Weld Passivation Enhancing Corrosion Resistance in Stainless Steel Structures
Weld Passivation Enhancing Corrosion Resistance in Stainless Steel Structures - Understanding the Passivation Process for Stainless Steel Welds
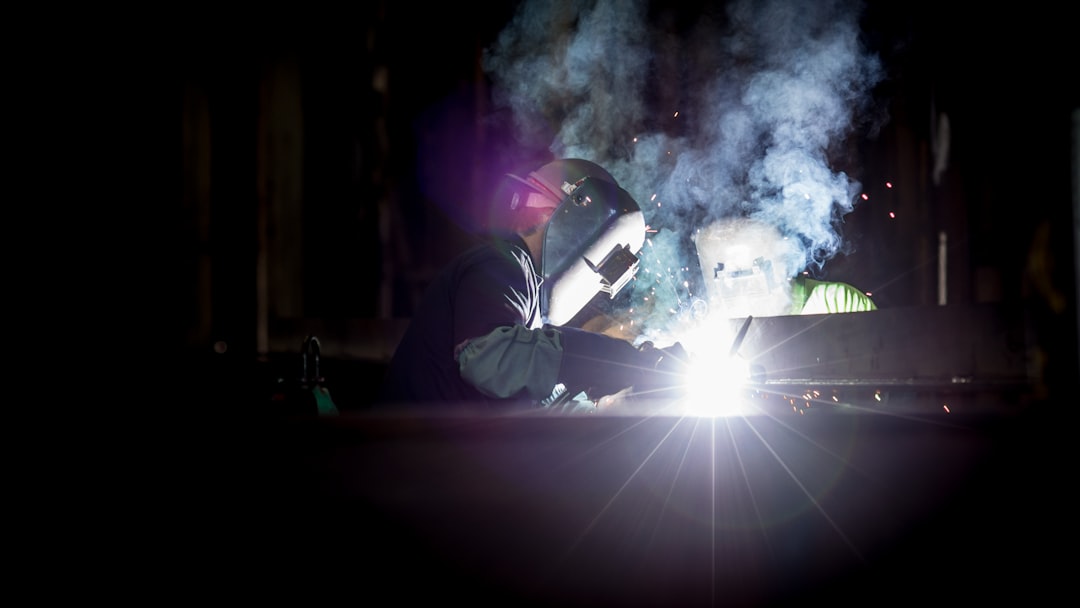
Comprehending the passivation process applied to stainless steel welds is fundamental for maximizing the material's ability to withstand corrosion. This process centers around developing a protective layer of chromium oxide on the weld's surface. This layer acts as a barrier against harmful environmental influences and contaminants that could otherwise compromise the metal. A crucial part of the passivation process is the elimination of residual iron particles that can linger from manufacturing processes like machining and fabrication. These iron particles, if left unchecked, pose a risk to the weld's integrity. While passivation noticeably enhances the look and extends the service life of stainless steel, it's essential to understand that it doesn't guarantee a permanent solution. The effectiveness of passivation depends on several factors, including the specific environment where the stainless steel will be used and the chosen passivation technique. Ongoing maintenance and careful selection of appropriate passivation methods based on application demands are crucial for ensuring long-term corrosion resistance and optimal performance.
Stainless steel's corrosion resistance stems from a thin, protective chromium oxide layer formed through a process called passivation. However, welding introduces complexities. Techniques like electropolishing can often create a superior passivation layer compared to traditional chemical methods, improving smoothness and corrosion resistance. This emphasizes the importance of chromium, as its content directly impacts the effectiveness of the passivation layer, especially within the weld's heat-affected zone (HAZ). The HAZ undergoes microstructural changes during welding, potentially compromising corrosion resistance, highlighting the necessity of post-weld passivation.
The duration of exposure to the passivating solution is crucial. Even minor adjustments can significantly influence corrosion resistance, emphasizing the importance of precise passivation timeframes. Similarly, the temperature of the solution is sensitive, with higher temperatures generally accelerating the process but potentially leading to damage if uncontrolled. The optimal pH range for the solution is typically neutral to slightly acidic, as this helps in forming a dense and high-quality oxide layer.
Successful passivation requires a meticulously clean surface. Any remaining oils, oxides, or contaminants can disrupt the formation of a uniform passivation layer, highlighting the need for thorough surface preparation. While chromium plays a vital role, other alloying elements such as molybdenum and nickel can further enhance the process, but their impact is alloy-specific. It's crucial to realize that passivation is not foolproof; a poorly performed passivation can lead to localized corrosion. Tests like ASTM A967 are valuable tools to verify the thoroughness of the process. In industries with stringent regulatory requirements, certification of the passivation procedure might be essential, ensuring that it meets specific industry standards.
Weld Passivation Enhancing Corrosion Resistance in Stainless Steel Structures - Key Benefits of Weld Passivation in Structural Applications
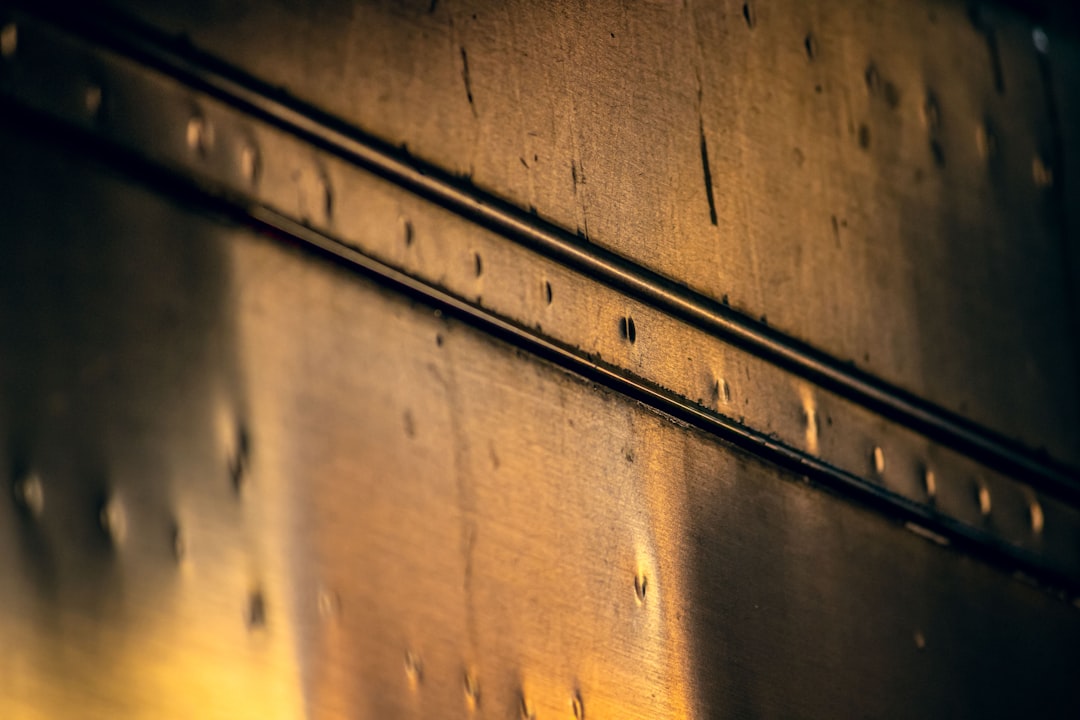
Weld passivation offers a critical advantage for stainless steel structures, especially in applications where corrosion resistance is paramount. The process helps repair the protective chromium oxide layer that can be damaged during the welding process, significantly reducing the chance of corrosion-related issues like localized corrosion. Beyond removing contaminants like iron particles and other residues from fabrication, it also prepares the surface for optimal performance in harsh conditions. This meticulous preparation, however, is essential. If the process isn't executed with care, including ensuring a clean surface prior to passivation, the protective layer might not form properly and will not offer the expected corrosion resistance. This emphasizes the critical need to understand and adhere to best practices when implementing passivation to achieve the desired long-term performance and reliability. It is important to recognize that passivation, despite its advantages, doesn't automatically ensure perfect corrosion protection in all cases. The effectiveness is directly linked to proper surface preparation and precise adherence to passivation procedures. As a result, a clear understanding of the limitations and best practices for weld passivation in different structural environments continues to be crucial for maximizing the structural integrity and longevity of stainless steel structures.
Recovering the protective chromium oxide layer on stainless steel after welding is a key aspect of weld passivation, crucial for maintaining its corrosion resistance. This process involves immersing the welded component in an acidic bath, often nitric acid, to remove debris like iron particles, oils, and other contaminants. Through this process, a thin yet robust chromium oxide layer is created on the stainless steel surface, providing a barrier against environmental attack.
This treatment is particularly important because it directly strengthens the inherent corrosion resistance of stainless steel alloys, making it vital for components facing aggressive environments. Specifically, the removal of free iron contamination during the passivation step significantly lessens the risk of localized corrosion issues that can lead to premature component failure.
However, the effectiveness of passivation hinges on a precise execution. Poor passivation can compromise the protective layer, leading to corrosion problems and shortened component lifespan. This emphasizes that thorough surface cleaning before passivation is crucial because any remaining contamination can obstruct the formation of a continuous protective oxide layer.
The chromium content within the stainless steel greatly influences passivation's success; alloys with higher chromium levels form a more resistant oxide layer. Other elements, like molybdenum and nickel, can further bolster corrosion resistance, but this effect varies by specific alloy. The creation of this layer also contributes to a smoother surface, resulting in a more polished aesthetic.
Furthermore, passivation isn't limited to just enhancing corrosion resistance. Some studies suggest passivation can improve wear and fatigue resistance, specifically by strengthening the weld zone and reducing the chance of cracks forming in those areas that experience repetitive loads.
The heat-affected zone (HAZ), altered during welding, is particularly susceptible to corrosion due to microstructural changes. As such, meticulous passivation of this area is crucial to maintain structural integrity. Additionally, passivation plays a role in surface cleanliness, acting as a decontamination method in preparation for the intended application. This makes it especially important for stainless steel grades containing sulfides where passivation counteracts the impact of these elements.
The duration, temperature, and pH of the passivating solution play critical roles in the process. Minor adjustments can significantly impact the quality of the oxide layer, highlighting the need for meticulous control. Electropolishing methods, while more advanced, are often observed to create a thicker and smoother protective layer compared to chemical passivation, potentially leading to superior long-term corrosion resistance.
It's important to note that specific industries may have regulatory requirements for passivation, often including certification processes and testing like ASTM A967 to guarantee that the weld meets quality and performance criteria. This reinforces that the passivation process is not just a post-weld treatment but rather a crucial aspect of quality assurance and ensuring components endure harsh environments for their intended service life.
Weld Passivation Enhancing Corrosion Resistance in Stainless Steel Structures - Common Techniques and Methods for Effective Passivation
Passivation is a key step in ensuring the long-term corrosion resistance of stainless steel, particularly after welding. The process generally involves using acidic solutions, like nitric acid, to clean the surface and encourage the formation or reformation of a chromium oxide layer. This protective layer acts as a barrier against corrosive agents, hindering the degradation of the metal. The effectiveness of passivation hinges heavily on the thoroughness of the surface preparation before treatment. Any lingering contaminants like oil or iron residue can disrupt the development of a uniform oxide layer, compromising its protective function.
More sophisticated techniques, such as electropolishing, can provide a smoother and often more durable passivated surface compared to traditional chemical methods. Factors like the temperature and pH of the passivation solution, as well as the duration of immersion, play crucial roles in the process. Careful control of these parameters is vital for ensuring the formation of a dense and effective chromium oxide layer. Optimizing passivation techniques in combination with meticulous cleaning protocols is crucial for achieving the maximum corrosion resistance desired for stainless steel structural components.
1. **Electropolishing's Influence**: Electropolishing stands out as a method that can produce a smoother surface compared to the more standard chemical passivation processes. Interestingly, it also seems to result in a thicker and denser chromium oxide layer. This suggests that in harsher conditions where corrosion is a larger concern, electropolishing may offer a more effective solution than traditional methods.
2. **Molybdenum's Role**: The presence of molybdenum within the stainless steel alloy appears to significantly enhance the resistance to pitting corrosion, especially when the environment includes high concentrations of chloride ions. This illustrates how the careful selection of alloying elements can be pivotal in maximizing the results of the passivation process and enhancing overall corrosion resistance.
3. **Solution Temperature's Importance**: While a higher temperature during passivation accelerates the reaction, there's a risk of damaging the oxide layer if not carefully managed. Even minor temperature fluctuations could result in a lower quality passivation layer, and in turn, a compromised level of corrosion resistance.
4. **The Balancing Act of Acid Concentrations**: The concentration of the acid bath employed during passivation is a critical factor to consider. A concentration that's too high could excessively etch the stainless steel surface. On the other hand, if the concentration is too low, it might not be effective at removing all the necessary contaminants. Finding the ideal concentration is crucial for achieving an effective passivation outcome.
5. **The HAZ's Vulnerability**: The heat-affected zone (HAZ), which experiences significant microstructural changes during the welding process, becomes susceptible to localized corrosion. This emphasizes that specific passivation techniques might need to be employed for this particular area.
6. **Chromium's Threshold for Effectiveness**: The efficiency of passivation is tied to the stainless steel's chromium content. In fact, alloys with less than 10.5% chromium might not achieve an adequate passivation effect. This underscores the importance of considering the material's properties during the design phase to ensure the desired level of corrosion resistance can be achieved.
7. **Verifying Success with Standards**: Standards like ASTM A967 provide objective measures for evaluating the effectiveness of the passivation process. When these procedures aren't rigorously followed, welds can remain susceptible to corrosion. This underscores the necessity of careful testing and validation to ensure passivation has successfully been achieved.
8. **Surface Preparation's Role**: The success of the passivation procedure hinges heavily on the thoroughness of the initial surface preparation. If remnants of the welding process such as slag and oxides are not adequately removed, they can lead to localized corrosion, effectively hindering the passivation layer's protection.
9. **Time, Thickness, and the Optimal Balance**: The relationship between the duration of passivation and the thickness of the resulting oxide layer isn't simply a linear one. In other words, simply extending the immersion time doesn't always lead to significantly thicker oxide layers. Finding the optimal exposure time is crucial for balancing a high-quality passivation with efficient process management.
10. **Regulations and Industry Requirements**: In specific industries like aerospace or biomedical, adhering to passivation standards is a critical aspect of compliance. Certification processes are commonly integrated into workflows to ensure the passivation process meets demanding performance and safety standards. This illustrates that passivation has evolved beyond simply being a post-weld treatment and has become a vital aspect of quality control and ensuring that critical components can reliably function in challenging environments.
Weld Passivation Enhancing Corrosion Resistance in Stainless Steel Structures - Impact of Passivation on Chromium Oxide Layer Formation
Passivation's influence on the formation of a chromium oxide layer is central to improving stainless steel's resistance to corrosion, especially after welding. The process typically involves a thorough surface cleaning to eliminate contaminants, followed by exposure to an acid solution. This facilitates the creation of a stable, uniform chromium oxide layer that shields the metal from environmental factors. This protective layer plays a pivotal role in maintaining weld integrity, particularly within the heat-affected zone (HAZ), a region often more prone to corrosion. The chemical composition and characteristics of the stainless steel, most notably its chromium content, greatly affect the effectiveness of the passivation process. Achieving a desirable outcome requires careful control of the passivation parameters to prevent localized corrosion. While passivation offers significant benefits, it's crucial to emphasize that the process itself can be easily compromised if not carried out correctly. If poorly executed, the protective chromium oxide layer will not be optimal, leading to reduced corrosion resistance.
The formation of a chromium oxide layer through passivation is generally considered uniform, but environmental factors can introduce inconsistencies. These variations can create areas more susceptible to localized corrosion, which is something researchers and engineers need to be mindful of.
During passivation, particularly with acidic solutions, there's a risk of hydrogen generation. If this hydrogen isn't adequately released, it could lead to hydrogen embrittlement and potentially harm the stainless steel's structural integrity, highlighting a potential drawback.
While chromium is fundamental to passivation, other alloying elements like nickel and molybdenum play roles that differ. For example, molybdenum's benefits seem to be concentrated in resisting pitting and crevice corrosion, whereas nickel's influence is primarily seen in improved ductility. How these impacts intersect with the formation and overall performance of the passivation layer requires further investigation.
It's intriguing that the thickness of the chromium oxide layer doesn't follow a straightforward relationship with the time spent in the passivation solution. After a certain point, increasing the immersion time may not deliver a proportionally thicker oxide layer, nor necessarily enhance corrosion resistance. Finding that optimal exposure period for best results is a key area of study.
It appears that electropolishing has advantages beyond just removing surface imperfections. It can potentially reduce iron particle buildup and improve how the chromium oxide layer sticks to the surface, resulting in a greater degree of corrosion resistance compared to traditional methods.
There's a narrow range for ideal passivation temperatures, generally considered to be between 20-50°C. Exceeding these limits can either lead to an inadequate oxide layer or even damage the existing one, showcasing a very delicate balance in the process.
A smoother stainless steel surface generally allows for a more uniform passivation layer. In contrast, a rough surface may create traps for contaminants, interfering with the cleaning process and impacting the effectiveness of passivation.
Residual iron left on the surface after passivation can accelerate localized corrosion, particularly in environments containing chlorides. This underscores that meticulous surface preparation before passivation is paramount to achieving the desired outcome.
The economic consequences of poor passivation can be severe, particularly in industries where corrosion-related failures can have wide-ranging impact. Besides increased maintenance and repair costs, neglecting careful passivation can also lead to potential liabilities, making adherence to proper protocols not only a quality measure, but also a key aspect of risk management.
Compliance with standards and industry practices, such as ASTM A967, is no longer merely a step in the process, but is increasingly becoming a core component of structural integrity and manufacturing operations in many sectors. Understanding these regulatory requirements, and the reasoning behind them, is increasingly important for engineers and designers working in the field.
Weld Passivation Enhancing Corrosion Resistance in Stainless Steel Structures - Challenges and Considerations in Weld Passivation Procedures
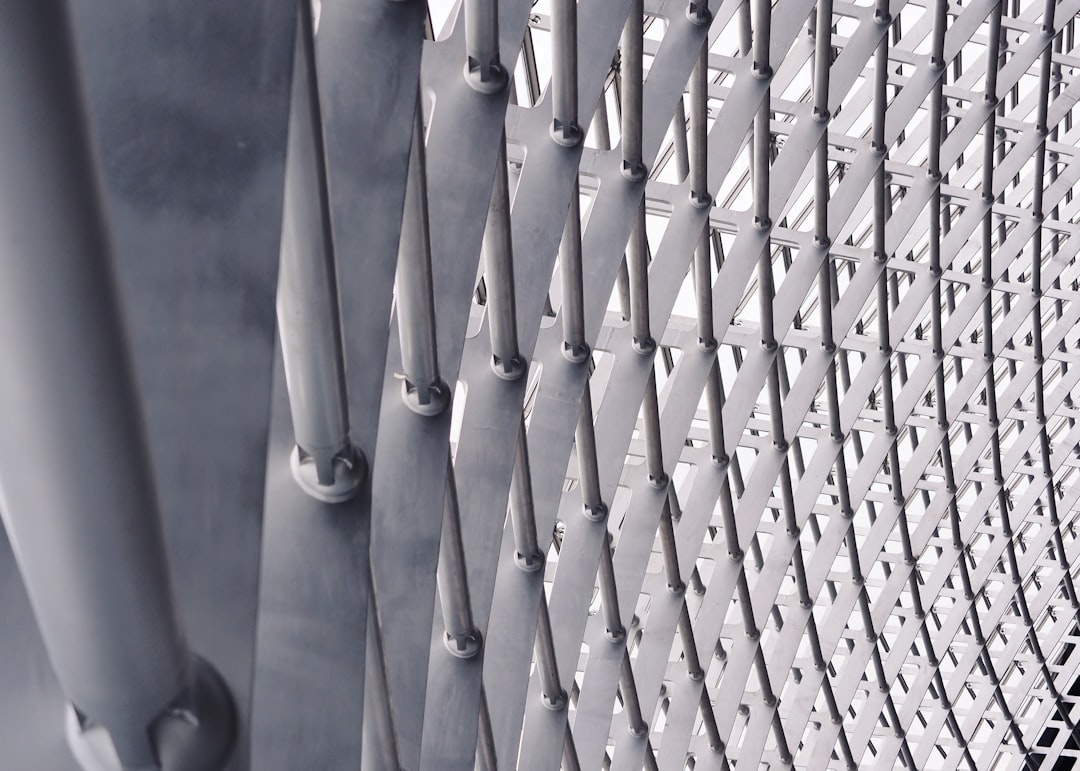
The section on "Challenges and Considerations in Weld Passivation Procedures" highlights the crucial factors that influence the success of passivation in restoring and improving the corrosion resistance of stainless steel after welding. Maintaining a pristine surface is paramount, as any leftover contaminants from machining or fabrication can disrupt the formation of a consistent, protective chromium oxide layer, potentially leading to corrosion. Furthermore, carefully managing the passivation process is critical, including the temperature, pH, and duration of exposure to the passivating solution. Even small variations in these factors can impact the quality and longevity of the oxide layer. A key challenge arises in the heat-affected zone (HAZ), which undergoes microstructural changes during welding, and necessitates special consideration for effective passivation. Ultimately, recognizing these obstacles and adhering to the proper passivation protocols is essential for ensuring optimal corrosion resistance in various stainless steel structural applications.
The welding process, while joining metal components, unfortunately disrupts the inherent protective chromium oxide layer that grants stainless steel its exceptional corrosion resistance. This disruption is particularly evident in the heat-affected zone (HAZ), where the material undergoes significant microstructural alterations due to the intense heat, making it more prone to localized corrosion. Therefore, the implementation of post-weld passivation treatments becomes crucial to restore and optimize corrosion resistance in these susceptible areas.
However, passivation isn't without its own set of challenges. During acid-based passivation procedures, hydrogen can be generated. If this hydrogen becomes trapped within the stainless steel's structure, it could trigger hydrogen embrittlement, a phenomenon that can seriously impact the material's structural integrity. Moreover, the surface condition of the stainless steel prior to passivation plays a significant role in the process's success. A rough surface can act as a trap for contaminants, hindering their removal during cleaning and increasing the likelihood of localized corrosion at those trapped areas.
The selection of stainless steel alloy composition also influences passivation's efficacy. Alloying elements like nickel and molybdenum contribute in distinct ways. For instance, molybdenum proves particularly beneficial in resisting the insidious effects of pitting corrosion, especially in environments laden with chloride ions, showcasing how careful alloy selection can tailor corrosion performance during passivation itself. The temperature of the passivation bath is also a critical factor. Maintaining an optimal temperature range between 20-50°C is crucial, as exceeding these limits can either result in a deficient oxide layer or damage the protective layer already formed.
The time spent immersing the stainless steel in the passivation solution does not always directly correlate to the thickness of the resulting oxide layer. Reaching a point of diminishing returns emphasizes that achieving an ideal exposure duration requires careful consideration to optimize the process. Furthermore, the solution's pH level plays a major part in oxide layer development. Generally, a neutral to slightly acidic pH is preferred for promoting a high-quality oxide layer, but extreme values can either hamper or damage this protective barrier.
In industries with stringent regulatory standards, like aerospace and pharmaceutical applications, meticulous compliance with passivation procedures is essential. Standards like ASTM A967 guide these practices and ensure the weld's integrity and safety. Failing to adhere to these standards can not only compromise the stainless steel's corrosion resistance but also potentially lead to severe safety and liability repercussions.
Compared to conventional chemical passivation methods, electropolishing offers a distinct advantage. It yields a noticeably smoother surface along with a thicker, denser chromium oxide layer. In highly corrosive environments, electropolishing appears to offer a superior approach for protecting against corrosion.
Finally, the economic ramifications of inadequate passivation can be significant, ranging from increased maintenance and repair costs to potentially catastrophic failures in demanding applications. These consequences underscore the crucial need for well-executed passivation, not merely as a technical step but also as a vital business consideration that directly influences the long-term performance and safety of stainless steel structures.
Weld Passivation Enhancing Corrosion Resistance in Stainless Steel Structures - Future Trends in Passivation Technology for Stainless Steel Structures
The increasing use of stainless steel in diverse applications necessitates continuous improvement in passivation technologies to ensure optimal corrosion resistance. Emerging trends indicate a focus on developing advanced passivation methods for newer stainless steel alloys, including duplex and super duplex grades. These alloys, with their unique microstructures, offer enhanced mechanical properties and corrosion resistance, making them suitable for demanding environments such as marine, oil and gas, and nuclear industries. Specifically, duplex passivation techniques have demonstrated potential in significantly reducing susceptibility to pitting corrosion in stainless steel structures. Furthermore, electropolishing is gaining traction as a more sophisticated method, providing a thicker, smoother chromium oxide layer compared to traditional chemical passivation. Despite these advancements, ensuring optimal passivation remains a delicate balance. The presence of residual contaminants from welding or machining can interfere with the protective layer formation, potentially leading to localized corrosion issues. Therefore, practitioners must remain mindful of surface preparation and carefully control passivation parameters like temperature, pH, and exposure duration to achieve a durable and effective oxide layer. As the challenges of corrosion become more complex, continued research and development will be crucial to refine existing passivation techniques and explore innovative solutions to ensure long-term performance and durability of stainless steel structures in a variety of corrosive conditions.
The effectiveness of passivation in stainless steel structures, particularly after welding, is significantly influenced by a variety of factors. For instance, the surface texture of the stainless steel plays a role, with rougher surfaces more prone to trapping contaminants that can disrupt the formation of a uniform chromium oxide layer. This can lead to localized corrosion, which can compromise the intended protection offered by passivation.
While traditional chemical methods often utilize nitric acid, more advanced techniques like electropolishing can create a superior passivation layer. Electropolishing not only results in a smoother surface but also a denser and thicker chromium oxide layer, suggesting that it could be a more effective approach for applications in harsh environments where corrosion is a major concern.
Temperature control is a delicate balancing act in the passivation process. While a higher temperature speeds up the oxide layer formation, temperatures beyond 50°C can lead to undesirable etching of the stainless steel surface. Conversely, if the temperature is too low, the oxide layer may not fully develop.
The chromium content of the stainless steel alloy is also a critical factor in determining passivation success. Surprisingly, alloys containing less than 10.5% chromium may not be able to form a sufficiently protective oxide layer during passivation. This suggests that material selection is vital in the design phase to ensure adequate corrosion resistance can be achieved.
Hydrogen, a byproduct of certain passivation processes, can be detrimental if it becomes trapped within the stainless steel. This can lead to hydrogen embrittlement, potentially jeopardizing the mechanical integrity of the structure. Thus, carefully managing the passivation conditions is crucial, especially for structural components subjected to significant stresses.
The presence of molybdenum within the stainless steel alloy has been shown to specifically enhance resistance to localized corrosion, particularly in environments rich in chloride ions. This emphasizes how alloy composition plays a role in shaping the final protective capabilities of the passivation process.
Interestingly, the relationship between the time spent during passivation and the oxide layer thickness isn't straightforward. Increasing the immersion time beyond a certain point does not necessarily correlate with a proportional increase in the layer thickness or in overall corrosion resistance. This signifies that carefully identifying the optimal exposure time is crucial for maximizing the benefits of passivation.
The pH of the passivation solution is another important factor impacting the quality of the oxide layer. While a neutral to slightly acidic range is generally ideal, extreme pH values can either impede the formation of a protective layer or even damage the one already present. Maintaining the pH within an appropriate range during passivation is important for achieving the desired outcomes.
Adherence to specific passivation standards and procedures is crucial in several industries like aerospace and medical devices. Regulations such as ASTM A967 are in place to ensure a consistent level of quality and safety. Ignoring these standards can not only negatively impact performance but also introduce severe safety and liability risks, especially in situations where structural integrity is paramount.
Finally, the economic consequences of insufficient passivation can be substantial, ranging from elevated maintenance expenses to potential catastrophic failures in crucial applications. This underlines the importance of careful and thorough passivation, not merely as a post-processing step but as a fundamental aspect of risk management for engineering projects that rely on long-term corrosion resistance.
More Posts from aistructuralreview.com: