Temperature Effects on 316 Stainless Steel Tensile Strength Analysis of Strength Variations Between -50°C and 500°C
Temperature Effects on 316 Stainless Steel Tensile Strength Analysis of Strength Variations Between -50°C and 500°C - Temperature Dependent Yield Strength Analysis From -50°C to 500°C
Examining the yield strength of 316 stainless steel across a wide temperature range, from -50°C to 500°C, uncovers a clear pattern of change. The material's capacity to resist deformation under stress isn't constant but instead shows a distinct shift. Below 200°C, its yield strength falls sharply, which then slows down until temperatures reach approximately 500°C. After this point, the yield strength drops considerably. This behavior highlights how increasing temperatures can significantly weaken the material, especially impacting its ability to withstand tensile forces and its overall flexibility.
It's important to acknowledge that the behavior of 316 stainless steel isn't solely driven by temperature. Other variables, such as how quickly the material is deformed (strain rate) and its past heat treatment history, influence how it reacts under thermal stress. This complexity underscores the need for a careful assessment when designing components intended for environments with fluctuating temperatures. Recognizing the impact of temperature on 316 stainless steel's ability to withstand loads is vital for engineers to ensure the structural safety of the components they design across this temperature range.
Examining the yield strength of 316 stainless steel across a broad temperature range, from -50°C to 500°C, unveils some intriguing behavior. At cryogenic temperatures, like -50°C, the material experiences a notable drop in yield strength compared to its room-temperature value. This considerable decrease necessitates careful consideration in applications requiring the steel to function in ultra-cold environments. Conversely, at elevated temperatures near 500°C, the yield strength suffers a significant decline, potentially exceeding 60% of its room-temperature value. This emphasizes the need for robust design considerations when 316 stainless steel is employed in high-heat settings.
The temperature range under investigation encompasses distinct microstructural transformations. The creation and behavior of dislocations and precipitates are key to understanding how the material's strength changes. We observe a "ductile-to-brittle transition" at low temperatures, where the primary mode of failure shifts, impacting the safety margins incorporated into designs.
At high temperatures, oxidation becomes crucial to assessing the yield strength. While initially, the protective oxide layer may improve strength, sustained exposure can introduce embrittlement, a factor engineers need to factor in for long-term performance. The relationship between temperature and yield strength is not linear, necessitating meticulous and specifically-targeted experimental measurements to capture accurate data across the entire range. Strain rate becomes yet another critical factor, particularly when considering real-world applications with various loading scenarios. How quickly the material is loaded can either amplify or lessen the observed changes in yield strength.
Furthermore, the precise alloying elements and their interactions with temperature impact yield strength, complicating efforts to engineer for both good mechanical properties and corrosion resistance in extreme thermal conditions. This interplay of elements and temperature also becomes crucial when considering fatigue behavior. Both low and high temperatures can lead to reductions in fatigue resistance, so a thorough grasp of yield strength variations over the full temperature spectrum is required for ensuring long-term service in critical components. Further complicating things is the material's anisotropic nature at different temperatures, implying that its yield strength can vary directionally. This directional dependency adds more intricacy to the structural design process, especially when dealing with complex geometries. Understanding these subtleties is fundamental for engineers tasked with ensuring the structural integrity of systems exposed to fluctuating thermal environments.
Temperature Effects on 316 Stainless Steel Tensile Strength Analysis of Strength Variations Between -50°C and 500°C - Strain Hardening Behavior Changes at Sub Zero Temperatures
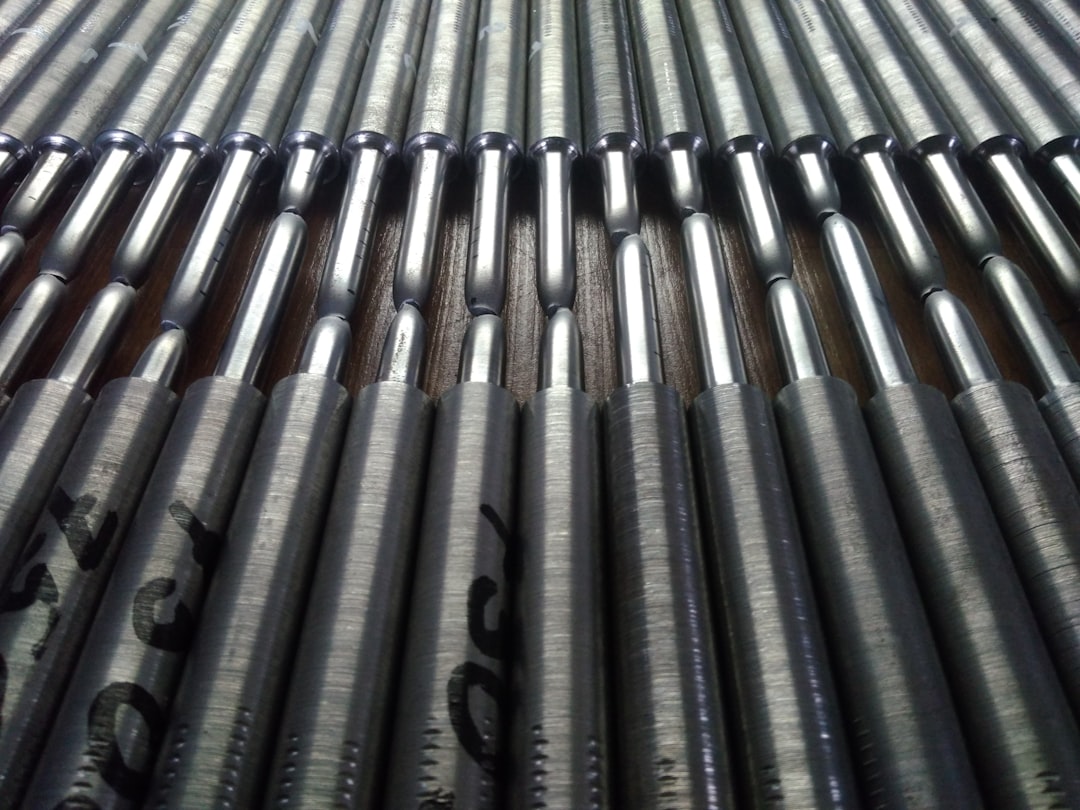
When exploring the behavior of 316 stainless steel at extremely low temperatures, we find that its capacity to harden under strain changes in a notable way. At sub-zero temperatures, the material displays a transition to a new phase of strain hardening. This new hardening phase exhibits a steeper increase in strength, suggesting a potential for higher mechanical performance in challenging environments.
Underlying this altered behavior are changes within the material's structure. The formation of features like twins within the steel seem to play a key role in enabling the material to retain a good balance of strength and ductility, even when temperatures are severely cold. This unique characteristic is important because it demonstrates that 316 stainless steel can maintain its desirable qualities even in the most demanding conditions.
However, the way this material responds to deformation isn't always straightforward. While we can quantify its tendency to harden at room temperature using the strain hardening exponent, the material acts very differently at lower temperatures. This underscores how vital it is to carefully consider the full range of temperatures 316 stainless steel might encounter in practical applications.
As 316 stainless steel is being used more and more in applications where robust performance is crucial, understanding this altered hardening behavior in sub-zero environments is increasingly critical for engineers. By recognizing these changes, designers can optimize designs for optimal performance and safety in real-world, extreme-temperature environments.
At sub-zero temperatures, the way 316 stainless steel hardens under strain takes on a different character, often leading to increased strength, which isn't what we'd typically expect given the reduced ductility we often see in materials at low temperatures. This unexpected strength can potentially lead to failure modes we don't anticipate if we aren't careful.
It seems that something called "strain aging" can happen in 316 stainless steel at low temperatures. This involves how past deformation influences future deformation, and it could potentially make the material more brittle over time, potentially leading to premature failure.
The specific temperature where stainless steel transitions from ductile to brittle behavior varies based on the particular grade. For 316, this transition can occur as high as -50°C, which is a significant point where the material's toughness noticeably decreases.
When the temperature drops, the movement and creation of dislocations within the material's structure are hindered. This leads to a higher yield strength, but unfortunately also a lower overall ductility. This behavior adds complexity to designing components for cryogenic applications.
The microscopic arrangement of different phases in 316 stainless steel, such as sigma and chi phases, can change at lower temperatures. This alteration might result in localized areas where the material is weaker, and these areas might worsen the impact of strain hardening when tensile stress is applied.
Intriguingly, at low temperatures, the strain hardening exponent—a measure of the material's capacity to harden during deformation—can actually increase. This implies that 316 stainless steel can be surprisingly resilient under certain cold-working conditions.
In situations where 316 stainless steel is subjected to rapid temperature swings, the combined effects of strain rate and sub-zero temperatures can amplify the differences in yield strength. This poses another challenge in achieving reliable component performance.
Fracture toughness, which essentially measures how much energy a material can absorb before fracturing, can paradoxically increase at low temperatures in some cases with 316 stainless steel. This creates a bit of a puzzle where the steel can potentially withstand more energy before failing but at the same time is more prone to brittle failure due to microstructural alterations.
The residual stresses introduced during manufacturing processes can interact with low-temperature exposure, leading to unexpected strain hardening responses. This emphasizes the importance of thoroughly evaluating manufacturing methods in relation to the intended application conditions.
Finally, understanding how 316 stainless steel reacts under various loading conditions at low temperatures is crucial. This is because it exhibits unique strain hardening behaviors that influence performance. This points to a need for custom-tailored design approaches when dealing with cold environments.
Temperature Effects on 316 Stainless Steel Tensile Strength Analysis of Strength Variations Between -50°C and 500°C - Mechanical Property Shifts at Key Temperature Thresholds
316 stainless steel's mechanical properties are dramatically affected by certain key temperature points. Notably, as temperatures plummet, especially near -50°C, the steel's ability to deform before breaking (ductility) declines significantly, and it becomes more prone to brittle failure. This change makes using it in ultra-cold environments more difficult. Conversely, when temperatures rise towards 500°C, the material's resistance to deformation (yield strength) noticeably decreases. This weakening is crucial to consider when designing parts that will operate in high-heat situations, as it can impact their ability to withstand loads.
The reasons behind these shifts are intricately linked to changes within the steel's internal structure. How dislocations, which are essentially defects in the crystalline structure, move and interact is critical in determining the material's response to stress and strain. Furthermore, the very nature of strain hardening, the process by which a material gets stronger when deformed, is also altered at these temperature thresholds. It's important to understand these changes in structure and behavior to properly design components that will reliably function across a wide range of temperatures. The challenges are significant, requiring a deeper understanding of the material's behavior at different temperatures to ensure safe and robust performance in a diverse array of applications. It's clear that simply applying a one-size-fits-all approach isn't sufficient, and that designing components that rely on 316 stainless steel in fluctuating temperature conditions must consider how these properties can change at different points.
The mechanical behavior of 316 stainless steel across a wide temperature range is quite complex, with several key thresholds where its properties change significantly. For instance, around -50°C, we see a ductile-to-brittle transition, implying a noticeable reduction in toughness. This shift is a concern in cold environments as it can compromise safety margins in designs. We also need to consider the potential for strain aging, a phenomenon where the material's ductility decreases over time in the presence of prior deformation. This subtle shift can complicate the assessment of long-term reliability, especially in applications with fluctuating loads at sub-zero temperatures.
Interestingly, at low temperatures, 316 stainless steel displays increased yield strength, which is unusual for many materials. This strengthening, possibly due to the formation of twins in the microstructure, could lead to enhanced mechanical performance in cryogenic applications. It does, however, add another layer of complexity to designing for such environments, since the enhanced strength can influence failure modes in ways we may not anticipate.
Furthermore, the material's response to stress at high temperatures, around 500°C, is influenced by oxidation. Initially, oxidation appears to contribute to some strengthening through a protective layer formation, but prolonged exposure leads to embrittlement, impacting long-term performance. This complicates material selection for high-temperature applications where long-term durability is critical.
The mechanical response of 316 stainless steel is also influenced by loading direction. It's anisotropic at various temperatures, meaning yield strength can vary depending on the direction of applied stress. This adds yet another level of intricacy when designing for complex geometries and multi-axial stress states. Additionally, the material's sensitivity to strain rate is particularly evident at extreme temperatures. Rapid loading can significantly amplify the temperature-dependent variations in yield strength.
This highlights the need to carefully consider loading scenarios in real-world applications to ensure designs are robust. Moreover, both low and high temperatures can compromise the fatigue resistance of 316 stainless steel, impacting its durability. Engineers designing components for cyclic loading environments must consider the full temperature range to ensure long-term structural integrity.
The emergence of certain microstructural phases, like sigma and chi, at lower temperatures can also impact yield strength. These phases can result in localized areas of weakness, which may worsen under stress concentration, possibly leading to premature failure. It is also interesting to note that while fracture toughness might seem to improve at low temperatures, the increase in energy absorption can be deceptive. This is because the fracture mode tends to become more brittle under these conditions, making it essential to understand how this aspect influences overall material behavior.
Finally, it's clear that the mechanical behavior of 316 stainless steel is not a simple, predictable response to temperature variations. Understanding these subtle variations in its properties across the operating temperature range is critical for reliable and safe component design. The observed changes in strain hardening behavior, susceptibility to strain aging, anisotropy, and fracture toughness at various temperatures add to the complexities of applying this versatile material in extreme conditions. A thorough knowledge of the complete behavior profile is crucial to making optimal design choices.
Temperature Effects on 316 Stainless Steel Tensile Strength Analysis of Strength Variations Between -50°C and 500°C - Deformation Mechanisms Between Hot and Cold Testing Conditions
When examining how 316 stainless steel deforms at different temperatures, we find very different behaviors in hot and cold environments. At high temperatures, processes like dynamic recrystallization and dynamic recovery become important, subtly altering how the material resists deformation. This is seen in the flow curves obtained during testing. In contrast, cold temperatures, especially those close to cryogenic levels, produce unique changes within the steel's structure. We see the formation of twins and even phase transformations like the development of martensite. These changes lead to a noticeable increase in strength, but they often come at the cost of reduced ductility, which is the material's ability to stretch before it breaks.
The fact that temperature so profoundly affects how this material behaves means that designs need to be very carefully considered. If a component is built from 316 stainless steel and is expected to operate in a range of temperatures, engineers need to be certain that the design anticipates the possible ways it could fail due to the temperature-dependent changes that occur. A clear understanding of these temperature-driven deformation mechanisms is critical to getting the most out of this material in a variety of applications, helping to ensure the components operate as intended and are structurally sound.
Exploring the mechanical behavior of 316 stainless steel across a wide range of temperatures reveals a fascinating interplay of factors that influence its strength and ductility. One noteworthy aspect is the ductile-to-brittle transition, which can occur at temperatures as high as -50°C for 316. This transition significantly reduces toughness, making it crucial for engineers to be aware of this change when designing components for cold environments.
Interestingly, 316 stainless steel bucks the trend of many materials at low temperatures by showing an increase in yield strength. This unusual strengthening behavior is associated with the formation of twins within the microstructure, which can improve mechanical properties even in extreme cold. However, the increased strength may influence failure modes in unexpected ways.
The behavior of dislocations within the material's crystal structure plays a critical role in its response to stress and strain, especially at different temperatures. At low temperatures, dislocation motion and formation are impeded, leading to higher yield strength, but unfortunately this also diminishes the material's ductility.
The interaction of 316 stainless steel with its environment at higher temperatures also presents complexities. While oxidation can initially strengthen the material through the formation of a protective oxide layer at around 500°C, sustained exposure can lead to embrittlement, a factor that engineers must acknowledge for long-term reliability in high-temperature applications.
Furthermore, 316 stainless steel's mechanical properties aren't uniform across all directions; it exhibits anisotropy, which means that the yield strength can vary depending on the direction of applied stress. This directional dependency adds more layers of complexity to design, especially when dealing with intricate geometries and stress states.
The speed at which a load is applied, or strain rate, also has a pronounced effect on yield strength, particularly at extreme temperatures. Rapid loading can further amplify the temperature-induced variations in yield strength. This underscores the need for careful consideration of loading conditions in real-world scenarios.
At low temperatures, changes in the material's microstructure, such as the emergence of sigma and chi phases, can create localized weak points. These areas might become more susceptible to failure under concentrated stress, potentially impacting the material's overall performance and leading to premature component failure.
The fatigue resistance of 316 stainless steel can be notably affected by both high and low temperatures. This underscores the importance of a comprehensive assessment of fatigue behavior across the entire temperature range in cyclic loading applications where long-term durability is paramount.
Another interesting aspect of 316 stainless steel's low-temperature behavior is the phenomenon of strain aging. Strain aging describes how the material's previous deformation history can influence its subsequent responses to stress. It can subtly alter the material's ductility, potentially leading to increased brittleness and potentially unforeseen failure modes.
Finally, while the material's fracture toughness might seem to increase at low temperatures due to greater energy absorption, it is important to realize that this improvement can be misleading. This energy absorption often accompanies a transition to more brittle failure modes, making it essential to understand this dual nature of behavior to prevent premature failures.
In conclusion, the mechanical behavior of 316 stainless steel across various temperatures is far from simple. Understanding these variations in material properties is vital for engineers seeking to develop robust and reliable components. The intricate interplay of strain hardening, dislocation behavior, anisotropic response, strain aging, and fracture toughness across temperature ranges adds layers of complexity to designing components that operate in environments with fluctuating temperatures. A comprehensive understanding of the material's full behavior profile is crucial for making well-informed design choices.
Temperature Effects on 316 Stainless Steel Tensile Strength Analysis of Strength Variations Between -50°C and 500°C - Impact of Strain Rates Across Temperature Ranges
The influence of strain rate across different temperature ranges significantly impacts the mechanical response of 316 stainless steel, adding a layer of complexity to its already intricate behavior. Research indicates that the material's ability to stretch before failure (true failure strain) increases as temperature rises, but this capacity is reduced with increasing strain rates. This reveals a crucial relationship between temperature and ductility, along with the impact of how quickly a load is applied. At low temperatures, the material behaves unexpectedly, displaying a greater yield strength, possibly due to the formation of twins within its crystalline structure. Conversely, at high temperatures, especially around 500°C, the potential for oxidation-induced embrittlement becomes a concern, impacting long-term performance predictions. Furthermore, the material's mechanical properties exhibit directionality (anisotropy), meaning its strength can change depending on the direction of the applied stress. This adds another factor for engineers to consider when designing parts that might experience diverse loading conditions. It's clear that designing components for environments with varying temperatures requires a thorough understanding of these intricate interactions to ensure reliable and safe structural performance.
The response of 316 stainless steel to extreme temperatures presents a fascinating dual nature—it strengthens at low temperatures and weakens at high ones, which defies typical material behaviors. This characteristic, observed across our temperature range of interest, presents unique challenges for design and analysis.
A curious aspect is the presence of strain aging at low temperatures, a phenomenon not common in many materials. This means the material's history of prior deformation can subtly change its subsequent mechanical behavior, adding a degree of complexity to how we predict its long-term reliability. It's important to fully understand how past events affect the material's response, as these subtle shifts could lead to unanticipated failures in a real-world environment.
When exploring the material's behavior at low temperatures, we find that the movement of dislocations within its crystalline structure is significantly suppressed. This inhibition paradoxically results in both increased yield strength and reduced ductility, creating a design dilemma for applications in cryogenic conditions. This makes it a tough balancing act for engineers trying to ensure adequate material strength in very cold conditions without compromising the material's ability to stretch and absorb energy before failure.
Another unexpected characteristic at low temperatures is the formation of twins within the microstructure. This structural adjustment enhances mechanical performance and, intriguingly, allows 316 stainless steel to retain desirable attributes like ductility even when subjected to frigid environments. It's unusual for a material to maintain some measure of elasticity at such low temperatures.
At higher temperatures, around 500°C, we observe the impact of oxidation. While an oxide layer initially seems beneficial and may increase strength, prolonged exposure ultimately introduces detrimental embrittlement. This complication is critical to consider in applications involving prolonged high-heat exposure. This suggests a trade-off in choosing 316 stainless steel where the material needs to be corrosion resistant, but where operating conditions may lead to this gradual embrittlement process.
Furthermore, the mechanical properties of 316 stainless steel are not the same in every direction. This anisotropy suggests that the material's strength varies depending on how a load is applied, which can greatly influence design when dealing with multifaceted stress situations. This means that the geometry of a component or the loading it experiences could lead to unpredictable behavior.
When studying the microstructure at low temperatures, we see the formation of phases such as sigma and chi, which can introduce localized weaknesses within the material. These weak areas are prone to failure under stress concentration, underscoring the need for a comprehensive understanding of the material's microstructural evolution. This emphasizes the importance of having a thorough grasp of how the material behaves when we move outside of typical operating conditions.
Fatigue resistance, a key aspect in cyclical loading environments, appears to be negatively impacted at both extremes of the temperature range. This presents challenges for designing parts subject to repetitive loading conditions in either hot or cold environments. Fatigue resistance appears to be very sensitive to the material's microstructure, which can change under the thermal load and/or the stress cycle.
The strain rate at which a load is applied significantly influences yield strength, particularly at extreme temperatures. It's a crucial consideration because faster loading can exacerbate the temperature-dependent changes in yield strength, highlighting the need to meticulously analyze real-world loading scenarios for various applications. How a load is applied makes a big difference, even for materials that are typically considered robust, which is something we need to be wary of when evaluating designs.
One final aspect is the seemingly counterintuitive observation that fracture toughness increases at low temperatures. While this might seem like a good thing, it's a bit misleading, since this improvement in energy absorption can coincide with a shift to brittle failure modes. Understanding this duality in fracture behavior is essential for safe design. Engineers need to understand that not all changes in behavior are favorable, even if they appear to be initially.
In conclusion, the behavior of 316 stainless steel across various temperatures is intricate and nuanced. Recognizing these intricate property variations is critical for engineers tasked with designing dependable and robust components. The delicate interplay of strain hardening, dislocation behavior, anisotropic responses, and fracture toughness at differing temperatures makes for a challenging design space when operating in fluctuating thermal conditions. This suggests a need for highly accurate computational models that can be used to understand and predict the effects of temperature on 316 stainless steel performance. This is particularly important in critical applications where a component's failure could have severe consequences.
Temperature Effects on 316 Stainless Steel Tensile Strength Analysis of Strength Variations Between -50°C and 500°C - Thermal Effects on Material Microstructure and Performance
The way temperature affects the internal structure (microstructure) and the resulting performance of 316 stainless steel is fundamental to understanding how it behaves under various conditions. At very low temperatures, the material undergoes changes that are not typical of many other materials. For instance, it can form new internal features like "twins" and even transform into different phases like martensite, which, although increasing its strength, often comes with the downside of decreased ductility. This change in behavior introduces challenges in understanding how it will fail in specific situations, highlighting the need for design choices that account for these temperature-induced alterations. As the temperature increases, things become more complex near 500°C. Oxidation becomes a significant factor, initially offering a degree of strength but ultimately promoting brittleness over time. This balance between the positive and negative aspects of oxidation needs careful consideration when choosing this material for high-temperature applications. Ultimately, grasping these intricate relationships between temperature, internal structure, and resulting performance characteristics is essential for ensuring components made of 316 stainless steel will perform reliably and safely in both extremely cold and extremely hot environments.
The behavior of 316 stainless steel across varying temperatures reveals a complex interplay of factors impacting its mechanical properties, particularly its strength and ductility. One notable observation is the occurrence of a ductile-to-brittle transition at temperatures as high as -50°C. This transition significantly reduces the material's toughness, posing a serious concern in cold environments, as it increases the likelihood of brittle failure in components. Furthermore, the material can experience a phenomenon called strain aging at low temperatures. This refers to how past deformation can subtly alter its future mechanical response, which can lead to greater brittleness and potentially unexpected failures in components under cyclic loading.
Interestingly, 316 stainless steel deviates from the trend of many other materials by experiencing increased yield strength at low temperatures. This unexpected strengthening seems to be linked to restricted dislocation movement within the material's structure, as well as the development of features known as twins. This intriguing behavior offers potential performance advantages in cryogenic applications, although it adds a layer of complexity to component design, as it could lead to atypical failure modes. Additionally, 316 stainless steel's mechanical behavior isn't uniform across all directions; it's anisotropic. This means its yield strength can vary based on the direction of applied stress, which is a significant consideration in designs involving complex loading and geometries.
At elevated temperatures, specifically around 500°C, the oxidation behavior of 316 stainless steel comes into play. While the formation of an oxide layer initially provides some measure of strengthening, continuous exposure at these temperatures can result in embrittlement, impacting the long-term integrity of components. This adds yet another factor engineers must consider when designing for applications where sustained high temperatures are anticipated.
We've also observed changes in the steel's microstructure at low temperatures, specifically the development of sigma and chi phases, which can lead to localized areas of weakness within the material. These areas of weakness are more susceptible to stress concentration, and under load, they can promote premature failures in components. We also find that the material's fatigue resistance is negatively affected at both low and high temperatures, which is significant in applications where components experience cyclic loading. Moreover, the rate at which a load is applied (strain rate) can significantly influence yield strength, particularly at extreme temperatures. The faster the loading, the more pronounced the temperature-dependent variations in yield strength can become.
Finally, while fracture toughness appears to improve at low temperatures with an increased ability to absorb energy before fracturing, this observation can be deceiving. The improved energy absorption tends to be accompanied by a transition to more brittle failure modes, highlighting the importance of carefully understanding this dual nature of fracture behavior.
In conclusion, understanding the mechanical behavior of 316 stainless steel across a broad range of temperatures is critical for effective design. This material displays a fascinating array of intricate property changes influenced by temperature, strain rate, and microstructure. The complexities introduced by phenomena like strain aging, anisotropy, and the duality of fracture toughness demand a comprehensive understanding of this material's behavior to ensure reliable performance and safe operation in a wide range of applications. This intricate behavior underscores the need for detailed computational models that can accurately predict how the material will behave at various temperatures, particularly in mission-critical components.
More Posts from aistructuralreview.com: