can vary drastically depending on the location of the project and the type of soil involved. For example, excavating clay soils might trigger different safety and environmental standards compared to sandy soils, making the permitting process more complicated and potentially increasing the cost by 10% to 20%.
One significant factor affecting costs is the sheer time it can take to obtain the necessary permits. In some areas, securing permits can take as long as six months. This delay impacts the project timeline and increases overall costs by about 15% due to the added financing burdens associated with project start delays.
Inspection fees, while seemingly minor, can add up quickly and are often forgotten during budgeting. The cost of inspections can vary from a few hundred dollars to well over $5,000, depending on the permitting agency's requirements.
Furthermore, soil testing is often mandated before excavation, especially in regulated areas. This testing can easily add $1,000 to $3,000 to the cost, and if there are discrepancies requiring further testing to meet compliance standards, costs can easily rise further.
The challenge becomes even more pronounced when dealing with contaminated soil. Projects on contaminated sites face unique regulatory hurdles and often require specialized permits and remediation strategies. This regulatory burden can increase compliance costs by as much as 40%, reflecting the complex safety and environmental protocols that are needed.
Some jurisdictions also require third-party audits to ensure compliance. While these audits may cost between $3,000 and $8,000, they can ultimately help prevent costly fines and work stoppages due to non-compliance. This is an interesting case of paying for oversight that can save you money in the long run.
Even weather delays can impact compliance costs. If bad weather forces a delay, you might have to apply for a temporary permit, which can be a logistical nightmare and add even more costs—sometimes up to 5% of the entire project budget.
Another wrinkle is the impact of local zoning laws. If excavation requires a change in zoning classification, it can introduce a great deal of added complexity and expenses, potentially inflating the budget by 15%.
Permitting issues can also lead to legal problems. Contentious situations, disagreements, or delays in getting approvals can create an opportunity for lawsuits, and the cost of defending or settling such issues can easily exceed 10% of a project's total budget in some regions. This further complicates financial planning.
Finally, the burden of record keeping is often underestimated. Regulations necessitate meticulous documentation for excavation projects, which increases the amount of administrative work. Maintaining these extensive records can represent as much as 5% of the project's budget, especially if long-term retention is mandated. It seems that the regulatory environment of excavation projects is not only technically complex but also adds a lot of uncertainty into cost forecasting, making accurate budget management challenging.
More Posts from aistructuralreview.com: